设备状态监测与故障诊断作业070赵洪乐讲解Word文档格式.docx
《设备状态监测与故障诊断作业070赵洪乐讲解Word文档格式.docx》由会员分享,可在线阅读,更多相关《设备状态监测与故障诊断作业070赵洪乐讲解Word文档格式.docx(15页珍藏版)》请在冰豆网上搜索。
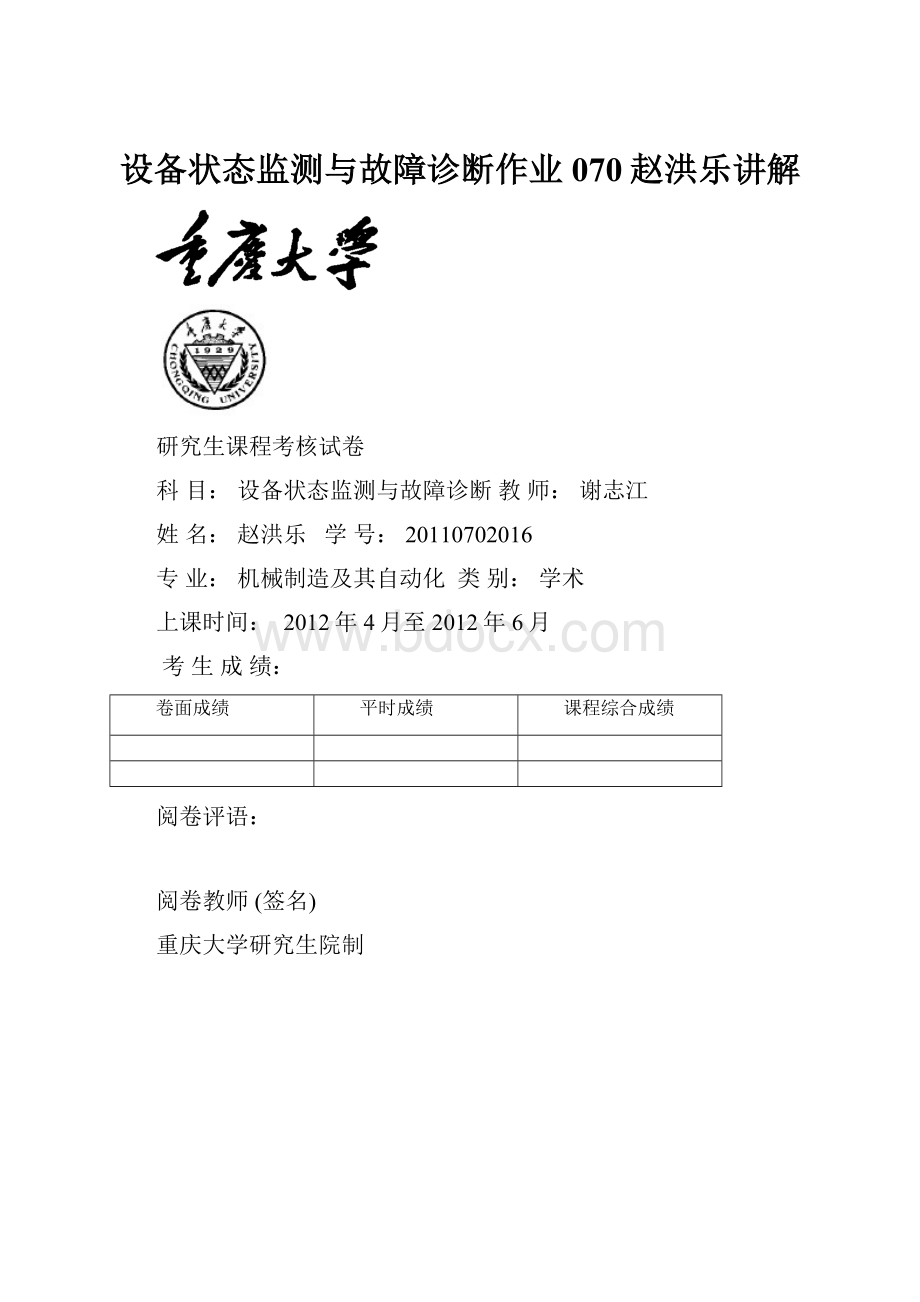
1.齿轮啮合频率产生的机理
齿轮啮合频率(GearMeshFrequency)等于该齿轮的转频(转每秒或Hz)乘以它的齿数。
相互啮合的两个齿轮的啮合频率是相等的。
即
,
因此,齿轮的振动机理与信号特征分析如下:
齿轮传动系统是一个弹性的机械系统,由于结构和运动关系的原因,存在着运动和力的非平稳性。
当齿轮副只有一个啮合点时,随着啮合点沿啮合线移动,从动轮的角速度存在波动;
当有两个啮合点时,因为只能有一个角速度,因而在啮合的轮齿上产生弹性变形力,这个弹性变形力随啮合点的位置、轮齿的刚度以及啮合的进入和脱开而变化,是一个随时间变化的力。
同理,即使主动轮传递的是一个恒转矩,在从动轮上仍然产生随时间变化的啮合力和转矩。
而且单个轮齿可看成是变截面悬臂梁,啮合齿轮对的综合刚度也随啮合点的变化而改变,这就造成轮齿振动的动力学分析更加复杂。
因此,齿轮传递系统的啮合振动是不可避免的。
振动的频率就是啮合频率,也就是齿轮的特征频率,其计算公式如下:
齿轮啮合频率:
啮合频率的高次谐波频率:
=2,3,4,…,n
式中:
------齿轮轴的转速(r/min)
-------齿轮的齿数
齿轮啮合频率的产生原因主要有:
(1)齿轮啮合过程中齿上所承受载荷的变化及齿轮啮合处刚度的变化
随着啮合点位置的变化,参加啮合的单一轮齿的刚度发生了变化,参加啮合的齿数在变化。
例如对于重合系数在1-2之间的渐开线直齿轮,在节点附近是单齿啮合,在节线两侧某部位开始至齿顶、齿根区段为双齿啮合。
显然,在双齿啮合时,整个齿轮的载荷由两个齿分担,故此时齿轮的啮合刚度就较大;
同理,单齿啮合时啮合刚度较小。
从一个轮齿开始进入啮合到下一个轮齿进入啮合,齿轮的啮合刚度就变化一次。
由此可计算出齿轮的啮合周期和啮合频率。
总的来说,齿轮的啮合刚度变化规律取决于齿轮的重合系数和齿轮的类型。
直齿轮的刚度变化较为陡峭,而斜齿轮或人字齿轮刚度变化较为平缓,较接近正弦波。
若齿轮副主动轮转速为
、齿数为
;
从动轮转速为
,则齿轮啮合刚度的变化频率(即啮合频率)为:
(2)节点附近的力方向和运动方向的变化
主动轮与从动轮在啮合线区域任意S点啮合时它们在该点的绝对速度分别是
和
。
由啮合原理可知,
沿法线方向的速度分量应相等,即:
