基于CCLink液位控制系统设计.docx
《基于CCLink液位控制系统设计.docx》由会员分享,可在线阅读,更多相关《基于CCLink液位控制系统设计.docx(38页珍藏版)》请在冰豆网上搜索。
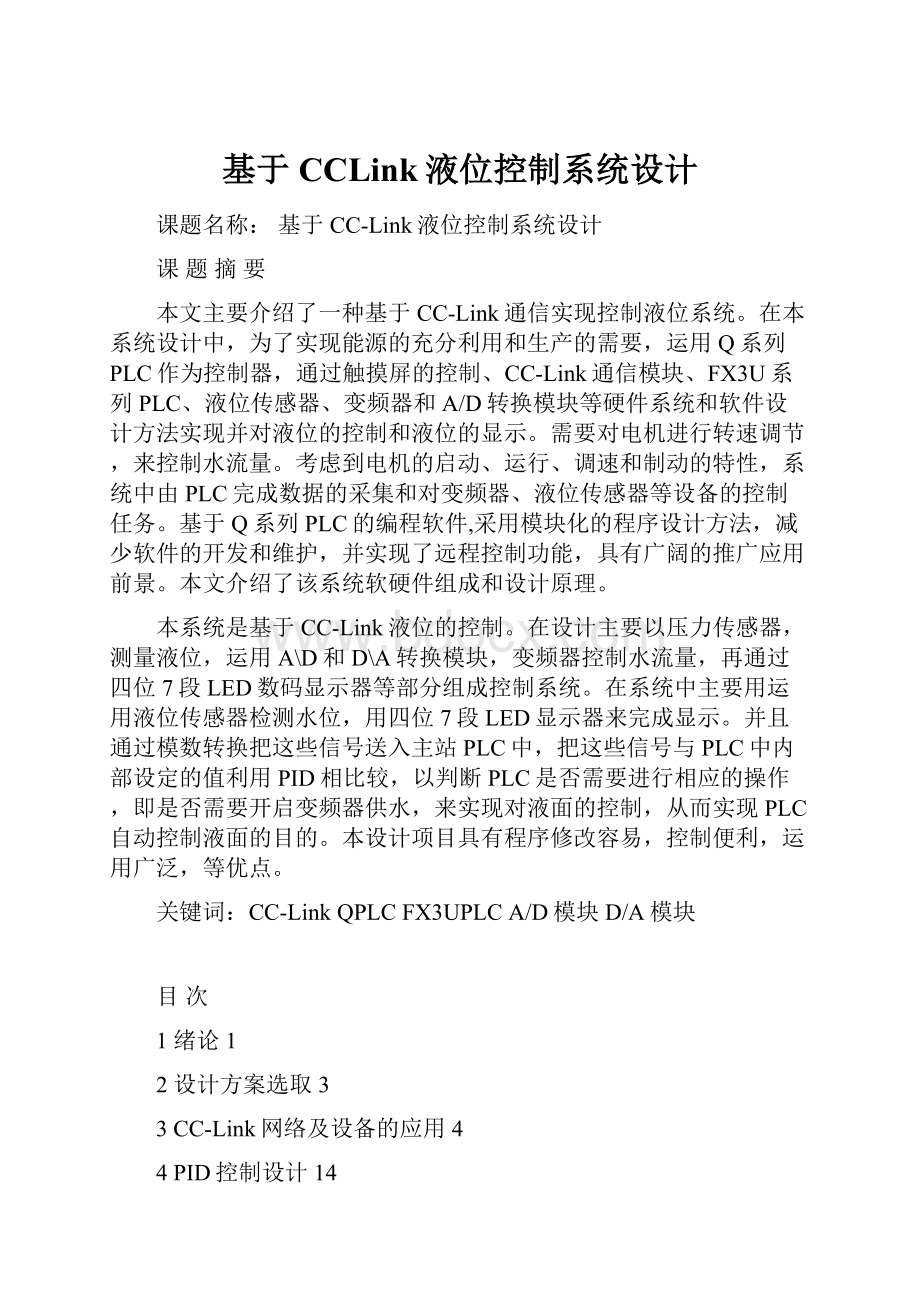
基于CCLink液位控制系统设计
课题名称:
基于CC-Link液位控制系统设计
课题摘要
本文主要介绍了一种基于CC-Link通信实现控制液位系统。
在本系统设计中,为了实现能源的充分利用和生产的需要,运用Q系列PLC作为控制器,通过触摸屏的控制、CC-Link通信模块、FX3U系列PLC、液位传感器、变频器和A/D转换模块等硬件系统和软件设计方法实现并对液位的控制和液位的显示。
需要对电机进行转速调节,来控制水流量。
考虑到电机的启动、运行、调速和制动的特性,系统中由PLC完成数据的采集和对变频器、液位传感器等设备的控制任务。
基于Q系列PLC的编程软件,采用模块化的程序设计方法,减少软件的开发和维护,并实现了远程控制功能,具有广阔的推广应用前景。
本文介绍了该系统软硬件组成和设计原理。
本系统是基于CC-Link液位的控制。
在设计主要以压力传感器,测量液位,运用A\D和D\A转换模块,变频器控制水流量,再通过四位7段LED数码显示器等部分组成控制系统。
在系统中主要用运用液位传感器检测水位,用四位7段LED显示器来完成显示。
并且通过模数转换把这些信号送入主站PLC中,把这些信号与PLC中内部设定的值利用PID相比较,以判断PLC是否需要进行相应的操作,即是否需要开启变频器供水,来实现对液面的控制,从而实现PLC自动控制液面的目的。
本设计项目具有程序修改容易,控制便利,运用广泛,等优点。
关键词:
CC-LinkQPLCFX3UPLCA/D模块D/A模块
目次
1绪论1
2设计方案选取3
3CC-Link网络及设备的应用4
4PID控制设计14
5液位控制系统的软件设计18
6触摸屏画面设计25
结论28
致谢29
参考文献30
附录A主站程序31
附录B本地站程序33
附录C远程站程序34
附录D7站程序36
附录E8站程序37
1绪论
随着科学技术的发展,生产中自动过程控制系统已代替传统仪器仪表,实现了对生产工艺参数的检测、显示、记录、调节、控制及报警等功能,它对提高化工生产线的作业率,改善产品质量及缩短新产品、新工艺的开发周期起到了极其重要的作用。
自动控制系统的特点是对生产过程进行实时监控,控制过程复杂,监控参数多且数据变化快,数据处理及存储量大。
根据过程控制系统的特点及不同生产工艺过程控制要求,应用不同的控制系统才可以既安全可靠又经济高效地完成生产任务。
CC-Link通信控制是许多工业生产中的重要参数之一,在化工生产领域,对液位的测量和控制效果直接影响到产品的质量。
PLC运行程序速度很快,在控制过程系统中的设备等单个或多个实际应用的工艺流程。
以往的硬接线继电器必须在每次更改工艺流程或产品后手动重新布线,使用CC-Link后,只需对其编程重新编写,即可完成整个控制,同时克服了以往继电器耗费高且效率低的缺陷。
由于PLC运行程序修改容易,控制便利,运用广泛,可靠性高等特点,所以广泛应用于生产实际中。
本文讨论了一种以CC-Link为住,设计的液位控制系统。
