拉伸模的一小常识.docx
《拉伸模的一小常识.docx》由会员分享,可在线阅读,更多相关《拉伸模的一小常识.docx(9页珍藏版)》请在冰豆网上搜索。
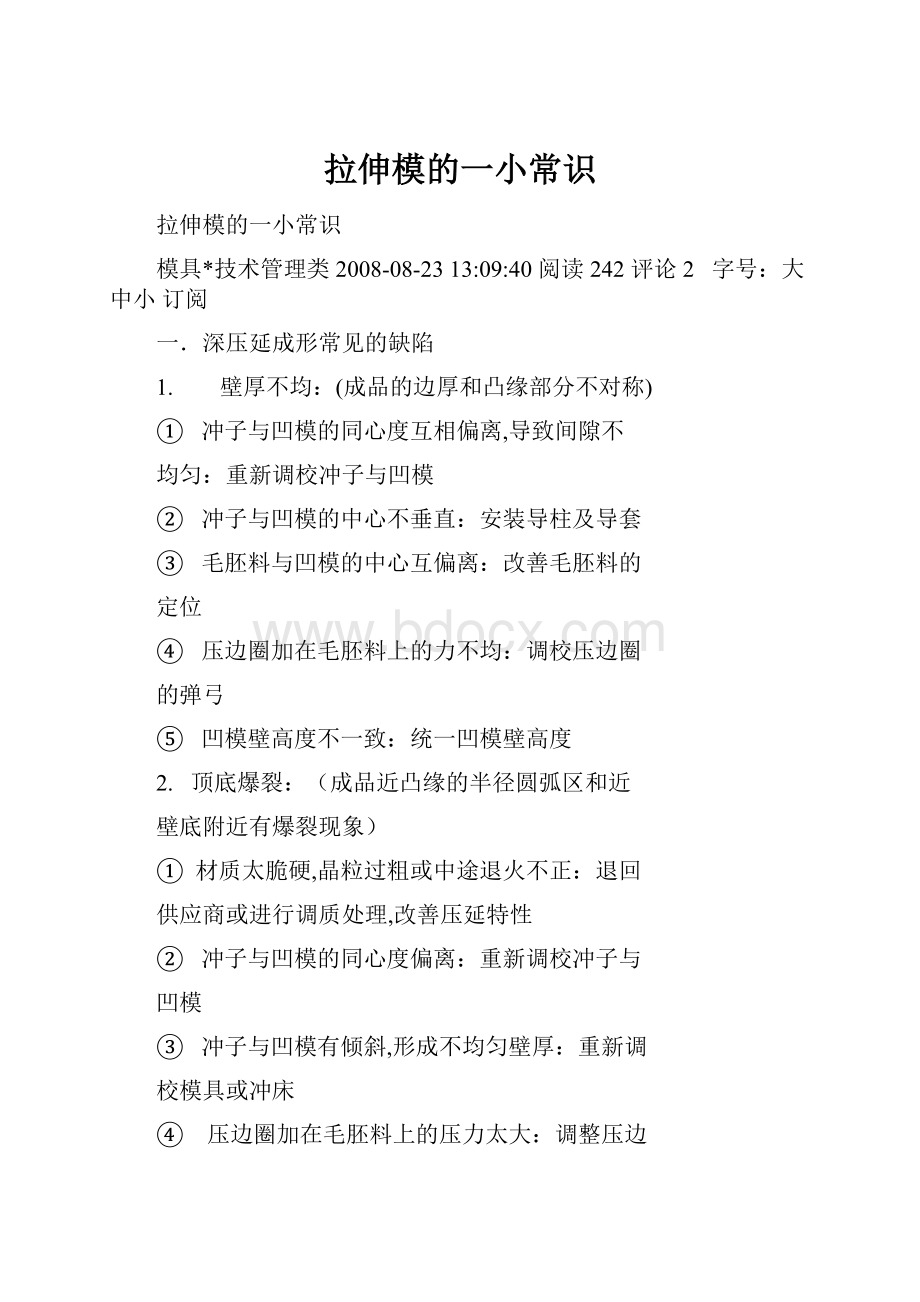
拉伸模的一小常识
拉伸模的一小常识
模具*技术管理类2008-08-2313:
09:
40阅读242评论2 字号:
大中小 订阅
一.深压延成形常见的缺陷
1. 壁厚不均:
(成品的边厚和凸缘部分不对称)
① 冲子与凹模的同心度互相偏离,导致间隙不
均匀:
重新调校冲子与凹模
② 冲子与凹模的中心不垂直:
安装导柱及导套
③ 毛胚料与凹模的中心互偏离:
改善毛胚料的
定位
④ 压边圈加在毛胚料上的力不均:
调校压边圈
的弹弓
⑤ 凹模壁高度不一致:
统一凹模壁高度
2. 顶底爆裂:
(成品近凸缘的半径圆弧区和近
壁底附近有爆裂现象)
① 材质太脆硬,晶粒过粗或中途退火不正:
退回
供应商或进行调质处理,改善压延特性
② 冲子与凹模的同心度偏离:
重新调校冲子与
凹模
③ 冲子与凹模有倾斜,形成不均匀壁厚:
重新调
校模具或冲床
④ 压边圈加在毛胚料上的压力太大:
调整压边
圈的压力
⑤ 冲子与凹模的间隙不够:
改善冲子与凹模的
间隙
⑥ 凹模模肩圆弧半径太小:
加大模肩圆弧半径
3. 桶状皱摺:
(成品近壁顶部产生群摺现象)
① 毛胚厚度不够:
计算改善冲子与凹模的间隙
毛胚料尺寸
② 毛胚料尺寸过小,其凸缘面积不足,发挥不到
压边效果:
重新设计毛胚料尺寸
③ 成品高度小于图纸高度和开口部分有波浪
形状皱摺,成因是冲子与凹模的间隙太大:
改善冲子与凹模的间隙(缩小)
④ 成品高度过高与图纸高度,成因是冲子与凹
模的间隙偏小:
改善冲子与凹模的间隙(加
大)
⑤ 压边力太大和凹模模肩圆弧半径太小:
改善
加大圆弧半径,调校压边力
⑥ 压边力不足和凹模模肩圆弧半径太大:
修细模肩
的圆弧半径,调校压边力
4. 抓痕:
(成品外壁有线性直纹现象)
① 愿材料表面已有伤痕:
更换材料
② 原材料表面附有尘埃杂物污垢:
更换材料或
使用软布及清洁剂除去表面污垢
③ 因润滑剂不洁:
选择清洁或经过滤之润滑剂
④ 模具受损,尤以凹模模口圆弧半径范围:
应估
计模具的寿命,要设定某生产数量后,模具应
要重新抛光
5. 状压痕(成品在壁身面上有多个环状形压痕)
