螺口容器注射模设计本科学位论文.docx
《螺口容器注射模设计本科学位论文.docx》由会员分享,可在线阅读,更多相关《螺口容器注射模设计本科学位论文.docx(24页珍藏版)》请在冰豆网上搜索。
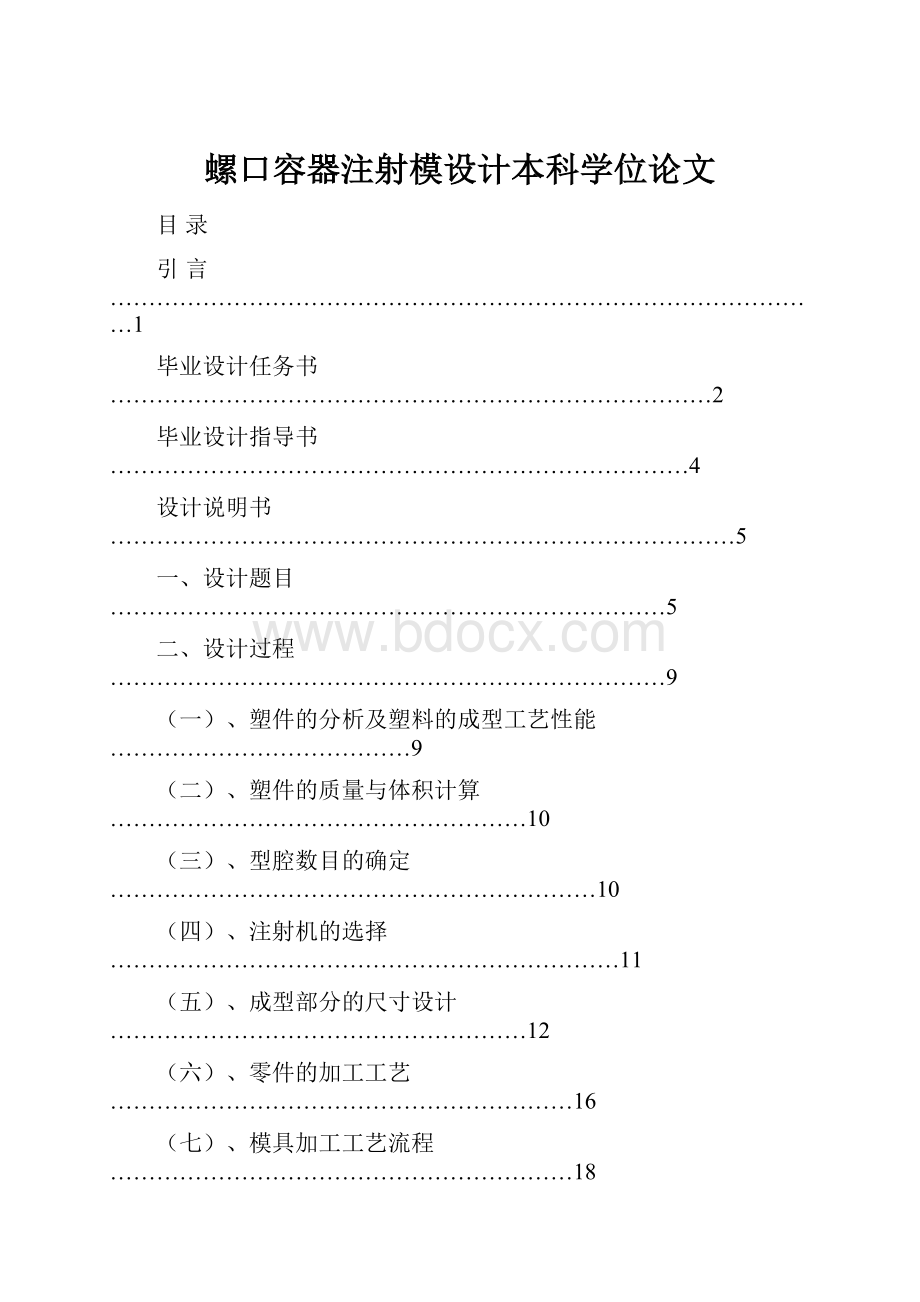
螺口容器注射模设计本科学位论文
目录
引言…………………………………………………………………………………1
毕业设计任务书……………………………………………………………………2
毕业设计指导书…………………………………………………………………4
设计说明书………………………………………………………………………5
一、设计题目………………………………………………………………5
二、设计过程………………………………………………………………9
(一)、塑件的分析及塑料的成型工艺性能…………………………………9
(二)、塑件的质量与体积计算………………………………………………10
(三)、型腔数目的确定………………………………………………………10
(四)、注射机的选择…………………………………………………………11
(五)、成型部分的尺寸设计………………………………………………12
(六)、零件的加工工艺……………………………………………………16
(七)、模具加工工艺流程……………………………………………………18
(八)、浇注系统的设计……………………………………………………19
(九)、冷却系统的设计……………………………………………………21
(十)、脱模机构的设计……………………………………………………22
(十一)、模架的选择…………………………………………………………23
(十二)、压力机的校核……………………………………………………24
(十三)HIPS(高抗冲聚苯乙烯)的成型条件………………………………25
(十四)、参考文献…………………………………………………………26
设计体会…………………………………………………………………………27
引言
本说明书为机械类塑料模注射模具设计说明书,是根据塑料模具设计手册上的设计过程及相关工艺编写的。
本说明书的内容包括:
毕业设计任务书,毕业设计指导书,毕业设计说明书,毕业设计体会,参考文献等。
编写本说明书时,力求符合设计步骤,详细说明了塑料注射模具设计方法,以及各种参数的具体计算方法,如塑件的成型工艺,塑料脱模机构的设计。
本说明书在编写过程中,得到有张蓉老师和相关同学的大力支持和热情帮助,在此谨以致意。
由于本人设计水平有限,在设计过程中难免有错误之处,敬请各位老师批评指正。
毕业设计任务书
一.设计题目:
螺口容器注射模材料HIPS(高抗冲聚苯乙烯)
图如下:
二.原始数据
1尺寸公差按SJ1372—78,3级(参考塑料模设计资料一,表6-6)孔类尺寸为正公差,轴类尺寸公差为负公差;
2尺寸公差为
;
3角度公差为
4塑胶件表面光亮无划伤痕迹;
5生产批量为大批量。
三.设计要求
1尽量选用标准模架,在保证生产率和质量的同时,力求降低模具成本和使用寿命。
2在保证模具强度的前提下,注意外形美观和各部分协调。
3所设计的模具要便于搬运和安装,并且方便、可靠。
