乘用车离合器设计Word文档下载推荐.docx
《乘用车离合器设计Word文档下载推荐.docx》由会员分享,可在线阅读,更多相关《乘用车离合器设计Word文档下载推荐.docx(25页珍藏版)》请在冰豆网上搜索。
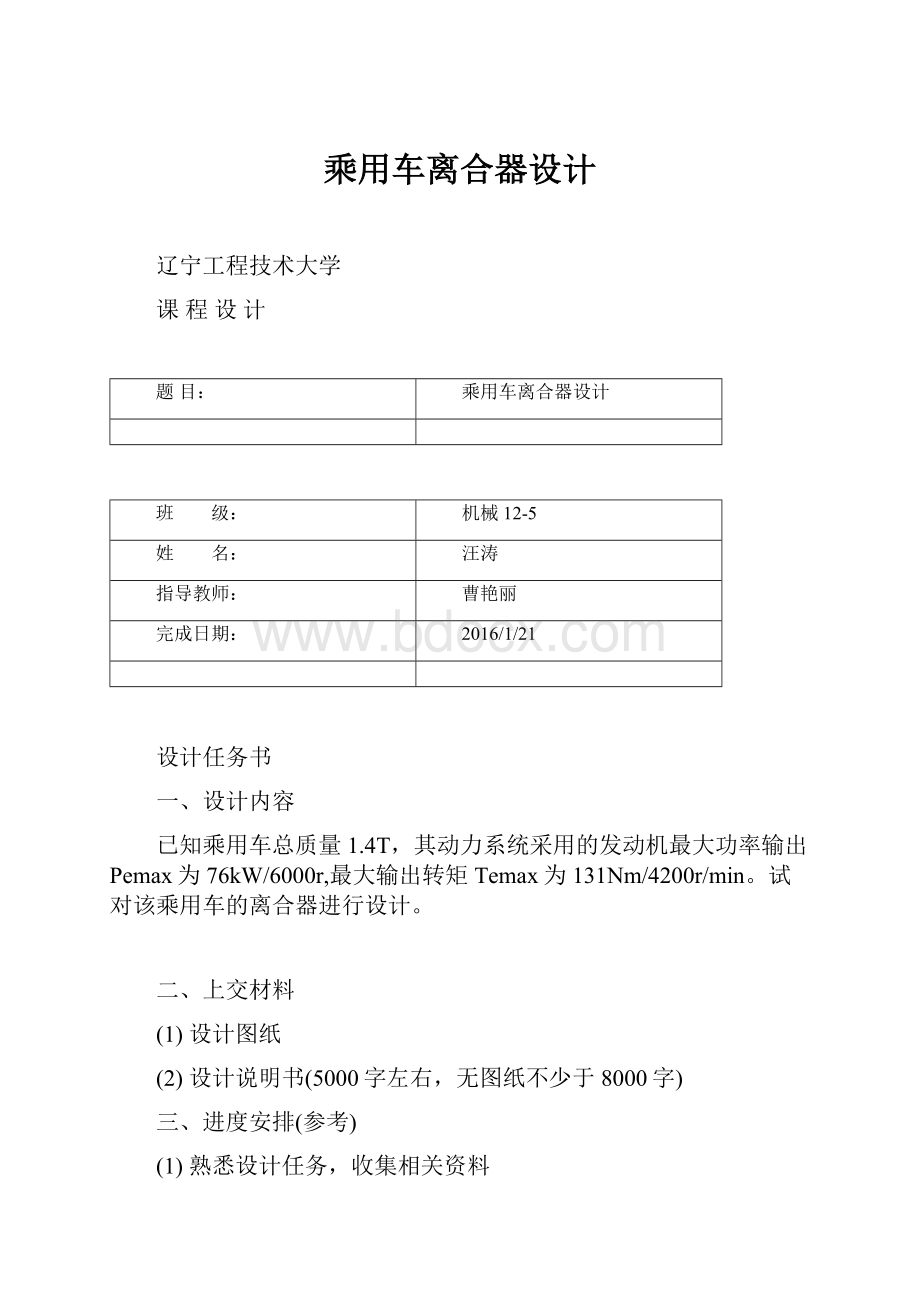
选用拉式膜片弹簧离合器。
(1)膜片弹簧离合器与其他形式的离合器相比,有如下优点:
●膜片弹簧具有较理想的非线性弹性特性,弹簧压力在摩擦片的允许磨损范围内基本保持不变,因而离合器工作中能保持传递的转矩大致不变;
相对圆柱螺旋弹簧,其压力大大下降,离合器分离时,弹簧压力有所下降,从而降低了踏板力。
对于圆柱螺旋弹簧,其压力则大大增加。
●膜片弹簧兼起压紧弹簧和分离杠杆的作用,结构简单、紧凑,轴向尺寸小,零件数目少,质量小。
●高速旋转时,弹簧压紧力降低少,性能较稳定;
而圆柱螺栓弹簧压紧力则明显下降。
●膜片弹簧以整个圆周与压盘接触,使压力分布均匀,摩擦片接触良好,磨损均匀。
●易于实现良好的通风散热,使用寿命长。
●膜片弹簧中心与离合器中心线重合,平衡性好。
(2)拉式膜片弹簧离合器是目前汽车离合器中比较流行的新结构.尽管它有结构复杂和拆装较困难的缺点,但因其优越的综合性能,目前在各种汽车中的应用日益广泛。
1.3膜片弹簧的支撑形式
拉式膜片弹簧的支承结构形式主要有单支承环形式和无支承环形式。
本次设计采用的是单支承环形式,将膜片弹簧大端支承在离合器盖中的支承环上。
膜片弹簧离合总成由膜片弹簧、离合器盖、压盘、传动片和分离轴承总成等部分组成。
1.4扭转减振器
它能降低发动机曲轴与传动系接合部分的扭转刚度,调谐传动系扭振固有频率,增加传动系扭振阻尼,抑制扭转共振响应振幅,并衰减因冲击而产生的瞬态扭振,控制动力传动系总成怠速时离合器与变速器的扭振与噪声,缓和非稳定工况下传动系的扭转冲击载荷和改善离合器的接合平顺性。
故要有扭转减振器。
1.5膜片弹簧离合器的工作原理
由下图可知,离合器盖与发动机飞轮用螺栓紧固在一起,当膜片弹簧被预加压紧,离合器处于接合位置时,由于膜片弹簧大端对压盘的压紧力,使得压盘与从动摩擦片之间产生摩擦力。
当离合器盖总成随飞轮转动时(构成离合器主动部分),就通过摩擦片上的摩擦转矩带动从动盘总成和变速器一起转动以传递发动机动力。
要分离离合器时,将离合器踏板踏下,通过操纵机构,使分离轴承总成前移推动膜片弹簧分离,使膜片弹簧呈反锥形变形,压盘在传动片的弹力作用下离开摩擦片,切断了发动机动力的传递。