显然,在该点处主动轮和从动轮之间没有相对滑动。
在啮合线区域,主动轮和从动轮的相对运动是从动轮齿廓沿主动轮齿廓向主动轮的齿根处滑动,摩擦力方向与运动方向相反,指向齿根的齿廓切线方向。
2.齿轮故障诊断方法分析如下
(一)、常见齿轮故障
(1)轮齿的断裂
齿轮副在啮合传递运动时,主动轮的作用力和从动轮的反作用力都通过接触点分别作用在对方轮齿上,最危险的情况是接触点某一瞬间位于轮齿的齿顶部,此时轮齿如同一个悬臂梁,受载后齿根处产生的弯曲应力最大,若因突然过载或冲击过载,很容易在齿根处产生过载断裂。
即使不存在冲击过载的受力工况,当轮齿重复受载后,由于应力集中现象,也易产生疲劳裂纹,并逐步扩散,致使轮齿在齿根处产生疲劳断裂。
对于斜齿轮或宽直齿齿轮,也常发生轮齿的具备断裂。
另外,淬火列了、磨削裂纹和严重磨损后齿厚过分减薄时,在轮齿的任意部位都可能产生裂纹。
(2)齿面磨损
齿轮传动中润滑不良、润滑油不洁或热处理质量差等,均可造成磨损或划痕,磨损可分为粘着磨损、磨粒磨损、划痕(一种很严重的磨粒磨损)和腐蚀磨损等。
1)粘着磨损是油膜被破坏而发生齿面金属的直接接触形成的。
其原因可能是齿轮工作在低速、重载、高温、润滑油黏度太低、供油不足和齿面粗糙等情况。
2)磨粒磨损和划痕当润滑油不洁(夹杂直径大于30um以上的磨粒,包括外来砂粒或摩擦过程中产生的金属磨屑),都可以产生磨粒磨损与划痕。
一般齿顶、吃根部摩擦较节圆部严重,这是因为吃了啮合过程中,节圆处为滚动接触,而齿顶、齿根处为滑动接触。
3)腐蚀磨损润滑油中含有酸、碱和水等易对金属产生腐蚀的化学物质,与齿面发生化学反应,由腐蚀导致齿面损伤。
齿轮磨损后,齿的厚度变薄,齿廓形状变得瘦长。
齿轮磨损后,工作时产生动载荷,不仅振动和噪声加大,而且可能导致齿的折断。
(3)齿面疲劳(点蚀、剥落)
所谓齿面疲劳主要包括齿面点蚀与剥落。
造成点蚀的原因,主要是由于工作表面的交变应力引起的微观疲劳裂纹,润滑油进入裂纹后,由于啮合过程可能先封闭入口然后挤压,微观疲劳裂纹内的润滑油在高压下使裂纹扩展,结果小块金属从齿面脱离,留下一个小坑,形成点蚀。
如果表面的疲劳裂纹扩展的较深、较远或一系列小坑由于坑间材料失效而连接起来,造成大面积或大块金属脱落,这种现象叫剥落。
剥落与严重点蚀只有程度上的区别,而无本质上的不同。
实验表明:
在闭式齿轮传动中,点蚀是最普遍的破坏形式。
在开式齿轮传动中,由于润滑不够充分,以及进入的污物增多,磨粒磨损总是先于点蚀破坏。
(4)齿面塑性变形
软齿面齿轮传递载荷过大(或在大载荷冲击下)时,易产生齿面塑性变形。
