化工资源及其初步加工Word文档下载推荐.docx
《化工资源及其初步加工Word文档下载推荐.docx》由会员分享,可在线阅读,更多相关《化工资源及其初步加工Word文档下载推荐.docx(20页珍藏版)》请在冰豆网上搜索。
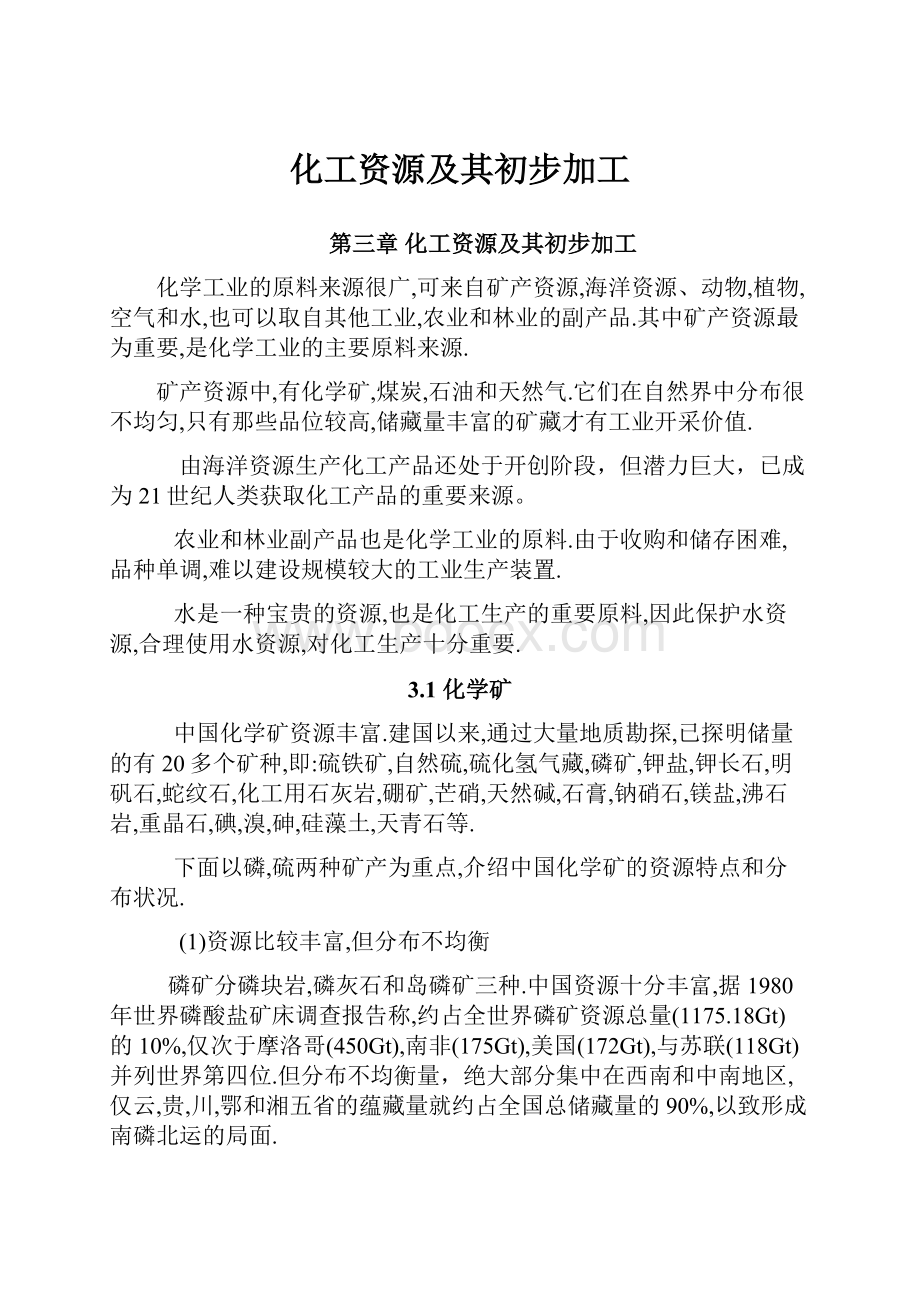
一、概述
(一)石油的组成与性质
石油又称原油,是从地下深处开采的棕黑色可燃粘稠液体。
石油是古代海洋或湖泊中的生物经过漫长的演化形成的混合物,与煤一样属于化石燃料。
组成石油的化学元素主要是碳(83%~87%)、氢(11%~14%),其余为硫(0.06%~0.8%)、氮(0.02%~1.7%)、氧(0.08%~1.82%)及微量金属元素(镍、钒、铁等)。
由碳和氢形成的烃类构成石油的主要组成部分,约占95%~99%,含硫、氧、氮的化合物对石油产品有害,在石油加工中应尽量除去。
不同产地的石油中,各种烃类所占比例相差很大,这些烃类主要是烷烃、环烷烃、芳香烃。
通常称以烷烃为主的石油为石蜡基石油;
称以环烷烃、芳香烃为主的为环烷基石油;
介于二者之间的称为中间基石油。
我国主要原油的特点是含蜡较多,凝固点高,硫含量低,镍、氮含量中等,钒含量极少。
除个别油田外,原油中汽油馏分较少,渣油占l/3。
组成不同的石油,加工方法有差别,产品的性质也不同,应当物尽其用。
大庆原油的主要特点是含蜡量高,凝固点高,硫含量低,属低硫石蜡基原油。
(二)石油炼制工业的发展
石油的发现、开采和直接利用由来已久,炼油工业始于19世纪30年代,到20世纪40~50年代形成的现代炼油工业,是最大的加工工业之一。
19世纪30年代起,陆续建立了石油蒸馏工厂,产品主要是灯用煤油;
汽油尚无用途当废料抛弃。
19世纪70年代建造了润滑油厂,并开始把蒸馏得到的高沸点油做锅炉燃料。
19世纪末内燃机的问世使汽油和柴油的需求猛增,仅靠原油的蒸馏(即原油的一次加工)不能满足需求,于是诞生了以增产汽油、柴油为目的,综合利用原油各种成分的原油二次加工工艺。
如1913年实现了热裂化,1930年实现了催化裂化,1940年实现了催化重整,此后加氢技术也迅速发展,这就形成了现代的石油炼制工业。
20世纪50年代以后,石油炼制为化工产品的发展提供了大量原料,形成了现代的石油化学工业。
1999年全世界的石油加工能力为38×
108t,我国为1.5×
108t。
大型炼油厂的年加工能力已超过1×
107t。
二、石油产品
石油产品可分为:
石油燃料、石油溶剂与化工原料、润滑剂、石蜡、石油沥青、石油焦等6类。
其中,各种燃料产量最大,约占总产量的90%;
各种润滑剂品种最多,产量约占5%。
各国都制订了产品标准,以适应生产和使用的需要。
汽油是消耗量最大的品种。
沸点范围(又称馏程)为30~205℃,商品汽油按其在气缸中燃烧时抗爆震燃烧性能的优劣区分,标记为辛烷值70、80、90或更高。
