火箭发动机燃烧室壳体成形工艺设计.doc
《火箭发动机燃烧室壳体成形工艺设计.doc》由会员分享,可在线阅读,更多相关《火箭发动机燃烧室壳体成形工艺设计.doc(22页珍藏版)》请在冰豆网上搜索。
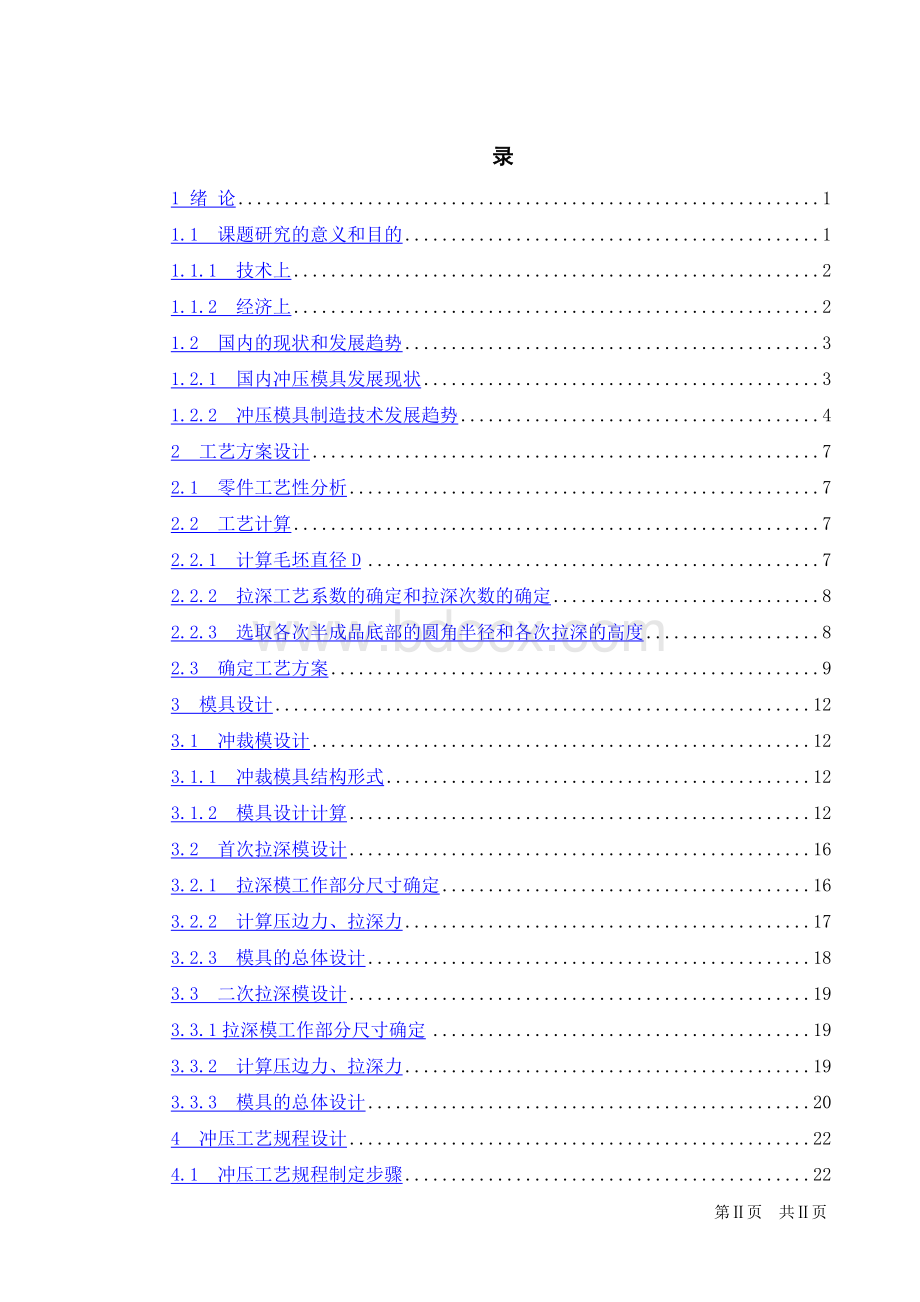
录
1绪论 1
1.1课题研究的意义和目的 1
1.1.1技术上 2
1.1.2经济上 2
1.2国内的现状和发展趋势 3
1.2.1国内冲压模具发展现状 3
1.2.2冲压模具制造技术发展趋势 4
2工艺方案设计 7
2.1零件工艺性分析 7
2.2工艺计算 7
2.2.1计算毛坯直径D 7
2.2.2拉深工艺系数的确定和拉深次数的确定 8
2.2.3选取各次半成品底部的圆角半径和各次拉深的高度 8
2.3确定工艺方案 9
3模具设计 12
3.1冲裁模设计 12
3.1.1冲裁模具结构形式 12
3.1.2模具设计计算 12
3.2首次拉深模设计 16
3.2.1拉深模工作部分尺寸确定 16
3.2.2计算压边力、拉深力 17
3.2.3模具的总体设计 18
3.3二次拉深模设计 19
3.3.1拉深模工作部分尺寸确定 19
3.3.2计算压边力、拉深力 19
3.3.3模具的总体设计 20
4冲压工艺规程设计 22
4.1冲压工艺规程制定步骤 22
4.2该零件冲压工艺的难点 22
4.3冲压工艺规程方案的确定 23
5模具主要零件的工艺设计 24
5.1机械制造工艺设计的一般性原则:
24
5.1.1零件的工艺分析:
结构分析与技术要求分析 24
5.1.2毛坯选择 24
5.1.3基准选择 24
5.1.4拟定工艺路线 24
5.1.5机床和工艺装备的确定 25
5.1.6工序及加工余量的确定 25
5.1.7工序尺寸和公差的确定 25
5.1.8切削参数的计算确定 25
5.1.9工艺文件的编制 25
5.2首次拉深模凹模加工工艺设计 26
5.2.1零件分析 26
5.2.2选择毛坯 27
5.2.3工艺规程设计 28
5.2.4工艺卡片的填写 32
6结论 33
参考文献 34
致谢 35
1绪论
1.1课题研究的意义和目的
火箭发动机,是指由飞行器自带推进剂(燃料和氧化剂)不依赖外界空气的喷气发动机[1]。
火箭发动机主要由燃烧室、燃气发生剂、点火装置及燃气喷嘴组成。
其中火箭发动机燃烧室是用来贮存固体推进剂装药并在其中燃烧的部件。
由筒体壳体、两端封头壳体及绝热层组成。
燃烧室是火箭发动机的重要组成部件,同时也是弹体结构的组成部分,装药在其内燃烧,将化学能转换成热能。
燃烧室承受着高温高压燃气的作用,还承受飞行时复杂的外力及环境载荷[2][3]。
图1.1固体火箭发动机
图1.2液体火箭发动机
由于火箭发动机燃烧室工作时产生高温、高压和强振动,一些推进剂具有极低温和强腐蚀性能,因此燃烧室要求有极高的耐热、耐极低温、抗疲劳、抗腐蚀的性能和良好的机械性能(如强度、刚度等)。
