高线车间平面布置图.docx
《高线车间平面布置图.docx》由会员分享,可在线阅读,更多相关《高线车间平面布置图.docx(9页珍藏版)》请在冰豆网上搜索。
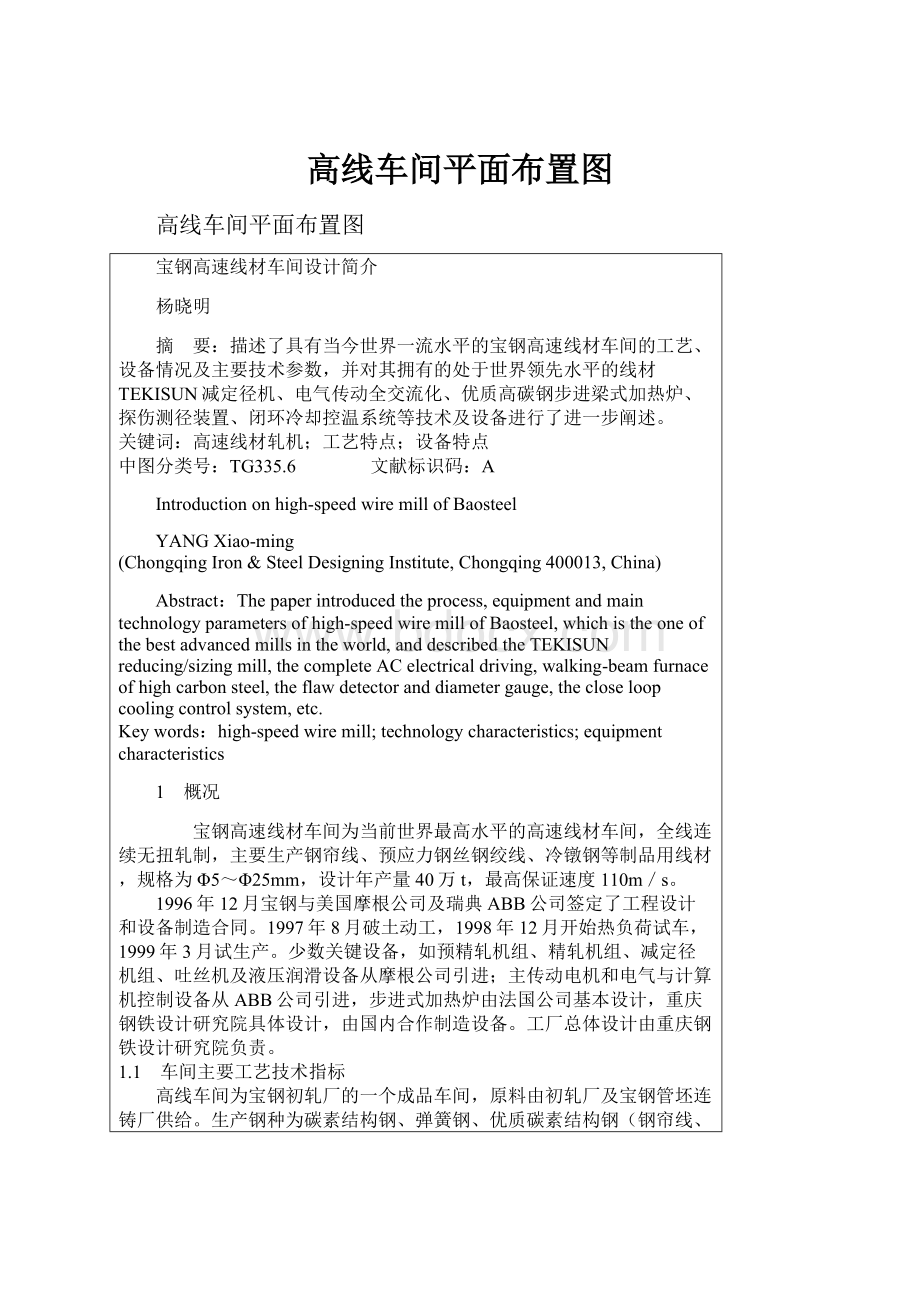
高线车间平面布置图
高线车间平面布置图
宝钢高速线材车间设计简介
杨晓明
摘 要:
描述了具有当今世界一流水平的宝钢高速线材车间的工艺、设备情况及主要技术参数,并对其拥有的处于世界领先水平的线材TEKISUN减定径机、电气传动全交流化、优质高碳钢步进梁式加热炉、探伤测径装置、闭环冷却控温系统等技术及设备进行了进一步阐述。
关键词:
高速线材轧机;工艺特点;设备特点
中图分类号:
TG335.6 文献标识码:
A
Introductiononhigh-speedwiremillofBaosteel
YANGXiao-ming
(ChongqingIron&SteelDesigningInstitute,Chongqing400013,China)
Abstract:
Thepaperintroducedtheprocess,equipmentandmaintechnologyparametersofhigh-speedwiremillofBaosteel,whichistheoneofthebestadvancedmillsintheworld,anddescribedtheTEKISUNreducing/sizingmill,thecompleteACelectricaldriving,walking-beamfurnaceofhighcarbonsteel,theflawdetectoranddiametergauge,thecloseloopcoolingcontrolsystem,etc.