号愈大,性能愈好。
汽油主要用作汽车、摩托车、快艇、直升飞机、农林用飞机的燃料。
商品汽油中掺入添加剂(如抗爆剂)以改善使用和贮存性能。
喷气燃料主要供喷气式飞机使用。
沸点范围为60~280℃或150~315℃(俗称航空煤油)。
为适应高空低温高速飞行需要,这类油要求发热量大,在一50℃不出现固体结晶。
煤油沸点范围为180~310℃,主要供照明、生活炊事用。
要求火焰平稳、光亮而不冒黑烟。
目前产量不大。
柴油沸点范围为180~360℃和350~400℃两类。
前者称为轻柴油,后者称为重柴油。
商品柴油按凝固点分级,如10、一20等区分不同牌号,表示最低使用温度。
柴油广泛用于大型车辆、船舰。
由于高速柴油机(汽车用)比汽油机省油,柴油需求量增长速度大于汽油,一些小型汽车也改用柴油。
对柴油质量要求是燃烧性能和流动性好。
燃烧性能用十六烷值表示,愈高愈好,大庆原油炼制的柴油十六烷值可达68。
高速柴油机用的轻柴油十六烷值为42~55,低速的在35以下。
燃料油用作锅炉、轮船及工业炉的燃料。
商品燃料油用粘度大小区分不同牌号。
石油溶剂用于香精、油脂、试剂、橡胶加工、涂料工业作溶剂;
或清洗仪器、仪表、机械零件。
从石油制得的润滑油约占总润滑剂产量的95%以上。
除润滑性能外,还具有冷却、密封、防腐、绝缘、清洗、传递能量的作用。
产量最大的是内燃机油(占40%),其余为齿轮油、液压油、汽轮机油、电器绝缘油、压缩机油,合计占40%。
商品润滑油按粘度分级,负荷大、速度低的机械用高粘度油,否则用低粘度油。
炼油装置生产的是采取各种精制工艺制成的基础油,再加多种添加剂,因此具有专用功能,附加产值高。
润滑脂俗称黄油,是润滑剂加稠化剂制成的固体或半流体,用于不宜使用润滑油的轴承、齿轮部位。
石油蜡包括石蜡(占总消耗量的10%)、地蜡、石油脂等。
石蜡主要做包装材料、化妆品原料及蜡制品,也可作为化工原料生产脂肪酸(肥皂原料)。
石油沥青主要供道路、建筑使用。
石油焦用于冶金(钢、铝)、化工(电石)行业做电极。
除上述石油商品外,各个炼油装置还得到一些在常温下是气体的产物,总称炼厂气,可直接做燃料或加压液化分出液化石油气可作燃料或化工原料。
炼油厂提供的化工原料品种很多,是有机化工产品的原料基地。
常压下的气态原料主要制乙烯、丙烯、合成氨、氢气、乙炔、炭黑等。
液态原料(液化石油气、轻汽油、轻柴油、重柴油)经裂解可制成发展石油化工所需的绝大部分基础原料(乙炔除外),是发展石油化工的基础。
三、主要炼油工艺简介
炼油厂因生产规模、原料油性质、产品需求不同,建有不同的加工装置,基本的加工工艺为:
常减压蒸馏、催化裂化、催化重整、石油焦化、加氢裂化、炼厂气加工、石油产品精制等。
同一种加工工艺,也可采用不同的技术。
造成这一现象的原因是炼油技术发展较快,催化剂更新换代快,各地原料性质不一致。
(一)常减压蒸馏
