甲醇教案.docx
《甲醇教案.docx》由会员分享,可在线阅读,更多相关《甲醇教案.docx(12页珍藏版)》请在冰豆网上搜索。
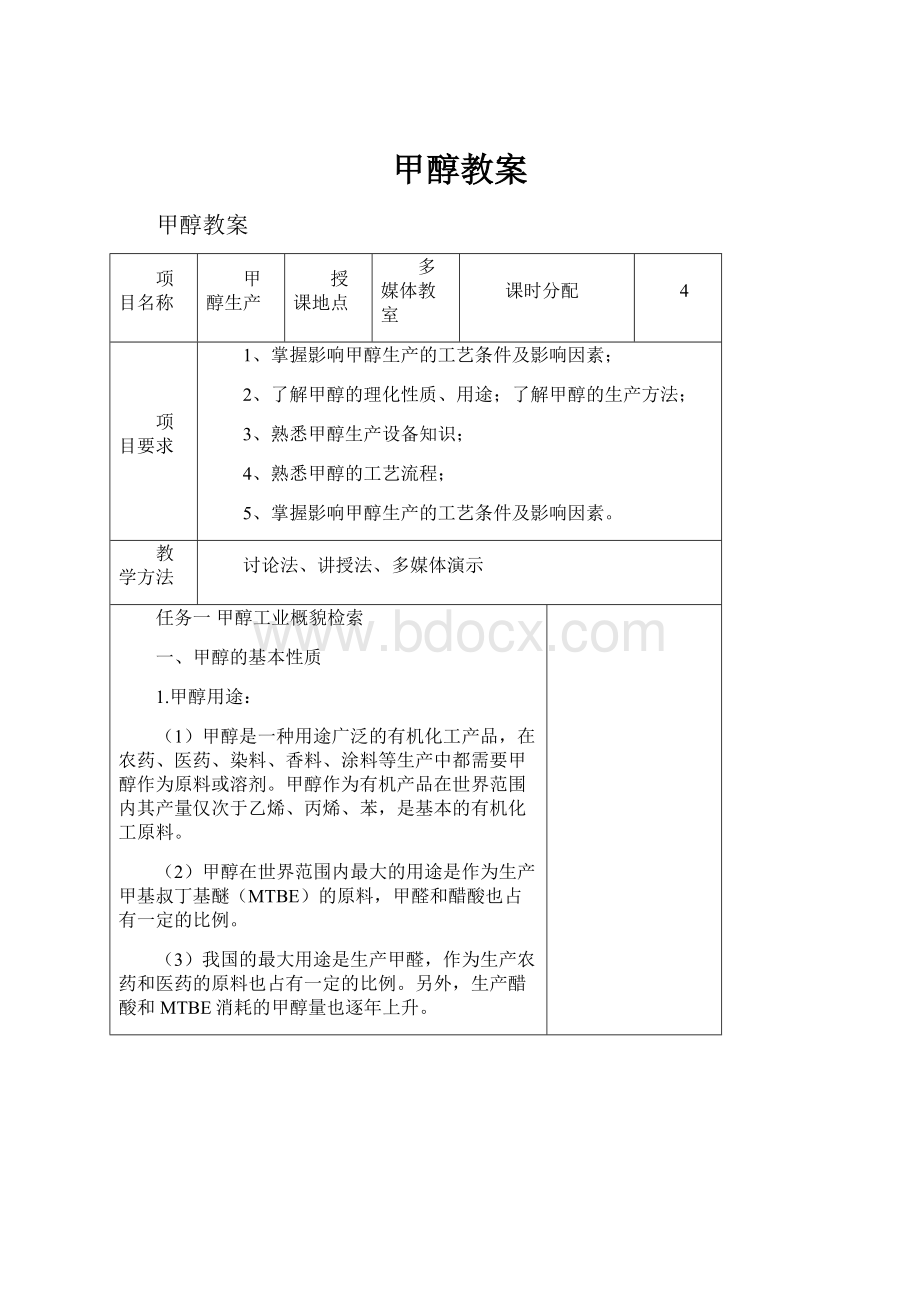
甲醇教案
甲醇教案
项目名称
甲醇生产
授课地点
多媒体教室
课时分配
4
项目要求
1、掌握影响甲醇生产的工艺条件及影响因素;
2、了解甲醇的理化性质、用途;了解甲醇的生产方法;
3、熟悉甲醇生产设备知识;
4、熟悉甲醇的工艺流程;
5、掌握影响甲醇生产的工艺条件及影响因素。
教学方法
讨论法、讲授法、多媒体演示
任务一甲醇工业概貌检索
一、甲醇的基本性质
1.甲醇用途:
(1)甲醇是一种用途广泛的有机化工产品,在农药、医药、染料、香料、涂料等生产中都需要甲醇作为原料或溶剂。
甲醇作为有机产品在世界范围内其产量仅次于乙烯、丙烯、苯,是基本的有机化工原料。
(2)甲醇在世界范围内最大的用途是作为生产甲基叔丁基醚(MTBE)的原料,甲醛和醋酸也占有一定的比例。
(3)我国的最大用途是生产甲醛,作为生产农药和医药的原料也占有一定的比例。
另外,生产醋酸和MTBE消耗的甲醇量也逐年上升。
2.物理性质:
甲醇是一种无色、略带乙醇香气的挥发性可燃液体,在常压情况下,密度0.8100g/mL,甲醇沸点为64.7℃,自燃点473℃(空气中)、461℃(氧气中)与水互溶,在汽油中有较大的溶解度。
3.化学性质:
①氧化(或脱氢)——银催化剂,600~650℃
催化剂也可是铜、铁钼等
②与碱金属发生取代反应
③脱水:
单独生成二甲醚——在催化剂和高温条件下,与氨反应脱水生成甲胺——在催化剂和高温、高压条件下。
④与芳胺反应生成甲基芳胺——在硫酸存在下加压加热反应
⑤酯化反应
⑥与氢卤酸反应生成卤代甲烷
⑦与亚硝酸反应生成硝基甲烷
⑧与乙炔生成甲基乙烯基醚——碱金属醇化物为催化剂
⑨与一氧化碳合成醋酸——铑催化剂,150~220℃和3.04MPa
⑩与异丁烯合成甲基叔丁基醚——离子交换树脂为催化剂,100℃以上
⑾热分解——350~400℃下分解为一氧化碳和氢
4.甲醇对人体危害
甲醇蒸汽与空气或氧气可形成爆炸性混合物,遇明火易燃;与氧化剂发生强烈反应;对眼睛和皮肤有强烈刺激性,可通过皮肤、呼吸道、消化道等引起中毒。
内服10mL有失明危险,30mL致人死亡,空气中最高允许浓度50mg/m3。
任务二甲醇生产工艺路线分析与选择
一、甲醇生产方法
早期的木材干馏法,今天在工业上已灾被淘汰子。
目前是以含碳原料转化为碳化合物,然后合成甲醇。
含碳原料目前主要是石油、煤炭,今后木材、农副产品、有机废料、城市垃圾等将成为甲醇生产的主要原料。
1、氯甲烷水解法
CH3Cl+H2O+NaOH→CH3OH+NaCl+H2O
2、甲烷部分氧化法
2CH3+O2→2CH3OH
3、由碳的氧化物与氢合成
CO+2H2→2CH3OH
CO2+3H2→2CH3OH+H2O
二、反应特点
甲醇合成反应是在有催化剂存在的一个体积缩小的、可逆的、伴有多种副反应发生的放热反应。
催化剂:
铜基催化剂。
主要成分:
CuO、ZnO、AL2O3,其中有活性的是铜,必须还原后使用。