Keywords:
high-speedwiremill;technologycharacteristics;equipmentcharacteristics
1 概况
宝钢高速线材车间为当前世界最高水平的高速线材车间,全线连续无扭轧制,主要生产钢帘线、预应力钢丝钢绞线、冷镦钢等制品用线材,规格为Φ5~Φ25mm,设计年产量40万t,最高保证速度110m/s。
1996年12月宝钢与美国摩根公司及瑞典ABB公司签定了工程设计和设备制造合同。
1997年8月破土动工,1998年12月开始热负荷试车,1999年3月试生产。
少数关键设备,如预精轧机组、精轧机组、减定径机组、吐丝机及液压润滑设备从摩根公司引进;主传动电机和电气与计算机控制设备从ABB公司引进,步进式加热炉由法国公司基本设计,重庆钢铁设计研究院具体设计,由国内合作制造设备。
工厂总体设计由重庆钢铁设计研究院负责。
1.1 车间主要工艺技术指标
高线车间为宝钢初轧厂的一个成品车间,原料由初轧厂及宝钢管坯连铸厂供给。
生产钢种为碳素结构钢、弹簧钢、优质碳素结构钢(钢帘线、胎圈钢丝、预应力钢丝及钢铰线)、冷镦钢和焊条钢。
车间主要工艺设备技术参数见表1。
表1 车间主要工艺设备技术参数
参 数
参 数 值
车间年产量/万t
40
产品规格/mm
Φ5.0~Φ25.0
卷重/kg
2180
盘卷尺寸/mm
Φ1250/Φ850×1800
(外径/内径×高)
产品精度/mm
Φ5~Φ25±0.1
椭圆度为尺寸总偏差的60%
原料规格/mm×mm
轧制坯140×140×13650~14650
连铸坯160×160×10800~11500
轧机型式
30架单线全连续高速无扭线材轧机
终轧速度/m.s-1
Φ5~Φ7mm成品保证速度110
最大操作速度120
车间设备总质量/t
2390
车间电气设备总容量/kW
24965(轧线全交流)
其中 主传动容量/kW
17600
主厂房面积/m2
29067
轧机年工作小时/h
6000
轧机负荷率/%
89.0
1.2 生产工艺流程及工艺平面布置
生产工艺流程如下,
工艺平面布置见图1。
图1 工艺平面布置简图
1-上料台架;2-步进梁式加热炉;3-高压水除鳞装置;4-粗轧机组;5-飞剪;6-中轧机组;7-飞剪;8-预精轧机组;9-水冷段;10-测径仪;11-飞剪;12-精轧机组;13-水冷段;14-减定径机组;15-水冷段;16-测径仪;17-夹送辊吐丝机;18-散卷冷却运输线;19-集卷站;20-PF钩式运输线;21-压紧打捆机;22-卸卷站
2 工程设计特点
该工程设计具有以下特点:
(1)产品大纲以钢帘线、预应力钢丝钢绞线等制品用线材为主,填补了目前我国线材市场高级硬线的短缺与空白,社会效益、经济效益显著。
规格由Φ5.0~Φ25.0mm,扩大了线材产品范围。
Φ5.0mm的产品还可使下部制品工序节约拉拔道次,降低成本,提高竞争力。
(2)采用高速轧制新工艺,保证速度为110m/s,处于世界领先水平,在细线比高达73%的情况下单线年产量为40万t,处于世界先进行列。
(3)所有规格产品的精度均可达到±0.1mm,椭圆度为尺寸总偏差的60%,这一精度为世界先进指标,对金属制品和标准件加工用户极为有利。
(4)机组由30架轧机组成,实现了小延伸精密轧制;粗、中、预精轧机组机架采用平立交替布置,精轧和减定径机组机架呈V型布置,实现全线无扭轧制;机架间采用微张力或活套控制。
由于这些措施的采用,因而产品精度提高,轧制事故减少。
(5)国内首家采用摩根公司最新专利TEKI-SUN轧机技术,即在精轧机水冷段后增加4机架减定径机组。
该工艺具有以下特点:
①可降低高速区线材形变带来的急速温升,实现了低温高速温控轧制,从而可确保产品尤其是高碳优质线材的质量;
