化工原理课程设计利用浮阀塔分离正戊烷与正己烷的工艺的设计副本.docx
《化工原理课程设计利用浮阀塔分离正戊烷与正己烷的工艺的设计副本.docx》由会员分享,可在线阅读,更多相关《化工原理课程设计利用浮阀塔分离正戊烷与正己烷的工艺的设计副本.docx(23页珍藏版)》请在冰豆网上搜索。
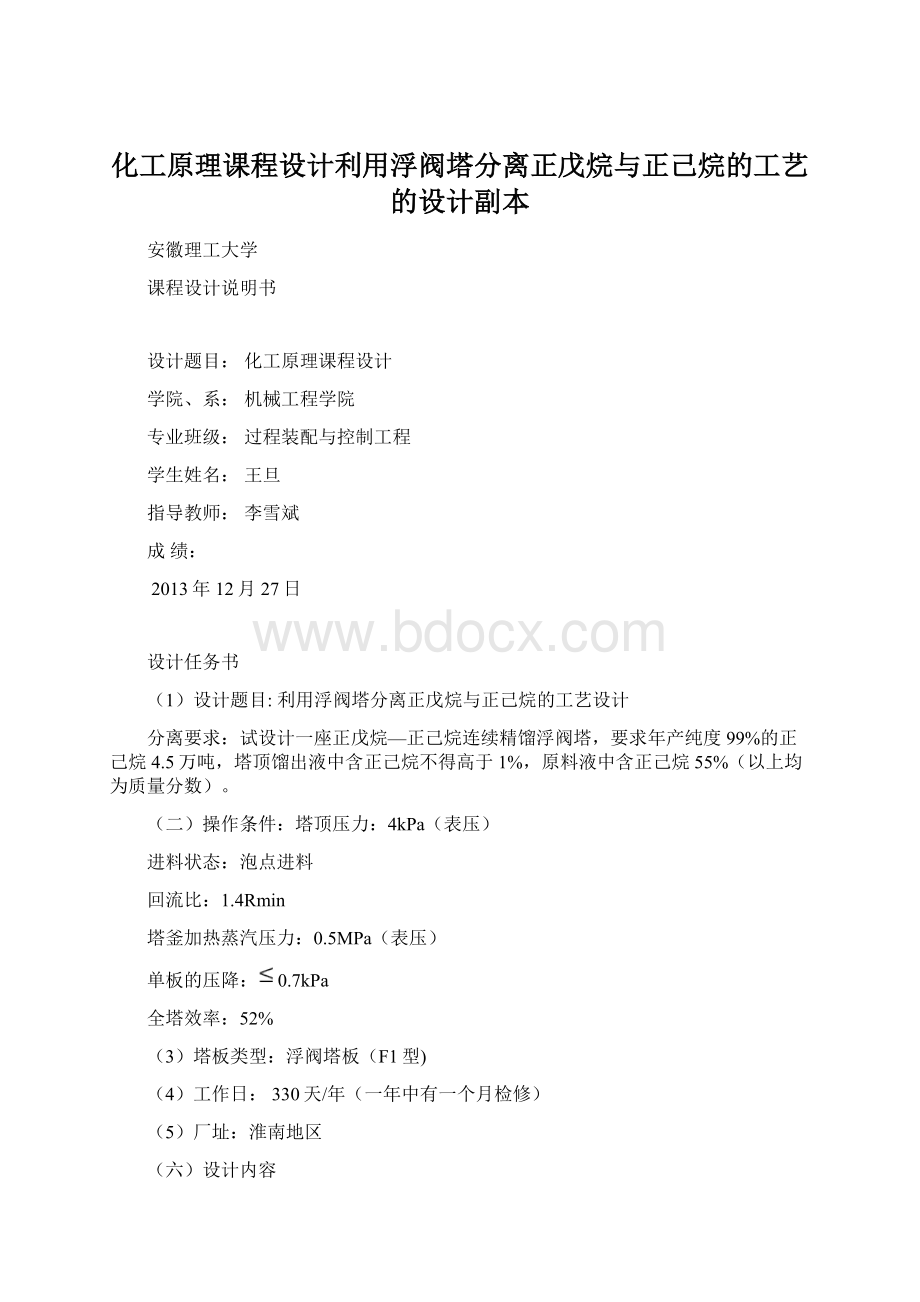
化工原理课程设计利用浮阀塔分离正戊烷与正己烷的工艺的设计副本
安徽理工大学
课程设计说明书
设计题目:
化工原理课程设计
学院、系:
机械工程学院
专业班级:
过程装配与控制工程
学生姓名:
王旦
指导教师:
李雪斌
成绩:
2013年12月27日
设计任务书
(1)设计题目:
利用浮阀塔分离正戊烷与正己烷的工艺设计
分离要求:
试设计一座正戊烷—正己烷连续精馏浮阀塔,要求年产纯度99%的正己烷4.5万吨,塔顶馏出液中含正己烷不得高于1%,原料液中含正己烷55%(以上均为质量分数)。
(二)操作条件:
塔顶压力:
4kPa(表压)
进料状态:
泡点进料
回流比:
1.4Rmin
塔釜加热蒸汽压力:
0.5MPa(表压)
单板的压降:
0.7kPa
全塔效率:
52%
(3)塔板类型:
浮阀塔板(F1型)
(4)工作日:
330天/年(一年中有一个月检修)
(5)厂址:
淮南地区
(六)设计内容
①精馏塔的物料衡算
②塔板数的确定
③精馏塔的工艺条件及有关物性数据的计算
④塔体工艺条件尺寸
⑤塔板负荷性能图
正戊烷—正己烷连续精馏浮阀塔的设计
第1章序言
精馏是分离液体混合物,一种利用回流是液体混合物得到高度分离的蒸馏方法,是工业上应用最广的液体混合物分离操作,广泛应用与石油、化工、轻工、食品、冶金等部门。
精馏过程在能量剂的驱动下,使气液两相多次直接接触和分离,利用液相混合物中各组分挥发度不同,使挥发组分由液相向气相转移,难挥发组分由气相向液相转移,实现原料混合液中各组分分离。
该过程是同时进行传质传热过程。
精馏塔分为板式塔填料塔两大类。
板式塔又有筛板塔、泡罩塔、浮阀塔等。
