模具毕业设计82线圈架注塑模具设计Word文件下载.docx
《模具毕业设计82线圈架注塑模具设计Word文件下载.docx》由会员分享,可在线阅读,更多相关《模具毕业设计82线圈架注塑模具设计Word文件下载.docx(31页珍藏版)》请在冰豆网上搜索。
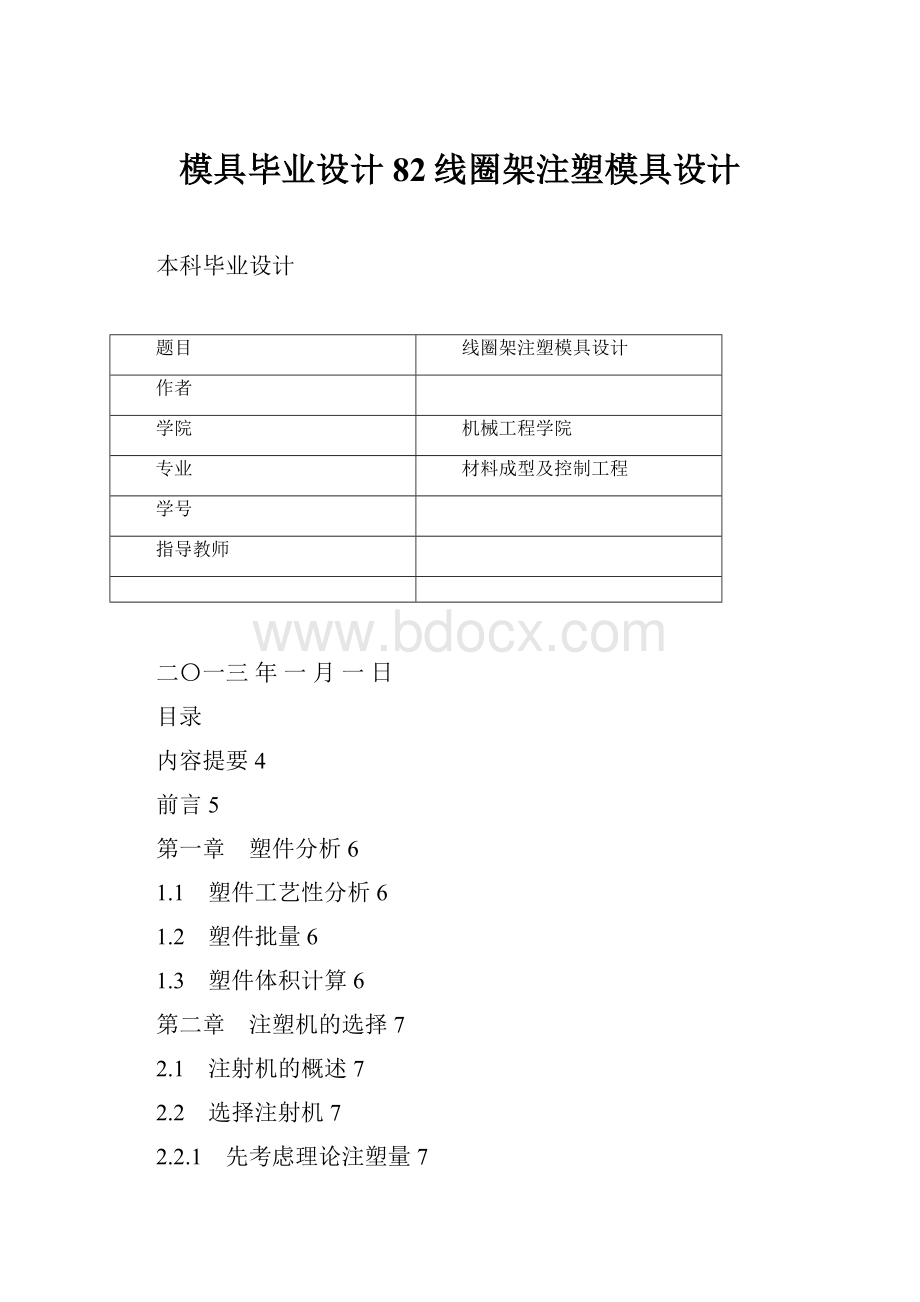
4.4 塑件脱模机构设计18
4.5 侧向分型与抽芯机构设计19
4.5.1 抽拔距的计算19
4.5.2 斜导柱的尺寸与安装形式19
4.5.4 锁紧楔形式21
4.6 模具温度调节系统22
第五章 注塑机参数的校核23
5.1 最大注塑量的校核23
5.2 注塑压力的校核23
5.3 锁模力的校核23
5.4 模具与注塑机安装部分相关尺寸校核24
5.4.1 模板尺寸和拉杆间距是否相适合24
5.4.2 模具闭合高度的校核24
5.5 开模行程与顶装置的校核24
符号说明25
参考文献27
致谢28
内容提要
本设计主要讲述了以聚乙烯(PE)为材料的线圈架注塑模具的设计过程。
此模具在设计时,充分考虑了生产批量、以提高生产效率、降低生产成本为主要宗旨。
本产品为电动机绕线圈,形状规则,内空心,侧有凹槽,根据计算出的体积与质量选择SZ-100-60型号的注塑机注塑。
由于塑件内空心,侧有凹槽要求模具必需采用斜导柱侧抽芯机构分型。
经过比较,采用斜导柱在定模,斜滑块在动模的结构。
整体斜楔定位,斜导柱侧抽芯分型,推板推出工件的工作原理。
设计中对主要零件一一的进行了设计。
文中插入了非标准零件图,以及模具结构图。
前言
随着塑料工业的发展,塑料制品在工业及日常生活中使用越来越大,因此对塑料模具设计人员的需求也在逐年的增加。
同时对设计的人员的先进的设计思维、掌握较多先加工技术以及加工工艺也是非常必要的。
作为学习模具专业的学生,我们有必须以提高自己的基础理论为前提,为促进我国模具行业的发展而努力,为促进我国工业提高标准化水平而做出自己的贡献。
模具毕业设计是模具专业最为重要的环节之一,同时它也是最后的一个关键教学环节。
它是由学生过渡到生产的一步,由学校走向工厂的桥梁。
是我们第一次系统地把所学理论应用在实际生产。
通过此次的毕业设计制造的各个环节有了更加深入明确的了解从而培养和提高设计的能力。
毕业设计的目的有两个,第一个目的是让我们掌握模具设计的基本技能,如绘图,计算,查阅设计资料和手册。
熟悉国标和各种标准的能力,能够熟练运用CAD,Pro/E。
进行绘图。
第二个目的是了解和掌握模具设计与制造的工艺,从而独立的设计一般的塑料模具,为走出学校走向社会打下基础。
我设计的是一副斜导柱抽芯机构的模具。
采用斜导柱在定模,哈夫块(斜滑块)在动模的结构。
但因本人经验不足,又加上时间仓促。
因此难避免存在一些错误,敬请各位老师批评和指正,以便取得更大的进步。
