铸钢上冠铸件工艺设计与数值模拟仿真毕业设计 精品.docx
《铸钢上冠铸件工艺设计与数值模拟仿真毕业设计 精品.docx》由会员分享,可在线阅读,更多相关《铸钢上冠铸件工艺设计与数值模拟仿真毕业设计 精品.docx(39页珍藏版)》请在冰豆网上搜索。
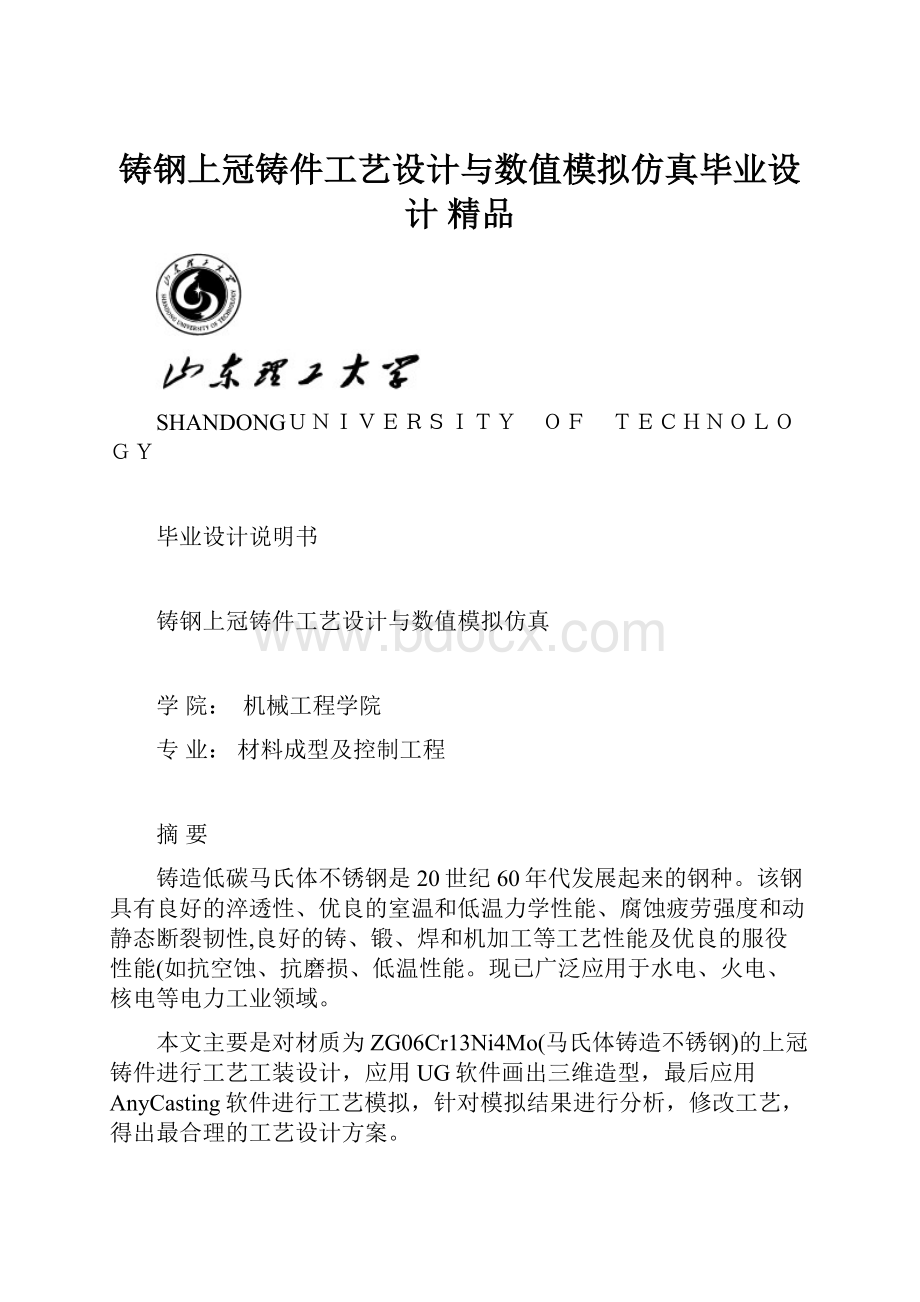
铸钢上冠铸件工艺设计与数值模拟仿真毕业设计精品
SHANDONGUNIVERSITY OF TECHNOLOGY
毕业设计说明书
铸钢上冠铸件工艺设计与数值模拟仿真
学院:
机械工程学院
专业:
材料成型及控制工程
摘要
铸造低碳马氏体不锈钢是20世纪60年代发展起来的钢种。
该钢具有良好的淬透性、优良的室温和低温力学性能、腐蚀疲劳强度和动静态断裂韧性,良好的铸、锻、焊和机加工等工艺性能及优良的服役性能(如抗空蚀、抗磨损、低温性能。
现已广泛应用于水电、火电、核电等电力工业领域。
本文主要是对材质为ZG06Cr13Ni4Mo(马氏体铸造不锈钢)的上冠铸件进行工艺工装设计,应用UG软件画出三维造型,最后应用AnyCasting软件进行工艺模拟,针对模拟结果进行分析,修改工艺,得出最合理的工艺设计方案。
上冠铸件,要求具有高强度,良好的抗磨耐蚀性,不允许有砂眼、缩松。
造型采用呋喃树脂砂,熔炼采用碱性电弧炉返回法,为保证铸件质量,浇注系统为顶注式,直浇道采用圆柱状,并在浇口杯处安放过滤网,在有热结处安放冷铁。
这样可以大大提高铸件出品率,提高了铸件的质量。
关键词:
铸造,铸造合金,变质处理,浇注系统设计,工艺工装设计
Abstract
Castinglow-carbonmartensiticstainlesssteeldevelopedinthe1960s.Thesteelhasgoodhardenability,goodroomtemperatureandlowtemperaturemechanicalproperties,corrosionfatiguestrengthandstaticanddynamicfracturetoughness,goodcasting,forging,weldingandmachiningprocessperformanceandexcellentserviceperformance(suchasanti-cavitationabrasionresistance,lowtemperatureperformance).Ithasbeenwidelyusedinthefieldofhydropower,thermalpower,nuclearpowerindustry.
Inthispaper,wedesignedthetechnologyandequipmentoftheShangguancastingsthatthematerialforZG06Cr13Ni4Mo(martensiticcaststainlesssteel).IusedUGsoftwaretodrawthree-dimensionalshape,thenusedAnyCastingsoftwaretoprocesssimulation,analysisedthesimulationresults,modifyedtheprocess,arrivedatthemostreasonableprocessdesignfinally.
Shangguancastingsrequiredthatthehighstrength,goodwearandcorrosionresistance,andnotallowedtohavetrachoma,shrinkage.WeusedthefuranresinsandtoModeling,thealkalineelectricarcfurnacereturnmethodtoMelting.Toensurethequalityofcastings,gatingsystemusingthetopnote,sprueusingacylindrical,andplacingthefilteratthegateCup,thecoldironinthehotjunction.Inthemethod,wecanimprovecastingyield,andthequalityofthecastingsgreatly.
