气动调节阀检修规程.docx
《气动调节阀检修规程.docx》由会员分享,可在线阅读,更多相关《气动调节阀检修规程.docx(19页珍藏版)》请在冰豆网上搜索。
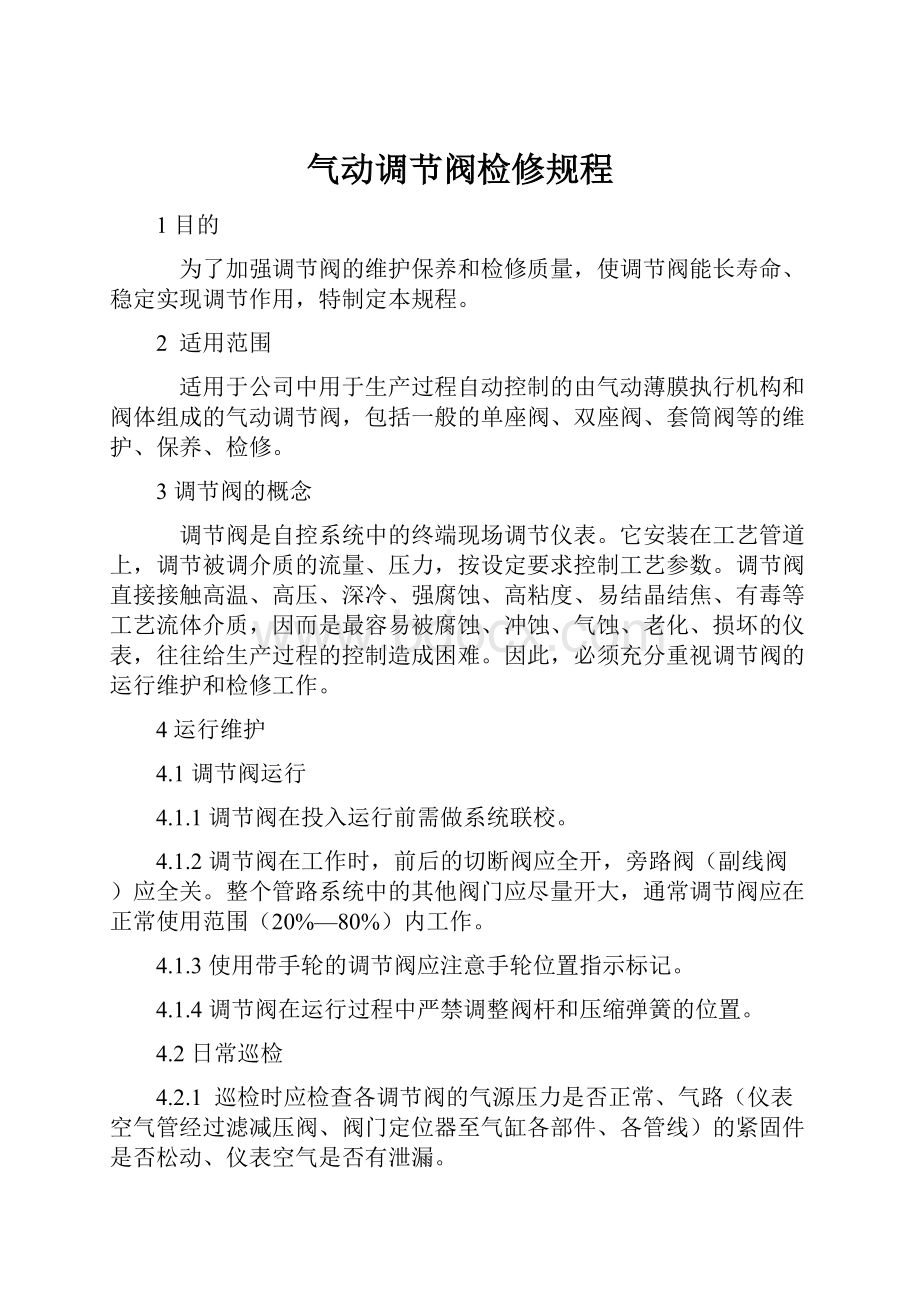
气动调节阀检修规程
1目的
为了加强调节阀的维护保养和检修质量,使调节阀能长寿命、稳定实现调节作用,特制定本规程。
2 适用范围
适用于公司中用于生产过程自动控制的由气动薄膜执行机构和阀体组成的气动调节阀,包括一般的单座阀、双座阀、套筒阀等的维护、保养、检修。
3调节阀的概念
调节阀是自控系统中的终端现场调节仪表。
它安装在工艺管道上,调节被调介质的流量、压力,按设定要求控制工艺参数。
调节阀直接接触高温、高压、深冷、强腐蚀、高粘度、易结晶结焦、有毒等工艺流体介质,因而是最容易被腐蚀、冲蚀、气蚀、老化、损坏的仪表,往往给生产过程的控制造成困难。
因此,必须充分重视调节阀的运行维护和检修工作。
4运行维护
4.1调节阀运行
4.1.1调节阀在投入运行前需做系统联校。
4.1.2调节阀在工作时,前后的切断阀应全开,旁路阀(副线阀)应全关。
整个管路系统中的其他阀门应尽量开大,通常调节阀应在正常使用范围(20%—80%)内工作。
4.1.3使用带手轮的调节阀应注意手轮位置指示标记。
4.1.4调节阀在运行过程中严禁调整阀杆和压缩弹簧的位置。
4.2日常巡检
4.2.1 巡检时应检查各调节阀的气源压力是否正常、气路(仪表空气管经过滤减压阀、阀门定位器至气缸各部件、各管线)的紧固件是否松动、仪表空气是否有泄漏。
4.2.2 巡检时应检查填料函及法兰连接处是否有工艺介质泄漏,压兰及阀杆连接件是否紧固,阀杆是否有严重的摩擦划痕或变形。
4.2.3 巡检时需检查仪表线路的防护情况,仪表进线口密封是否良好。
4.2.4 巡检时应检查阀杆运动是否平稳,行程与输出信号是否基本对应,阀门各部件有无锈蚀,重点是阀杆、紧固件、气缸等。
4.3专项检查
4.3.1 专项检查指不是日常巡检必须进行,但随季节变化或需周期性进行的检查,比如仪表空气带水情况,阀门定位器防雨情况等。
4.3.2 仪表空气带水检查
4.3.2.1在夏季雨水较多和冬季结冰时段,需择机进行仪表空气带水情况检查,因为在夏季,空气湿度大,仪表空气带水会顺空气过滤减压阀、阀门定位器能到达气缸膜室,腐蚀弹簧、损伤膜片;冬季空气凝点低,仪表空气带水会堵塞气路,造成阀门失效。
4.3.2.2在检查仪表空气带水时,可在仪表空气管路末端进行排污(有些地方设末端排污球阀),观察带水情况。
如果没有排污阀,需征得工艺操作人员同意(填写《检修工作票》),按调节阀检修处理,
将仪表管路从气源球阀后拆开,观察带水情况。
检查结束后与工艺人员交代清楚,填写操作票的完成情况。
4.3.3防雨检查
在夏季雨后,需安排进行防雨检查,主要检查阀门定位器仪表接线口是否进水受潮。
4.4维护保养
4.4.1保养主要指对阀门各部件进行润滑、清理,延长阀门各部件使用寿命。
4.4.2定期清扫,保持整洁,特别是阀杆、定位器的反馈杆等活动部位;清扫一般半月一次;对于需加润滑油的填料,一般每星期加油一次,并使注油器内有足够的存油,润滑油的品种不得随意变更。