第一章 塑件分析
1.1 塑件工艺性分析
本产品为绕线圈,在工程中,我们都知道要求选择有良好绝缘性能的材料,具有此种性能的也较多,但此塑件选用聚乙烯(PE)这种材料还具有耐光性、耐化学腐蚀性、耐磨性。
以下图1.1为塑件的实物图及实际测量塑件的尺寸
图1.1
1.2 塑件批量
本产品在工业生产中广泛应用,因为作为常期生产的塑件,可以说其批量值是比较大的,属于大批量生产。
故设计模具要有较高的效率,浇注系统要能自动脱模。
1.3 塑件体积计算
塑件质量的计算是为了选择合理的注塑机,提高设备利用率,确定模具的型腔数目。
因此;
塑件质量的计算则为;
(由UG设计绘图得)
式中ρ=0.92g/cm3(查塑料模具设计手册)
第二章 注塑机的选择
2.1 注射机的概述
注射机的类型和规格很多,分类方法各异,按结构型式可分为立式、卧式、直角式三类,国产卧式注射机已经标准化和系列化。
这三类不同结构形式的注射成型机各特点如下:
立式注射机的注射柱塞(或螺杆)垂直装设,锁模装置推动模板也沿垂直方向移动,这种注射成型机主要优点是占地面积小,安装或拆卸小型模具很方便,容易在动模上(下模)。
安放嵌件,嵌件不易倾斜或坠落。
其缺点是制品自模具中顶出以后不能靠重力下落。
需人工取出,有碍于全自动操作,但附加机械手取产品后,也可以实现全自动操作,此类注射机注射量一般均在60克以下。
卧式注射机是目前使用最广、产量最大的注射成型机,其注射柱塞或螺杆与合模运动均沿水平方向装设,并且多数在一条直线上(或相互平行)。
优点是机体较低,容易操纵和加料,制件顶出模具后可自动坠落,故能实现全自动操作,机床重心较低安装稳妥,一般大中型注射机均采用这种形式。
缺点是模具安装比较麻烦嵌件放入模具有倾斜或落下的可能,机床占地面积较大。
直角式注射机的柱塞或螺杆与合模运动方向相互垂直,主要优点是结构简单,便于自制适于单件生产者,中心部位不允许留有浇口痕迹的平面制件,同时常利用开模时丝杠的转动来拖动螺纹型芯或型环旋转,以便脱下塑件。
缺点是机械传动无准确可靠的注射和保压压力及锁模力,模具受冲击振动较大。
2.2 选择注射机
2.2.1 先考虑理论注塑量
理论注塑量是指注塑机在对空注塑的条件下,注塑螺杆(或柱塞)作一次最大注塑行程时,注塑装置所能达到的最大注塑m3)的最大克数(g)为标准,称之为理论注塑质量;
另一种规定以注塑塑料的最大容积(cm3)为标准,称量。
理论注塑量一般有两种表示方法:
一种规定以注塑聚乙烯(PE)(密度约为0.92g/c之为理论注塑容量。
2.2.2 其次要考虑实际注塑量
根据实际情况,注塑机的实际注塑量是理论注塑量的80%左右。
即有
MS=aM1(2.1)
Vs=aV1 (2.2)
式中:
M1——理论注塑质量,g;
V1——理论注塑容量,cm3;
MS——实际注塑质量,g;
VS——实际注塑容量,g;