还原方程式为:
CuO+H2=Cu+H2O
三、甲醇生产的热力学和动力学
1.热力学分析
反应热效应
放热反应,25℃反应热为△H0298=-90.8KJ/mol。
温度不同,热效应也不同温度越高反应的热效应也越大。
低温对反应有利
2.压力对平衡常数的影响
P↑,KN↑,xE↑,故应在高压下操作。
任务三甲醇生产工艺参数确定
一、反应温度的确定
由合成气合成甲醇的反应为可逆放热反应,其总速度是正、逆反应速度之差。
随着反应温度的增加,正、逆反应的速度都要增加,但是吸热方向(逆反应)反应速度增加的更多。
因此,可逆放热反应的总速度的变化有一个最大值,此最大值对应的温度即为“最适宜温度”,它可以从反应速度方程式计算出来。
实际生产中的操作温度取决于一系列因素。
如催化剂、压力、原料气组成、空间速度和设备使用情况等。
尤其取决于催化剂。
高压法锌铬催化剂上合成甲醇的操作温度是低于最适宜温度的。
在催化剂使用初期为640~650K,后期提高到650~680K。
温度太高,催化剂活性和机械强度很快下降,而且副反应严重。
低、中压合成时,铜催化剂特别不耐热,温度不能超过570K,而470K以下反应速度又很低,所以最适宜温度确定为500~540K。
反应初期,催化剂活性高,控制在500K,后期逐渐升温到540K。
二、反应压力的确定
与副反应比,主反应是摩尔数减少最多而平衡常数最小的反应,因此增加压力合成甲醇有利。
但是增加压力要消耗能量,而且还受设备强度限制,因此需要综合各项因素确定合理的操作压力。
(参见书图2-2)
用ZnO-Cr2O3催化剂时,反应温度高,由于受平衡限制,必须采用高压25-35Mpa,以提高其推动力。
而采用铜基催化剂时,由于其活性高,反应温度较低,反应压力也相应降至5-10Mpa。
三、原料气的组成确定
甲醇合成原料气化学计量比为H2︰CO=2︰1
CO过量:
不利温度控制;引起羰基铁在催化剂上的积聚,使催化剂失活,一般采用氢过量
H2过量:
抑制高级醇、高级烃和还原性物质的生成,提高甲醇的浓度和纯度;氢导热性好,利于防止局部过热和催化剂床层温度控制。
氢过量太多会降低反应设备的生产能力。
Zn-Cr2O3催化剂:
H2/CO为4.5左右;
铜基催化剂:
H2/CO为2.2-3.0
四、原料气纯度
原料气中有一定含量的二氧化碳时,可以降低反应峰值温度。
对于低压法合成甲醇,二氧化碳含量体积分数为5%时甲醇收率最好。
此外,二氧化碳的存在也可抑制二甲醚的生成。
原料气中有氮及甲烷等惰性物存在时,使氢气及一氧化碳的分压降低,导致反应转化率下降。
反应系统中的惰性气体含量保持在一定浓度范围。
工业生产上一般控制循环气量为新鲜原料气量的3.5-6倍。
原料气中硫化氢存在时,使铜催化剂中毒。
五、空间速率
空速影响选择性和转化率,直接关系到生产能力和单位时间的放热量。
适宜的空速与催化剂的活性、反应温度及进塔气体的组成有关
ZnO-Cr2O3:
35000-40000h-1
CuO-ZnO-Al2O3:
10000-20000h-1
增加空速在一定程度上能够增加甲醇产量。
增加空速有利于反应热的移出,防止催化剂过热。
