第十一章作业改革文档格式.docx
《第十一章作业改革文档格式.docx》由会员分享,可在线阅读,更多相关《第十一章作业改革文档格式.docx(22页珍藏版)》请在冰豆网上搜索。
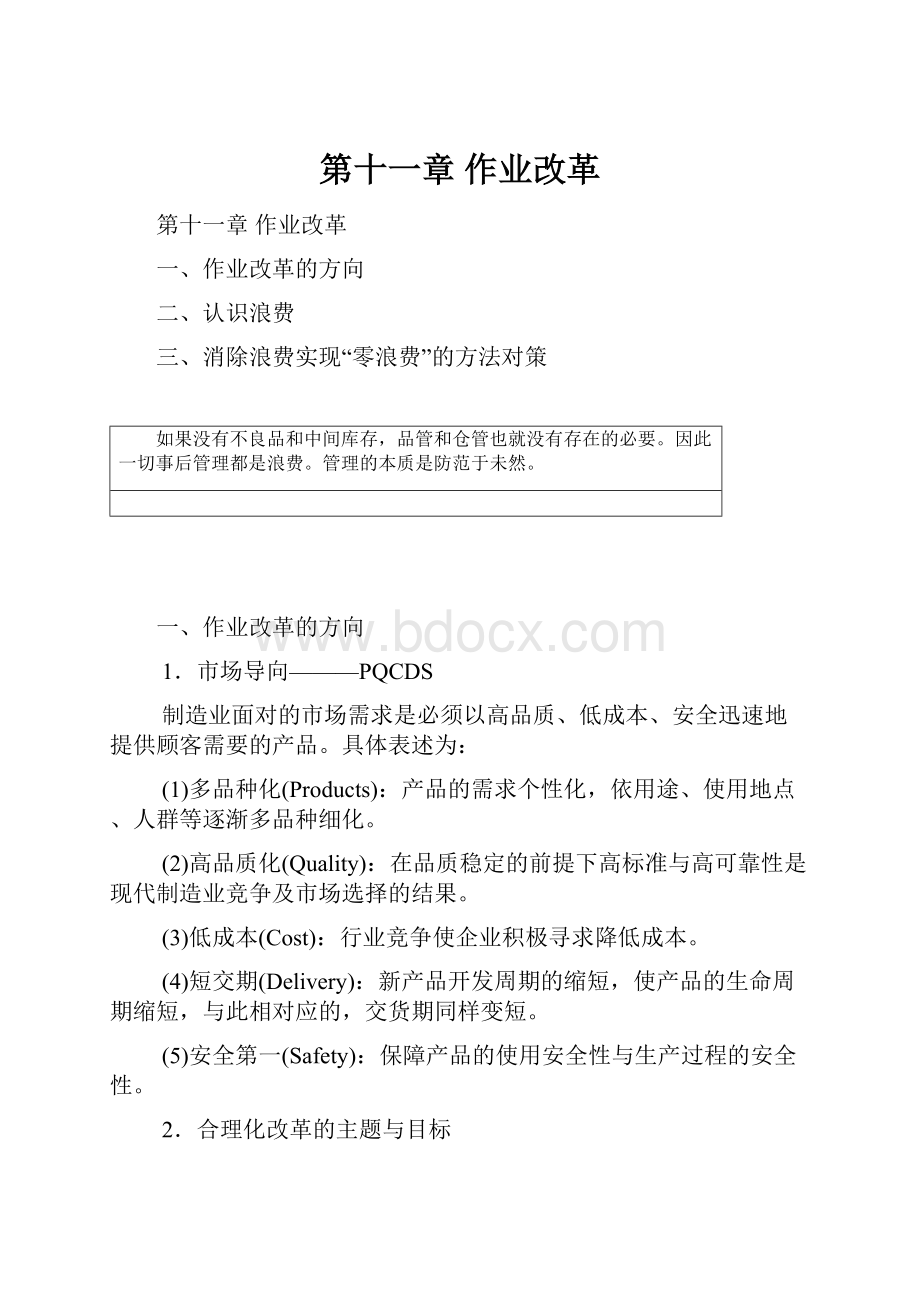
随时可以买到的普通包装箱半年前一次采购一大批,然后逐月慢慢使用;
等等,毫无疑问,这些会造成场所浪费、租金损失、流动资金被占用、利息损失“过量储藏等的报废、无谓工时的发生、管理成本的增加。
这些浪费现象无异于在“烧”钱。
精益生产的特点是消除一切浪费追求精益求精和不断改善。
去掉生产环节中一切无用的东西,每个工人及其岗位的安排原则是必须增值,撤除一切不增值的岗位。
精简是它的核心,精简产品开发设计、生产、管理中一切不产生附加值的工作,旨在以最优品质、最低成本和最高效率对市场需求作出最迅速的响应。
精益生产所言之浪费,比通常所说的浪费的概念要广泛得多、深刻得多。
按照丰田公司的定义,“凡是超过生产产品所绝对必要的最少量的设备、材料、零件和工作时间的部分,都是浪费”。
这个定义中的“绝对必要”比较含糊,没有一定的标准。
美国一位管理专家对此作了修正,“凡是超出增加产品价值所必需的绝对值最少的物料、机器和人力资源的部分,都是浪费”。
这里有两层含意:
一是不增加价值的活动,是浪费;
二是尽管是增加价值的活动,所用的资源超过了“绝对最少”的界限,也是浪费.