常压蒸馏和减压蒸馏习惯上合称为常减压蒸馏,被称为炼油工艺的“龙头”。
常减压蒸馏直接加工原油,它的加工能力被称为炼油厂生产规模。
大型炼油厂的常减压能力已超过每年l×
常减压蒸馏基本上属于物理化学过程,没有化学反应。
原料油在蒸馏塔内按挥发度的差别被分割成沸程不同的油品(称为馏分),这些油有的经调和、加添加剂后以产品形式出厂,相当大的部分是后续加工的原料,因此,常减压蒸馏又称为原油的一次加工。
常减压蒸馏通常包括3个工序:
原油的脱盐、脱水;
常压蒸馏;
减压蒸馏。
原油的脱盐、脱水又称预处理。
从油田送往炼油厂的原料往往含有盐(主要是氯化物)、水(溶于油或呈乳化状态),可导致设备的腐蚀,在设备内壁结垢和影响成品油的组成,需在加工前脱除。
常用的办法是加破乳剂和水,使油中的水聚集,并从油中分出,而盐分溶于水中,再加以高压电场配合,使形成的较大水滴顺利除去。
原油经预处理预热至200-240℃后先进入初馏塔。
设初馏塔的好处是1)可提高装置的处理量,尤其在处理轻馏分含量高的原油时;
2)减小换热系统的压力降;
3)可进一步对原油脱水、脱盐。
初馏塔底油料经加热炉加热至360-370℃,进入常压塔。
常压蒸馏的目的是把原油按沸点范围分为汽油、煤油、柴油各个馏分,这些馏分直接由塔内分出,故称直馏馏分,塔底残余油称为常压渣油,又称重油,作为减压蒸馏或二次加工的原料。
常压蒸馏的主要操作条件是:
蒸馏塔塔顶压力接近常压,塔内各处温度与原油的组成和产品要求有关,塔底温度约为350℃。
常压渣油在加热炉中加热至380-400℃进入减压塔。
减压蒸馏是对常压渣油继续蒸馏分出有用的馏分。
采用减压蒸馏操作是为了降低蒸馏温度,防止常压渣油在长时间下高温加热发生化学变化和结焦影响正常操作。
减压蒸馏可蒸出柴油、润滑油和二次加工原料,塔底产物常压下沸点在500℃以上,可制沥青、石油焦,也可作燃料。
减压蒸馏塔塔顶压力为2~8kPa(相当于大气压的2%~8%),塔底温度一般不超过400℃。
常减压蒸馏的流程示意图见图2—5。
图2-5常减压蒸馏流程示意图
经脱水、脱盐的原油再经加热后进人初馏塔,塔顶蒸出轻汽油。
塔底出料再加热至370℃进常压塔,塔顶蒸出汽油馏分,塔的中部侧方开有3个出料口(侧线),常压一线产品为煤油馏分,常压二线产品为轻柴油馏分,常压三线产品为重柴油馏分。
常压塔底的常压渣油经加热至400℃后进入减压蒸馏塔,塔的真空由水蒸气喷射泵或机械式真空泵抽气形成。
减压塔顶蒸出柴油馏分,侧线一般有4个。
原油经常减压蒸馏的产率主要取决于原油的性质。
如大庆原油属于石蜡基石油,130℃以前汽油馏分的收率为4.2%,130~240℃的喷气燃料馏分为9.9%,240~350℃的轻柴湖的馏分组14.5%,三者合计只有28.6%。
350~500℃的馏分约29.7%,减压渣油为41.7%。
山东胜利油田原油属于中间基石油,200℃以前馏分为7%,200~350℃馏分约18%,350~525℃馏分约30%,减压渣油约45%。
