IATF16949钣金件产品生产过程全流程控制计划.docx
《IATF16949钣金件产品生产过程全流程控制计划.docx》由会员分享,可在线阅读,更多相关《IATF16949钣金件产品生产过程全流程控制计划.docx(123页珍藏版)》请在冰豆网上搜索。
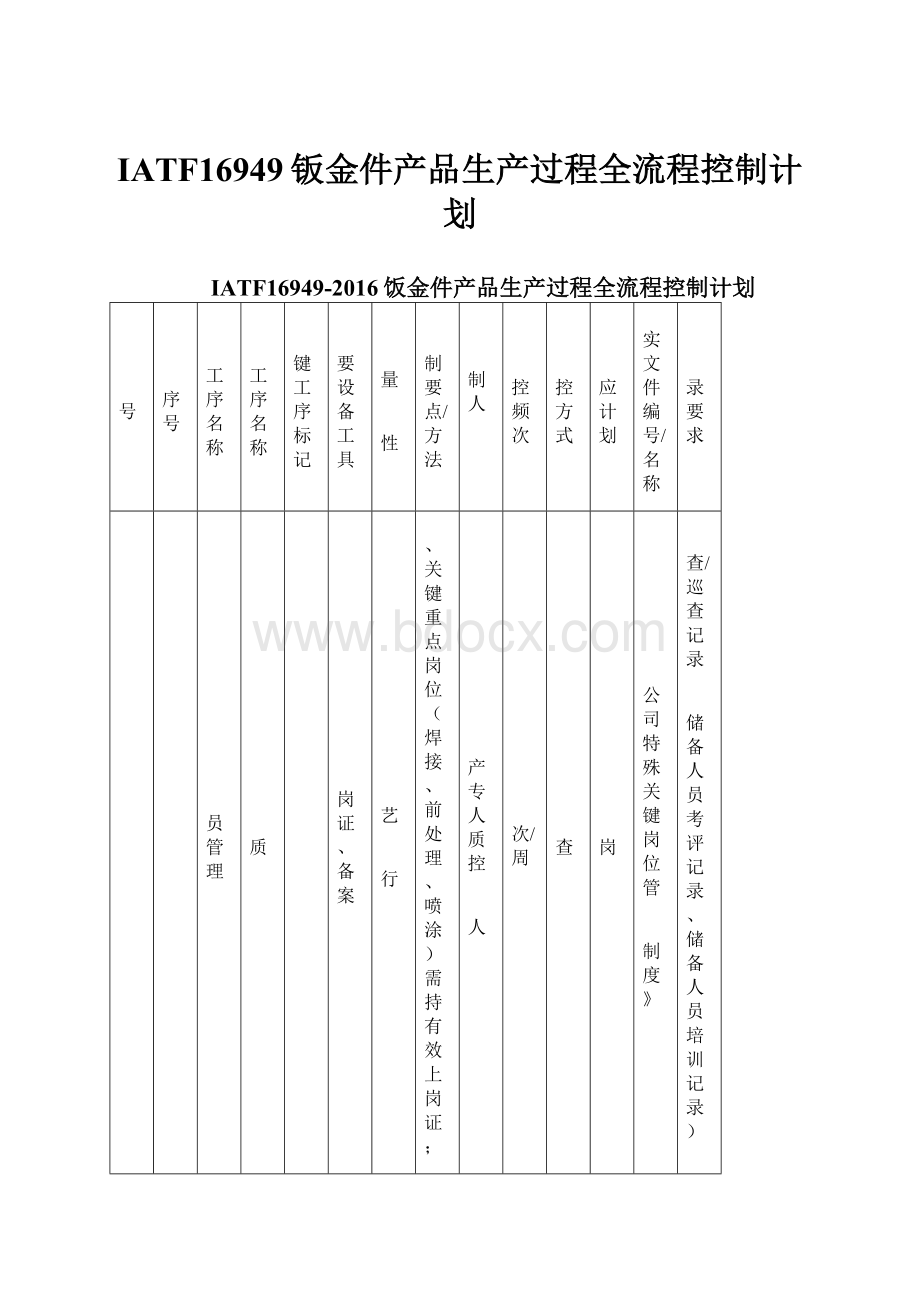
IATF16949钣金件产品生产过程全流程控制计划
IATF16949-2016饭金件产品生产过程全流程控制计划
序号
工序号
总工序名称
子工序名称
关键工序标记
主要设备工具
质量
特性
控制要点/方法
控制人
员
监控频次
监控方式
反应计划
落实文件编号/名称
记录要求
1
1
人员管理
资质
/
上岗证、备案
工艺
执行
1、关键重点岗位(焊接、前处理、喷涂)需持有效上岗证;
2、对焊接、检验操作人员,有工作经验、操作技能等特殊要求,需进行内部备案,否则不予以上岗。
生产专人质控
专人
1次/周
巡查
停岗
《公司特殊关键岗位管
理制度》
抽查/巡查记录
(储备人员考评记录、储备人员培训记录)
2
2
技能
/
/
/
1、掌握相关岗位所需的理论知识和质量知识;2、
熟练使用相关岗位所需的实际操作能力。
生产专人质控专人
1次/周
抽查
停岗
3
3
新员工
/
袖章
/
1、新员工必须经过岗前培训;
2、新员工实习期间1个月内必须佩带新员工袖章,三天内不能独立上岗操作,考评合格后可独立上岗;
生产专人质控专人
1次/周
巡查
停岗
4
4
原材料
(入库、仓储、出
库)
领料
/
目视
错混料
领用原材料钢板、螺栓、螺母等按计划单对所需材料批次、物料编码、数晕:
等信息进行记录并核对。
领料员
每次领料
自检
纠正、停岗培训
/
领料单
5
仓储
/
目视
仓储要求:
1、区域标识消晰、醒目;
2、同一个叉板上只能摆放同一种物料编码(状态相符);
3、板或笼应该有唯一的物料标识,且标识清晰、完整;
生产专人质控专人
1次/周
抽查
巡查记录表
6
定期盘点并记录。
仓管员
1次/月
自检
盘点记录表
7
出库
/
目视
1、依据饭金件计划单从从仓库领料;
2、对原材料进行核对(物料编码、订单号、银金件厂家、操作日期等信息记录);
仓管员
每次领料
自检
出库记录表、粉末
(前处理液)使用记录表
5
8
物料管控
生产过程现场物料管理
/
目视
错混
料
生产现场物料严格执行“三定”(定置、定量、定容)及6S(整理、整顿、安全、素养、清洁、清扫)管理,生产过程工序间物料确保一物一标识,对于旧标识要及时清理,不允许叠加方式打标识,半成品及成品、相似易误用物料应有效隔离及醒目标识,不合格物料、待处理物料必须有明确醒目的物料标识进行区分和有效隔离,储存运输物料的摆放严格按工艺要求执行。
班组长
每班一次
自检
纠正、停岗培训
/
/
6
9
仓储状况
/
目视
错混
料
1、各原材料是否按要求区分摆放;
2、每板或每个周转器具应有唯一的物料标识,且标识清晰、完整;
3、粉末、前处理液仓储符合要求。
生产专人质控专人
1次/周
专检
纠正、停岗培训
/
巡查记录表
7
10
成品仓储
/
目视
错混
料
1、应有清晰、醒目的区域标识,同种物料需摆放在同一区域;2、