什么是浪费:
·
不增加价值的活动,是浪费;
尽管是增加价值的活动,所用的资源超过了“绝对最少”的界限,也是浪费。
以下的说明将有助于我们理解精益生产方式中有关浪费之定义的内涵。
在生产过程中,只有实体上改变了物料的活动才能在生产过程中增加价值。
加工零件,增加价值;
组装产品,增加价值;
油漆、包装,也增加价值。
不过,工厂中很多常见的活动并不增加价值。
例如:
点数不增加价值,库存不增加价值,品质检验也不增加价值。
许多人认为搬运会增加价值,其实恰恰相反,搬运不仅不增加价值,反而可能会减少价值(常常引起损伤、报废)。
这些活动不增加价值,但增加了成本,因而都是浪费。
此外,工序间如果有2个在制品就能维持正常生产,则超出2个的部分都是浪费,因为所用的资源超过了“绝对最少”的界限。
2.浪费的种类
现代IE从两个方面来专业分析发现这此浪费。
(1)全面生产系统的浪费
5MQS的浪费(见表11—1)
表11-15MQS的浪费
分类
浪费
说明
5
M
人
的
浪
费
1.行走的浪费
2.监视的浪费
3.寻找的浪费
4.动作的浪费
5.职责不清的浪费
走一步一秒的浪费
CNC操控的无谓监视
找寻物品的时间浪费
不增值的动作浪费
不知自己的真正职责,人制管理的浪费
材
料
1.原料的浪费
2.螺栓的浪费
3.焊接的浪费
4.功能的浪费
5.不良报废的材料
多余原料
过多螺栓连接,设计不良,螺栓连接本身就是浪费
焊接过多
多余功能造成的材料浪费
报废本身就是浪费
设
备
1.大型机械的浪费
2.通用机械的浪费
3.传送带的浪费
4.压缩机的能力过剩
5.故障的浪费
批量生产带来的搬运、停滞等大型设备所致的浪费
通用机械功能多数只用一半,一半以上的多余投资
只用作传送的皮带是一种浪费
全自动气动装置造成压缩机过多投入
机械故障的浪费
作
业
方
法
的
浪
费
1.批量加工的浪费
2.库存的浪费
3.搬运的浪费
4.放置(停滞)的浪费
5.等待的浪费
6.不平衡的浪费
由于批量生产造成的浪费
库存本身就是浪费
设备布局的浪费
工序过于细分化造成的浪费
能力不平衡造成的各种等待、停滞
流程混乱造成的浪费
管
理
1.资料的浪费
2.会议的浪费
3.管理的浪费
4.通信的浪费
5.工作单的浪费
资料不用便是浪费
会议本身的目的不明确就是浪费
管理本身就是浪费,目标、职责不清
信息的目的性不明确就是浪费
工作单的编制填写确认保管都是浪费
Q
Q
品
质
1.不良品的浪费
2.修正不良的浪费
3.错误的发生
4.检验的浪费
5.品质管理的浪费
不良本身就是浪费
治标不治本的浪费
只有临时对策,不追究根本原因的浪费
品质管理的事后检查本身就是浪费
S
安全
灾害与事故的防止
安全的疏忽是对人、对社会最大的危害,安全第一
生产要素的5MQS是Man(人),MateriaI(材料),Machine(机械),Method(作业方法),Management(管理),Quality(品质),safety(安全)。
(2)现代IE的八大浪费
现代IE的八大浪费是现场管理与革新中的浪费重点(见表11-2)。
表11-2现代IE的八大浪费
NO
制造现场的浪费
说明
管理部门的浪费
1
过多制造的浪费
在不必要的时候制造不必要的产品
超前预计市场的结果
2
库存的浪费
成品、中间品、原材料的库存浪费
超前储备的浪费带来大量的管理浪费
3
搬运的浪费
物料搬运的浪费
搬运步行的浪费
4
不良品的浪费
制造不良的浪费,之后还有进行检测的浪费
低可靠性带来的各种事中、事后的浪费
加工的浪费
与产品价值核心的功能不相关的加工与作业都是浪费
作业浪费
6
动作的浪费
