高新申报 项目真实案例 生产类rd撰写 教学Word格式.docx
《高新申报 项目真实案例 生产类rd撰写 教学Word格式.docx》由会员分享,可在线阅读,更多相关《高新申报 项目真实案例 生产类rd撰写 教学Word格式.docx(19页珍藏版)》请在冰豆网上搜索。
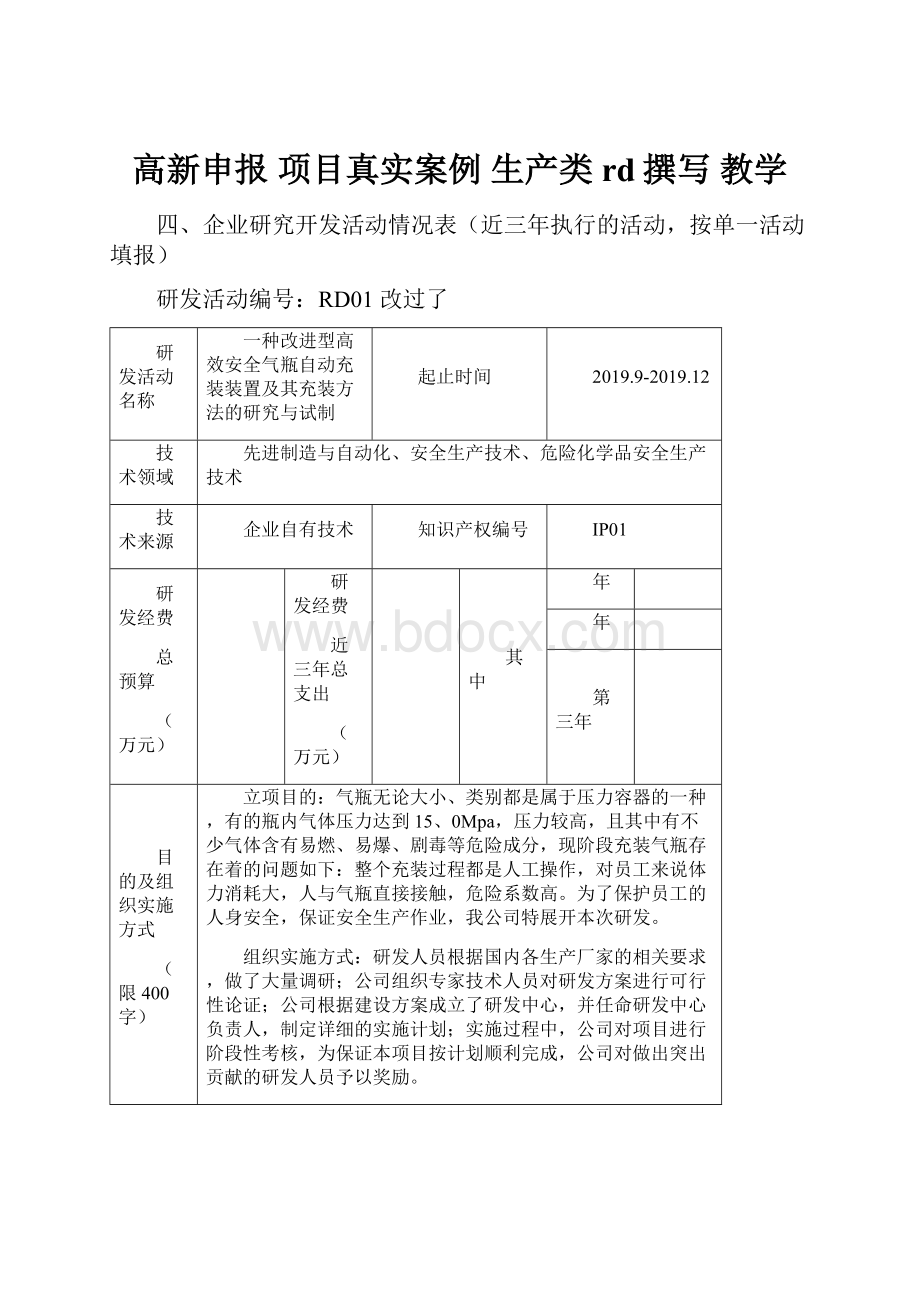
其中
年
第三年
目的及组织实施方式
(限400字)
立项目的:
气瓶无论大小、类别都是属于压力容器的一种,有的瓶内气体压力达到15、0Mpa,压力较高,且其中有不少气体含有易燃、易爆、剧毒等危险成分,现阶段充装气瓶存在着的问题如下:
整个充装过程都是人工操作,对员工来说体力消耗大,人与气瓶直接接触,危险系数高。
为了保护员工的人身安全,保证安全生产作业,我公司特展开本次研发。
组织实施方式:
研发人员根据国内各生产厂家的相关要求,做了大量调研;
公司组织专家技术人员对研发方案进行可行性论证;
公司根据建设方案成立了研发中心,并任命研发中心负责人,制定详细的实施计划;
实施过程中,公司对项目进行阶段性考核,为保证本项目按计划顺利完成,公司对做出突出贡献的研发人员予以奖励。
核心技术及
创新点
本项目属于《高新技术领域》:
二、先进制造与自动化、
(二)安全生产技术、2.危险化学品安全生产技术。
核心技术:
1、光电传感器四用于检测充气奶嘴固定夹具位置和测瓶阀手轮的位置;
2、采用机械设计设计书抓取机械手实现气瓶抓取功能;
3、采用机械设计设计出气瓶旋转定位功能,使能够进一步与自动充装工位契合;
4、充装箱内从上向下依次安装瓶阀开关机构、瓶阀检测充装机构和气瓶旋转机构;
5、瓶阀开关机构包括开关瓶阀电机、扭矩传感器和瓶阀卡具,开关瓶阀电机安装在充装箱内壁上。
创新点:
1、通过设计滑块,钳口夹紧气瓶,替代人工进行气瓶抓取,提高了效率;
2、通过PLC控制器控制升降驱动机构和气瓶旋转机构工作,控制充装箱下降的同时带动气瓶旋转,到达设定位置后,瓶阀检测充装机构检测纠正瓶阀的朝向,避免了员工长时间处于危险环境中。
取得的
阶段性成果
本项目取得的阶段性成果如下:
1、本项目于2019年9月经公司开始开发,于2019年12月结束,历时3个月,成功研发出了该项目,并取得了预期成果。
2、该项成果采用PLC自动化配制,实现自动充装,充装人员在气体充装过程中得到隔离,避免充装气体发生危险时对充装人员的伤害,其次减轻了人员的劳动强度,大大节省劳动力。
3、该项目的成功研发应用了我公司原有发明专利1项,专利名称:
XXXXXX,专利号:
XXXX。
RD02
气瓶散装格悬臂吊的研究开发
2019.12-2020.8
在智能气体充装工序中,首先要将集装格中连同其中的气瓶运送到指定的位置,再取出气瓶,充装气体。
