缓蚀剂的作用机理研究现状及发展方向Word下载.docx
《缓蚀剂的作用机理研究现状及发展方向Word下载.docx》由会员分享,可在线阅读,更多相关《缓蚀剂的作用机理研究现状及发展方向Word下载.docx(14页珍藏版)》请在冰豆网上搜索。
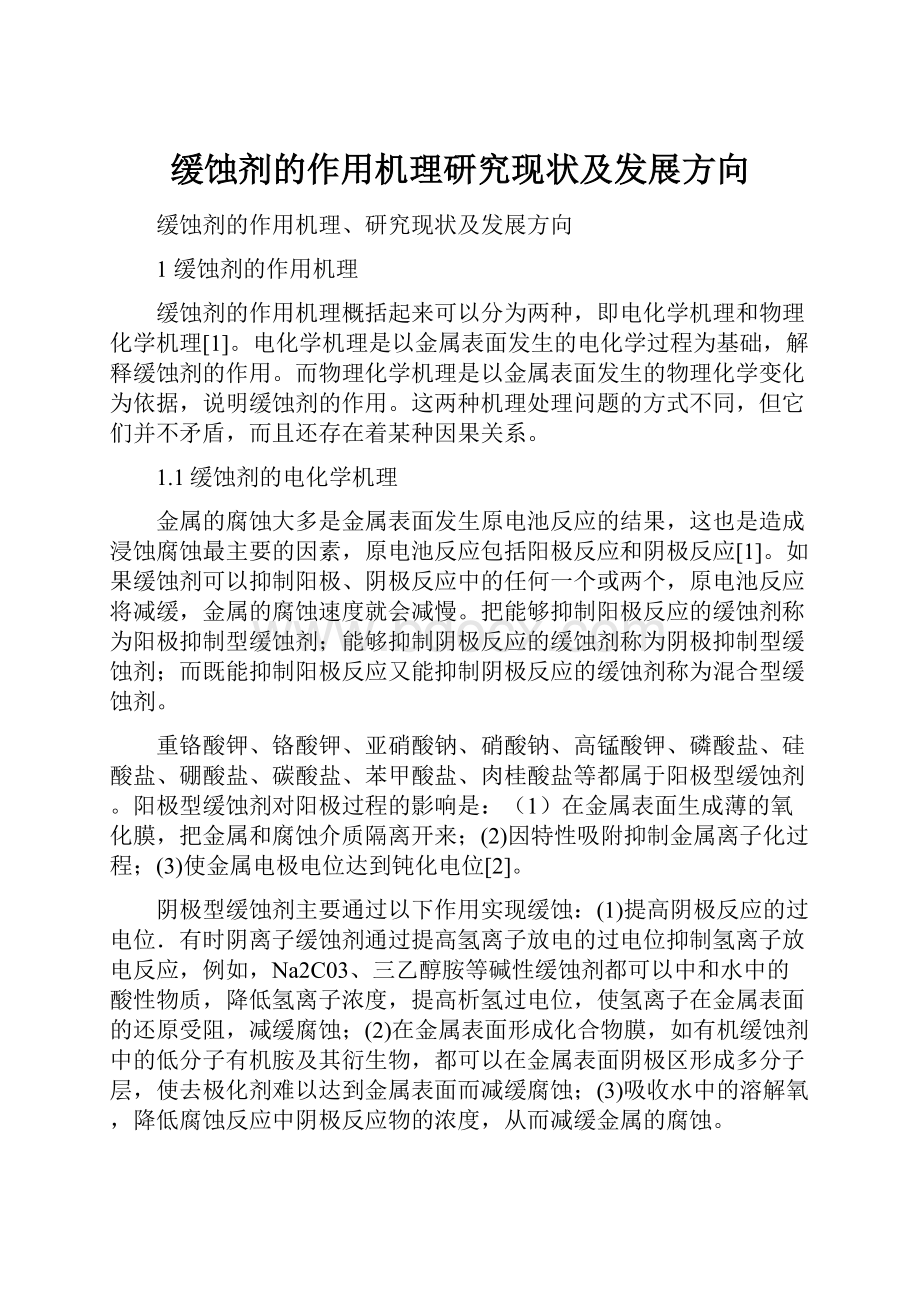
(3)吸收水中的溶解氧,降低腐蚀反应中阴极反应物的浓度,从而减缓金属的腐蚀。
混合型缓蚀剂对腐蚀电化学过程的影响主要表现在:
(1)与阳极反应产物反应生成不溶物,这些不溶物紧密地沉积在金属表面起到缓蚀的作用,磷酸盐如Na3P04、Na2HP04对铁、镁、铝等的缓蚀就属于这一类型;
(2)形成胶体物质,能够形成复杂胶体体系的化合物可作为有效的缓蚀剂,例如Na2Si03等;
(3)在金属表面吸附,形成吸附膜达到缓蚀的目的,明胶、阿拉伯树胶等可以在铝表面吸附,吡啶及有机胺类可以在镁及镁合金表面吸附,故都可以起到缓蚀的作用[2]。
1.2缓蚀剂的物理化学机理
从物理化学的角度来理解,缓蚀剂的作用可以分为生成氧化膜、沉淀膜和吸附膜3种。
因此缓蚀剂也分为氧化膜型缓蚀剂、沉淀膜型缓蚀剂和吸附膜型缓蚀剂[3]。
1.2.1氧化膜型缓蚀剂
氧化膜型缓蚀剂本身是氧化剂,可以和金属发生作用。
或本身不具有氧化性,以介质中的溶解氧为氧化剂,使金属表面形成紧密的氧化膜,造成金属离子化过程受阻,从而减缓金属的腐蚀,这种缓蚀剂又称钝化剂。
重铬酸钾、铬酸钾、高锰酸钾在含氧的水溶液中对铝、镁的缓蚀作用就属于这一类。
氧化膜型缓蚀剂,缓蚀效率高,已得到广泛的应用。
但如果用量不足,则可能在金属表面形成大阴极小阳极而发生孔蚀。
所以这一类缓蚀剂又称为“危险型缓蚀剂[3]。
1.2.2沉淀膜型缓蚀剂
沉淀膜型缓蚀剂,就是在金属表面生成了沉淀膜。
沉淀膜可由缓蚀剂分子之间相互作用生成,也可由缓蚀剂和腐蚀介质中的金属离子作用生成。
在多数情况下,沉淀膜在阴极区形成并覆盖于阴极表面,将金属和腐蚀介质隔开,抑制金属电化学腐蚀的阴极过程,即阴极抑制型。
有时沉淀膜能覆盖金属的全部表面,同时抑制金属电化学腐蚀的阳极过程和阴极过程,这一种称为混合抑制型[4]。
硫酸锌、碳酸氢钙、石灰、聚磷酸盐、硅酸盐及有机膦酸盐都属于阴极抑制型缓蚀剂。
在中性含氧的水中,锌离子可以和阴极反应生成的氢氧根离子反应生成难溶的氢氧化锌沉淀膜覆盖于阴极,而抑制阴极反应。
磷酸盐如Na2HP04或Na3P04,在有溶解氧情况下,可以和Fe3+反应生成一种不溶性的r-Fe203和FeP04·
2H20混合物薄膜,抑制铁的腐蚀。
需要注意的是,介质中氧的存在对缓蚀剂有加强作用。
只有存在氧,才能发挥缓蚀剂的作用。
混合抑制型缓蚀剂多为有机化合物。
