质量工程课题设计Word文档格式.docx
《质量工程课题设计Word文档格式.docx》由会员分享,可在线阅读,更多相关《质量工程课题设计Word文档格式.docx(36页珍藏版)》请在冰豆网上搜索。
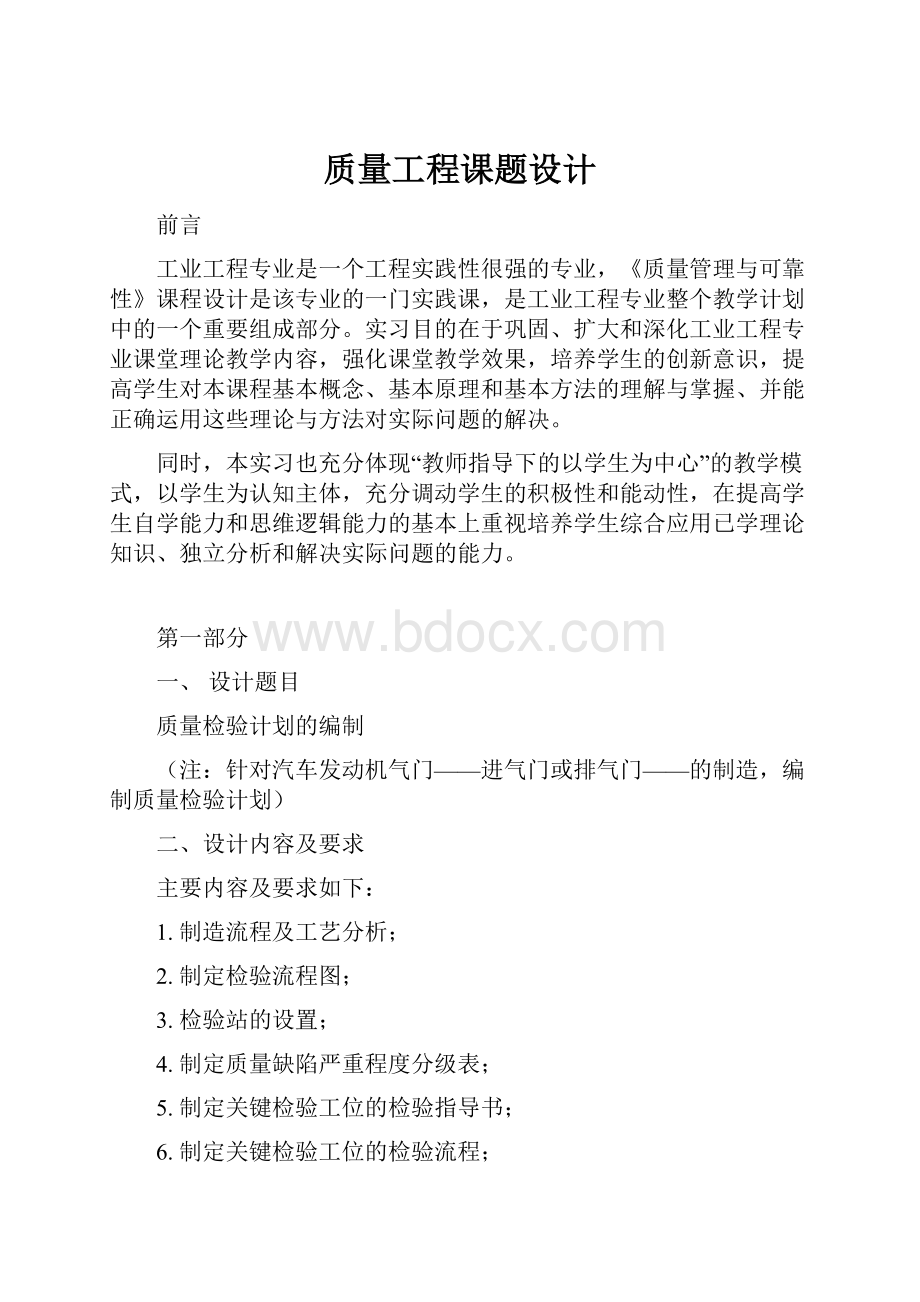
0.009
6
4.983
4.976
4.979
0.008
7
4.974
4.973
4.974
8
0.003
9
4.976
0.001
10
4.975
11
4.972
12
4.978
4.977
13
14
15
16
0.006
17
0.005
18
19
20
21
22
23
24
25
平均
0.004
2)直方图的绘制
最大值、最小值以及极差
MIN=4.972
MAX=4.984
R=0.012
K=8
分组:
组号
分段
频数
4.9725
4.9745
4.9765
35
4.9785
4.9805
26
4.9825
4.9845
4.986
合计
120
图1-1直方图
3)工序能力指数的计算
均值μ=4.9780与公差中心M=4.9775不重合
ε=μ-M=4.9780-4.9775=0.0005
T=4.985-4.970=0.015
S=0.0028637
K=0.0622222
工序能力指数Cpk=(T-2ε)/6σ=0.8187
查《现代质量工程》P174表6-1得到该产品加工属于三级加工,不合格率P为0.27%~4.55%,工序能力不足:
必须采取措施提高工序能力;
加强质量检验,必要时进行全数检验或增加检验的频次。
4)控制图的绘制
查《现代质量工程》表6-4得:
N=4,A2=0.729,D4=2.282;
X图的控制界限:
UCL=4.981,LCL=4.975,CL=4.978;
作x控制图见图1-2:
图1-2均值控制图
R图的控制界限:
UCL=0.010,CL=0.004,D3为负值故不考虑LCL
作R控制图见图1-3:
图1-3极差控制图
2、制造流程及工艺分析
表2-1流程及工艺
工序
工艺要求
说明
进料
进货检验(材料性能及材料化学成份)
细长条状
毛坯加工
下料
冲床
磨杆
M1080无心磨床
磨端面及倒角
专用设备
电热镦粗
D92-12A电热镦机
热压模锻成形
整体调质处理
1.毛坯杆部硬度进行抽检;
能用
2.对于金相组织进行抽检。
能用挑选型
3.毛坯杆部抗拉强度进行抽检不能挑选型,标准型,调整型特殊水平小样本
表面清理(抛丸)、防锈处理
校正
校正杆部直线度;
盘部相对杆部的跳动度
毛坯成品检验
1)宏观检查金属宏观组织的纤维方向与外观是否一致;