5调节阀的检修
5.1对调节阀检修前,需填写《检修工作票》,征得调度及工艺人员同意并签字,待工艺人员关闭自调阀前后截止阀,如果截止阀有泄漏,应加装盲板,并用旁路阀调节后,工艺人员现场监护各项安全措施落实到位后,待阀内介质降温、泄压后,方可开始调节阀的检修。
5.2检修的一般程序
打标记→(下线)→清洗→解体→零部件检修→研磨→装配→调校与试验→(上线)→动作检查→回路联试→投运。
5.3打标记
为保证调节阀离线检修后能正确复位,应重视打标记程序。
应能清晰标明以下方位
5.3.1调节阀阀体法兰与管道法兰的连接方位;
5.3.2阀体与上、下阀盖及其执行机构的连接方位。
5.4清洗
滞留在阀体腔内的某些工艺介质是具有腐蚀或有毒的,在进入解体工序前必须以水洗或蒸汽吹扫的方法,将调节阀被工艺介质浸渍的部件清洗干净。
5.5解体
5.5.1气开式调节阀需往薄膜气室加入适当的气压信号,使阀芯与阀座脱离接触后,再旋转阀杆,使之与执行机构的推杆分离。
5.5.2有如必要,需将执行机构组件完全分解,对薄膜、弹簧等易损件进行检查。
5.5.3在阀门分解后所得的零部件应集中存放,以防散失或损伤。
5.6零部件检修
5.6.1生锈或脏污的零部件要以合适的手段进行去锈和清洗,要注意清洁好机加工面,特别要保护好阀杆、阀芯和阀座的密封面。
5.6.2重点检查部位
5.6.2.1阀体:
阀体的内壁和连接阀座的内螺纹处易受流体介质的腐蚀和冲蚀。
5.6.2.2阀座:
密封面、与阀体连接的外螺纹处易受腐蚀和气蚀。
5.6.2.3阀芯/阀杆组件:
阀芯的密封面和调节曲面以及导向圆柱面处均易受到腐蚀和磨损的;阀杆上部与密封填料接触部位不得松动,阀杆不得弯曲。
5.6.2.4上阀盖的填料函处的腐蚀。
5.6.2.5阀体、上阀盖、下阀盖各法兰密封面的腐蚀程度。
5.6.2.6执行机构中薄膜片和“O”形密封圈老化、裂损程度。
5.6.3根据零部件损伤情况各异,决定采用更新或修复处理。
5.6.3.1每一次检修,不论损伤与否,必须更新的零件有密封填料、法兰垫圈、“O”形密封圈。
5.6.3.2经检查发现损伤而又不能保证下一运行周期工作的零件应予更换,如薄膜片、弹簧等。
5.6.3.3其余的各式零部件如损伤严重时,应予更新;轻度损伤时,可采用补焊、机加工等手段予以修复。
5.7装配
5.7.1在装配的全过程中要特别重视各零件相互间的对中性。
5.7.2阀体与上、下阀盖组装时,应采取对角线“十”字逐次旋紧法。
螺栓上应涂抹润滑剂。
5.7.3密封填料装配时需注意以下几点:
5.7.3.1 在使用开口填料时,应使相邻两填料的开口相错180°或90°。
5.7.3.2在一般情况下,“V“形填料的开口向下,但在真空阀中使用时,应使开口向上。
5.7.3.3对需定期向填料加注润滑油的调节阀,应使填料函中的填料套(亦称灯笼环)处于适中位置,与注油口对准。
5.7.3.4按填料的材质选用合适的润滑密封油膏。
5.7.4执行机构与阀两大部件组装时,要注意解体前所做的标记,确保相对方位恢复原位。
5.8调校与试验
