日用瓷缺陷分析Word格式.docx
《日用瓷缺陷分析Word格式.docx》由会员分享,可在线阅读,更多相关《日用瓷缺陷分析Word格式.docx(21页珍藏版)》请在冰豆网上搜索。
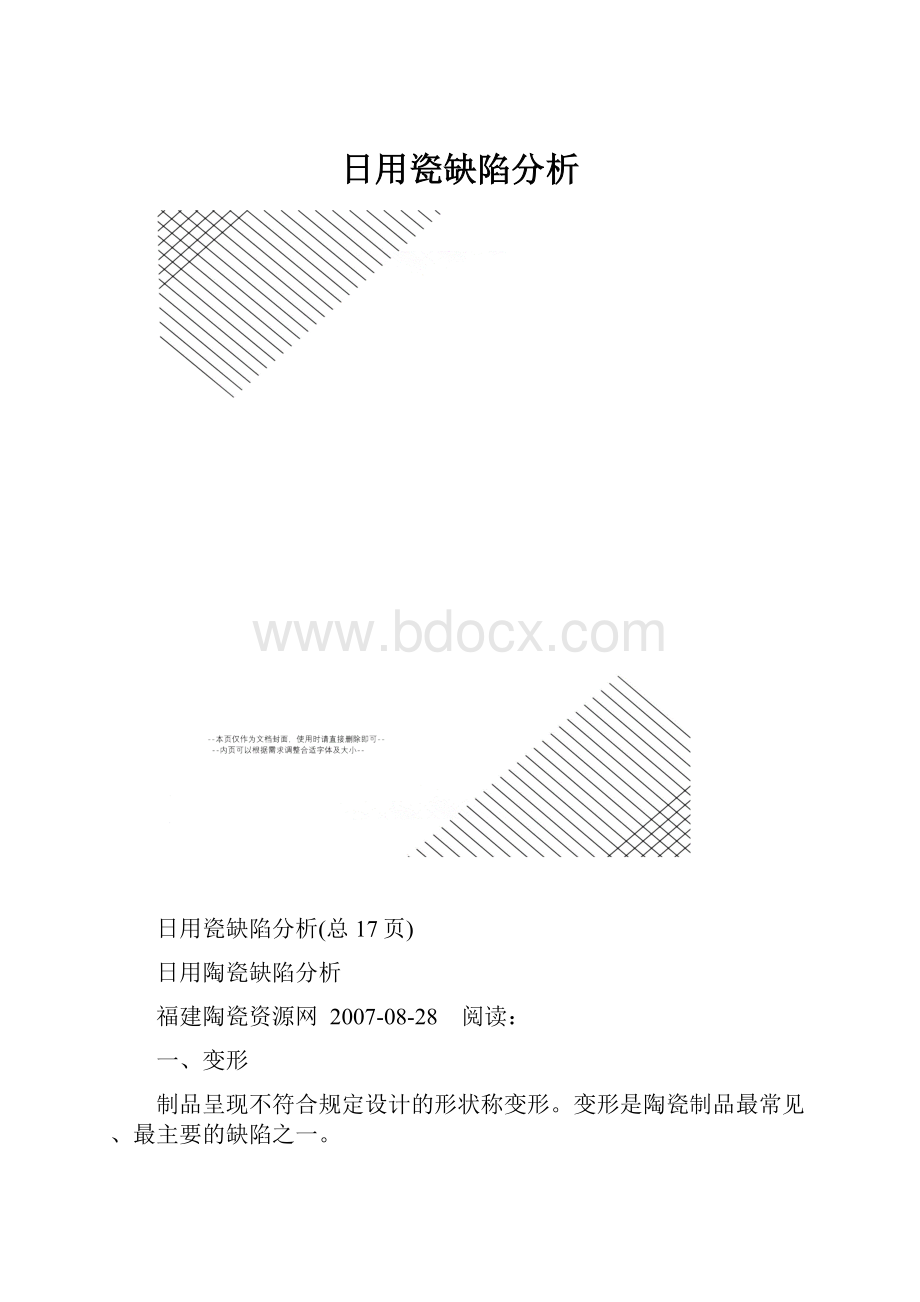
②坯体各部位干燥不均匀。
③坯体放置不平或放置方法不妥。
6、装坯、装窑工艺不当
①坯体入窑水分过高。
②使用高温结构强度低的匣钵、棚板等窑具;
使用的匣钵内底不平、开裂又未用垫饼;
使用不平或有杂质的垫饼。
③装坯不正或因搬动时振动,使坯底足部分窜离垫饼,位移下码,烧成时坯体因收缩不均匀而向一边倾斜。
④匣钵柱未保持平、稳、正。
7、烧成工艺不当
①窑内各处温差过大。
②烧成时升温过急;
烧成温度过高;
高火保温时间过大。
8、石膏模品质差
①石膏模结构不合理;
制造不符合要求;
规格不统一;
致密度不一致。
②石膏模含水率不均匀;
过干、过湿、过旧;
模型变形或磨损。
③石膏模与模座的吻合度差,不同心。
总之,根据陶瓷生产工艺的特点,变形的起因基本上可归纳为三个方面:
机械应力、结构应力、坯料组成。
当破坏力不大于破坏活动体强度时导致变形,当破坏力超过坯体强度时则发生开裂。
(二)日用陶瓷的变形表征及产生原因
日用陶瓷变形的表征有多种,其中几种最常见的变形及产生原因,分述于下:
1、边沿下垂
边沿下垂是指制品口沿坍塌或直直口器的口沿向外翻撇,边缘局部或全部下垂。
①制品造型设计不合理,器皿腹部的厚度不够;
底径过小;
折边的转折处结构不合理,折边向四周伸展幅度过大;
蓄泥厚度及位置不当等。
②滚头或样板刀位置调整不好,使坯体口沿太薄。
③模型、滚头的沿部弧度小,使坯体口沿外翻。
④塑压成形的坯体太软,因边缘余泥自重使坯体变形。
⑤坯体太湿即进行脱模,脱模操作用力过大,动作过猛,坯体附于托坯饼上成跌落趋势,使坯体口沿外翻。
2、收口
收口是指制品口沿向内收缩过大。
主要因脱模、整形操作不当而引起。
3、三角变形
三角变形是指制品边沿呈三角形变形。
多产生于脱模工序,如模型干湿不均匀或带模干燥时温度不均匀;
强行脱模等。
4、多角变形
多角变形是指制品呈多边形变形。
①模型本身变形;
含水率不均匀。
②坯泥水分不均匀。
③滚压、旋压成形时割边不平整或不干净,坯体口沿留有成形余泥。
④干燥不均匀;
强行脱模或脱模操作不当捏伤坯体腹部;
托坯饼不平。
5、塌坯
塌坯是指制品整体往下坍塌变矮或向一边垮。
①脱模操作不当,使坯身向一边垮。
②湿坯因跌落而造成坍塌变矮。
③烧成温度过高或高火保温时间过长,使制品塌陷变形。
6、凹凸底
凹凸底是指制品底部中心小范围呈弧形凹陷或凸起。
①坯料耐火度低;