2离合器基本参数的确定
摩擦离合器是靠存在于主、从动部分摩擦表面间的摩擦力矩来传递发动机转矩的。
离合器的静摩擦力矩为:
(2-1)
式中,f为摩擦面间的静摩擦因数,计算式一般取0.25-0.30;
F为压盘施加在摩擦面上的工作压力;
为摩擦片的平均摩擦半径;
Z为摩擦面数,单片离合器的Z=2,双片离合器的Z=4。
为了保证离合器在任何工况下都能可靠地传递发动机的最大转矩,设计时应大于发动机最大转矩,即
(2-2)
式中,为发动机最大转矩;
β为离合器的后备系数,定义为离合器所能传递的最大静摩擦力矩与发动机最大转矩之比,β必须大于1
2.1后备系数β
后备系数β是离合器设计中的一个重要参数,它反映了离合器传递发动机最大转矩的可靠程度。
在选择β时,考虑到摩擦片在使用中磨损后仍能可靠地传递发动机最大转矩、防止离合器滑磨时间过长、防止传动系统过载以及操纵轻便等因素。
因此,在选择β时应考虑以下几点:
●为可靠传递发动机最大转矩,β不宜选取太小;
●为减少传动系过载,保证操纵轻便,β又不宜选取太大;
●当发动机后备功率较大、使用条件较好时,β可选取小些;
●当使用条件恶劣,为提高起步能力、减少离合器滑磨,β应选取大些;
●汽车总质量越大,β也应选得越大;
●柴油机工作比较粗暴,转矩较不平稳,选取的β值应比汽油机大些;
●发动机缸数越多,转矩波动越小,β可选取小些;
●膜片弹簧离合器选取的β值可比螺旋弹簧离合器小些;
●双片离合器的β值应大于单片离合器。
各类汽车离合器β的取值范围见表2-1。
表2-1离合器后备系数β的取值范围
车型
后备系数β
乘用车及最大质量小于6t的商用车
1.20-1.75
最大总质量为6-14t的商用车
1.50-2.25
挂车
1.80-4.00
本次课程设计的对象为乘用车,故本次课程设计的后备系数β范围为1.20-1.75,
初取β=1.5
2.2单位压力P0
单位压力P0决定了摩擦表面的耐磨性,对离合器工作性能和使用寿命有很大影响,选取时应考虑离合器的工作条件、发动机后备功率的大小、摩擦片尺寸、材料及其质量和后备系数等因素。
离合器使用频繁,发动机后备系数较小时,P0应取小些;
当摩擦片外径较大时,为了降低摩擦片外缘处的热负荷,P0应取小些;
后备系数较大时,可适当增大P0
当摩擦片采用不用的材料时,P0取值范围见表2-2。