5.8.1调节阀的调校与试验前需得到工艺确认,校验过程需认真填写《调节阀调试记录》。
5.8.2基本误差校验
将输入信号平稳地按增大和减小方向给阀门定位器,观察各点所对应的行程值,试验点为输入信号范围的0%、25%、50%、75%、100%五个点,各点偏差应在±1%左右。
5.8.3回差校验
在同一输入信号所测得的正反行程的最大差值即为回差。
用调节阀的额定行程的百分数表示,不应超过1.0%。
5.8.4始终点偏差校验
将输入信号的上、下限值分别加入定位器,测量相应的行程值,偏差不应超过1%。
要特别注意到保证气开式调节阀的始点、气关式调节阀的终点在阀关位置上。
5.8.5死区校验
在输入信号的25%、50%、75%三点上进行校验,方法为缓慢改变(增大或减小)输入信号,直到观察出一个可察觉的行程变化(0.1mm),此点上正、反两方向的输入信号差值即为死区。
不应超过全量程的3%。
5.9阀门检修后,各部件按要求紧固安装后,调试合格后,由工艺人员开启前后截止阀,关闭旁路阀,待调节平稳后将《检修工作票》填写完整,清理好现场,做到“工完、料静、场地清”。
6.调节阀常见故障、产生原因及处理方法
6.1 有输入信号但无动作
6.1.1执行机构故障:
检查执行机构
6.1.2阀杆弯曲或折断:
更换阀杆。
6.1.3阀芯脱落(螺母松扣):
拧紧螺母。
6.1.4阀芯与衬套或套筒卡死:
检查同轴度并重新安装。
6.1.5定位器中放大器的恒节流开堵塞:
用细铜丝去除恒节流孔中杂物。
6.2阀全闭时泄漏量大
6.2.1阀芯或套筒密封面腐蚀、磨损:
轻度可研磨阀芯密封面,重度更换阀芯、套筒。
6.3阀达不到全闭位置
6.3.1介质差压大于阀的允许差压:
选取大一档输出力的执行机构或安装定位器。
6.3.2阀体内有异物:
清除异物。
6.4阀动作不稳定有振动现象
6.4.1执行机构刚度偏小:
选取大一档刚度的执行机构或安装定位器。
6.4.2阀杆摩擦力大:
减少阀杆摩擦。
6.4.3支撑不稳:
加固支撑。
6.4.4附近有振动源:
消除振动源。
6.5密封填料渗漏
6.5.1填料压盖没压紧:
压紧填料压盖。
6.5.2填料变质损坏;更换填料。
6.5.3阀杆损坏:
更换阀杆。
6.6阀动作迟钝
6.6.1阀体内有泥浆或粘性大的介质,使阀堵塞或结焦:
清除。
6.6.2填料硬化变质:
更换填料。
6.6.3膜片漏气:
更换膜片。
气动调节阀检修规程
(适用于单座/套筒/双座)
1.总则
我公司是生产制造各类切断阀、调节阀、执行机构及附件的国家重点企业。
生产加工设备齐全,技术力量雄厚,拥有国内最大的流量试验装置。
是多家国际品牌阀门的代理商,产品广泛用于石油、化工、电力、制药、橡胶、造纸、煤炭等行业。
我公司除了为广大用户提供一流完好的产品外,还常年提供本公司阀门、国内其他厂家及国外制造的阀门产品的定期维护、检修、抢修、保运。
经我公司检修的阀门,完全按照同品级新产品的技术标准和试验手段进行,质保期等同于新品。
2.准备工作
2.1注意事项:
检修人员在进入检修现场时,要佩带好安全帽、手套、眼镜等防护用品。
