螺母板支座模具的设计说明书.docx
《螺母板支座模具的设计说明书.docx》由会员分享,可在线阅读,更多相关《螺母板支座模具的设计说明书.docx(43页珍藏版)》请在冰豆网上搜索。
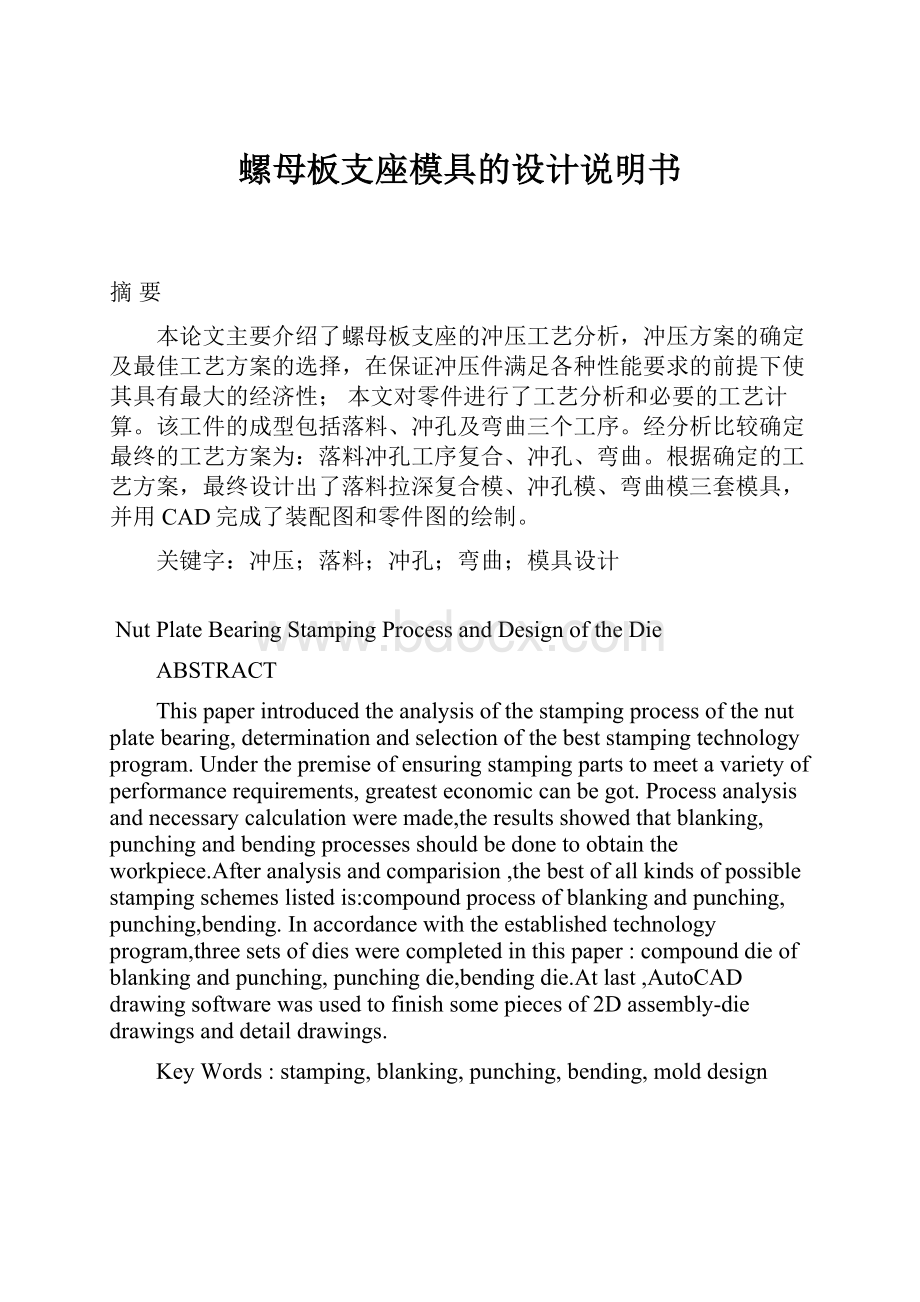
螺母板支座模具的设计说明书
摘要
本论文主要介绍了螺母板支座的冲压工艺分析,冲压方案的确定及最佳工艺方案的选择,在保证冲压件满足各种性能要求的前提下使其具有最大的经济性;本文对零件进行了工艺分析和必要的工艺计算。
该工件的成型包括落料、冲孔及弯曲三个工序。
经分析比较确定最终的工艺方案为:
落料冲孔工序复合、冲孔、弯曲。
根据确定的工艺方案,最终设计出了落料拉深复合模、冲孔模、弯曲模三套模具,并用CAD完成了装配图和零件图的绘制。
关键字:
冲压;落料;冲孔;弯曲;模具设计
NutPlateBearingStampingProcessandDesignoftheDie
ABSTRACT
Thispaperintroducedtheanalysisofthestampingprocessofthenutplatebearing,determinationandselectionofthebeststampingtechnologyprogram.Underthepremiseofensuringstampingpartstomeetavarietyofperformancerequirements,greatesteconomiccanbegot.Processanalysisandnecessarycalculationweremade,theresultsshowedthatblanking,punchingandbendingprocessesshouldbedonetoobtaintheworkpiece.Afteranalysisandcomparision,thebestofallkindsofpossiblestampingschemeslistedis:
compoundprocessofblankingandpunching,punching,bending.Inaccordancewiththeestablishedtechnologyprogram,threesetsofdieswerecompletedinthispaper:
compounddieofblankingandpunching,punchingdie,bendingdie.Atlast,AutoCADdrawingsoftwarewasusedtofinishsomepiecesof2Dassembly-diedrawingsanddetaildrawings.
KeyWords:
stamping,blanking,punching,bending,molddesign
1前言
板料成形通常称为冲压或冷冲,即在室温下,利用安装在压力机上的冲压模具(冷冲模、冲模)对材料(板料、条料或带料)施加压力,使其产生分离或发生塑性变形,从而获得所需形状和尺寸、具有一定力学性能的零件的一种压力加工方法。