表2-2摩擦片单位压力P0的取值范围
摩擦片材料
单位压力P0/MPa
石棉基材料
模压
0.15-0.25
编织
0.25-0.35
粉末冶金材料
铜基
0.35-0.50
铁基
金属陶瓷材料
0.70-1.50
本次设计摩擦片为石棉基材料,P0选择:
0.15≤P0≤0.35MPa
2.3摩擦片外径D、内径d和厚度b
摩擦片外径是离合器的重要参数,它对离合器的轮廓尺寸、质量和使用寿命有决定性的影响。
当离合器结构形式及摩擦片材料已选定,发动机最大转矩已知,适当选取后备系数β和单位压力P0,可估算出摩擦片的外径,即:
(2-3)
摩擦片外径D(mm)也可根据发动机最大转矩(N﹒m)按如下经验公式选用:
(2-4)
式中,为直径系数,取值范围见表3-3。
表2-3直径系数的取值范围
直径系数KD
乘用车
14.6
最大总质量为1.8-14.0t的商用车
16.0-18.5(单片离合器)
13.5-15.0(双片离合器)
最大总质量大于14.0t的商用车
22.5-24.0
本次设计的对象是乘用车,故KD=14.6,
该车型的发动机的最大扭矩:
131Nm/4200rpm。
故根据公式(2-4)可算出摩擦片外径D
(2-5)
按初选
以后,还需尽量注意摩擦片尺寸的系列化和标准化,应符合尺寸系列标准
《汽车用离合器面片》表2-4为我国摩擦片尺寸的标准。
表2-4离合器摩擦片尺寸系列和参数
参数
数值
外径
D/mm
180
200
225
250
280
300
325
350
内径
125
140
150
155
165
175
190
195
厚度
3.5
4
0.694
0.700
0.667
0.620
0.589
0.583
0.585
0.557
0.657
0.703
0.762
0.796
0.802
0.800
0.827
单位面积
132
160
221
302
402
466
546
678
故,选取摩擦片的尺寸为
D=200mm,d=140mm,厚度b=3.5mm,c=0.7,单位面积=160。
摩擦片尺寸应符合尺寸系列标准GB5764--86《汽车用离合器面盖片》,所选的D应使摩擦片最大圆周速度不超过65~70m/s,以免摩擦片发生飞离。
(2-6)
=π*6000*200*/60=62.83m/s<
70m/s满足要求。
为了保证扭转减振器的安装,摩擦片内径d必须大于减振器弹簧位置直径约50mm.