而冲压件刚性好、强度高、重量轻、表面质量好。
冲压加工过程中,材料表面不易遭受破坏,且通过塑性变形还可以使制件的机械性能有所提高[4]。
故用冲压模具来制造该零件。
模具是当今工业生产中使用极为广泛的主要工艺装备,是最重要的工业生产手段和工艺发展方向,一个国家工业水平的高低在很大程度上取决于模具工业的发展水平,模具工业的发展水平是一个国家工业水平的重要的标志之一。
模具工业称作“黄金工业”[5]。
冲压模具作为模具种类之一有以下的优点[6]:
1.1.1技术上
(1)在材料消耗不大的前提下,制造出的零件重量轻、刚度好、精度高。
由于在冲压过程中材料的表面不受破坏,使得制件的表面质量较好,外观光滑美观。
并且经过塑性变形后,金属内部组织得到改善,机械强度有所提高。
(2)在压力机的简单冲击作用下,一次工序即可完成由其他加工方法所不能或难以制造完成的较复杂形状零件加工。
(3)制件的精度较高,且能保证零件尺寸的均一性和互换性。
不需要进一步的机械加工即可满足一般的装配和实验要求。
1.1.2经济上
(1)原材料是冶金厂大量生产的价廉的轧制板或带料。
(2)采用适当的工艺后,可大量节约金属材料,可以实现少切屑和无切屑的加工方法。
材料利用率可达75%—85%,因而制件的成本相应地比较低。
(3)节省能源。
冲压时不需要加热,也不象切削加工那样将金属切成碎屑而需要消耗很大的能量。
(4)生产率高。
每分钟一台冲压设备可生产零件从几件到几十件。
目前的高速冲床生产率则每分钟高达数百件甚至上千件。
(5)操作简单,便于组织生产。
在大批量的生产中,易于实现机械化和自动化,进一步提高劳动生产率。
(6)对操作人员的技术要求不高。
当生产需要时,用短期培训的方法既可解决操作人员不足的问题。
由于冲压模具有以上的优点和发展前景和火箭发动机燃烧室壳体严格的质量要求,因此,利用冲压模具来制造火箭发动机热燃烧室壳体工艺设计具有重要意义。
所以本课题的目的就是要制定合理的设计制造工艺(包括模具设计)。
1.2国内的现状和发展趋势
1.2.1国内冲压模具发展现状
改革开放以来,随着国民经济的高速发展,市场对模具的需求量不断增长。
近年来,模具工业一直以15%左右的增长速度快速发展,模具工业企业的所有制成分也发生了巨大变化,除了国有专业模具厂外,集体、合资、独资和私营也得到了快速发展。
浙江宁波和黄岩地区的“模具之乡”;广东一些大集团公司和迅速崛起的乡镇企业,科龙、美的、康佳等集团纷纷建立了自己的模具制造中心;中外合资和外商独资的模具企业现已有几千家。
随着与国际接轨的脚步不断加快,市场竞争的日益加剧,人们已经越来越认识到产品质量、成本和新产品的开发能力的重要性。
而模具制造是整个链条中最基础的要素之一,模具制造技术现已成为衡量一个国家发展水来的标志。
近年许多模具企业加大了用于技术进步的投资力度,将技术进步视为企业发展的重要动力。