现在有技术中只有单独运送气瓶的装置,缺少运送集装格的设备,不但效率低,而且存在一定的危险性,为了提高效率以及保证工作安全,进而开展该项目。
为保证本项目的顺利实施,公司任命项目总工程师,然后项目由总工程师进行指挥管理,然后协调项目研发过程中各项工作;
设立研发中心,研发中心总体进行负责,研发中心负责搜集国内外文献资料,出具立项报告,确定研发方法和技术路线,并进行检测;
财务人员负责公司项目费用预算开支控制。
项目实施过程中实行阶段性考核,确保项目按计划实施,并对做出突出贡献的研发人员给与奖励。
1、该气瓶散装格悬臂吊由回转支撑柱,以及安装在回转支撑柱的顶端的悬壁框架为主要部件构成;
2、悬壁框架上通过螺母、丝杠安装的可以上下移动的升降框架;
3、升降框架通过回转支撑连接吊钩架,升降框架上的动力组件驱动吊钩架。
1、通过升降框架四角安装的丝杠,以及动力组件,将集装格进行自动化运输,可以替代人工进行气瓶搬运,提高了工作效率;
2、通过悬壁框架上安装的伸缩组件,实现了运送集装格功能,一次可以运送多个气瓶,实现智能充装的气瓶输送功能,提高工作的安全性。
1、本项目于2019年12月经公司批准立项开发,于2020年8月结束,历时8个月,项目按计划顺利完成并取得了相应的阶段性成果。
2、针对目前液体气瓶均没有装卸功能,气瓶装卸过程完全依靠人力完成,费时费力,且存在气瓶倾倒砸伤操作人员的安全风险,开发出一种气瓶散装格悬臂吊,吊钩架两侧有滑轨,滑轨上有滑块,动铁芯的顶部设置有向外延伸的限位圈,实现了运送集装格功能,一次可以运送多个气瓶,实现智能充装的气瓶输送功能,提高输送效率。
3、我公司研发出气瓶散装格悬臂吊,可以更加高效的搬运气瓶,该研发成果为公司带来了可观的经济效益和社会效益。
RD03
氩气、二氧化碳混合气体智能充装设备的研究开发
2019.12-2020.7
IP02
在现有技术中,氩气和二氧化碳混合气体充装流程按照应用要求比例混合充装在钢瓶内,传统的充装设备采用人工完成,劳动强度大、准确率低,充装后存在产品合格率偏低,危险性也极大,我公司因此进行氩气、二氧化碳混合气体智能充装设备的研究开发。
为了保证氩气、二氧化碳混合气体智能充装设备项目的顺利实施,公司成立研发中心,进而开展工作,协调项目研发过程中各项工作,研发中心总体负责。
研发中心负责搜集国内外文献资料,出具立项报告,确定研发方法和技术路线,并进行检测;
财务办公司负责项目费用预算开支控制。
项目实施过程中实行阶段性考核,确保项目按计划实施,通过设立奖励制度对。
1、该充装设备包括氩气充装管道、二氧化碳气充装管道,连通氩气源与氩气充装管道的进气口;
2、二氧化碳气源连通二氧化碳气充装管道的进气口,氩气充装管道的出气口和二氧化碳气充装管道的出气口相连;