在齿面间过大的摩擦力作用下,齿面接触应力会超过材料的抗剪强度,齿面材料进入塑性状态,造成齿面金属的塑性流动,是主动轮节圆附近的齿面形成凹沟,从动轮节圆附近的齿面形成凸棱,从而破坏了正确的齿形。
有时可在某些类型从动齿轮的齿面上出现“飞边”,严重时挤出的金属充满顶隙,引起剧烈振动,甚至发生断裂。
(二)、常用齿轮故障诊断方法
(1)功率谱分析法
功率谱分析可确定齿轮振动信号的频率构成和振动能量在各频率成分上的分布,是一种重要的频域分析方法。
振幅谱也能进行类似的分析,但由于功率谱是振幅的平方关系,所以功率谱比振幅谱更能突出啮合频率及其谐波等线状谱成分,而减少了随机振动信号引起的一些“毛刺”现象。
功率谱分析对齿轮的大面积磨损、点蚀等均匀固有有比较明显的分析效果,但对齿轮早期故障和局部故障不敏感,因而应采用其他分析方法。
(2)边频带分析法
边频带出现的机理是齿轮啮合频率
的振动受到了齿轮旋转频率
的调制而产生,边频带的形状和分布包含了丰富的齿面状况信息。
一般从两个方面进行边频带分析:
一是利用边频带的频率对称性,找出
的频率关系,确定是否为一组边频带;
二是比较各次测量中边频带振幅的变化趋势。
根据边频带呈现的形式和间隔,有可能得到以下信息:
1)当边频带间隔为选择频率
时,可能有齿轮偏心、齿距的缓慢周期变化及载荷的周期波动等缺陷存在,齿轮每旋转1周,这些缺陷就重复作用一次,根据选择频率
可判断出问题齿轮所在的轴。
2)齿轮的点蚀等分布故障会在频谱上形成类似a的边频带,但其边频阶数少,而集中在啮合频率及其谐频的两侧,如下图所示
3)齿轮的剥落、齿根裂纹及部分断齿等局部故障会产生特有的瞬态冲击调制,在啮合频率及其两侧产生一系列边频带。
其特点是边频带阶数多而谱线分散,由于高阶边频的互相叠加而使边频带族形状各异(下图)。
严重的局部故障还会使旋转频率fr及其谐波成分的振幅增高。
(3)包络分析法
包络分析法就是提取载附在高频信号上的低频信号,从时域上看,为取时域波形的包络轨迹。
像具有齿轮、轴承等零部件的旋转机械故障诊断常常用到包络分析。
当旋转机械的轴承零部件有点蚀、剥落等损伤类故障时,伴随设备运转这些故障会产生周期性脉冲冲击力,激起设备的各阶固有振动。
选择冲击激起的高频固有振动为研究对象,通过滤波将其从信号中分离出来,然后通过包络检波,提取出载附在其上的与周期脉冲冲击力对应的包络信号,从其强度和频次就可以判断零件损伤的程度和部位。
这种技术称为包络解调,也称为早期故障探测法,它是判断设备零件损伤类故障的一种有效的手段。
(4)小波分析法
小波变换作为一种新的数学理论和方法,己在不少领域得到了广泛的应用。
在振动信号分析中,小波变换属于一种多分辨率的时频分析方法,具有很多优点,为非平稳信号的分析提供了一个有价值的工具。