一些国内模具企业已普及了二维CAD,并陆续开始使用UG、Pro/Engineer、I-DEAS、Euclid-IS等国际通用软件,个别厂家还引进了Moldflow、C-Flow、DYNAFORM、Optris和MAGMASOFT等CAE软件,并成功应用于冲压模的设计中。
以汽车覆盖件模具为代表的大型冲压模具的制造技术已取得很大进步,东风汽车公司模具厂、一汽模具中心等模具厂家已能生产部分轿车覆盖件模具。
此外,许多研究机构和大专院校开展模具技术的研究和开发。
经过多年的努力,在模具CAD/CAE/CAM技术方面取得了显著进步;在提高模具质量和缩短模具设计制造周期等方面做出了贡献。
例如,吉林大学汽车覆盖件成型技术所独立研制的汽车覆盖件冲压成型分析KMAS软件,华中理工大学模具技术国家重点实验室开发的注塑模、汽车覆盖件模具和级进模CAD/CAE/CAM软件,上海交通大学模具CAD国家工程研究中心开发的冷冲模和精冲研究中心开发的冷冲模和精冲模CAD软件等在国内模具行业拥有不少的用户。
虽然中国模具工业在过去十多年中取得了令人瞩目的发展,但许多方面与工业发达国家相比仍有较大的差距。
例如,精密加工设备在模具加工设备中的比重比较低;CAD/CAE/CAM技术的普及率不高;许多先进的模具技术应用不够广泛等等,致使相当一部分大型、精密、复杂和长寿命模具依赖进口。
我国的模具技术有了很大发展,模具的精密度、复杂程度和寿命都有很大提高。
如,主要的汽车模具企业已能生产大型、精密的轿车覆盖件模具;体现高水平制造技术的多工位级进模的覆盖面增加;塑料模热流道技术日渐成熟,气体辅助注射技术开始采用;压铸工艺得到发展。
此外,CAD/CAM/CAE技术得到广泛应用,高速加工、复合加工等先进的加工技术也得到进一步推广;快速原型进展很快;模具的标准化程度也有一定提高。
但是,由于我国的模具行业起步较晚,与国外相比,仍存在不小的差距,主要体现在:
(1)产需矛盾:
随着工业发展水平的不断提高,工业产品更新速度的加快,对模具的需求越来越大。
无论是数量还是质量都无法满足国内市场的需要,只达到70%左右。
造成矛盾突出的原因是模具企业的专业化、标准化程度低,生产周期长。
另外,设计和制造工艺水平还不能完全适应发展的需要。
(2)企业结构不合理:
我国很多模具生产能力集中在各主机厂的模具分厂或车间内,模具的商品化程度低,而国外70%以上都是专业模具厂,且走的是“小而精”的道路,因此生产效率和经济效益俱佳。
(3)产品水平:
衡量模具的产品水平,主要有模具加工的制造精度和表面粗糙度,加工模具的复杂程度,以及模具的制造周期和使用寿命。
而这几项指标与国外相比的差距都十分明显。
(4)模具工业的整体装备水平也存在相对落后,利用率低的现象。
高素质的模具技术人才缺乏,产品的综合开发能力还急需加强。
1.2.2冲压模具制造技术发展趋势
模具技术的发展应该为适应模具产品“交货期短”、“精度高”、“质量好”、“价格低”的要求服务。
