后制动支架铸造工艺设计.doc
《后制动支架铸造工艺设计.doc》由会员分享,可在线阅读,更多相关《后制动支架铸造工艺设计.doc(17页珍藏版)》请在冰豆网上搜索。
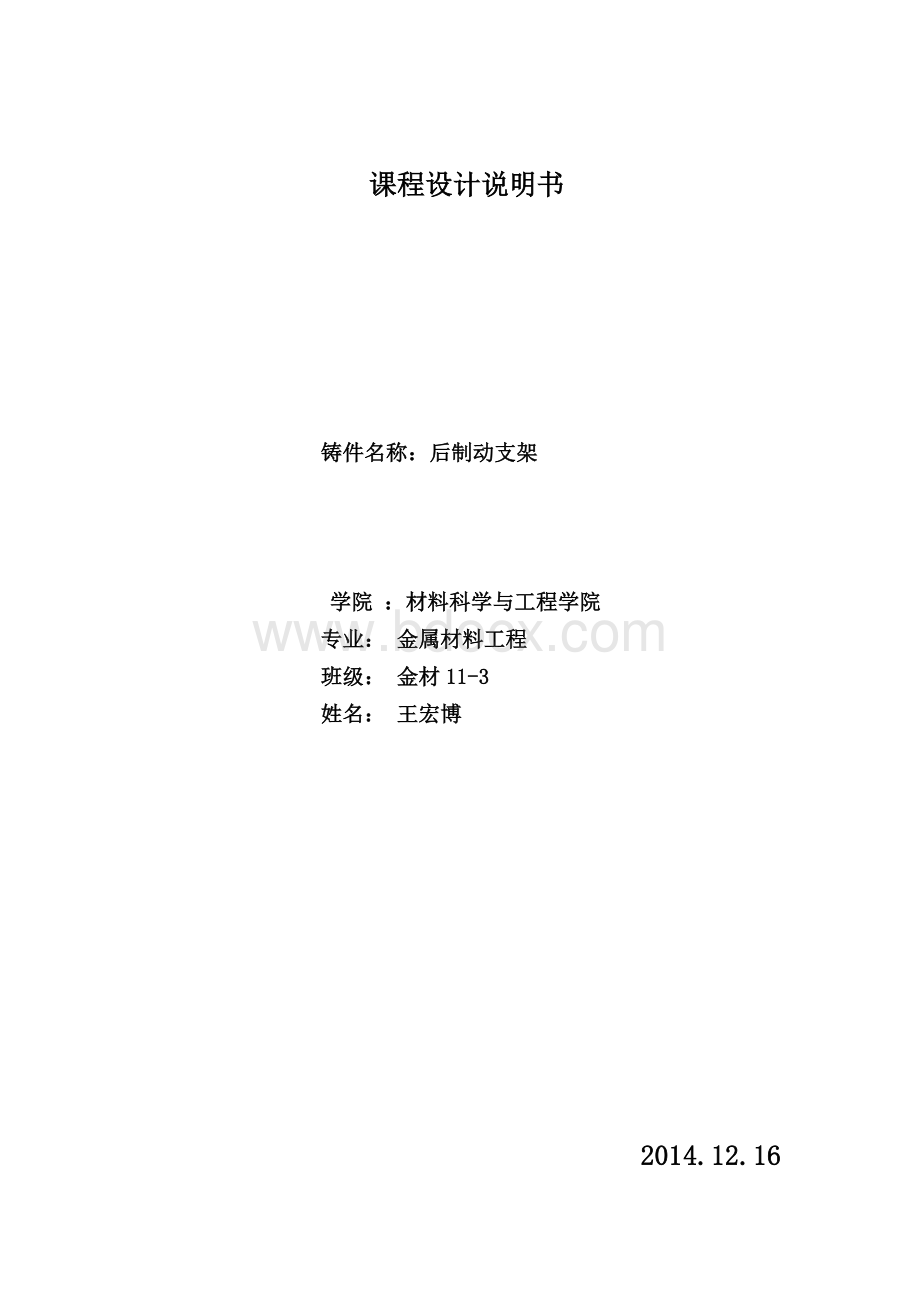
课程设计说明书
铸件名称:
后制动支架
学院:
材料科学与工程学院
专业:
金属材料工程
班级:
金材11-3
姓名:
王宏博
2014.12.16
设计说明书目录
一、零件铸造工艺要求和特点
1.1.零件的生产条件、结构及技术要求
1.2.零件的铸造工艺性
二、零件铸造工艺方案
2.1造型,造芯方法的选择
2.2浇注位置和分型面的确定
三、铸造工艺参数设计
3.1铸件尺寸公差
3.2机械加工余量
3.3最小铸出孔和槽
3.4拔模斜度
3.5铸造收缩率
3.6其他工艺参数设计
四、砂芯设计
4.1芯头的设计
4.2压环、防压环和集砂槽芯头结构
4.3芯骨设计
五.浇注系统设计
5.1浇注系统类型的选择
5.2浇注时间
5.3静压头的计算
5.4浇注系统各组元截面面积的计算
5.5直浇道窝的设计
5.6浇口杯的设计
5.7校核最小压力头
5.8.砂箱尺寸及造型机选择
六、模板模样设计绘制模板装配图
6.1.设计原则
6.2.模板模具设计
6.2.1选择模板类型、结构
6.2.2设计模底板、材料、结构尺寸及定位销,销耳尺寸
6.2.3设计金属模样结构及尺寸
6.2.4模样在底板上的装配,布置、紧固
6.2.5模底板、砂箱定位装置
6.2.6模底板的搬运结构
6.2.7模底板在造型机上的安装
6.2.8浇道在模底板上的装配
七、设计绘制芯盒装配图
7.1芯盒材料的选择
7.2芯盒内腔尺寸的确定
7.3芯盒的壁厚
7.4芯盒的边缘及防磨片
7.5芯盒的定位与夹紧
7.6金属芯盒的尺寸偏差
7.7芯盒的搬运
八、铸件缺陷分析与解决方案
九、参考文献
一、零件铸造工艺要求和特点
1.零件的生产条件、结构及技术要求
l零件名称:
后制动支架
l零件生产批量:
成批生产
l零件材质:
球铁(QT450-10)
l零件的外型示意图如图1所示,支架的零件图如图2所示,支座的外形轮廓尺寸为365mm280mm138mm,主要壁厚15mm,最小壁厚11mm,最大壁厚32mm,为一小型铸件;铸件除满足几何尺寸精度及材质方面的要求外,无其他特殊技术要求。
图1后制动支架外形示意图
图2后制动支架零件图
2.零件的铸造工艺性
零件结构的铸造工艺性是指零件的结构应符合铸造生产的要求,易于保证铸件品质,简化铸件工艺过程和降低成本。
审查、分析应考虑如下几个方面:
(1)铸件应有合适的壁厚,为了避免浇不到、冷隔等缺陷,铸件不应太薄。