步行、放置、大幅度的动作
7
等待的浪费
人、机械、部件、在不必要时发生的各种等待
等待的浪费
8
管理的浪费
管理本身成为一种专职的工作发生的浪费
事后管理的浪费
现代IE的八大浪费:
①制造过多(早)的浪费:
精益生产强调“适时生产”:
必要的东西在必要的时候,做出必要的数量,此外都是浪费。
而所谓必要的东西和必要的时间,就是指顾客(或下道工序)已决定要的数量与时间。
例如:
顾客要买1000个,1元/个,生产了1200个,它并没有带来1200元的收益。
多余的200个仅仅变成了库存,没有产生利益,是浪费。
同样,许多工厂内在许多工序处都放置有不少在制品,所有工序处的在制品数量之和换算成现金恐怕是一笔巨款吧。
与理想状态之各工序间只有一个在制品在流动的状况相比,多余的都是浪费,算一算,触目惊心。
许多工厂都存在制造过多或过早的现象,最大的原因恐怕是因为他们不知道这是一种浪费。
相反,在我们所接触的许多企业经营管理者认为多做能提高效率,提早做好能减少产能损失(设备买回来是用来生产零件的,让设备停下来简直不可思议),这是一个很大的误解!
企业的利润从何而来?
绝不是来自中间工序多生产的在制品,真正利润的产生是来自于卖出去的产品。
生产没能带来效益仅是增加厂库存量,是浪费!
因此,认为制造过多与过早能够提高效率或减少产能损失,是一种见树不见林的思维,它只反映过程控制的低水平,必须摒弃。
制造过多(早)的浪费在八大浪费中被视为最大的浪费,它会带来以下现象:
·
提早用掉了材料费、人工费而已,并不能得到多少实在的好处。
把“等待的浪费”隐藏起来,使管理人员漠视等待的发生而使之永远存在下去。
失去了不断改善、进而增强企业体质的机会。
使工序间积压在制品,会使制造周期变长,且所需的空间变大(许多企业车间像仓库,到处都是原材料、在制品、完成品,或有许多面积不小的所谓中转库是十分典型的现象),产生大量工时浪费。
产生搬运、堆积的浪费,并使得先入先出的物流作业变得困难。
增加踏板、包装箱(周转箱)的需要。
库存量变大,管理工时增加。
利息负担增加。
②库存的浪费(含中间在制品)
库存包括:
零部件、材料的库存;
半成品的库存;
成品的库存;
已向供应商订购的在途零部件。
已发货的在途成品库存的浪费主要表现在:
产生不必要的搬运、堆积、放置、防护、寻找等浪费的动作;
使先入先出作业困难;
资金占用(损失利息)及额外的管理费用;
物品的价值衰减,变成呆料、废料;
占用空间、影响进出料,且造成多余的仓库建设投资;
掩盖问题,其中最大的问题是管理混乱,无法做到量化管理。
图11-1库存水平与问题
如图11-1所示,库存水平高会将许多管理不善的问题掩盖起来,使问题得不到及时解决,就像水掩盖了水中的石头一样。
如机器经常发生偶发故障、设备调整时间太长、设备能力不平衡、工人缺勤、备件供应不及时等问题,由于库存水平高,不易被发现。
此时你所能看到的(露出水面)只是不良品、设备故障,当减少库存时就能发现许多问题。
解决这些问题,然后再减少库存。
最终物料就能顺利地按计划在各车间、各工序间流动。
精益生产就是要通过不断减少各种库存来暴露管理中的问题,不断消除浪费,进行永无休止的改进。
它不仅是一种方法体系,更是一种精神、一种文化、一种战略。
库存更严重的是其造成的无形损害:
没有改善的紧迫感,阻碍改善的活性化
因为库存量一多,机械故障不会马上有大的影响,故对策可以慢慢来,产生了不良品也一样,可以慢慢来。
同样地,换模调整时间也永远不会排在优先解决之列,这样,就似乎变成没有什么需要改善了。
一个没有改善意愿的企业思想是僵化的,一个缺乏改善意愿的企业是难以长期生存!