空速太高:
转化率降低,循环气量增加,从而增加能量消耗;增加分离设备和换热负荷,引起甲醇分离效果降低;带出热量太多,造成合成塔内的催化剂温度难以控制。
任务四催化剂的选择与使用
一、甲醇合成催化剂
方法
催化剂
条件
备注
特点
压力,MPa
温度,℃
高压法
ZnO-Cr2O3
二元催化剂
25~30
380~400
1924年工业化
(1)催化剂不易中毒,再生困难
(2)副反应多
低压法
CuO-ZnO-Al2O3
三元催化剂
5~10
220~270
1966年工业化
(1)催化剂易中毒,再生容易,寿命为1-2年
(2)副反应少
中压法
CuO-ZnO-Cr2O3
三元催化剂
10~15
220~270
1970年工业化
二、催化剂使用
XCN-98型催化剂,用于低温低压下由一氧化碳与氢合成甲醇,可适用于各种类型的甲醇合成反应器,具有低温反应活性高,热稳定性好的特点。
化学组成
组分
CuO
ZnO
Al2O3
含量(质量分数)%
>52
>27
>8
催化剂的特性
外观
外形尺寸mm
(直径×高)
堆密度
103kg/m3
径向抗压碎强度
102N/m
有黑色金属光泽圆柱体
5×(4.5-5)
1.3-1.5
>270
三、注意事项
①为延长催化剂寿命,开始易用较低温度,过一定时间再升至适宜温度,其后随着催化剂老化程度升高,反应程度也相应高。
②因反应放热,反应热应及时移出,否则副反应增加,催化剂易烧结,活性降低。
故严格控制温度,及时有效地移走反应热是合成塔设计、操作之关键。
③停车时催化剂的操作
任务五典型设备的选择
一、甲醇生产设备
1.合成反应器
2.甲醇分离器
3.循环压缩机
二、甲醇合成反应器
(1)在操作上,要求催化剂床层的温度易控制,调节灵活,在5.0MPa下,合成反应器的转化率高,催化剂的生产强度大,能以较高能位回收反应热,床层中气体分布均匀,压降低。
(2)在结构上,要求简单紧凑,高压空间利用率高,触媒装卸方便。
(3)在材料上,要求具有抗羰基化物及抗氢脆的能力。
(4)在制造、维修、运输、安装上要求方便。
三、几种合成塔型式
⑴I.C.I公司多段冷激型甲醇合成反应器
单塔操作,能力大,控温方便,冷激采用菱形分布器专利技术,触媒层上下贯通,触媒装卸方便,所以普遍使用。
这类反应器因有部分气体与未反应气体之间的返混,所以催化剂空时产率不高,用量较大。
我国四川维尼龙厂首先引进此类反应器。
⑵MHI/MGC管壳-冷管复合型甲醇合成反应器
该反应器为Lurgi反应器的改进型,在管壳反应器的催化管内加一根冷管,用以预热原料气。
⑶Topsφe径向流动甲醇合成反应器
合成系统由三台绝热操作的径向流动反应器组成,三台反应器之间设置外部换热器移走反应热量,气体在床层中向心流动,床内装填Topsφe公司MK-101高活性催化剂。
⑷MFR多段径向流动甲醇合成反应器
该反应器由日本TEC公司开发,由外筒、催化剂筐和许多垂直的沸水管组成,沸水管埋于催化床中,合成气由中心管进入,径向流过催化床,反应后气体汇集于触媒筐与外筒之间的环形集流流道中,向上流动,由上部引出。
反应热传给冷管内沸水使其蒸发成蒸汽。