实际应用中常使用简单方便的二进离散小波变换。
从多分辨率分析的角度上看,小波分解相当于一个带通滤波器和一个低通滤波器,每次分解总是把原信号分解成两个子信号,分别称为逼近信号和细节信号,每个部分还要经过一次隔点重采样。
如此分解N次即可得到第N层(尺度N上)的小波分解结果。
小波变换常以下面3种方法用于齿轮箱运行状态和故障诊断分析:
(1)小波包能量谱进行监测;
(2)边带识别;
(3)奇异点的模极大值及过零点检测。
随着小波分析技术的发展及计算机容量和运算能力的飞速发展,最近人们开始对连续小波变换应用于故障诊断分析。
连续小波变换能为基小波的选择提供很大方便,当己知需检成分的特征时,就可以选取成构造与之对应的基小波,作连续小波变换来揭示这些成分的分布和大小。
小波变换虽然是一种很好的信号分析工具,但它仍然存在下面两个问题:
(1)小波变换分析的结果不如傅立叶变换那样直观明了,需要分析人员具有一定的小波分析理论基础进行判断,不宜于使用计算机对结果进行自动分析和处理。
(2)小波变换的核函数不是唯一确定的,需要根据工程应用中的实际进行选择。
二、滚动轴承故障的特征频率推导计算
方法1:
设外圈和内圈滚道上分别有一接触点A和B,如果径向游隙为零,则A和B点的圆周速度分别为:
、
—接触点处圆周速度,mm/s
—接触点处直径,mm
—外圈、内圈的转速,r/min
由图可见
滚动体围绕轴承中心线的公转线速度是
速度的平均值,即
滚动体的公转线速度也就是保持架中心圆的线速度。
保持架中心圆上某一点的线速度为:
由上面两式得保持架的转速为:
内圈相对于保持架的转速为:
外圈相对于保持架的转速为
滚动体的自转转速
可由接触点处两物体线速度相等的关系求得。
例如,滚动体与内圈接触的B点线速度为:
式中负号,表示滚动体与内圈接触点B的选择方向相反。
内圈滚道上与滚动体接触的B点相对于滚动体中心的线速度为:
根据纯滚动条件,滚动体上接触点B和内圈滚道上相应的B点速度相等,得到
由此可得滚动体滚动体的自转转速为:
绝大多数滚动轴承在实际应用中总是保持外圈静止,内圈与轴一起旋转,当轴的转速为n时,则
内圈相对于保持架的转速:
因为保持架有z个滚动体,所以内圈上某一点每分钟通过的滚动体数为:
保持架相对于外圈的转速:
外圈上某一点每分钟通过的滚动体数:
滚动体自转速度为:
保持架:
滚动轴承保持架故障频率:
滚动轴承滚动体旋转故障频率:
滚动轴承外环故障频率:
滚动轴承内环故障频率:
以上符号:
d=滚动体直径;
D=滚动轴承平均直径(滚动体中心处直径)
α=径向方向接触角
z=滚动体数目
N=轴的转速。
注:
1.滚动轴承没有滑动;
2.滚动轴承几何尺寸没有变化;
3.轴承外环固定不旋转.