3、氩气充装管道有二个分路,每个分路各有一个控制阀,每个分路的出气口各连接一个二氧化碳气充装管道出气口和汇流排;
4、汇流排上安装压力传感器,氩气控制阀、二氧化碳气控制阀和压力传感器连接控制器。
该设备利用控制系统压力传感器检测到的钢瓶剩余压力,然后根据PLC数据库自动计算出氩气和二氧化碳气分别需要充装的压力、速度和时间,实现智能切换相应控制阀门进行充装,代替人工操作,提高效率和准确率。
1、本项目于2019年12月经公司批准立项开发,于2020年7月结束,历时7个月,项目按计划顺利完成并取得了相应的阶段性成果。
2、针对目前氩气和二氧化碳混合气体充装过程中存在的效率和安全问题,开发出一种氩气、二氧化碳混合气体智能充装设备,通过氩气充装管道有二个分路,每个分路各有一个控制阀,每个分路的出气口各连接一个二氧化碳气充装管道出气口和汇流排,避免了人工直接接触,降低了劳动强度,又从而提高了产品的合格率。
3.该项目成果已获得实用新型专利1项,专利名称:
XXXX,专利号:
XXXX,专利权人:
XXXX。
RD04
用于散装和集装的钢瓶格的研究开发
2019.12-2020.6
IP03
气瓶装载框主要用于装运高压气体钢瓶,现有钢瓶格底座是固定的,在散装或集装时只能横向移动单个钢瓶,无法实现多个钢瓶的竖向移动,不能适应气瓶智能化充装方式,搬运效率低,会发生倾倒等危险情况。
该研发项目采用由我公司单独研发设计,公司任命项目总工程师,项目由总工程师指挥管理,协调项目研发过程中各项工作,研发中心总体负责。
1、该钢瓶格包括底部框架和框架周围的立柱,其中框架的一面铰接围板;
2、框围板两侧利用扣合件与相邻立柱实现可拆卸连接,框架的其它面上方安装横杆,横杆两端固定在两立柱上;
3、托板底面的四角各安装了一圆柱,其中框架内侧固定多个V形槽。
1、托板与框架可拆卸,由升降装置带动托板上下移动,从而带动托板上的多个钢瓶移动,以适应智能充装方式;
2、底部框架设计可活动底板,而且底板设计一定的倾斜经过设计可保证气瓶定期后不倾倒和剩余气瓶不倾倒,保证气瓶的安全性,保护工人操作安全。
1、本项目于2019年12月经公司批准立项开发,于2020年6月结束,历时6个月,项目按计划顺利完成并取得了相应的阶段性成果。
2、针对现有气瓶装载框主要用于装运高压气体钢瓶,目前的装运的效率低且存在倾倒及碰撞的险情,采用理论与实践相结合的研究方式,开发出一种用于散装和集装的钢瓶格,立柱顶端固定挂钩,方便自动充装系统吊装,框架底板上设有多个可拆卸的托板,每块托板上可载5只气瓶,相对应的托板可由外部升降机构将一排5只气瓶同时升起和降落,提高了搬运气瓶的效率。
3、应用该项目成果,我公司对原有生产技术进行了改造升级,产品推入市场后便得到广大用户的喜爱和青睐,为公司带来了可观的经济效益和社会效益。
