个别改善的推行方法.docx
《个别改善的推行方法.docx》由会员分享,可在线阅读,更多相关《个别改善的推行方法.docx(35页珍藏版)》请在冰豆网上搜索。
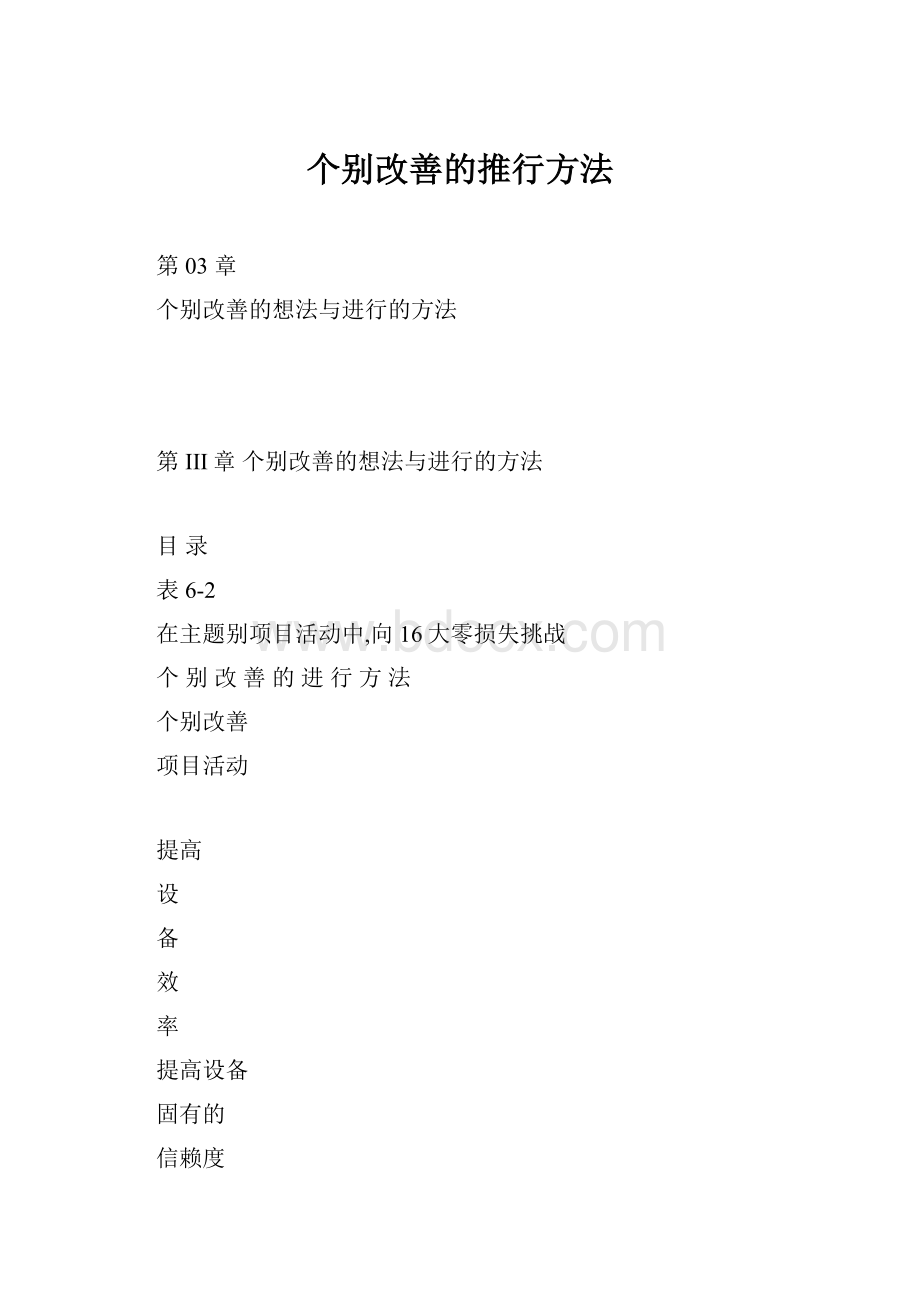
个别改善的推行方法
第03章
个别改善的想法与进行的方法
第III章个别改善的想法与进行的方法
目录
表6-2
在主题别项目活动中,向16大零损失挑战
个别改善的进行方法
个别改善
项目活动
提高
设
备
效
率
提高设备
固有的
信赖度
个别改善
项目活动
16大损失
掌握
确认
项目小组
组成
示范
设备
设定
决定主题
制作推动
计划
水平展开
提高使用信
赖度
防止再发:
标准
重新检讨
.生产技术
.生产现场管理者(Leader)
.设计
1)故障损失
.保养幕僚
故障分析手法
PM分析
机能停止
功能降低
5)短暂停机,空转损失
6)速度下降损失
.其他
7)不良,手工修正损失
16大损失:
2)换模换线,调整损失
自主保养体制
12)物流损失
10)动作损失
IE手法
QC手法
VE手法
其他
3)刀具交换损失
.瓶颈工程
计划保养体制
作业效率低
8)SD损失
质量保养体制
13)测试调整损失
.损失较大
管理,间接部门的效率化体制
14)成品率损失
.水平展开效果较大
决定主题选定顺序条件
.设备.生产线,工程为对象
9)管理损失
需求较多者
11)编成损失
.使它与自主保养示范
设备一致
4)暖机损失
约3个月就可改善者
16)模具,治工具损失
15)能源损失
可能会产生较大成果者
1.个别改善的进行方法
TPM活动中第一个支柱「个别改善」是指设备、人或原物料的效率化也就是追求生产性的极限,并以实质效果为目标。
为了彻底消除16大损失,藉由这个活动,提升及发挥相关人员的技术能力、分析能力、及改善能力。
消除损失若以设备装置为主,是进行将阻碍设备效率化的8大损失降为零的活动,及消除阻碍人的效率化的五大损失中,除了管理损失、编成损失、物流损失之外的其他损失项目。
至于以人为主的组立部门,则以消除阻碍人的效率化的五大损失为活动进行重点。
个别改善活动在TPM活动中与其他支柱的位置,如图III-2所示。
依所负责之损失项目进行改善,必能得到效果。
自主保养
个别改善
·适用于现场的换模换线调整损失等主题
·实施水平展开项目
品质保养
计划保养
管理、间接部门
零管理损失
零工程不良
零故障
图III-2
展开此项活动的意义,是指提升生产性或质量,并降低成本,缔造良好业绩,创造开朗的工作环境。
如图如III-1「个别改善的进行方法」所示,在实施导入阶段时的手法是,在工厂内选定示范设备,以生产技术、保养幕僚、现场管理者等相关人员组成项目小组,以提升生产效率、进行个别改善,并将实绩与成果显现出来。
开始大会(Kickoff)之后的个别改善,则在各课、组、班中选出示范设备,并由现场管理者、幕僚人员、第一线工作人员中的管理层,组成项目小组,并以此示范设备作为项目小组小集团活动的目标,为了有计划、有效率的展开这项活动,必须要在开始大会之前完成,并达成在第I章6.4项中所设定制作个别改善计划表的目标。
1.1个别改善计划的制定方法