摩擦片的内、外径比c应在0.53-0.70范围内,
即:
0.53≤0.70≤0.70由此可见,满足要求。
2.4摩擦因数f、摩擦面数Z和离合器间隙△t
摩擦片的摩擦因数f取决于摩擦片所用的材料及其工作温度、单位压力和滑磨速度等因素。
各种摩擦材料的摩擦因数f的取值范围见表2-5
表2-5摩擦材料的摩擦因数f的取值范围
摩擦材料
摩擦因数f
0.20-0.25
0.4
取f=0.25。
在前面的设计分析中已经陈述了本次设计选用的是单片拉式膜片弹簧离合器,故Z=2。
离合器间隙△t是指离合器处于正常接合状态、分离套筒被回位弹簧拉到后极限位置时,为保证摩擦片正常磨损过程中离合器仍能完成接合,在分离轴承和分离杠杆内端之间留有的间隙。
取△t=3mm。
2.5离合器摩擦力据Tc和单位压力P0的计算
因此,静摩擦力矩Tc:
(2-7)
摩擦片的平均摩擦半径:
(2-8)
施加在摩擦面上的工作压力为
(2-9)
单位压力P0的计算:
满足0.15≤P0≤0.35MPa
3离合器零件的结构选型及设计
3.1从动盘总成设计
3.1.1从动盘总成的结构型式的选择
从动盘总成主要由摩擦片、从动片、减振器和从动盘毂等组成。
从动盘对离合器工作性能影响很大,应满足如下设计要求:
●转动惯量应尽量小,以减小变速器换挡时轮齿间的冲击。
●应具有轴向弹性,使离合器接合平顺,便于起步,而且使摩擦面压力均匀,减小磨损。
●应装扭转减振器,以避免传动系共振,并缓和冲击。
摩擦面片采用有机材料。
选用带扭转减振器的从动盘,从动片通常用1.3~2.0mm厚的钢板冲压而成。
将其外缘的盘形部分磨薄至0.65~1.0mm,以减小其转动惯量。
整体式弹性从动片一般用高碳钢(如50)或65Mn钢板,热处理硬度38~48HRC。
3.1.2从动片结构型式的选择
从动片设计时,要尽量减轻其重量,并应使其质量的分布尽可能地靠近旋转中心,以获得最小的转动惯量。
为了使离合器结合平顺,保证汽车平稳起步,单片离合器的从动片一般都做成具有轴向结构,这样的从动片有3种结构型式:
1、整体式弹性从动片;
2、分开式弹性从动片;
3、组合式弹性从动片。
选择整体式弹性从动片,它能满足达到轴向弹性的要求,生产率高。
3.1.3从动盘毂的设计
从动盘毂是离合器中承受载荷最大的零件,它装在变速器输入轴前端的花键上,一般采用齿侧定心的矩形花键,花键轴与孔采用动配合。
从动盘毂轴向长度不宜过小,以免在花键轴上滑动时产生偏斜而使分离不彻底,一般取1.0~1.4倍的花键轴直径。
本设计取1.4倍的花键轴直径。
从动盘毂一般采用锻钢(如45,40Cr等),表面和心部硬度一般在26~32HRC。
为提高花键内孔表面硬度和耐磨性,可采用镀铬工艺,对减振弹簧窗口及与从动片配合处应进行高频处理。
减振弹簧常采用60Si2MnA、50CrVA、65Mn等弹簧钢丝。
花键的结构尺寸可根据从动盘外径和发动机转矩按国标GB1144—1974表3-1选取。
表3-1花键轴规格表
从动盘外径D(mm)
发动机最大扭(NM)
花键齿数
n
花键
(mm)
齿厚(mm)
有效齿长(mm)
150
10
32
26
30
35
28
40
310
5
50
380
480
55
600
60
410
720
45
36
65
430
800
根据发动机最大转矩为Temax=131Nm,选取结果见表3-2:
表3-2所选从动盘毂花键参数
从动盘外径D/mm
花键外径D′/mm
花键内径d′/mm
齿厚b/mm
有效齿长
/mm
挤压应力
11.3
花键尺寸选定后应进行强度校核。
由于花键损坏的主要形式是由于表面受挤压过大而破坏,所以花键要进行挤压应力计算。
挤压应力计算公式:
(3-1)
式中,
,
—花键的内外径
;
Z—从动盘毂的数目,Z=1;
—发动机最大转矩
—花键齿数;
—花键齿工作高度
(3-2);
—花键有效长度
。
式中,P为花键的齿侧面压力(
),由下式确定:
(3-3)
花键的齿侧面压力P:
(3-4)
故根据式(3-1)挤压应力
:
(3-5)
满足要求。
3.2离合器盖总成设计
3.2.1离合器盖设计
为了减轻重量和增加刚度,轿车的离合器盖常用厚度约为3~5mm的低碳钢板(如08钢板)冲压成比较复杂的形状。