这表明单靠常减压蒸馏无法满足对汽油、柴油的需求,需对350℃以上的馏分继续加工,来增加汽油、柴油的供应,同时合理利用该馏分生产润滑油、石蜡、石油焦。
这些加工被称为原油的二次加工。
(二)催化裂化
催化裂化是在热裂化的工艺基础上发展起来的。
热裂化反应,主要是把含碳原子数多的高分子量烃类裂化为含碳原子数少的低分子量烃类,同时伴有脱氢、环化、聚合和缩合等反应。
热裂化汽油辛烷值仍较低,只有50左右,安定性不好。
因此在炼油厂中已被催化裂化所取代。
催化裂化过程是把沸点较高即分子中含碳原子数较多的原料在热、催化剂的作用下,分子发生断裂,由大分子转成较小分子,对应沸点、粘度下降的一种工艺。
催化裂化是当前炼油厂提高原油加工深度,生产优质汽油、柴油最重要的工艺操作。
国内炼油企业经济效益的50%来自催化裂化。
由于使用了催化剂,与热裂化相比,烷烃分子链的断裂在中间而不再在末端,因此产物以C3、C4和中等大小的分子(即从汽油到柴油)居多,C1和C2的产率明显减少。
在催化剂作用下,异构化、芳构化(如六节环烷烃催化脱氢生成苯)、环烷化(如烷烃生成环烷烃)的反应得到加强,从而使裂解产物中异戊烷烃、环烷烃和芳香烃的含量增多,使裂化汽油的辛烷值提高。
在催化剂作用下,氢转移反应(缩合反应中产生的氢原子与烯烃结合成饱和烃的反应)更易进行,使得催化汽油中容易聚合的二烯烃类大为减少,汽油安定性较好。
当然,催化裂化和热裂化一样,也会发生聚合、缩合反应,从而使催化剂表面结焦。
由于进行的裂解、缩合(脱氢)、芳构化等反应都是吸热的,因此从总体上说,和热裂化一样,催化裂化也是吸热的。
催化裂化的原料范围比较宽,主要是350~540℃馏分的重质油,近期技术的发展是向原料油掺入更高沸点范围的渣油。
催化裂化的汽油、煤油、柴油总收率约为70%~80%,汽油质量好,柴油还需精制。
副产的气体可作石油化工原料。
催化裂化工艺由3部分组成:
原料油催化裂化、催化剂再生、产物分离。
催化裂化的反应温度为480~530℃,反应压力为常压或稍高于常压下(0.14MPa表压)进行。
催化裂化催化剂有人工合成的的无定形硅酸铝(SiO2·
Al203),Y型分子筛、ZSM-5沸石以及用稀土改性的Y(或x)分子筛。
催化裂化反应器有固定床、移动床和流化床三种,当今世界各国广泛采用的是流化床反应器。
催化裂化装置一般由反应-再生系统、分馏系统和吸收稳定系统3部分组成。
现以馏分油高低并列式提升管催化裂化装置为例说明反应-再生系统的工艺流程,如图2-6所示。
原料油与回炼油汇合后,送入原料油预热炉加热到300℃~380℃,送到提升管反应器下部的喷嘴。
原料油用蒸汽雾化后经多个喷嘴喷入提升管内,在其中与来自再生器的高温再生催化剂(640~700℃)相遇,立即气化并进行反应。