2)目测检查毛坯表面有无裂纹、过烧、腐蚀冷隔、疤痕等锻造缺陷;
3)对毛坯形状公差进行检验;
4)对毛坯位置公差进行检验。
(进)气门冷加工
第一次磨杆
杆部圆柱度及直线度:
公差等级6~7级;
尺寸公差:
IT8~9;
表面粗糙度:
粗车大外圆、大端面
端面对杆部的圆跳动度:
公差等级10级;
IT10;
普通车床C0616
切断
IT9~10
CM0632、C0616
第一次磨小端面
小端面对杆部的圆跳动度:
公差等级8~9级;
气门端面磨削设备
车(钻)小端焊坑
堆焊后应安排抽检。
1)气孔、夹渣、缩松等缺陷;
2)焊层的尺寸。
车床C0616(钻床Z12A)
时效处理
第二次磨小端面
公差等级8级;
第二次磨杆
公差等级5~6级;
IT5~6;
M1050无心磨床
磁力探伤
T1000型磁力探伤机、或荧光探伤
粗车锥面
锥面对杆部的圆跳动度:
C0630
车圆弧角、R圆弧、过渡圆弧及颈部
Y1017液压仿形车床
车锁夹槽
锁夹槽对杆部的圆跳动度:
Y1014液压半自动多刀车床(
)
滚压锁夹槽
IT9;
专用设备(滚丝机改造)
小端倒角
第三次磨小端面
公差等级7~8级;
第三次磨杆
公差等级7级;
IT6;
。
1、为了确保精加工定位精度,应安排工序间检验。
抽检
M1050
精车锥面、大外圆及大端面倒角
公差等级9级;
Y1013液压半自动多刀车床
粗磨锥面
锥面圆度:
IT6~7;
M120
精磨锥面
设备、夹具精度要求较上道工序更高
第四次磨杆
公差等级6级;
整体软氮化
表面硬度:
600HmV,氮化层深度不小于6um
精磨小端面
除锥面氮化层
;
1、不允许有黑疤、斑纹等缺陷存在。
M120A外圆磨床改造
清洗、防锈
成品检验
1.气门杆部直径:
千分尺
2.气门杆部圆柱度:
圆度柱测量仪
3.气门总长:
游标卡尺
4.气门盘厚度:
专用检具
5.盘部大外圆直径:
6.小端面相对于杆部跳动度:
百分表
7.小端面相对于杆部垂直度:
8.锥面相对于杆部跳动度:
9.锥面角度:
用投影仪将气门头斜面角放大,精确测量。
10.颈部直径:
游标卡尺。
11.杆端面硬度:
硬度仪。
12.杆身硬度:
13.锁夹槽形状:
投影仪放大、测量
14.锁夹槽底径:
15.锁夹槽中心到小端面尺寸:
专用检具。
3.检验流程图的绘制
检验流程图是用图形的方式来表达检验活动流程、检验站的设置、选定的检验方法及其相互关系。
首先熟悉和了解产品技术标准及设计技术文件、图样和质量特性分析;
其次熟悉产品形成的作业文件,了解工艺流程。
然后,根据作业流程,确定检验工序和作业工序的衔接及主要的检验工作方式、方法、内容,绘制检验流程图见图3-1~图3~2.
