数控加工被动伞齿轮及专用夹具的设计.docx
《数控加工被动伞齿轮及专用夹具的设计.docx》由会员分享,可在线阅读,更多相关《数控加工被动伞齿轮及专用夹具的设计.docx(47页珍藏版)》请在冰豆网上搜索。
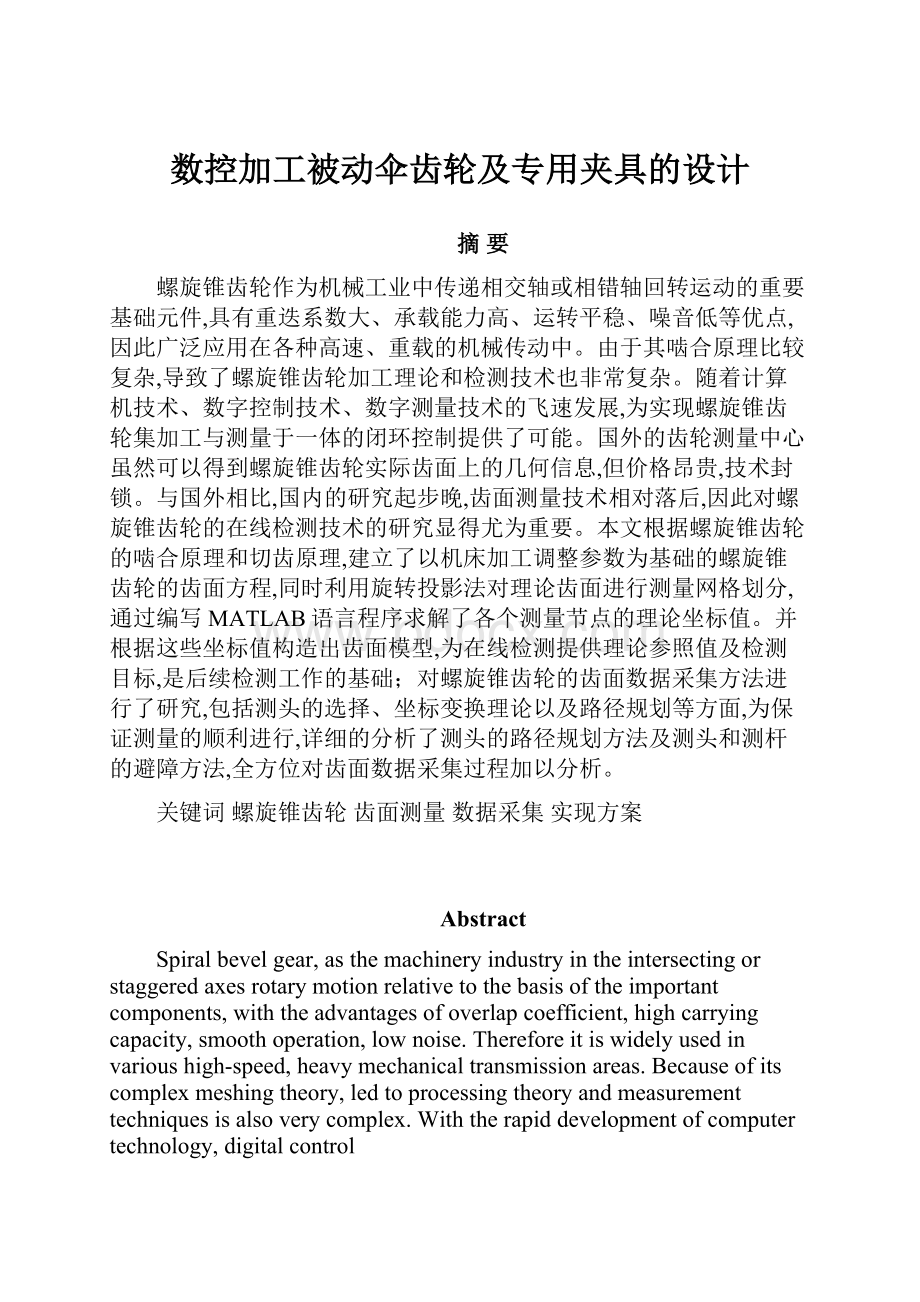
数控加工被动伞齿轮及专用夹具的设计
摘要
螺旋锥齿轮作为机械工业中传递相交轴或相错轴回转运动的重要基础元件,具有重迭系数大、承载能力高、运转平稳、噪音低等优点,因此广泛应用在各种高速、重载的机械传动中。
由于其啮合原理比较复杂,导致了螺旋锥齿轮加工理论和检测技术也非常复杂。
随着计算机技术、数字控制技术、数字测量技术的飞速发展,为实现螺旋锥齿轮集加工与测量于一体的闭环控制提供了可能。
国外的齿轮测量中心虽然可以得到螺旋锥齿轮实际齿面上的几何信息,但价格昂贵,技术封锁。
与国外相比,国内的研究起步晚,齿面测量技术相对落后,因此对螺旋锥齿轮的在线检测技术的研究显得尤为重要。
本文根据螺旋锥齿轮的啮合原理和切齿原理,建立了以机床加工调整参数为基础的螺旋锥齿轮的齿面方程,同时利用旋转投影法对理论齿面进行测量网格划分,通过编写MATLAB语言程序求解了各个测量节点的理论坐标值。
并根据这些坐标值构造出齿面模型,为在线检测提供理论参照值及检测目标,是后续检测工作的基础;对螺旋锥齿轮的齿面数据采集方法进行了研究,包括测头的选择、坐标变换理论以及路径规划等方面,为保证测量的顺利进行,详细的分析了测头的路径规划方法及测头和测杆的避障方法,全方位对齿面数据采集过程加以分析。
关键词螺旋锥齿轮齿面测量数据采集实现方案
Abstract
Spiralbevelgear,asthemachineryindustryintheintersectingorstaggeredaxesrotarymotionrelativetothebasisoftheimportantcomponents,withtheadvantagesofoverlapcoefficient,highcarryingcapacity,smoothoperation,lownoise.Thereforeitiswidelyusedinvarioushigh-speed,heavymechanicaltransmissionareas.Becauseofitscomplexmeshingtheory,ledtoprocessingtheoryandmeasurementtechniquesisalsoverycomplex.Withtherapiddevelopmentofcomputertechnology,digitalcontrol
Keywords:
SpiralBevelGearsToothSurfaceMeasuringDataCollectionImplementationProgram
3.1机床的选择23
1绪论
1.1数控工业的发展
我国数控机床发展中存在的问题
我国数控机床的发展已经经历了40个年头,但是由于种种原因,造成我国数控机床水平低、质量差,缺乏市场竞争力,这就对我国数控机床的发展产生了严重的冲击,造成这一局面的主要问题如下:
一、我国数控技术的发展战略与策略趋于保守而缺乏灵活;