1.1液位控制系统
1.1.1液位控制系统现状
现在在生产中运用液位控制自动化主要是操控,就液位开关而言有许多类型,比如电容式液位开关、浮球式液位开关、电极式液位开关、电子式液位开关、电容式液位开关、光控式液位开关,自动控制可以采用PLC可编程逻辑控制器,也可以采用PAC可编程自动化控制器。
国内目前常采用PLC方式,随着社会经济的发展及公共管理科技水平的提高,今后可能会采用PAC控制方式。
当今,自动化仪表及装置有了很大的发展,表现为具有数字化、智能化、模块化、高精度化和小型轻量化等特点。
伴随着这些发展,出现了可编程控制器(PLC)、总线式工控机和新一代现场总线式智能仪表等。
其中,自控装置发展的最重要特点是智能化,通过现场总线技术,使自控装置间的信号传递由模拟量变为编码的数字量,实现了信号传递的重大转变。
PLC控制系统在挤出吹塑成型机的应用上也较为广泛。
挤出吹塑成型机是目前产量最大的一种生产容器和中空制品的吹塑成型设备,可生产出从最小只有1mL到最大可达10000L的各种容器制品。
如,牛奶瓶、饮料瓶、洗涤剂瓶、化妆品瓶、饮料桶、矿泉水桶以及化学试剂桶等。
近年来,挤出吹塑成型机的主要技术趋势是朝着自动化、智能化、高精度和高速度的方向发展。
1.1.2自动控制技术在化工领域的应用分析
随着现代科学技术的进步,由于在工业生产过程中实现了自动化,人们可通过自动化装置来管理生产,因此自动化装置与工艺及设备已结合成为有机的整体。
其中以PLC控制系统的技术较为成熟,在工业生产过程中的应用较为广泛,它具有结构简单、编程方便、性价比高、可靠性高和适应恶劣工业环境能力强等优点。
现在我国很多化工厂对化学反应炉的液位控制依然采用手工操作,这种工作方式具有工人工作紧张、工作条件艰苦、反应炉液位波动很大等缺点。
利用PLC控制系统对其进行改造,可实现整个工艺的控制,同时可控制精度在±0.5℃以内。
对于液位控制系统,我们在传统算法基础上作了改进,采用PID控制算法进行。
对于积分部分,采用了“不完全积分”处理方法。
通过试验,该系统达到了预期效果,可将水位高度误差控制在±0.5cm以内,而且动态性能比较好。
1.2本文研究的目的和意义
近年来,随着科学技术的快速发展,自动化仪表及装置有了很大的发展,表现为具有数字化、智能化、模块化、高精度化和小型轻量化等特点,伴随着这些发展,出现了可编程控制器(PLC)、分散型控制系统(DCS)、总线式工控机和新一代现场总线式智能仪表等。
其中.自控装置发展的最重要特点是智能化,通过现场总线技术,使自控装置间的信号传递由模拟量变为编码的数字量,实现了信号传递的重大转变。
可编程逻辑控制器是一种小型计算机,其运行速度很快,可控制过程系统中的设备等单个或多个实际应用的设备。
以往的硬接线继电器必须在每次更改工艺流程或产品后手动重新布线,使用PLC后,只需对其重新编程即可完成整个操作,同时克服了以往继电器耗费高且效率低的缺陷。
2设计方案选取
液位控制是工业中常见的过程控制,它对生产的影响不容忽视。
单容液位控制系统具有非线性、滞后、耦合等特征能够很好地模拟工业过程特征。
对于液位控制系统,常规的PLC控制由于采用固定的参数,难以保证控制适应系统的参数变化和工作条件变化,得不到理想效果。
