车床主轴的零件机械加工工艺规程设计附cad图.docx
《车床主轴的零件机械加工工艺规程设计附cad图.docx》由会员分享,可在线阅读,更多相关《车床主轴的零件机械加工工艺规程设计附cad图.docx(19页珍藏版)》请在冰豆网上搜索。
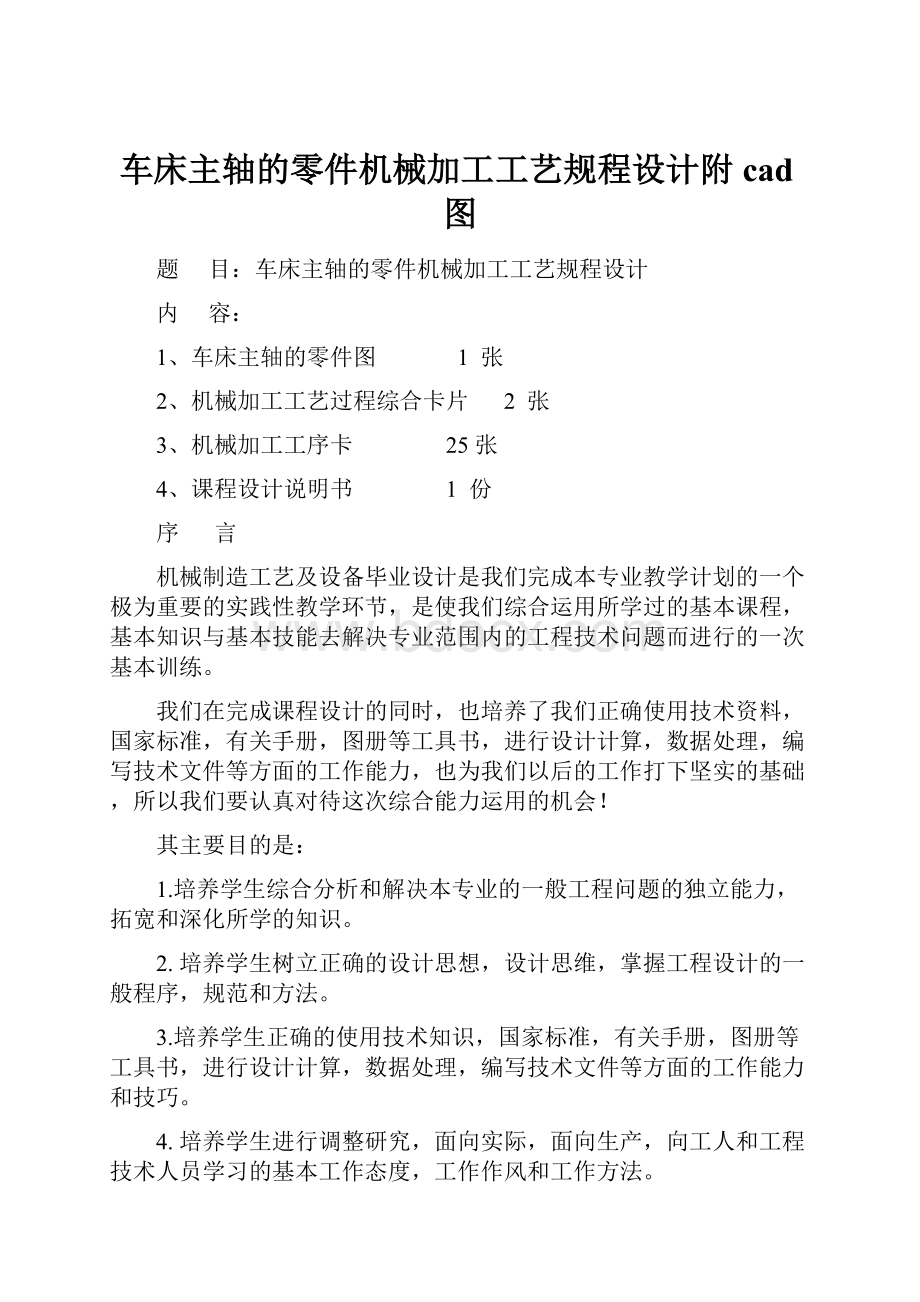
车床主轴的零件机械加工工艺规程设计附cad图
题 目:
车床主轴的零件机械加工工艺规程设计
内 容:
1、车床主轴的零件图 1 张
2、机械加工工艺过程综合卡片 2 张
3、机械加工工序卡 25张
4、课程设计说明书 1 份
序 言
机械制造工艺及设备毕业设计是我们完成本专业教学计划的一个极为重要的实践性教学环节,是使我们综合运用所学过的基本课程,基本知识与基本技能去解决专业范围内的工程技术问题而进行的一次基本训练。
我们在完成课程设计的同时,也培养了我们正确使用技术资料,国家标准,有关手册,图册等工具书,进行设计计算,数据处理,编写技术文件等方面的工作能力,也为我们以后的工作打下坚实的基础,所以我们要认真对待这次综合能力运用的机会!