汽油与雾化蒸汽及预提升蒸汽一起以4.5~7.5m/s的入口线速携带催化剂沿提升管向上流动,在460~510℃的反应温度下停留2.5~4s,以10~18m/s的高速通过提升管出口的快速分离器进入沉降器,
图2一6高低并列式催化裂化装置和流程示意图
1一油泵;
2一加热炉;
3一提升管反应器;
4一沉降器;
5一再生器;
6一待再生催化剂输送管;
7一分馏塔;
8一汽提塔;
9一冷却冷凝器;
lO一气液分离器;
11一再沸器
与大部分催化剂迅速分离。
携带少量催化剂的反应产物经若干组两级旋风分离器分离出夹带的催化剂后,进入集气室,并通过沉降器顶部出口进入分馏系统。
经快速分离器分出的积有焦炭的催化剂,落入沉降器底进入汽提段。
经旋风分离器回收的催化剂经料腿也流入汽提段。
汽提段内装有多层人字形挡板(或圆形挡板),最下面3排人字挡板下方设有汽提蒸汽管,通入约400℃的过热蒸汽,把待再生催化剂上吸附的油气及颗粒之间空隙的油气置换出来,置换出来的油气返回沉降器。
经汽提后的待生剂通过待生斜管、待生单动滑阀以切线方向进入再生器密相床。
再生器的主要作用是烧去催化剂上因反应而生成的积炭,使催化剂的活性得以恢复。
再生催化剂流入溢流管(或淹流管),经再生斜管、再生单动滑阀送回提升管反应器循环使用。
烧焦生成的烟气经再生器稀相段、若干组两级旋风分离器除去携带的催化剂后,进入集气室,再经双动滑阀排入烟囱(或送去烟气能量回收系统)。
回收的催化剂经料腿返回床层。
双动滑阀自动调节两器压差,控制催化剂循环的压力平衡。
在生产过程中,为了维持系统内的催化剂藏量,需要定期向系统补充新鲜催化剂。
分馏系统
从反应器来的460~510℃高温油汽,在分馏塔精馏段将油气混合物分离成汽油、轻柴油、重柴油和回炼油或锅炉染料送出装置。
催化裂化产物主要是气体(称为催化裂化气)和液体。
固体产物(焦炭)生成量不多,且在催化剂再生器中已被烧掉。
催化裂化气产率为原料重量的10%~17%,其中乙烯含量为3%~4%,丙烯为13%~20%,丁烯为15%~30%,烷烃约占50%。
因此,催化裂化气实际上是一个很有经济价值的化工原料气源。
在国内外的大中型炼油厂中,都建有分离装置,将催化裂化气中的烯烃逐个地分离出来,经进一步提纯后用作生产高聚物的单体或有机合成原料。
催化裂化所得的液体产物经分馏后可得到汽油、柴油和重质馏分油。
有部分油返回反应器继续加工称为回炼油。
(三)加氢裂化
加氢裂化和催化裂化不同之处在于过程是在高压、氢气存在下进行,相同之处是都需要催化剂,把重质原料转化成汽油、煤油、柴油和润滑油。
加氢裂化由于有氢存在,原料转化的焦炭少,可除去有害的含硫、氮、氧的化合物,操作灵活,可按产品需求调整,产品收率较高(对汽油为75%,对喷气燃料和柴油为85%)而且质量好。
但是由于操作压强高、(10~20MPa),设备要求高,还需配置氢装置,应用不如催化裂化广泛。
但从提高油品质量考虑,应适当加以发展。