有机缓蚀剂分子上的反应基团和腐蚀过程中生成的金属离子相互作用生成沉淀膜,而抑制阴阳两极的电化学过程。
例如,丙炔醇对铁在酸性水溶液中有良好的缓蚀效果。
研究发现,丙炔醇发生作用时,先吸附于金属表面,受铁上析出氢的还原作用,发生聚合反应而生成聚合的配合物膜。
覆盖于整个金属的表面,同时抑制腐蚀电化学反应的阳极反应和阴极反应。
又如,8-羟基喹啉在碱性介质中对铝的腐蚀有缓蚀作用,这是由于缓蚀剂和铝离子反应生成的不溶性配合物沉淀膜覆盖在铝表面,抑制了铝在碱性水溶液中的腐蚀。
苯并三氮唑对铜的缓蚀作用也认为是生成了不溶性的聚合物沉淀膜。
1.2.3吸附膜型缓蚀剂
吸附膜型缓蚀剂多为有机缓蚀剂,它们在腐蚀介质中对金属表面有良好的吸附性,这种吸附改变了金属表面的性质,抑制了金属的腐蚀。
因为这类缓蚀剂分子结构具有不对称性,分子由极性基和非极性基组成。
非极性基为烃基,有亲油性,而极性基如-COOH、-S03H等具有亲水性,对金属表面也具有亲和性。
当缓蚀剂分子的极性基在金属表面吸附后,其较长的非极性基也在范德华力的作用下紧密排列,从而形成牢固的吸附膜。
表面吸附一方面改变了金属表面的电荷状态和界面性质,使金属表面的能量状态趋于稳定,增加腐蚀反应活化能,减缓腐蚀速度;
另一方面,非极性基的隔离作用将金属表面和腐蚀介质隔开,阻碍电化学反应相关的电荷或物质的转移,从而减缓腐蚀[4]。
如果缓蚀剂在金属表面的吸附起源于缓蚀剂离子与金属表面电荷产生的静电引力和两者之间的范德华力,这种吸附就称为物理吸附。
这种吸附速度快,可逆,吸附热小,受温度影响小,而且金属和缓蚀剂间没有特定组合。
例如,有机胺类化合物在酸性介质中,氮原子接受一个质子而转化为烷基胺阳离子,该阳离子被金属表面带负电荷部分所吸引,形成单分子的吸附层,就是典型的物理吸附。
铁、镍等过渡金属都具有未占据的空d轨道,易接受电子。
有机缓蚀剂的极性基大部分含有O、N、S、P等电负性元素,它们都具有未共用电子对,能和金属作配位结合。
这种以配位键作用形成的吸附称为化学吸附。
胺和硫醇与金属的化学吸附如下式所示(M表示金属)。
在双键、叁键及苯环中存在的丌电子也可以发生类似的化学吸附。
2缓蚀剂的研究现状
2.1酸洗缓蚀剂的研究及其应用
2.1.1硫酸酸洗缓蚀剂
硫酸常在酸洗用量较大的金属材料酸浸除锈过程中作清洗主剂和在锅炉污垢中钙化合物含量很低的情况下用于酸洗锅炉[5]。
由于硫酸浓度高,密度大,所以在等物质的量清洗条件下,洗一台锅炉所用工业硫酸的体积仅为盐酸的1/4,而且浓硫酸对钢铁几乎不腐蚀,这给化学清洗带来了极大的方便,可以大大简化储存、运输和配酸的系统。
用于硫酸溶液中的缓蚀剂主要有两种,一种是含氮化合物缓蚀剂,如胺、吡啶以及吡啶碱和醌、2-甲基吡啶、吡啶碘化合物和吡啶卤化物;