(2)铸件结构不应造成严重的收缩阻碍,注意薄壁过渡和圆角铸件薄厚壁的相接拐弯等厚度的壁与壁的各种交接,都应采取逐渐过渡和转变的形式,并应使用较大的圆角相连接,避免因应力集中导致裂纹缺陷。
(3)壁厚力求均匀,减少肥厚部分,防止形成热节。
(4)利于补缩和实现顺序凝固。
(5)防止铸件翘曲变形。
(6)避免浇注位置上有水平的大平面结构。
对于零件的铸造工艺性审查、分析如下:
零件的轮廓尺寸为365mm280mm138mm。
砂型铸造条件下该轮廓尺寸的最小允许壁厚查《铸造工艺课程设计》表1-2得:
最小允许壁厚为4~5mm。
而设计零件的最小壁厚为11mm。
符合要求。
表1砂型铸造时铸件最小允许壁厚(mm)
合金种类
零件轮廓尺寸
最小允许壁厚
球铁
200~400
4~5
从零件的整体结果及尺寸看,该零件的壁厚相差并不是很大,而且在壁厚不一致处的过度属于平缓过度,能够满足铸造生产的要求,因此,该零件的结构满足铸造工艺性要求。
二、零件铸造工艺方案
1.造型,造芯方法的选择
零件的轮廓尺寸为365mm280mm138mm,铸件尺寸较小,属于中小型零件且要成批生产。
采用湿型粘土砂造型灵活性大,生产率高,生产周期短,便于组织流水生产,易于实现机械化和自动化,材料成本低,节省烘干设备、燃料、电力等,还可延长砂箱使用寿命。
因此,采用湿型粘土砂机器造型,模样采用金属模。
采用树脂砂手工制芯。
2.浇注位置和分型面的确定
铸件的浇注位置是指浇注时铸件在型内所处的状态和位置。
确定浇注位置是铸造工艺设计中重要的环节,关系到铸件的内在质量,铸件的尺寸精度及造型工艺过程的难易程度。
分型面是指两半铸型相互接触的表面。
分型面的优劣在很大程度上影响铸件的尺寸精度、成本和生产率。
(a)(b)(c)
图3零件分型面位置图
根据该零件的结构特点可以选择如图3所示的三种分型位置。
图3(a)为将零件轴线水平放置,图3(b)、(c)为将零件的轴线垂直放置。
将零件轴线水平放置,即砂芯水平放置,可以方便于下芯,同时能够使上、下砂箱的高度一致,但缺点是不能保证铸件圆周方向上质量均匀一致。
将零件的轴线垂直放置,即砂芯垂直放置,虽然会使铸件处于上、下砂箱的高度不同,但能够保证铸件圆周方向的质量均匀一致。
采用图3(b)的分型位置,铸件大部分位于上砂箱,而这种情况下,铸件的最薄壁厚位于铸件的顶部,容易引起浇不足缺陷,铸件的重要部分也没能全部置于下部,大平面朝上放置容易产生气孔、非金属夹杂物等缺陷。
。
采用图3(c)所示分型位置,铸件的大部分处于下砂箱,铸件的重要部分大部分置于下部,这样置于下部的重要部分可以得到上部金属的静压力作用下凝固并得到补缩,组织致密。
综合以上,采用图3(c)所示分型位置。
浇注位置在分型面上。
三、铸造工艺参数设计