二、产业结构不合理:
1、我国数控机床生产厂规模大、职工多、效益差;2、专业化生产体系没有形成、配套体系不完整;3、支持数控产业的支撑体系还没有形成;4、生产集中度差。
三、我国数控机床生产企业也存在着一些问题:
1、企业数控产品的开发、研制、创新能力差;2、技术装备和加工工艺落后、先进装备利用率低:
3、企业经营、销售机制急待健全;4、生产批量太小,成套能力差;5、组织结构落后;6、企业对激烈的市场竞争还很不适应。
我国数控机床产业化发展的战略思考
我国数控产业经历了“八五”、“九五”公关,有了较大的发展,面对全方位开放性的市场经济运行新环境,重新思考并构架新路子可以从以下方面分析和考虑:
掌握市场运作规律,在“技、工、贸”中成功的贸易上狠下功夫;
在全方位开放性市场经济运行环境中走出技术进步和产业化的不良循环;
企业必须精通管理和营销,这是数控技术产业化的要点;
产研学分工合作,找到各自的准确定位;
数控产业化公关要重点突破、面向国际、改革公关组织方式;
引入风险投资,促进数控产业化发展。
创新是推动经济长期增长的重要因素,也是企业持续繁荣和增长的关键。
因为创新既可以为企业进行现有的业务活动提供更有效的方法(降低成本),也可以增加产品或服务的购买价值(产品差异),从而加强企业的竞争力。
对我国的中小企业而言,传统产业中的中小企业普遍存在技术水平落后、设备陈旧、产品缺乏竞争力等问题,因此,企业只有不断进行技术改进和创新,才能实现产业转型和升级;对于高新技术产业领域的中小企业来说,其产品的生命周期非常短,只有不断地进行产品设计、制造工艺以及技术上的改进,保持旺盛的创新活动,才能在日益激烈的国内和国际市场竞争中立于不败之地。
中小企业技术创新活动的动力在于企业的研究发展(R&D)能力。
中小企业受自身规模、资金、人力资源等条件的限制,其R&D能力也呈现出特殊性;研究表明,组建战略技术联盟不失为增强中小企业RaD能力的有效途径。
“发展高科技,实现产业化”是一个时期以来我国科技工作的重点。
在政府各项激励和扶持政策的推动下,我国高技术产业发展迅速。
高技术产业的发展除了凭借良好的政策环境和经济环境,产业实力的提升还依赖于掌握具有竞争力的技术和人才,拥有先进的技术是企业参与市场竞争的重要筹码。
资料表明,虽然我国高技术产业相对其他产业具有较高的RAD强度,但技术密集程度的特点并不十分突出,RAD强度更远远低于发达国家。
高技术产业化,实施主体是企业,目标是产业化,前题和支撑是高技术。
我国高技术产业化所依托的技术主要由谁提供?
对提高竞争力有何影响?
是一个从政策制定者到企业经营者都关注的问题。
相对其他产业而言,中国的制造业是发展较快、国际竞争力较强的产业门类,也是加入世贸组织后受益可能性较大的部门。
中国制造业得以快速发展、产业竞争力明显提升的基本经验有二:
一是较早和较大程度的对外开放。
中国多年来一直是吸引外资最多的发展中国家,外商直接投资中超过?
0%的份额投入到了制造业领域。
对外商开放投资,开放市场,中国的制造业不仅并未因此而萎缩,而且通过与外商在合作中学习,在竞争中提高,产业的规模、水平和竞争力不断扩张、提升和增强,许多产品产销量位居世界前茅,工业制成品占出口总额的比例达到90%。
二是较深层次、较大范围的市场化改革。