另一种是含硫化合物的缓蚀剂,如硫脲以及硫脲衍生物等,后者对碳钢在硫酸中的缓蚀效率更高[6]。
2.1.2盐酸酸洗缓蚀剂
盐酸酸洗的效果好,盐酸本身的危险性比硫酸小,在当量浓度下,与氧化铁之间的反应速率比硫酸快。
但盐酸在超过40℃时易挥发,会导致酸液浓度下降,影响酸洗效果,故应注意控制温度。
另外,盐酸对金属氢脆敏感性较硫酸小,而且硫酸溶液中具有腐蚀抑制作用的缓蚀剂一般在盐酸溶液中也有缓蚀作用,因而盐酸酸洗日益取代了硫酸酸洗。
对碳钢盐酸酸洗有效的缓蚀剂大多为含有N、O、S、P原子的有机杂环化合物,而以含氮化合物用得最多[7]。
常见盐酸酸洗缓蚀剂有下列三种:
(1)含氨化合物缓蚀剂,包括烷基胺和芳胺,饱和及不饱和的氮环化合物或乙烯氮化物缩合的多胺所合成的马尼什碱以及季铵、酰胺、聚胺等,如乌洛托品;
(2)含硫化合物的缓蚀剂硫脲及衍生物,在酸洗液中,Fe3+离子是一种较强的去极化剂,如果积累较多会加剧钢的腐蚀而产生过酸洗的现象,苯硫脲与NH4HF3复合物能与Fe3+离子生成络合物,从而阻止过酸洗。
另外稀土硫脲化合物也是一种有效的缓蚀剂;
(3)其他化合物的缓蚀剂,某些含磷化合物,如磷酸三丁酯既能抑制钢基体腐蚀和氢渗透避免发生过酸洗,又利于酸液再生循环。
2.1.3氢氟酸酸洗缓蚀剂[8]
氢氟酸是一种弱无机酸,在空气中挥发,其蒸汽具有强烈的腐蚀性及毒性。
但其溶解氧化物的速率快,具有溶解硅垢(硅的氧化物)的特殊性能。
1968年氢氟酸酸洗首次在西德的一台运行后的超临界压力锅炉上使用获得成功。
此后,西德有40%的锅炉都采用氢氟酸酸洗。
虽然用氢氟酸酸洗存在操作不安全、价格高及污染环境的弊端。
但从氢氟酸的特性考虑,应用了新型缓蚀剂后,它的使用范围仍然很广泛。
国外研制的氢氟酸酸洗缓蚀剂,如西德研制的烷基硫脲和有机胺复配的Berin-31、BerinO-74、Rodine-31A、Rodine-58、Dodigen-95、Fiumin-34;
美国专利报道用含活泼氢的有机胺与α-酮或α-醛的缩合物做氢氟酸缓蚀剂。
国内生产的品种有IMC-5、Lan-826、SH416、SH406、N-1-A、W-19、BH-2、F-102、TPRI-Ⅲ、新洁尔灭等缓蚀剂,这些缓蚀剂经过试验和大型机组的实际使用,证明其对10CrMo910的缓蚀效率均可达到98%以上,腐蚀速率可控制在0.3-1.8g/(m2·
h),这些缓蚀剂已在氢氟酸酸洗中广泛使用。
2.1.4硝酸酸洗缓蚀剂[8]
硝酸对锅炉垢物和金属氧化物溶解性较强,故硝酸有时代替盐酸酸洗。
硝酸是一种氧化性很强的酸,而现在大多数的缓蚀剂是有机物,易发生氧化还原反应,因此,硝酸酸洗缓蚀剂种类较少。
硝酸酸洗缓蚀剂常见的是硫脲和Na2S的混合物,吲哚(C8H7N)与NH4SN或Na2S的混合物。