Keywords:
casting,castingalloy,Modification,gatingsystemdesign,technologyandequipmentdesign
第一章引言
目前国内外水轮发电机过流部件广泛采用低碳马氏体不锈钢,典型材料为ZG06Cr13Ni4Mo(简称13-4),这种钢属于马氏体铬镍不锈钢,是在ZG10Cr13和ZG20Cr13不锈钢的基础上,降低C含量,提高Cr含量,同时将镍的含量控制在4%到6%范围内,并加入适量的Mo,使铸态组织基本为单一的板条马氏体。
因此,该钢具有一定的耐腐蚀性能,良好的强度、韧性、可焊性以及耐磨蚀性能以外,还具有良好的抗空蚀性能。
该钢抛弃了高碳马氏体与形成碳化物的强化手段,而以具有较高韧性的的低碳马氏体的形成和以镍、钼等合金元素作补充强化手段,通过适当地热处理使之具有低碳板条状马氏体与逆转变奥氏体的复相组织,从而既保留了高的强度水平又提高了钢的韧性和可焊性。
而以具有较高韧性的的低碳马氏体的形成和以镍、钼等合金与该钢抛弃了高碳马氏体形成碳化物的强化手段其结果是:
在改善力学性能、韧性和焊接性能等方面,都有突破性的进展。
经过长期研究和实践,现有的铸造技术已能保证13-4水轮机铸件的力学性能与标准要求相比有较大的裕度。
1.1低碳合金不锈钢铸造技术分析
低碳合金不锈钢铸造是在铸钢的基础上加入其他金属或非金属元素,不仅能保持铸钢的基本性能,而且由于合金化及热处理的作用,使低碳合金不锈钢具有良好的综合性能。
低碳钢和低碳合金不锈钢在工业上占有重要的地位,大量用于军事、工业、农业和交通运输等领域,也广泛用作建筑结构材料、家庭生活用具和体育用品等。
几十年来,围绕铸造低碳合金成分、组织、性能进行了大量的研究,使传统的低碳合金不锈钢综合性能上了一个新台阶。
其中研究和应用较多的是铬镍系合金和铬钼系合金。
与此同时,低碳合金不锈钢的熔炼及处理技术也飞速地发展,一方面这些先进的合金液处理技术提高了合金性能及铸件的整体性能;另一方面,更有利于生产和环境的保护。
1.1.1铬镍钼系合金性能
铬在钢中与碳和铁形成碳化物,并能部分地溶入固溶体中,并具有改善钢的高温性能的作用。
不锈钢最重要的技术要求是耐蚀性,合适的力学性能,良好的冷、热加工和焊接等工艺性能。
铬是不锈钢获得耐蚀性的基本元素。
当钢中含铬量达到12%左右时,钢在氧化性介质中的耐蚀性发生突变性的上升。
此时钢的表面形成一层极薄而致密的铬的氧化膜,阻止金属基体被继续侵蚀。
镍是不锈钢中的主要合金元素,其主要作用是稳定奥氏体,使钢获得完全奥氏体组织,从而使钢具有良好的强度和塑性,韧性的配合,并具有优良的冷,热加工性和冷形成性以及焊接,低温与无磁等性能,同时提高不锈钢的热力学稳定性,使之不仅比相同铬,钼含量的铁素体,马氏体等类不锈钢有更好的不锈性和耐氧化性介质的性能,而且于表面膜稳定性的提高,从而使钢还具有更加优异的耐一些还原性介质的性能。
铬镍钢中加入钼元素后,显著改善淬透性,有良好的空气硬化性能,并有优良的抗回火脆性能力,所以铬镍钼铸钢易于制造大型或复杂形状的铸件,采用正火热处理后仍可得到高强度的力学性能。
广泛应用于有高强度要求的工件。
此钢在高温下仍能保持较好的强度。
1.2计算机在铸造生产中应用
铸造成形是极其复杂的高温、动态、瞬时过程,其间发生一系列复杂的物理、化学、冶金变化,这些变化不能直接观察,也难以测试,所以其工艺设计多凭个人经验,技艺性强,而科学性不足。
计算机在铸造生产中的应用导致了铸造技术的发展和根本变革。