其主要目的是:
1.培养学生综合分析和解决本专业的一般工程问题的独立能力,拓宽和深化所学的知识。
2.培养学生树立正确的设计思想,设计思维,掌握工程设计的一般程序,规范和方法。
3.培养学生正确的使用技术知识,国家标准,有关手册,图册等工具书,进行设计计算,数据处理,编写技术文件等方面的工作能力和技巧。
4.培养学生进行调整研究,面向实际,面向生产,向工人和工程技术人员学习的基本工作态度,工作作风和工作方法。
课题介绍
1.1、课题
车床主轴是车床的主要零件,它的头端装有夹具、工件或刀具,工作时要承受扭曲和弯矩,所以要求有足够的刚性、耐磨性和抗振性,并要求很高的回转精度。
所以主轴的加工质量对机床的工作精度和使用寿命有很大的影响。
其原始资料如下:
零件材料:
45钢
技术要求:
1、莫氏锥度及1:
12锥面用涂色法检查,接触率为大于等于70%。
2、莫氏6号锥孔对主轴端面的位移为+2。
3、用环规紧贴C面,环规端面与D端面的间隙为0.05~0.1。
4、花键不等分积累误差和键对定心直径中心的偏移为0.02。
生产批量:
中等批量
零件数据:
(见零件图)
图1 车床主轴零件图
1.2、设计要求
要求编制一个车床主轴零件的机械加工工艺规程,按照老师的设计,并编写设计说明书。
具体内容如下:
选择毛胚的制造方法,指定毛胚的技术要求。
拟定车床主轴的机械加工工艺过程。
合理选择各工序的定位定位基准。
确定各工序所用的加工设备。
确定刀具材料、类型和规定量具的种类。
确定一个加工表面的工序余量和总余量。
确定一个工序的切削用量。
确定工序尺寸,正确拟定工序技术要求。
计算一个工件的单件工时。
编写工艺文件。
编写设计说明书。
第二章 有关零件的分析
根据轴类零件的功用和工作条件,其技术要求主要在以下方面:
⑴尺寸精度 轴类零件的主要表面常为两类:
一类是与轴承的内圈配合的外圆轴颈,即支承轴颈,用于确定轴的位置并支承轴,尺寸精度要求较高,通常为IT5~IT7;另一类为与各类传动件配合的轴颈,即配合轴颈,其精度稍低,常为IT6~IT9。
⑵几何形状精度 主要指轴颈表面、外圆锥面、锥孔等重要表面的圆度、圆柱度。
其误差一般应限制在尺寸公差范围内,对于精密轴,需在零件图上另行规定其几何形状精度。
⑶相互位置精度 包括内、外表面、重要轴面的同轴度、圆的径向跳动、重要端面对轴心线的垂直度、端面间的平行度等。
⑷表面粗糙度 轴的加工表面都有粗糙度的要求,一般根据加工的可能性和经济性来确定。
支承轴颈常为0.2~1.6μm,传动件配合轴颈为0.4~3.2μm。
⑸其他 热处理及外观修饰等要求。
2.1、零件的结构特点
图1所示零件是车床的主轴,它属于台阶型轴类零件,由圆柱面、轴肩、螺纹、退刀槽和键槽等组成。
轴肩一般用来确定安装在轴上零件的轴向位置;键槽是便于安装键,以传递转矩;螺纹用于安装各种锁紧螺母和调整螺母。
从图1所示的车床主轴零件的支撑轴颈A、B是装配基准,故对A、B两段轴颈的加工提出了很高的要求。
主轴的支撑轴颈、配合轴颈、锥孔、前端圆锥面及端面、锁紧螺纹等表面是轴的主要加工表面。
其中支撑轴颈本身的尺寸精度、几何形状精度、相互位置精度和表面粗糙度尤为重要。
2.2、加工工艺性
次零件的技术要求不高,用车床、铣床和钻床就可以加工出来,精度要求一般是7到8级,而且表面粗糙度要求也不太高,是一个较好加工的零件。