冲压模具是指在冷冲压加工中,将材料(金属或非金属)加工成零件(或半成品件)的一种特殊工艺装备。
冲压成型加工必须具备相应的模具。
模具是技术密集型产品,其制造属于单件小批量生产具有难加工、精度高、技术要求高、生产成本高(约占产品成本的10%~30%)的特点。
所以,只有在冲压件生产批量大的情况下,冲压成型加工的优点才能得到充分体现,从而获得好的经济效益。
冲压生产具有生产率高,材料利用率高,生产的制件精度高、复杂程度高、一致性高等一系列突出优点,因此在批量生产中得到了广泛应用,在现代工业生产中占有十分重要的地位,是国防及民用工业生产中必不可少的加工方法。
冲压加工是完成金属塑性成形的一种重要手段,它是最基本、最传统、最重要的金属加工方法之一。
冲模设计是冲压工艺设计中关键的一环,工艺设计结果直接影响模具的结构和生产的冲压产品质量。
冲压工艺方案的产生和处理是冲压工艺设计的主要内容,其中工序生成、工序排序及工序组合是工艺方案设计的主要工作。
在冲压生产中,冲压模具作为冲压工艺的具体执行工具,是冲压生产必不可少的工艺装备,是技术密集型产品。
冲压件的质量、生产效率以及生产成本等,与模具设计和制造有直接关系。
模具设计与制造技术水平的高低,是衡量一个国家产品制造水平高低的重要标志之一,在很大程度上决定着产品的质量、效益和新产品的开发能力。
因此,开发和推广冷冲压生产工艺,必须高标准地超前攻克冲模技术,这是必然的逻辑和规律。
早在20世纪50年代,美、日等工业发达国家已注意及此,在开发应用冷冲压新技术的同时,集中了部分优势人才和资金,结合市场的需要,将模具作为一个统一的产业来发展,因而取得明显的效果。
经过多年的耕耘,不仅在模具精度、模具结构、模具寿命、模具周期等方面取得了明显的突破,而且在板材成形过程模拟、模具优化和可靠性设计等方面形成了新的理论和方法,为适应新的市场环境进一步实现快速制模,开辟新的效益空间,打下了基础[1]。
我国冲压模具无论在数量上,还是在质量、技术和能力等方面都已有了很大发展,但与国发经济需求和世界先进水平相比,差距仍很大,一些大型、精密、复杂、长寿命的高档模具每年仍大量进口,特别是中高档轿车的覆盖件模具,目前仍主要依靠进口。
一些低档次的简单冲模,已趋供过于求,市场竟争激烈。
改革开放以来,随着国民经济的高速发展,市场对模具的需求量不断增长。
近年来,模具工业一直以15%左右的增长速度快速发展,模具工业企业的所有制成分也发生了巨大变化,除了国有专业模具厂外,集体、合资、独资和私营也得到了快速发展。
浙江宁波和黄岩地区的“模具之乡”;广东一些大集团公司和迅速崛起的乡镇企业,科龙、美的、康佳等集团纷纷建立了自己的模具制造中心;中外合资和外商独资的模具企业现已有几千家。
21世纪开始CAD/CAM技术逐渐普及,现在具有一定生产能力的冲压模具企业基本都有了CAD/CAM技术。
其中部分骨干重点企业还具备CAE能力。
模具CAD/CAM技术能显著缩短模具设计与制造周期,降低生产成本,提高产品质量,已成为人们的共识。
在“八五”、“九五”期间,已有一大批模具企业推广普及了计算机绘图技术,数控加工的使用率也越来越高,并陆续引进了相当数量CAD/CAM系统。
