轴类型加工工艺设计.docx
《轴类型加工工艺设计.docx》由会员分享,可在线阅读,更多相关《轴类型加工工艺设计.docx(10页珍藏版)》请在冰豆网上搜索。
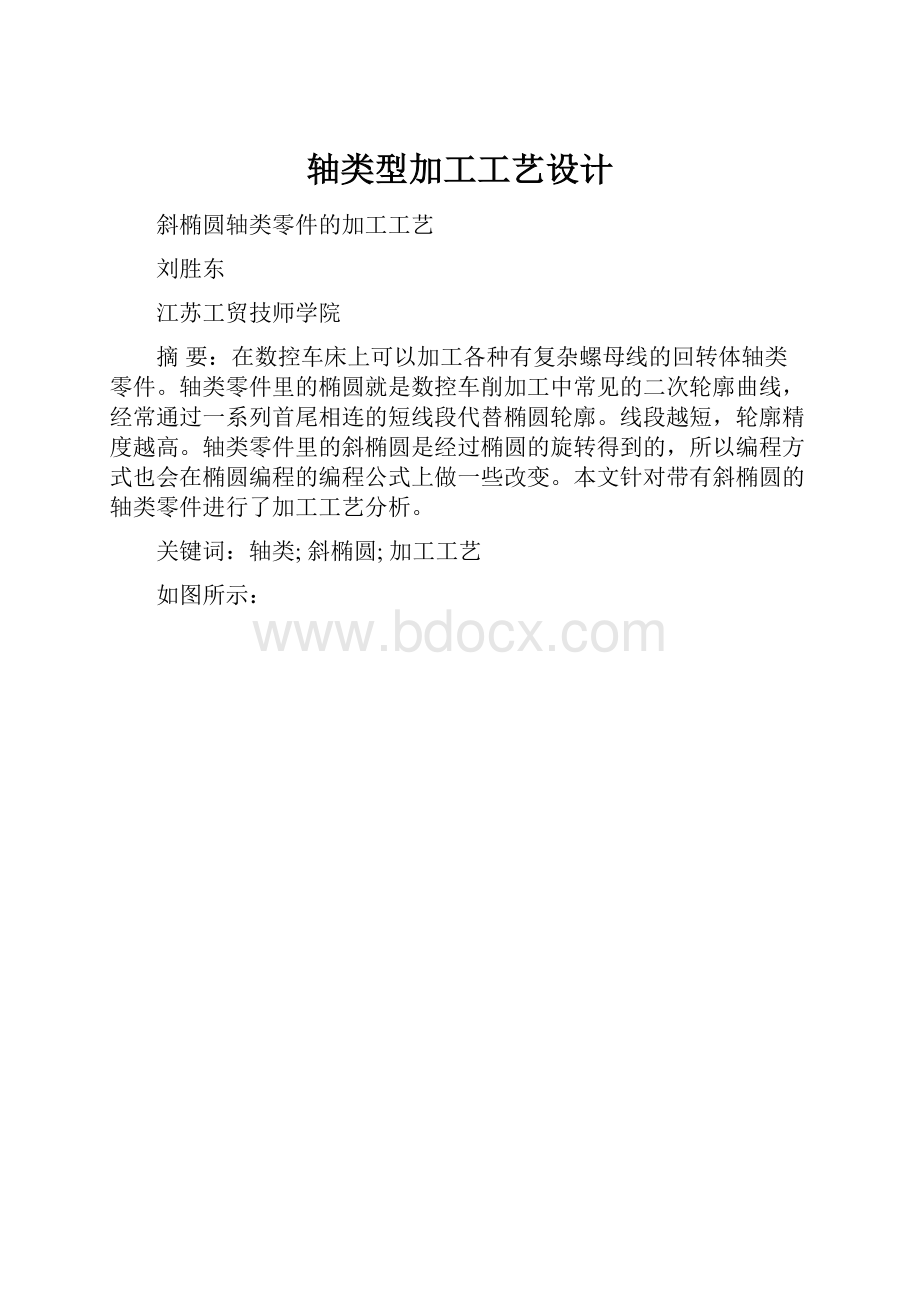
轴类型加工工艺设计
斜椭圆轴类零件的加工工艺
刘胜东
江苏工贸技师学院
摘要:
在数控车床上可以加工各种有复杂螺母线的回转体轴类零件。
轴类零件里的椭圆就是数控车削加工中常见的二次轮廓曲线,经常通过一系列首尾相连的短线段代替椭圆轮廓。
线段越短,轮廓精度越高。
轴类零件里的斜椭圆是经过椭圆的旋转得到的,所以编程方式也会在椭圆编程的编程公式上做一些改变。
本文针对带有斜椭圆的轴类零件进行了加工工艺分析。
关键词:
轴类;斜椭圆;加工工艺
如图所示:
图(A)
一、图纸分析:
1、材料分析:
如(A)所示,该零件所用毛坯料的尺寸为φ50X55的棒料。
材料为45号钢。
45号钢为优质碳素结构用钢,硬度不高易于切削加工。
2、工件结构:
如图(A)所示主要有内轮廓的孔,外轮廓的斜椭圆、圆柱面、沟槽和梯形螺纹组成。
二、加工前准备:
1、机床的选择:
因图(A)中的零件是带有非圆曲线的轴类零件,所选择的机床为数控车床,但是由于各种条件的约束,而且所选择的机床要能加工出合格的零件,本文选择Fanuc0iCAK5085作为加工的机床。
2、夹具的选择:
因为本文所要加工的零件为轴类零件,而三爪自定心卡盘的三个卡爪是同步运动的,能自动定心,一般不需要找正。
并且三爪自动定心卡盘装夹工件方便、省时、自动定心好,但夹紧力小,只适用于装夹外型规则的中、小型工件。
因为我得工件没有行为公差的要求,所以选择三爪自定心卡盘.