2.3、确定零件毛胚
考虑到零件的经济性和综合性能要求,零件材料为45钢。
第三章 基准的选择
3.1、有关基准的选择说明
1、粗基准的选用原则
1、保证不加工表面与加工表面相互位置要求原则。
当有些不加工表面与加工表面之间有相互位置要求时,一般不选择加工表面作为粗基准。
2、保证各加工表面的加工余量合理分配的原则。
应选择重要加工表面为粗基准。
3、粗基准不重复使用的原则。
粗基准的精度低,粗糙度数值大,重复使用会造成较大的定位误差,因此,同一尺寸方向的粗基准,通常只允许使用一次。
2、精基准的选用原则
1、基准重合原则。
尽可能使设计基准和定位基准重合,以减少定位误差。
2、基准统一原则。
尽可能使用同一定位基准加工个表面,以保证各表面的位置精度。
如轴类零件常用两端顶尖孔作为统一的定位基准。
3、互为基准原则。
当两个加工表面间的位置精度要求比较高的时候,可用互为基准的原则反复加工。
4、自为基准的原则。
当要求加工余量小而均匀时,可选择加工表面作为自身的定位基准。
3.2、确定零件的定位基准
主轴加工中,为了保证各主要表面的相互位置精度,选择定位基准时,应遵循基准重合、基准统一和互为基准等重要原则,并能在一次装夹中尽可能加工出较多的表面。
由于主轴外圆表面的设计基准是主轴轴心线,根据基准重合的原则考虑应选择主轴两端的顶尖孔作为精基准面。
用顶尖孔定位,还能在一次装夹中将许多外圆表面及其端面加工出来,有利于保证加工面间的位置精度。
所以主轴在粗车之前应先加工顶尖孔。
为了保证支承轴颈与主轴内锥面的同轴度要求,宜按互为基准的原则选择基准面。
如车小端1∶20锥孔和大端莫氏6号内锥孔时,以与前支承轴颈相邻而它们又是用同一基准加工出来的外圆柱面为定位基准面(因支承轴颈系外锥面不便装夹);在精车各外圆(包括两个支承轴颈)时,以前、后锥孔内所配锥堵的顶尖孔为定位基面;在粗磨莫氏6号内锥孔时,又以两圆柱面为定位基准面;粗、精磨两个支承轴颈的1∶12锥面时,再次用锥堵顶尖孔定位;最后精磨莫氏6号锥孔时,直接以精磨后的前支承轴颈和另一圆柱面定位。
定位基准每转换一次,都使主轴的加工精度提高一步。
第四章 轴类零件的材料、毛坯及热处理
4.1、轴类零件的材料
常用45钢,精度较高的轴可选用40Cr、轴承钢GCr15、弹簧钢65Mn,也可选用球墨铸铁;对高速、重载的轴,选用20CrMnTi、20Mn2B、20Cr等低碳合金钢或38CrMoAl氮化钢。
4.2、轴类毛坯
常用圆棒料和锻件;大型轴或结构复杂的轴采用铸件。
毛坯经过加热锻造后,可使金属内部纤维组织沿表面均匀分布,获得较高的抗拉、抗弯及抗扭强度。
4.3、轴类零件的热处理
锻造毛坯在加工前,均需安排正火或退火处理,使钢材内部晶粒细化,消除锻造应力,降低材料硬度,改善切削加工性能。
调质一般安排在粗车之后、半精车之前,以获得良好的物理力学性能。
表面淬火一般安排在精加工之前,这样可以纠正因淬火引起的局部变形。
精度要求高的轴,在局部淬火或粗磨之后,还需进行低温时效处理。
第五章 制定加工工艺路线
拟订零件的加工路线是制定工艺规程的总体布局,主要任务是选择各表面的加工方法,及定位基准,确定加工顺序,各工序采用的机床设备和工艺装备等。
5.1主轴加工工艺过程分析