加氢裂化的催化剂主要成分为钨、钼、钴、镍的硫化物,将它们负载在二氧化硅、氧化铝或分子筛上。
根据原料、产品和生产规模的不同,加氢裂化可采用一个或两个反应器,故称一段法或二段法。
为防止含氮化合物使催化剂中毒,应在加氢裂化反应器前加氢精制原料油。
流程示意图见图2-7。
图2-7加氢裂化流程示意图
原料油、循环油及氢气混合物经加热进入0反应器,反应压强为10~20MPa,温度为370~450℃,因反应放热量大,靠向反应器不同部位通入冷氢来控制温度。
反应物经分离器分离成含氢气体和生成油,含氢气体加压后循环使用,生成油降压后进入蒸馏系统获得产品。
本法的缺点是所得汽油的辛烷值比催化裂化低,需再经重整将它的辛烷值提高。
因需高压和消耗大量的氢,操作费用比催化裂化高。
工业上,加氢裂化是用来作为催化裂化的一个补充,而不是替代催化裂化。
例如,它可以用来加工从催化裂化得到的沸点范围在汽油以上的,含有较多的多核芳烃的油料,而这些油料是很难进一步催化裂化的。
(四)催化重整
催化重整(简称重整)是在催化剂和氢气存在下,将常压蒸馏所得的轻汽油转化成含芳烃较多的重整汽油的过程,制得高辛烷值的汽油。
如果以80~180℃馏分为原料,产品为高辛烷值汽油;
如果以60~165℃馏分为原料油,产品主要是苯、甲苯、二甲苯等芳烃,经分离后可作化工原料,是当前最主要的上述芳烃的来源,在美国和中国,用催化重整制得的芳烃、占芳烃总量的三分之二左右。
重整过程副产氢气,可作为炼油厂加氢操作的氢源。
从化学反应来分析,重整过程主要是把含6~9个碳原子的链烷烃和环烷烃转化成相应同碳原子数的芳香烃,常被称为芳构化。
因此,对原料组成有要求,碳原子数太高或太低都不适合,原料中环烷烃易转成芳烃,烷烃较难,要求烷烃尽可能转成芳烃,需采用较苛刻的条件。
催化重整因长期使用铂催化剂故又被人们称为铂重整。
经研究,在铂催化剂作用下,催化重整反应主要有:
①六节环烷烃的脱氢
②五节环烷烃异构化后再脱氢
③烷烃环化再脱氢
④烷烃异构化
⑤加氢裂化
以上五类反应中,①、②、③三类反应都生成芳烃,所以叫作“芳构化反应”。
反应①和②在铂催化剂存在下,进行得非常迅速,是我们希望发生的主要反应。
另外,芳构化反应伴生大量氢气。
从主要反应是一个强吸热和体积增大的反应来判断,操作应在加热和低压下进行。
但低压下易造成催化剂表面结焦,使催化剂很快失活,故催化重整一般在加压下进行。
重整过程使用的催化剂是铂(加有铼、铱等),分散在氧化铝(载体)上,还需要有氟或氯的化合物调节其酸性(助催剂)。
原料油的不饱和烃(烯烃)、水、砷、铅、铜、硫、氮能使催化剂中毒,故需在重整反应前除去。
重整的反应条件是:
反应温度为490~525℃,反应压力为1~2MPa。
重整的工艺过程可分为原料预处理和重整两部分,生产芳烃需再配分离部分(通常称芳烃抽提)。
重整原料的预处理包括从预分馏塔塔顶除去原料中沸点过低(O~60℃)的部分,然后进入预加氢除去对催化剂有毒的含砷、铅、硫、氮、氧等化合物。