本次设计任务是设计双组份连续精馏浮阀塔,实现从正戊烷、正己烷的混合溶液中分离出一定纯度的正己烷。
本次设计选用浮阀塔。
本次设计基本流程:
原料液(正戊烷、正己烷混合液,泡点进料),经过预热器预热达到指定温度后,送入精馏塔的进料板上,进料中的液体和上塔段下来的液体逐板溢流,最后流入塔底再沸器中,经过再沸器得到汽化,蒸汽沿塔上升,余下的液体作为塔底产品。
进料中的蒸汽和下塔段来的蒸汽一起沿塔逐板上升,上升的蒸汽进入冷凝器,部分蒸汽得到冷凝返回塔顶,其余镏出液作为塔顶产品。
在整个精馏塔中,气液两相逆流接触,进行相互传质。
液相中的易挥发组分进入汽相,汽相中的难挥发组分转入液相。
在每层板上,回流液与上升蒸气互相接触,进行使热和使质过程。
操作时,连续地从再沸器取出部分液体作为塔底产品(斧残液),部分液体气化,产生生升蒸气,依次通过各层塔板。
塔顶蒸气进入冷凝器中被全部冷凝,并将部分冷凝液送回塔顶作为回流液体,其余部分经冷却器冷却后被送出作为塔顶产品(馏出液)。
本次设计主要内容是物料衡算、塔板数的确定、精馏塔的工艺条件及有关物性数据的计算、塔板负荷性能图和生产工艺流程图。
精馏塔工艺流程图
基础数据
表1.组分的饱和蒸汽压Pio(mmHg)
温度(℃)
36.1
40
45
50
55
60
65
68.7
Pio
正戊烷
101.33
115.62
136.05
159.16
185.18
214.35
246.89
273.28
正己烷
31.98
37.26
45.02
54.05
64.66
76.36
89.96
101.33
x
1
0.82
0.62
0.45
0.31
0.18
0.07
0
y
1
0.93
0.83
0.71
0.57
0.38
0.17
0
表2.组分的液相密度ρ(kg/m3)
温度(℃)
20
40
60
80
100
ρ
正戊烷
626.2
605.5
583.7
560.3
535.0
正戊烷
657.2
638.9
620
600.2
579.3
表3.表面张力()
温度(℃)