为了要完成TPM目标之个别改善计划,首先,在开始大会之前,在各课、组及各生产线工程设备上,确实掌握有关设备、原物料、人员的损失项目并参考表III-1的模式完成改善目标(受审年度之目标)。
特别是有关于人员的生产性方面,比较在BM(BenchMark,基准点)时点和目标时点上的生产体制人员(节省人力之计划),并思考提升设备总合效率时的人员体制。
在以设备为主体的工厂,主要是追求设备总合效率的极限而进行个别改善,以求减少七大损失,而提升生产力与人的要素关系较少。
但在以人力为中心的组立工厂,则以人的五大损失为追求对象,并以提升总合能率为主(参考II-5.6项)进行个别改善活动上,期望追求人员生产性的极限。
实际上,在开始大会前,仍有很多困难的事,因此,不但要完成有关LINE、工程设备的图表,而且要着手进行相关示范线等所有的细节,在开始大会实行后半年之内,彻底的实行推进计划,并设立推进室、个别改善分科会等。
表III-1个别改善计划表实例
生产线、工程、设备、业务名
大主题
中主题
小主题
推进计划
进度状况
达标率(%)
区分
名称
数量
件名
B》M
目标
现状
件名
B》M
目标
现状
件名
B》M
目标
现状
负责
开始
完成
由示范设备、示范产品组成,作为第一项
进行黄;完成蓝;达成红
OO制造生产线
1
提升设备总合效率
降低原料成本
提升人员生产性
个/人
(人)
(个/M)
提升时间稼动率
提升性能稼动率
提升良品率
提升原材料使用率
降低刀具成本
节省能源
总合能率
%
“
“
故障损失
件/MH/M
换模换线、调整损失
次/日分/回
刀具交换损失
次/日分/回
暖机损失
次/日分/回
其他损失
短暂损失
速度损失
工程不良、修整
头尾料损失
刀具损失
排热损失
运转监视损失
物流损失
自动化更换损失
次/日分/回
次/日分/回
TACK分
个/M%
Hr/班
Hr/班
Hr/班
1.2个别改善活动的进行方法
为了有效的推行开始大会之后的个别改善活动,以个别改善为基础,在各厂、各课设定示范线,以便有计划的进行活动。
关于这个进行方法,如下图(表III-2)所示的步骤。
此项进行计划,必须以个别改善分科会或是推进室,彻底的进行推进管理。
并将个别改善计划的推进管理事例(每月的计划追踪表)和水平展开事例列于表III-3、表III-4中。
表III-2展开个别改善的10步骤
步骤
活动内容
步骤1
选定示范设备,示范线,示范工程
·个别改善计划中,瓶颈生产线,工程,设备中损失较多者
·重要性大者,进行水平展开
·与自主保养活动1~3步骤相同对象之设备,工程,生产线
步骤2
组成项目小组
·所属部门的管理者为领导人(部门示范为经理、课示范为课长)
·技术、生产技术、设计、生产的幕僚加入,依损失别由各单位分担
·项目小组由推进室登录并指挥
步骤3
掌握现状的损失
·确认及掌握损失
·损失之数据不足或缺少时,要建立收集这些数据
步骤4
改善主题及目标的设定
·以现况调查结果为基准,设定改善主题
·以零损失的观念,设定挑战的目标和的期间
·决定各损失对策之负责人
步骤5
拟定改善计划
·完成分析、对策、实施改善等顺序、制作推动计划的日程表
·实施高阶诊断
步骤6
进行分析及拟定对策与评估