改革传统的计划经济体制,放松或放开市场准入管制,鼓励和促进市场公平、有效的竞争,焕发了企业微观主体的活力,尤其是民营经济的进入与发展,在许多行业形成了多种所有制在竞争中相互促进、共同发展的格局。
纯粹的国有企业占制造业产出的比例已从1980年的76%,下降到了目前的不足30%。
体制改革带来的“内生增长效应”在制造业领域得到很大程度地体现。
1.1.1加工中心的发展
立式加工中心:
立式加工中心的主要用户层面为,以看好汽车零部件的行业为首,还有模具,飞机,医疗设备,IT,光学设备等行业。
在飞机制造业因绝大多数加工件为多品种,小批量的产品,因此五轴加工机为主的立式加工中心有潜在的需求。
今后电子零部件,精密机技零部件,半导体模具等行业也具有需求潜力。
各生产厂家面对预期需求扩大的飞机,模具,半导体等行业,正在抓紧开发五轴加工机。
和几年前的以生产一般零部件为主的立式加工中心形成鲜明对比的是,突出以加工模具为主的设备方案不断从厂家出现,由此可以看出对高速,高效,高品位的需求正在增加。
针对高精度加工,一些厂家比较注重研制对不易切削材质搞重切削加工机型。
同时,以减少工件更换时间和集中工序为目地的复合化加工技术也在不断创新。
为进一步提高效率,有些厂家正在尝试在立式加工中心的控制方面再加上1~2个轴,形成五轴控制,这样对于形状复杂的工件和自由曲面等工件都可完成一次装卡加工。
在产品开发方面,由于客户的要求更加严格,不得不在保持低价位的同时不断地追求高性能的技术。
由于正在加快适应环保要求的新技术开发。
因此,更加需要可以调整品种,数量的可形成柔性结构的设备。
现在T式切削也在研制之中,如已经出现的使用高纯度的氮气的T式加工系统。
以氧化来控制精度变化。
同时为改善作业环境,提高经济效率,对于切削的处理也采用了易于回收的方式。
卧式加工中心:
卧式加工中心因其加工面是垂直的,切屑易脱落,比较适应长时间无人操作。
又因是模块结构。
可以短时间可以导入最适当规模的系统。
因其无人操作时间较长,在成本费用方面与单机相比效果更好。
从用户需求来看,对卧式加工中心的要求更加趋向于适应多品种小批量的生产,要求加工设备能够灵活的适应工序集中导致的生产型加工件的变化。
现在由于汽车厂家的设备投资呈上升趋势,需求有望进一步扩大。
此外,因对于产品制造的认识和对生产体系的看法正在发生根本的变化。
由此而派生的新的生产体系可能对能形成柔性线的小型机种产生需求。
着手生产以上机床的厂家在追求高速高精度的同时,还在如何使机床小型化及成本控制方面下功夫。
也就是说此类产品的开发的重点在于机体的小型化,适应形成柔性线体系方面。
从技术开发动向来看,是谋求提高主轴转速,进给速度,提高精密度,并将对应热变化,模块化体现出来。
其中,作为机床基本课题的高速化研究也不断取得成果。
由于提高进给速度直接关系到产品的加工时间,以提高生产效率,因此在高速进给方面,驱动装置采用直线电机的机型正在增多。
同时也在厂家在开发不使用直线电机,采用进给轴以大导程滚珠丝杆为驱动,进给加速度1.5G~2G,快速进给速度120mm/min的高速卧式加工中心。
并在主轴上采用双面约束刀具,主轴转速为2万r/min,快速进给速度为60m/min,以尽量缩短重复定位,刀至刀等的非切削时间。