a——注塑系数,一般取值为0.8。
在注塑生产中,注塑机在每一个成型周期内向模内注入熔融塑料的容积或质量称为塑件的注塑量M,塑件的注塑量M必须小于或等于注塑机的实际注塑量。
当实际注塑量以实际注塑容量VS表示时,如式(2.3):
MS,=
,VS(2.3)
式中:
MS,——注塑密度为
时塑料的实际注塑质量,g;
,——在塑化温度和压力下熔融塑料密度,g/cm3。
,=C
(2.4)
——注塑塑料在常温下的密度,g/cm3;
C——塑化温度和压力下塑料密度变化的校正系数;
对结晶型塑料,C=0.85,对非结晶型塑料C=0.93。
当实际注塑量以实际注塑质量MS表示时,有式(2.5):
MS,=MS(
/
ps)(2.5)
ps——聚乙烯(PE)在常温下的密度(约为0.92g/cm3)。
所以,塑件注塑量M应满足式(2.6):
MS,≥M=nMZ=+MJ(2.6)
n——型腔个数;
MZ——每个塑件的质量,g;
MJ——浇注系统及飞边的质量,g
根据塑料制品的体积或质量查《塑料成型工艺及模具设计》教材 附录G 或查相关手册选定注塑机型号为;
XS-Z-30
注塑机的参数如下;
注塑机的最大注塑量…………………………………………30cm3
锁模力…………………………………………………………250KN
注塑压力………………………………………………………119Mpa
最小模厚………………………………………………………60mm
模板行程………………………………………………………130mm
注塑机定位孔直径……………………………………………100mm
喷嘴前端孔径…………………………………………………ø
4mm
喷嘴球面半径…………………………………………………SR12
第3章 模具设计的有关计算
3.1 成型零件工作尺寸的计算
根据塑件图可知,线圈高骨架外形尺寸无精度要求,只是塑件本身就要求达到IT8级的精度,它属于一般精度要求。
故主要计算出相对于固定型芯和哈夫块组合而成的型腔尺寸,其余型芯与型腔的尺寸则直接按产品尺寸。
3.1.1 型芯尺寸的计算
型芯的径向尺寸的计算:
按平均收缩率计算型芯的径向尺寸:
经查《塑料模具设计手册》可知PE的平均收缩率为2.5%。
根据塑件精度等级(IT5)查得《塑料模具设计》中“塑件公差数值表”,其径向基本尺寸为6mm,那么它的浮动尺寸为
根据公式
(3.1)
=[6+6×
2.5%+34×
0.05]-δ
=
式中LM—零件制造径向尺寸;
LS—径向的基本尺寸;
δ—对于小型零件等于Δ/3(Δ为制件允许的公差值);
型芯尺寸的高度计算,同样也是按收缩率来计算值:
3.1.2 型腔尺寸的计算
因为以面的型芯尺寸的计算时都是以型腔为准的,因此有一部分的尺寸(15mm的尺寸)我们只考虑了型腔各尺寸的制造加工尺寸。
(1)型腔径向尺寸的计算为:
同上以是按平均收缩率来计算其尺寸,已知在给定条件下的平均收缩率SCP,制件型腔的名义尺寸为LM(最小尺寸),公差值为δ(正偏差),则型腔的平均尺寸为:
LM+δ2。
考虑到收缩量和磨损值,
故也根据公式LM=[LS+LS·
SCP-34Δ]+δ(3.2)
可得:
基本尺寸为15mm时,可得如下值;
LM=[15+15×
2.5%-34×
0.08]+Δ/3
LM=
那么LM′=
基本尺寸为3mm时,可得如下值;
LM=[3+3×
2.5%-34×
0.05]+Δ/3
(2)型腔深度尺寸的计算;
也是按平均收缩率计算型腔的深度尺寸,在型腔深度尺寸的计算中,规定制件高度的名义尺寸为HS为最大尺寸,公差以负偏差表示。
型腔深度名义尺寸HM为最小尺寸,公差以正偏差表示。
型腔的底部或型芯的端面与分型面平行,在脱模过程中磨损很小磨损量就不考虑,据HM=[HS+HS·
SCP-23Δ]+δ(3.3)
深度尺寸为13mm时:
HM=[13+13×
2.5%-23×
0.08]
HM=
3.2 成型腔壁厚的计算
成型腔应具有足够的壁厚以承受塑料熔体的高压,如壁厚不够可表现为刚度不足,即产生过大的弹性变形值;
也可表现为强度不够,即塑腔发生塑隆变形甚至破裂。
模具的型腔在注射时,当型腔全部充满时,内压力达到极限值,然后随着塑料的冷却和浇口的封闭,压力逐渐减小,在开模时接近常压。
型腔壁厚计算以最大压力为准。
理论分析和实践证明,对于大尺寸的型腔,刚度不足是主要原因,应按刚度来计算;
而小尺寸和型腔在发生的弹性变形前,其内应力就超过了许用应力,因此按强度来计算。
而此次设计的塑件尺寸不是很大,因此,我们就按强度来计算型腔壁厚。
模具结构中,都采用的是整体式且是矩形型腔,它的按强度来计算侧壁的厚度比较的复杂。
而在《模具设计手册》里可以查得一些经验值,如图3.1所示:
图3.1
第4章 模具结构的设计
4.1 浇注系统设计
4.1.1 浇口套的选用
浇口套属于标准件,在选够浇口套时应注意:
浇口套进料口直径和球面坑半径。
因此,所选浇口套如图4.1所示:
图4.1
4.1.2 冷料井的设计
根据实际,采用底部带有顶杆的冷料井,推杆装于推杆固定板上。
如图4.2所示:
图4.2
4.1.3 分流道的设计
(1)分流道截面形状
分流道截面形状可以是圆形、半圆形、矩形、梯形和U形等,圆形和正方形截面流道的比表面积最小(流道表面积与体积之比称为比表面积),塑料熔体的温度下降少,阻力亦小,流道的效率最高。
但加工较困难,而且正方形截面不易脱模,所以在实际生产中较常用的截面形状为梯形、半圆形、U形及圆形。
(2)分流道的尺寸
分流道尺寸由塑料品种、塑件的大小及长度确定。
对于重量在200g以下,壁厚在3mm以下的塑件可用下面经验公式计算分流道的直径,如式(4.1)。
(4.1)
D---分流道的直径,mm;
W---塑件的质量,g;
L---分流道的长度,mm.
