钢铁的缸体.docx
《钢铁的缸体.docx》由会员分享,可在线阅读,更多相关《钢铁的缸体.docx(27页珍藏版)》请在冰豆网上搜索。
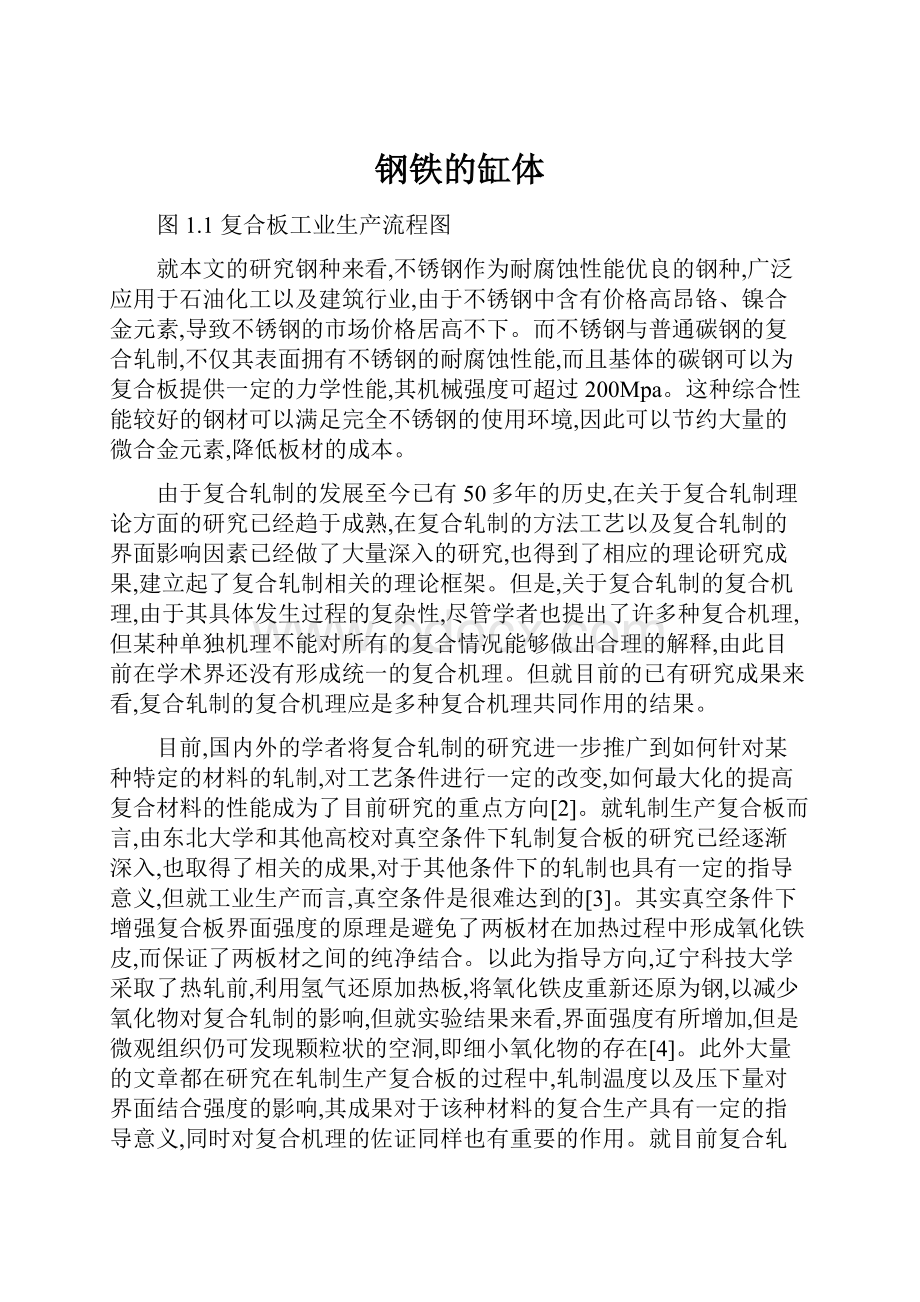
钢铁的缸体
图1.1复合板工业生产流程图
就本文的研究钢种来看,不锈钢作为耐腐蚀性能优良的钢种,广泛应用于石油化工以及建筑行业,由于不锈钢中含有价格高昂铬、镍合金元素,导致不锈钢的市场价格居高不下。
而不锈钢与普通碳钢的复合轧制,不仅其表面拥有不锈钢的耐腐蚀性能,而且基体的碳钢可以为复合板提供一定的力学性能,其机械强度可超过200Mpa。
这种综合性能较好的钢材可以满足完全不锈钢的使用环境,因此可以节约大量的微合金元素,降低板材的成本。
由于复合轧制的发展至今已有50多年的历史,在关于复合轧制理论方面的研究已经趋于成熟,在复合轧制的方法工艺以及复合轧制的界面影响因素已经做了大量深入的研究,也得到了相应的理论研究成果,建立起了复合轧制相关的理论框架。
但是,关于复合轧制的复合机理,由于其具体发生过程的复杂性,尽管学者也提出了许多种复合机理,但某种单独机理不能对所有的复合情况能够做出合理的解释,由此目前在学术界还没有形成统一的复合机理。
但就目前的已有研究成果来看,复合轧制的复合机理应是多种复合机理共同作用的结果。
目前,国内外的学者将复合轧制的研究进一步推广到如何针对某种特定的材料的轧制,对工艺条件进行一定的改变,如何最大化的提高复合材料的性能成为了目前研究的重点方向[2]。
就轧制生产复合板而言,由东北大学和其他高校对真空条件下轧制复合板的研究已经逐渐深入,也取得了相关的成果,对于其他条件下的轧制也具有一定的指导意义,但就工业生产而言,真空条件是很难达到的[3]。
其实真空条件下增强复合板界面强度的原理是避免了两板材在加热过程中形成氧化铁皮,而保证了两板材之间的纯净结合。
以此为指导方向,辽宁科技大学采取了热轧前,利用氢气还原加热板,将氧化铁皮重新还原为钢,以减少氧化物对复合轧制的影响,但就实验结果来看,界面强度有所增加,但是微观组织仍可发现颗粒状的空洞,即细小氧化物的存在[4]。
此外大量的文章都在研究在轧制生产复合板的过程中,轧制温度以及压下量对界面结合强度的影响,其成果对于该种材料的复合生产具有一定的指导意义,同时对复合机理的佐证同样也有重要的作用。
就目前复合轧制的复合材料来看,主要集中于碳钢与不锈钢的复合轧制,铝合金与不锈钢的复合轧制,铜与钼电子封装材料的复合轧制。
尽管对于中间材的加入会会对复合板的界面结合处产生重要影响的实验结论已经被掌握,但是这种现象并没有被深入的研究,其提高界面结合强度以及避免界面结合处的氧化等深层机理也没有在相关的学术论文中提及,因此对于中间材对复合轧制的影响具有理论以及实践意义。
1.2影响轧制界面强度的因素
1.2.1表面质量
在金属复合板的工业生产中,对金属表面进行处理的方法主要有机械法、化学法以及其他方法,每种材料均能够找到是何其本身材料性质的表面处理方法[5]。
表面质量具体包括表面的杂质和相对表面的大小,表面杂质以及油污会对复合界面产生恶化,干扰两复合金属之间形成新的金属键从而影响复合界面结合;而相对表面是指在复合金属板之间采用机械打磨或者化学腐蚀的方法,使得金属表面之间产生机械划痕或者腐蚀沟壑,以增加复合金属接触的相对表面积,从而提高金属界面之间的结合。