烧成温度过高。
②坯泥含水率过高或过低,水分分布不均匀。
加工不当;
滚头顶部超越坯体中心的距离过小或过大;
滚头转速偏低或偏高;
转速比过小或过大。
④滚头或型刀安装不正确。
⑤石膏模底板工作面平度不符合要求;
模型太湿,吸水率减弱。
⑥制品器型结构不合理,口径与底部比例不当,底径过大超过自身负荷而沉底。
7、厚薄不匀
厚薄不匀是指对称形制品同一横断面厚薄不一致,呈一边厚一边薄。
①石膏模衔口车削不好,使石膏模与模座配合太松或太紧。
②滚压或旋压成形时,模型在模座中放置不平整。
③成形机制造精度差,轴承间隙过大,成形时振动大。
④修坯布时,坯件在模座上晃动,操作时用力不均匀。
8、嘴耳把歪
①嘴、耳、把的位置、大小、轻重、伸张角度等设计不合理。
②强行脱模,用力过重,脱模后存放的托板不平,使嘴、耳、把附件变形,其形状不标准;
或其接头处的形状修削得不好,与主体的形状不相吻合;
主、附件的含水率不一致,悬殊大。
③粘接泥配方、制备、使用不当;
粘接泥无专人配制,其细度、水分、添加剂等控制不好。
④粘接手法、技巧掌握不好,粘接时附件与主体未对正位置,着力不均匀或用力过重,使粘接后出现歪斜、附件变形。
⑤干燥不均匀,烧成温度过高等,因变形而导致嘴、耳、把歪斜。
9、盖身不合
盖身不合是指制品盖与身子不相吻合。
又称为盖子盖合不严。
①盖、身的形状或尺寸设计不当。
②成形或修坯不佳,使盖、身的形状不符合标准。
③烧成时,在盖或身的口面上有釉缕、疙瘩或粘附物等。
④分别烧成盖和身时,烧成温度显著不同,其中之一过烧或生烧,使其形状、尺寸发生了变化。
盖与身同时烧成时,配错了盖和身。
二、裂纹
裂纹是指制品胎、釉开裂而形成的纹状缺陷。
下面按裂纹产生的部位。
分述各种裂纹产生的主要原因。
1、层裂层裂是指胎体有分层现象而产生开裂。
注浆成形的坯体其中间分层又叫重皮。
①坯料本身含有空气,存在夹层。
②成形操作不当。
2、口裂口裂是指制品口部开裂。
①坯泥可塑性与结合性差;
含水率太底或不均匀。
②热滚压成形时,滚头温度过高;
旋压、滚压成形时割边不平整、不干净、坯体口沿粘附有余泥,使坯体口沿干燥收缩不均匀。
③注浆成形时,泥浆性能差;
石膏模过干或其口沿部位吸水过快。
④脱模过旱或过迟,倍模操作不当,使坯体口沿部位受损伤。
⑤修坯、施釉、釉下装饰、取釉时,坯体口沿过薄、未干、未放置平稳,操作不当,用力过重而伤坯或碰损。
装坯时,用一只手取坯,大拇指掰坏坯体。
⑥机械设备不精良。
振动大。
3、底裂底裂是指制品的底部开裂。
①旋压、滚压成形时,泥料过硬或水分不均匀;
投料不够后又添料;
投泥不正;
下压动作过猛。
②半成品加工过程中,坯体过湿,所用吸坯器的面积太小,吸坯、放坯时用力过大。