并与岗位人员联系好,确认阀门所在管线是否与生产系统断开,管线内物料是否处理干净,电源、气源是否切断,一切具备条件后方可进行拆卸。
2.2在生产现场拆卸阀门时,先松开两端法兰螺栓,在固定好阀门后(人抬或者机器吊装)方可退掉所有连接螺栓,把所有螺栓、垫片、螺母等附件交给岗位或我方妥善保管。
2.3对送检的阀门在搬卸过程中,也要佩带好手套,不要裸手直接接触阀门。
2.4待修阀门送入检修车间后,首先检查阀门的故障点或根据用户反映的情况做针对性检查并记录。
2.5对定位QI、过滤器、电磁阀、气源接口、介质流向要特别标注记录并拍照。
2.6对阀门建立档案,包括:
用户单位、测控位置、阀门位号、介质名称、入库时间、外观描述、故障说明、交货期限、附件说明等,见表1。
2.7用数码相机对阀门整体、阀门所带的重要附件、阀门故障点、标牌、重要连接位置从多个角度进行拍照,并把图片编号连同2.4、2.5、2.6记录的内容一起存入公司检修档案库内。
2.8用高压水枪对阀体的内腔和外部进行简单的清洗,清除残余物料和污垢,清洗时要佩带胶皮手套和防护眼镜,以免阀门内腐蚀性物料喷溅伤人。
2.9安装好定位QI,对0%、25%、50%、75%、100%各个点进行实际标定,并填写好检测记录,存档保存。
2.10在每台阀门上挂一个检修计划卡,注明用户单位、位号、入库日期、主要故障、计划工期、达到的标准。
2.11对执行机构与阀门、上阀盖与下阀体要用特殊线或符号做标注。
表1 阀门检修登记卡
阀门检修登记卡
编号
用户单位
阀门档案
测控位置
阀门位号
介质名称
阀门名称
阀门型号
阀门规格
外观描述
故障说明
附件说明
备注
入库时间
交货期限
经办人
检修单位
表2 阀门检修计划卡
阀门检修计划卡
用户单位
阀门位号
检修编号
故障说明
检修内容
达到标准
入库时间
计划工期
经办人
检修人
检修单位
3.阀门的拆分
3.1阀门先按执行机构、阀体、QI及附件三部分拆分。
3.2根据各个部件的标牌和实物详细登记执行机构、阀体、定位QI的型号、规格、生产日期及外观状况。
3.3对执行机构进行通气测试并填写记录;对执行机构进行拆分和外观检查并填写记录。
3.4对阀体进行拆分,对阀体和阀内各个部件进行外观检查并填写记录。
3.5分段拆分步骤
3.5.1断开QI及附件与阀门的连接。
3.5.2断开执行机构推杆与阀杆之间的连轴节或螺扣。
3.5.3拆下执行机构支架和阀体的连接螺栓或螺母压帽。
3.5.4用手锤敲打垫在阀体或支架上的木方,使之分离。
3.6阀体拆分步骤
3.6.1把阀门上盖螺丝拆下,用手锤轻敲阀体,使阀体与上盖分开。
3.6.2把压兰螺丝拆下取出压兰,拆下阀杆螺母,从上阀盖侧取出阀芯和阀杆。
3.6.3取出轴套和密封填料。
3.6.4用专用工具取出阀座。
3.6执行机构拆分步骤
3.6.1拆下两个膜盖螺丝,用较长螺丝替换,带上螺母。
3.6.2均匀松开膜盖上各个方向的螺丝,逐渐释放弹簧的弹力,切不可急于求成,以免弹簧伤人。
3.6.3在弹簧卸力后,取下上膜盖、膜片、弹簧、和推杆。
4.确定检修、修复、完善内容
4.1在不做任何调整的情况下,对定位QI分别进行性能检测,填写检验记录。