同时,复合轧制界面结合机理中的薄膜理论认为,异种材料复合效果与本身的材料特性无关,而是与其界面结合后处的表面状态相关,该理论认为金属表面不可避免的存在金属氧化膜,在轧制作用下氧化膜的破碎新鲜金属的暴露并形成金属键,该理论并强调硬而脆的氧化膜易于界面结合,而软而韧的氧化膜不利于界面结合[6]。
对于热轧而言,由于在金属加热过程中,不可避免产生氧化铁皮,不利于金属的复合,因此,在很长的一段时间内,对热轧生产复合金属板的研究都在真空的环境下进行。
1.2.2压下量
压下量对界面的结合强度的影响表现在两个方面,首先只有复合金属之间达到一定得压下量,才能保证复合板有一定的界面结合强度;其次,当压下量达到一定得值之后,增加压下量对界面的结合强度增强的作用减弱[7]。
这种影响依据金属键理论可解释为,由于形成一定强度的界面,必须有一定数量的新化学键形成,化学键的形成必须满足分子之间作用力到达一定的距离,这在宏观上表现为必须要达到一定的压下量;然而,随着压下量的进一步增大,压下量不再是影响界面结合的关键因素,因此,随着压下量的进一步增加,界面结合强度增加的趋势变缓。
值得指出的是,在压下量对复合轧制的影响中,首道次压下量对界面结合的影响效果最为显著。
由于其界面氧化物形成于初道次轧前加热过程中,且其夹杂物位于其两复合金属界面结合表面处,初道次大的压下量对界面氧化物的破碎作用是相对明显的[8],而在后续的轧制过程中的夹杂物的形态转变只有通过界面附近金属的延展的破碎以及其再结晶过程的迁移[9]。
因此,首道次对界面夹杂物的形态以及分布产生重要影响,首道次压下量越大意味轧制压力越大,对界面夹杂的破碎作用越强烈,夹杂物尺寸越小,对后续轧制中夹杂物的迁移和再次破碎均产生有利的影响,由此认为首道次较大的压下率是提高界面结合的决定性因素[10]。
1.2.3轧制温度
轧制温度对界面结合强度的影响,可分为两种情况进行讨论,对于非真空复合轧制而言,一方面随着温度的升高可以提高金属的塑性能力以降低轧制压力,更多的金属被挤压至界面结合处以激活更多的原子,同时复合机理中的再结晶理论认为随着压下量的增加,材料的位错密度和畸变能增加,再结晶通过形成新的晶粒来减小畸变能,再结晶的理论已经证实,随着温度的升高再结晶的强度逐渐增加。
对于复合板界面来讲,其本质就是在基材和复材在结合界面处形成的新的原子之间的结合,这种结合可以看作是由再结晶引起。
因此温度的升高会提高其界面结合强度,但在非真空轧制条件下,温度的升高会导致其界面容易生成脆性氧化物,且脆性氧化物的厚度与温度成正比,对后续轧制过程对厚度较厚的氧化物的破碎以及迁移较为困难,因此会影响界面结合强度,两者共同作用会导致双层金属界面结合强度会在某一温度达到最大值[11]。
另一方面,对于真空对于热轧而言,由于四周密闭的空间及条件下,温度的升高不会引起其界面氧化物的数量以及成分的改变随着轧制温度的升高,复合板的界面强度随之升高。
这种影响可通过再结晶理论进行解释,因此,随着轧制温度的升高,复合板界面强度随之增加。
1.1引言
2014年11月18日,中国钢铁工业协会在北京召开14年度钢铁行业技术创新大会,在大会中发布了由中国钢铁工业协会与十几位相关专家编著的《钢铁行业2015-2025年技术发展预测》,为我国钢铁产业在未来的发展指明了方向。