4、该项目成果已获得实用新型专利1项,专利名称:
XXXX,申请号:
RD05已修改
称重法智能气体充装系统的研究与设计
2020.7-2020.12
液化气体一般采用称重法进行气体充装,存在充装压力高、易燃、易爆、剧毒等风险,且气瓶属压力容器,存在充装破裂风险,现阶段液化气体充装存在着的问题如下:
整个充装过程都是人工操作,对员工来说体力消耗大,人与气瓶直接接触,危险系数高,需要自动充装设备替代人式操作。
为保护操作工人的人身安全,我公司决定展开该项目的研究。
1、研发人员对项目相关内容进行市场调研,提出试验方案。
2、公司组织有关生产、技术、市场等人员对方案进行研讨论证,完善并批准方案。
3、成立项目研发中心,由项目研发中心负责人分配项目各项工作,进行方案细化并实施。
4、研发中心主任负责对该项目实施过程进行全程监督检查,至最终完成研发。
1.该气体充装系统包括带有滑轨的工位框架、行走框架和充装工位框架。
2.工位框架上有同步带,同步带驱动行走框架移动。
3.行走框架内有气瓶夹紧组件和底部的安装电子秤的气瓶托盘。
4.充装工位框架内有可上下移动且带有手轮开关充装框架,手轮开关下方安装瓶阀充装组件。
1.通过设计手轮开关卡紧气瓶的手轮,瓶阀充装组件夹紧瓶阀,手轮开关拧开手轮,气瓶夹紧组件向气瓶中充装气体并称重,充装结束后,手轮开关关闭手轮,手轮开关和气瓶夹紧组件松开并上升,行走框架移动到工位框架后端。
2.通过位框架、行走框架和充装工位框架等实现自动充装、称重、输送,完全替代人工操作,在提高充装效率的同时,还保障了操作工人的人身安全。
1、本项目于2020年7月经公司批准立项开发,于2020年12月结束,历时5个月,项目按计划顺利完成并取得了相应的阶段性成果。
2、针对目前整个充装过程都是人工操作,对员工来说体力消耗大,因此开发出一种称重法智能气体充装系统,充装工位框架上有电动机,电动机带动丝杠转动,丝杠上有螺母,螺母安装在充装框架上,实现自动充装、称重、输送,完全替代人工操作,安全,效率高。
3、应用该项目成果,我公司设计了一套自动化智能气体充装设备,解决了目前人与气瓶直接接触危险大的问题,提高了工人的安全系数,也间接的为公司节约了成本。
4.该项目成果目前已申请实用新型专利1项,专利名称:
XXXX,申请人:
RD06已修改
一种气瓶充装卡具的研究开发
现阶段充装气瓶存在着的问题如下:
整个充装过程都是人工操作,对员工来说体力消耗大,人与气瓶直接接触,险系数高。
而且人工每次拧紧时,产生的力矩大小不一,容易造成密封不严气体泄漏,或者过度拧紧,破坏密封面从而导致气体泄露,而存储的气体中多数有易燃、易爆、剧毒等危险成分,容易对操作工人造成威胁。
为此,我公司决定研发该气瓶充装卡具,以保障工人的工作安全。