⑸Linde公司等温型甲醇合成反应器
Linde等温型甲醇合成塔,其结构与高效螺旋盘管换热器类似,盘管内为沸水,盘管外放置催化剂,反应热通过盘管内沸水移走。
⑹Lurgi公司管壳型甲醇合成反应器
其结构类似于常见的管壳型换热器,在管内装填催化剂,管外用4.0MPa的沸腾水充满,反应气体流经反应管,反应放热,热量通过管壁传给沸腾水,使其汽化,转变成蒸汽,管中心与沸腾水相差仅10℃左右。
⑺绝热-管壳外冷复合型甲醇合成反应器
绝热-管壳外冷复合型甲醇合成反应器与一般管壳型甲醇合成反应的区别为:
①在上管板上部有一绝热层,绝热层中催化剂体积为整个催化剂体积的1/5-1/4。
②列管直径¢44×2mm,使床层内径与颗粒直径之比等于8,且管子根数与¢38×2mm相比,减少20%,对制造有利。
③气体入口处设有气体分布器,以使触媒层中气体均匀布。
任务六甲醇生产工艺流程组织
一、甲醇生产工艺
碳的氧化物与氢合成甲醇工艺过程
(一)高压法
高压法是最初生产甲醇的方法,采用锌铬催化剂,反应温度为360-400℃。
由于脱硫技术的进展,高压法也有采用活性强的铜催化剂,以改善合成条件,达到提高有效率和增产甲醇的效果。
高压法已经有50多年的历史。
(二)中压法
随着甲醇工业规模的大型化,已有日产2000吨的装置,甚至更大的规模,如采用低压法,势必将工艺管路和设备制造得十分庞大,且不紧凑,因此出现了中压法。
中压法仍采用高活性的铜系催化剂,反应温度与低压法相同,具有与低压法相似的优点,且由于提高了合成压力,相应提高了甲醇的合成效率。
出反应器气体中的甲醇含量由低压法的3%提至5%。
目前,工业上一般中压法的压力为9.8MPa(100at)左右。
(三)低压法
低压法是60年代后期发展起来的,主要由于铜基催化剂得到了工业应用。
铜系催化剂的活性高于锌系,其反应温度240-300℃,因此在较低压力下即获得相当的甲醇产率。
开始工业化时选用压力为4.9MPa(50at)。
铜系催化剂不仅活性好,且选择性好,因此减少了副反应,改善了粗甲醇质量,降低了原料的消耗。
显然,由于压力低,工艺设备的制造比高压法容易得多,投资少,能耗约降低四分之一,成本亦降低,显示了低压法的优越性。
甲醇生产方法主要操作条件比较
项目
高压法
中压法
低压法
联醇法
催化剂
锌铬催化剂
铜基催化剂
铜基催化剂
铜基催化剂
压力
20~30MPa
10~20MPa
4~10MPa
12MPa
温度
340~380℃
270℃左右
210~260℃
240~280℃
特点
投资及生产成本高
设备紧凑
设备庞大
与中小型合成氨联合
与高压法工艺相比,中、低压法工艺在投资和综合技术经济指标方面都具有显著优势。
以天然气为原料的甲醇厂,高压法能耗达64.8GJ/t甲醇,而大型低压法装置为29.5~31.5GJ/t甲醇。
1970年代后国外新建的大中型甲醇装置全部采用低压法,超大型装置(大于50万吨/年)采用中压法,高压法渐趋淘汰。
从目前国内外甲醇工业发展情况来看,预计以副产蒸汽、等温合成为特征的中低压合成工艺将是今后相当长一段时期内甲醇合成的主流工艺
作业:
1.甲醇的主要生产方法及原理?