③挖底时,机械设备振动,坯体受力不均衡,使坯体内表面产生裂纹,或裂纹呈内表面长、外表面短的形态,并且坯身向里面凹陷。
4、肩裂肩裂是指制品的肩部开裂。
①坯料可塑性和结合性差,使坯体干燥强度低;
坯泥含水率过低;
成形时投泥位置不正。
②在半成品加工过程中,将坯件放置于坯座时碰伤坯体肩部;
坯座直径过大、过小或其形状不适合坯
③用吸坯器吸坯时,下压用力过猛或未吸稳坯件,坯件不慎跌落,损伤其肩部。
5、底足裂底足裂是指制品的底足开裂。
①坯泥含水率过低,可塑性与结合性差;
成形时,泥饼直径过小,投泥位置不正,成形压力过大。
②带模干燥时间过长,脱模过迟,坯体在模型中底足开裂;
脱模时,足部被模型排气孔中的余泥粘坏,使底足破裂。
③挖底、取釉操作不当;
刀具不锋利;
用力过猛或不均匀;
使用的机械设备振动,使坯体底足撞击受伤。
④磨坯布时,手法不当,手指在坯底板上用力过重有伤坯体,其裂纹一般从底足到肩部。
⑤大件产品垫底烧粉过少,烧成时影响坯体收缩,使坯体烧结与收缩不均匀。
6、嘴耳把裂踊耳把裂是指嘴、耳、把附件与主体的接头处开裂。
①粘接件之中的主件坯体过薄或过湿;
嘴、耳、把附件与主体的含水率相差过大,或接头处的形状不相吻合;
或附件与主体的素烧温度不同,吸水率不同。
②粘接泥配方不当,粘性差;
粘接泥浆调配不好,水分过低。
③粘接技术不熟练,粘接时用力过猛或过轻,使嘴、耳、把的接头处其周围粘接泥浆压喷不均匀或未压喷出来造成粘接不牢;
粘接壶嘴、把等施加泥时用力过重有损粘接件;
粘接操作时,取、放坯体不正确,使体受冲击。
7、眼裂眼裂是指壶类制品的漏水孔眼周围局部形成裂纹,或指玲珑眼边缘开裂。
①泥料可塑性与结合性差,坯体干燥强度低。
②在坯体含水率过低时打孔眼;
打眼机本身有毛病,打眼管不符合要求,打眼器具不锋利,打眼时用力过大。
三、斑点斑点是指制品表面呈现的有色污点。
又称为铁点、黑点。
1、原料自身因素及坯、釉料制备方面
①原料含有过多的有害杂质,使坯、釉料中混入含铁杂质,且在坯、釉料精制过程中未能兖分磨细、过筛、磁选而除去。
②原料精制、加工、运输过程中,设备磨损或生锈,有金属铁的铁锈混入坯、釉料。
③坯、釉料管理不善;
回坯泥管理与处理不当。
2、半成品制作过程方面
使用了生锈的铁器工具与设备。
3、厂区环境卫生方面
环境卫生不好,飘尘污染;
釉坯存放过久,且未清除干净灰尘即装坯、入窑。
4、使用窑具方面
使用含硫化铁等杂质较多的匣钵、垫饼等窑具。
5、烧成控制方面
四、熔洞熔洞是指易熔物在烧成过程中熔融而产生的孔洞。
①原料拣选、洗涤不严;
在坯、釉料制备过程中,过筛次数少,筛网目数低,跑筛和漏筛;