对于流动性极好的塑料(如PE,PA等),当分流道很短时,其直径可小到2mm左右;
对于流动性差的塑料(如PC,HPVC及PMMA等),分流道直径可以大到13mm;
大多数塑料所用分流道的直径为6mm~10mm。
4.3.3 分流道的布置
在多型腔模具中分流道的布置中有平衡式和非平衡式两类。
平衡史布置是指分流道到各型腔浇口的长度、断面形状、尺寸都相同的布置形式。
它要求各对应部位的尺寸相等。
这种布置可实现均衡送料和同时充满型腔的目的,使成型的塑件力学性能基本一致,但是,这种形式的布置使分流道比较长。
非平衡式布置的指分流道到各型腔浇口长度不相等的布置。
这种布置使塑料进入各型腔有先有后,因此不利于均衡送料,但对于型腔数量多发模具,为不使流道过长,也常采用。
为了达到同时充满型腔的目的,各浇口的断面尺寸要制作得不同,在试模4.3.4.分流道设计要点
(1)、在保证足够的注塑压力使塑料熔体顺利充满型腔的前提下,分流道截面面积与长度尽量取小值,分流道转折处应圆弧过度。
(2)、分流道较常时,在分流道的末端应开设冷料井。
(3)、分流道的位置可单独开设在定模板上或动模板上,也可以同时开设在动、定模板上,合模后形成分流道截面形状。
(4)、分流道与浇口连接处应加工成斜面,并用圆弧过度。
在选择浇口套时应注意:
①、浇口套进料口直径如式(4.2)
D=d+(0.5~1)mm(4.2)
d---注塑机喷嘴口直径。
②、球面凹坑半径R
R=r+(0.5~1)mm;
(4.3)
r---注塑机喷嘴球头半径。
③、浇口套与定模板的配合
在单腔模中,常不设分流道,而在多腔模中,一般都设置有分流道,塑料沿分流道流动时,要求通过它尽快地充满型腔,流动中温度降低尽可能小,阻力尽可能低。
同时,应能将塑料熔体均衡地分配到各个型腔。
从前两点出发,分流道应短而粗。
但为了减少浇注系统的加回料量,分流道亦不能过粗。
过粗的分流道冷却缓慢,还倒增长模塑的周期。
而该设计中使用了梯形断面形状的分流道。
如图4.3所示;
图4.3
因为梯形断面的这种分流道易于机械加工,且热量损失和阻力损失均不大,故它也是一种常用的形式.其断面尺寸比例为;
H=2/3W,X=3/4W,或将斜边与分模线的垂线呈5°
—10°
的斜角。
4.1.4 浇口设计
浇口又称进料口,是连接分流道与型腔之间的一段细流道(除直浇口外),它是浇注系统的关键部分,其主要作用是:
1、型腔充满后,熔体在浇口处首先凝结,防止其倒流。
2、易于在浇口切除浇注系统的凝料,浇口截面约为分流道截面的0.03~0.09。
浇口长度约为0.5mm~2mm,浇口具体尺寸一般根据经验确定,取其下限值,然后在试限时逐步纠正。
当塑料熔体通过浇口时,剪切速率增高,同时熔体的内摩擦加剧,使料流的温度升高,粘度降低,提高了流动性能,有利用充型。
但浇口尺寸过小会使压力损失增大,凝料加快,补缩困难,甚至形成喷射现象,影响塑料质量。
浇口的形状和尺寸对制品质量影响很大,浇口在多情况下,系整个流道断面尺寸最小的部分(除主流道型的浇口外),一般汇报口的断面积与分流道的断面积之比约为0.03~0.09。