铸造工艺设计参数通常是指铸型工艺设计时需要确定的某些数据,这些工艺数据一般都与模样及芯盒尺寸有关,及与铸件的精度有密切关系,同时也与造型、制芯、下芯及合箱的工艺过程有关。
这些工艺数据主要是指加工余量、起模斜度、铸造收缩率、最小铸出孔、型芯头尺寸、铸造圆角等。
工艺参数选取的准确、合适,才能保证铸件尺寸精确,使造型、制芯、下芯及合箱方便,提高生产率,降低成本。
3.1铸件尺寸公差
铸件尺寸公差是指铸件公称尺寸的两个允许的极限尺寸之差。
在两个允许极限尺寸之内,铸件可满足机械加工,装配,和使用要求。
零件为砂型铸造机器造型大批量生产,由《铸造工艺课程设计》查表2-2得:
铸件的尺寸公差为CT8~10级,取CT9级。
零件的轮廓尺寸为365mm280mm138mm,由《铸造工艺课程设计》查表2-1得:
铸件尺寸公差数值为3.2mm。
3.2机械加工余量
机械加工余量是铸件为了保证其加工面尺寸和零件精度,应有加工余量,即在铸件工艺设计时预先增加的,而后在机械加工时又被切去的金属层厚度。
零件为砂型铸造机器造型大批量生产,由《铸造工艺课程设计》查表2-9得:
铸件的加工余量G级。
零件的轮廓尺寸为365mm280mm138mm,由《铸造工艺课程设计》查表2-8得:
铸件加工余量数值为4.5~5.5mm,因采用机器造型,金属模板,芯盒,铸件尺寸精度高,故加工余量选小值4.5mm。
3.3最小铸出孔和槽
零件上的孔、槽、台阶等,究竟是铸出来好还是靠机械加工出来好,这应该从品质及经济角度等方面考虑。
一般来说,较大的孔、槽等应该铸出来,以便节约金属和加工工时,同时还可以避免铸件局部过厚所造成热节,提高铸件质量。
较小的孔、槽或则铸件壁很厚则不易铸出孔,直接依靠加工反而方便。
根据零件生产批量由《铸造工艺课程设计》查表2-16得:
最小铸出孔直径尺寸为15~30mm。
因此只需铸出直径较大的四个孔,其余孔无需铸出,机械加工较为经济方便。
3.4起模斜度
为了方便起模,在模样、芯盒的出模方向留有一定斜度,以免损坏砂型或砂芯。
这个斜度,称为起模斜度。
起模斜度应在铸件上没有结构斜度的,垂直于分型面的表面上应用。
设计采用金属模具,根据零件的结构及尺寸,采用“增加厚度法”设置拔模斜度,初步设计的起模斜度如下:
上模外型模的高29mm的起模斜度由《铸造工艺课程设计》查表2-11得:
粘土砂造型外表面起模斜度为а=1°10',a=0.8mm
下模外型模高109mm的起模斜度由《铸造工艺课程设计》查表2-11得:
粘土砂造型外表面起模斜度为а=0°25',a=1.2mm
但是同一铸件要尽量选用同一起模斜度,以免加工金属模时频繁的更换刀具。
所以选用同一起模斜度为а=1°10',a=0.8mm
表2铸孔起模斜度(mm)
铸孔直径
(mm)
铸孔高度
21~40
起模斜度a
≤30
8°
51~70
8°
3.5铸造收缩率