① 冲子与凹模不同心:
重新调校冲子与凹模
② 帽子形的半成品不能稳定安放在下模上,造成
倾斜:
可考虑冲子在下,凹模在上,令帽子形
的半成品套在冲子上
③ 退火程序不正确使机械性能不均匀:
退回供应
商或进行调质处理,改善压延特性
④ 在薄化压延中因壁厚不均匀:
毛胚料和模具的
润滑不平均
⑤ 薄化系数太小(程度大):
调节冲子直径(缩
小)
⑥ 冲子前端的圆弧半径和凹模模肩圆弧半径偏
小:
圆弧半径不可小于材料许可的最小圆弧半径
值
6. 橙皮纹:
(成品外壁有如橙皮状纹的不良现象)
① 原材料的性质偏向韧性:
更换材料
② 原材料的晶粒偏大或表面被腐蚀:
更换材料或
进行调质处理
③ 压延深度偏高:
可加道次令压延深度渐次增加
7. 烧边(成品外壁局部有明显的直线状纹)
① 冲子与凹模的间隙不够:
改善冲子与凹模的间
隙
② 凹模模肩圆弧半径太小:
改善加大圆弧半径,
加凸米
8. 耳缘(成品上端有明显的高低不平和厚薄不均现
状)
① 毛胚料安放不对中:
加适当管位
② 冲子与凹模的同心度偏离:
重新调校冲子与凹
模
③ 原材料和模具的润滑剂不平均:
改善润滑方法
如送料系统上令片料通过油毡,以求获得均匀的
润滑剂
④ 材料的晶粒方向性,常见于非原型产品:
可预
留材料供最后修正
二.润滑油与模具和片材的影响
深压延加工成形时,材料与工具接触面之摩擦现象是一种复杂问题,润滑的最大目的是减低片材压
料板与凹模面之间的摩擦力,有助散去加工热
量,增加模具寿命,而增加压延界限比则是主要目标。
润滑剂应符合以下要求:
① 润滑剂需有一定附著力,即粘度高,易在片材和
工具间形成强的薄膜层,此特别有利于不锈钢片
材在深压延中的表现
② 滑剂主要涂在冲子和材料之间,避免下模与片材
间的摩擦力不足够而产生滑落的失控现象
③ 不能对工具和材料有化学(腐蚀)反应
④ 容易清理,甚至不用清洗
⑤ 深压延中应用的润滑剂多含有滑石及硫的成分
以强化薄膜层
三.压料力的作用
在压延过程中,压料力是利用压料板上的压边圈施加作用力与成品胚料上,其功能是主要提供压边力来抑制毛胚料进入凹模的流量,以下为压边力对产品质量的影响:
① 压边力过大时,毛胚不容易压延进入下模,而令
底部圆弧角处被拉裂
② 压边不足时,其凸缘边区直径因受压缩作用而向
内缩小,这压缩应力足令边区直径产生皱纹,而
这皱纹亦阻止了毛胚进入凹模,而令底部圆弧转
