05布置与配管Rev02Word文件下载.docx
《05布置与配管Rev02Word文件下载.docx》由会员分享,可在线阅读,更多相关《05布置与配管Rev02Word文件下载.docx(27页珍藏版)》请在冰豆网上搜索。
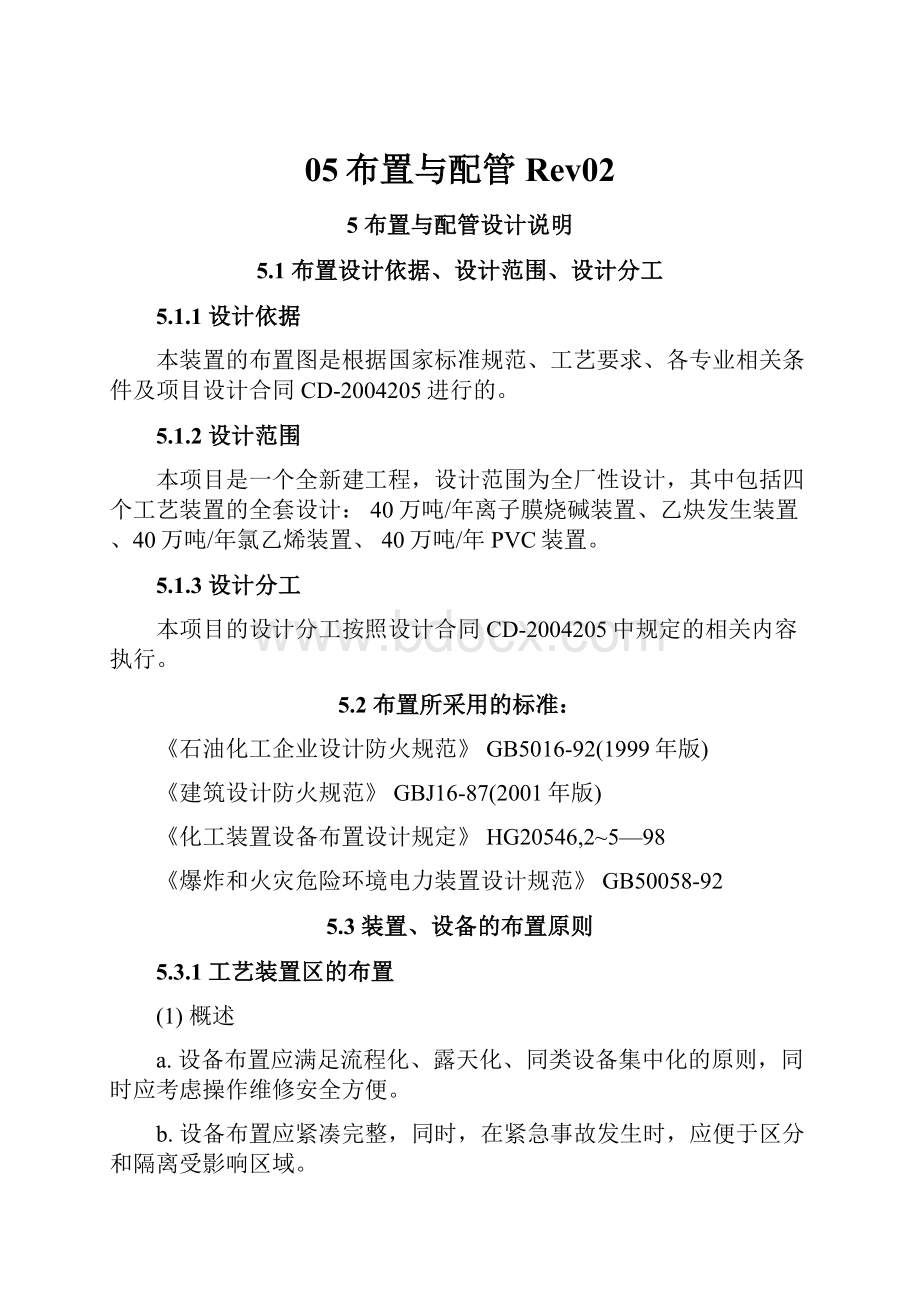
c.装有强酸、强碱、有毒和其他腐蚀性介质的设备,应集中布置。
(2)泵的布置
a.为了使泵的入口管线尽可能短,泵的布置应尽可能靠近容器的出口。
b.为了节省空间,泵可布置在管廊下。
(3)压缩机
a.当接管口在压缩机下方时,压缩机应架空布置,以便管线及其附件布置在压缩机下方的平台上。
b.压缩机应布置在室内,特殊情况除外。
c.为了压缩机及其附件的维修,应设置起重机或吊车。
(4)塔和容器
a.塔和立式容器通常平行地布置在管廊的旁边。
b.为了使管线尽可能的短,卧式容器应尽可能的布置在管廊的旁边。
c.对于装有催化剂或内件需定时更换的塔、容器、反应器,应在进口提供足够的空间,以便装卸催化剂和更换内件。
d.除非工艺特殊要求或技术原因外,容器通常布置在地面。
(5)换热器
a.概述
除非工艺特殊要求或技术原因外,换热器通常布置在地面。
换热器的布置应考虑维修空间和逃离路线。
管壳式换热器叠放时,不应超过三个,当壳层的直径大于或等于600毫米时,叠放不应超过两个。
b.抽芯式换热器
为了实现抽芯,抽芯式换热器的抽芯端应有足够的抽芯空间。
抽芯检修时要利用起重机,若起重机不能靠近抽芯端,则应设置永久的维修梁和检修吊钩。
c.固定管板式换热器
固定管板式换热器的布置,应考虑拆卸空间,以便清理和维修。
若将换热器移到维修车间(厂)去维修,应考虑移动和运输设备的通道和空间。
5.3.3管廊
(1)高度
管廊的最底层的高度应满足下面的要求:
a.当管廊通过主要交通道路时,其净高不低于5.5米。
b.保证足够的空间,以便维修时,吊起、移动需维修的设备。
c.保证足够的空间,以便管廊下容器和换热器的配管。
d.维修时,保证管廊下交通工具的畅通。
e.管廊上应预留10%--30%的空间。
(2)管廊上的检修通道
通常,大型管廊上仪表桥架的旁边应设置600毫米宽的检修通道。
由于管廊空间狭小,部分管廊上不考虑设置检修通道。
5.3.4安全距离
(1)对于设备与公共建筑、道路及相连设备间的安全距离,必须符合《石油化工企业设计防火规范》GB50160-92(1999年版)的规定。
(2)安全疏散通道的要求
a.长度超过8米的设备平台,应设置不少于两个通往地面的梯子,作为安全疏散通道。
多个安全疏散通道彼此不能相连,也不能与危险源相连。
5.4各装置布置设计说明
5.4.1离子膜烧碱装置
5.4.1.1装置的组成
按照合同要求,离子膜烧碱全部为新建工程。
装置布置设计包括以下几个工序:
一次盐水工序、电解工序、氯氢处理工序、废气处理工序、蒸发固碱工序、液氯工序、HCl合成及高纯盐酸工序、液体罐区、装置内管廊。