在设计中要特别注意的是刚度、对中、通风散热等问题。
离合器盖的刚度不够,会产生较大变形,这不仅会影响操纵系统的传动效率,还可能导致分离不彻底、引起摩擦片早期磨损,甚至使变速器换挡困难。
离合器盖内装有压盘、分离杠杆、压紧弹簧等,因此,应与飞轮保持良好的对中,以免影响总成的平衡和正常的工作。
对中方式采用定位销或定位螺栓,也可采用止口对中。
离合器盖的膜片弹簧支承处应具有高的尺寸精度。
为了加强离合器的通风散热和清除摩擦片的磨损粉末,防止摩擦表面温度过高,在保证刚度的前提下,可在离合器盖上设置循环气流的入口和出口,甚至可将盖设计成带有鼓风叶片的结构。
本次设计离合器盖要求离合器盖内径大于离合器摩擦片外径,能将其他离合器上的部件包括在其中即可。
3.2.2压盘设计
对压盘设计的要求:
压盘应具有较大的质量,以增大热容量,减小温升,防止其产生裂纹和破碎,有时可设置各种形状的散热筋或鼓风筋,以帮助散热通风。
中间压盘可铸出通风槽,也可采用传热系数较大的铝合金压盘。
压盘应具有较大的刚度,使压紧力在摩擦面上的压力分布均匀并减小受热后的翘曲变形,以免影响摩擦片的均匀压紧及离合器的彻底分离,厚度约为15~25mm。
与飞轮应保持良好的对中,并要进行静平衡,压盘单件的平衡精度应不低于15~20g.cm。
压盘高度(从承压点到摩擦面的距离)公差要小。
初步确定压盘厚度为15mm,外径225mm,内径120mm。
材料为灰铸铁HT20铸成,密度为
C=481.4J/(kg.℃)
压盘的厚度初步确定后,应根据下式来校核离合器一次接合的温升
(3-6)
式中,
—压盘温升(℃),不超过8~10℃;
c—压盘的比热容,铸铁的比热容为
℃);
—传到压盘的热量所占的比例,对单片离合器,γ=0.5;
L—消磨功,对单片离合器一般为8000J
可算得压盘质量m=3.816kg。
根据(3-6)得温升
(3-7)
3.3离合器分离装置设计
3.3.1分离轴承和分离套筒
分离轴承在工作中主要承受轴向分离力,同时还承受在告诉旋转时离心力作用下的径向力。
以前主要采用推力球轴承或向心球轴承,但其润滑条件差,磨损严重、噪声大、可靠性差、使用寿命低。
目前国外已采用角接触推力球轴承,采用全密封结构和高温锂基润滑脂,其端部形状与分离指舌尖部形状相配合,舌尖部为平时采用球形端面,舌尖部为弧形面时采用平端面或凹弧形端面。
本设计采用角接触推力球轴承。
本设计使用的是适合拉式离合器的自动调心式分离轴承装置。
轴承外圈与分离套筒外凸缘和外罩之间以及内圈与分离套筒内凸缘之间都留有径向间隙,这些间隙保证了分离轴承相对于分离套筒可径向移动1mm左右。
在外圈轴承不工作时不会发生晃动。
当膜片弹簧旋转轴线与轴承不同心时,分离轴承便会自动径向浮动到与其同心的位置,以保证分离轴承能均匀压紧各分离指舌尖部。
这样可以减小振动和噪声,减小分离指与分离轴承断面的磨损,是轴承不会出现过热而造成润滑脂流失分解。
延长轴承寿命。
另外,分离轴承由传统的外圈转动改为内圈转动、外圈固定不转,由内圈来推动分离指的结构,适当地增大了膜片弹簧的杠杆比,且由于内圈转动,在离心力作用下,润滑脂在内、外圈间的循环得到改善,提高了轴承使用寿命。
这种拉式分离轴承室将膜片弹簧分离指舌尖直接压紧在碟形弹簧与档环之间,再用弹性锁环卡紧,结构较简单。
3.4膜片弹簧的设计
3.4.1膜片弹簧基本参数的选择
(1)比值H/h和h的选择
比值H/h对膜片弹簧的弹性特性影响极大。
当H/h<
A时,为增函数;
当H/h=M时,有一极值,该极值点恰为拐点;
当H/h>
N时,有一极大值和一极小值;
当H/h=2时,的极小值落在横坐标上。
为保证离合器压紧力变化不打和操纵轻便,汽车离合器用膜片弹簧的H/h一般为1.5~2.0,板厚h为2~4mm。
初取h=3mm,H/h=1.5,H=4.5m
(2)R/r比值和R、r的选择
研究表明,R/r越大,弹簧材料利用率越低,弹簧越硬,弹性特性曲线受直径误差的影响越大,且应力越高。
根据结构布置和压紧力的要求,R/r一般为1.20~1.35。
为使摩擦片上的压力分布较均匀,推式膜片弹簧的R值宜取为大于或等于摩擦片的平均半径=85mm.