成形用的坯泥、泥浆、釉料等保管不善,有杂质混入。
②成形割边、修余泥时,将石膏模碎屑刮入坯体或坯料中。
③厂区及车间卫生管理不好;
回坯泥不清洁又处理不好,有杂质混入。
五、落渣落渣是指制品釉面粘有匣钵、糠头灰等渣粒。
①匣钵、棚板品质低劣,热稳定性差,耐火度与高温荷重软化温度低;
匣钵粗糙、疏松,有裂隙与破损,口沿松散,口沿与外底没有涂层或涂层过薄,匣钵有粗砂剥落掉入制品。
②装坯、装窑操作一规范。
六、粘疤与底沿粘渣粘疤是指烧成时坯体与外物粘接形成的残缺。
底沿粘渣则是脂制品底足边缘粘有细小渣粒。
①一匣多坯的匣钵,因品质不好,耐火度低或高温荷重软化温度低,匣底凹陷变形,或坯体端面不平,使几只制品互相粘接。
一匣一坯的匣钵,因造型不当,设计高度太低,直径过小,匣钵内残留有碎渣等而造成制品粘匣。
②装坯、装窑不端正、不平衡,使坯体间隔的均衡性发生变化,坯体产生位移,使坯体与坯体,或坯体与匣钵相接触,以致损坏釉面或胎体。
③彩烤时,产品之间不留间隔,摆放过密,烤花温度过高,使制品釉面熔化而相互粘连。
④入窑坯件严重变形,坯体耐火度低;
器皿的底足造型不当;
施釉过厚,釉高温粘度过低,烧成温度过高而造成流釉;
坯体取釉高度不够或取峦不干净;
垫饼耐火度低或有易熔物;
垫饼涂料太薄或不均匀;
钵底烧粉垫得过少且有粗颗粒熔融,烧成后均容易使制品底足粘在垫饼或匣钵上。
⑤烧粉品质不好,垫粉操作不谨慎,钵底烧粉铺得过厚或不均匀,局部形成堆积,造成制品底沿粘渣,或在装坯时用粘有烧粉的手触摸坯体。
⑥制品的口沿或底足、装坯针点未打磨光滑,不平整。
七、底足粘脏底足粘脏是指制品的底足粘有其它杂质而变色。
①装坯时,匣钵底部未垫Al2O3粉或垫得太少;
所用Al2O3粉内混有某种杂质而粘于制品的底足;
用垫饼装坯时,垫饼太湿或垫饼之下烧粉含水分太多,烧成后生成红色物质。
②匣钵未涂涂料,涂层太薄或脱落;
匣钵上的铁点粘染于制品底足,烧成后铁质熔化沾染,底足被着成红色。
③坯泥原料和匣钵中含铁等着色氧化物,在高温下为γ—Al2O3所收集,被制品无釉的底足吸收,使底足着成黄色。
④烧成泠却初期的高温阶段冷却速度过慢,已经还原的低价铁又重新被氧化成高价铁,使底足呈黄色。
八、疙瘩与泥渣疙瘩是指釉下坯体凸起的瘤状实心体。
而泥渣则是指尚未清除的泥屑、釉渣残留于坯体造成的缺陷。
①在石膏模制造过程中,因膏水比、搅拌、脱气、注模速度等方面控制不好,使石膏模的工作面产生较大气孔;
或在石膏模干燥、运输过程中损伤模型工作面,使其成形的坯体表面产生疙瘩。
②原料与成形车间未做好卫生工作,有较干泥料颗粒混入坯料面造成疙瘩。
③因成形、修坯、施釉、挖底、取釉、装坯等工序操作不慎,将泥屑或带釉残渣粘附于坯体表面,又未及时清除干净即流入烧成,而造成制品泥渣缺陷。