4.2对阀芯和阀座进行精密测绘并填写记录。
4.3根据上面的外观检查记录、性能检测记录、精密测绘记录,确定各个阀门部件需要修复的范围、内容、标准、工期及所需材料、专用工具等。
5.阀内件的修复
5.1确认阀座与阀芯的密封线损伤情况,轻微磨损可采用研磨进行效准。
5.2对于阀座、阀芯严重损伤情况,先确认其材质,然后进行实物测绘与阀特性计算相结合的方式,确定阀座的零件加工尺寸图纸。
5.3对于阀座、阀芯轻微损伤情况,先确认其材质,然后用氩弧堆焊、司太莱堆焊及金属材料喷焊补齐,再上车床进行加工,这样反复几次,最终达到新品的等级标准,并根据现场使用情况或用户要求进行高温热处理。
5.4把加工好的阀芯和阀座放在研磨机上进行粗磨(粗砂),每研磨5-8分钟,观察阀芯和阀座密封线结合情况,进行几个周期后,改为细磨(细砂),每研磨5-8分钟,观察阀芯和阀座密封线结合情。
研磨到完全结合为止。
5.5外观观测阀杆的曲直度,偏差明显的可考虑重新制造,确认材质、实物测绘、绘制图纸、精密加工。
5.6对于套筒型阀座,阀杆与阀芯(套筒)装配完后(焊接或丝扣固定),要进行找正,阀杆与套筒的偏差不能大于套筒和阀座间的间隙量。
对于超差情况,要及时更正,重新装配、标定,直到合格为止。
6.组装
6.1把阀座固定在下阀体内,垫好上阀盖与下阀体间的密封垫片(垫片必须更换新的),放入阀芯组件,合上上阀盖,按对角线方向逐个紧固阀盖螺栓。
6.2逐个加入密封填料(填料必须更换新的),用压兰压紧后固定,压兰螺丝要均衡把紧。
6.3把弹簧、膜片、推盘、密封环依次装入气室内,盖好上膜盖,用螺丝紧固。
6.4用螺丝固定阀体和支架。
6.5对于正作用执行机构,要在气室通入比额定的最大气信号小15-20KPa的气信号时,连接阀杆和执行机构推杆,以确保关闭时阀门泄漏量最小。
6.6对于反作用执行机构,要在气室不通入比最小气信号大15-20KPa的气信号时,连接阀杆和执行机构推杆,以确保关闭时阀门泄漏量最小。
7.打压试验
7.1强度试验:
阀门组装后进行打压试验,先把阀门放在打压设备试验台上夹紧,然后启动打压泵。
同时从进口、出口加压,逐渐提高水压,直至升高到该阀公称压力的1.5倍为止。
此时,观察下阀体、上阀盖、阀盖连接处、密封填料等处有无泄漏并填记录。
如无泄漏,说明打压合格,进行下一步。
有泄漏时,找出泄漏原因,重新组装、打压,直到合格为止。
如果是下阀体和上阀盖渗漏,只能更换新的。
7.2泄漏试验:
阀门组装后进行内漏试验,把阀门进口端接在打压泵上,增加(气关阀)或者减少(气开阀)气信号,使得阀门关闭。
启动打压泵,逐渐提高水压,直至升高到该阀最大关闭压差的1.2倍为止。
此时,观察阀门出口渗漏情况,按泄漏等级的标准,核实泄漏是否超标,并填记录。
如符合标准要求,说明内漏测试合格,进行下一步。
超出标准很多时,重新调整阀杆和推杆的初始位置,直到合格为止。
如果仍然不合格,打开阀体,对阀芯和阀座进行重新研磨、组装、打压、测试,直到合格为止。
8.调试与测试
8.1确认阀门关闭位置指针是否指在刻度盘的关闭位置上,如果不是,需调整。
8.2执行机构推杆上部涂一层润滑脂,阀杆下部应涂少量机油。