在具体的10个发展方向中,其中第8位重点强调了复合材料制造技术,其关键性技术具体包括材料设计以及高效组坯技术、阻隔复合界面元素扩散材料设计及复合界面性能控制技术、复合界面组织固态相变及其控制技术、特殊用途复合材料轧制复合以及后续热处理技术以及异种材料复合轧制过程的协调变形及其控制技术[1]。
这不仅强调了轧制复合板作为我国钢铁技术重要发展趋势,同时也为复合轧制的具体的关键性技术指明了方向。
轧制金属复合板是随着科学技术的发展而产生,特殊功能的机械元件对其制作材料提出了很高的要求,传统单一的金属和合金的使用性能并不能满足工件的要求,将两种或两种以上的金属通过某种工艺生产的具有两种材料综合力学性能复合材料,其材料使用性能的适用性要大于单一材料,复合板材的生产有着广阔的市场空间,因此国内外各大钢铁企业也在尝试生产复合板,其生产工艺流程如下图所示。
1.2.4中间材
在复合轧制复合界面处添加一种异于复材与基材的材料称之为中间材,按照中间材料在轧制温度下的状态分为液态中间材料和固态中间材料,下面具体分析其对复合轧制的影响。
由于在基材复材和中间材装配结合时,基材与中间材以及中间材与复材之间不可避免的存有缝隙,当中间材的熔点低于轧制加热温度时,中间层材料就会以液体状态通过润湿以及毛细作用填满基材与复材之间的缝隙,由于中间材与基材复材化学成分之间的差异,所以中间材除了凝固发生相互物理结合之外,还会存在原子之间形成较为牢固的冶金结合[12]。
对于固态中间材而言,在材料装配阶段便于基材和复材的压实,在板材加热以及热加工的工程中,可以抑制氧化膜的生成以及降低在热加工过程中脆化层的厚度,从而提高复合板的安全性和可靠性。
虽然某些元素作为中间材会对复合板的综合性能产生重要影响,但选用不当的中间材会在复合界面析出碳化物而导致复合效果恶化,因此对中间材的科学合理选择是提高复合面界面结合率以及提高界面结合强度的关键,已有的研究表明中间材在复合板中已有以下实践,具体如下表所示1.1所示[13]。
表1.1中间材在复合金属中的应用
复合材料
真空度
/Pa
轧制温度/℃
压下率
/%
夹层方式
夹层材质
/um
剪切强度
/MPa
304/SS41
真空
1200
90.0
箔:
插入
Ni、Cu、Fe
(100)
结合良好
316/SS41
0.001~1.30
1250
83.0
箔:
插入
Ni(100)
380.0
316/16MnR
-
1050
-
电镀
Ni
结合良好
304/Q235
氩气保护
650
-
热喷涂
Ag基材料(8~12)
结合良好
304/Q345
0.010
1200
80.0
箔:
插入
Ni(800)
489.5
0.010
1200
80.0
箔:
插入
Nb(800)
55.0
1Cr13/Q235A
-
610~685
32.0~62.3
板、箔:
插入
Al-Cu-Mg
(600~900)
结合良好
316L/SM409B
0.030
650~900
-
箔:
插入
Ni、Cu、Fe、MO(10)
300~500
不锈钢/碳钢
0.010
880~1000
30.0~85.0
箔:
插入
Ni(50~1000)
460~500
Ti/钢
13.300
800~1050
30.0~80.0
板、箔:
插入
Ni-Cr(100)
256~299