在现代技术迅猛发展的今天,要想圆满完成一套模具的设计,除了要有模具设计相关方面的知识外,还要全面了解与模具制造有关的新技术、新方法,从而不断更新、改进落后传统的设计原则,形成面向制造、面向世界的模具制造设计原则:
制造可行性、制造合理性、制造经济性、制造效率、制造设备等。
这几方面相互依存、相辅相成,进行模具设计时要综合考虑。
本次设计即是依据以上原则,尽量兼顾节材、高效、低成本拟定的工艺方案,从而设计模具。
本次设计共分为六章:
第一章,主要介绍模具设计任务书和工件图;第二章,主要从技术和经济两个方面对工件进行工艺分析;第三章,通过工艺分析和比较,选定最佳工艺方案;第四章,主要介绍各个工序冲裁力的计算方法,同时选择合理的冲压设备;第五章,主要介绍落料、冲孔复合模的结构和设计;第六章,主要介绍弯曲模的结构和设计。
2产品图
本次的设计任务是通过多道冲压工序完成螺母板支座的成型。
制件图如图1-1所示:
图2-1制件图
3冲压工艺分析
该零件为螺母板支座,零件外形对称,无尖角、凹陷或其他形状突变,是典型的板料冲压件。
零件外形尺寸公差要求不高,壁部圆角半径r1,相对圆角半径r/t=0.5,大于参考文献[2]表3-5所示的最小弯曲半径值。
弯曲件直边高度h>2t,因此可以弯曲成形。
Ф4mm的两个孔均布在零件的两个弯曲直边上,孔距有位置要求,但孔径无公差配合。
Ф10mm圆孔无公差配合,弯曲角为90
,也无公差配合。
通过上述工艺分析,可以看出该零件为普通的板料弯曲件,尺寸精度要求不高,因此可以用冲压方法生产。
4工艺方案的确定
4.1毛坯展开尺寸计算
4.1.1计算公式的确定
零件有落料,冲孔,弯曲工序,所以应将其展开计算:
根据参考文献[1]弯曲件r=0.5t:
有圆角半径的弯曲件,其展开长度是根据弯曲前后应变中性层长度不变的原则进行计算的。
弯曲件毛皮长度等于直线部分的长度和弯曲部分应变中性层展开长度之和。
L=∑l直+∑l弯
式中L—弯曲件毛坯长度(mm)
∑l直—弯曲件各直线段长度之和(mm)
∑l弯—弯曲件各弯曲部分(圆弧部分)应变中性层展开长度之和(mm)
该工件属于双直角弯曲且
,因此
(文献[1])
图4-1
4.1.2毛坯尺寸计算
当
(文献[1])
所以毛坯总长度为
所得毛坯如图3-2所示:
图4-2产品毛坯图
4.2确定排样方式和计算材料利用率
零件外轮廓尺寸较复杂,考虑操作方便和材料利用率的问题,采用双排。
如图4-3所示。
图4-3工件排样图
由参考文献[2]表2-13查得搭边数值为:
a=2.0mm,
a1=2.2mm
条料宽b=42+24+2a+a1
=(42+24+2×2.0+2.2)mm
=72.2mm
进距A=B+a
=(52.71+2.0)mm
=54.71mm
选用板料规格为2mm×800mm×2500mm,采用横排,剪切条料尺寸为72.2mm×2500mm。
条数n1=800/72.2=11条余5.8mm
每条个数n2=(2500-2.2-24)/54.71=45个余11.85mm
每板个数n3=2n1n2=2×11×45=990个
冲片面积
材料利用率η=(1096.77×990)/(800×2500)×100%