不要指望兔子都会睡觉,让乌龟慢慢赶超,那只是童话而已。
设备能力及人员需求的误判
由于库存量存在,设备能力不平衡也不容易看出来(库存越多,越不容易看出),人员需求是否过剩也无法了解。
企业严重流失基层的智慧
当人感到自己只是企业或别人赚钱的工具时,他所愿意贡献的智慧是有限的,企业的活力就无从谈起,这与精益生产的以人为本、全员参与是相背的。
与传统管理中“库存是必要的恶物”的观点截然不同,精益生产认为“库存是万恶之源”,必须加以消灭或大幅度减少!
③搬运的浪费
搬运是一种不产生附加价值的动作。
搬运的损失分为放置、堆积、移动、整列等动作浪费。
物品移动所要的空间浪费;
时间的耗费;
人力、工具的占用的浪费。
目前国内有不少企业管理者认为搬运是必要的,不是浪费。
其现由是没有搬运如何做下面的工作?
正因为如此,很多人对这种浪费视而不见,更谈不上消灭它。
也有些人利用传送带的方式来减少“搬运”,此种做法可谓治标不治本,造成搬运的问题并没解决,生产流水化同步化才是减少搬运的根本之道。
④不良品的浪费
是指企业内发生不良品造成的各种质量成本及由此造成的相关浪费。
材料的损失;
设备、人员工时的损失;
额外的修复、挑选、追加检查;
额外的检查预防人员;
降价处理;
出货延误取消定单;
信誉下降。
⑤加工的浪费
亦称为“过分加工的浪费”,一是指多余的加工。
另一方面是指过分精确的加工,如实际加工精度比加工要求要高,造成资源的浪费。
需要多余的作业时间和辅助设备;
生产用电、气压、油等能源浪费;
管理工时增加。
⑥动作的浪费
精益生产总结出常见的12种动作浪费:
两手空闲;
单手空闲;
作业动作不连贯停顿;
动作幅度太大超出“经济动作”范围;
左右手交换;
步行多;
转身角度大;
移动中变换“状态”;
不明技巧;
伸背动作;
弯腰动作;
重复/不必要的动作。
这些动作浪费在流水线式生产时十分常见,了解并排除这些浪费是提高生产作业效率的利器。
精益生产的管理专家们认为:
一般来说作业者有一半的时间是“无效的”!
⑦等待的浪费
因断料、作业不平衡、计划不当等造成无事可做的等待,也称之为停滞的浪费。
此外在许多企业,你可以发现有不少人站在机器设备旁,只是看着机器,两手抱袖,大部分时间无所事事,此谓监视的浪费(等待浪费的一种)。
精益生产的实践表明,在很多情况下,完全可以通过有效的方法排除或大幅度减少这种浪费。
等待的浪费主要有:
生产线的品种切换;
每天的工作量变动很大,当工作量少时,便无所事事;
时常因缺料而使机器闲置;
因上游工序发生延误,导致下游工序无事可做;
机器设备时常发生故障;
生产线未能取得平衡
有劳逸不均的现象
材料虽己备齐,但制造通知单或设计图并未送来,导致等待。
⑧管理的浪费
企业与工厂中进行的管理几乎都是因为某种既成事实而进行的事后管理:
因为出现不良所以有品质管理,又因为有仓库所以有仓库管理……为此管理成为一种独立的工作,由此产生的管理部门又不遗余力地宣讲加强管理力度的必要。
那么如果没有不良品和中间库存,品管和仓管也就没了存在的必要。
管理的本质是防患于未然。
3.浪费产生与固化的过程
为什么会发生上述这么多浪费呢?