3、刀具的选择:
数控机床对刀具的选择有着很高的选择,不仅要求刀具精度高,刚性好,耐用度高,而且要求安装、调整、刃磨方便断屑及排屑性能很好。
所以我选用的刀具材料为涂层硬质合金材料的刀具.
刀具卡片:
序号
刀具号
刀具规格名称
数量
加工表面
刀尖半径
1
T01
45º硬质合金端面刀
1
车端面保证工件长度
0.5㎜
2
T02
90º硬质合金左偏外圆刀
1
粗精车外圆表面
0.8㎜
3
T03
φ16麻花钻
1
钻工件右端的孔
4
T04
硬质合金外槽刀
1
切梯形螺纹退刀槽
4㎜﹙刃宽﹚
5
T05
30º的硬质合金梯形螺纹刀
1
加工左端梯形螺纹
6
T06
硬质合金镗刀
1
镗右端内孔表面
0.4mm
4、切削用量的选择:
(1).背吃刀量:
工件上已加工表面和待加工表面间的垂直距离。
背吃刀量是每次进给时车刀切入工件的深度,所以又称切削深度。
车外圆时背吃刀量计算公式为:
ap=(dw-dm)/2,其中:
ap:
背吃刀量
dw:
工件待加工表面直径
dm:
工件已加工表面直径。
(2).切削速度:
车削时刀具切削刃上某选定点相对于待加工表面在主运动方向上的瞬时速度称为切削速度。
切削速度也可理解为车刀在1mm内车削工件表面的理论展开直线长度。
切削速度可用下式计算:
Vc=dnπ/1000
Vc:
切削速度
n:
主轴转速
d:
工件直径一般取最大直径。
通过查找手册,加工45号钢选Vc为100-300m/min,根据现有加工刀具和设备,选Vc粗=100m/min,Vc精=300m/min.得出我加工所需要的转速.
确定切削用量的意义:
数控加工时对同一加工过程选用不同的切削用量会产生不同的切削效果。
合理的切削用量应能保证工件的质量要求。
如图所示,加工精度最高为0.01mm,粗糙度要求为1.6。
切削不同强度,刚性允许的条件下,充分利用机床功率,最大限度的发挥刀具的切削性能,并保证刀具具有一定的使用寿命。
如果背吃刀量与进给量同时增大,切削力就大,工件的变形也随之变大,对车削工件不利。
如果减小背吃刀量,增大进给量,切削力虽然有所下降,但是工件表面残余面积增大,表面粗糙度也大,强度不好,所以导致工件的内应力增加,工件因此而变形。
所以粗加工时,背吃刀量与进给量可以选的大一些。
精车时,背吃刀量一般为0.2~0.5mm,进给量一般为0.1~0.2mm/r,切削速度一般为60~120m/min。
合理选用车削三要素就可减少切削力,从而减小工件的变形。
5、切削液的选择:
金属切削过程中,合理选择切削液,可改善刀具与工件之间的摩擦状况,降低切削力和切削温度,减小工件摩擦和热变形,从而可以提高刀具的耐用度、加工效率和加工质量。
切削的选择应考虑以下几个因素:
1)润滑具有良好润滑能力的切削液可减少刀具和工件或切削间的直接接触,减轻摩擦和粘结,因此,可减少刀具磨损,提高工件表面质量。
2)冷却具有良好冷却作用的切削液能从切削区域带走大量的切削热,使切削温度降低。
3)清洗具有良好清洗能力的切削液可以冲走切削区域与机床上的细碎切屑和脱落的磨粒,防止划伤已加工表面和导轨。
4)防锈切削液中加入防锈剂,如亚硝酸钠、磷酸三钠和石油硫酸钡等,可以在金属表面形成一层保护膜,起防锈作用。
冷却液名称
主要成分
主要作用
水溶液
水、防锈剂
冷却
乳化液
水、乳化油、乳化剂
冷却、润滑、清洗
切削油
矿物油、动植物油、
复合油
润滑
在加工本文所示轴类零件时根据该工件材料、刀具材料、加工方法、加工要求及冷却液的作用来考虑,我加工时选择乳化液比较合理。
三、工艺性分析:
1、可采用标准刀具和通用量具根据零件的结构尺寸加工零件即钻工艺孔----镗孔----车外圆----切槽----车螺纹
2、规定选择端面和圆轴面在一次装夹完成。
3、正确选择定位基准,确保工件夹紧。
4、分析该轴类零件是否有足够的刚度,能承受夹紧力和切削力,以便提高加工效率。
基于上述分析,可采取以下工艺措施:
(1)、加工的方法:
该零件的实际结构有外表面、孔和螺纹等。