摆放高度应符合产品摆放规范要求;
3、产品按仓库内的区域放置,周转器具或工装车不能压超黄色斑马线。
仓管员
全检
自检
封存/纠正
/
/
8
11
成品出库
出库
/
目视
错混
料
1、发货遵循先入先出的原则,避免银金件长时间储存导致生锈、积尘;
2、物料标识包含产品型号、数量、物料编码等信息;
3、己封存(贴红票)产品严禁发货;
4、发往总装同一生产线的物料放在同一发货区(包含产品型号、数量、物料编码等信息);
仓管员
全检
自检
纠正、停岗培训
/
/
9
12
生产设备管理
设备维护保养
/
设备
尺寸、
外观
1、每台生产设备上应有设备的铭牌标识;
2、应在每台生产设备上挂标识牌,标明设备保养责任人和监督人;
设备专
人
1次/周
专检
纠正、停用
《工装设备保养制度》
《设备运转台时记录表》、《设备操作交接班记录表》、《空调银金分厂设备日常点检表》
13
设备点检
应按照周期要求对生产设备进行点检。
生产专
人
开机前
自检
纠正
10
14
不合格品管控
不合格品判定
/
卷尺、游标卡尺
判定错误
严格依据图纸和检验标准要求执行。
生产专人质控
专人
自检
自检
纠正
《镀锌饭金件检验标准》、《镀锌板喷塑件检验标准》
11
15
不合格品隔离
标识不清
车间员工或巡检员在生产和检验过程中发现不合格品时,第一时间对不合格品用红色标签进行封存,标签注明不合格原因;
生产专人质控专人
自检
自检
纠正
《不合格零部件处置管
理规定》
12
16
不合格品处理
不合格品流入下道工序
班长或指定人员负责跟进处理不合格品,原则上要求不合格品在24小时内处理完毕。
生产专人质控
专人
每班一次
巡查
纠正、停岗培训
《不合格品调换单》
13
17
不合格品解除封存
不合格品流入下道工序
返修处理好的不合格品,要根据品管部巡检或工艺员的处理意见办理代用手续,报品管部巡检或技术部工艺人员签字确认;对于返修后仍无法达到要求的产品进行报废处理,填写好《报废品登记表》并将报废品拉到报废区由分厂制定人员进行接收。
生产专人质控
专人
每班一次
巡查
纠正、停岗培训
《报废品登记表》
14
18
不合格品报废
混料
分厂根据根据填写的《报废品登记表》,对相关的责任班组、工序或个人进行考评;分厂接收报废涂料后,由分厂接收的退料进行分类,分为分厂生产过程责任及原料厂家责任,最后分厂退料员按公司正常程序退料处理。
生产专人质控
专人
每班一次
巡查
纠正
《报废品登记表》
15
19
监督检查
/
/
目视
产品性能
1、检查各物料标识、记录是否按要求填写;
2、检查各物料摆放需符合《冷冲压工艺规程》或《银金及喷涂件摆放
(堆)放和包装工艺要求》;
3、各操作岗位是否按要求佩戴上岗证;
4、模具装配机床是否符合工艺吨位;
5、检查首检、抽检是否按要求正常
操作;6、
检查各设备参数是否符合工艺要求;
7、抽查各岗位应知应会是否己宣贯到位。
生产专人质控专人
2次/周
巡查
纠正、停岗培训
《冷冲压工艺规程》、
《饭金及喷涂件摆放
(堆)放和包装工艺要求》
稽查监督检查表
16
20
生产计划下发
/
/
ERP系统、生产日报表
生产
计划组根据生产制造部下发的总计划任务,下发生产计划单(班组、生产订单号、物料编码、物料名称、数量等信息)。