还有硫代硫酸盐、氯化苯胺、硫氰化钾、重铬酸钾、生物碱、苯肼等都是较好的硝酸酸洗缓蚀剂,但工业的使用价值不高。
70年代以来国内研制了缓蚀效果较好的Lan-5、Lan-826和BH-25等硝酸缓蚀剂。
2.1.5氨基磺酸酸洗缓蚀剂[9]
氨基磺酸是一种粉末状中等酸性的无机酸。
在酸洗过程中,不易挥发,在水中的溶解性好,不会发生盐类析出沉淀的现象,且不含卤离子,适于清洗钙量多及其他金属的碳酸盐、氢氧化物的垢类。
但它酸洗氧化铁能力差,并且在60℃以上则发生分解现象。
故其很少应用于大型锅炉的酸洗,一般应用于铜管的酸洗。
氨基磺酸酸洗缓蚀剂主要有Lan-826、O'
Bhibit(二丁基硫脲)、LN500系列。
此外还有二丙炔基硫醚、丙炔醇、季铵盐、乙基硫脲和十二胺等。
现国内常使用的氨基磺酸酸洗缓蚀剂为TPRI-7型缓蚀剂,通过对各种材质的静态腐蚀速率试验结果表明,缓蚀剂的腐蚀速率控制在0.6g/(m2·
h)左右,效果很好。
此外,对于EDTA清洗缓蚀剂,我国研究EDTA清洗技术是从20世纪80年代初开始的,EDTA清洗缓蚀剂大部分是复配而成的,如MBT+乌洛托品+OP-15、对十二烷基吡啶氯化物+OP-15及MBT+联氨+硫脲+乌洛托品等。
这些缓蚀剂的配方在现场应用时,需要将每个组分单独加入,且缓蚀效果不理想,不利于现场操作,都没能得到发展。
目前国内常见的EDTA清洗缓蚀剂有MBT、TSX-04、N2H4、乌洛托品、YHH-1、TRP-6等。
另外,选择柠檬酸酸洗时,由于柠檬酸酸洗时的温度高,循环速度快,因此在选择柠檬酸酸洗时,缓蚀剂必须适用这种条件。
常用的缓蚀剂有乌洛托品、硫脲、邻二甲苯硫脲、若丁、工业二甲苯硫脲等。
2.2油田缓蚀剂的研究现状
国外研究油田缓蚀剂起步较早,1949年,美国报道了有机含N咪唑啉及其衍生物抗CO,腐蚀的油田缓蚀剂专利。
70年代未,华中理工大学和四川石油管理局井下作业处合作研制出7701复合缓蚀剂[10],我国才解决了油井酸化缓蚀剂技术难题。
由于各油田的工况不同,影响缓蚀剂的因素也不相同,没有具有普遍适用性的油田缓蚀剂,国内石油管材研究所、沈阳腐蚀所、四川石油管理局、大庆、华北、胜利等油田的研究所等研制出CZ3、DPI、IMC、CT2、TG、WSI等系列油田缓蚀剂,并成功运用于各油气田,取得了良好的缓蚀效果。
目前,国内外在油田缓蚀剂领域的研究仍十分活跃,主要针对全面腐蚀,特别是对CO,和HC1腐蚀的缓蚀技术的研究更为突出。
近几年,许多油气田的腐蚀速率极高,不能用电化学腐蚀解释,经分析腐蚀产物,发现有微生物尸体存在,抽取井底样液,在显微镜下观察到活动的微生物,Johnson[11],Rosser[12],Fan[13]引等研究了抑制微生物腐蚀的缓蚀剂,取得了较好的成效。
然而对抑制其他局部腐蚀尤其是应力腐蚀的缓蚀剂研究较少,有关报道很少。