毛坯加工检验流程图:
图3-1毛坯加工检验流程图
进气门加工检验流程图:
图3-2进气门加工检验流程图
4、检验站的设置
检验站是根据生产作业分布(工艺布置)及检验流程设计确定的作业过程中最小的检验实体,是检验人员进行检验活动的场所。
其作用是通过对产品的检测,履行产品检验和监督的职能,防止所辖区域不合格品流入下一作业过程或交付(销售、使用)。
合理设置检验站可以更好地保证检验工作质量,提高检验效率;
设置的基本原则:
(1)质量控制的关键作业部位和控制点;
(2)满足生产作业过程的需要,并和生产作业节拍同步和衔接;
(3)适宜的工作环境;
(4)节约成本,有利于提高工作效率。
通常检验站按工艺流程可分(设)为进货检验站、过程检验站、完工检验站、成品检验站。
表4-1检验站设置
序号
所处工序位置
检验站名
检验目的
仓库
进货检验站
进货检验(E、SP)
检验材料性能及材料化学成份是否符合要求
理化检验(F、I、SP)
检验毛坯杆部硬度、金相组织及抗拉强度是否符合要求
毛坯成品检验(N、S、L)
1)宏观检查金属宏观组织的纤维方向与外观是否一致;
2)目测检查毛坯表面有无裂纹、过烧、腐蚀冷隔、疤痕等锻造缺陷;
毛坯成品检验(P、SP)
4)对毛坯位置公差进行检验。
过程检验站
工序检验(S、P、SP)
1)气孔、夹渣、缩松等缺陷;
2)焊层的尺寸。
无损检测(F、L)
检验产品内部是否有损伤
工序检验(P、SP)
确保精加工定位精度
感官检验(S、L)
剔除有黑疤、斑纹等缺陷存在的零件
成品检验站
成品检验(ZP、SP)
7.小端面相对于杆部垂直度:
投影仪放大气门头斜面角,精确测量
11.杆端面硬度:
5、质量缺陷严重程度分级表
由于产品质量特性的重要性、及质量缺陷所造成后果的严重性各不相同,为此,企业在编制产品检验计划时,应当依据分级原则,明确列出该产品的缺陷项目、状况及严重性级别,形成具体的质量缺陷严重性分级表,从而有利于检验资源的安排、检验计划的制订与实施。
表5-1质量缺陷严重程度分级表
因素
级别
安全
运转或运行
寿命
可靠性
装配
使用安装
外观
下道工序
本系统内处理权限
检验严格性
致命缺陷(A)
影响安全的所有缺陷
会引起难以纠正的非正常情况
会影响寿命
必然会造成产品故障
会造成产品安装的困难
一般外观缺陷构不成致命缺陷
肯定造成下道工序的混乱
总质量师
100%严格检验加严检验
严重缺陷(B)
不涉及
可能引起易于纠正的异常情况
可能影响寿命
可能会引起易于修复的故障
肯定会造成装配困难
可能会影响产品安装的顺序
使产品外观难于接受
给下道工序造成较大困难
检验部门负责人
严格检验正常检验
一般缺陷(C)
不会影响运转或运行
不影响
不会成为故障的起因
可能会影响装配的顺序
对产品外观影响较大
对下到工序影响较大
检验工程师
一般正常检验抽样检验
轻微缺陷(D)
对产品外观有影响
可能对下道工序有影响
检验站,组长
抽样检验放宽检验
6、检验流程的制定
1)原材料入库检验流程,如下图6-1所示:
图6-1原材料入库检验流程图
2)过程检验流程
抽样检验流程,如图6-2所示:
图6-2抽样检验流程图
全数检验流程,如图6-3所示:
图6-3全数检验流程图
3)成品检验流程,如图6-4所示:
图6-4成品检验流程图
7、制定检验指导书
检验指导书是用来指导检验人员正确实施检验作业的规程性文件,其目的是为重要的检验活动提供具体的指导。
由于检验对象、检验方法、检测手段及检验标准等的不同,不同的检验作业也应有不同的检验指导书。