主轴加工工艺过程可划分为三个加工阶段,即粗加工阶段(包括铣端面、加工顶尖孔、粗车外圆等);半精加工阶段(半精车外圆,钻通孔,车锥面、锥孔,钻大头端面各孔,精车外圆等);精加工阶段(包括精铣键槽,粗、精磨外圆、锥面、锥孔等)。
在机械加工工序中间尚需插入必要的热处理工序,这就决定了主轴加工各主要表面总是循着以下顺序的进行,即粗车→调质(预备热处理)→半精车→精车→淬火-回火(最终热处理)→粗磨→精磨。
综上所述,主轴主要表面的加工顺序安排如下:
外圆表面粗加工(以顶尖孔定位)→外圆表面半精加工(以顶尖孔定位)→钻通孔(以半精加工过的外圆表面定位)→锥孔粗加工(以半精加工过的外圆表面定位,加工后配锥堵)→外圆表面精加工(以锥堵顶尖孔定位)→锥孔精加工(以精加工外圆面定位)。
当主要表面加工顺序确定后,就要合理地插入非主要表面加工工序。
对主轴来说非主要表面指的是螺孔、键槽、螺纹等。
这些表面加工一般不易出现废品,所以尽量安排在后面工序进行,主要表面加工一旦出了废品,非主要表面就不需加工了,这样可以避免浪费工时。
但这些表面也不能放在主要表面精加工后,以防在加工非主要表面过程中损伤已精加工过的
对凡是需要在淬硬表面上加工的螺孔、键槽等,都应安排在淬火前加工。
非淬硬表面上螺孔、键槽等一般在外圆精车之后,精磨之前进行加工。
主轴螺纹,因它与主轴支承轴颈之间有一定的同轴度要求,所以螺纹安排在以非淬火-回火为最终热处理工序之后的精加工阶段进行,这样半精加工后残余应力所引起的变形和热处理后的变形,就不会影响螺纹的加工精度。
5.2、工艺路线的拟定
为保证几何形状、尺寸精度、位置精度及各项技术要求,必须判定合理的工艺路线。
工艺路线方案一
序号
工序名称
工 序 内 容
定位基准
设 备
5
备 料
10
锻 造
磨 锻
立式精锻机
15
热处理
正 火
回火炉
20
锯
锯小端,保持总长为890+2.5mm
锯 床
25
铣端面打中心孔
车端面钻
=5mm的中心孔
小端外形
铣床、钻床
30
车
粗车各段外径,均放余量为2.5~3mm
大端外形及断面、小端中心孔
车 床
35
车
粗车D、E面及
165mm外圆,均放余量为2.5~3mm
小端外形,
115mm表面
车 床
40
车
粗车大端后断面及
115mm外圆与上边工序接平
大端外形,小端中心孔
车 床
45
钻
钻
45mm的导向孔
小端外形,
115mm表面
钻 床
50
钻
钻
45mm的通孔
小端外形,
115mm表面
深孔钻床
55
热处理
调质220~240HB
60
车
车小端面,内孔光出即可,长度不少于10mm
大端外形,
89表面
车 床
65
车
半精车各档外圆及1:
12锥面,均留0.5~0.6mm,螺纹外径留磨量0.2~0.3mm
大端外形,小端孔口
仿形车 床
70
车
半精车大端D、E面及莫氏锥孔半精车大端后断面,切割各槽
大端外形,小端孔口
车 床
75
钻
扩
48mm通孔
大端外形,
89表面
深孔钻床
80
热处理
按图要求对各部位进行热处理
85
车
半精车大端D、E面;车6号莫氏锥孔,精车端面
小端外形
车 床
90
磨
半精磨各档外圆,1:
12锥面,螺纹外圆,大端外圆及端面
用锥套心轴夹持找正
89mm、
115mm外圆,径向圆跳动不大于0.005mm
外圆磨床
95
铣
铣键槽12H9
80外圆
3#万能铣床