所以加工的重点放在带公差的各个尺寸上,其粗糙度要求均较高,到Ra1.6µm。
利用数控车床的粗车循环功能及精车的恒线速度功能以适当的的切削量,即可达到尺寸的精度要求及保证各表面的粗糙度要求。
因为图(A)中的右端需要手动钻孔,所以在钻孔的同时还要特别注意切削液的使用。
(2)、加工顺序:
加工顺序的确定由粗到精、由近到远的原则确定。
结合图(A)零件的特点,先加工右端φ46圆柱及椭圆—钻孔—镗孔—掉头—左端φ35圆柱—退刀槽—梯形螺纹。
(3)、加工步骤:
首先加工工件的右端。
①、夹紧零件毛坯伸出卡盘29mm。
②、用φ16的麻花钻在工件的右端钻深为19mm的孔。
③、平右端面车1mm即可。
④、粗精加工右端内孔至尺寸要求。
⑤、加工右端外圆面至尺寸要求。
⑥、回换刀点,程序结束。
掉头加工工件的左端。
①、夹紧工件右端φ46长度22mm处。
②、加工工件左端外圆至尺寸要求。
③、加工工件左端梯形螺纹的退刀槽至尺寸要求。
④、加工工件左端Tr35X4的梯形螺纹至尺寸要求。
⑤、回换刀点,程序结束。
加工工序卡片:
序号
程序编号
夹具名称
夹具编号
使用设备
车间
三爪定心卡盘
数控车床
工序号
工步内容
刀具号
刀具规则/mm
主轴转速r/min¹
进给速度mm•r-¹
背吃刀量mm
备注
1
钻深18mm孔
T03
φ16麻花钻
460
手动加工
2
车工件右端面
T01
45°硬质合金端面刀
600
0.3
2
确定机床原点
3
粗镗右端内孔
T06
镗刀
800
0.2
1.5
自动加工
4
精镗右端内孔
T06
镗刀
1000
0.1
0.12
自动加工
5
粗车右端外圆表面
T02
90°外圆偏刀
1200
0.3
1.5
自动加工
6
精车右端外表面
T02
90°外圆偏刀
1600
0.15
0.15
自动加工
7
掉头装夹
夹住工件右端22mm处
8
粗车左端外圆φ35mm处
T02
90°外圆偏刀
1200
0.3
1.5
自动加工
9
精车左端外圆φ35mm处
T02
90°外圆偏刀
1600
0.15
0.2
自动加工
10
车左端梯形螺纹退刀槽
T04
外槽刀
500
0.2
自动加工
11
车左端Tr35×4梯形螺纹
T05
30°梯形螺纹刀
600
0.05
自动加工
四、相关计算:
1、椭圆的标准方程:
X²/a²+Z²/b²=1﹙a﹥0,b﹥0﹚
2、椭圆顺时针旋转315°相当于逆时针旋转45°得到旋转后的斜椭圆的示意图:
图(B)
注:
以图(B)中椭圆的中心为原点。
向右的方向为Z正方向。
向上的的方向为X方向。
顺时针旋转θ度后的公式:
﹙Xcosθ-Zsinθ﹚²/a²+﹙Zcosθ+Xsinθ﹚/b²=1---①
把θ=315°长半轴12,短半轴6代入①式中,经化简得旋转后得椭圆的方程为:
﹙X+Z)²/288+﹙X-Z)²/72=1﹣﹣﹣﹣﹣﹣﹣②
把A、B点得X向坐标代入②式中的到A点到B点的距离为:
5.08。
八、程序中的变量的确定与注意事项:
旋转椭圆程序变量的赋值是一个重要环节,因为宏程序是利用许多段微小的直线来逼近轮廓的,取值大,轮廓表面的逼近误差也大。
在加工中,变量的赋值可以按粗车来取值。
粗加工程序变量的取值应根据预留加工余量的大小来确定,在保证加工不过切的前提下,我们可以选择较大的程序变量,但是也不能过大,变量过大会使精加工余量不均匀或形成过切;精加工时我们主要是保证工件的质量,为使工件的几何形状达到要求,需要减少拟合的误差,因此我们应该选择一个较小的程序变量。
总结
本文简单介绍了斜椭圆轴类零件加工工艺中所涉及到的一些相关问题的解决。
在加工的过程中主要是加工前的准备和工艺的合理安排。
所以在实际加工过程中要特别注意。
这次的论文使我对以前的知识更加的巩固,同时我也发现了自身的不足之处,在以后的学习生活中我会更加的努力。
参考文献:
1、张立新何玉忠数控车削编程与加工北京化学工业出版社2008·7
2、任国兴数控车床加工工艺与编程操作北京机械工业出版社2006·4
3、韩鸿鸾数控加工工艺学北京中国劳动社会保障出版社-2005