达到这一要求急需发展如下几项[7]:
(1)全面推广CAD/CAM/CAE技术
模具CAD/CAM/CAE技术是模具设计制造的发展方向。
随着微机软件的发展和进步,普及CAD/CAM/CAE技术的条件已基本成熟,各企业将加大CAD/CAM技术培训和技术服务的力度;进一步扩大CAE技术的应用范围。
计算机和网络的发展正使CAD/CAM/CAE技术跨地区、跨企业、跨院所地在整个行业中推广成为可能,实现技术资源的重新整合,使虚拟制造成为可能。
(2)高速铣削加工
国外近年来发展的高速铣削加工,大幅度提高了加工效率,并可获得极高的表面光洁度。
另外,还可加工高硬度模块,还具有温升低、热变形小等优点。
高速铣削加工技术的发展,对汽车、家电行业中大型型腔模具制造注入了新的活力。
目前它已向更高的敏捷化、智能化、集成化方向发展。
(3)模具扫描及数字化系统
高速扫描机和模具扫描系统提供了从模型或实物扫描到加工出期望的模型所需的诸多功能,大大缩短了模具的在研制制造周期。
有些快速扫描系统,可快速安装在已有的数控铣床及加工中心上,实现快速数据采集、自动生成各种不同数控系统的加工程序、不同格式的CAD数据,用于模具制造业的“逆向工程”。
模具扫描系统已在汽车、摩托车、家电等行业得到成功应用,相信在“十五”期间将发挥更大的作用。
(4)电火花铣削加工
电火花铣削加工技术也称为电火花创成加工技术,这是一种替代传统的用成型电极加工型腔的新技术,它是有高速旋转的简单的管状电极作三维或二维轮廓加工(像数控铣一样),因此不再需要制造复杂的成型电极,这显然是电火花成形加工领域的重大发展。
国外已有使用这种技术的机床在模具加工中应用。
预计这一技术将得到发展。
(5)提高模具标准化程度
我国模具标准化程度正在不断提高,估计目前我国模具标准件使用覆盖率已达到30%左右。
国外发达国家一般为80%左右。
(6)优质材料及先进表面处理技术
选用优质钢材和应用相应的表面处理技术来提高模具的寿命就显得十分必要。
模具热处理和表面处理是否能充分发挥模具钢材料性能的关键环节。
模具热处理的发展方向是采用真空热处理。
模具表面处理有热喷涂技术、激光表面处理、离子注入表面改性、等离子体化学气相沉淀等[8]。
(7)模具研磨抛光将自动化、智能化
模具表面的质量对模具使用寿命、制件外观质量等方面均有较大的影响,研究自动化、智能化的研磨与抛光方法替代现有手工操作,以提高模具表面质量是重要的发展趋势。
(8)模具自动加工系统的发展
模具自动加工系统应有多台机床合理组合;配有随行定位夹具或定位盘;有完整的机具、刀具数控库;有完整的数控柔性同步系统;有质量监测控制系统。
(9)开发新的成形工艺和模具
如粉末冶金的注塑成形工艺等,将扩大模具成形的加工范围,为模具工业带来更大的发展空间[9]。
由以上的分析可以看出,我国冲压模具和国外相比还存在一定的差距。
但随着模具行业的兴起和发展