100
钻
大端面上各孔
D、E面
专用钻床
105
车
精车M74X1.5、M100X1.5、M115X1.5mm螺纹及大端面后端面
大端外圆,小端孔口找正
89mm、
115mm外圆,径向圆跳动小于0.005mm
车 床
110
磨
精磨各档外圆,D、E面及锥面
锥套找正
89mm、
115mm外圆,径向圆跳动小于0.005mm
外圆磨床
115
磨
精磨大端锥孔
89mm、
115mm外圆轴肩找正,径向跳动小于0.005mm
专用磨床
120
清 除
清洗去毛刺
125
检查
按图样技术要求项目检查
工艺路线方案二
序号
工序名称
工 序 内 容
定位基准
设 备
5
备 料
10
锻 造
磨 锻
立式精锻机
15
热处理
正 火
回火炉
20
锯
锯小端,保持总长为890+2.5mm
锯 床
25
铣端面打中心孔
车端面钻
=5mm的中心孔
小端外形
铣床、钻床
30
车
粗车各段外径,均放余量为2.5~3mm
大端外形及断面、小端中心孔
车 床
35
车
粗车D、E面及
165mm外圆,均放余量为2.5~3mm
小端外形,
115mm表面
车 床
40
车
粗车大端后断面及
115mm外圆与上边工序接平
大端外形,小端中心孔
车 床
45
车
车小端面,内孔光出即可,长度不少于10mm
大端外形,
89表面
车 床
50
车
半精车各档外圆及1:
12锥面,均留0.5~0.6mm,螺纹外径留磨量0.2~0.3mm
大端外形,小端孔口
仿形车床
55
车
半精车大端D、E面及莫氏锥孔
半精车大端后断面,切割各槽
大端外形,小端孔口
车 床
60
车
半精车大端D、E面;车6号莫氏锥孔,精车端面
小端外形
车 床
65
钻
钻
45mm的导向孔
小端外形,
115mm表面
钻 床
70
钻
钻
45mm的通孔
小端外形,
115mm表面
深孔钻床
75
热处理
调质220~240HB
80
钻
扩
48mm通孔
大端外形,
89表面
深孔钻床
85
热处理
按图要求对各部位进行热处理
90
磨
半精磨各档外圆,1:
12锥面,螺纹外圆,大端外圆及端面
用锥套心轴夹持找正
89mm、
115mm外圆,径向圆跳动不大于0.005mm
外圆磨床
95
铣
铣键槽12H9
80外圆
3#万能铣床
100
钻
大端面上各孔
D、E面
专用钻床
105
车
精车M74X1.5、M100X1.5、M115X1.5mm螺纹及大端面后端面
大端外圆,小端孔口找正
89mm、
115mm外圆,径向圆跳动小于0.005mm
车 床
110
磨
精磨各档外圆,D、E面及锥面
锥套找正
89mm、
115mm外圆,径向圆跳动小于0.005mm
外圆磨床
115
磨
精磨大端锥孔
89mm、
115mm外圆轴肩找正,径向跳动小于0.005mm
专用磨床
120
清 除
清洗去毛刺
125
检查
按图样技术要求项目检查
两个工艺路线的分析:
相比工艺路线方案一,工艺路线方案二采用先铣面,后钻孔的思路,符合工序集中和先面后孔的原则,但在加工右边圆柱上平面和左边圆柱下平面时不便于定位和装夹,且不符合基准先行的原则;而加工方案一不仅符合先面后孔的原则和基准先行原则,而且便于定位和装夹。
另外,选择方案时还应考虑工厂的具体条件等要素,如:
设备能否借用工、夹、量具等。
本次设计采用工艺路线一.
