机械制造工艺学课程设计举例Word下载.docx
《机械制造工艺学课程设计举例Word下载.docx》由会员分享,可在线阅读,更多相关《机械制造工艺学课程设计举例Word下载.docx(22页珍藏版)》请在冰豆网上搜索。
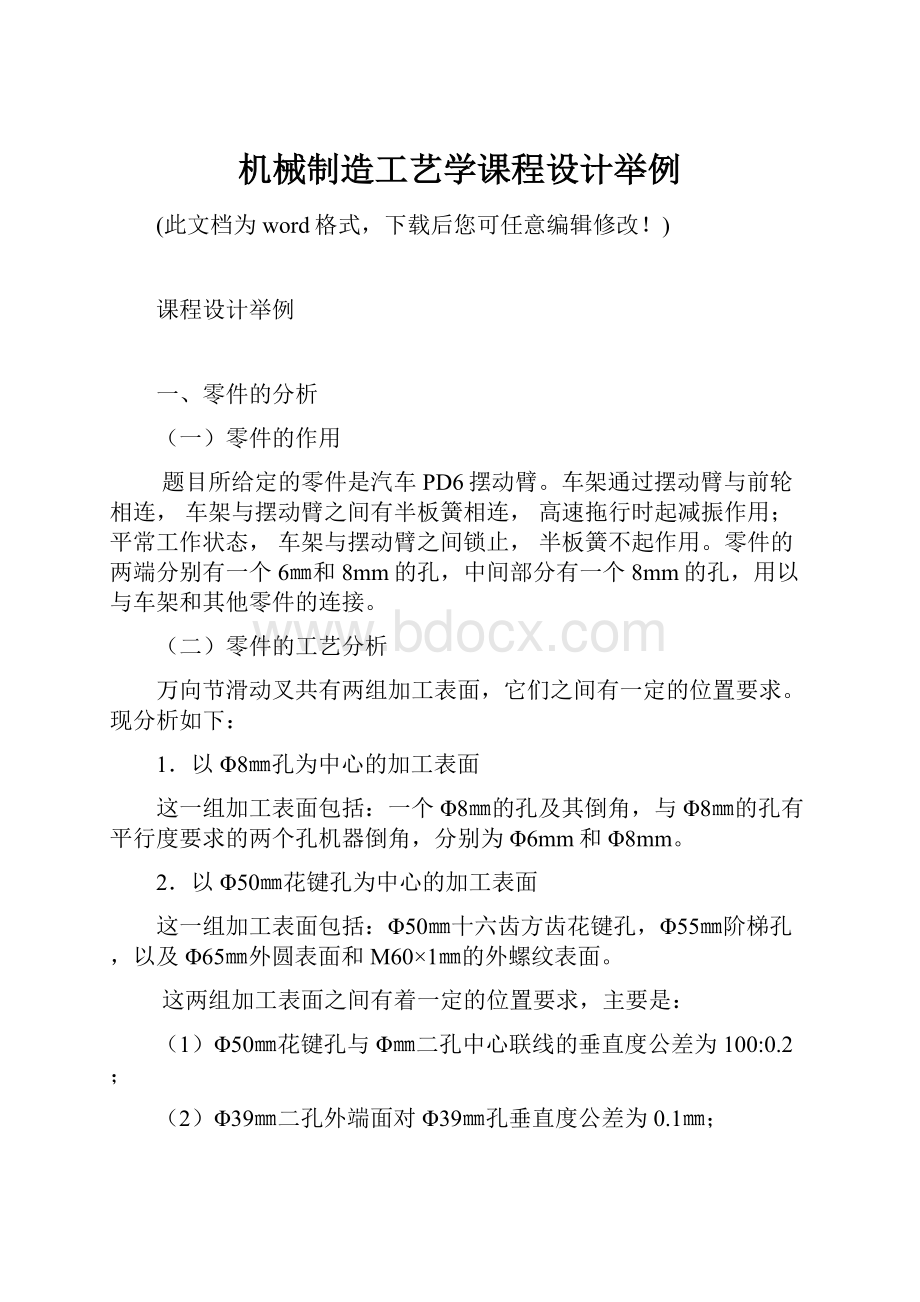
60㎜,车螺纹M60×
1㎜。
工序Ⅱ两次钻孔并扩钻花键底孔Ø
43㎜,锪沉头孔Ø
55㎜。
工序Ⅲ倒角5×
30˚。
工序Ⅳ钻Rc18底孔。
工序Ⅴ拉花键孔。
工序Ⅵ粗铣Ø
39㎜二孔端面。
工序Ⅶ精铣Ø
工序Ⅷ钻、扩、粗铰、精铰两个Ø
39㎜孔至图样尺寸并锪倒角2×
45°
。
工序Ⅸ钻M8㎜底孔Ø
6.7㎜,倒角120°
工序Ⅹ攻螺纹M8㎜,Rc18。
工序Ⅺ冲箭头。
工序Ⅻ检查。
2.工艺路线方案二
工序Ⅰ粗铣Ø
工序Ⅱ精铣Ø
工序Ⅲ钻Ø
39㎜二孔。
(不到尺寸)
工序Ⅳ镗Ø
工序Ⅴ精铣Ø
39㎜二孔,倒角2×
工序Ⅵ车外圆Ø
工序Ⅶ钻、镗孔Ø
43㎜,并锪沉头孔Ø
工序Ⅷ倒角5×
30°
工序Ⅸ钻Rc18底孔。
工序Ⅹ拉花键孔。
工序Ⅺ钻M8㎜底孔Ø
工序Ⅻ螺纹M8㎜,Rc18。
工序ⅩⅢ冲箭头。
工序ⅩⅣ检查。
3.工艺方案的比较与分析
上述两个工艺方案的特点在于:
方案一是先加工以花键孔为中心的一组表面,然后以此为基面加工Ø
39㎜二孔;
而方案二则与此相反,先是加工Ø
39㎜孔,然后再以此二孔为基准加工花键孔及其外表面。
两相比较可以看出,先加工花键孔后再以花键孔定位加工Ø
39㎜二孔,这时的位置精度较易保证,并且定位及装夹都比较方便。
但方案一中的工序Ⅷ虽然代替了方案二中的工序Ⅲ、Ⅳ、Ⅴ,减少了装夹次数,但在一道工序中要完成这么多工作,除了选用专门设计的组合机床(但在成批生产时,在能保证加工精度的情况下,应尽量不选用专用组合机床)外,只能选用转塔车床,利用转塔头进行加工。
而转塔车床目前大多选、用于粗加工,用来在此处加工Ø
39㎜二孔是不合适的,因此决定将方案二中的工序Ⅲ、Ⅳ、Ⅴ移入方案一,改为两道工序加工。
具体工艺过程如下:
粗基准的选择如前所述。
55㎜,以Ø