分厂计划组
每班次
自检
纠正
/
《生产计划单》
17
21
领料
/
/
ERP系统、生产日报表
用错
料
依据计划单进行领料作业,主要核对:
材料厚度、物料编码。
领料员
每次领料
自检
退料
重领
/
《生产计划单》
18
22
下料
分条
/
分条机、卷尺
尺寸、
外观
1、需持有该岗位的上岗证才能安排操作设备;2、
检查操作台按钮开关是否完整、灵活、可靠,工作正常;
3、操作人员要按保养要求对设备进行保养,并记录在交接班记录本上;
4、操作时需将内村纸取出,料头或料尾经检测符合使用要求后可改剪其他坯料,不良部分需切除报废;
5、分条时材料表面不能出现划伤,切口处毛刺CO.1mm,如超出需立即调整间隙或更换刀具;
6、分条时应依据条料表面油污情况,适当增加除油布进行擦拭;
7、分条料需符合生产计划(工艺)的下料尺寸,需核对分条尺寸是否公差带要求;分条方式及所用卷料按《钥金定额计算平台》执行;
8、分条后按要求在标识上填写分条后钢卷厚度、主要用途及生产班组等信息;
9、停机需按关闭急停,电源开关关
分条员
每卷分条
自检
纠正
《数控板料开卷校平剪切操作规程》、《设备保养作业指导书》
《设备运转台时记录表》、《设备操作交接班记录表》、《空调银金分厂设备日常点检表》
闭,停电源开关,关闭气源的顺序执行:
10、设备需悬挂责任人、操作人、监督人标识牌。
23
剪饭
/
剪板机、卷尺
错混料、尺寸
1、依据计划单进行领分条作业;
2、领取的分条料标识清洗清晰、可辨,与生产计划单信息一致;
3、需持有该岗位的上岗证才能安排
操作设备;4、
材料表面不允许有氧化、变形、生锈等不良现象;
5、开机前应将上、下刀片进行对刀,并调整好挡料装置,经空转二三次,一切正常后,方可开始工作;
6、剪切不同厚度和不同材质板料时,压板弹簧的压力及刀片间隙要调整适当,防止弹崩或损伤刃口(刀片间的间隙不得大于板料厚度的1/30);
7、严禁从机床后面送料加工;
8、开料尺寸符合工艺要求,尺寸公差按工艺标注公差执行,没有标注公差的,按GB/T15055-M级执行;坯料的对角线误差如果没有明确规定按下列要求控制:
坯块长、宽尺寸W200mm的,对角线相互误差^0.8mm;坯块长、宽尺寸在200〜600mm范围内的,对角线相互误差<1.5mm;坯块长、宽尺寸在600mm以上的,对角线相互误差<2.0mmo
剪饭员
每卷剪
饭
自检
纠正
《钢板下料工艺文件》、
《剪板机操作、保养作业指导书》
《设备运转台时记录表》、《设备操作交接班记录表》、《空调银金分厂设备日常点检表》
9、停机时需保证模具处于闭合状态再关闭电源开关;
10、设备需要悬挂贵任人、操作人、监督人标识牌;
11、物料标识包含但不限于:
零件名称、数量、尺寸大小、生产班次。
19
24
生产班组分解计划
/
/
/
1、按生产计划单由生产小组长领取取当天所需生产制件工艺文件,下班后归还;
2、依据生产计划单开领料单、调模单;
班组长
每班次
自检
纠正
/
/
20
25
转运物料
/
/
叉车
1、叉车人员根据班组长下发的领料单、调模单将材料与模具运至下料区领取对应机床,领取物料、模具时需核对标识需与领料单、调模单一致,核对是否有制定钢卷厂家;