5.3、车床主轴机械加工工艺过程卡
序号
工序名称
工 序 内 容
定位基准
设 备
5
备 料
10
锻 造
磨 锻
立式精锻机
15
热处理
正 火
回火炉
20
锯
锯小端保持总长为890+2.5mm
保持总长为890+2.5mm
锯 床
25
铣端面打中心孔
车端面钻
=5mm的中心孔
小端外形
铣床、钻床
30
车
粗车各段外径,均放余量为2.5~3mm
大端外形及断面、小端中心孔
车 床
35
车
粗车D、E面及
165mm外圆,均放余量为2.5~3mm
小端外形,
115mm表面
车 床
40
车
粗车大端后断面及
115mm外圆与上边工序接平
大端外形,小端中心孔
车 床
45
钻
钻
45mm的导向孔
小端外形,
115mm表面
钻 床
50
钻
钻
45mm的通孔
小端外形,
115mm表面
深孔钻床
55
热处理
调质220~240HB
60
车
车小端面,内孔光出即可,长度不少于10mm
大端外形,
89表面
车 床
65
车
半精车各档外圆及1:
12锥面,均留0.5~0.6mm,螺纹外径留磨量0.2~0.3mm
大端外形,小端孔口
仿形车床
70
车
半精车大端D、E面及莫氏锥孔
半精车大端后断面,切割各槽
大端外形,小端孔口
车 床
75
钻
扩
48mm通孔
大端外形,
89表面
深孔钻床
80
热处理
按图要求对各部位进行热处理
85
车
半精车大端D、E面;车6号莫氏锥孔,精车端面
小端外形
车 床
90
磨
半精磨各档外圆,1:
12锥面,螺纹外圆,大端外圆及端面
用锥套心轴夹持找正
89mm、
115mm外圆,径向圆跳动不大于0.005mm
外圆磨床
95
铣
铣键槽12H9
80外圆
3#万能铣床
100
钻
钻大端面上各孔
D、E面
专用钻床
105
车
精车M74X1.5、M100X1.5、M115X1.5mm螺纹及大端面后端面
大端外圆,小端孔口找正
89mm、
115mm外圆,径向圆跳动小于0.005mm
车 床
110
磨
精磨各档外圆,D、E面及锥面
锥套找正
89mm、
115mm外圆,径向圆跳动小于0.005mm
外圆磨床
115
磨
精磨大端锥孔
89mm、
115mm外圆轴肩找正,径向跳动小于0.005mm
专用磨床
120
清 除
清洗去毛刺
125
检 查
按图样技术要求项目检查
5.4、加工余量的确定
工艺路线拟定以后,应确定每道工序的加工余量、工序尺寸及其公差。
工序尺寸是工件加工过程中,每个工序加工应保证的尺寸,工序尺寸允许的变动范围就是工序尺寸的公差。
工序尺寸的确定与加工余量有着密切的关系。
零件图上的尺寸和公差就是最终的加工工序尺寸和公差。
将此尺寸加上加工余量就是上一工序的工序尺寸。
第六章 轴类零件的检验
6.1、加工中的检验
自动测量装置,作为辅助装置安装在机床上。
这种检验方式能在不影响加工的情况下,根据测量结果,主动地控制机床的工作过程,如改变进给量,自动补偿刀具磨损,自动退刀、停车等,使之适应加工条件的变化,防止产生废品,故又称为主动检验。