其中一次盐水工序由化盐和精制两部分组成,化盐部分总图上布置在铁路的东侧,精制部分布置在烧碱装置内;
液体罐区布置在铁路东侧,盐堆厂的北侧;
蒸发固碱布置在铁路西侧。
5.4.1.2工序布置说明
(1)一次盐水工序
一次盐水工序的化盐部分结合当地的气候特点,采用室内化盐,3个溶盐桶(V0102A/B/C)、粗盐水槽(V0103)、粗盐水泵(P0102A/B)全部布置在室内,厂房北侧紧邻盐堆厂。
一次盐水精制部分布置在装置的南侧,北面是二期的发展预留用地。
由于当地的冬季持续时间长,且气温又低,泵基本布置在泵房内;
根据工艺特点及配管的需要设有5个泵房。
压滤厂房由于没有压滤机的厂商条件,现在仅为一个经验设计,待有条件后再具体调整。
(2)电解工序
电解工序为引进,由于尚无外商资料,暂时仅在装置内留有70米x144米的占地面积,待有外商资料后再作详细设计。
(3)氯氢处理工序和废气处理工序
这部分主要由3个单元组成:
氯处理及废气处理厂房,氯压缩厂房,氢处理厂房。
废气处理及氯气洗涤和干燥部分的设备布置在三层混凝土厂房内。
氯处理工序的洗涤塔和干燥塔放在EL100000平面.因废气处理工序的吸收塔和尾气塔自流出的液体要流入对应的循环槽内,故吸收塔和尾气塔布置在EL107500平面上,风机放在EL118000平面且厂房封闭放置,循环槽放在框架外。
氯气压缩机布置在压缩厂房内,厂房为封闭设计,土建设计时考虑通风。
由于现阶段没有氯压机厂商资料,此部分的布置仅供参考,在详细设计阶段根据厂商资料再作相应的调整。
氢处理工序的氢气洗涤塔及压缩和冷却联合布置在一个厂房内,洗涤塔、冷却器及捕沫器放在三层框架内。
该厂房为防爆区,土建设计考虑通风及防爆。
由于现阶段没有氢压机厂商资料,此部分的布置仅供参考,在详细设计阶段根据厂商资料再作相应的调整。
(4)蒸发固碱工序
蒸发固碱工序为引进,由于尚无外商资料,暂时仅在该部分装置内留有80米x130米的占地面积(未包括仓库),待有外商资料后再作详细设计。
(5)液氯工序
液氯冷凝机组及液化器布置在两层封闭的框架厂房内;
液氯贮槽和液氯包装为敞开式布置;
同时考虑当地的气候条件,在包装区域设一个临时休息室。
由于没有冷凝机组的厂商资料,此部分的布置仅供参考,待有详细资料后再具体调整。
(6)HCL合成及高纯盐酸工序
该工序的布置仅为一个经验布置,由于一些关键设备(二合一合成炉R0701A~J,氯化氢冷却器EA0701A~J,降膜吸收器T0701A~C,尾气吸收塔T0702A~C等)没有厂商资料,厂房的一些具体尺寸无法给出,待有条件后再将其细化。
(7)液体罐区
本工序由液体贮罐区和泵房及装车站台组成。
盐酸及硫酸采用汽车槽车运输,液碱既用火车运输又用汽车运输。
(8)装置内管廊
来往于各工序的工艺管道,公用工程管道及仪表电气桥架布置在装置内管廊上,本装置的内管廊全部采用钢筋混凝土,分三层,8米宽,每层高分别为5.5米7.5米和9.5米