对于不锈钢—碳钢复合板的中间材而言,从抑制氧化、抑制扩散、抑制裂纹扩展以及焊接性方面考虑出发,其对复合板的影响可具体分为以下几个方面[14]:
注:
1为真空焊接添加中间材;2为真空焊接无中间材;3为空气焊接添加中间材;4为大气焊接无中间材
图1.2中间材Ni对不锈钢复合板界面结合率的影响
第一,以镍作为中间材可以提高基材和复材的装配压实,避免了基材与复材之间氧化性气体的过度残留;同时在相同的压下量下,添加镍箔作为中间材可明显增加复合板的结合率;其对界面结合率的影响如图1.2所示,同时,谢广明在其专利《防止真空复合轧制不锈钢复合板的界面氧化的方法》[15]中也指出中间材Ni的加入能够抑制界面的氧化;李龙等在研究中间材Ni对不锈钢复合轧制界面氧化的影响,亦得出同样的结论,但其减少氧化的机理尚不明确[16],且其抑制界面氧化的实验结论亦须进一步证实。
第二,由于基材和复材之间必然存在一定的碳和其他元素的浓度梯度,这种浓度梯度必在界面结合处发生一定的扩散,而使得材料界面结合处的组织发生变化。
以不锈钢和碳钢的复合为例,对于不锈钢而言元素的扩散通常被称为"增碳和贫铬",即碳钢中相对较高浓度梯度的C会迁移到复合界面以及不锈钢一侧中,同时不锈钢中浓度梯度较高的铬会进扩散到复合界面以及碳钢中。
碳的迁移以及铬的扩散对复合板会产生三种影响:
首先,碳钢的脱碳通常会在碳钢侧的界面结合处形成一定厚度的纯铁素体区域;其次,C通常会在界面结合处与Cr形成高硬度的碳化物,对从而对界面结合塑性产生影响;最后,无论是增碳还是贫铬都会恶化界面结合处的不锈钢的耐腐蚀性。
而中间材的加入会抑制两板材之间特定元素的扩散,从而减轻甚至消除"脱碳贫铬"对复合轧制碳钢—不锈钢的影响。
对于中间材Ni对碳钢—不锈钢复合轧制的组织的影响的相关研究表明,中间材Ni的加入由于可明显抑制C的扩散,因此在非添加中间材元素的界面结合处形成的铁素体带消失,界面结合附近即为碳钢组织与不锈钢组织;而非添加中间材组织碳钢侧出现铁素体带,不锈钢侧由于增碳以及较高的合金元素导致其界面可能出现马氏体组织[17]。
a)未添加Nib)加Ni
图1.3中间材Ni对316不锈钢—Q345碳钢界面结合处成分的影响
关于中间材Ni的加入对其Cr元素的扩散状况的影响,不同的文章有着不同的阐述:
李龙等研究学者认为[16]认为中间材能够有效抑制Cr元素的扩散,其对未添加与添加中间材Ni后的316不锈钢—Q345碳钢复合轧制的界面结合处的成分扫描结果如下图所示,通过图1.3可明显发现中间材能够有效抑制Cr的扩散;而李炎等研究学者认为[14]其添加中间材Ni的复合板其界面结合处存在50um内的Fe、Cr、Ni的扩散区域,但Ni的添加对C的扩散的抑制作用不明显;李萌盛[18]在研究国产03Cr13Al和16MnR复合板,与日本生产的03Cr13Al和16MnR进行对比发现,进口板在其界面结合处出现白色亮带,并对界面结合处成分扫描得到图1.4,该成分图同样显示Ni对Cr元素抑制扩散的效果不明显。
a)未加Nib)加Ni
图1.4中间材Ni对03Cr13Al—16MnR复合界面结合处成分的影响
第三,镍的加入对不锈钢复合板而言,可以防止并阻止腐蚀引起的龟裂。
实验研究表明,在腐蚀环境下,由于基材受损后,加入镍中间材后的复合板可以阻止裂纹腐蚀的进一步加深。
其对复合板界面腐蚀界面的裂纹扩展情况如图1.5所示。
a)未加Nib)加Ni