油田缓蚀剂的研制思路基本上是分析具体井中设备腐蚀机理,确定抑制腐蚀的化学结构,利用软硬酸理论等进行缓蚀剂的目标分子的设计,选择合适的合成路线进行制备,并用各种方法进行性能测试和缓蚀效果评价单靠一种成分难以达到满意的缓蚀效果,石油工业用缓蚀剂往往都是几种缓蚀成分按一定比例进行复配,通过协同效应提高缓蚀率。
产生协同效应的机理随体系而异,许多还不太清楚。
原则上阴极型和阳极型缓蚀剂复配,缓蚀剂和增溶分散剂复配,兼顾不同金属的复配等。
腐蚀介质、流速、温度、压力、缓蚀剂浓度与类型、加药量、加药方式(连续注入和一次性注人)和加药周期都是影响缓蚀剂性能的因素[14]。
目前,国内外使用的油田缓蚀剂大多是吸附型缓蚀剂,主要缓蚀成分是有机物,如链状有机胺及其衍生物、咪唑啉及其盐、季铵盐类、松香衍生物、磺酸盐、亚胺乙酸衍生物及炔醇类等。
丙炔醇类、有机胺类、咪唑啉及其衍生物类、季铵盐类缓蚀效果较好。
从报道的情况看,研究的吸附型缓蚀剂主要有液相、气/液双相和沉降型缓蚀剂。
液相缓蚀剂只适用液相介质中防腐,对气相中的设备无缓蚀效果。
气/液双相缓蚀剂用于抑制含水井液体部分及液面100~500m管段的腐蚀,它既含液相又含气相缓蚀成分[15],因此,既具液相又具气相保护作用。
由于加入油气井中的缓蚀剂,易被流动的介质带走,或是被提取出的物质携出,造成浪费,因此,开始研究沉降型缓蚀剂。
沉降型缓蚀剂(加重缓蚀剂),易沉降到井底,并在井底缓慢释放[16]。
在一定工艺条件下,沉降型缓蚀剂的缓蚀是采用螯合技术或高分子膜技术,将交联剂、螯合剂或高分子膜体和溶剂混合生成螯合物或制成微胶囊状,目前以螯合物产品为主。
2.3气相缓蚀剂的研究现状
2.3.1单组份气相缓蚀剂
在早期,人们常用樟脑来保护铁制的军用物资、机器和零部件。
随着科学技术的发展,研究者发现胺和胺盐能有效地保护钢铁,现在已经二环己胺和二环己胺盐以及其他胺是很好的钢铁大气缓蚀剂[17—19]。
1943年6月美国壳牌公司(ShellDeveIopmentCo.)研制出亚硝酸二环己胺(PI一260),并获得成功。
使用之后,引起了防锈工作者的极大兴趣,已发表有关文献200多篇。
由于亚硝酸二环己胺室温下的饱和蒸气压低,保护时间长,保护效果好,到目前为止,它仍然是用得最多、最普遍的钢铁气相缓蚀剂。
但一般试验条件下,亚硝酸二环己胺的保护效果并不好,其原因被认为是缓蚀剂通过液体薄层扩散到金属表面的速度过慢,即它保护的诱导期比氧腐蚀的诱导期长,以致在缓蚀剂到达金属表面时金属已发生了腐蚀[20]。
研究表明[21],亚硝酸二环己胺只有在充分预挥发、充分预膜的条件下,才能对钢铁设备起到非常好的保护效果,所形成的保护膜才具有很好的耐久性,而且保护时对系统的严密性要求不高,可用于经常打开的包装体系,但由于诱导期过长。