九、缺泥与磕碰缺泥是指坯体残缺现象。
而磕碰则是指制品被冲击或残缺。
①制品造型设计不合理,口部过薄;
底足较薄、过深,弧度不当。
②坯料可塑与结合性差,成形困难,坯体干燥强度低。
③成形时用了破旧模型;
投泥不足、不正,后又添补泥料;
坯体口沿余泥未截平整;
成形压力不够;
石膏模过干、工作面局部凸起;
成形底面积特别大的坯体时所用泥饼未经预压,使成形后的坯体残缺。
④在半成品加工、运输过程中造成坯体残缺或碰损,又未进行必要的修补;
坯体素烧温度过低或取放不当,使素坯残缺;
装坯检查不严,带有残缺之坯体进入烧成,均会导致缺坯。
⑤从本烧出窑起均可能发生制品磕碰,主要由于开窑、搬运、彩饰、检验、包装等工序操作失误所致。
十、起泡起泡分坯泡与釉泡两种。
坯泡是指釉下坯体凸起的空心泡。
而釉泡则是指釉表面的小泡。
1、坯泡
①坯料中碳酸盐、硫酸盐、碳素、有机物等杂质含量过多。
②可塑坯料陈腐与捏练不充分,内夹有空气泡或混有块状杂质;
注浆成形时,注浆速度过快;
泥浆的电解质用量不当;
剧烈地搅拌泥浆;
泥浆存放过久或落入杂质,致使泥浆中窝藏有空气泡带入坯体;
成形时石膏模太干、太热。
③烧成时因氧化不足产生氧化泡,主要原因有:
坯体入窑水分过高;
装窑密度过大;
窑内温差大;
氧化气氛不足或波动、不稳定;
氧化阶段升温过急,中火保温不充分;
还原阶段开始过早,使坯体各组分氧化分解反应不充分,水蒸气、CO2、SO2等气体未能充分排出,当釉熔融,封闭坯体气孔以后,气体还继续向外排出而呈现凸泡。
④烧成时因还原不足产生还原泡,主要原因有:
氧化结束时温度过高,还原阶段开始过迟,或操作时不能保持还原气氛,升温过快,窑内温差过大使局部区域还原严重不足,致使硫酸盐和高价铁的分解温度提高,产生的气体无法逸出而形成气泡。
表现为胎体断面粗糙、透明度差,气泡断面呈淡黄色。
⑤烧成时因过烧产生过火泡,主要原因有:
烧成温度过高或窑内局部温度过高,超过坯体烧结温度范围,使坯体膨胀起泡。
2、釉泡
①釉料中高温分解物含量高;
釉料始熔温度偏低,玻化过早;
釉熔体粘度太高或表面张力过大,对釉层内气体逸散起阻滞作用。
②釉浆过细、过稠;
存放过久,有机物腐烂发酵;
杂质混入。
③施釉时坯体过干、过热,不但使釉料未能被坯体均匀吸收,同时还易封闭住气孔,使釉中水蒸气无法外逸而形成釉泡。
釉浆搅拌不均匀,颗粒沉淀,表面水分多;
湿坯施釉;
两次施釉之间的时间相隔太久;
釉坯存放时间过长等均容易产生釉泡。
④素烧温度低;
使用含硫量过多的燃料;
坯体入窑水分过高,窑内水蒸气过多;
氧化不足或还原过早,使分解产物和沉积的碳素在釉玻化之前未能全部分解逸出,窝藏在釉层中;