4模具总装配图、动、定模板、凸模、凹模、定位圈、浇口套等图纸各一张。
(其中至少要有一张1号以上的计算机绘图)
四.设计目的
综合运用在学校所学的理论知识和技能,设计汽车仪表/电子计时器等塑料模具,使学生熟悉设计开发模具的流程,培养学生的独立思考能力,检验学生的学习效果和动手能力,提高学生的工程实践能力,为将来实际工作打下坚实的基础。
五、设计图纸
模具总装图一张、动、定模板、凸模、凹模、定位圈、浇口套、型芯等所有非标准零件图及电子文件(即*.doc/*.dwg/*.prt/*.asm文件,其中至少要有一张1号以上的计算机绘图)。
六、设计说明书(要求不少于1万字,)
1、资料数据充分,并标明数据出处。
2、计算过程详细、完全。
3、公式的字母含义应标明,有时还应标注公式的出处。
4、内容条理清楚,按步骤书写。
5、说明书要求用计算机打印出来。
七、整个设计资料包括:
全套图纸、设计计算说明书、设计任务书、设计笔记。
八、自选两个重要模具成型零件编制加工工艺过程卡。
九、编制模塑成型工艺卡。
十、参考资料:
1、国家标准总局编《塑料模国家标准》中国标准出版社,1999
2、陈万林编著《塑料模具设计与制作教程》北京希望电子出版社,
2000
3、黄健求编《模具制造》机械工业出版社,2001
4、黄毅宏编《模具制造工艺学》机械工业出版社,1996
5、王孝培编《塑料成型工艺及模具简明手册》机械工业出版社,2000
6、陈晓华、王秀英编《典型零件模具图册》机械工业出版社,2001
7、翁其金编《塑料模塑工艺与塑料模设计》机械工业出版社,1999
8、塑料模具技术手册编委会《塑料模具技术手册》机械工业出版社,1997
9、孙凤勤编《冲压与塑压设备》机械工业出版社,1997
10、黄锐编《塑料工程手册》机械工业出版社,2000
11、屈华昌编《塑料成型工艺与模具设计》机械工业出版社,1995
毕业设计指导书
一、题目:
螺口容器注射模材料HIPS(高抗冲聚苯乙烯)
二、明确设计任务,收集有关资料
1、了解毕业设计的任务、内容、要求和步骤,制定设计工作进度计划(一般需6—8周)
2、将Pro/E零件图,转化为AUTOCAD平面图,并标好尺寸
3、查阅、收集有关的设计参考资料
4、了解所设计零件的用途、结构、性能,在整个产品中装配关系、技术要求、生产批量
5、塑胶厂车间的设备资料
6、模具制造技能和设备条件及可采用的模具标准情况
三、工艺性分析
分析塑胶件的工艺性包括技术和经济两方面,在技术方面,根据产品图纸,主要分析塑胶件的形状特点、尺寸大小、尺寸标注方法、精度要求、表面质量和材料性能等因素,是否符合模塑工艺要求;在经济方面,主要根据塑胶件的生产批量分析产品成本,阐明采用注射生产可取得的经济效益。
1、塑胶件的形状和尺寸:
塑胶件的形状和尺寸不同,对模塑工艺要求也不同。
2、塑胶件的尺寸精度和外观要求
塑胶件的尺寸精度和外观要求与模塑工艺方法、模具结构型式及制造精度等有关。
3、生产批量
生产批量的大小,直接影响模具的结构型式,一般大批量生产时,可选用一模多腔来提高生产率;小批量生产时,可采用单型腔模具等进行生产来降低模具的制造费用。
4、其它方面
在对塑胶件进行工艺分析时,除了考虑上述因素外,还应分析塑胶件的厚度、塑料成型性能及模塑生产常见的制品缺陷问题对模塑工艺性的影响。