0
20
40
60
80
100
正戊烷
18.20
16.00
13.85
11.76
9.719
7.752
正己烷
20.10
18.02
15.99
13.23
12.06
10.18
表4.混合物的粘度(mpa.s)
温度(℃)
0
25
50
75
100
正戊烷
6.23
6.80
7.37
7.96
8.50
正己烷
6.00
6.54
7.10
7.66
8.20
第2章精馏塔的物料衡算
2.1.物料衡算
F:
原料液流量(kmol/h)xF:
原料组成(mol%)
D:
塔顶产品流量(kmol/h)xD:
塔顶组成(mol%)
W:
塔底残液流量(kmol/h)xW:
塔底组成(mol%)
正戊烷—正己烷的相对摩尔质量分数分别为72kg/kmol和86kg/kmol
1.原料液及塔顶、塔釜产品的摩尔分率
正戊烷的摩尔质量
正己烷的摩尔质量
2.原料液及塔顶、塔釜产品的平均摩尔质量
3.物料衡算
原料处理量
总物料衡算
正戊烷物料衡算
联立解得
2.2.常压下正戊烷—正己烷气、液平衡组成与温度的关系
温度:
利用表1中的数据由拉格朗日插值可求得tF、tD、tW.
tF:
tF=48.71℃
tD:
tD=36.27℃
tW:
tW=68.07℃
精馏段的平均温度:
==42.49℃
提镏段的平均温度:
℃
=42.49℃时的x1及y1
℃时的x2及y2
第3章塔板数的确定
3.1.理论板数的确定
由查得:
精馏段操作线方程
提馏段操作线方程
根据相对挥发度的求取得:
精馏段有5块塔板,第6块为进料板,全塔共有13块理论板。
3.2.实际板数的确定
全塔效率为ET=0.52
精馏段实际板数:
全塔实际板数:
即:
全塔板数为N=13/0.52=25(块)
第4章精馏塔的工艺条件及有关物性数据
4.1.操作压力的计算
塔顶操作压力
每层塔板压降
进料板压力
精馏段平均压力
塔底操作压力
提馏段平均压力
4.2.密度的计算
已知:
混合液密度:
(质量分率,为平均相对分子质量),不同温度下正戊烷和正己烷的密度见表2.