还原阶段,还原气氛过浓,还原时间过长,造成碳素沉积,在釉熔化后碳素继续燃烧,所生成的气体被釉液包裹,遂成釉泡。
⑤烧成温度偏低,釉的高温粘度大或釉层级过厚,气泡不易排除而滞留在釉层中;
烧成温度过高,溶解在釉中的气体又被放出形成新的气泡。
⑥因坯体内可溶性盐类在干燥过程中随水分扩散蒸发,而聚集在坯体的口部边沿或棱角处,降低了这些部位的软化温度,在烧成过程中,这些部位的受热面积较大,较早地玻化,气体不易逸出而形成一连串小釉泡,俗称“水泡边”。
十一、针孔与橘釉
针孔是指制品釉面呈现的小孔,又称棕眼、猪毛孔。
针孔是陶瓷制品最常见、最主要的缺陷之一。
若釉机密集针孔群,使釉面缺乏光泽,外观呈橘子皮状,则称之为橘釉。
1、坯料方面
①原料中有机物、碳素、碳酸盐、硫酸盐、氧化铁等杂质含量过多;
坯料中高可塑性粘土用量多,坯料灼减量大,烧成时排出气体多;
坯体透气性差;
化妆土厚度不当等。
②可塑泥料颗粒过粗或含水率过高;
陈腐时间短,捏练不充分;
真空练泥机真空度不足,未充分排除泥料中的空气;
坯料混有油污等。
③注浆用的泥浆存放过久或存放处温度太高,泥浆中有机物发酵;
泥浆未进行真空脱泡,搅拌不均匀或太剧烈使泥浆夹带空气泡;
泥浆泵使用不当,漏入空气;
电解质选择及用量不当;
泥浆密度过大,流动性小;
注浆速度过快,窝藏在泥浆中的空气泡不易排除而带入坯体。
2、釉料方面
①釉料始熔温度低,高温粘度大,流动性小,熔融釉不能均匀布满胎体表面;
表面张力过小,使峦面小气泡破裂时所形成的针孔难以弥合。
②釉料颗粒过粗;
存放时间过长,釉浆中有机物腐烂发酵。
③釉浆过浓或过稀,水分不均匀。
3、成形、施釉方面
①注浆成形时,石膏模过干、过热。
②施釉时,坯体过干、过热,水分不均匀;
坯体有浮灰、油污,未清除干净;
坯体修整不善,表面不平。
③第一次施釉与第二次施釉之间的间隔时间过长;
坯体较疏松且施釉前坯体太湿,施釉过薄;
素烧坯气孔率过高,施釉过薄,釉被坯体所吸收。
④施釉时间过长,生坯长时间接触釉浆,吸水过多,在釉层鼓起小泡。
釉层过厚,不仅产生釉裂,也易产生闭口气孔而引起针孔。
4、烧成方面
①坯体入窑水分过高;
燃料含硫量高;
窑内温差大。
②烧成时氧化不足,有机物、碳素、碳酸盐、硫酸盐尚未充分分解而釉已玻化,气孔封闭在釉内,逸出时冲破已玻化的釉面易形成针孔。
③釉熔融温度过高而烧成温度低,升温过急,高温保温时间短,釉熔化不良,逸出气体的痕迹未被釉液填充。
④窑内通风不良,水蒸气过多;
还原气氛过浓,还原时间过长,游离碳素沉积在釉面上,燃烧后残留针孔。
⑤烧成温度过高,釉液化时升温过快,釉面发生“沸腾”形成橘釉;