如果用Q系列PID控制器的比例、积分、微分系数,就能更好地适应控制系统的参数变化和工作条件的变化。
从设备方面比较:
在工业中心307自动化实训室里,有一套完整的CC-Link网络设备,运用CC-Link控制,能够远距离的进行控制设备,在工厂里,能实现,人工不用到生产线上,只要在控制室里,就能实现操作。
从控制方面比较:
一个CC-Link网络最多可以连接64个内存站。
具有原理简单,易于实现,适用面广,控制参数相互独立,参数的选定比较简单。
从运算方面比较:
在PID控制期间,将由传感器测量的值(测定值)与预先设置的值(设置值)进行比较,然后调节输出值(操作值)以消除测定值与设置值之间的差。
PID控制器参数的自动调整是通过智能化调整或自校正、自适应算法来实现。
能良好的自我调节,更能准确的实现控制液位。
从可靠性,可维护性上比较:
电PLC无触点,采用密封、防尘、抗震的外壳封装结构,能适应工作现场的恶劣环境,使用寿命长,且有自我诊断功能,对程序执行的监控功能,现场调试和维护方便。
从速度上比较:
CC-Link网络传输速度有156kbps,625kbps,2.5Mbps,5Mbps,10Mbps,可满足高实时性的要求。
综合上面所说,设计需要达到性能要求,同时需要把PID控制和PLC运行,且同时要求远程控制与现场操作。
最终形成的方案是,利用PID为控制核心,设计一个对供水箱液位进行监控的系统。
根据监控的收入值,对水箱液位高度进行实时监控,并于起先输入的参数值进用PID不完全积分进行比较,再去控制变频器的参数,从而来进行控制流入水箱的液体流量的大小,最终达到液位的预设定值。
在运行中,液位传感器检测到液位,检测液位超出上限范围,报警器将开启,变频器参数值下降,关闭水泵,停止输入水箱的液体。
3CC-Link网络及设备的应用
3.1CC-Link发展史
在1996年11月,以三菱电机为主导联合其他38家公司,在其MELSECNET/MINIS3网络的基础上,经过协议的改进,软件、硬件的整合,推出了CC-Link这一全新的多厂商、高性能、省配线的现场网络。
并于1997年获得日本电机工业会(JEMA)颁发的杰出技术成就奖。
推出的CC-Link网络,是开放式架构的现场总线协定。
在2000年三菱电机释出了通讯协定的规范,因此CC-Link成为开放式的现场总线协定,同年也成立非盈利组织CLPA(CC-LinkPartnerAssociation)管理及监督CC-Link的网络技术并且提供技术协助。
CC-Link相容的产品包括工业电脑、可编程控制器、机器人、伺服驱动器、变频器、液压阀、类比或数位输入输出模组、温度控制器及流量控制器等。
CC-Link的技术协议从最基本的CC-Link开始,到2002年4月推出针对传感器层通信的CC-Link/LT,2002年11月推出将数据通信量扩大8倍的CC-LinkV2.0,再到2006年10月推出安全性网络CC-LinkSafety,CC-Link家族协议日渐丰满。
CC-Link技术通过国际CC-Link协会在全球推广和普及。
到2006年年底,CC-Link已经拥有800家合作伙伴公司,800种兼容产品。
CC-Link于2001年5月取得国际半导体行业标准SEMIE54.12,2005年5月取得中国国家标准GB/Z1976至2005,2006年4月取得国际标准ISO15745。