断面形状如图4.3所示,浇口台阶长1~1.5㎜左右.虽然浇口长度比分流道的长度短的多,但因为其断面积甚小,浇口处的阻力与分流道相比,浇口的阻力仍然是主要的,故在加工浇口时,更应注意其尺寸的准确性。
然而,根据塑件的样品图1.1、生产的批量等,采用一模四腔结构。
浇口采用一般矩形形如图4.4所示:
图4.4
4.1.5 浇口位置的选择
(1)浇口的位置的应使填充型腔的流程最短
这样的结构使压力损失最小,易保证料流充满整个型腔。
对于型塑件,要进行流动比的校核。
流动比K由流动通道的长度L与厚度t之比来确定。
如下式(4.4):
K=Σ(Lτ/tτ) (4.4)
Lτ---各段流程的长度,mm;
tτ---各段流程的厚度或直径,mm;
流动比的允许值随塑料熔体的性质、温度压力等的不同而变化。
流动比的计算公式为(7-6/8):
①K=L1/t1+L2+L3/t2(4.5)
②K=L1/t1+L2/t2+L3/t3+2L4/t4+L5/t5(4.6)
(2)浇口位置的选择要避免塑件变形
(2)浇口位置的设置应减少或避免产生熔接痕
熔接痕是充型时前端较冷的料流在型腔中的对接部位,它的存在会降低塑件的强度,所以设置浇口时应考虑料流的方向。
为提高熔接痕处强度,可在熔接处增设溢流槽,使冷料进入逸流槽。
筒形塑件采用环行浇口无熔接痕,而轮辐式浇口会有熔接痕产生。
浇口的位置塑与件质量有直接影响,位置选择不当会使塑件产生变形、熔接痕等缺陷。
图4.4为浇口位置的布局。
4.2 模具结构草案
由于塑件内空心,侧有凹槽所要求模具结构必须采用斜导柱抽芯机构。
并采用斜导柱在定模,哈夫块(斜滑块)在动模的结构。
可以绘出模具草图,如图4.6所示;
图4.6
4.3 合模导向机构设计
导向机构对于塑料模具是必不可少的部件,因为模具在闭合时要求有一定的方向和位置,所以必须设有导向机构,导柱安装在动模一边或定模这一边均可.通常导柱设在主型芯周围。
导向机构的主要定位、导向、承受一定侧压力三个作用。
在该设计中采用了导柱导向机构,而导柱导套为标准件。
所以,
,以下为选用的导柱形式,如图4.7所示:
图4.7
从图4.7中我们知道,其中对导柱结构有要求:
1、导柱的长度必须比型芯端面的高度高出6~8mm;
2、导柱应具有硬而耐磨的表面,多采用T8或T10硬度为 50~55HRC
,导向孔的结构要求如图4.8所示:
,导柱导套配合形式,如图4.9所示:
以上图形,导柱装入模板多用二级精度第二种过渡配合,而导套用二级精度静配合。
,导柱布置方式,如图4.10所示:
图4.10
4.4 塑件脱模机构设计
在注塑成型的每一个循环中,塑件必须由模具型腔中脱出,在该设计中,为了使符合脱模机构的要求:
使塑件留于动模;
塑件不变形损坏
这是脱模机构应当达到的基本要求。
要做到这一点首先必须分析塑件对模腔的附着力的大小和所在部位,以便选择合适的脱模方式和脱模位置,使脱模力得以均匀合理的分布。
良好的塑件外观
顶出塑件的位置应尽量设在塑件内部,以免损坏塑件的外观。
结构可靠
因此,根据4.6装配图所示,其模具结构的脱模机构主要由中心拉料杆拉断浇口,然后由顶杆推动推板使工作推出,还有在设计主型芯时也会有一定的拨模作斜度
。
4.5 侧向分型与抽芯机构设计