国内有关高等院校、科研院所和重点铸造企业经过20多年的努力,取得了积极的成果先后开展了计算机工艺辅助设计、成分和力学性能辅助设计,铸造合金凝固过程及温度场数值模拟、铸件充型过程的数值模拟,铸造过程、铸造合金品质和铸件品质以及铸造设备的检测与控制,铸造数据库、管理、计算机识图、机械手和机器人的应用等,并在生产中得到运用,应用范围越来越广,取得良好的经济效益,实现了基础理论定量指导工艺过程的目标。
同时计算机在铸造生产中的应用也促使铸造行业建立了完整的教育、科研、协会、学会、标准、质检、出版、信息体系[1]。
1.2.1UG软件介绍
UG是Unigraphics的缩写,是美国UnigraphicsSolutions公司开发的三维参数化软件,主要通过其虚拟产品开发(VPD)的理念提供多级化的、集成的、企业级的包括软件产品与服务在内的完整的MCAD解决方案。
目前拥有46000家客户,全球装机量近400万台套。
80年代后期引进我国以来,已广泛应用于航空航天、汽车、通用机械、模具等领域。
为了更好地了解UG在我国的研究、应用状况,我们对1979年以来国内所发表的有关UG的研究成果进行统计分析,试图从文献引证的角度揭示该领域的研究现状和研究动向,进而对UG在我国的研究、应用和发展进行测度,并寻求一些规律,为UG在我国的推广应用提供参考[2]。
1.2.2UG的主要应用领域分布
UG是一个集CAD/CAM/CAE于一体的计算机辅助机械设计制造软件,它具有强大的三维实体造型功能、曲面造型、虚拟装配及创建工程图等功能。
UGNX含有4大功能模块:
基础模块、CAD模块、CAM加工模块以及CAE模块。
CAD模块由许多独立功能的子模块构成,建模模块、制图模块、装配模块就是引入到机械制图教学当中的模块。
建模模块提供了草图、曲线、实体、自由曲面等工具,可以设计各种形状复杂的实体和曲面。
制图模块使设计人员能方便地获得与三维实体模型完全相关的二维工程图,当3D模型改变时,二维工程图也会同步更新。
这两个功能模块在协助讲解组合体以及机件的表达方法内容时,能通过迅速改变实体的形状,让学生从各种不同的角度观看和了解形体,提高学生分析视图的能力。
装配模块可以对装配体进行虚拟装配,具有很强的仿真性,提高了授课质量和效率。
UGS是航空/国防、汽车及运输、电子及电讯、制造及组装行业公认的领导者。
1.2.3UG在我国研究应用的发展趋势
UnigraphicsCAID/CAD/CAM/CAE系统提供了一种基于过程的产品设计环境,使产品开发从设计到加工真正实现了数据的无缝集成,从而优化了企业的产品设计与制造。
UG面向过程驱动的技术是虚拟产品开发的关键技术,在面向过程驱动技术的环境中,用户的全部产品及其精确的数据模型能够在产品开发全过程的各个环节保持相关,从而有效地实现了并行工程。
该软件不仅具有强大的实体造型、曲面造型、虚拟装配和生成工程图等设计功能,而且在设计过程中可进行有限元分析、机构运动分析、动力学分析和仿真模拟,从而提高了设计的可靠性。
同时,可采用建立的三维模型直接生成数控代码用于产品的加工。
另外它所提供的应用开发语言UG/OpenGRIP和UG/OpenAPI功能强大、简单易学,便于用户开发专用CAD系统。
具体来说,该软件具有以下特点:
(l)具有统一的数据库,真正实现了CAID、CAD、CAE和CAM等模块之间无数据交换的自由切换,并且可实施并行工程;
(2)采用复合建模技术,将实体建模、曲面建模、线框建模、显示几何建模与参数化建模等建模技术融于一体;
(3)采用基于特征的建模和编辑方法作为实体造型的基础,形象直观,类似于工程师传统的设计方法,并能采用参数驱动;
(4)曲面设计采用非均匀有理B样条作为基础,可用多种方法生成复杂曲面,特别适合于汽车外形和汽轮机叶片等复杂曲面的造型;