2009年8月时,CLPA的成员已超过1000个,和CC-Link相容的产品也已超过1000种。
2010年12月时,CC-Link网络上的设备已经超过7百万个。
3.1.1CC-Link组成
CC-Link网络可以将总共64个远程设备站、远程I/O站、本地站、备用主站或智能设备站连接到一个单独的主站。
网络结构如图3-1所示。
PLC模块检查来自主站模块的C-link网络信息,根据系统功能要求发送相应的控制信息给主站模块。
主站模块控制整个CC-Link网络,负责CC-Link网络的运行,并作为CC-Link网络与PLC之间的连接模块,接收来自远程站模块的数据信息,传送给PLC控制器,接收来自PLC控制器的控制信息并通过CC-Link网络发送到远程站模块。
将多个PLC模块控制的CC-Link网络连接在一起,才组成了一个简易的CC-Link简易的分布式系统。
图3-1CC-Link通信网络
3.1.2CC-Link性能
CC-Link以设备层为主,同是覆盖较高层次的控制层和较低层次的传感器层。
一般情况下,CC-Link整个网络可由1个主站和64个子站组成。
它采用总线方式通过屏蔽双绞线连接,网络中的主站由三菱FX系列一上的PLC或计算机担当,子站可以远程I/O模块、特殊功能模块、带有CPU的PLC本地站、人机界面、变频器、伺服系统、机器人以及各种测量仪表、阀门、数控系统等现场仪表设备。
如果需要增强系统的可靠性,可以采用主站和备用主站备份的网络系统构成方式。
CC-Link具有高速的数据传输速率,最高可以达到10Mb/s。
CC-Link提供循环传输和瞬时传输两种方式的通信,其循环传输每次链接扫描的最大容量是2048位和512字。
在循环传输数据量不够用的情况下,CC-Link提供瞬时传输功能,可将960字的数据用指令送给目标站。
CC-Link在连接64个远程I/O站、通信速率为10Mb/s的情况下,循环通信的链接扫描时间为3.7ms。
3.1.3CC-Link系统设备选型
表3-1主/本地模块选择类型表
产品名称
型号名称
说明
占用的站数
站类型
主/本地模块
QJ61BT11
Q系列的主/本地模块
对于本地找,1或者4个站
主站或本地站
A1SJ61BT11
AnS系列的主/本地模块
AJ61BT11
A系列的主/本地模块
A1SJ61QBT11
Q2AS系列的主/本地模块
AJ61QBT11
QnA系列的主/本地模块
在选择Q系列PLC主站、本地站的模块中,类型具有表3-1中的几类,这次我们设计运用的智能模块选择的是QJ61BR11N。
在运用CC-Link的时候,只要通过安装QJ61BT11N,不用创建顺控程序,只要打开电源,就启动CC-Link并刷新所有数据。
但是,如果连接模块的数目小于64的话,就有必要设定网络参数以优化链接扫描时间。
3.1.4数据传输方式
CC-Link的底层通讯协议遵循RS485。
CC-Link提供循环传输和瞬时传输2种通信方式。
一般情况下,CC-Link主要采用循环传输的方式进行通讯。
具体的方式是:
主站将刷新数据(RY/RWw)发送到所有从站,与此同时轮询从站1;从站1对主站的轮询作出响应(RX/RWr),同时将该响应告知其它从站;然后主站轮询从站2(此时并不发送刷新数据),从站2给出响应,并将该响应告知其它从站;依此类推,循环往复。