2、叉车在车间内速度不得超过15km/h;
叉车工
每次操
作
自检
纠正
/
/
21
26
冲压作业
装模
/
扳手
/
1、装模时需依据模具铭牌和工艺指导书等综合因素核对机床、吨位是否符合要求,不符合工艺要求不允许安排装模;
2、调模作业需要按照模具闭合高度和设备吨位综合因素进行调整;
3、检查各压力表压力,平衡气压保持在4-6kg/cm2,离合器气压保持在5kg/cm2,超负荷气压保持在
3.5kg/cm2;
4、为保护设备及模具,不管是拉伸还是冲裁模具,所用吨位必须在设
调模工
每次换模/换产品/换程
序
自检
纠正
《钥金冲床作业指导书》、《自动冲压线冲床安全作业
指导书》
《设备运转台时记录表》、《设备操作交接班记录表》、《空调银金分厂设备日常点检表》
备额定公差能力范围内,并留有足够余量,严禁设备超负荷使用。
设备使用负荷比例范围应该按以下执行:
连续模60%-70%(大偏载往60%靠拢,小偏载可放宽如70%靠拢);单冲模70%-75%(大偏载往70%靠拢,小偏载可放宽入75%靠拢),超出此范围的模具不得保用。
5、装模或清扫模腔等作业需双手进入上下模空间的,必须从机床侧取下安全枕木放置于该空间内后方可进行。
27
银金冲压
/
冲床、
模具
尺寸、
外观
1、依据生产计划单进行领料,领料时标识清晰、可辨,与生产订单信息、实物一致;
2、核对模具、钢卷规格型号是否与生产计划单备注的一致(坯料主要核对板料厚度、长宽尺寸;半工序来料需主要核对上道工序半成品尺寸和外观是否符合图纸或工艺文件要求;
冲压工
每次换模/换状态
自检
纠正
《钥金冲压作业指导
书》、《工装设备保养
制度》
《设备运转台时记录表》、《设备操作交接班记录表》、《空调银金分厂设备日常点检表》、《钥金分厂冲压首检记录表》
1模/小时
纠正、封存
28
机械手自动冲压线
/
冲床、
模具
尺寸、
外观
1、依据生产计划单领取分条料,领料时标识清晰、可辨,与生产订单信息、实物一致,核对材料型号、尺寸是否与工艺相符;
2、模具定期保养
冲压工
自检
纠正、封存
《饭金冲压作业指导书》、《工装设备保养
制度》
《设备运转台时记录表》、《设备操作交接班记录表》、《空调饭金分厂设备日常点检表》、《饭金分厂冲压首检记录表》
29
首检
/
高度尺、角度尺、游标卡尺、卷尺、止通规、螺纹规等
尺寸、
外观
1、检查模具吨位是否符合工艺文件,设备压力参数符合设备要求;
2、核对模具、钢卷规格型号是否与
生产计划单备注的一致(坯料主要核对材料长、宽和厚度尺寸;半工序来料需主要核对半成品是否与工艺文件或图纸相符,是否盖有检验章或签字);3、
成型(压型)模需检查制件压型状态、拉伸深度和尺寸是否达到图纸/工艺要求,不能出现明显拉锌、锌丝等问题;4、折弯
/变型模需检查压型折弯角度、方向、尺寸是否达到图纸/工艺要求,不能出现明显拉锌、锌丝等问题;
5、边板类制品孔内不允许出现锌丝,且孔边缘部位不允许出现压印,杜绝割管隐患;
6、电器盒类制品叠边不允许出现条状锌丝,防止因锌丝问题导致控制元件损坏;
7、其他类无特殊要求,需保证制品尺寸、结构符合图纸或工艺文件要求。
检验员
每次换模/换产品/换程序