②可实现精密轧制,保证尺寸精度,使所有产品规格的精度均可达±0.1mm;
③可实现一定规格的自由轧制,增加产品规格。
如可生产Φ5.75mm产品,满足用户对线材尺寸的特殊要求;
④可简化孔型系统,所有规格产品均由减定径机组完成成品轧制,减少轧线换辊次数,利用减定径机组的快速换辊小车,提高轧机作业率约5%。
(6)轧线设有轧件温度闭环控制系统,使轧件全长温差控制在20℃以内,并可根据需要控制轧件在各变形区的轧制温度。
吐丝温度偏差为±10℃,大风量延迟冷却型Stelmor散卷冷却运输线长103m,大部分钢种可完成在线热处理工艺,可提高产品的冶金质量及性能均匀性,控制氧化铁皮成分组成,减少下部工序热处理道次及表面清理难度,最终获得各方面品质均为一流的产品。
(7)加热炉出口设有大流量、快速(通过速度1m/s)高压水除鳞装置,除鳞效果好,尤其对钢帘线等高碳钢生产十分有利。
(8)精轧机前及减定径机后分别设有1台光学测径仪。
精轧机组后设有涡流探伤仪,对线材表面质量、尺寸精度进行连续监控,快速反馈,减少了调整时间,从而使作业率提高,确保了产品质量及产量。
(9)钢坯加热炉采用侧装侧出料步进梁式加热炉,控制系统网络为二级结构,可完成最佳化燃烧数字模型的计算和控制,使生产操作灵活,钢坯加热温度均匀,氧化烧损减少,脱碳层深度减小,实现了节能降耗。
(10)采用ABB两级自动化控制系统,提高了生产操作水平,减轻了劳动强度。
L1级为电气传动、基础自动化与过程控制级集散型轧钢控制系统,主要完成从上料至卸卷站所有设备全自动控制、轧制区最佳化控制等功能。
L2级为生产管理计算机级,主要完成车间内的物料跟踪、原料及成品库管理、轧辊间管理、质量合同及生产计划管理等工作。
其控制水平在世界同类型线材厂中处于领先地位。
(11)轧线电气系统实现全交流化,更能适应高速线材轧制要求。
交流电动机结构坚固,适应环境能力强,维护和备件储备方面的投资比直流电机减少60%~70%;交流传动功率因素高,可减少或不需无功补偿方面的投资;交流电机采用强迫通风,大都不需水冷,可节约净环冷却水约160t/h,对减少维护投资、提高质量和节省能源、降低生产成本起到了重要作用。
(12)主轧线采用高架平台布置,轧线设备布置在平台上,各种管道、风机、高压水泵站、液压润滑站、电缆、飞剪切头收集装置等布置在平台下,大大改善了设备检修维护条件。
同时减少了大量地下工程量,易于防水,节省投资,尤其对宝钢处于的地理位置,效果明显。
(13)粗轧、中轧立辊轧机下传动,使轧线区域开阔、视线明朗,处理事故容易,立辊换辊时间缩短。
(14)轧辊间上下两层布置,上层与高架平台连接,布置有高速区辊环导卫维护设备,易于高速区的辊环导卫更换。
轧辊间主要设备均采用数字控制系统,自动化程度高。
(15)车间设有性能良好、功能齐全的线材检验室,可承担线材的力学性能测试、金相检验、冷(热)顶锻试验、氧化铁皮检验、低倍酸浸组织检验等工作,满足高等级线材生产的需要。
(16)车间地下室采用先进的低压二氧化碳自动管道灭火技术,灭火效果良好,对人及设备危害很低。
3 主要设备特点
3.1 加热炉
加热炉为辊道侧装侧出步进梁式加热炉,炉子内宽15.3m,有效长度21m,有效面积321.3m2。
实行二级自动化系统控制,共计8个温度自动控制段,严格控制各钢种的脱碳层深度,保证钢坯加热均匀。
炉子额定加热能力为120t/h,最大加热能力为130t/h。
3.2 主轧机
根据钢坯断面、产品规格及其尺寸精度的要求,全线采用连续无扭轧制。
由粗轧6架、中轧8架、预精轧4架、精轧8架及减定径机4架共30架轧机组成。
主轧机基本参数见表2。
表2 主轧机基本参数
工
序
轧机
架号
轧辊直径/mm
主电机
最大
最小
辊身长
功率/kW
型式
粗
轧
1H
650
560
800
400
AC
2V
650
560
800