·活用为改善所做的分析、调查、实验等所有的技术方法和发挥固有的技术,并建立改善案及其评估方法
·不断的追求,直到达成目标为止
·进行高阶诊断(以发表会方式寻找更佳的方法)以求充实
步骤7
实施改善
·实施必要的预算管理,并且实施改善
步骤8
确认效果
·确认实施改善各损失别后的效果
步骤9
标准化
·实施制造标准、作业标准、资材标准、保养标准等必要的标准化与再发防止对策
·制作水平展开手册
·进行高阶诊断
步骤10
·相同的生产线,工程,设备水平展开
(注)·项目小组人员,除本身负责之损失项目外,也要对小组其他人员负责之损失项目进行技术的分析,改善案之支持与检讨,以发挥人际关系之功能。
表III-3个别改善主题一览表
领导人姓名
大项主题
中项主题
小项主题
今后的目标
(设备名)
姓名
BM
实绩
(“91/6)
目标
专案
BM
实绩
目标
目标/实绩
BM
实绩
目标
迈进状况
目标/实绩
%
%
%
担当
开始
结束
状况
N-LINE
(P-1016
P-1014)
示范
提升设备总合效率(%)
总合CT
(秒)
22.0
9.09
30.4
6.58
76.0
2.63
时间稼动率
60.1
66.7
79.7
1.11
换模换线损失(分*回)
30*48
38*46
10*6
王
91/9
91/11
完
成
工具、调整损失(分)
0
70
0
李
91/9
91/11
机械故障损失(分*回)
1560
58*10
50*2
王
91/11
进
O
搬动损失(分)
其他(分)
100
0
55
158
100
0
根
根
91/8
91/9
91/11
91/11
性能稼动率
36.7
45.7
95.3
1.24
短暂停机损失(分)
缩短周期时间(秒)
2992
2.00
2886
2.00
147
2.00
王
91/11
进
O
良品率
100
99
100
1.00
不良、修正损失(次)
20
155
0
李
91/9
91/11
提升人员生产性
(数/人.h)
(人)
(数/月)
提升人员生产性
396.0
0.8
51241
548.7
0.8
72795
1368.0
0.4
90000
省人
(人/班)
2.0
2.0
1.5
100
工作供给装置更新
王
88/4
92/3
进行中
O
N-LINE
(P-1016
P-1014)
示范
提升设备总合效率(%)
总合CT
(秒)
29.1
15.48
39.2
12.41
60.0
7.50
时间稼动率
60.1
66.7
79.7
1.11
换模换线损失(分*回)
21*20
26*30
10*40
王
91/9
91/11
完
成
工具、调整损失(分)
0
70
0
李
机械故障损失(分*回)
1560
58*10
50*2
王
搬动损失(分)
其他(分)
100
0
55
158
100
0
根
根
性能稼动率
36.7
45.7
95.3
1.24
短暂停机损失(分)
缩短周期时间(秒)
2992
2.00
2886
2.00
147
2.00
王
良品率
100
99
100
1.00
不良、修正损失(次)
20
155
0
李
提升人员生产性
(数/人.h)
(人)
(数/月)
提升人员生产性
232.9
05