管廊预留15%的空间。
5.4.2乙炔装置
5.4.2.1装置的组成
按照合同要求,乙炔装置全部为新建工程。
乙炔发生工序、乙炔清净工序、电石渣压滤工序,以及一部分经澄清池沉降后的滤液回用等四部分,按照两个独立的系列设计,气柜、碱液系统、次氯酸钠配置系统共用。
5.4.2.2工序布置说明
(1)乙炔发生工序
乙炔发生单套厂房占地约为567m2,采用封闭式钢筋混凝土框架,第二、三层楼板采用篦子板以利于通风,其余层均采用强制通风。
乙炔发生器贮斗以上的电石加料系统由粉体专业设计,相关的设备布置详见粉体专业的布置图。
考虑到机运设备检修,设置一3x3m检修吊装孔,在厂房两端各有一个楼梯通道。
由于缺乏乙炔发生器的设备条件,因此现有的厂房布置是根据经验设计的,待设备条件具备后,再调整厂房布置。
乙炔气柜、分离器、阻火器露天布置,在乙炔压缩机厂房以南40米处,占地大约为1600m2。
(2)乙炔清净工序
乙炔清净工序塔区采用开敞式钢筋混凝土框架,框架分为三层,两端各有一个楼梯通道。
碱液、次氯酸钠配置系统采用露天布置。
泵类设备分别放置在三个单层厂房内,在泵房上面布置管廊。
单套六台乙炔压缩机布置在15x54m的单层厂房中,厂房采用钢筋混凝土结构,设有电动检修葫芦。
由于乙炔压缩机定货设备条件未到,此布置仅为经验布置,待有条件后再将其细化。
(3)电石渣压滤工序
压滤厂房是按照业主提供的设备资料布置的。
厂房为7米和14米两层,采用钢筋混凝土结构,一层为开敞式,二层采用封闭结构。
厂房设有单梁电动吊车及吊装检修区。
压滤厂房占地大约为1710m2。
(4)装置内管廊
两套系列之间内管廊呈T形布置。
管廊柱子为钢筋混凝土结构,上部的纵梁和横梁采用钢结构,分为两层,管廊宽8米,层高为5米和7米。
上层为电气仪表桥架。
5.4.3氯乙烯装置
5.4.3.1装置的组成
根据工艺装置过程,此装置共分6个工序:
混合脱水工序、合成工序、粗氯乙烯净化压缩工序、氯乙烯精馏工序、污水处理、罐区。
5.4.3.2工序布置说明
(1)混合脱水工序
混合脱水、粗氯乙烯净化和合成工序的中间贮槽根据工艺的特点和要求放在同一个框架内,其中乙炔干燥为成套装置,也为一个反应系列。
此框架为钢筋混凝土,两系列采用对称布置,其中泵房为封闭,其余为敞开。
框架共分两层(6米、12米),占地面积(74米X18米)X2(套),其中标高12米的只有一部分。
(2)合成工序
此框架为钢筋混凝土,两系列采用对称布置,但此框架的屋顶楼面为钢结构,主要是考虑合成器从上往下吊装。
框架共分两层(7米、14米),占地面积(85米X18米)X2X2(套)。
框架高度定为7米、14米主要是考虑设备较长,需要一定的起吊高度。
(3)粗氯乙烯净化、压缩工序
压缩厂房由于没有压缩机的厂商条件,现在仅为一个经验设计,待有条件后再具体调整。
两个系列的压缩机考虑放在一个厂房内,便于检修和操作。
其中盐酸脱吸为成套装置(目前无条件),将单独布置它。