方法2:
经验公式
外环故障频率:
内环故障频率:
保持架故障频率:
3.轴承外环固定不旋转。
三、建立煤气鼓风机状态监测与故障诊断系统,描述其测点布置、系统硬件结构组成(框图)及各部分功能
1.煤气鼓风机故障机理简析
煤气鼓风机等旋转机械的故障常在振动状况方面体现出来,因此根据振动信号进行监测与诊断是目前风机设备维护管理的主要手段,经过多年的发展与完善,煤气鼓风机振动故障诊断已经形成了比较完备的理论与技术体系,总体来说风机的振动故障可能产生于四个方面电机风机本身基础和风管。
其因果分析如下图所示,其中由风机本身原因引起的故障占主导地位。
2.状态监测与故障诊断系统设计
该系统的主要作用是用于采集煤气鼓风机运行中的振动温度和压力等数据,传感器主要有:
加速度传感器、位移传感器、温度感器、压力传感器等。
组成调理电路主要是由电荷放大器、电涡流放大器等组成,工作流程把传感器信号送入调理电路,然后把经调理电路整定后的信号送入数据采集卡,进行转换,然后进入计算机,通过数据采集系统对数据进行处理并上传到数据库服务器。
3.测点布置
设备振动信号是设备异常和故障信息的载体。
选择最佳监测点并采用合适的检测方法是获得有效故障信息的重要条件。
真实而充分地检测到足够数量能客观地反映设备情况的振动信号是监测诊断能否成功的关键。
如果所检测到的信号不真实、不典型或不能客观地充分地暴露设备的实际状态,那么后续的各种功能再完善也等于零。
因此,监测点选择的正确与否关系到能否对故障做出正确的监测和诊断。
一般情况下,监测点数量及方向的确定应考虑的一条总原则是:
能对设备振动状态做出全面描述;
尽可能选择机器振动的敏感点,离机器核心部位最近的关键点和容易产生劣化现象的易损点。
监测点的选择应考虑环境因素,避免选择高温、高湿度、出风口和温度变化剧烈的地方作为监测点,以保证监测的有效性。
从信号频段的角度考虑,对于低频段的确定性振动(常为低频振动)必须同时测量径向的水平和垂直两个方向,有条件时还应增加轴向测量点;
而对于高频的随机振动和冲击振动可以只确定一个方向作为测量点。
这是因为低频信号的方向性强,而高频信号对方向不敏感的缘故。
测轴承的振动时,测量点应尽量靠近轴承的承载区;
与被监测的转动部件最好只有一个界面,尽可能避免多层相隔,以减少振动信号在传递过程中因中间环节造成的能量衰减;
测量点必须要有足够的刚度,轴承座和侧面是较好的监测点。
监测点也不是越多越好,要以最少的传感器,最灵敏地测出整个机组系统的工况,确定必不可少的监测点。
这就需要对整个机组的结构特性作全面了解和分析。
监测点一经确定其位置一定要固定不变,如果发生偏移,监测值的离散度在高频时将达到好几倍。
下图为煤气鼓风机测量点布置示意图:
4.系统硬件结构组成(框图)及各部分功能
硬件组成:
(1)传感器。
选择量程50g,频响1.2~4000HZ的加速度传感器。
(2)数据采集器。
由A/D卡、变参数共振解调信号处理箱构成,其中前者主要采集车辆振动、速度等数据,后者主要采集抗混滤波频率设定,放大倍数选择、冲击信号监测等数据。
(3)中心服务器。
中心服务器的关键就是数据库,数据库应选择扩展性良好、支持分布式计算和集群的数据库。
甲骨文公司是世界上最流行的关系数据库系统,它是物理上存放于网络的多个ORACLE数据库,逻辑上可以看成一个单个的大数据库。
需要时只需将该角色授予一个用户或一组用户,这样可以降低安全机制的负担和成本。
(4)硬件连接图。
如图1所示,即将几个加速度传感器分别装在同步齿轮箱需要检测的位置,然后将他们输出的端与第一N路多路开关及第二N路多路开关的输入端联接,其中,第一N路多路开关的输出公共端“COM”与变参数共振解调信号调理箱相连,连接点是第一子系统和第二子系统的同号输入端“IN+”,相对应的,第二N路多路开关的输出公共端“COM”与反号输入端“IN-”联接。
子系统内部接线是:
第一子系统输出端AH0~AH2分别与A/D转换卡的输入端BH0~BH2对应连接;
相对应的,第二子系统的输出端与转换卡的输入端BH3~BH5对应连接。
A/D转换卡的输出端D0~Dn-1
通过总线与主控机的PC1扩展槽连接,最后,主控机通过以太网与服务器连接。