角处被拉裂
③ 压料板冲子毛胚材料与下模间在工作时会产
生摩擦力,同样是摩擦力,过大时抑制毛胚的流
动量,若减低压料板力时会产生皱纹,所以摩擦
力的减少也得与压料板相互配合的
④ 适当抑皱压边力的范围,跟成形深度,冲子端
半径,凹模角半径,润滑油,表面光洁度,材料,
板厚等条件变化有关
四.变薄拉深
变薄拉深与一般拉深不同,变薄拉深时工件直径变化很小,虽然工件底部厚度与一般拉深相似,但工件侧面壁厚故意变薄,工件高度相应增加。
变薄拉深的方法主要用来制造厚底薄壁,而高度很大的圆筒形零件,或用来制造壁很薄的管胚。
经常采用变薄拉深工艺的工件材料有:
铜白铜黄铜磷青铜德银铝铝合金软钢不锈钢可伐合金等。
(一)变薄拉深特点:
1. 工件材料变形较大,金属晶粒细密,强度增加
2. 变薄拉深工件的表面粗糙度数值低,可达
Ra0.4μm以内
3. 壁厚偏差可在±0.01以内,上下均匀一致
4. 没有起皱问题,不需压料装置
5. 残余应力较大,需低温回火消除,以免储存时自行
开裂
(二)凹模结构
1. 凹模的锥角:
a=7°~10°,a过大,
变形困难。
a1=2a
2. 工作带高度h不宜太大,太大增加
摩擦阻力太小则易磨损:
D <10 10~20 20~30 30~50 >50
h 0.9 1 1.5~2 2.5~3 3~4
(三)凸模结构
1. 为方便脱模,取凸模的斜度β=1°
2. 凸模工作部分长度L大于工件长度(加工
修边留量)
3. 凸模出气孔直径D=(1/3~1/6)d
五.拉深废品分析
(一)退火与酸洗
拉深过程中材料发生硬化,当材料硬化至不能进行下一道拉深时,需要退火软化(一般采用低温退火),为了去除材料退火产生的氧化皮,需要酸洗净化。
酸洗前先用苏打水去油,酸洗后用冷水冲洗,以温度为60℃~80℃弱碱溶液中和酸性并用热水洗涤。
(二)深废品形式产生原因和解决措施
1. 开裂或脱底
① 材料太薄:
选用合格厚度的材料
② 材料硬度金相组织或质量不符要求:
退火或更
换材料
③ 带铁屑等微粒或已受伤:
保持材料表面完好清
洁
④ 凹模或压料圈工作表面不清洁:
磨光工作表面
⑤ 凹模或凸模圆角太小:
加大圆角
⑥ 间隙太小:
放大间隙
⑦ 间隙不匀:
调整间隙
⑧ 压料力过大:
调整压料力
⑨ 拉深系数过小:
增加工序,放大拉深系数
⑩ 润滑不足或不合格:
用合适的润滑剂充分润滑?