广播-轮询时的数据传输帧格式请参照下图,该方式的数据传输率非常高。
除了循环传输方式以外,CC-Link也支持主站与本地站、智能设备站之间的瞬时通讯。
从主站向从站的瞬时通讯量为150字节/数据包,由从站向主站的瞬时通讯量为34字节/数据包。
瞬时传输时的数据传输帧格式请参照下图,由此可见瞬时传输不会对循环传输的。
所有主站和从站之间的通讯进程以及协议都由通讯用LSI-MFP控制,其硬件的设计结构决定了CC-Link的高速稳定的通讯。
3.2PLC发展史
1968年美国通用汽车公司提出取代继电器控制装置的要求。
1969年,美国数字设备公司研制出了第一台可编程控制器PDP—14,在美国通用汽车公司的生产线上试用成功,首次采用程序化的手段应用于电气控制,这是第一代可编程序控制器,称Programmable,是世界上公认的第一台PLC。
1969年,美国研制出世界第一台PDP-14。
1971年,日本研制出第一台DCS-8。
1973年,德国研制出第一台PLC。
1974年,中国研制出第一台PLC。
发展:
20世纪70年代初出现了微处理器。
人们很快将其引入可编程控制器,使PLC增加了运算、数据传送及处理等功能,完成了真正具有计算机特征的工业控制装置。
此时的PLC为微机技术和继电器常规控制概念相结合的产物。
个人计算机发展起来后,为了方便和反映可编程控制器的功能特点,可编程序控制器定名为ProgrammableLogicController(PLC)。
20世纪70年代中末期,可编程控制器进入实用化发展阶段,计算机技术已全面引入可编程控制器中,使其功能发生了飞跃。
更高的运算速度、超小型体积、更可靠的工业抗干扰设计、模拟量运算、PID功能及极高的性价比奠定了它在现代工业中的地位。
20世纪80年代初,可编程控制器在先进工业国家中已获得广泛应用。
世界上生产可编程控制器的国家日益增多,产量日益上升。
这标志着可编程控制器已步入成熟阶段。
20世纪80年代至90年代中期,是PLC发展最快的时期,年增长率一直保持为30~40%。
在这时期,PLC在处理模拟量能力、数字运算能力、人机接口能力和网络能力得到大幅度提高,PLC逐渐进入过程控制领域,在某些应用上取代了在过程控制领域处于统治地位的DCS系统。
20世纪末期,可编程控制器的发展特点是更加适应于现代工业的需要。
这个时期发展了大型机和超小型机、诞生了各种各样的特殊功能单元、生产了各种人机界面单元、通信单元,使应用可编程控制器的工业控制设备的配套更加容易。
3.2.1Q系列PLC
Q系统PLC是日本三菱新推出的大/中型PLC,其基板的面积只是Ans系列的40%,另外新增加了12槽底板以符合用户的需求。
内置程序存储量可到252k步,如用扩展内存卡,则存储量可到32MB。
可以加7个扩展基板,总模块数可达64个本地输入/出点均数可达4096点,最远距离为13.2米。
可以用USB接口进行高速在线编程及监控。
Q系统可在以太网、MelsecNet、CC-Link等网络间实现无缝通讯。
凭借其强大的网络及软件功能,Q系统可实现工厂自动化与信息自动化的完美融合。
表3-2Q模式基本模块,性能模块规格
操作模式