四、确定成型方案及模具型式:
根据对塑胶零件的形状、尺寸、精度及表面质量要求的分析结果,确定所需的模塑成型方案:
制品的后加工、分型面的选择、型腔的数目和排列、成型零件的结构、浇注系统等。
五、工艺计算和设计
1、注射量计算:
涉及到选择注射机的规格型号,一般应先进行计算。
对于形状复杂不规则的制品,可以利用Pro/E的“分析/模型分析/模型质量属性”来计算质量。
或者采用估算法估计塑料的用量,以保证足够的塑料用量为原则。
2、浇注系统设计计算:
这是设计注射模的第一步,只有完成浇注系统的设计后才能估算型腔压力、注射时间、校核锁模力,从而进一步校核所选择的注射机是否符合要求。
浇注系统设计计算包括浇道布置、主流道和分流道断面尺寸计算、浇注系统压力降计算和型腔压力校核。
3、成型零件工作尺寸计算:
主要有凹模和型芯径向(长/宽)尺寸和高度(深度)尺寸,其最大值直接关系到模具尺寸大小,而工作尺寸的精度则直接影响到制品精度。
为计算方便,凡孔类尺寸均以其最小尺寸作为公称尺寸,即公差为正;凡轴类尺寸均以其最大尺寸作为公称尺寸,即公差为负;进行工作尺寸计算时应考虑塑料的收缩率和模具寿命(磨损裕量)等因素。
4、模具冷却与加热系统计算:
冷却系统计算包括冷却时间和冷却参数计算。
冷却时间计算有三种方法,根据塑料制品形状和塑料性能选择适当的公式进行计算即可。
冷却参数包括冷却面积、冷却水空长度和孔数的计算及冷却水流动状态的校核和冷却水入口与出口处温度差的校核。
模具加热工艺计算主要是加热功率计算。
5、注射压力、锁模力和安装尺寸校核:
模具初步设计完成后,还需校核所选择的注射机注射压力和锁模力能否满足塑料成型要求,校核模具外形尺寸可否方便安装,行程是否满足模塑成型及取件要求。
六、进行模具结构设计
1、确定凹模(模板)尺寸:
先计算凹模(模板)厚度,再根据厚度确定凹模(模板)周界尺寸(长X宽),在确定凹模(模板)周界尺寸时要注意:
第一,浇注系统的布置,特别是对于一模多腔的塑料模应仔细考虑模腔位置和浇道布置;第二,要考虑凹模上螺孔的布置位置;第三,主流道中心与模板的几何中心应重合;第四,凹模(模板)外形尺寸尽量按国家标准选取。
2、选择模架并确定其他模具零件的主要参数:
在确定模架结构形式和定模、动模板的尺寸后,可根据定模、动模板的尺寸,从《塑料模国家标准》GB/T12555—1990(塑料注射模大型模架)和GB/T12556—1990(塑料注射模中小型模架及技术条件)中确定模架规格。
待模架规格确定后即可确定主要塑模零件的规格参数。
再查阅标准中有关零部件图表,就可以画装配图了。
七、画装配图
一般先画主视图,再画侧视图和其他视图。
由于注射机大多为卧式的,故注射模也常按安装位置画成卧式,画主视图最好从凸凹模结合面(即分型面)开始,向左右两个方向画较为方便,且不易出错。
模具装配图包括:
1、主视图:
绘制模具工作位置的剖面图
2、侧视图:
一般情况下绘制定模部分视图,
3、俯视图、局部剖视图等。
4、列出零件明细表,注明材质和数量,凡标准件须注明规格。
5、技术要求及说明,包括所选注射机设备型号,所选用的标准模架型号,模具闭合高度,模具间隙及其它要求。
八、绘制各非标准零件图