公司领导根据公司的发展,进行前期的立项需求分析;
1.该卡具包括电动机、箱体、卡爪、充气奶嘴,电动机通过联轴器连接箱体内的齿轮,箱体内有哦安装在丝杠上的且可前后滑动的底座。
2.从动齿轮安装在副丝杠上,丝杠内部中空,前端连接充气奶嘴,丝杠后端连接充装进气管。
3.底座与箱体之间安装弹簧。
4.卡爪为半圆形,内侧设有与气瓶阀匹配的螺纹,螺纹可以是正丝螺纹,也可以是反丝螺纹。
1、通过底座与箱体之间设有弹簧,可以耐受150atm高压。
2.该卡具能应于各种不同规格的气瓶,自动快速卡紧充气阀,实现了人员与气瓶的隔离,保证操作人员的人身安全,减轻了人员的劳动强度,大大节省劳动力。
1、该项目于2020年7月开始研发,经过5月的努力研发,于2020年12月顺利研发完成,成功研发出了该X,项目如期完成,并取得了预期成果。
2针对目前的气瓶属于压力容器,配气过程存在危险性,而且某些气体含有毒性,也存在一定的危险性,开发出的气瓶充装卡具,能应于各种不同规格的气瓶,自动快速卡紧充气阀,实现了人员与气瓶的隔离,保证操作人员的人身安全,减轻了人员的劳动强度,大大节省劳动力。
3、自项目成果自应用以后,明显减少了气瓶的危险事故,避免气瓶爆炸产生的碎片划伤作业人员的风险,进一步提高了充气过程的安全性。
4.该项目成果已申请实用新型专利1项,专利名称:
XXXX,申请人:
RD07
气瓶水压试验测试快速连接头的研究开发
2020.8-2020.12
目前对气瓶采用外测法水压试验法进行检测,气瓶与管道连接部分,是模仿装卸瓶阀的结构原理,来实现密封后进行水压试验。
整个过程都是人工操作,存在员工体力消耗大,密封不严谨,生料带浪费等缺陷,以及工人工作不安全等问题,为了解决上述问题,进行了该项目的研发。
本项目采用独立研究方式进行研究,公司成立研发中心,由公司总工程师担任项目总指挥,研发中心作为主力部门,其他部门予以配合。
由项目负责人编制各阶段项目实施大纲,研发中心、生产部和其他部门成员根据大纲要求编写详细、切实可行的实施方案,经全体讨论后实施。
项目负责人实时追踪项目完成情况,定期召开总结大会,及时解决出现的问题,确保计划目标的实现。
公司在资金和人员方面为项目的顺利实施提供保障。
1、该快速连接头有中控轴和密闭的壳体为主要部件构成;
2、中控轴的内部贯通,上端连接充水管,下端连接膨胀杆;
3、壳体上端安装上密封件,下端安装了下密封座,其中上密封件安装在中控轴外侧。
1、通过中控轴与密闭的壳体配合,保证了快速连接头的密闭性,从而实现气瓶在检测过程中的安全性;
2、通过壳体上下密封件,不仅可以自动卡紧气瓶螺纹,有效的密封住连接口,还能节省密封生料带,减轻人员的劳动强度,大大节省劳动力。
1、本项目于2020年8月经公司批准立项开发,于2020年12月结束,历时4个月,项目按计划顺利完成并取得了相应的阶段性成果。