基本模块
高性能模块
CPU型号
QOOJCPU
QOOCPU
QO1CPU
QO2CPU
QO2HCPU
Q06CPU
Q12HCPU
Q25HCPU
编程语言
梯形图/列表
梯形图/列表/SFC
I/O控制
刷新
I/O软元件点数
2048点
8192点
I/O点数
256点-1024点
4096点
程序容量(步)
8K
14K
28K
60K
124K
252K
运
算
速
度
LD指令
200ns
160ns
100ns
79ns34ns
MOV指令
700ns
560ns
350ns
237ns102ns
浮点加
---
1.8us782ns
变址赋值
无延迟时间
PCMIX值
1.6
2.0
2.7
4.410.3
常数处理
16位整数,32位整数
16位整数,32位整数,单精度实数,字符串
通信端口
RS-232:
115.2kbps(最大)
RS-232:
115.2kbps,USB:
12Mbps
I/O槽最大数
16
24
64
3.2.2FX3U-PLC
FX3U系列PLC的基本功能强大。
CPU处理速度达到了0.065us基本指令。
内置了高达64K步的大容量RAM存储器。
通过CC-Link网络的扩展可以实现最多达384点的控制。
大幅增加了内部软元件的数量。
FX3U系列PLC中集成了多项业界领先的功能。
晶体管输出型的基本单元内置了3轴独立最高100kHz的定位功能,并且增加了新的定位指令:
带DOG搜索的原点回归(DSZR),中断单速定位(DVIT)和表格设定定位(TBL),从而使得定位控制功能更加强大,使用更为方便。
内置6点同时100kHz的高速计数功能。
还有,FX3U系列PLC还专门强化了一部分功能。
FX3U系列专门增强了通信的功能,其内置的编程口可以达到115.2kbps的高速通信,而且最多可以同时使用3个通信口(包括编程口在内)。
FX3U系列此次新增加了高速输入输出适配器,模拟量输入输出适配器和温度输入适配器,这些适配器不占用系统点数,使用方便。
其中通过使用高速输出适配器可以实现最多4轴、最高200kHz的定位控制,通过使用高速输入适配器可以实现最高200kHz的高速计数。
3.3A/D、D/A模拟量输入输出模块
A/D输入转换模块有两种转换方法。
采样处理是对模拟输入值连续进行模/数转换并且转换的数字输出值存储在缓冲存储器中采样处理时间依据使用的通道数通道数设置成模/数转换允许和温度漂移补偿功能是否可用而定。
平均处理是对于指定了平均处理的通道按设定的次数或设定的时间进行模/数转换扣除最大值和最小值的数值之和算出平均值然后存储在缓冲存储器中。
(1)采样处理计算方法如:
不带温度漂移补偿功能
(处理时间)=(使用的通道数)*80(μs/1个通道)
带温度漂移补偿功能
(处理时间)=(使用的通道数)*80(μs/1个通道)+160μs
(2)平均处理计算方法:
当按设定的时间制定平均处理时,设定时间内处理重复的数目依据使用的通道数(允许模/数转换的通道数)和是否使用温度漂移补偿而定。
不带温度漂移补偿功能:
(处理重复的数目)=(设定的时间)*1000/{(使用的通道数)*80(μs/1个通道)}
带温度漂移补偿功能:
(处理重复的数目)=(设定的时间)*1000/{(使用的通道数)*80(μs/1个通道)+160}