为解决速度提高带来的热变位影响,防止精度下降,一般都采用独自的补正装置或主轴冷却结构,冷却装置等。
数控立式车床:
适用于加工大直径,大吨位外圆形工件的立式机床,也被各行业采用。
由于其市场的局限性,产品在很多方面上反映了用户的意向。
很多是以专用机的形式交货投付使用的。
这也是用户与厂家形成密切联系的主要原因。
最近,对于中国出口看好的建设机械厂家对立式车床的需求令人瞩目,造船行业的订货则似乎要暂时告一段落。
数控车床生产厂家期待着飞机,高性能发电机,风力发电机等方面设备投资比较活跃的重电机行业的订货。
由于市场在交货期,质量,价格方面的要求越来越高,一些中小规模设备的用户为缩短产品的生产周期,更青睐一次性装卡,可搞多种加工的复合型加工机。
考虑到环保的要求而采用的T式加工的需求也在增加,根据这类用户的需求,OM制作所以产协作的方式开发出使用半气化热半T式加工技术,并加强了节约能源的措施,控制了电力的使用。
现在,低价位的小型数控立式机床的需求仍在扩大,同时,和卧式数控车床一样,带有加工中心意识功能型复合机的开发研制比较活跃。
因配置了C轴,不同的复合加工也可通过一次装卡进行。
此外,在以切削为主的同时,加上采用单刀具的双面约束ATC方式后,在铣加工功能方面也见到不少可进行可重切加工的工序集约型产品。
1.2螺旋锥齿轮的历史
螺旋锥齿轮是机械传动的基础元件,用于传递两相交或交错轴间的运动,具有重叠系数大、音小,承载能力高的优点,广泛运用于汽车、机、床及矿山机械等领域,是目前汽车、机等高精高速重载设备的主传动元件。
螺旋锥齿轮技术是经历了一个漫长的历史过程而发展起来的成熟的机械传动技术,同时又是面临工程实践挑战而充满发展机遇的技术。
1.2.1螺旋锥齿轮技术的历史
人类很早就将齿轮用于机械传动,但第一个将共轭齿面用于齿轮传动的是丹麦天文学家Olaf.Roemer(1674),他用相互包络的摆线作为齿轮齿廓得到了第一对共轭齿面齿轮。
瑞士数学家Euler.L(1765)首次阐明了齿轮传动的共轭原理,并论述了渐开线作为平面齿轮齿廓在制造、装和传动等方面的优越性能,这使渐开线齿轮在平行轴传动中牢固占据支配地位。
首先研究空间啮合理论的是法国的几何学家T.Olivier和俄国学者Χ.И.Гохман[4],T.Olivier提出了求解共轭齿面的包络曲面法,他论证了利用辅助曲面得到线接触或点接触的共轭曲面的可能性,并提出了螺旋锥齿轮的概念(1820)。
但他把共轭齿面的求解完全归结为画法几何学问题,这引起了争议,其理论被认为不够严谨且不具一般性。
Χ.И.Гохман建立了齿轮啮合解析原理的理论基础,此后螺旋锥齿轮技术沿着解析法的方向发展。
直到最近由于计算机技术在螺旋锥齿轮齿面设计方面的应用,人们才开始重新注意到T.Olivier的几何法的工程应用价值。
对螺旋锥齿轮技术的理论研究表明,螺旋锥齿轮齿面是与一种螺旋运动关系相对应的复杂曲面,它必须通过能是与一种螺旋运动关系相对应的复杂曲面,它必须通过能在刀具和工件之间产生这种螺旋运动的机床才能实现。
因此螺旋锥齿轮技术的发展必然依赖螺旋锥齿轮加工机床的发展,其设计理论的发展又必然推动新的切齿机床和加工方法的出现尽管螺旋锥齿轮的概念早在1820年时就随着空间啮合理论的研究而提出,但是由于缺乏必要的加工手段,直到一个世纪之后,随着加工机床的出现,螺旋锥齿轮才从概念变为现实。