62㎜外圆为定位基准。
工序Ⅳ钻Rc18锥螺纹底孔。
39㎜二孔端面,以花键孔及其端面为基准。
工序Ⅷ钻孔两次并扩孔Ø
39㎜。
孔至图样尺寸并锪倒角2×
工序Ⅸ精镗并细镗Ø
工序Ⅵ、Ⅷ、Ⅸ的定
位基准均与工序Ⅳ相同。
工序Ⅹ钻M8㎜底孔Ø
工序Ⅺ攻螺纹M8㎜,Rc18。
工序Ⅻ冲箭头。
工序ⅩⅢ检查。
以上加工方案大致看来还是合理的。
但通过仔细考虑零件的技术要求Ø
以及可能采取的加工手段之后,就会发现仍有问题,主要表现在Ø
39㎜两个孔其端面加工要求上。
图样规定:
Ø
39㎜二孔中心线应与Ø
55㎜花键孔垂直,垂直度公差为100:
39㎜二孔与其外端面应垂直,垂直度公差为0.1㎜。
由此可以看出:
因为Ø
39㎜二孔的中心线要求与Ø
55㎜花键孔中心线相垂直,因此,加工及测量Ø
39㎜孔时应以花键孔为基准。
这样做,能保证设计基准与工艺基准相重合。
在上述工艺路线制订中也是这样做了的。
同理,Ø
39㎜二孔与其外端面的垂直度(0.1㎜)的技术要求在加工与测量时也应遵循上述原则。
但在已制订的工艺路线中没有这样做:
39㎜孔加工时,以Ø
55㎜花键孔定位(这是正确的);
而Ø
39㎜孔的外端面加工时,也是以Ø
55㎜定位的。
这样做,从装夹上看似乎比较方便,但却违反了基准重合的原则,造成了不必要的基准不重合误差。
具体来说,当Ø
39㎜二孔的外端面以花键孔为基准加工时,如果两个端面与花键孔中心线已保证绝对平行的话(这是很难的)。
那么由于种种原因Ø
39㎜二孔中心线与花键孔仍有100:
0.2的垂直度公差,则Ø
39㎜孔与其外端面的垂直度误差就会很大,甚至会造成超差而报废。
这就是由于基准不重合而造成的恶果。
为了解决这个问题,原有的加工路线可仍大致保持不变,只是在Ø
39㎜二孔加工完了以后,再增加一道工序:
以Ø
39㎜孔为基准,磨Ø
39㎜二孔外端面。
这样做,可以修正由于基准不重合造成的加工误差,同时也照顾了原有的加工路线中装夹较方便的特点。
因此,最后的加工路线确定如下:
工序Ⅰ车端面及外圆Ø
60㎜并车螺纹M60×
以两个叉耳外轮廓及Ø
62㎜外圆为粗基准,选用C620-1我式车床并加专用夹具。