19403
290.1
1.1
51131
480.0
0.5
37000
省人
(人/班)
1.0
1.0
1.0
100
工作供给装置更新
(课人员)
课长
1
1
1
股长
1
1
1
冲床股
20
25
15
热处理股
5
5
2
配料股
0
0
3
换模股
0
0
0
总合计
27
32
22
(生产性)
生产数
(次/月)
213618
261144
280000
负荷时间
(H/月)
4072.1
4328.5
2975.2
人生产性
(数/人/H)
52.5
60.3
94.1
比率
1.0
1.2
1.8
表III-4个别改善水平展开案例
小项主题:
缩短换模时间
NO
机号
展开项目
1
2
3
示范
4
5
6
7
8
9
1
依据chainblock2系统化将模具吊上作业变成外作业
2
机台旁预加热
3
模具组
2.
个别改善的分析、改善手法和PM分析
个别改善是短期间进行的活动,但是,是对于慢性的问题点,却很难有其效果。
所以要结合有关故障的分析、IE、QC、VE、及独自开发之手法等,以适合者作为主题,并加以改善。
为了分析慢性的课题,若适当的利用故障分析手法之一的PM分析,在短期间内能够发挥效用的实例很多。
2.1个别改善的分析、改善手法
在此介绍有关故障分析手法和IE手法
(1)信赖性的分析、评估手法
在表III-5中显示对设备的信赖性分析,评估所使用的手法。
例如在开发阶段中所使用之FHA,是使用于故障或灾害的分析评估。
故障分析的目的是为了「明显的追溯先前所发生的潜在根源故障,并予以除去」,它从原本的目的、依据之原因、发生的过程、及检查发生之机构、确认以及预测评估的对策。
因此,不可遗漏偶发现象及不可避免的现象。
因此,不但要好好了解基本的分析方法,更重期待能够配合自己公司并加以活用。
参考文献
高木晃研修:
[信赖性工学讲座3
高田嵩着:
信赖性技术-设计制造使用]东京电机大学出版社
监见弘着:
[故障分析和诊断]
表III-5故障分析手法
手法
目的
手法概要
依查核表(CheckList)作安全诊断
实行安全性检讨的第一步、判断要不要分析评估
依方法、经验、技术性判断等作成查核表作诊断
预备事故分析(PHA)
(PreliminaryHazardsAnalysis)
关于系统的开发阶段中的危险的子系统作分析、评估
除去危险的子系统主要是分析评估危险水平和调查防止之手段和效果
故障事故分析(FHA)
(FaultHazardsAnalysis)
关于系统的开发阶段中的全部系统、评估其个别子系统之安全性
针对子系统的要素于故障时直接灾害发生的现象来施行
故障的模式分析(FMA)
(FailureEffectAnalysis)
如果发生故障时,要掌握是属何种模式的故障,并且预防它再扩大和发展
针对系统及机器的各项构成要素,收集可能的故障模式
故障的影响分析(FEA)
(FailureEffectAnalysis)
发生故障模式时,分析对系统及机器的影响
针对各项构成要素及影响较大的项目作重点分析
故障的致命度分析(FCA)
(FailureCriticalAnalysis)
评估故障的影响,而且视其程度分类、建立对策
致命度的水平评估
(作定性的,质的判定)