大约占地面积(24米X12米),厂房高度目前考虑为8米,有检修吊车,条件具备之后再做调整。
(4)氯乙烯精馏工序
此框架为钢结构,两系列采用对称布置,其中残液槽和残液泵为一个系列,将根据后面的具体情况考虑摆放的位置。
此框架共分三层,6米、12米、20米。
占地面积(30米X12米)X2(套),
(5)污水处理
此工序独立布置,钢筋混凝土结构,并采用封闭厂房,单层,屋顶高度暂定为15米,占地面积(30米X21米)。
(6)罐区
罐区内包括氯乙烯成品罐、粗氯乙烯贮罐、VCM气柜、冷剂贮罐和泵房。
占地面积大约为(164米X64米)。
(7)装置内管廊
整个氯乙烯装置的管廊为丁字形的布置,钢筋混凝土结构,并考虑管廊下设通道。
管廊的宽度分别为8米,6米。
8米宽的分为三层,高度分别为5米、7米、9米;
6米宽的分为三层,高度分别为6米、8米、10米。
两系列基本按其中一条6米管廊对称布置。
5.4.4PVC装置
5.4.4.1装置的组成
按照合同要求,PVC装置全部为新建工程。
化学品配制与准备工序、VCM及脱盐水加料工,气提工序,聚合工序,VCM单体回收工序,干燥工序
全厂规模为40万吨PVC/年,除干燥工序外,其余大体分成两条线,每条线20万吨,整套PVC装置的占地大概为260米X160米,由于有几个工序条件还不完整,占地面积可能还有调整。
5.4.4.2工序布置说明
(1)化学品配制与准备工序
每20万吨用一套化学品配制与准备,每套占地面积为21米X36米
根据工艺要求,该工序为钢筋混凝土三层框架结构,由于加料等工作量比较大,设置有电梯、检修吊车。
(2)VCM及脱盐水加料工序
每20万吨用一套VCM及脱盐水加料,每套占地面积为36米X45米
另外加上干燥离心母液回用系统,也是每20万吨用一套,每套占地面积为30米X10米。
VCM加料采用露天布置,脱盐水加料泵房为钢筋混凝土全封闭结构,由于目前还没有机泵的具体尺寸,泵房的大小目前仅为一个经验设计,待有条件后再具体调整。
(3)聚合工序
每20万吨采用一套聚合,每套占地面积为45米X26米
由于聚合釜一般供货周期比较长,为设备吊装方便,这部分全部采用三层钢结构,聚合釜顶设置检修吊车。
(4)VCM单体回收工序
每10万吨采用一套VCM单体回收,全装置共用4套,每套占地面积暂定为20米X20米。
压缩厂房由于没有厂商条件,现在仅为一个经验设计,待有条件后再具体调整。
由于压缩厂房为防爆区,采用钢筋混凝土全封闭结构,设置检修吊车。
冷凝器和混合槽为露天布置。
(5)汽提工序
每10万吨采用一套汽提,全装置共用4套,每套占地面积为40米X15米
本工序包括浆料汽体和废水汽体两个工序,均采用钢结构露天布置,
汽提塔的资料暂缺,目前框架高度仅为一个经验设计,待有条件后再具体调整。
(6)干燥工序
全装置共采用一套,暂时规划占地30米X40米