工序Ⅱ钻、扩花键孔Ø
62㎜外圆为基准,选用C365L转塔车床。
工序Ⅲ内花键孔5×
30˚倒角。
选用C620-1车床加专用夹具。
工序Ⅳ钻锥螺纹Rc18底孔。
选用Z525立式钻床及专用钻模。
这里安排钻Rc18底孔主要是为了下道工序拉花键孔时为消除回转自由度而设置的一个定位基准。
本工序以花键内底孔定位,并利用叉部外轮廓消除回转自由度。
利用花键内底孔、Ø
55㎜端面及Rc18锥螺纹底孔定位,选用L6120卧式拉床加工。
39㎜二孔端面,以花键孔定位,选用X63卧式铣床加工。
工序Ⅶ钻、扩Ø
39㎜二孔及倒角。
以花键孔及端面定位,选用Z535立式钻床加工。
工序Ⅷ精、细镗Ø
选用T740型卧式金刚镗床及专用夹具加
工以花键内孔及其端面定位。
工序Ⅸ磨Ø
39㎜二孔端面,保证尺寸㎜,以Ø
39㎜孔及花键孔定
位,选用M7130平面磨床及专用夹具加工。
工序Ⅹ钻叉部四个M8㎜螺纹底孔并倒角。
选用Z525立式钻床及专用夹具加工,以花键孔及孔Ø
39㎜定位。
工序Ⅺ攻螺纹4-M8㎜及Rc18。
以上工艺过程详见附表1“机械加工工艺过程卡片”。
三、夹具设计
为了提高劳动生产率,保证加工质量,降低劳动强度,需要设计专用夹具。
(一)问题的提出
本夹具主要用来粗铣Ø
39mm二孔的两个端面,这两个端面对¢39㎜孔及花键都有一定的技术要求。
但加工本道工序时,Ø
39㎜孔尚未加工,而且这两个端面在工序Ⅸ还要进行磨加工。
因此,在本道工序加工时,主要应考虑如何提高劳动生产试验率,降低劳动强度,而精度则不是主要问题。
(二)夹具设计
1.定位基准的选择
由零件图可知,Ø
39m二孔端而应对花键孔中心线有平行度及对称度要求,其设计基准为花键孔中心线。
为了使位误差为零,应该选择以花键定位的自动定心夹具。
但这种自动定心夹具在结构上将过于复杂,因此这里只选用以花键孔定位的自动定心夹具。
但这种自动定心夹具在结构上将过于复杂,因此这里选用以花键孔为主要定位基面。
为了提高加工效率,现决定用两把镶齿三面刃铣刀对两个Ø
39㎜孔端面同时进行加工。
同时,为了缩短辅助时间,准备采用气动夹紧。