当按设定时间指定平均处理时,为了存储使用缓冲存储器中的平均次数计算的平均值所需的时间依据使用的通道数(设置成模/数转换允许的通道数)和是否使用温度漂移补偿而定。
不带温度飘逸补偿功能:
(处理时间)=(设定的次数)*{(使用的通道数)*80}/1000
带温度漂移补偿功能:
(处理时间)=(设定的次数)*[{(使用的通道数)*80}+160]/1000
表3-3A/D模数转换模块的性能规格
项目
型号
Q64AD
模拟输入点
4点
模拟输入
电压
-10至10VDC(输入电阻值1MΩ)
电流
0至20mADC(输入电阻值250Ω)
数字输出
16位标志的二进制(正常分辨率模式:
-4096至4095)
I/O特点、最大分辨率
模拟输入范围
正常分辨率模式
高分辨率模式
数字输出值
最大分辨率
数字输出值
最大分辨率
电压
0至10V
0至4000
2.5mV
0至16000
0.625mV
0至5V
1.25mV
0至12000
0.416mV
1至5V
1.0mV
0.333mV
-10至10V
-4000至4000
2.5mV
-16000至16000
0.625mV
用户范围设置
0.375mV
-12000至12000
0.333mV
电流
0至20mA
0至4000
5μA
0至12000
1.66μA
4至20mA
4μA
1.33μA
用户范围设置
-4000至4000
1.37μA
-12000至12000
1.33μA
D/A输出模块可以获得与PLC,CPU同步的模拟输出。
在同步输出请求(YD),设置成ON并且在过了指定为PLC“CPU处理时间+120us”时间后将更新模拟输出。
然而模拟输出将固定为CH1不能使用其它通道(CH2至CH8),写入方式如图3-2:
图3-2PLC,CPU同步的模拟输出
表3-4D/A模数转换模块的性能规格如
项目
型号
Q64DA
模拟输出点数
4个通道
数字输入
16位标记的二进制
模拟输入
电压
-10至10VDC
电流
0至20mADC
I/O特点,最大分辨率
模拟输出范围
正常分辨率模式
高分辨率模式
数字输入值
最大分辨率
数字输入值
最大分辨率
电压
0至5V
0至4000
1.25mv
0至12000
0.416mv
1至5V
1.0mv
0.333mv
-10至10V
-4000至4000
2.5mv
-16000至16000
0.625mv
用户范围设置
0.75mv
-12000至12000
0.333mv
电流
0至20mA
0至4000
5μA
0至12000
1.66μA
4至20mA
4μA
1.33μA
用户范围设置
-4000至4000
1.5μA
-12000至12000
0.83μA
3.4D700变频器
3.4.1控制面板设计
图3-3变频器D700控制面板
表3-5控制面板按钮介绍
显示/按钮
功能
备注
RUN显示
运行时点亮/闪灭
点亮:
正在运行中
慢闪灭(1.4S/次):
反转运行中
快闪灭(0.2S/次):
非运行中
PU显示
PU操作模式时点亮
计算机连接运行模式时,为慢闪亮
监示用4位LED
表示频率,参数序号等
EXT显示
外部操作模式时点亮
计算机连接运行模式时,为慢闪亮
设定用按钮
变更频率设定.参数的设定值