烧成后在高温冷却阶段冷却速度过慢,釉面析晶、失透无光。
十二、釉缕釉缕是指釉熔化后流聚成的缕状物。
①坯体造型与修整不良,施釉时多余的釉浆得不到均匀流淌。
②釉料调配不良,高温粘度过低,釉发生过熔;
或烧成温度低,釉的熔融状态不佳。
③釉浆密度与施釉操作不当。
十三、缺釉缺釉是指制品表面脱釉,包括压釉和滚(缩)釉。
1、压釉压釉即坯体接头凹下处细条状缺釉。
①粘接泥配方不当,其耐火度过高;
施外釉之前,嘴、耳、把等附件与坯身的接头处已经开裂。
②嘴、耳、把等附件与坯身的含水率不一致;
附件与坯身接头处的形状不相吻合;
粘接操作不当,接头处缺少粘接泥浆或接头周围粘接泥浆压喷不均匀、敷泥施加不均匀,均会使接头处产生较大的应力以致引起压釉。
③施釉前,坯体接头处的棱角部位未抹水或抹水不均匀;
釉料过细;
釉浆过稠;
施釉后釉头未清除干净,造成局部积釉过厚。
④烧成温度过低,釉熔化不好。
2、滚(缩)釉滚(缩)釉即釉面边缘滚缩形成中间缺釉。
①施釉前,未清除干净坯体上的坯粉、灰尘、油渍、落蜡等,使坯与化妆土、釉结合不良;
素烧温度过高或过低;
素烧坯表面过于光滑,或表面有下凹和凸起之处。
②坯釉配方不相适应,釉润湿性能差,高温粘度和表面张力过大;
釉料中ZnO未煅烧且用量大;
釉浆在坯体上的附着力差;
坯釉膨胀系数相差过大;
坯釉在干燥和烧成当中有较大收缩差,导致釉层开裂甚至剥离,减弱了坯釉结合性。
③釉料过细;
施釉过厚;
浸釉操作不当。
釉浆未均匀布满坯体的全部,或局部积釉引起缩釉;
施釉后各工序操作不慎,坯体受碰撞、摩擦、振动,造成釉层局部脱落。
④坯体入窑水分过高,烧成时窑内水蒸气太多,使坯峦分离,釉层剥离而造成缺釉;
大件坯体瓷化不均匀也可能出现剥釉。
十四、釉面擦伤釉面擦伤是指制品釉面出现条痕和局部失光的现象。
①在生产过程中各工序对坯体处理不慎重,坯体伤痕未经修补即进入烧成工序。
②釉面硬度低,容易被擦伤。
③开窑时,制品之间未垫纸,在搬运或堆码制品时擦伤釉面。
④用砂纸擦拭制品上某些缺陷,或在打磨制品边口、装坯针点等处时,不慎摩擦釉面造成伤痕。
十五、生烧与过烧制品未达到或超过烧成温度称为生烧或过烧。
生烧的制品往往发黄,吸水率偏高,釉面光泽度低并且粗糙,抗折强度降低,尺寸不符,敲击时声音不脆。
过烧的制品则会发生过烧变形,尺寸不符,抗折强度降低,釉面起泡或流釉。
①原料品质波动幅度过大;
制泥控制不严;
坯、釉料配方不当;
坯料烧成温度范围狭窄。
②燃料性质不稳定;
烧成温度偏低或偏高;
高温保温时间不足或过长;
烧成气氛不同。
③装窑密度分布不合理,局部过密或过稀;
窑内温差太大,造成了局部制品生烧或过烧。
④测温误差;
匣钵、棚板、窑车耐火材料的材质影响传热。