8.3增加(气开阀)或者减少(气关阀)气信号,使得阀门开到最大位置,确认指针与刻度盘是否应吻合,误差不应大于全行程的百分之二。
如果误差超过允许范围,断开阀杆和推杆的连接件,重新调整阀门初始位置,并做内漏测试。
8.4按额定气信号分别标定0%、25%、50%、75%、100%各点,填写效验记录。
8.5安装好阀门定位QI,设定好减压阀输出压力值,进行整机调试,分别标定0%、25%、50%、75%、100%各点,记录下各点的实际值,计算相对误差和变差,误差在允许范围内,即为合格,填写检验记录。
如果超标,重新调整标定,直到合格为止。
9.喷漆
阀门组装、打压、测试、检验完成后,应根据用户要求或者原阀门的颜色进行喷漆。
喷漆前,要对锈蚀和磨损部位进行除锈、打磨、抛光处理。
喷漆时,要把执行机构推杆、阀杆、行程牌、标牌、定位QI、气源管路、电磁阀等部位用胶带包好,等漆干后拆除。
10.产品检验报告。
产品检验报告
制表单位:
品名
型号
规格
编号
1.误差检验:
输入值
标准值
实际值
(KPa)
(%)
上行
误差
下行
误差
变差
0
25
50
75
100
最大允许误差
最大允许变差
实际基本误差
实际基本变差
2.强度试验:
按公称压力的1.5倍做水压试验,即( )MPa,阀体和密封均无渗漏。
3.泄漏试验:
按最大压差的1.2倍做水压试验,即( )MPa,泄漏等级为( )级。
4.检验结果
检验人
审核人
日期
1 技术标准
1.1 外观
零部件齐全,装配正确,紧固件不得有松动,损伤等现象,整体整洁。
1.2 气源压力
最大值为500 KPa,额定值为250 KPa。
1.3 输入信号范围
1.3.1 标准压力信号范围为20~100 KPa或40~200 KPa;
1.3.2 带有电/气阀门定位器时,标准信号范围为4~20mA DC;
1.3.3 两位式控制时,可在气源压力额定值内任意选取。
1.4 执行机构室的密封性
将设计规定的额定压力的气源通入封闭气室中,切断气源,5分钟内薄膜气室中的压力下降不得超过2.5 KPa
1.5 耐压强度
调节阀应以1.5倍公称压力进行不少于3min的耐压试验,不应有肉眼可见的渗漏;
1.6 填料函及其它连接处的密封性
应保证在1.1倍公称压力下无渗漏;
1.7 泄漏量
调节阀在规定试验条件下的泄漏量应符合国家标准GB/T4213-92《气动调节阀》规定的要求。
2 检查与校验
2.1 外观检查
按本节第1.1条要求,用肉眼观察的方法进行检查
2.2 执行机构气室的密封性试验
按本节1.4要求将额定压力(一般为140 KPa或250 KPa)的气源输入薄膜气室中,切断气源。
2.3 耐压强度试验
按本节1.5要求,用1.5倍公称压力的室温水,在调节阀的入口方向输入阀体内,另一端封闭,使所有在运行中受压的阀腔同时承受5min的实验压力,试验期间调节阀应处于全开位置。
2.4 填料函及其它连接处的密封性实验。
按本节1.6条要求,用1.1倍公称压力的室温水,按规定的入口方向输入调节阀的阀体,另一端密封,同时使阀杆作1~3次往复动作,持续时间应少于5min观察调节阀的填料函及上、下阀盖与阀体的连接处。