砷、铝、钼、汞、硫和氮等都会使催化剂中毒。
铂催化剂对砷特别敏感,要求原料油含砷量不大于O.1ppm。
因此,在进入重整反应器前,原料油需进行加氢处理以除去这些杂质。
预加氢的化学反应:
1脱硫、脱氮、脱氧反应
原料油中的硫化物、氧化物、氮化物与氢反应生成H2S、H2O、NH3和烃类。
H2S、H2O、NH3等与冷凝下来的油分开,用作燃料烧掉。
2脱金属反应
原料油中金属杂质(砷、铝、钼、汞等)以金属有机化合物的形式存在,在加氢条件下,金属有机化合物分解,金属沉积在催化剂上面而从油中除去。
重整装置因催化剂的再生方法不一而有不同的型式。
我国大部分采用半再生式,即反应一段时间催化剂性能下降到某一水平时,停止进原料,对催化剂用含少量氧气的氮气在高温下再生,再生合格后重新进原料。
循环再生型是多个反应器,每个反应器都可从生产线上切换出进行再生而不影响整个生产。
连续再生型是催化剂在反应器和再生器内流动,正常生产时只需部分催化剂抽出进行再生,再生后返回。
重整反应强吸热,原料反应后温度下降,需加热再进入下一个反应器。
通常用3~4个反应器串联来保证原料的转化率。
反应后氢气与油分开,气体循环使用,油进行蒸馏得到重整汽油。
半再生式重整工艺流程示意图见图2-8(图中未绘预处理部分)。
图2-8重整工艺流程示意图
1一加热炉;
2一反应器;
3一分离器;
4一压缩机
重整油主要由两类化合物组成,即芳香烃和非芳香烃(烷烃和环烷烃),它们相互溶解,沸点相近,有的仅差0.6℃,不宜采用蒸馏的办法分离。
为此加入溶剂(如二甘醇、三甘醇、环丁砜等)溶解芳香烃,实现芳烃与非芳烃的分离,故这些溶剂称为萃取剂,这个生产过程被称为芳烃抽提。
芳烃抽提系统将重整油用二乙二醇醚(或其他溶剂)在抽提塔中进行液相逆流抽提,提取物为芳烃混合物,通入水蒸气蒸馏分出溶剂的混合芳烃进芳烃精馏系统。
提余物为非芳烃,分出溶剂可作为汽油组分。
芳烃精馏系统是将混合芳烃通过精馏的方式分离为苯、甲苯、二甲苯等单一芳烃产品和重质芳烃。
图2-9芳烃抽提和芳烃精馏装置构成示意图
二甲苯塔所得为混合二甲苯,其中有间位、对位、邻位二甲苯及乙苯,其中以对二甲苯需求量最大(制涤纶纤维)。
有的装置为了进一步分离单一二甲苯而将二甲苯塔顶得到的混合二甲苯送入邻二甲苯塔(需100-150块塔板),从塔底得到邻二甲苯,将邻二甲苯塔顶产物送入乙苯塔(需300-350块塔板),从塔顶得乙苯,塔底为间、对二甲苯,它们的沸点仅差0.712,难于用精馏的方法分开,需采用专门的吸附法或冷冻结晶法分离。
过去对C9以上的重芳烃一般认为是无多大用途的副产品而和非芳烃一起做为汽油原料,目前由于1,2,4-三甲苯做为1,2,4-苯三酸酐、苯偏三酸酐(增塑剂、涂料和高分子材料的重要原料)和维生素E的原料,因此对C9芳烃的利用已引起各国的重视。
图2-10芳烃精馏工艺原理流程图