910年,德国人PaulBttcher[1]发表了一系列关于螺
旋锥齿轮加工技术的专利报告,这些报告包含的内容非常基础和广泛。
在报告中,他首次提出了采用铣刀盘加工螺旋锥齿轮的技术。
他提出的加工方法包括单齿分度加工方法(见图1a,singleindexingmanufacturingmethods)和连turingmethods)。
PaulBttcher制造了一台原型机,以验证他的方法。
采用此原型机,他加工出了第一种采用端面铣削方法加工的螺旋锥齿轮副。
这时,齿面修形的概念还没有出现,因为大小轮采用相同的产形轮加工,这两种方法加工出的齿轮副都是完全共轭的等高齿。
1913年,美国的格利森公司的工程师James.Gleason设计出了第一台螺旋锥齿轮端面切削机床。
1919年,格利森公司获得了PaulBttcher的发明专利,并致力于单齿分度加工方法的研究。
为了改善切削过程中的运动关系,使轮齿在从大端到小端的截面比例保持一致,避免小端齿顶变尖,ErnestWildhaber为格利森公司引入了渐缩齿的概念(图2a、b)。
格利森No.16型机床是这个时期的代表性机床。
从这时起,格利森公司生产的螺旋锥齿轮加工机床及加工方法为美国汽车工业的大批量生产方式提供了有力的支持。
20世20年代,格利森公司首先推出了轴线偏置的准双曲面齿轮并进行了理论研究。
轴线偏置导致小轮螺旋角的增加,锥齿轮的端面模数因此增大。
在齿轮副的整体装配空间不变的情况下,小轮的直径增大,从而提高了小轮强度。
小轮模数的增大使小轮的最少齿数从9个齿降低到5-6个齿。
同时,齿轮副的重合度也明显的增加了。
总之,轴线偏置齿轮副降低了啮合冲击,改善了轮齿在节线附近的润滑状态,增加了齿面抗压强度和齿根强度。
轴线偏置对齿轮副传动性能的最大不利影响是齿面啮合时,接触齿面沿齿长方向的相对滑动速度增大。
相对滑动速度的增加很容易破坏齿面油膜,引起齿面疲劳破坏。
为了解决这个问题,1924年格利森公司同壳牌石油公司(ShellOilCompany)合作,开发出了一种新型的耐压润滑油,从而防止了齿面擦伤和局部微小焊接作用的形成。
但相对滑动速度的增大也使齿面的研磨变得更加容易,改善了齿面研磨的加工工艺性。
1925年,格利森公司推出了可以加工准双曲面齿轮的加工机床No.16H。
1926年,壳牌石油公司向市场推出了准双曲面齿轮润滑油。
同年,美国福特汽车公司开始在其生产的所有车辆上使用准双曲面齿轮,这是世界上第一家采用准双曲面齿轮的汽车公司。
螺旋锥齿轮技术的另一项巨大进步是刀倾法的引入。
这种方法也是格利森公司提出并首先实现的,第一台带刀倾机构的螺旋锥齿轮加工机床出现在1930年之前。
采用带刀倾机构的切齿机床,可对齿面进行沿齿长和齿廓方向的修正。
自此,点接触齿面开始出现,从而极大地提高了锥齿轮副的齿面接触性能。
1954年,格利森公司推出的No.116机床(见图3)
达到了纯机械齿轮加工机床的顶峰(最大化的机械智能,最小化的电气控制)。
这种机床带有刀倾机构,能选择应用变性机构或螺旋展成运动。
它是第一台能够把高级啮合理论在螺旋锥齿轮副上变成现实的机床。
这种机床所有的运动优化都是通过改变驱动齿轮、偏心机构及凸轮实现的。