铸造收缩率又称铸件线收缩率,用模样与铸件的长度差除以模样长度的百分比表示:
K=[(L1-L2)/L1]*100%
K—铸造收缩率
L1—模样长度
L2—铸件长度
零件受阻收缩率由《铸造工艺课程设计》查表2-14得:
表3铸铁的铸造收缩率
铸铁种类
线收缩率(%)
阻碍收缩
自由收缩
球铁:
中小型铸件
0.8~1.0
0.9~1.1
受阻收缩率为0.9%。
3.6其他工艺参数的设计
本课程设计所进行的球铁后制动支架铸造工艺设计,由于属于大批量生产,因此,经过工艺优化之后,无需进行如“分型负数”、“分型负数”“反变形量”等工艺参数的设计
四、砂芯设计
砂芯的功用是形成铸件的内腔、孔和铸件外型不能出砂的部分。
砂型局部要求特殊性能的部分有时也用砂芯。
后制动支架需两种砂芯,共计两个,采用树脂砂手工制芯。
4.1芯头的设计
砂芯主要靠芯头固定在砂型上。
对于垂直芯头为了保证其轴线垂直、牢固地固定在砂型上,必须有足够的芯头尺寸。
表4垂直型芯头的高度和芯头与芯座的配合间隙(JB/T5106-91)(mm)
L
砂型类别
D或
≤25
>40~63
s
h
s
h
>100~160
湿型
0.2
20~25
≤100
湿型
0.3
25~30
第一种砂芯:
根据实际设计量取计算砂芯高度:
L=147mm
砂芯直径:
D=23mm
芯头长度由《铸造工艺课程设计》查表3-1得:
S=0.5mm,h=20~25mm取h=25mm
第二种砂芯:
根据实际设计量取计算砂芯高度:
L=54mm
砂芯直径:
D=51mm
芯头长度由《铸造工艺课程设计》查表3-1得:
S=0.5mm,h=25~30mm取h=30mm
表5垂直型芯头的斜度(JB/T5106-91)(mm)
表6垂直型芯头顶面与芯座的配合间隙(JB/T5106-92)(mm)
4.2压环、防压环和集砂槽芯头结构
在湿型大批量生产中,为了加速下芯、合芯及保证铸件质量,在芯头的模样上常常做出压环、防压环和集砂槽。
表7压环、防压环和集砂槽尺寸(mm)
第一种砂芯:
压环、防压环和集砂槽尺寸由《砂型铸造工艺设计》查表4-7得:
e=1.5mmf=3mmr=1.6mm
第二种砂芯:
压环、防压环和集砂槽尺寸由《砂型铸造工艺设计》查表4-7得:
e=2mmf=3mmr=2mm
4.3芯骨设计
为了保证砂芯在制芯、搬运、配芯和浇注过程中不开裂、不变形、不被金属液冲击折断,生产中通常在砂芯中埋置芯骨,以提高其刚度和强度。
因为砂芯尺寸较小,而且采用树脂砂,故砂芯强度较好,砂芯内不用放置芯骨。
五、浇注系统设计
浇注系统是铸型中引导液体金属进入型腔的通道,它由浇口杯、直浇道、横浇道和内浇道组成。
5.1浇注系统类型的选择
由于该铸件材质为球铁,要求浇注系统撇渣能力较强,铁水充型平稳,所以选择半封闭式浇注