2、针对目前气瓶的水压检测操作全由人工观察,操作工的熟练程度、责任心等都会影响到试验的漏检,底部试验状况不能观察出现盲区,因此开发出一种气瓶水压试验测试快速连接头,专用快速接头,上端为专用快速接头锁紧雄头,下端配有专用快速接头对应钢瓶螺纹,专用快速接头对应钢瓶螺纹顶端有配套的专用密封圈,专用快速接头的中部配有借力杆。
通过该结构,方便油缸锁紧装置通过液压传动对专用快速接头进行锁紧,并保证用专用快速接头锁紧后试验瓶瓶口的密封性。
3.该项目成果已申请实用新型专利1项,专利名称:
RD08
液氧制备装置的研究
全液体空分离设备是以空气为原料,通过压缩循环深度冷冻的方法把空气变成液态,再经过精馏而从液态空气中逐步分离生产出液氧、液氮等液态产品的设备,由全液体空分设备生产的液氧产品进入贮罐系统,贮罐系统由于绝热损失,罐内液氧蒸发成氧气。
但是经过多年的实践发现,采用现有技术中常用的空分设备,仍然无法得到更为纯净的液氧,造成很大的浪费。
公司领导为了保证项目的实施,公司专门成立项目开发小组。
由总工程师指挥管理,协调项目研发过程中的各项工作。
项目组负责搜集国内外文献资料,出具立项报告,确定研究方法和技术路线;
财务部负责项目费用预算开支控制;
研发中心、生产、采购部门、综合管理部门配合实施方案。
项目实施过程中实行阶段性考核,确保项目按计划实施,达到设计要求,并对做出突出贡献的研发人员予以奖励。
1、该液氧制备装置包括用于接收预处理装置输出的空气的纯化器、预处理装置和精馏塔;
2、精馏塔包括下塔、上塔两部分;
3、下塔的底部安装用于承接自纯化器纯化后的饱和气体入口;
4、预处理装置包括沿空气的流动方向依序排布设置的空气过滤器、空压机、回热器、冷却器、预冷器。
1、采用纯化器,提高液氧产出量;
2、采用预处理装置,进行深冷分离工艺分离出来的液氧纯度稳定,质量控制在5N及以上;
3、当精馏塔出口温度达60℃时,电控装置自动关掉电加热器,及时进行设备内部的工位转换。
1、本项目于2020年8月经公司批准立项开发,于2020年12月结束,历时12个月,项目按计划顺利完成并取得了相应的阶段性成果。
2、针对目前经过多年的实践发现,通过现有的液氧制造设备仍然无法得到纯净更高的液氧,因此开发出一种液氧制备装置,在吸附筒加热再生时,回热器工作,即三通阀接通去回热器、电加热器加温,而在精馏塔转入吹冷阶段时,纯化器电控柜联锁控制三通阀将再生气直接送入吸附筒吹冷。
这样做是为了在加热阶段,进入电加热器的再生气有较高的温度,以减少电加热器的功率,提高了制氧效率。
3、应用该项目成果,我公司设计的液氧制备设备,可以得到更为纯净的液氧,为公司带来了可观的经济效益和社会效益。
RD09
液氩生产方法及装置研究与开发
先进制造与自动