故障的模式及影响(FMEA)
(FailureModeandEffectsAnalysis)
针对影响系统原因作分析,并找出故障和检修的方法
将FMA,FEA连贯一起进行分析
故障的模式、影响及(FMECA)
致命度模式分析
(FailureModeEffectsandCriticalityAnalysis)
发现致命性的故障模式并建立对策
将FMA,FEA,FCA连贯一起进行分析
现象序列分析(ESA)
(Event-SequenceAnalysis)
以事故或故障的因果关系为基本,求出危险分析发生机率
ETA,FTA的变形
将异常现象的发生以时间顺序作列列展开
现象树分析(ETA)
(EventTreeAnalysis)
针对从发生的原因到最后事故(灾害)的发生之发展顺序并展开防止手段,并检讨评估
针对影响故障大的项目,以发生时间的顺序作分析,并求得信赖度
故障树分析(FTA)
(FaultTreeAnalysis)
针对从发生现象(灾害)发生到发生的原因,展开安全性的分析并加以评估
以定量的分析为基础,将因果关系做统一的表达,并求得灾害的发生机率
故障间隔分析(MTBF)
(MeanTimeBetweenFailure)
评估平均故障间隔,并对发生故障多之处,建立对策
PM分析
调查慢性故障或不良的分析,并建立对策
在设备建设及保养阶段中活用故障分析的手法,如图III-3中所示。
为了对公司内设备做有效的预测检讨,必须对公司内之故障数据(MTBF)或设备制造之其他设备、机器、零件、行为等信赖度及实验室之资料做预测。
图III-3在设备建设及保养阶段中活用故障分析的手法
2.1.2IE手法
在生产现场,是结合人和设备与原料以进行生产,因此,针对机器与人的效率化,有必要将其组合起来,而IE手法是其中重要的工具。
以IE手法来发掘现况的问题点,并且进行改善,图III-4中显示其改善的顺序和重点。
所谓IE的技术,即是指测定技术与分析技术,(如图III-5)依照改善的着眼点,彻底的进行改善案并作检讨。
改善的着眼点
分
析
图III-5IE的测定与分析手法
对于人的行为、动作有目的进行分析,针对此目的价值与其对应的效率问题,是motion-minded所面临的一大重点。
所谓(Motion-minded)是
●对于人员工作方法的浪费,一直注意着并持有警觉性
●拥有改善工作浪费方法的法则及常识
●学得高效率的工作方法的顺序之习惯
2.2PM分析
2.21何谓PM分析
PM分析是将现象(Phenomena)作物理(Physical)分析,并从机构上(Mechanism)做分解说明,并取其第一个字母组成,最适合用于改善慢性损失。
为了降低复杂的慢性损失,以前的改善方法中,均对发生现象未做深入的分析,虽然能列出所能想到的原因,但是,往往会遗漏其中最重要原因,而列出一些不相关的原因,所以即使进行各种对策,也无法有效降低损失,而对此种缺失,使用PM分析是最有效的手段。
P
不适当的要实施复原或改善。
确实实行维持管理,考虑尽量节省工时。
实施复原或改善以及维持管理
依据实际的调查结果,把不合应有的基准值或有微缺陷等加以列出。
把不正常部份列出来
已列单的要因,实际情形是如何?
(是否如预测?