当塑件上具有与开模方向不同的内外侧孔时,塑件不能直接脱模,必须将成型侧孔的零件做成可动的,在塑件脱模前先将活动型芯抽出,然后再自模中通过顶杆顶出塑件。
而此次的设计完全符合以上要求,因此,也采用了侧向分型抽芯机构。
又,该塑制品是大批量的生产,故也使用了机动侧向分型抽芯。
4.5.1 抽拔距的计算
因为抽拔距等于侧孔深加2~3mm的安全系数,而当结构比较特殊时,如成型圆形线圈骨架,以及该外形为正方形的线圈骨架,(如下图所示)设计的抽拔距不能等于线圈骨架凹模深度S2,因为滑块抽至S2时塑件的外径仍不能脱出滑块的内径,必须抽出S1的距离再加上(2~3)mm,塑件才能脱出。
故抽拔距为:
S=S1+(2~3)=15+(2~3)mm=17~18mm
式中S—抽拔距;
S1—抽拔的极根尺寸(此为塑件最大的外形尺寸);
4.5.2 斜导柱的尺寸与安装形式
斜导柱的形状与基本尺寸;
斜导柱的基本尺寸主要以长度尺寸为主,斜导柱的长度计算为如下式:
L=1/2Dtanα+h×
1/cosα+1/2dtanα+S/sinα+(10~15)mm(4.4)
=1/2×
8×
0.36+50×
1/0.94+1/2×
20×
0.36+18/0.34+(10~15)mm
≈120mm
式中L—斜导柱的长度;
D—斜导柱固定部分大端直径;
h—斜导柱固定板厚度;
斜导柱的形状与尺寸如图4.11所示;
斜导柱的安装固定形式:
如图4.11所示,斜导柱的倾斜角a为20°
,而一般来说锁紧块的角度a′=a+(2~3)mm,斜导柱与固定板之间用三级精度第三种过渡配合。
由于斜导柱只起驱动滑块的作用,滑块运动的平稳性由导滑槽与滑块间的配合精度保证,滑块的最终位置由锁紧块保证,因此为了运动灵活,斜导柱和滑块间采用比较松的配合,斜导柱的尺寸为 Φ8-0.5-1.0,头部做成圆锥形,同时圆锥部的斜角为30°
度,它大于斜导柱的倾斜角,这样避免了斜导柱的有效长度离开滑块时,其头部仍然继续驱动滑块。
那么固定形式如图4.12:
4.5.3 滑块形式与导滑槽的形式
滑块分为整体式与组合式,因根据设计的需要,采用了组合式(哈夫块)。
而导滑槽的形式就是要能达到在抽芯的过程中,保证滑块远动平稳,无上下窜动和卡紧的现象。
同时又要方便加工,故导滑槽采用组合式(由导滑板与推件板组成)其组合图为4.13
4.5.4 锁紧楔形式
在塑料的注塑过程可中,型芯受到塑料很大的推力作用,这个力通过滑块传给斜导柱,而一般斜导柱为细长杆件,受力后容易变形,因此必须设置锁紧楔,以便在模具闭模后锁住滑块,承受塑料给予型芯的推力,锁紧楔与模件的边连接可以根据推力的大小,选取不同的方式,而该设计所选取的是整体式结构,牢固可靠,侧向力较大。
它直接与定模固定,可见装配图可知。
而锁紧楔的角度在斜导柱的固定形式已讲述了,这里不再重复。
斜导柱侧向分型最小开模行程的校核;
因为该塑件所用斜导柱侧向芯是在水平的位置,因此要完成S抽拔距所需要的开模行程H由下式求得;
H=S×
ctgα=18×
ctg20°
≈27mm;
斜导柱的受力分析及强度计算
斜导柱的受力分析;
根据斜导柱的形式,可以按公式:
Fw=Ft/cosα(4.2)
Fk=Ft·
tanα(4.3)式中 Fw—侧抽芯时斜导