十六、烟熏烟熏是指制品局部或全部呈现灰黑、褐色现象。
又称吸烟、串烟、吃烟。
①釉料中钙含量偏高,且釉层过厚容易产生烟熏。
②釉料始熔温度过低,高温粘度过大。
③注浆料中掺兑过多的电解质水玻璃。
④燃煤品质差;
窑内通风不良。
⑤烧成时,氧化期与还原期安排不妥,氧化不充分或还原过早,使坯体内的碳素、有机物或低温沉碳未能烧尽就被釉层封闭;
还原气氛过浓,还原结束过迟,烟气严重倒流,均能造成釉层内高温沉积碳素过多,使制品的釉面呈灰黑色。
⑥使用含硫多的燃料,因硫的影响,使釉面呈黄、黄绿或褐色的硫磺斑。
钛含量较多的坯体在氧化气氛中烧成时呈黄色,在还原气氛中烧成时呈不稳定的灰色。
十七、火剌由火焰中飞灰造成制品的黄褐色粗糙面称为火剌。
①匣钵品质不高,有裂隙、缺口、其重叠处密封程度差。
②燃煤挥发分含量高,火焰直接锓蚀制品。
十八、阴黄阴黄是指制品局部或全部发黄。
①坯、釉料中含铁、钛杂质多,且还原气氛太弱;
窑内局部温度偏低还原不足;
强还原阶段开始温度过高,升温过急,使釉面过早熔融,坯体过早烧结,气孔被封闭,还原气氛不能渗入坯内,坯体内Fe2O3未能充分还原成FeO而呈黄色。
②烧成中,高温阶段未期,气氛控制不当,或冷却初期未采取急冷,FeO被重新氧化成Fe2O3,从而使制品泛黄。
③烧成温度过低,使制品生烧,色泽发黄。
烧成温度过高,使制品过烧而呈暗黄色。
十九、色脏制品表面呈现不应有的杂色现象,称为色脏。
①坯体或釉浆中混有某些显色物质,烧成后成为色脏。
②印花或印刷花纸时使用了不清洁的印刷工具;
贴花时使用了不清洁的橡皮刮;
操作者手上染有色料未及时洗净;
贴花的粘贴液中混有脏物;
施彩时操作者不慎将色料、金水、电光水等喷涂到不应有的部位;
用铜版制作的青花贴花纸粘有铜粒且混入釉中,烧成后釉面出现污点。
③彩饰立即将未烤烧的制品堆叠起来,花面相碰、摩擦损坏,互相染成色脏;
或彩烤装炉、装窑时徘列过密,花面相互碰粘,或有碎屑杂物落到制品上生成污点。
二十、彩色不正彩色不正是指制品同一花纹色彩浓淡不均匀或由于欠火而产生不光亮的现象。
①颜料和花纸品质不好,同一花纹存在色彩浓淡不均匀的现象;
贴花纸过期、受潮变质;
贴花粘液含有杂质。
②用铜版制作的花纸,因铜版已旧或印刷时压印不均匀,造成印刷的花纸彩色不均匀。
③颜色釉因配方、施釉不当或过烧而流釉,使釉色不均匀。
④装饰时,手工描绘操作不严,调和颜色的水或油料混有杂质;
喷彩或手工填色不均匀。
⑤烤花窑结构上存在缺陷或局部破损,装窑量或装窑方式不当,窑内温差大,使烤花温度不均匀;
彩烤时间过长或过短;
彩烤温度过高或过低,造成显色不均匀。
⑥烤花窑使用的燃料含硫成分过多;
颜料发生变化。
二十一、画面缺陷画面