=54.3%
考虑到冲裁送料时板料的定位问题,剪切条料尺寸修正为:
73.2mm×2497.52mm。
4.3冲压工序性质和工序次数的选择
冲压该零件,需要的基本工序和次数有:
1.落料
2.冲Ф4孔2个
3.冲Ф10孔1个
4.弯曲成形
4.4工序组合及其方案比较
根据以上这些工序,可以作出下列组合方案。
方案一:
1.落料
2.冲Ф10孔1个
3.弯曲成形
4.冲侧壁Ф4孔2个
方案二:
1.落料
2.冲Ф10孔1个
3.冲Ф4孔2个
4.弯曲成形
方案三:
1.落料
2.冲Ф4孔2个,冲Ф10孔1个
3.弯曲成形
方案四:
1.落料,冲Ф10孔1个
2.冲Ф4孔2个
3.弯曲成形
从生产效率、模具结构和寿命方面对以上四种方案进行比较,可以看出:
方案一:
将落料和冲孔分开加工,有利于降低冲裁力和提高模具寿命,同时模具结构也较简单。
但是,须设计四套模具,浪费材料,显然生产效率不高。
另外,在弯曲成形之后再冲侧壁孔,可以提高孔距精度,保证零件质量,但在壁部冲孔增加了操作难度,操作不便,同时模具费用也较高。
方案二:
情况与方案一基本相同,但弯曲成形安排在冲孔之后,操作方便,弯曲成形在冲孔以后进行,弯曲回弹后孔距不易保证,影响零件精度。
方案三:
将三个孔组合到一套模具上冲压,减少了一套模具,节省了工序,降低了生产成本。
弯曲工序在冲孔之后进行,产生与方案二相同的缺点。
方案四:
落料与冲孔符合,满足最小壁厚要求。
模具结构紧凑且少一套模具设计。
弯曲工序在冲孔之后进行,与上述方案基本相同。
通过以上的方案分析,结合零件对孔距精度要求不高的情况,可以看出,方案四的模具设计无论是工艺性还是经济性都比较合理,符合本次设计,故选用方案四的模具设计。
5各工序冲压力的计算和冲压设备的选择
5.1冲裁力的计算
5.1.1冲裁力计算公式的确定
计算冲裁力的目的是为了合理地选用压床和设计模具。
所选用的压床的吨位必须大于所计算的冲裁力,以适应冲裁的要求[2]。
一般情况下,冲裁件从板料切下以后,径向因弹性变形而扩张,板料上的孔则沿径向发生弹性收缩。
同时,冲下的零件与余料还要力图恢复弹性穹弯。
这两种弹性恢复的结果,会使落料梗塞在凹模内,而冲裁后剩下的板料则箍紧在凸模上。
从凸模上将零件或废料卸下来所需要的力称卸料力。
从凹模内顺着冲裁方向把零件或废料从凹模腔顶出的力称推件力。
影响这些力的因素较多,主要有材料的机械性能、材料厚度、模具间隙、零件形状尺寸以及润滑情况等[2]。
冲裁时的冲压力是冲裁力、卸料力和推件力之和,这些力在设计模具和选择压力设备时是否需要考虑进去,应根据不同的模具结构区别对待。
由于本部分落料、冲孔模具的设计是采用弹性卸料装置和下出料方式,所以冲裁力为:
F总=F+F顶+F卸(5-1)
本部分设计采用平刃口模具冲裁,考虑到模具刃口的磨损,凸、凹模间隙的波动,材料机械性能的变化,材料厚度偏差等因素,实际冲裁力按参考文[2]献式(2-1)计算:
F=1.3Ltτ(5-2)
式中F—冲裁力;
t—材料厚度;
τ—材料抗剪强度,[τ]为MPa;
L—冲裁周长。
5.1.2所需落料力的计算
因为L=(2×22+15×2+2×30.71+2×18+2×9)mm