不宜单独用于闲置设备的保护。
英国于1945年起对气相缓蚀剂进行了研究,发现碳酸环己胺(CHC)对钢铁具有较好的保护作用。
研究发现[22],碳酸环己胺在室温下的蒸汽压为53.33Pa,能较快起保护作用,可用于需要很快起保护作用的场合。
据报道[23],碳酸环己胺可用于经常打开的包装体系,因为它的蒸气能迅速饱和容器,但实际上碳酸环己胺对常用设备的保护效果并不理想,英国曾用碳酸环己胺保护停用设备获得成功。
但后来发现它难以保护垢下金属。
魏刚等人[24,25]研究了碳酸环己胺的使用工艺及作用规律后发现,碳酸环己胺在不预挥发和不预膜的情况下,就能够起保护作用,但是它存在保护期短、保护膜耐久性差、对系统密封性要求过严和难以保护沉积物下方的金属等不足,认为碳酸环己胺仅适用于封存严密的、表面干净的化工装备金属的保护,此外,碳酸环己胺的价格也较贵。
每公斤在80元以上。
碳酸按、碳酸氢铵、苯甲酸铵和乌洛托品也可以单独作为气相缓蚀剂保护剂使用;
碳酸铵和碳酸氢铵容易挥发,都是有效的气相缓蚀剂,但它们气味难闻,对保护体系的密封性要求高,所以限制了它们的推广应用[26—30]。
2.3.2混合型气相缓蚀剂
选择气相缓蚀剂必须具备两个最基本的条件,即在其成分中应该含有一个或一个以上的缓蚀基团,再就是要具有适当的蒸气压。
蒸气压过低,诱导期太长。
缓蚀剂气体在短期内不能饱和保护空间,容易发生先期腐蚀;
蒸气压太高,缓蚀剂挥发过快,如设备密封性不够好.缓蚀剂气体流失过快,使防锈期变短,需增加用量,提高保护成本。
因此需要将不同蒸气压的两种或两种以上的缓蚀剂混合使用,如国内外较多使用的亚硝酸二环己胺与碳酸环己胺的混合药剂,亚硝酸二环己胺在21℃时的饱和蒸气压为0.016Pa。
而碳酸环己胺在2l℃时为53Pa,两者混合使用,可取长补短,既能持续长效防锈,又能缩短缓蚀剂气氛达到平衡的时间,抑制设备的先期腐蚀。
气相缓蚀剂的混合配方,一般是从各种无机、有机气相缓蚀剂中筛选复配后经试验来获取的。
气相缓蚀剂混合起来使用的例子很多;
如尿素和亚硝酸单乙醇胺的混合物、亚硝酸二环己胺80%和亚硝酸二异丙胺20%的混合物、苯甲酸和乌洛托品的混合物、苯甲酸、乌洛托品和亚硝酸钠的混合物、苯甲酸铵、碳酸铵和亚硝酸钠的混合物等。
王忠义等人[31]研究认为苯甲酸与乌洛托品可以代替碳酸环己胺,用于停用设备保护,没有明显的毒害作用,气味也不太难闻,可以用于长期停用的设备的保护。
采用氯化钱加碱类物质对停用设备进行保护,也取得了较好的保护效果,且药剂价格极为便宜,降低了保养费用。
国内兰州华荣清洗防腐技术公司研制的TH901和HL91l停用设备保护剂[32],经一些厂家的使用,取得了较好的保护效果。