明确规定的检验方法和所用的检测手段。
必须针对质量特性和不同进度等级的要求合理选择适用的测量工具或仪表,并在指导书中注明它们的型号、规格和编号,甚至说明其使用方法。
8、检验方案的制定
计数标准型一次抽样方案:
目的:
1、同时保护供需双方的利益
2、不需要提供待检批产品的质量数据
3、易于实施
适用于孤立批产品的抽样检验。
进货与出货检验符合标准型抽样方案
1、确定质量要求
规定杆直径在4.97~4.985mm为合格品,凡超出这个范围为不合格品。
2、确定P0、P1及α、β四个参数。
一般取生产者风险α=0.05,使用者风险β=0.01,假设取P0=2%,P1=8%。
3、检验批的确定
由于生产方年产75万件,所以先进一个月的毛坯取N=60000,并将其定为检验批
4、检索抽样方案
查表8-6,得n=120,c=4。
即抽样方案为(120,4)
5、随机抽样样本
在提交的3000件零件中随机抽取120件样品。
6、检验样本获取数据
对120件样品进行检验,其中不合格品为0件。
7、批质量判断
由于d=0<
c=4
8、批的处置
接收该批产品。
计数调整型抽样方案:
1、调整检验的严格程度,促使生产方改进和提高产品质量。
2、使用方可按质量好坏选择供应方。
GB/T2828.1使用于连续批检验的下列场合:
成品、部件和原材料、操作、在制品、库存品、维修操作、资料或记录、管理程序。
另外,还可用于一定条件下的孤立批检验。
成品入库检验符合该抽样方案
1、选取抽样标准。
查GB/T2828.1-2003《抽样检查导则》表8-7、表8-8、表8-9。
2、研究标准规定的检验程序。
检验程序步骤:
规定产品质量标准;
确定批量(N);
规定检验水平(IL);
规定合格水平(AQL);
确定抽样方案类型(一次、两次和多次);
确定抽样方案;
批的组成与提交;
检验、判定与记录;
的在提交与不合格的处理。
3、实施检验程序
1)规定产品的质量标准。
应以进气门杆的外径Ф5mm为检验的质量特性,并规定外径尺寸在4.97~4.985之间为合格品,凡超出这个范围的为不合格品。
2)确定批量(N)。
由于工厂日产量为3000件,所以可取N=3000
3)规定检验水平(IL)。
由于本例为一般性检验,故取检验水品Π。
4)确定合格质量水平AQL。
假设本例采用过程平均法来规定AQL值。
由于不合格品率为0。
所以去AQL=0.1。
5)确定抽样方案的类型。
采用一次抽样,抽样严格度分为正常检验、加宽检验、特宽检验和加严检验几种。
在实施检验过程中,应根据检验结果进行检验严格度转换。
6)确定抽样方案。
本例中N=3000,AQL=0.1,查表8-10得样本字码为K,再查表8-11得
正常检查一次抽样方案:
n=125,c=0,Re=1。
加严检查一次抽样方案:
n=125,c=0,Re=1;
放宽检查一次抽样方案:
n=50,c=0,Re=1;
绘制OC图:
对于正常检验,L(P/AQL=1)=0.881,说明正常抽样方案将以88.1%的概率被判为批合格。
对于加严检验,L(P/AQL=1)=0.881,说明加严抽样方案将以88.1%的概率被判为批合格。
对于放宽检验,L(P/AQL=1)=0.9508,说明放宽抽样方案将以95.08%的概率被判为批合格。
挑选型抽样方案:
按事先规定的抽检方案对交检批进行抽检,对于合格批,样本中的不合格品换成合格品,准许接收;
对于不合格批,进行百分之百检验,把所有的不合格口全部换成合格品后再被检验接收。
毛坯成品检验符合该抽样方案
1、规定产品质量标准