则可初取r=87.5mm,R=105mm。
(3)α的选择
膜片弹簧自由状态下圆锥底角α与内截高度H关系密切,一般在9°
~15°
范围内。
可算得α=14.42°
满足要求。
(4)膜片弹簧工作点位置的选择
膜片弹簧工作点位置如图5-1所示,该曲线的拐点H对应着膜片弹簧的压平位置,而且。
新离合器在接合状态时,膜片弹簧工作点B一般取在凸点M和拐点H之间,且靠近或在H点处,一般,以保证摩擦片在最大磨损限度范围内的压紧力从到变化不打。
当分离时,膜片弹簧工作点从B变到C。
为最大限度的减小踏板力,C点应尽量靠近N点。
图3-1膜片弹簧工作点位置
(5)分离指数目n的选择
分离指数目n常取为18,大尺寸膜片弹簧可取24,小膜片弹簧可取12。
本次设计取n=16。
(6)膜片弹簧小端内径及分离轴承作用半径的确定
由离合器的结构决定,其最小值应大于变速器第一轴花键的外径,应大于。
取R内=28mm,R轴=32mm
(7)切槽宽度B、及半径r`的确定
切槽宽度范围3.2~3.5mm,半径范围9~10mm,取值应满足r-。
本次设计取切槽B=3.4mm,r`=9mm,满足r-。
(8)压盘加载点半径R1和支承环加载点半径R2的确定
两者的取值将影响膜片弹簧的刚度。
应略大于r且尽量接近r,应略小于R且尽量接近R。
本次设计,取R1=87.5mm,R2=100mm。
3.4.2膜片弹簧基本参数约束条件的检验
(1)弹簧各部分有关尺寸的比值应符合一定的范围:
(3-8)
R/r=1.2;
2R/h=70;
R/ro=3.75满足条件。
(2)为使摩擦片上的压紧力分布比较均匀,推式膜片弹簧的压盘加载点半径R1应位于摩擦片的平均半径与外半径之间。
即
(3-9)
符合要求。
(3)根据弹簧结构布置要求,
与
之差应在一定范围内,即
(3-10)
R-R1=5;
r1-r=0;
rf-ro=4符合要求。
(4)膜片弹簧的分离指起分离杠杆的作用,因此其杠杆比应在一定范围内先取,
(3-11)
3.4.3膜片弹簧材料及制造工艺
国内膜片弹簧一般采用60Si2MnA或50CrVA等优质高精度钢板材料。
为了保证其硬度、几何形状、金相组织、载荷特性和表面质量等要求,需进行一系列处理。
为了提高膜片弹簧的承载能力,要对膜片弹簧进行强压处理,即沿其分离状态的工作方向,超过彻底分离点后继续施加过量的位移,使其分离3~8次,以产生一定的塑性变形,从而使膜片弹簧的表面产生与其使用状态反向的残余应力而达到强化的目的。
一般来说,经强压处理后,在同样的工作条件下,可提高膜片弹簧的疲劳寿命5%~30%。
另外,对膜片弹簧的凹面或双面进行喷丸处理,即以高速弹丸流喷到膜片弹簧表面,使其表层产生塑性变形,从而形成一定厚度的表面强化层,起到冷作硬化的作用,同样也可提高承载能力和疲劳寿命。
为了提高分离指的耐磨性,可对其端部进行高频淬火。
在膜片弹簧与压盘接触圆形处,为了防止由于拉应力的作用而产生裂纹,可对该处进行挤压处理,以消除应力源。
膜片弹簧表面不得有毛刺、裂纹、划痕、锈蚀等缺陷。
碟簧部分的硬度一般为45~50HRC,分离指端硬度为55~62HRC,在同一片上同一范围内的硬度差不大于3个单位。
碟簧部分应为均匀的回火屈氏体和少量的索氏体。
单面脱碳层的深度一般不得超过厚度的3%。
膜片弹簧的内、外半径公差一般为H11和h11,厚度公差为±
0.025mm,初始底锥角公差为±
10′。
膜片弹簧上下表面的表面粗糙度为1.6μm,底面的平面度一般要求小于0.1mm。
膜片弹簧处于接合状态时,其分离指端的相互高度差一般都要求小于0.8~1.0mm
3.5扭转减振器
3.5.1扭转减振器的功用
●降低发动机曲轴与传动系接合部分的扭转刚度,调谐传动系扭振固有频率;
●增加传动系扭振阻尼,抑制扭转共振影响振幅,并衰减因冲击而产生的瞬间扭振;
●控制动力传动系总成怠速时离合器与变速器轴系的扭振,消减变速器怠速噪声和主减速器与变速器的扭振和噪声;
●缓和非稳定工况下传动系的扭转冲击载荷,改善离合器的接合平顺性。
3.5.2减振器的结构设计
(1)极限转矩
极限转矩是指减