400
AC
3H
650
560
800
400
AC
4V
495
420
700
400
AC
5H
495
420
700
600
AC
6V
495
420
700
400
AC
中
轧
7H
420
360
650
600
AC
8V
420
360
650
400
AC
9H
420
360
650
600
AC
10V
420
360
650
600
AC
11H
420
360
650
600
AC
12V
420
360
650
600
AC
13H
420
360
650
600
AC
14V
420
360
650
600
AC
预
精
轧
15H
285
255
70
600
AC
16V
285
255
95
600
AC
17H
285
255
70
600
AC
18V
285
255
95
600
AC
精
轧
19~23
228.3
205
71.7
4800
AC
24~26
170.7
153
70.0
减
定
径
27~28
228.3
205
71.7
3200
AC
29~30
156
142
57.3
粗、中轧机组机架呈平立交替布置,为双支点、长辊身、多孔型紧凑机架,立式轧机为下传动。
预精轧机组为悬臂辊环式紧凑型机架,呈平
立交替布置,碳化钨辊环,辊缝由偏心套对称调节。
精轧机和减定径机均为顶交45°超重型无扭轧机,分别由1台交流电机经联合齿轮箱集中传动,碳化钨辊环,辊缝由偏心套对称调节,8架精轧机辊环采用液压专用工具更换,4架减定径机则用换辊小车整机架快速更换。
轧机导卫:
椭圆轧件进入下一机架时及精轧机组、减定径机组入口处均配有滚动导卫,其余断面入口及各机架出口均配置滑动导卫。
3.3 剪机
全轧线共有3台切头尾飞剪,分别布置在6V轧机、12V轧机后、精轧机组前,均为启停工作制。
剪切力分别为520、135、84kN。
在精轧机组前另布置1台碎断剪,事故时使用。
全轧线在粗轧机组前、预精轧机组前、精轧机组前、减定机组前均设置气动卡断剪,以便及时进行事故处理。
3.4 在线涡流探伤仪及光学测径仪
宝钢高线厂在精轧机组后设置1台涡流探伤仪,在线反馈轧件表面质量。
其体积小,精度高,对0.004mm的缺陷均可探到。
在精轧机组前和减定径机组后分别设置1台可移动小车式光学测径仪,ORBIS系统,测量精度为±0.002mm,可在线反映轧件精度,及时调整各轧机机组,提高成品的质量和产量。
3.5 冷却精整区主要设备
(1)吐丝机:
卧式,水平倾角为20°,设计最大速度150m/s,吐圈直径1075mm,一般允许振动值范围2.50~3.81mm/s,最大为5.04mm/s。
(2)散卷冷却运输线:
带有佳灵系统的斯太尔摩标准型及带保温罩的延迟冷却型。
长度103m,保温罩长81m,冷却速度0.3~20℃/s,冷却风机14台,每台风量154000m3/h。
(3)集卷站:
由集卷鼻锥、集卷室、双芯棒回转装置和运卷小车组成,带有线圈分配器及液压分卷装置,集卷周期66s,分卷时集卷周期40s,集卷高度能力3100mm,收集卷高2400mm(带线圈分配器)。
(4)积放式钩式运输机:
长度约560m,钩子60个,运行速度0.25m/s。
(5)压紧打捆机:
卧式,最大压紧力400kN,压紧后最大高度1800mm,带钢捆扎4道。
(6)卸卷站:
液压驱动式,最大储存能力4卷。
4 结束语
近年来全国陆续引进了近10套高速线材轧机,为改善我国线材的产品结构,提高线材质量作出了重要贡献。
但是,高质量制品用线材的生产厂还为数不多。
我国线材市场钢帘线等高品质线材仍然存在被国外产品垄断的情况。
宝钢高线厂利用宝钢优质钢坯,引进世界最先进水平的高速线材生产线,并严格控制产品精度、金相组织、力学性能,保证下部制品的工序流畅和产品质量优良,从而使我国线材生产水平上升到更高层次。