该工序的布置仅为一个经验布置,由于一些关键设备还没完成选型,目前初步按照其他同等规模的厂房布置,待有条件后再将其细化。
(7)装置内管廊
来往于各工序的工艺管道,公用工程管道及仪表电气桥架布置在装置内管廊上,本装置的内管廊多为柱子采用钢筋混凝土,上部的纵梁和横梁采用钢结构。
东西向的管廊分三层,8米宽,每层高分别为4米6米和8米。
南北向的管廊分三层,6米宽,每层高分别为5米7米和9米。
5.5管道输送的介质及其分类
管道输送的介质及其分类按《接触性毒物危害程度分级》GB5044,《石油化工企业设计防火规范》GB50160,《建筑设计防火规范》GBJ16,具体见初步设计劳动安全卫生专篇。
管道输送的介质及其分类按《压力管道设计单位认证与管理办法》的划分,将在工程设计的管道命名表中详细列出。
5.6厂区外管设计说明
5.6.1设计范围
本设计的设计范围为厂区界区线(B.L)范围内的各工艺生产装置、辅助生产装置之间的工艺、热力及采暖外管道的设计(给水、排水、循环水、消防水、污水等埋地管道不属于本设计的设计范围),具体分工范围如下:
本设计与厂外联系的管道的设计分界点在厂区界区线(B.L)外1m。
本设计与厂内各工艺生产装置、辅助生产装置联系的管道的设计分界点在各装置的界区线(B.L)外1m。
5.6.2设计原则
(1)满足工艺生产装置和辅助生产装置的要求。
(2)符合安全规范要求。
(3)满足工艺操作和维护要求,在需要的部位设置操作平台。
(4)留有发展余地,预留20%的承载能力。
(5)节约投资。
(6)注意结构、布置和厂容的美观。
5.6.3敷设方式
为了操作、维修方便,且节约投资,基本上采用架空敷设方式。
为不影响交通,厂内管廊的净空高度为5.5~6.5m。
但在不影响交通的地方采用矮管墩敷设(如采暖管线沿围墙敷设)。
天然气管线埋地进厂后即改为架空敷设。
5.6.4设计概况
本工艺供热外管道中的公用物料管线主要为蒸汽管、冷凝水管、脱盐水管、工厂空气管、仪表空气管、氮气管、冷冻水管、热水管等;
化工物料管线主要为天然气管、乙炔管、母液管、盐酸管、硫酸管、烧碱管、次氯酸钠管、氯化氢、废气管等
管线总长约65000m其中不锈钢管约14200m.保温管线总长12000m,保冷管线总长500m。
管架总长约4250m。
最大碳钢管为DN800,最大不锈钢管为DN250。
设计将尽量采用自然补偿,在自然补偿不能满足要求的地方,尽量采用价格便宜,安全可靠,维修量少的∏形弯进行管道的伸缩补偿。
在公用物料管线的分支处设是否设置阀门,可根据业主关于操作管理方面要和意见决定。
初步设计已考虑了一定数量的支线阀门。
对所有易燃易爆物料都考虑了防静电接地措施。
管架设计情况见结构专业设计,保温、防腐设计见管材专业说明。
5.7管道材料设计概述
5.7.1设计范围
本说明仅适用于亿利40万吨/年PVC项目烧碱装置、乙炔装置、VCM装置、PVC装置、公用工程内各工序管道材料的设计说明。
5.7.2设计依据