(5)二维图功能强大,可方便地从三维实体模型直接生成二维工程图,可以按照ISO标准和国标生成各种剖视图、标注尺寸、形位公差和汉字说明等;
(6)以Parasolid为实体建模核心,目前许多著名CAD/CAE/CAM软件均以此作为实体造型的基础;
(7)提供了界面良好的应用开发工具,并能通过高级语言接口,使UG的图形功能与高级语言的计算功能紧密结合,便于用户开发专用CAD系统;
(8)具有良好的用户界面,绝大多数功能都可通过图标实现;进行对象操作时,具有自动推理功能;在每个操作步骤中,都有相应的提示信息,便于用户做出正确的选择。
1.3Anycasting软件
AnyCasting是韩国AnyCasting公司自主研发的新一代基于Windows操作平台的高级铸造模拟软件系统。
是专门针对各种铸造工艺过程开发的仿真系统,可以进行铸造的充型、热传导和凝固过程的模拟分析。
它具有模拟准确、操作简便、功能全面及运算速度快等特点。
早在1985年,我们就研制出了AnyCasting软件核心求解器,1990年开始推广为商业化软件,通过多年来为大量不同领域如汽车、电子、重工、连续铸造行业的客户提供铸造工程咨询服务,AnyCasting积累了丰富的铸造工程经验,并不断地将实际的工艺经验在软件功能中得以实现,使得AnyCasting日益成为当今世界上技术最先进,包含丰富实际工程经验的铸造模拟分析软件系统[3]。
AnyPRE作为AnyCasting的前处理程序,AnyPRE可以实现CAD模型的导入,有限差分网格的划分,模拟条件的设置,并调用AnySOLVER进行求解。
使用AnyPRE,您可以进行多种设置包括工艺流程和材料的选择来模拟铸造成型过程,设置边界、热传导和浇口条件,也能通过特殊功能模块来设置一些设备和模型。
另外,你还可以通过AnyPRE提供的CAD功能来查看、移动/旋转实体坐标系统。
AnyMESH能编辑由AnyPRE生成的网格文件。
您可以轻松地修改网格信息而不改变几何模型。
AnyDBASE作为一个能概括铸造成型中熔体,模具和其他材料性能的数据库管理程序,AnyDBASE主要分为常规数据库和用户数据库。
常规数据库提供了具有国际标准的常用材料性能,而用户数据库使用户能保存和管理修改或附加的数据。
用户能简单的选择感兴趣的材料而不需要输入几百种不同的材料性能。
另外,它还提供每种材料的传热系数,提高了程序的方便性。
AnySOLVER作为AnyCasting的求解器,AnySOLVER能够根据你的设定计算流场和温度场。
铸造成型模拟包括计算熔体充型过程的流动分析和熔体凝固过程的传热/凝固分析。
只有在两个分析都准确的前提下才能正确预测可能造成缺陷的区域。
anyPOST作为AnyCasting的后处理器,可以通过读取anySOLVER中生成的网格数据和结果文件在屏幕上输出图形结果。
使用anyPOST,你可以用二维和三维观察充型时间,凝固时间,等高线(温度,压力,速率)和速度向量,也可以用传感器的计算结果来创建曲线图。
这个程序具备动画功能使用户把计算结果编辑成播放文件,通过结果合并功能来观察各种二维或三维的凝固缺陷。
图1.1AnyCasting软件的组成部分
第二章上冠铸件的铸造工艺设计
随着现代科学技术的发展,要求金属铸件具有高的力学性能、尺寸精度和低的表面粗糙度值,要求生产周期短、成本低。
因此,本上冠铸件在生产之前,首先应进行铸造工艺设计,使铸件的整个工艺过程都能实现科学操作,才能有效地控制铸件的形成过程,达到优质高产的效果。
上冠铸件的铸造工艺设计要根据其结构特点、技术要求、生产批量和生产条件等,确定铸造方案和工艺参数,绘制铸造工艺图等技术文件的过程。