专检
纠正、
封存
《冷冲压工艺规程》
《首检记录表》
30
抽检
22
31
钾接
钾接
/
压力机
/压钥模具
产品性能、
安全
性能
1、检查压力表,确认压力是否正常
(0.6-0.8MPa之间);
2、钏枪紧固部分紧固不会松动;
3、符合螺纹止通规(或螺纹规)要求;
4、枷接后底脚不松动,敲击零件不
操作工
每次首检/换螺母
自检
纠正、封存
倾接作业
指导书》
《首检记录表》
分厂检验员
1次/2小时
发出杂音;
23
32
焊接
点焊
★
点焊机
产品性能、
安全
性能
1、需持有该岗位上岗证才能安排操作设备;2、半工序来料需主要核对泵脚螺栓选用是否与工艺相符;
3、电压、气压是否符合工艺要求;
《点焊工艺规范》
《首检记录表》
33
检验
/
胶锤、铁刀、卡尺、
卷尺
外观
1、核对材料厚度、之间状态是否符合工艺要求;
2、检查各参数是否符合工艺参数;
3、点焊牢固性、外观需符合工艺要求;
分厂巡检
每次首
检
专检
纠正、封存
《点焊工艺规范》
34
打磨
/
打磨机
外观
对焊接处的焊瘤、夹渣、钗边、飞溅物、氧化皮进行取出。
保证零件表面平整、光洁。
操作工
全检
自检
纠正、停岗培训
《返修作业指导书》
《日常点检表》
24
35
喷涂
上件
/
专用挂具、输
送链
外观
1、确保外机流水线线速控制在10m/min以下;内机流水线线速控制在5m/min以下;
2、将饭金件悬挂在专用挂具上,并挂牢;
3、确保产品之间保持相应的距离,防止产品相互碰撞;
4、对于挂具上变形的挂钩,要及时的使用老虎钳进行纠正;
5、对于质量有缺陷的产品不能上件,如:
生锈、印子、变形、板坏、脱焊、虚焊。
操作工
全检
自检
纠正、停岗培训
《喷涂作业指导书》
日常检验表
25
36
前处理
★
硅烷处理剂
1、EDTA:
(1.0〜3.0)点(作记录);
2、PH值3.5〜4.5;
操作工
1次/2小时
自检
纠正
《硅烷处理作业指导
钥金件喷涂作业记录单
3、喷嘴喷射压力(0.05〜0.12)
MPa(作记录);
4、硅烷处理温度为(常温);
5、流水线线速控制在5m/min以下,确保银金件硅烷处理的时间控制在3min以上;
6、饭金件硅烷处理后,用指甲轻划
表面,可见轻微划痕;7、
硅烷层应结晶致密、均匀,不得出现露底的现象;8、钥
金件表面不得出现锈蚀、绿斑及大面积返黄;9、表面
无水迹、擦白、挂灰现象。
26
37
喷涂
★
喷涂设备
1、电压(60-80)kv;
2、压缩空气压力控制在(0.5-0.8)Mpa;
3、外机流水线线速控制在10m/min
以下;内机流水线线速控制在5m/min以下,保证产品静电喷涂时间;4、
保证银金件与枪头的距离在
(100-180)mm;
5、喷房温度控制在15-35°C,湿度控制在20%-80%;
6、喷涂过程中,确保冷冻干燥机、油水分离器处于正常工作状态,保证压缩空气无水、无油;
7、对易露底或不易上粉地方采取人工补喷(预喷或滞后喷);
8、粉末一定要保持干燥,否则影响
操作工
1次/2小时
自检
纠正、停岗培训
《饭金件喷涂作业指导书》
日常检验表
送粉流畅;9、柜
内机喷塑件返喷时,不允许将原喷涂颜色的工件返喷为另一种颜色的工件;