直至现在,这种机床还在得到广泛的使用。
我国在上世纪七十年代从美国引进的螺旋锥齿轮切齿机主要就是这种机床。
这种机床的设计概念模型(见图4)已经成为螺旋锥齿轮技术的经典。
在螺旋锥齿轮技术和螺旋锥齿轮切削机床的发展过程中,除美国的格利森公司(GleasonWorks)外,瑞士的奥利gelnbergSons)也产生了巨大的影响。
这两家公司主要致力于延伸外摆线齿形制螺旋锥齿轮的加工,它们设计的机床采用连续分度的方法滚切加工齿轮。
这三家公司之间既相互竞争,又相互借鉴与合作,共同推动了锥齿轮技术的不断进步与发展。
它们的技术发展历程基本相似,但由于加工方法和齿面几何结构之间的差异,三家公司分别制定了各自不同的标准。
随着控制技术的发展,电气控制在螺旋锥齿轮加工机床中拥有了一席之地。
1973年,奥利康公司首次将PLC控制技术应用于S17型机床中,这标志着螺旋锥齿轮加工技术进入了PLC控制阶段。
1986年,格利森公司推出的GMAXX2010型机床使螺旋锥齿轮的加工技术又向前迈进了一大步。
这是第一台可以自由选择单齿分度加工法和连续分度加工法的螺旋锥齿轮切削机床。
它的摇台、件、刀盘之间的协调运动完全采用数控系统进行控制,机床参数调整完全数控化。
1989年,格利森公司推出的Phoenix系列全CNCFree-form型机床彻底突破了传统切齿机床的设计思想,抛弃了传统的摇台、倾、性等复杂的机构建立了六坐标的机械结构(见图5),齿面的成形由六轴之间的协调运动来完成。
它在大大简化传统摇台类机床复杂机械结构的同时,提高了机床的动静态刚度和加工精度,而且使机床可更加灵活的进行控制。
这是一种万能型齿轮加工机床,它不仅能加工格利森齿制的齿轮,也能加工奥利康或克林根贝格齿制的齿轮。
1989年,德国的克林根贝格公司(KlingelnbergSons)也推出了自己的万能型齿轮加工机床KNC40,它的设计思想和图5类似。
1.z轴 2.x轴 3.y轴 4.工件立柱
5.机座 6.刀具主轴(C轴)
7.回转台(B轴) 8.工件主轴(A轴)
图5
在理论推动齿轮加工机床技术不断发展的同时,空间啮合理论自身也在不断深化。
格利森公司的著名科学家[6]论文完整论述螺旋锥齿轮技术的微分几何和运动学原理,提出了对间接展成局部啮合齿面具有重要意义的概念-极ter提出了一个准双曲面几何模型,进一步完善了螺旋锥齿轮节面分析的数学模型,并分析了局部共轭齿轮副的齿面接触过程,给出了一种确定失配齿面接触和运动传递情况的定量分析方法,即齿面接触分析方法(TCA),提出了螺旋锥齿轮的“二阶曲面范成”原理。
上世纪50年代日本学者酒井高男用二元矢量、量等数学工具,严密而简洁地论证了有关弧齿锥齿轮的理论问题,还引入了媒介齿轮的概念,导出了滑移线曲率的计算公式,讨论了两类啮合界限问题。
国际著名学者F.L.Litvin教授自上世纪60年代至今一直致力于以格利森锥齿轮设备和加工方法为基础的新的螺旋锥齿轮共轭齿面形成方法的研究。
提出了改善齿面接触特性的齿面综合分析方法及齿面综合优化的数学模型,对各种安装加工误差对运动精度的影响进行了解析描述。
应该提及的是这一时期,日俄等国有工程师也提出了自己的螺旋锥齿轮加工机床的设计模型或设想(见图6),由于设计方案在机床运动的稳定性和刚度以及切齿技术方法等方面存在明显缺陷,因而没有在实践中采用,或在实际应用中因难以控制的误差而被淘汰。