零件图上应注明全部尺寸、公差与配合、形位公差、表面粗糙度、所用材料、热处理方法及其它要求。
九、编写技术文件
1、编写注射成型工艺卡片:
根据塑料的成型特点,查阅有关资料,确定合理的注射成型工艺参数,并作成工艺卡片。
2、编写加工工艺过程卡片:
选取两个重要模具成型零件,确定加工工艺路线,并作成加工工艺过程卡片
3、编写设计说明书
设计说明书
第一部分设计题螺口容器注射模材料HIPS(高抗冲聚苯乙烯)
第二部分设计过程
一、塑件的分析及塑料的成型工艺性能
1、塑件工艺性分析
1)塑件的尺寸较小,精度等级高精度,性能要求一般,采用一模二腔来提高生产率。
塑件壁薄,对制品不进行后加工。
5浇口采用探针浇口,适用于一模二腔,浇口截面为圆形。
6了方便加工和热处理,型腔与型芯部分来镶拼结构。
2、材料的成型工艺性能
1)塑件采用HIPS,HIPS的主要工艺性能有:
物理性能:
HIPS的相对密度介于0.98~1.10之间,耐磨性好,冲击强度比PS高。
热性能:
热变形温度为64~92.5
电性能:
HIPS电性能优异,耐高频绝缘性好。
力学性能:
HIPS具有优异的力学性能,包括拉升强度、压缩强度和硬度,PP的主要力学性能数据为:
拉伸强度/MPa14~48
压缩强度/MPa28~112
缺口冲击强度(KJ/m2)0.5~11.0
化学性能:
HIPS的化学稳定性好。
HIPS的主要缺点是:
注射时应防止溢料,制品易产生内应力,易开裂。
HIPS的主要用途是:
装饰材料、容器、家用电器、建材等。
2)注塑成型条件
注射成形机类型:
螺杆式
密度(g/cm3):
0.98~1.10
计算收缩率(%):
0.4~0.7
预热温度(℃):
64~92.5
料筒温度前段:
170~180
料筒温度中段:
170~200
料筒温度后段:
150~160
模具温度(℃):
20~50
注射压力(Mpa):
60~100
塑件内形(内径)与凸模外形(外径)尺寸(mm)对应关系。
d凸=(Ds+QsQcp+x∆s)
式中d凸—凸模型芯外形(外径)尺寸(mm)
Ds—塑件内形(内径)基本尺寸(mm)
即塑件实际内形尺寸Dsَ
→(Dsَ+δ2)
=Ds
Δs—塑件公差
Qcp—塑料平均收缩率(%),取0.55%
X—综合修正系数,取x=0.75
Δm—模具制造公差,取Δm=1/4Δs
D芯=
=
2、型芯深度尺寸计算
H芯—型腔深度尺寸
hs—塑件高度基本尺寸,即塑件的实际高度尺寸
hs´→(hs´+δ1)
=hs
∆s—塑件公差
Qsp—塑料平均收缩率,取0.55
X—综合修合系数,取x=0.75
∆m—模具制造公差,取∆m=1/4∆s
H芯=
=
5、成型中心矩尺寸
塑件中心距与模具成型中心尺寸关系
L中=(Ls+LsQcp)±1/2∆m
式中L中—成型中心距尺寸(mm)
Ls—塑件中心距基本尺寸(mm),即塑件实际中心距尺寸
Ls´
→(Ls´+1/2δ2)±1/2(δ1-δ2)
=Ls±1/2∆s
∆s—塑件公差
Qcp—塑料平均收缩率(%),取0.55%
∆m—模具制造公差,∆m=1/4∆s
L中=(40+40×0.55%)±1/2∆m
=40.22±1/8∆s
=40.22±0.023
六、零件的加工工艺:
1.定模型芯
定模型芯是主要的工作零件,我们选用T8A的材料,同时考虑到此塑料对尺寸精度要求一般,但对表面要求较高,根据本工厂的实际设备情况,在对材料进行粗加工后,留0.5mm的单边,淬火,低温回火后,用电火花机放电到位,最后还需要对成型表面进行抛光。
其浇道衬套孔要与衬套配合,在粗加工后,留单边0.2—0.5mm的余量,热处理
后采用慢走丝割出即可。
综上所述,定模型芯加工工艺如下:
1.材料:
T8A
2.加工工艺:
1)开料:
开出底面半径为35,高为100的圆柱毛坯。
2)磨基准:
按照零件图基准方位在平面磨床上磨出基准面,同时磨平各平面,留0.1—0.3mm单边余量。
3)按照图样,在铣床上钻螺纹孔,运水孔。
4)在数控铣床上采用Mastercam9.0软件,按照图样要求铣出两个型腔的形状,单边留0.2—0.5mm的余量。
5)送热处理车间进行热处理:
淬火(油淬+低温回火),使其表面硬度达到56—60HRC。
6)按照图样要求加工型芯各表面,保证型芯的平行度,垂直度,要求型芯磨后六面见光。
2.动模型芯
同定模型芯一样。
3.行位
a)材料:
T8A
b)加工工艺:
1)开料:
在钢板上割出一块底面半径为50,高为90的毛坯。
2)在平面磨床上磨基准。
3)在铣床上有角度分度头调好角度,粗铣左侧的圆柱面。
4)在铣床上铣出如图所示右侧的形状及其导滑部分。
6)钻螺钉固定孔。
7)热处理:
淬火+低温回火,淬硬表面硬度为54—58HRC。
8)磨削基准平面及其圆柱面,使各部分的尺寸加工到位。
9)在滑块斜面磨出45度,宽大10mm,深0.2mm的储油槽,其它的零件在此就不一一叙述。
七、模具加工工艺流程:
1、根据零件结构和制造工艺,模架的基本组成零件有两种:
导柱、导套等回转零件;模板等平板零件。
导柱、导套的加工主要是内、外圆柱面加工,平板内零件的制造过程主要进行平面加工和孔隙加工,他们在模具中起定位的导向作用,保证凹凸模在工作时具有正确的相对置,除了要保证导柱,导套配合表面尺寸形状精度外,还应该保证导柱、导套各自配合面之间的同轴度要求。
导柱、导套一般采用低碳钢进行渗碳、淬火处理,也可选用碳素工具钢T10淬火处理,淬火处理硬度58-62HRC。
根据分析,导柱、导套加工艺过程如下:
备料——粗车、半精车内外圆柱表面——热处理——研磨导柱中心孔——粗磨、精磨配合表面——研磨导柱、导套重要配合表面。
1凸模加工工艺过程如下:
下料——锻造——退火——粗加工——精磨基面准面——划线——工作型面半精加工——淬火、回火——磨削——修研。
2凹模加工工艺过程如下:
下料——锻造——退火——粗加工六面——精磨基面准面——划线—型孔半精加工——型孔精加工——淬火、回火——精磨(研磨)
3模架的装配:
导柱、导套与模板之间一般采用过盈配合,装配时可采用手动压力机将导柱压入动模板的导柱孔,复位机构的装配复位杆与固定板一般采用过度配合。
模架的装配比较的简单,主要是用螺钉将装有导套的定模板连接起来。
4模具表面强化处理工艺特点及应用:
渗氮处理:
渗氮处理是向模具零件表面渗入氮原子的过程,
模具渗氮前应加工到尺寸精度和表面粗糙度,最好是经过试模确认完全合格后再进行渗氮处理。
根据模具的技术要求分别采用以下两种工艺路线:
精密模具:
备料——锻造——退火或回火——粗加工——调质——半精加工——装配——试模——渗氮——研磨抛光——装配;
一般模具:
备料——粗加工——调质——精加工——糁氮——研磨——装配;
5总装的技术要求
a、装配后的模具安装表面的平行误差不大于0.05;
b、模具闭合后分型面应均密合;
c、导柱、导套滑动灵活,推件时推杆和卸料板动作一致;
d、合模后动模部分和定模部分的型芯必须紧密接触
6试模:
模具在装配完成之后,在交付生产时试模,其目的是检查模具在设计制造上是否存在缺陷,若有,则要求排除;对模具成型工艺条件进行试验以有利于模具成型工艺的确定和提高。
八、浇注系统的设计
1、浇口套的设计
采用一模二腔,须设定分流道;采用分体式,浇口套材料选用优质钢T8A,淬火处理。
为了便于凝料的拔出,主流道设计为锥孔,内壁Ra为0.63um,锥角为40,,其小端直径D1=D2+(0.5~1)=3+0.5=3.5,主流道大侧面圆角R=3mm,浇口套大端高出定模端面H=5~10mm,起定位作用,与注射机定模板的定位孔呈间隙配合,衬口套球面半径Sr=SR+(0.5~1),取Sr=16mm,定位环外径D取50mm,厚度取10mm。
流道及平衡布置:
(1)分流道是进料通道,采用U形侧面,其分流道加工较容易,热量损失和流动阻力均不大,是最常用形式,分流道侧面尺寸视塑件尺寸、塑料品种、注射速率以及分流道长度而定;分流道侧面尺寸应满足良好的压力传递和保证合理的填充时间,U形侧面分流道深度h=2r(r为圆弧半径),h=2×4=8mm,斜度α取60,分流道长度Lf通常取8~30mm,分流道表面不要求太光洁,表面粗糙度通常取Ra1.25~Ra2.5um。
(2)分流道的平衡布置
多型腔模具应尽量采用平衡式分流道,能让熔融塑料几乎同时到达每个型腔的进料口,以致塑料到每个型腔的压力和温度是相同的,这样不易产生熔接痕和填充不足等缺陷,其流道布置形式如图。
2、浇口的设计
浇口的设计与塑料性能、塑件形状、侧面尺寸、模具结构及注射工艺参数等有关,要是熔料以比较快的速度进入并充满型腔,同时在充满后能适时冷却封闭。
因此浇口的侧面要小,长度要短这样可增大料流的速度,快速冷却封闭,且便于塑件与浇口凝料分离,不留明显的浇口痕迹,保证塑件的外观质量、浇口位置,形状及尺寸对塑件性能和质量的影响很大。
(1)浇口的选用
浇口可分为限制性和非限制性浇口两种,限制性浇口一方面通过侧面的突变,使其成为理想的流动状态,迅速而均衡地充满型腔;另一方面改善塑料熔体进入型腔时的流动特性,调节浇口尺寸,可使多型腔同时充满,可控制填充时间、冷却时间及塑件表面质量,同时起着封闭型腔,防止塑料熔体倒流。
我们采用的是60口,普遍使用于中小型塑件的多型腔模具,也可用于单型腔模具或表面不允许有较大痕迹的塑件。
在这套模具,其浇口尺寸如图所示。
浇口各部分尺寸取的都是经验值,L=0.3~2mmd=0.7~1.2α=60~150。
探针浇口的优点是浇口自动去除缺点是回料高,模具使用费用高。
九、冷却系统的设计
注塑模温对塑料熔体的流动、固化定型、生产率以及塑件的形状和尺寸精度有着直接的影响。