=189.42mm
查参考文献[3]表D-22得:
τ=360~480MPa
取τ=400MPa
代入式(5-2)得:
F1=1.3Ltτ=196996.8N
5.1.3所需冲孔力的计算
冲Ф10mm孔所需的冲裁力
因为L=πd
=π×10mm
=31.4mm
代入式(5-2)得:
F2=1.3Ltτ=32656N
5.1.4所需推件力的计算
顶件力参照参考文献[2]计算:
F顶=K顶F=K顶(F1+F2)(5-3)
式中F顶—顶件力,[F]为N;
K顶—顶件力系数,其值见表参考文献[2]表2-2;
F—冲裁力,[F]为N。
查参考文献[2]表2-2得:
K顶=0.06
代入式(4-3)得:
F顶=13779.168N
5.1.5所需卸料力的计算
卸料力参照参考文献[2]计算:
F卸=K卸F=K卸(F1+F4)(5-4)
式中F卸—卸料力,[F]为N;
K卸—卸料力系数,其值见表参考文献[2]表2-10;
F—冲裁力,[F]为N。
查参考文献[2]表2-2得:
K卸=0.04~0.05
取K卸=0.045
由式(5-4)得:
F卸=10334.376N
5.1.6所需总冲裁力的确定
F总=F1+F2+F顶+F卸
=196996.8+32656+13779.168+10334.376N
=253766.344N
≈254KN
5.2冲小孔工艺力计算
5.2.1冲裁力的计算
冲小孔时采用弹性卸料装置和下出料,故其总冲压力为
F总=F冲+F卸
因为L=2×πd=(2×3.14×4)mm=25.12mm
查参考文献[3]表D-22得:
τ=360~480MPa
取τ=400MPa
按参考文[2]献式(2-1)计算:
F冲=1.3Ltτ=(1.3×25.12×2×400)N=26124.8N
5.2.2所需卸料力的计算
卸料力参照参考文献[2]计算:
F卸=K卸F=K卸F冲(
式中F卸—卸料力,[F]为N;
K卸—卸料力系数,其值见表参考文献[2]表2-10;
F冲—冲裁力,[F]为N。
查参考文献[2]表2-2得:
K卸=0.04~0.05
取K卸=0.045
由式得:
F卸=1175.616N
故F总=F冲+F卸=(26124.8+1175.616)N=27300.416N
5.3弯曲力的计算
弯曲力是拟订板料弯曲加工工艺和选择设备的重要依据之一。
板料弯曲时,开始是弹性弯曲,其后是变形区内外层纤维首先进入塑性状态,并逐渐向板的中心扩展进行自由弯曲,最后是凸、凹模与板料相互接触并冲击零件的校正弯曲。
弯曲力包括自由弯曲力、校正弯曲力和压料力(或推件力)。
5.3.1自由弯曲力的计算
自由弯曲力参照参考文献[1]式(2.3-37)计算:
(5-5)
式中
—最大自由弯曲力,[
]为N;
—材料抗拉强度,[
]为MPa;
K—安全系数,一般取k=1.3;
B—弯曲件宽度,[b]为mm。
已知B=9mmt=2mmr=1mm
查参考文献[3]表D-22得:
σb=450~600MPa
取σb=500MPa
代入式得:
=5460N
5.3.2校正弯曲力
校正弯曲力按参考文献[1]式(2.3-38)计算:
Fj=f·A(5-6)