同时它又是如何固化下来呢?
我们从企业要面对的某些问题人手就不难找到答案。
首先当有一个问题发生时中间管理层往往会对不得不马上解决的问题给一个没办法情况下的临时对策,所有的问题就由这个临时对策产生了,其背后原因是问题产生的真正原因无法及时找到,或根本不愿意深究,从而采取逃避问题的办法,用仓存来抵消它,搬运也就产生了,临时检查工位也产生了,管理部门也就壮大起来,于是就有人专门为这些工作制定了一些不成文的惯例约定,长期下去竟然形成制度,又要IS0认证了,干脆把它标准化吧。
结果正如下图11-2所示的程序,浪费被固化下来,并成了很多人赖以生存的饭碗。
图11-2浪费的产生与固化过程
4.发现浪费的方法
制造现场及管理部门是最大的浪费集中地,人们在长期习惯某种工艺过程及管理方法之后就会认同这种浪费现象,为此而丧失了发现浪费的眼力。
下面从逆向思维法、流程再造及现状分析三个方面进行介绍。
(1)逆向思维法
首先我们在观察工作过程之前要问的是为什么要进行这一作业,它的目的是什么,为达到这一目的是否只能有一种方法,以及作业中什么才是达到此目的的有价值作业,除此以外全部是浪费。
(2)流程改善发现浪费
现代IE对流程改造时,首先考虑的是市场应变力,即柔性生产系统的改造。
这一点集中体现在“一个流”前提下的单元生产,它是IE作业研究要达到的目标。
为什么要抛弃批量生产及中间库存进行全面的流水化生产呢?
其目的就是要缩短Leadtime,提高应变力,与此相违背的全部方式方法都是造成浪费的根源。
(3)现状分析发现浪费
在流程分析的章节有较详细的分析方法介绍(见第三章“程序分析”)
二、消除浪费实现“零浪费”的方法对策
实现零浪费方法对策表
7个
零浪费
目的
现状
5S
思考方法与原则
对策手法
整
理
顿
清
扫
洁
修
养
零
切
换
多品
种
对
应
P
加工工序的转换品种,装配换机种时存在严重的工时浪费
○
◎
▲
◎
经济批量不经济
物流方式的JTF
生产计划的标准化
作业管理
标准化作业
设备小型化,专用化
LCA、SMED)
均衡化生产(混流生产)
动作经济原则
多工序合并(多能工)
成品放置流水化
标准时间(ST)
标准作业(SO)
作业标准(OS)
转产模块化(专用物流车)
2
零
库
存
发
现
真
正
问
题
I
产品、半成品、零件、原料大量库存,造成经营成本很高,周转困难.且现场
看不到产品在流动
○
库存问题的真正理由
库存与加工批量成正比
适当库存不当
均衡化生产
设备流水化(U形拉)
LCA、SMED
一个流
平均化生产
拉动式生产
看板管理
多工序合并(多能工)
转产模快化(专用物流车)
混载进货
进货验货流水化
降
低
成
本C
生产率低,浪费严重,但无法判断及采取相应对策
不能单纯加强局域生产能力
整体协调,能力均衡
“一个流”将浪费彻底暴露出来
流程线路图
设备流水化
一个流
拉动式生产
看板管理
多工序合并(多能工)
组织流程化
LINEBALANCING
SOANDOS
4
不
良
品
质
保
证
材料不良,精度不良,装配不良,外伤,等等
因品质进行事后补救的状态很多
抽检无法杜绝不良
加工批量的大小就是合格与不良批量的大小
零不良才是目标
设备小型化,流水化
LCA
一个琉
防错体系、方法
自检与根源追究
5
故
障
生产
维护
由于惧怕设备故障而不得不进行大量个间储备
▲
设备是有生命的东西
为什么会有故障
全面生产维护(TPM)
TPM
5S
6
停
滞
压
缩
交
货
周
期
经常发生交货推迟造成大量索赔16dtIH2e无
法压缩
同步化与均衡化
Layout流水化
设备小型化专用化
拉动式系统
SO
生产组织流程化
零灾害
第一
因为赶货而忽视安全,没有安全检查部门
安全第一
遵守安全标准
5S安全管理第一步
安全疏忽检查
SP巡视制度
安全责任制
▲一般见效;
○相对见效;
◎直接见效;