2.5 泄漏量试验
按本节1.7条要求,在薄膜气室中按不同作用方式输入一定的操作气压,使调节阀关闭。
将室温水以恒定压力按规定的入口方向输入调节阀,另一端放空,用秒表和量杯测量其1min的泄露量。
2.5.1 操作气压
2.5.1.1 气开式调节阀操作气压为0 KPa
2.5.1.2 气关式调节阀
2.5.1.3 弹簧范围为20~100 KPa的调节阀,其操作气压为120 KPa;
2.5.1.4 弹簧范围为40~200 KPa的调节阀,其操作气压为240 KPa;
2.5.2 试验水压
2.5.2.1 当调节阀允许压差大于0.35MPa时;实验压力为0.35Mpa;
2.5.2.2 当调节阀允许压差小于0.35MPa时;实验压力用设计规定的允许压差。
2.5.3 泄漏的计算公式按国家标准GB/T4213-92《气动调节阀》的规定进行。
3 运行维护
3.1 调节阀在投入运行前应做系统联校。
3.2 调节阀工作时,前后的切断阀应全开,副线阀应全关。
整个管路系统中的其他阀门应量开大,通常调节阀应在正常开度范围(20%~80%)内工作。
3.3 使用带手轮的调节阀应注意手轮位置指示标记。
3.3.1 手轮侧装的,应在中间或“自动”位置。
3.3.2 手轮顶部安装的,应在最高位置。
3.3.3 作限位用的,应在预定位置。
3.4 调节阀在运行中严禁调整阀杆和压缩弹簧管的位置。
3.5 经常检查调节阀及定位器等附属设备。
3.5.1 气源及输入、输出信号是否正常。
3.5.2 阀杆运动是否平稳,行程与输出信号是否对应。
3.5.3 连接管路是否严密不漏。
3.5.4 填料函及法兰连接处有无介质外漏;检查中发现的问题要及时作技术性处理,以保证调节阀正常运行。
∙
3.6 定期清扫,保持整洁,,特别是阀杆、定位器的反馈杆等活动部位。
3.7 需将生产现场对调节阀进行解体检查时,必须将调节阀两边的截止阀关闭,如截止阀有泄漏,应加盲板,待阀内介质降温,放空降压后方可进行。
4 检修
4.1 停工检修时,在调节阀离线前,应将放空阀打开,降温降压。
经生产装置有关人员确定,方可离线检修。
4.2 检修程序
打标记 (下线) 清洗 解体 零部件检修 研磨 装配
调校与试验 (上线) 动作检查 回路联试 开车联运。
4.3 打标记
4.3.1 调节阀阀体法兰与管道法兰的来年界方位;
4.3.2 阀体与上、下阀盖及其执行机构定的连接方位。
4.4 清洗
滞留在阀体腔内的工艺介质具有腐蚀或放射性,解体前必须以水洗或蒸汽吹扫的方法,将调节阀被工艺介质浸渍的部件清洗干净。
4.5 解体
4.5.1 对各连接部位喷洒松锈剂,使解体工作省时省力。
4.5.2 气开式调节阀须注膜室加入适当的气压信号,使阀芯与阀座脱离接触后,方能旋转阀杆,使之与执行机构的推杆分离。
4.5.3 必要时,须将执行机构组件完全分解,对薄膜、弹簧等易损件进行检查。
4.5.4 每一台调节阀分解后所得的零部件应集中存放,以防散失或碰伤。
4.6 零部件检修
4.6.1 生锈或脏污的零部件要以合适的手段去锈和清洗,要注意清洁好机加工面,特别要保护好阀杆、阀芯和阀座的密