主动检验属在线检测,即在设备运行,生产不停顿的情况下,根据信号处理的基本原理,掌握设备运行状况,对生产过程进行预测预报及必要调整。
在线检测在机械制造中的应用越来越广。
6.2、加工后的检验
单件小批生产中,尺寸精度一般用外径千分尺检验;大批大量生产时,常采用光滑极限量规检验,长度大而精度高的工件可用比较仪检验。
表面粗糙度可用粗糙度样板进行检验;要求较高时则用光学显微镜或轮廓仪检验。
圆度误差可用千分尺测出的工件同一截面内直径的最大差值之半来确定,也可用千分表借助V形铁来测量,若条件许可,可用圆度仪检验。
圆柱度误差通常用千分尺测出同一轴向剖面内最大与最小值之差的方法来确定。
主轴相互位置精度检验一般以轴两端顶尖孔或工艺锥堵上的顶尖孔为定位基准,在两支承轴颈上方分别用千分表测量。
总 结
时光飞逝,为期一年的机械制造实习课程设计已经接近尾声。
回首这段时间的实习过程,感慨万千。
使我从中学到了以前在课内根本就学不到的东西。
受益匪浅!
在这次设计过程中,使我真正的认识到自己的不足之处,以前上课没有学到的知识,在这次设计当中也涉及到了。
使我真正感受到了知识的重要性。
这次设计将我以前学过的机械制造工艺与装备、公差与配合、机械制图、工程材料与热处理工艺等知识很好的串联了起来,起到了穿针引线的作用,巩固了所学知识的作用。
在机械制造工艺课程设计中,首先是对工件机械加工工艺规程的制定,这样在加工工件就可以知道用什么机床加工,怎样加工,加工工艺装备及设备等,因此,工件机械加工工艺规程的制定是至关重要的。
在机械制造工艺课程设计中还用到了CAD制图和一些计算机软件,因为学的时间长了,因此在开始画图的时候有很多问题,而且不熟练,需参阅课本。
但不久就能熟练的画了。
CAD制图不管是现在,对以后工作也是有很大的帮助的。
因此,这次真正将以前所学的联系到实际应用中来了。
在这次机械制造工艺课程设计中,还有一个重要的就是关于专用夹具的设计,因为机床夹具的设计在学习的过程中只是作为理论知识讲的,并没有亲自设计过,因此,在开始的设计过程中,存在这样那样的问题,在师傅的细心指导下,我根据步骤一步一步的设计,画图,查阅各种关于专用夹具的设计资料,终于将它设计了出来,我感到很高兴,因为在这之中我学到了以前没有学到的知识,也懂得了很多东西,真正做到了理论联系实际。
在这次机械制造工艺课程设计中,我学到了很多知识,有一点更是重要,就是我能作为一个设计人员,设计一个零件,也因此,我了解了设计人员的思想,每一个零件,每件产品都是先设计出来,再加工的,因此,作为一个设计人员,在设计的过程中一点不能马虎,每个步骤都必须有理有据,不是凭空捏造的。
而且,各种标准都要严格按照国家标准和国际标准,查阅大量资料,而且设计一个零件,需要花好长时间。
亲自上阵后我才知道,做每件是都不是简简单单就能完成的,是要付出大量代价的。
因此,我们也要用心去体会每个设计者的心思,这样才能像他们一样设计出好的作品。