以毛坯杆直径大于等于毛坯最小杆直径,否则不合格。
假设最小杆直径为Ф5。
2、确定质量保证方式
质量保证方式有两种:
1)平均质量保证方式;
2)单批质量保证方式
本例采用平均保证方式
3、AOQL或LQ值的选择
假设AOQL=2.0%。
4、估算过程平均不合格品率
假设过程平均不合格率为p=0.2%。
5、组成检验批
设N=1000
6、检索抽样方案
查到AOQL=2.0%的表,再由批量N=1000的行与p=0.2%的列相交处,知n=41,Ac=1,即方案为(41,1)。
7、随机抽取样本
随机抽取n=41
8、检验样本
按产品的质量要求对样本中的每一个单位产品进行测试,判断其是否合格,并记录下样本中的不合格品的个数。
9、判断批接收或不接收
若d<
=c,则接收该批产品;
若d>
c,则拒收该批产品。
10、抽样检验后的处置
对已判断为合格的检验批次,应予以接收,而对不合格的检验批,则予以拒收。
第二部分
质量控制及Minitab工具的使用
注:
参见《工业工程专业课程设计指导》。
二、设计内容与要求
针对实例,利用排列图确定出现不合格品的主要环节和关键工序。
针对关键工序,利用控制图确定过程是否受控;
在受控情况下利用工序能力分析图对工序能力进行分析。
再利用因果分析图分析工序能力不足的原因。
针对所找出的原因,采取相应措施,提高工序能力。
再利用排列图对改进效果进行对比。
参见《工业工程专业课程设计指导》第四章第三节:
质量控制课程设计案例(P174)。
1、基于数据测量的原因分析
针对案例中不合格率比较高的现状,在数据测量的基础上寻找各种原因。
数据输入见图4-1:
图4-1Minitab的数据输入
导出排列图见图4-2:
图4-2机梁各工序不合格品的排列图
通过排列图可知不合格品数最多的是精铣机梁两外角尺平面,所以问题出现在精铣机梁两外角尺平面上。
2、利用排列图确定主要原因
根据图4-3精铣机梁两外角尺平面工序不合格品数据,绘制相应的排列图:
图4-3精铣机梁两外角尺平面工序不合格品数据
导出排列图见图4-4:
图4-4精铣机梁工序不合格品排列图
由图可知,平面度的工序是影响精铣机梁两外角尺质量的A类因素,即为主要因素。
4、工序稳定性及能力分析
找出主要原因后,对平面度的工序进行稳定性分析和工序能力指数计算,在工序受控的情况下,判断工序能力指数是否满足要求,以确定是否需要进行改进。
平面度的目标指标为:
0.11mm,最大不得超过0.15mm,最小不得低于0.07mm,从精铣机梁两外角尺平面工序中依加工次序随机抽取50件产品,得到的数据见图4-5:
图4-5平面度工序稳定性及工序能力指数测定
利用minitab软件导出控制图见图4-6、图4-7:
图4-6均值控制图
图4-7极差控制图
利用软件导出工序能力分析图见图4-8:
图4-8工序能力分析图
观图得到Cpk=0.59属于三级加工,不合格率P为0.27%~4.55%,工序能力不足:
5、因果分析及对策拟定
输入基本数据效果见图4-9:
图4-9影响因素的输入
按相关步骤操作软件得到因果图见图4-10:
图4-10因果图
进一步对造成机梁平面度不合格的原因进行分析,得到因果关系图见图4-11:
图4-11影响机梁平面度而造成不合格品的因果图
6、措施实施效果分析
测定工序能力指数
输入改进后的数据见图4-12:
图4-12改进后对平面度工序的工序能力指数测定
导出改进后的工序能力分析图见图4-13:
图4-13改进后的工序能力分析图
改进后的工序能力Cpk=1.07,属于二级加工,工序能力