其铸造工艺设计的好坏,对铸件品质、生产效率和成本起着重要作用。
2.1上冠铸件的结构工艺性分析
该上冠铸件属于壁厚相差悬殊的回转体结构,由于材料的导热性差且铸造时钢水在型腔内的温度差较高,使上冠的冷却极不均匀,产生较大的温度梯度形成较大的热应力与组织应力,且易在中间壁厚处形成缩松缩孔等缺陷。
所以要在上冠件壁厚处安放暗冒口,进行补缩,在外轮廓热节圆处安放冷铁,这样可以很好地补松补缩,提高铸件的工艺出品率和经济效益,同时也可以提高铸件的致密度和铸件质量。
2.1.1上冠铸件的主要技术要求
(1)铸件应作正回火处理;
(2)铸件材料及机械性能应符合JB/T10264-2001的要求;
(3)粗加工后按GB7233-87标准作超声波探伤检查,达Ⅱ级要求;
过流面加工后按GB/T9444-1988进行磁粉探伤,达Ⅱ级要求;
(4)同炉浇铸试验棒,回厂做化学成分和机械性能复核试验;
(5)过流面用样板检查。
2.1.2上冠铸件的结构分析
本上冠的材质为ZG06Cr13Ni4Mo,轮廓尺寸为1510mm×1510mm×623mm,毛量约为1950kg。
结构上属于厚、薄相差悬殊的大型回转体结构。
铸件各面均需加工,其中外侧弧面为精加工。
上冠铸件UG三维造型如图2-1所示。
图2-1上冠铸件UG三维造型图
2.2分型面位置的确定
分型面是指两半铸型相互接触的表面。
分型面的优劣,在很大程度上影响铸件的尺寸精度、成本和生产率。
我们在选择分型面时遵循的原则如下所述:
(1)应使铸件全部或大部分置于同一半型内。
为了保证铸件精度,如果做不到这项要求,也应该尽可能把铸件的加工面和加工基准面放在同一半型内。
(2)应尽量减少分型面的数目。
分型面少,铸件精度容易保证,且砂箱数目少。
(3)分型面应尽量选用平面。
平直分型面可简化造型过程和模底板的制造,易于保证铸件的精度。
(4)分型面的设计要便于下芯、合箱和检查型腔尺寸。
(5)不使砂箱过高,因为高砂箱造型困难,填砂、紧实、起模、下芯都不方便。
分型面通常选在铸件最大截面上。
(6)受力件的分型面的选择不应消弱铸件结构强度。
(7)注意减轻铸件的清理和机械加工工作量。
根据该上冠铸件的结构特点及选择分型面的一般原则,现提供选择分型面的三种方案如图2-2所示。
方案一:
优点:
1、有利于顺序凝固和冲型;
2、有利于铸件的补缩。
缺点:
钢液在铸型中的流动不稳定。
方案二:
优点:
1、重要面放在侧面和下面,有利于重要面得到致密的组织;
2、避免了吊芯。
缺点:
不利于顺序凝固和补缩。
方案三:
优点:
1、减小了砂箱尺寸;
2、有利于下芯。
缺点:
1、对上下箱的合箱、造型精度要求很高;
2、钢液在铸型中的流动不平稳。
(a) (b) (c)
图2-2分型面的选择方案(a)方案一(b)方案二(c)方案三
综合考虑各个分型面选择方案的优缺点,根据本铸件的实际结构及技术要求等因素,本上冠铸件采用方案一,使用两箱造型,铸件放在下砂箱。
2.3砂芯的设计及安放
砂芯的功用是形成铸件的内腔、孔和铸件外形不能出砂的部位。
芯头是指伸出铸件以外不与金属接触的砂芯部分。
芯头长度是指砂芯伸入铸型部分的长度。
为了合箱方便,避免上、下芯头和铸型相碰,对垂直芯头,上、下芯头都要设有斜度。
根据铸件结构、分型面的选择,本铸件的内部空腔采用一个砂芯来形成。
该砂芯设计的总的原则是:
使造芯到下芯的整个过程方便,铸件内腔尺寸精确,不致造成气孔等缺陷,使芯盒结构简单。
为了方便下芯,还要在芯头和芯座之间留有一定的间隙。
该砂芯的制芯方法选择自硬冷芯盒(原砂:
锆砂;粘结剂:
碱性酚醛树脂;催化剂:
甘油醋酸酯),其形状和尺寸如图2-3所示。