(1)根据工艺、系统专业所提供各装置工艺介质,压力及温度,选择该条件下相适应的管道材料及阀门。
(2)根据国内、外供货商提供管道材料所提出的特殊要求及规定,以此为参考确定各装置管路材料。
(3)对
(1)和
(2)条规定外,业主对管道材料的规定和要求也作为该工程的设计依据。
(4)管道设计严格执行管道材料等级规定中所规定的管道材料要求,若采购的材料与管道材料等级的要求不符合时,所变更的材料必须与材料等级中的要求相当或更好。
5.7.3管道材料的范围为:
管子,管件,法兰,阀门,垫片,螺栓和螺母材料。
(1)管件分为通用管件和特殊管件。
a.通用管件范围为:
弯头,三通,大小头,管帽,大曲率半径弯管,丝堵等标准管件。
b.特殊管件范围为:
蒸汽疏水器,限流孔板,爆破板,管道过滤器,消音器,视镜,8字盲板,喷嘴,软管接头与连接件,膨胀节,取样冷却器,事故沐浴器,洗眼器,阻火器等。
(2)阀门包括通用阀(闸阀,截止阀,止回阀,球阀,蝶阀,旋塞阀等)。
5.8管道材料专业设计采用的标准规范
国内标准:
GB5310-95高压锅炉用无缝钢管
GB12459-90钢制对焊无缝管件
GB50235-97工业管道工程施工及验收规范(金属管道篇)
GB50236-98现场设备,工业管道焊接工程施工及验收规范
GB50316-2000工业金属管道设计规范
HG20592-97钢制管法兰型式,参数(欧洲系列)
HG21547-93管道用钢制插板,垫板,8字盲板
HG20520-92玻璃钢/聚氯乙烯复合管道设计规定
HG/T21562-94衬聚四氟乙烯钢管和管件
HG/T21631-1990钢制有缝对焊管件
HG/T21632-1990锻钢承插焊,螺纹和对焊接管台
HG/T21634-1988锻制承插焊管件
HG/T21635-1988碳钢,低合金钢无缝对焊管件
HG/T21636-1987玻璃钢/聚氯乙烯(FRP/PVC)复合管和管件
HG/T20646-1999化工装置管道材料设计规定
HG/T20679-1990化工设备,管道外防腐设计规定
HG/T20695-1987化工管道设计规范
GB/T3091-93低压流体输送用镀锌焊接钢管
GB/T3092-93低压流体输送用焊接钢管
GB/T8163-99输送流体用无缝钢管
GB/T13793-92直缝电焊钢管
GB/T13927-92通用阀门压力试验
GB/T13401-92钢板制对焊管件
GB/T14976-94流体输送用不锈钢无缝钢管
GB/T12220-89通用阀门标志
GB/T12221-89法兰连接阀门结构长度
GB/T12224-89钢制阀门一般要求
GB/T12771-2000输送流体用不锈钢焊接钢管
5.9管道材料的一般选用
5.9.1管道材料共分三大类:
(1)普通碳钢:
用于工作温度不大于300℃、腐蚀性不强的工艺介质以及压力比较低的蒸汽、水、空气等公用介质管道。
对有轻腐蚀性的介质,通过增加腐蚀裕量、提高管壁厚度来解决。
(如稀碱液)