)要调查,要检讨调查方法。
对现象物理的理解
检讨现时的设备精度、标准,为发现缺陷调整其基准。
检讨应有的状态(基准值)
检讨与设备、治具、器工具、材料、作业方法之关连性,认为有因果关系的因素者皆可以列出。
检讨设备、治工具、材料、方法与人的关连性
只要条件齐全、要把会发生的一切案例加以整理
现象成立的条件
现象以物理的想法来加以分析后,从原理、原则来加以说明
对现象物理的理解
现象加以充分的区分
PM分析的步骤
现象的明确化
2.2.2PM分析的8个步骤
(1)第一步骤-明确发生的现象
首先,为了正确的认识现象,并检讨现象的出现、状态、发生的部位、机种间的不同,将现象的型态(PATTERN)进行层别分类。
(以现场、现物的事实为根据将可能之现象,进行层别分析)
(2)第二步骤-对现象作物理的分析
以物理的知识作现象的分析,然后进行结果的讨论,例如,在有损失发生时,分析是与物的接触造成的,或是因撞击而在物性较差的一方所产生的现象。
依据其判断的方法,将变动的要因列举出来。
以下为其方法
A.将现象以物理的看法,将变动要因列举出来。
B.从原理,原则上出发,以系统方式进行,如此就不会将要因遗漏。
C.避免以往直接由直觉即做出判断之举动。
(3)第三步骤-显示现象成立的条件
对构成可能发生现象的所有条件,进行整理。
一般而言,由于对现象成立条件的整理并不充足,就想利用整理出来的条件要因进行对策,也不再考虑其他可能成立的条件,结果是故障及不良,均无法有效降低。
(4)第四步骤-列举各项重要原因
针对各项成立的原因,以原理来思考有因果关系的设备、材料、方法及人的要因,不要考虑影响度的大小,要全部的列举出来。
很意外的,由于不了解设备的机构,动作原理,零件的机能,维持机能必要的精度及调整方法等基础知识,因此常将重要的要因遗漏,所以努力学习上述知识是必要的。
当然,关于材料制品的特性和加工的动静态特性,也要十分的清楚才行。
(5)第五步骤-应有状态的检讨
设定应有状态的项目,亦即以每个重要要因的机构、现物、图面,各项标准为基础,针对其应有的状态作检讨,并应作深入的检讨、学习,且将所检讨,发现不政党之状况,依顺序进行下一个步骤的检讨。
(6)第六步骤-检讨调查方法
针对各要因不正常之状况,而检讨其具体的调查方法和测定方法及范转。
(7)第七步骤-指摘出不正常之点
依据上述所检讨的调查方法,针对各项要因,找出不正常之点。
并注意,不要采取以前的观点和判断基准,应以原有的「应有之状态为何?
」及「微缺陷」之观点,找出不正常之点。
(8)第八步骤-提出实施改善案
针对指摘出之不正常点,订定改善案,并作评估与实施。
简单的PM分析演练
演练1
现象
物理的想法
成立的条件
氯酸钾
红磷
火柴之火无法打着
氯酸钾无法达到起火点
1.氯酸钾和红磷间之摩擦热不足。
2.摩擦热被消耗掉
演练2
现象
物理的想法
成立的条件
刹车毂
来令片
脚刹车的刹车不良
刹车来令片和刹车毂间之摩擦力太小
1.刹车来令片和刹车毂之接触面积太小
2.施予来令片上之力量太小
3.来令片和刹车毂之间有物体存在造成摩擦力变小。
演练:
物理的分析
现象
现象构成要素
连结两者之物理现象为何
物理量之状态
本体
灯泡
电池
脚
滑
地面
1
灯泡不亮
2
在所定的压力,油温下,电磁阀之内部漏油太多
Spool
3
刹车毂
来令片
点焊之熔接不足
外径尺寸有偏差
火柴的为无法打着
脚踏车的刹车不良
4
氯酸钾
红磷
5
工件
电极
工件
车刀
6
7
演练:
物理的分析,成立的条件
(1)
现象
物理的分析
成立的条件
氯酸钾
红磷
1
火柴之火无法打着
2
刹车毂
来令片
脚踏车后轮的刹车效果不好
回转台
工件
砂轮
3
平行度不良
工件加工基准面
演练:
物理的分析、成立的条件
(2)
现象
物理的分析
成立的条件
车刀
工件加工基准面
工件
夹具
4
宽度尺寸有偏差
5
自动铅笔之笔心无法出来
6
汽缸之滑动杆在行进途中停止
2.2.3
采用PM分析时的注意点
由于许多的复合原因组成