10、喷房内每天必须清理,保持喷涂环境的清洁。
27
38
下件
/
周转车、记号笔
外观
外观喷塑面:
1、工件表面应无明显气泡、气孔、油污、流痕、露底、皱纹、沙眼。
光滑平整无明显条纹,不得有粉化、堆积(流挂)、龟裂、污迹、碰伤等现象;
2、底盘、阀安装板及特殊要求部件内外表面涂层不允许露底、发青,底盘内表面边角位不允许发青;
3、底盘与底脚叠合位允许露底、发青,不允许有锈渍存在。
底脚安装孔边线8mm范围内,涂层不允许露底、发青;
4、底脚因补粉不到位造成发青时,允许使用进口耐腐蚀热塑性丙烯酸树脂气雾漆修补,修补处与其它部
位色差不大于1.2;
5、喷塑件的非装配孔位,如银金件方格口、钢丝网罩网格等,不允许出现挂钩痕迹,且不可以手工补漆;喷塑件的螺钉装配孔位,包含底盘底脚安装孔位,允许出现孔周边2mm范围内的钓钩印,2mm范围外的挂钩痕迹,需涂漆修补后才能使用;
操作工
每次首检
自检
纠正、停岗培训
《镀锌板喷塑件检验标准》
日常检验表、物料标识
6、室外机底盘、顶盖和底脚边缘要求光滑,边缘不能看见有露出铁基的发青现象;
7、阴角位对覆盖况状不作要求,但必须有肉眼可见粉末覆盖,不允许露底;
8、对于喷涂焊接部件的内腔不作覆盖要求(如柜内机后围板与电机安装板之间);
9、工件无明显色差,光洁度好,表面无橘皮现象。
10、在饭金件内侧盖上本组工号,要求工号位置适中、明显、容易辨认。
11、检验合格的零件从输送链上取下,整齐的摆放于周转箱内。
12、外观检验方法:
正常光线下,眼睛与样品待测面距离400mm〜500mm,成)20。
〜140°角度观看。
内表面和非外观喷塑表面:
1、部件的内表面、其他不影响外观的部件表面,斑点(包括黑点、沙粒)、粉粒、凹凸等缺陷,直径不大于4mm,碰焊点除外;
2、底盘内外表面不允许露底缺陷存在;
3、压缩机螺栓的螺纹部位,不能有影响螺母锁紧的涂层附着;
4、柜内机后围板组件的背面,按非外观喷涂表面判定;
涂层厚度要求:
1、外观件外表面、底盘内外表面及特殊要求部件,涂层平均厚度5011m〜250Um(含返工件),单点最薄不小于45Pm;
2、阀安装板内侧和左支撑条内侧涂层平均厚度要求不小于40um,单点最薄不小于35Um;
3、外观件内表面四周距产品边缘10颇以内不允许发青,涂层平均厚度不小于40uni,单点最薄不小于35Pm;
4、其他部件内表面涂层允许发青,涂层平均厚度不小于20um,单点最薄不小于15um;
28
39
返修
返修
/
打磨机、沙皮、小
铁锤
1、零件表面原则上是不允许打磨,如零件不打磨无法满足外观要求的情况下只允许对缺陷的局部小面积打磨、抛光处理,打磨面积不超过总面积的5%,非喷涂件(除边、角处)严禁打磨、抛光;所有经过打磨处理的饭金件,必须在打磨后48小时内二次加工为成品;
2、返修件用目测、手摸方式进行检验;目测表面平整光滑,用手戴上手套对局部返修过的位置快速来回触摸,触摸过过程平整顺畅没有明显的凹凸手感视为合格;
3、打磨时严格遵守打磨机操作要求,打磨后产品表面光滑过渡,无
返修工
每次返工
自检
纠正、返工
《返修作业指导书》
《返修记录表》
不平现象。
29
40
摆放、包装
合格品处理
/
目视
错混
料
1、零件完工后按《饭