图1.5中间材Ni对腐蚀裂纹扩展的影响
第四,镍可以改善复合板的焊接性。
第五,中间材Ni对碳钢-不锈钢复合轧制界面结合强度的影响,具体研究包括以下两个方面:
首先,专利[15]指出,中间材Ni对不锈钢复合板界面结合强度的影响,在相同的轧制工艺下,添加中间材Ni的复合板界面结合强度要高于未添加中间材试样约30MPa,历梁在其硕士毕业论文中,提及中间材Ni的加入亦可提高不锈钢复合板界面结合强度约5.6MPa[3];其次,李龙在研究不同厚度(0.1mm以及0.2mm)中间材Ni对复合轧制不锈钢界面结合强度的影响中,得到结果如图1.6所示,从图中可发现中间材的加入将会恶化复合板的界面结合,其界面结合强度随着压下量的增加下降约20MPa[16]。
图1.6不同中间材厚度下压下量与界面结合强度的关系
1.2.5轧后热处理工艺
轧后热处理对复合板界面的结合强度有着重要的影响:
首先,去应力退火。
由于在热轧的过程中材料的变形抗力较小,此时在界面处两部分金属在大的轧制压力条件下形成一定的结合,此时的结合是在较低的变形抗力条件下形成的金属键,但随着温度的降低,两金属的变形抗力逐渐增大且差异也逐渐明显,对于界面结合处产生较大的应力,会对结合处的界面产生一定的分离作用;其次扩散退火,由于轧制过程只能形成界面结合力较小的点结合,复合强度的增加需通过扩散退火使得接触面积进一步增大,为界面结合处处固态相变的晶粒长大的结果。
通过退火,可以消除界面结合处的应力,而且通过扩散使得接触面积增大,两者共同作用,进一步提高界面结合强度。
但是其界面结合强度并不是与轧后热处理温度的升高而绝对的升高[19]。
随着温度的升高,界面原子由于温度的热激活作用而在界面结合处产生更进一步的扩散,促进结合处的共晶的晶格转变,这种晶格转变可以促进界面结合处的宽度增加,从而促进其界面结合强度,但随着加热温度的升高及保温时间的延长,轧后板材发生再结晶以及晶粒长大,粗大晶粒以及界面结合复合板的处析出的脆性相会削弱复合板的力学性能。
1.3界面结合机理
目前,对轧制金属复合板界面结合机理,学术界有以下几种观点:
(1)金属键理论。
该理论是在1954年由M.S.Burton提出的,该理论认为由于轧制过程中,巨大的轧制压力作用下,使的基材与复材界面处的原子到达原子引力的距离范围而相互吸引,从而使的界面形成一定强度的结合[20]。
(2)薄膜理论。
薄膜理论认为金属原子引力普遍存在,因此热轧界面结合与材料本身的性质无关,只要材料表面足够的纯净就可以形成一定强度的结合[21]。
在热轧生产复合板工艺下的板坯经过轧机的强塑性变形作用,使得界面结合处的氧化膜破碎,界面结合处原本被氧化膜包裹的新鲜金属暴露出来,且大塑性变形作用使新鲜金属达到原子力作用范围,相互吸引形成冶金结合。
对于轧制生产复合板而言,薄膜理论强调压下量必须到达一定的程度,不仅仅要求塑性变形保证原子裸露,而且裸露原子需达到一定的数量,才能形成一定强度的结合。
(3)机械啮合理论。
机械啮合理论认为在材料的变形程度到达一定的范围后,金属的表面就会产生许多裂口,在机械作用下,会使金属产生塞积作用以及镶嵌作用下形成最初的轧制复合[22]。
随着压下的进一步进行,机械的压下作用促进金属表面的界面结合处的面缺陷和体缺陷的密度进一步增加,使得金属表面的不平整度继续增加。