常用的复合气相缓蚀剂主要有亚硝酸二环己胺80%+亚硝酸二异丙胺20%、苯甲酸钱+乌洛托品+亚硝酸钠、苯甲酸单乙醇胺+尿素+亚硝酸钠等[33,34]。
2.3.3高效低毒气相缓蚀剂
在气相缓蚀剂的研究和发展过程中,亚硝酸二环己胺曾占据着主导的位置,以至于世界各国在介绍气相缓蚀剂的文献中,仍常以亚硝酸二环己胺为代表。
但是,亚硝酸二环己胺的毒性越来越受人们重视,进入二十一世纪,在可持续发展战略的推动下,开发低公害、无污染的气相缓蚀剂是当务之急。
国外报道[35]的高效低毒和高稳定性的钢铁用气相缓蚀剂多系咪唑类化合物,诸如2一甲基咪唑、2一乙基-4-甲基咪唑和2一异丙基咪唑等,其防锈性能优良,可满足美军标准MIL—I一22110,热稳定性好,毒性低,对人体无有害的生理毒性。
并能被细菌降解。
它们可以从维生素髓生产过程中的副产物中提取,成本较低。
综上所述,大部分高效低毒型气相缓蚀剂尚处于实验室研究阶段,离大规模生产及使用尚存在一定距离,高效廉价的气相缓蚀剂既能提高设备的保护效果又能降低保护成本,是工业化应用的重点:
由于单组分气相缓蚀剂的挥发性与保护时间、保护效果之间的矛盾,即低挥发VPI与先期腐蚀、高挥发VPI与保护时间短的矛盾,因而混合型气相缓蚀剂是研究开发的重点。
2.4高效环境友好型缓蚀剂的最新进展
依据可持续发展的社会理念,当今社会需要的是绿色化学,对环境有好多的材料。
因此应运而发展的环境友好型缓蚀剂的发展。
2000年,刘铮[36]采用失重法研究了植物型缓蚀剂没食子酸对碳钢的缓释性能。
实验表明,在40℃和条件下,在5%稀盐酸中,使用没食子酸与六次甲基四胺有较强的协同作用,其复配缓蚀率大于96%。
通过研究找到了没食子酸在碳钢上的吸附等温式,计算出钢溶解的表观活化能,从而揭示了没食子酸在碳钢上的吸附机理。
2002年,张大全[37]讨论了缓蚀剂应用开发的进展及其对环境的影响。
基于绿色化学概念,从缓蚀剂的分子设计,合成路线、复配增效和应用性能等方面出发,综合评价和认识缓蚀剂应用开发的环境负荷及经济效益,探讨了缓蚀剂的发展方向。
王慧龙[38]等进一步介绍了环境友好缓蚀剂的研究进展,指出有机缓蚀剂中,醛类、胺类、梭类、杂环化合物通常由极性较大的N,O和S等原子为中心的极性基和C和H等原子组成的非极性基构成,能以某种键的形式与金属表面结合,氨基酸是分子中兼具有碱性氨基和酸性梭基的两性化合物,缓蚀效率随分子中碳氢链长度和氨基数目的增加而增大。
2007年M.M.EI-Rabiee,N.H.Helal[39]等人运用开路电位测量、极化曲线和电化学阻抗谱(EIS)的研究方法,测试了腐蚀电流Icorr、腐蚀电压Ecorr和电阻Rcorr。
研究了甘氨酸、谷氨酸、丙氨酸、领氨酸和半胧氨酸5种氨基酸,在不同的PH值的铅矿水溶液中的腐蚀控制。
考察了在酸溶液CL-对缓蚀效率的影响在中性和碱性溶液中,加人氨基酸能提高金属的腐蚀的极化电阻。