混合气体密度:
精馏段:
=41.28℃时,液相x1=0.77气相y1=0.90
液相:
气相:
提留段:
℃时,液相x2=0.28气相y2=0.52
液相:
气相:
tD=41.28℃时
tF=56.3℃时
精馏段气相平均密度
精馏段
提留段平均气相密度
提馏段
精馏段液相平均密度
提留段的液相平均密度
4.3.表面张力的计算
精馏段的平均温度=41.28℃时的表面张力
提留段的平均温度℃的表面张力
4.4.混合物的粘度
=41.28℃时
℃时
4.5.相对挥发度
tD=36.76℃时
tW=66.8℃时
第5章塔体工艺条件尺寸
5.1.气、液相体积流量计算
已知:
精馏段:
提馏段:
5.2.塔径的初步设计
精馏段
由
横坐标数值:
取板间距:
查图可知
安全系数取0.8
取整=1.6m
空塔气速:
提馏段:
横坐标数值:
取板间距:
查图可知
安全系数取0.8
取整=1.6m
空塔气速:
5.3.溢流装置
(1)堰长
取
出口堰高:
本设计采用平直堰,堰上液高度按下式计算:
近似取E=1
精馏段:
提馏段:
(2)弓形降液管的宽度和横截面积
查图得:
则:
验算降液管内停留时间:
精馏段:
提馏段:
(3)降液管底隙高度
精馏段:
取降液管底隙的流速
提馏段:
取降液管底隙的流速
因为不小于20mm,故满足要求。
5.4.塔板布置及浮阀数目与排列
(1)塔板分布
本设计塔径1.6m,采用分块式塔板,以便通过人孔装拆塔板。
阀孔临界速度
精馏段
提馏段
上下两段相应的阀孔动能因子为:
均属正常操作范围。
(2)浮阀数目与排列
精馏段
取阀孔动能因子则孔速为:
取边缘区宽度Wc﹦0.055m,安定区宽度,
开孔区面积
提馏段
取边缘区宽度Wc﹦0.030m,安定区宽度,
开孔区面积
其中,
,
(3)浮阀数与开孔率
F1型浮阀的阀孔直径为39mm
阀孔气速,其中取F0=10
浮阀数目
开孔率
精馏段
提留段
浮阀排列方式采用等腰三角形叉排,取同一横排的孔心距t=0.075m,则排间距为
精馏段
提留段
考虑到塔的直径较大,故采用分块式塔板,而各分快板的支撑与衔接将占去一部分鼓泡区面积,因此排间距应小于计算值,故取=80mm=0.08m
重新计算孔速及阀数
精馏段
提留段
由此可知,阀孔动能因数变化不大
第6章塔板负荷性能图
6.1.物沫夹带线
泛点率
据此可作出负荷性能图中的物沫夹带线,按泛点率80%计算:
精馏段:
查物性系数K=1.0
整理得:
由上式可知物沫夹带线为直线,则在操作范围内任取两个值算出
提馏段:
整理得:
精馏段
0.002
0.01
2.2285
2.0663
提馏段
0.002
0.01
2.0393
1.8908
6.2.液泛线
由此确定液泛线,忽略式中的
取0.5取0.5
而
精馏段:
整理得:
提馏段:
整理得:
在操作范围内任取两个值,算出相应的
精馏段
0.001
0.003
0.004
0.007
7.6739
7.0941
6.8109
5.8897
提馏段
0.001
0.003
0.004
0.007
8.0539
7.5712
7.3686
6.8158
6.3.液相负荷上限
液体的最大流量应保证降液管中停留时间不低于3~5秒。
液体降液管内停留时间
以作为液体在降液管内停留时间的下限,则:
6.4.漏液线
对于型重阀,依作为规定气体最小负荷的标准,则
精馏段:
提馏段:
6.5.液相负荷下限
取堰上液层高度作为液相负荷下限条件作出液相负荷下限线,该线为与气相流量无关的竖直线。
取E=1.0
由以上1—5作出塔板负荷性能图
精馏塔的负荷性能图
由塔板负荷性能图可以看出:
(1)在任务规定的气、液负荷下的操作点处在适宜操作区内的适中位置;
(2)塔板的气相负荷上限完全由物沫夹带控制,操作下由漏液控制;
第7章结束语
通过本塔的负荷性能图可以看出,操作线分别与液沫夹带线和漏液线相交,是以上限为液沫夹带控制,下限为漏液控制。
若操作点位于操作区内的适中位置时可获得稳定良好的操作效果。
但本塔的操作点偏于漏液线,在操作区偏下方。
使塔的正常操作受到一定影响。
可以通过减少塔板开孔率使漏液线下移,使操点位于操作区中心位置。
提高塔的操作效果。
精馏塔操作的基本要求是在