这种凹凸不平的表面引起表面摩察系数增加,在巨大的轧制压力下,表面由摩擦以及变形产生的热量使得金属表面的温度升高。
在较大的轧制压力下的摩擦以及较大的塑性变形,会对两种金属表面产生锁死作用,进一步增加了界面结合强度。
机械啮合保证更多的新鲜金属从薄膜中暴露出来,且随着位错密度的进一步升高,两者共同作用促使界面处的原子形成属于基材和复材共同金属键。
(4)扩散理论。
该理论是由前苏联学者卡扎可夫在上世纪70年代提出,该理论认为当双金属在加热到一定温度(0.6~0.8Tm)后,在其相互接触的区域存在一层非常薄的相互扩散区域,该相互扩散区域可以实现原子之间的冶金结合,从而在复合板界面结合处形成一定强度的结合[23]。
该理论虽然能够在一定程度上解释热轧复合板的结合机理,但对冷轧其界面结合无法进行解释,因此该理论具有一定的局限性。
(5)再结晶理论。
该理论由L.N.帕克斯在1953年提出的[24],该理论认为由于加工硬化的作用以及在高温作用下,界面处的原子的位错密度和畸变能急剧增加,会促使界面处原子形成新的晶格原子以释放较高的畸变能,从而形成基材和复材共同晶粒,从而形成一定强度的结合[25]。
再结晶理论的前提条件为较高的温度以及大的变形量,大的变形提供畸变能以及原子再结晶的原子距离,而较高的温度是保证再结晶发生的温度条件。
这一理论在解释冷轧复合时,有着很大的局限性。
(6)能量理论。
该理论是A.Π.西苗诺夫在1958年提出的[26]。
该理论旨在强调能量是引起金属间相互结合的条件,而非金属原子的扩散。
原子之间形成牢固的结合,必须保证金属表面处的原子处于最低的能量级状态,较低能量级状态时金属内部金属键的方向性减弱,易于在界面结合处形成一定的冶金结合;同时,由于在冷轧以及热轧工艺下的复合板均受到较大的轧制压力而产生强烈的塑性变形,使得金属原子不断接近至晶格常数数量级,且强烈的塑性变形使得界面结合处金属晶格积累了大量的畸变能,两者共同作用使得界面结合处原子被激活而客服势垒形成冶金结合。
这种强调原子间间距以及能量的作用,强调原子激活的观点称之为能量理论。
由于热轧复合板的过程非常复杂,其复合机理的理论研究自然也存在其多样性,但是就目前的研究成果来看,不可能由其中的一种理论来充分论证复合机理,每种理论都有其局限性。
但是,以上理论都在强调原子间的间距以及变形温度对复合的影响,因此本文中的轧制规程的设计要研究压下量与轧制温度对界面结合强度的影响。
1.4本文主要研究路线及内容
图1.7研究路线图
本文的研究路线如图1.7所示,本文的主要研究内容为加中间材Ni的碳钢—不锈钢复合轧制界面组织性能研究,同时结合于其他影响复合板轧制的影响因素,实验研究内容具体包括以下六个方面的内容:
(1)不同轧制工艺下,对复合界面结合率以及夹杂数量和成分的分析。
(2)加热温度以及中间材对复合轧制碳钢—不锈钢的复合板复合界面结合处的组织、成分以及力学性能的影响。
(3)压下量以及中间材对复合轧制碳钢—不锈钢的复合板复合界面结合处的组织、成分以及力学性能的影响。
(4)抽真空以及中间材对复合轧制碳钢—不锈钢的复合板复合界面结合处的组织以及力学性能的影响。
(5)热处理对复合轧制碳钢—不锈钢的复合板复合界面结合处的组织、成分以及显微硬度的影响。
(6)以现有数据为指导,提出Q235-316L复合轧制的实验室条件下的复合工艺。
2.1实验材料