上道拉深工序件太短或本道拉深太深,以至上道工
序件的凸缘重被拉入凹模:
合理调整上下道拉深工
序的参数和模具结构
2. 起皱
① 凸缘起皱,主要因压料力太小,增加压料力使皱纹消失;倾侧的卸料板是连续拉深起皱的一个原因,防止连续
拉深起皱的另一个办法是首次拉深的压料板单独分开
② 上口起皱(无凸缘)是因凹模圆角过大,间隙也过大。
最后变形的材料未被压住,形成的少量皱纹因间隙过
大而不能整平:
减小凹模圆角和间隙,也可采用弧形
压料圈,压住凹模圆角处的材料
③ 上口或凸缘单面起皱,是压料力单面的结果造成压料
力单面的原因有:
压料圈和凹模不平行坯料毛刺坯
料表面有微粒杂物等:
调整压料圈和凹模的平行度
去除坯料毛刺消除坯料表面杂物
④ 锥形件或半球形件等腰部起皱,是因压料力太小拉深
开始时大部分材料处于悬空状态:
加大压料力,采用
压料筋或更改工艺,以液压拉深代替
3. 无凸缘拉深件高度不匀或凸缘拉深件凸缘宽度不匀
① 坯料放置单面:
调整定位
② 模具间隙不匀:
调整间隙
③ 凹模圆角不匀:
修正圆角
④ 坯料厚度不匀:
更换材料
⑤ 压料力单面
4. 拉深件底部附近严重变薄或局部变薄
① 材料质量不好:
更换材料
② 材料太厚:
改用厚度符合规格的材料
③ 凸模圆角与侧面未接好:
修磨凸模
④ 间隙太小:
⑤ 凹模圆角太小:
放大圆角
⑥ 拉深系数太小:
合理调整各道工序的拉深系数或增
加工序
⑦ 润滑不合格:
用合适的润滑剂充分润滑
5. 拉深件上口材料拥挤
① 材料过厚或间隙过小,工件侧壁拉薄,使过多材料
挤入上口:
改用厚度符合规格的材料或放大间隙
② 再拉深凸模圆角大于工序件底部圆角,使材料沿侧
面上升:
减少凸模圆角
③ 工序件太长或再拉深凸模太短,以致坯料侧壁未全
部拉入凹模:
合理调整上下道拉深工序的参数和模
具结构
6. 拉深件表面拉毛
① 凹模工作表面不光滑:
修光工作表面
② 坯料表面不清洁:
清洁坯料
③ 模具硬度低,有金属粘附现象:
提高模具硬度或改
变模具材料
④ 润滑剂有杂物混入:
改用干净的润滑剂
7. 拉深件外形不平整
① 原材料不平:
改用平整材料
② 材料弹性回跳:
加整形工序
③ 间隙太大:
减小间隙
④ 拉深变形程度过大:
调整有关部门工序变形量
⑤ 凸模无出气孔:
增加气孔。