注射成型时,不同的塑料对模温有着不同的要求,控制适宜的模温来保证塑料熔体具有最佳的流动性,易于充满型腔,并使塑件脱模后的收缩、翘曲变形小,形状与尺寸稳定,具有较高的物理力学性能以及较高的表面质量。
通过温度调节与控制系统可收到如下效果。
2改善成型性能:
可以使模塑温度保持适应于各塑料的规格温度,以改善成型性能。
3稳定尺寸精度:
如果塑模温度发生变化,则塑料的收缩率也会有很大的变动,尤其对结果性塑料,因此,若塑模温度保持一定,收缩率也就得到稳定,塑件的尺寸精度自然就稳定了。
4减少塑件变形:
提高塑件精度。
5改善塑件表面质量:
消除外观缺陷,合理的模温可提高塑件的外观质量和降低表面粗糙度。
由于制品平均壁厚为1.5mm左右,制品尺寸又较小,根据经验数据,确定水孔直径为8mm,其循环回路如下:
十、脱模机构的设计
在注射成型的每一个循环中,塑件必须由模具型腔中或凸模/型芯上松动分离(即脱出),脱出机构的机构就叫塑件脱出机构,脱出机构的设计基本考虑:
1保证塑件质量
2脱出机构结构
3所需顶出行程、开模行程计算
顶出行程计算
S顶=h凸+e
式中S顶—所需顶出行程
h凸—型芯成型高度
e—顶出行程富裕量(mm)
S顶=90+5=95mm
所需开模行程计算
S开=h塑+h凸模+e
式中S开—开模行程(mm)
h塑—塑件及浇注系统在开模方向上的总投影高度(mm)
h凸模—动定模型芯突出分型面的高度总和(mm)
e—取件及取出浇注系统凝料的开模行程富裕量(mm)
S开=90+90+8=188(mm)(浇注系统无废料排出,顶出行程只计算塑件高度)
十一、模架的选择
根据所选设计的定模型腔的尺寸和设计的需要,采用香港龙记集团(LKM)
的大水口模架,其型号为:
3540-CI-A100-B30
其主要参数如下:
凹模板厚度A=100mm
凸模板厚度B=30mm
垫块厚度C=100mm
模具的闭合厚度H=270mm
模板宽B0=250长L0=177mm
座板宽B1=250长L1=237mm
定模座板厚H1=20mm
动模座板厚H2=20mm
推杆固定板h1=10mm
顶出底板厚度h2=25mm
顶出底板长度B2=184mm
导柱d1=30mm
推杆d3=190mm
十二、压力机的校核
(1)最大注射量的校核
K利G公≥G件+G废
式中G公—注射机公称质量注射量
K利—注射机最大注射量的利用系数,取0.8
G件—塑件的质量
G废—浇注系统等废料的质量
塑件重量14.5g,浇注系统重量0.3g
则每次注射所需塑料量为2×14.5+0.3=37.7g
注射机的最大注射量60×0.8=48g>37.7g,故能满足要求。
(2)锁模力与注射压力的校核
锁模力可按F≥Pm(nAz+Aj)校核
式中Pm—塑料注射压力Pm=80~130Mpa,,取Pm=100Mpa
Az—塑料在分型面上的投影面积(cm2)
Aj—浇注系统在分型面上的投影面积(cm2)
F—注射机额定锁模力SZ-60/40
注射机额定锁模力为400KN
投影面积计算:
估算:
Az=1.73(cm2)
Aj==36.29(cm2)
代入公式中得Pm=100(1.73+36.29)=370KN
由于F=400KN,故满足F>378KN,同样SZ-60/40的额定注射压力150KN>100KN,也能满足PMMA塑料的注射压力要求。
(3)模具厚度H与注射机闭合高度校