实验选用的不锈钢为316L不锈钢,其厚度为4.5mm;实验选用的碳钢为Q235碳钢,其厚度为10mm;实验选用的镍箔纯度为99.99%,其厚度为0.1mm。
实验用316L不锈钢以及Q235碳钢的成分如表2.1所示。
表2.1实验用不锈钢及碳钢成分
元素
C
Cr
Mn
Mo
Ni
P
S
Si
316L
≤0.030
16.00-18.00
≤
2.00
2.00-3.00
12.00-15.00
≤0.035
≤0.030
≤
1.00
Q235
0.19
-
0.25
-
-
≤0.02
≤0.01
0.04
2.2实验设备
(1)电火花数控切割机床
型号:
DK7732;江苏泰州方正数控机床厂
(2)焊接设备
型号:
MZ-630;苏州欧思特机电设备有限公司
(3)真空泵
型号:
2XZ-1;极限压力:
0.1Pa;椒江宏兴真空设备厂
(4)热轧机组
表2.2热轧机组实验设备参数
轧机主要参数
加热炉主要参数
轧辊尺寸180mm
额定功率10KW
额定功率45Kw
额定电压220V
最大轧制压力60t
极限加热温度1300℃
轧制速度25r/min
温度偏差±10℃
(5)金相显微镜
型号:
蔡司Axioplan2imaging;蔡司光学仪器(上海)国际贸易有限公司
(6)显微硬度计
型号:
HV-1000B;莱州华银试验仪器有限公司
(7)场发射扫描电子显微镜
型号:
Nova400NanoSEM;附件:
电子背散射衍射仪,X射线能谱仪,离子溅射仪;FEI香港有限公司
(8)电液伺服万能试验机
①型号:
CMT5105;深圳新三思材料检测有限公司
②型号:
WAW-1000C电液伺服万能试验机;济南试金集团有限公司
2.3实验方法
本文研究的加中间材Ni的复合轧制不锈钢-碳钢复合板的实验流程综述如下:
第一,对利用线切割加工为同种规格的碳钢、不锈钢以及镍箔的表面进行清理;第二,对清理后的板坯进行组坯同时装抽真空接口,对复合坯进行四周密闭焊接;第三,对四周密闭的板坯抽取真空并密封抽真空接口;第四,对抽取真空后的板坯进行加热和轧制;第五,对轧后板坯进行组织、成分以及力学性能等相关检测。
2.3.1实验材料的表面处理
由于轧制复合板其力学性能对复合界面处的油脂以及氧化物等杂质非常敏感,因此复合轧制界面必须洁净;同时,现有研究成果表明,复合界面粗糙度越高,其复合界面表面积会相应增加,有利于复合轧制效果的提升。
结合于这两个方面的考虑,本实验的碳钢和不锈钢的表面处理工艺选择为砂轮机打磨,以除去碳钢和不锈钢表面的杂质,同时保证界面有一定程度的沟槽,对于较薄的镍箔,选用200目水磨金相砂纸进行打磨。
打磨后的板材表面利用无水乙醇进行清洗,并用吹风机及时吹干。
2.3.2实验材料的焊接以及抽真空
表面处理后的试样进行组坯时,用普通胶带进行简单固定,以避免在焊接过程中碳钢与不锈钢之间的错动;对于抽真空接口位置通常选择为出轧机口位置,应避免将接口位置选择为板坯侧边,这是由于在焊接过程中,抽真空接口位置为保证一定的强度会熔敷大量的金属,在轧制过程中易于发生受力不均匀,而导致板坯入轧机产生斜轧,但板坯足够大时,抽真空接口位置不受上述限制;焊接过程中选用不锈钢专用焊条,并保证一定的焊缝宽度和厚度;抽真空接口材料选外径为10mm的不锈钢圆管,这种材料具有一定的强度和塑性,便于在抽取真空完毕后的压力密封。
对焊后冷却的板坯进行抽真空,真空泵与