为了保证该砂芯在制造、运输、装配和浇注过程中不变形、不开裂或折断,生产中在砂芯中埋置了芯骨,以提高其强度和刚度。
图2-3砂芯结构、尺寸
2.4上冠铸件的工艺参数
(1)铸件尺寸精度的确定。
铸件尺寸公差是指铸件各部分尺寸允许的极限偏差,它取决于铸造工艺方法等多种因素。
通过查阅资料,确定该上冠铸件的尺寸精度为CT12。
(2)机械加工余量的确定。
上冠铸件表面需要进行加工,因此要预留加工余量。
所谓加工余量,是指在铸件工艺设计时预先增加的,而后在机械加工时又被切去的金属厚度。
各面所留机械加工余量如表1-1所示:
表1-1铸件各部分的机械加工余量
序号
基本尺寸/mm
加工余量等级
加工余量数值/mm
公差等级
公差数值/mm
1
2
3
4
5
6
7
8
Φ1510
Φ1380
Φ300
Φ500
378.8
369
244
Φ190
G
H
H
H
H
H
G
H
5.5
8
5
6
5
5
2.8
4
CT12
CT12
CT12
CT12
CT12
CT12
CT12
CT12
13
13
9
10
9
9
8
8
(3)ZG06Cr13Ni4Mo的铸造收缩率的确定。
为了确定模样和芯盒的工作尺寸,需要确定该上冠铸件的铸造收缩率。
所谓铸造收缩率是指铸件从线收缩开始温度(从液相中析出枝晶搭成的骨架开始具有固态性质时的温度)冷却到室温时的相对线收缩量。
如表2-2所示。
表2-2ZG06Cr13Ni4Mo体收缩率的计算
成分
影响系数
体收缩率(﹪)
元素
质量分数(﹪)
C
Mn
Si
Cr
Ni
W
0.06
1.0
1.0
13
4
0.1
+2.9
+0.0585
+1.03
+0.12
-0.0354
-0.53
+2.9
+0.0585
+1.03
+1.56
-0.1416
-0.053
5.3539
合计
ⅰ浇注温度为1580℃。
ⅱ为安全起见,取体收缩率=6℅。
(4)起模斜度的确定。
该上冠铸件的最大外轮廓处需确定其起模斜度。
因为该上冠铸件是自硬砂造型,采用木摸样,并且测得铸件测量面高度为116㎜,所以查《铸造工艺设计》[4]得a=0°40′,α=2.0。
2.5浇注系统的设计
浇注系统是铸型中液态金属流入型腔的通道的总称。
本次上冠铸件的浇注系统设计,应根据其结构特点、技术条件、合金种类,选择浇注系统结构类型、确定引入位置、计算截面尺寸等[5]。
2.5.1浇注系统的确定
在这次浇注系统设计中,充分考虑了浇注系统对液态金属充型方式、铸型温度分布、铸件质量的影响,根据上冠的结构,以及分型面的位置,决定采用树脂砂铸造,浇注系统采用顶注式工艺。
由于铸件属厚、薄相差悬殊的大型回转体结构,为保证铸件的充型能力,浇注系统设置为一个的截面为圆柱形的直浇道,然后对应一个截面为圆柱形的横浇道,适当增加平均静压头高度,浇注系统设置位置如图2-4所示,浇注系统UG三维造型图如图2-5所示。
图2-4浇注系统位置图2-5浇注系统三维图
综之,浇注系统设计为开放式顶注浇注系统,使用这种浇注系统金属液进入型腔时流速小,充型平稳,为了更好的撇渣,在浇口杯处安放陶瓷制成的厚为20mm的过滤网片,网孔直径为6mm,提高了金属液的质量。
2.5.2直浇道的设计
我们确定好浇注系统的安放位置及设计思路确定后,紧接着确定了浇注系统各组元的截面积。
确定浇注系统各组元截面积的目的,在于保证该上冠铸件型腔在预定的时间内充满,控制金属液通过浇注系统各组元时的流速、流量、及充满状态,达到大流量、低流速、平稳地充填。
本次浇注系统采用底注包浇注,以包孔截面积作为控流面积,浇注时间按下式计算:
t=
式中t——浇注时间,s;
G——型内钢液重量,kg,含涨箱和冒口重量;
N——同时浇注的浇包数,个;
n——每个