2.切削力及夹紧力计算
刀具:
高速钢镶齿三面刃铣刀,Ø
225㎜,Z=20
(见《切削手册》表3.28)
其中:
=650,=3.1㎜,=1.0,=0.08㎜,=0.72,=40㎜,(在加工面上测量的近似值)=0.86,=225㎜,=0.86,=0,z=20
∴F=
=1456(N)
当用两把刀铣削时,=2F=2912(N)
水平分力:
=1.1=32.3(N)
垂直分力:
=0.3=873(N)
在计算切削力时,必须把安全系数考虑在内。
安全系数K=。
为基本安全系数1.5;
为加工性质系数1.1;
为刀具钝化系数1.1;
为断续切削系数1.1。
∴=K=1.5×
1.1×
3203=6395(N)
选用气缸一斜一斜楔夹紧机构,楔角a=10˚,其结构形式选用Ⅳ型,则扩力比i=3.42。
为克服水平切削力,实际加紧力N应力
N(+)=K
∴N=
其中及为夹具定位面及加紧面上的摩擦系数,==0.25。
则
N==12790(N)
气缸选用Ø
100㎜。
当压缩空气单位压力P=0.5Mpa时,气缸推力为390N。
由于已知斜楔机构的扩力比i
=3.42,故由气缸产生的实际夹紧力为
=3900i=3900×
3.42=13338(N)
此时N气已大于所需的12790的夹紧力,故本夹具可安全工作。
3.定位误差分析
(1)定位元件尺寸及公差的确定。
夹具的主要定位元件为一花键轴,该定位花键轴的尺寸与公差现规定为本零件在工作时与其相配花键的尺寸相同,即16×
43H11×
50H8×
5H10㎜。
(2)零件图样规定Ø
50㎜花键孔键槽宽中心线与Ø
㎜两孔中心线转角公差为2˚。
由于Ø
39㎜孔中心线应与其外端面垂直,故要求Ø
39㎜二孔端面之垂线应与Ø
50㎜花键槽宽中心线角公差为2º
此项技术要求主要应由花键槽宽配合中的侧向间隙保证。
已知花键孔键槽宽为㎜,夹具中定位花键轴键宽为5㎜,因此当零件安装在夹具中时,键槽处的最大侧向间隙为
△=0.048-(-0.065)=0.113(㎜)
由此而引起的零件最大转角a为
tga==0.00452
所以a=0.258˚
即最大侧隙能满足零件的精度要求.