宝钢高线厂于1999年3月投入试生产,7月份完成全部设计规格、钢种线材的轧制,并达到设计性能,同年10月份已生产合格线材22万t,盈利超过1亿元。
作者简介:
杨晓明(1967~),女(汉族),重庆人,工程师。
作者单位:
杨晓明(重庆钢铁设计研究院轧钢室,400013)
收稿日期:
1999-11-2
高速线材工程简介
一、高线轧机的生产工艺:
炼钢的150×150×9000的连铸坯进入钢坯跨用12.5+12.5t的电磁吊车吊上炉后上料台架,由推钢机将其推入18m×9.6m的三段连续式端进侧出的推钢式加热炉内加热到1050~1150℃后,由出钢机推出以拉料夹送辊、出炉地辊输送到轧制区进行轧制。
轧制区由粗轧、1#飞剪、中轧、2#飞剪、预精轧用预水冷、3#飞剪、碎断剪、精轧机组成,全线共有27台轧机轧制27个道次,全线正常生产时在1#、2#、3#飞剪进行三次切头、尾,前两个飞剪还具有事故状态下的碎断功能。
从精轧机出来的成品线材,以三段式穿水冷却进入夹送辊,再由吐丝机吐丝成卷,经过84m长的延迟型斯泰尔摩冷却线进入集卷站,再由总长350m的PF线的50个C型钩之一自动输送到两台压紧打捆机之一进行打捆,再由PF线依次自动输送到计量、卸卷站,然后由10t的电磁吊吊装到库房中堆码。
二、高线轧机主要装备:
全线设备总重1700t(不含液压、润滑设备),其中工艺设备重量1250t。
电器总装机容量15417KW。
1、加热炉区:
⑴12.5+12.5t可自动旋转电磁吊车1台,总重77.79t。
⑵100t推钢机2台
⑶30t齐头机2台
⑷18000×9600mm2三段连续式端进侧出推钢式加热炉1座,额定产量70t/h。
⑸3000kg出钢机1台
⑹上辊液压压下拉料夹送辊1台
2、粗轧区:
⑴Ф330×1000输送辊道1组
⑵Ф580×700水平轧机4台,主电机400KW4台,直流单独传动,机组总重225.04t
⑶Ф470×680水平轧机3台,主电机400KW3台直流单独传动,机组总重110.95t
⑷R235曲柄式飞剪一台,总重28.19t
3、中轧区:
⑴Ф475×680轧机2台,平立交替布置,主电机500KW2台直流单独传动,机组总重77.75t
⑵Ф330×600轧机4台,平立交替布置,主电机500KW4台直流单独传动,机组总重73.63t
⑶回转式飞剪1台,总重20.23t
4、预精轧区:
⑴立式活套4个,总重9.16t
⑵Ф275×95悬臂式辊环轧机4台,平立交替布置,主电机500KW4台直流单独传动,机组总重28.5t
⑶穿水冷却箱1组
⑷轧件输送导槽组
5、精轧区:
⑴回转式飞剪1台,自动回转式转辙器1台,总重6.94Tt
⑵带夹送辊的碎断剪1台,总重2.79t
⑶水平活套1个
⑷Ф210×72德马克型15°/75°高速无扭精轧机组,共10台轧机,由3台1250KW直流电机串联集体传动,机组总重92.05t
6、精整区:
⑴3组水冷箱总长38米,总重14.31t
⑵带夹送辊的吐丝机1台总重10.50t
⑶带保温罩延迟型斯泰尔摩冷却线1条,长度84.645m,总重266t
⑷全自动集卷站一个,包括集卷筒1个,双臂芯轴1套,运卷小车1台
⑸PF线,全长350m,共有50个C型钩,总重120t
⑹液压式半自动打捆机2台
⑺盘卷称量装置1套
⑻卸卷机1套
7、液压与润滑设备:
⑴粗轧与中轧液压、润滑站各1个
⑵预精轧及中轧液压、润滑站各1个
⑶集卷、打捆、称量卸卷、加热液压站各1个
8、水处理:
⑴旋流沉渣池1座,平流池2座
⑵净循环水处理系统1套
⑶浊循环水处理系统1套
9、装备水平:
全线设备中,钢坯电磁吊为全国先进水平,预精轧、精轧机所用油膜轴承为国外进口,全线液压与润滑油脂全部为国外进口,精整线装备为国内一流。
总体装备水平为国内九十年代先进水平。