这从一个侧面反映了螺旋锥齿轮技术的难度和复杂程度。
图6一种不能实际应用的机床设计方案
我国的锥齿轮和准双曲面齿轮技术兴起于二十世纪七十年代,以“格利森齿制”为主要目标,原机械工业部曾把“格利森成套技术的研究”列为重点研究课题,组织国内有关力量进行攻关,1971年南开大学的数学家严志达教授首先提出了相对微分法[2]这一有力的数学工具,形成一套有自己特色的理论体系。
吴序堂[8]、昌启[3]、韬[5]等对齿轮啮合理论进行了深入研究,他们不仅运用各自的方法正确推导了Gleason公司机床参数调整卡上的公式,分析了其理论实质,而且还指出并改进了其中的错误和不足。
西安交通大学机制教研室齿轮研究组[7]发展和改进了前苏联的一种精度很低的切齿计算方法,并将其用于分析Gleason公司No.116机床参数调整卡,得到了与原机床参数调整卡具有同等精度的计算结果。
到二十世纪八十年代,我国学者已基本弄清Gleason螺旋锥齿轮技术的理论实质和加工原理,并设计制造出国产机械式螺旋锥齿轮加工机床。
1999年由中南大学曾韬教授领导的科研团队研制出我国第一台七轴五联动全数控磨齿机YK2045。
并在2003年实现商品化(见图7)。
目前,国内研究螺旋锥齿轮技术的团队有重庆大学的齿轮传动国家重点实验室、西安交通大学、南大学和华中科技大学等。
1.2.2螺旋锥齿轮技术的现状
今天,在螺旋锥齿轮技术方面引领创新方向并占据主流高端市场的是美国的格利森公司。
进入本世纪,格利森公司推出了最新的CNCFree-form型机床———凤凰II型数控齿轮加工机床(见图8)以及与之配套的软件—格利森螺旋锥齿轮制造专家系统(GEMS系统)[13],这种最新系列的凤凰II型机床,利用全新的整体式床身设计,从而减少了占地面积,提高了机床刚性,主轴由数字直接驱动电机驱动,省掉了机械传动元件,提高了驱动速率,从而大大地降低了生产周期和提高了机床精度。
机床的其他运动轴由数字伺服电机直接驱动,以实现给定的齿面产形运动,凤凰机床采用自容式电器和液压装置设计,从而使安装和调整便捷。
GEMS系统是基于计算机网络的一体化制造系统(见图9),它将格里森公司现有软件模块(如GAGETM4WIN,G—AGETM4WIN,SummaryManager,FEA及UMCTM)集成,实现工程工作站和格利森数控机床之间的信息互换和享用。
GEMS提供了一个高效、缝和协同的圆锥齿轮生产制造系统。
GEMS系统由以下模块组成:
(1)应用软件,GAGETM4WIN程序,它是由多项功能模块组成的,为用户提供设计和分析圆锥齿轮的全套工具。
用户通过输入圆锥齿轮的基本参数,就可以利用该软件得到设计齿轮尺寸参数、TCA计算结果、TCA计算结果、根切计算检查、齿面失配图形、床调整数据、量数据以及刀具数据。
(2)格利森自动齿轮修正软件,该软件基于齿面误差测量数据和误差修正矩阵,对切齿或磨齿齿面进行修正,使齿面误差控制在误差范围内。
该软件可用于联机和脱机操作两种模式,用于脱机操作时,可在工程工作站上进行,用于联机操作时,可直接在测量机上运行。
(3)高阶运动曲线设计模式UMCTM模块,提供齿面优化功能,利用凤凰机的万能运动特性进行高阶运