常用的材料如下(以管子材料为基准):
碳钢20#钢,Q235-A
(2)奥氏体不锈钢:
用于需保证介质的清洁和耐腐蚀要求的工艺介质管道,如脱盐水、32%NaOH碱液等。
为了保证仪表空气及饮用水的无尘、无油的要求,采用不锈钢钢管。
0Cr18Ni9,00Cr17Ni12Mo2
(3)复合材料:
为保证一般金属材料难以满足要求的腐蚀性强的介质,如盐酸、含汞介质、次氯酸钠液等,同时又达到节约成本的目的,本设计中根据不同介质情况使用了多种不同的复合材料,如:
PVC/FRP、CS/PO、CS/F4管等,来满足工艺要求。
5.9.2一般工艺介质(腐蚀性轻微),温度小于不大于370oC管道材料选用20碳钢。
腐蚀裕度为1.5mm。
5.9.3对仪表空气惯用材料为镀锌钢管,根据CCECC规定(99-03)改成0Cr18Ni9不锈钢。
腐蚀裕度为0mm。
5.9.4对苛性钠工艺介质温度T<
80oC,浓度为30%以下,管道材料选用超低碳奥氏体18-8不锈钢00Cr19Ni10。
腐蚀裕度为0mm
5.9.5对苛性钠工艺介质温度80<
T<
120oC,浓度为32%<
=NaOH<
=50%,管道材料选用超低碳奥氏体Mo2Ti不锈钢00Cr17Ni14Mo2。
腐蚀裕度为0mm。
5.9.6对一般含氯离子腐蚀性工艺介质或温度T<
60oC,管道材料选用玻璃钢/聚氯乙烯(FRP/PVC)复合管和管件,腐蚀裕度为0mm。
5.9.7对氯气工艺介质,温度T<
100oC,管道材料选用耐温树脂玻璃钢管和管件,腐蚀裕度为0mm。
树脂为DERAKANE470
5.9.8对含氯离子腐蚀性工艺介质或温度60<
90oC,管道材料选用玻璃钢/氯化聚氯乙烯(FRP/CPVC)复合管和管件,腐蚀裕度为0mm。
其玻璃钢现场缠绕。
5.9.9循环碱液(电解厂房内)工艺介质温度80<
90oC,管道材料选用玻璃钢/高强聚丙烯(FRP/PPH)复合管和管件,腐蚀裕度为0mm。
5.9.10对<
95%-70%硫酸,高纯盐酸,氯化氢气体等工艺介质温度80<
120oC,管道材料选用20#钢/聚四氟乙烯(20#/PTFE)复合管和管件,腐蚀裕度为0mm。
5.9.11对粗盐水,一次盐水等工艺介质温度T<
60oC,管道材料选用20#钢/聚烯烃(20#/PO)复合管和管件,腐蚀裕度为0mm。
5.9.12对苛性钠工艺介质温度120<
180oC,浓度为52%<
=NaOH,管道材料选用软态纯镍Ni。
5.9.13对真空脱氯工艺介质温度T>
100oC,管道材料选用钛合金TA2。
(详细的管路材料选用见管道材料规定等文件)
5.9.14.所有管件、阀门、法兰的材料皆按上述原则分类,材料与所属管道材料性能相当。
5.9.15.树脂规定
本设计中材料FRP/PVC所使用的化学性能、机械性能施工性能均比较优异的乙烯基酯树脂。
界面粘合剂规定PVC/FRP界面粘合剂采用PF-2。
5.10管道等级代码及缩写说明
5.10.1管道等级代