式中Fj—校正弯曲力,[Fj]为N;
A—弯曲件校正部分的投影面积,[A]为mm2;
f—单位校正力,其值见参考文献[1]表2.3-4
因为A=27×9mm2
=243mm2
由参考文献[1]表2.3-4查得:
f=50~70MPa
取f=60MPa
代入式(5-6)得:
Fj=14580N
5.3.3压料力的计算
压料力参照参考文献[1]按下式计算:
Fd(或Fy)=kFz(5-7)
式中Fd—顶件力(N)
Fy—压料力(N)
Fz—自由弯曲力(N)
K—系数,可查表2.3-5文献[1]
计算顶件力时系数取0.4
计算压料力时系数取0.8
由式(5-7)得:
Fd=2184N
Fy=4368N
5.4冲压设备的选择
在冲压生产中,最常用的是摩擦压力机、偏心压力机和曲轴压力机(俗称冲床)以及油压机等。
冲压设备的选择是冲压工艺及模具设计中一项重要内容,它直接关系到冲压设备的安全使用,冲压工艺能否顺利实现和模具寿命、产品质量、生产效率、成本高低等重要问题。
冲压设备的选用包括选择设备类型和确定设备规格两项内容。
冲压设备类型的选择主要是根据冲压工艺特点和生产率、安全操作等因素来确定的。
在中小型冲压生产中,主要选用开式压力机;对需要变形力大的工序(如冷挤压等),应该选用刚性好且比较精密的闭式压力机;对于校平、整形和温、热挤压等工序,最好选用摩擦压力机;对于薄材料的冲裁工序,最好选用导向准确的精密压力机;对于大型拉深件的冲压工序,最好选用拉深压力机;在大量生产中,应该选用高速压力机或多工位自动压力机;对于不允许冲模导套离开导柱的冲压工序,最好选用行程可调整的偏心式压力机。
经过如上分析,本次螺母板支座冲压件的设计选用开式压力机。
在压力机的类型选定好之后,应该进一步根据变形力的大小、冲压件尺寸和模具尺寸来确定设备的规格。
具体地说,在完成某一工序而选用压力机时,必须考虑的参数有:
公称压力、滑块行程、行程次数、工作台面尺寸、闭合高度和电动机的功率等。
在实际选用设备时,除了要参照压力机的公称压力进行选择,还需要考虑模具空间的大小,工艺流程和设备负荷等因素,再作合理安排。
此次设计的模具由于制件尺寸较小,而且整个模具的外形结构也简单,只需选用开式压力机。
5.4.1落料、冲孔模
根据参考文献[5],通过工艺力及做功校核选择压力机
根据工艺计算力,可初选J23—40设备,因为此时工艺计算力图完全落在压力机许用负荷图安全区内。
做功校核。
对J23—40压力机Sg=7mm,Fg=400KN
根据式(2-18),压力机做功能力有文献[5]
而此时工件变形功A2为
故可选J23—40压力机
通过计算及校核可选400KN的开式压力机。
由参考文献[1]400KN开式可倾工作台压力机基本参数如下:
公称压力400KN
公称压力时滑块下死点距离7mm
滑块行程100mm
行程次数80次/min
最大封闭高度300mm
封闭高度调节量80mm
滑块中心到床身距离220mm
工作台尺寸左右630mm
前后420mm
工作台孔尺寸左右300mm
前后150mm
直径200mm
立柱间距离300mm
模柄孔尺寸Ф50×70mm
工作台板厚度80mm
倾斜角30º
垫板厚度65mm