在加缓蚀剂和无缓蚀剂情况下,研究了组氨酸、甘氨酸,在浓度比较低(25mmol/l)时最有希望作为环境友好性缓蚀剂。
有机胺类化合物是缓蚀剂中应用最多的一类物质。
脂肪胺、芳香胺、一元胺、二元胺或聚胺及它们的盐均被广泛应用于金属的缓蚀领域。
开发环境友好的胺类缓蚀剂必须引人新的低毒性的有机胺化合物来替代有毒的胺化合物及其盐的应用。
例如以更多的长链脂肪胺、聚胺来替代和减少芳香胺的应用。
聚胺及其衍生物主要用在石油工业中,由聚胺制成的酞胺、咪哩琳及聚酞胺等化合物作为低毒性的缓蚀剂被广泛用于抑制金属的腐蚀。
目前研究开发的狡酸类环境友好缓蚀剂多数为脂肪族取代梭酸,主要应用于中性水介质。
酞基肌氨酸合成原料易得,无毒性,易被生物降解,不会造成环境污染,且PH值适用范围很宽(6-11),是一种很有发展前途的缓蚀剂[4]。
其缓蚀机理主要是通过与金属离子赘合,形成单分子层的鳌合被膜吸附于金属表面,同时分子中疏水性的长链烃基可定向排列于金属表面,使金属得到保护。
S-梭乙基硫代琥珀酸[cesta]是近年来为满足环境保护的要求而出现的新型非磷缓蚀剂。
cesta具有溶于水、生物降解性好、低毒、在较宽PH值范围内均具有缓蚀和阻垢等特性。
目前已由日本MTS公司投产,应用前景良好。
3缓蚀剂的应用
缓蚀剂广泛地应用于石油化工、机械制造、交通等工业部门,并在某些工业生产中成为不可取代的重要防护措施,列入到生产工艺或操作规程中[2]。
石油工业是使用缓蚀剂最多的部门之一,从石油的钻探、开发、集输到炼制都要用到缓蚀剂,而用于油水井酸化的缓蚀剂,主要目的是为了减缓酸液对油管、套管的腐蚀,延长油管、套管的使用寿命[16],其中新型高效油气井酸化缓蚀剂——曼尼希碱与丙炔醇复配体系,缓蚀效果特别明显。
对一种咪唑啉衍生物的研究结果表明:
油田平均检泵周期由83d延长到158d,81口井由164d延长到256d以上,最长达到488d,井下管柱和地面集输系统的腐蚀明显减轻。
因此,炔醇类和咪唑啉类缓蚀剂在油田应用中起到重要作用。
随着技术的进步,缓蚀剂的应用领域已从传统部门扩展到新能源、电子器件、航天工业等高技术领域,一些新兴产业如化学电源、飞机制造、汽车等也开始使用缓蚀剂技术来改善产品的质量或提高生产效率。
对不同种类缓蚀剂对非晶态镁基储氢电极充放电循环稳定性影响的研究结果表明:
缓蚀剂可以改变镁基储氢电极表面与电解液之间的界面性质:
在不显著降低电极最大初始容量的同时,改善了电极的循环稳定性。
此外,随着能源战略的实施,缓蚀剂应用于污水治理和回用、烟气脱硫等环境治理工程开发报道越来越多。
4对缓蚀剂未来发展的展望
近年来,缓蚀剂受到了人们的极大重视。
缓蚀剂作为一种经济适用和高效的防腐蚀产品,在保护资源、减少材料损失方面起