(3)计算Ø
39㎜二孔外端面铣加工后与花键孔中心线的最大平行度误差。
零件花键孔与定位心轴外径的最大间隙为:
=0.048-(-0.083)=0.131(㎜)
当定位花键轴的长度取100㎜时,则由上述间隙引起的最大倾角为0.131100。
此即为由于定位问题而引起的Ø
39㎜孔端面对花键孔中心线的最大平行度误差。
39㎜孔外端面以后还要进行磨削加工,故上述下平行度误差值可以允许。
4.夹具设计及操作的简单说明
如前所述,在设计夹具时,应该注意提高劳动生产率。
为此,应首先着眼于机动夹紧而不采用手动夹紧。
因为这是提高劳动生产率的重要途径。
本道工序的铣床夹具就选择了气动夹紧方式。
本工序由于是粗加工。
因此,应首先设法降低切削力。
目前采取的措施有三:
一是提高毛坯的制造精度,使最大切削深度降低,以降低切削力;
二是选择一种比较理想的斜楔夹紧机构,尽量增加该夹紧机构的扩力比;
三是在可能的情况下,适当提高压缩空气的工作压力(由0.4Mpa增至0.5Mpa),以增加气缸推力。
结果,本来具总的感觉还比较紧凑。
夹具上装有对刀块,可使夹具在一批零件的加工之前很好地对刀(与塞尺配合使用);
同时,夹具体底面上的一对定位键可使整个机床工作台上有一正确的安装位置,以利于铣削加工。
附表1机械加工工艺过程综合卡片
东北林业大学
零件号
材料
45钢
编制
(日期)
机械加工工艺过程综合卡片
零件名称
万向节滑动叉
毛坯重量
6㎏
指导
生产类型
大批生产
毛坯种类
模锻件
审核
工序
安装
工位
工步
工序说明
工序简图
机
床
夹具或辅助工具
刀
具
量
走
刀
次
数
长
度
(㎜)
切
削
深
进
给
(㎜r)
主
轴
转
速
(rmin)
(mmin)
工时定额(min)
基
本
时
间
辅
助
工作地服务时间
Ⅰ
1
2
3
4
5
粗车端面至Ø
30mm,保证尺寸185㎜
粗车Ø
62mm外圆
车Ø
60mm外圆
车M60×
1㎜螺纹
粗车螺纹
精车螺纹
卧
式
车
床L620-1
专
用
夹
YT15外圆车刀
W18Cr4V
螺纹车刀
卡
板
螺
纹
规
17.5
94
24
18
1.5
0.17
0.08
0.5
600
770
96
184
122
145
34
0.096
0.31
0.06
0.75
0.18
Ⅱ
钻、扩花键底孔
43mm及锪沉头孔Ø
55mm
钻孔Ø
25mm
41mm
扩花键底孔Ø
43mm
锪圆柱式沉头孔Ø
塔
C365L
麻花钻
25㎜
41㎜
扩孔钻
43㎜
锪钻
55㎜
尺
164
159
154.5
10
12.5
8
6
0.41
0.76
1.24
0.21
136
58
44
10.68
7.47
7.7
8.29
3.55
2.14
1.08
Ⅲ
43mm内孔倒角5×
C129-1
样
120
16.2
0.83
东北林业大学
Ⅳ
钻锥螺纹Rc18底孔
(Ø
8.8㎜)
立
钻
Z525
专用夹具
麻花
钻头
8.8㎜
4.4
0.11
680
18.8
0.24
Ⅴ
拉花键孔16×
5H10㎜
拉
床L6120
专用
夹具
花键
拉刀
量规
0.06㎜齿
3.6
0.42
Ⅵ
粗铣Ø
39㎜两孔端面,保证尺寸㎜
铣
X63
高速钢镶齿三面刃铣刀
225㎜
卡板
105
3.1
60㎜min
37.5
26.5
1.75
Ⅶ
钻、扩Ø
39㎜二孔及倒角
扩钻Ø
37㎜
扩孔Ø
38.7㎜
倒角
2×
Z535
90°
62
56
50
0.85
0.25
0.57
0.72
195
68
15.3
7.9
8.26
1.27
1.44
1.02
Ⅷ
精镗、细镗Ø
39㎜二孔
精镗孔Ø
38.9㎜
细镗孔Ø
39㎜
金
刚
镗
床T740
YT30
镗刀
塞
52
0.1
0.05
816
100
0.64
Ⅸ
磨Ø
磨上端面
磨另一端面
平
面
磨
M7130
砂轮
WA46KV6P
350×
40×
127
73
27.5ms
3.64
Ⅹ
钻螺纹低孔4—Ø
6.7㎜并倒角
钻孔2—Ø
6.7㎜
锪钻
120°
23
3.35
960
20.2
0.48
Ⅺ
攻螺纹4—M8及Rc18
攻螺纹2—M8
攻Rc18
M8丝锥
Rc18
丝