5.4.2冲小孔冲孔模
方法同上述落料冲孔,由同样的方法可选择100KN的开式压力机。
由参考文献[1]100KN开式可倾工作台压力机基本参数如下:
公称压力100KN
公称压力时滑块下死点距离4mm
滑块行程60mm
行程次数135次/min
最大封闭高度180mm
封闭高度调节量50mm
滑块中心到床身距离130mm
工作台尺寸左右360mm
前后240mm
工作台孔尺寸左右180mm
前后90mm
直径130mm
立柱间距离180mm
模柄孔尺寸Ф30×50mm
工作台板厚度50mm
倾斜角30º
5.4.3弯曲模
由弯曲工艺可知,弯曲时的校正弯曲力与自由弯曲力、压料力不是同时发生的,且校正弯曲力比自由弯曲力和压料力大得多。
因此,在选择冲压设备时,可仅以校正弯曲力作为依据[1],即
F压力机≥(1.1~1.2)Fj(5-8)
根据以上计算,可选用40KN的压力机。
参照参考文献[1]40KN开式可倾工作台压力机基本参数如下:
公称压力40KN
公称压力时滑块下死点距离3mm
滑块行程40mm
行程次数200次/min
最大封闭高度160mm
封闭高度调节量35mm
滑块中心到床身距离100mm
工作台尺寸左右280mm
前后180mm
工作台孔尺寸左右130mm
前后60mm
直径100mm
立柱间距离130mm
模柄孔尺寸Ф3050mm
工作台板厚度35mm
倾斜角30º
5.5压力中心的计算
为了保证压力机和模具正常地工作,必须使冲模的压力中心与压力机滑块中心线相重合。
否则在冲压时会使冲模与压力滑块歪斜,引起凸、凹模间隙不均和导向零件加速磨损,造成刃口和其它零件的损坏,甚至还会引起压力机导轨磨损,影响压力机精度。
形状简单而对称的工件,如圆形、正多边形、矩形,其在冲裁时的压力中心与工件的几何中心重合。
形状复杂的工件、多凸模及连续模的压力中心则用解析法或作图法来确定。
由参考文献[5]可知对于形状不规则的冲压件,其压力中心可按下列公式计算:
x0=(l1x1+l2x2+…+lnxn)/(l1+l2+…+ln)(5-9)
y0=(l1y1+l2y2+…+lnyn)/(l1+l2+…+ln)(5-10)
式中l1,l2…ln—冲裁边各线段的长度;
x1,x2…xn—各线段中心的x坐标值;
y1,y2…yn—各线段中心的y坐标值;
x0,y0—压力中心的坐标值。
由于工件结构简单而且左右对称,故可设其压力中心O点坐标为(x0,y0),如图5-1所示:
由图5-1可知:
x0=26.55mm
由式(5-10)得:
y0≈21.47mm
即压力中心O点坐标为(26.55,21.47)。
图5-1压力中心计算
6落料冲孔模模具设计
图6-1落料冲孔模具示意图
6.1落料、冲孔模简介
从工件的外形分析,工件要先经落料、冲孔,才能进行下一步工序,由此根据模具设计的基本原则,选择使用落料、冲孔倒装复合模。
所谓复合模,是指在压力机的一次行程中,在模具的同一位置上同时完成落料、冲孔等多个冲压工序,而冲件材料无需随工序进给移动的模具。
复合模的结构,一般都很紧凑,具备导向、顶料、卸料、缓冲、复位等多种辅助系统。
复合模虽然生产效率高,冲压件精度高,但模具