转体桥研究报告DOCWord格式.docx
《转体桥研究报告DOCWord格式.docx》由会员分享,可在线阅读,更多相关《转体桥研究报告DOCWord格式.docx(30页珍藏版)》请在冰豆网上搜索。
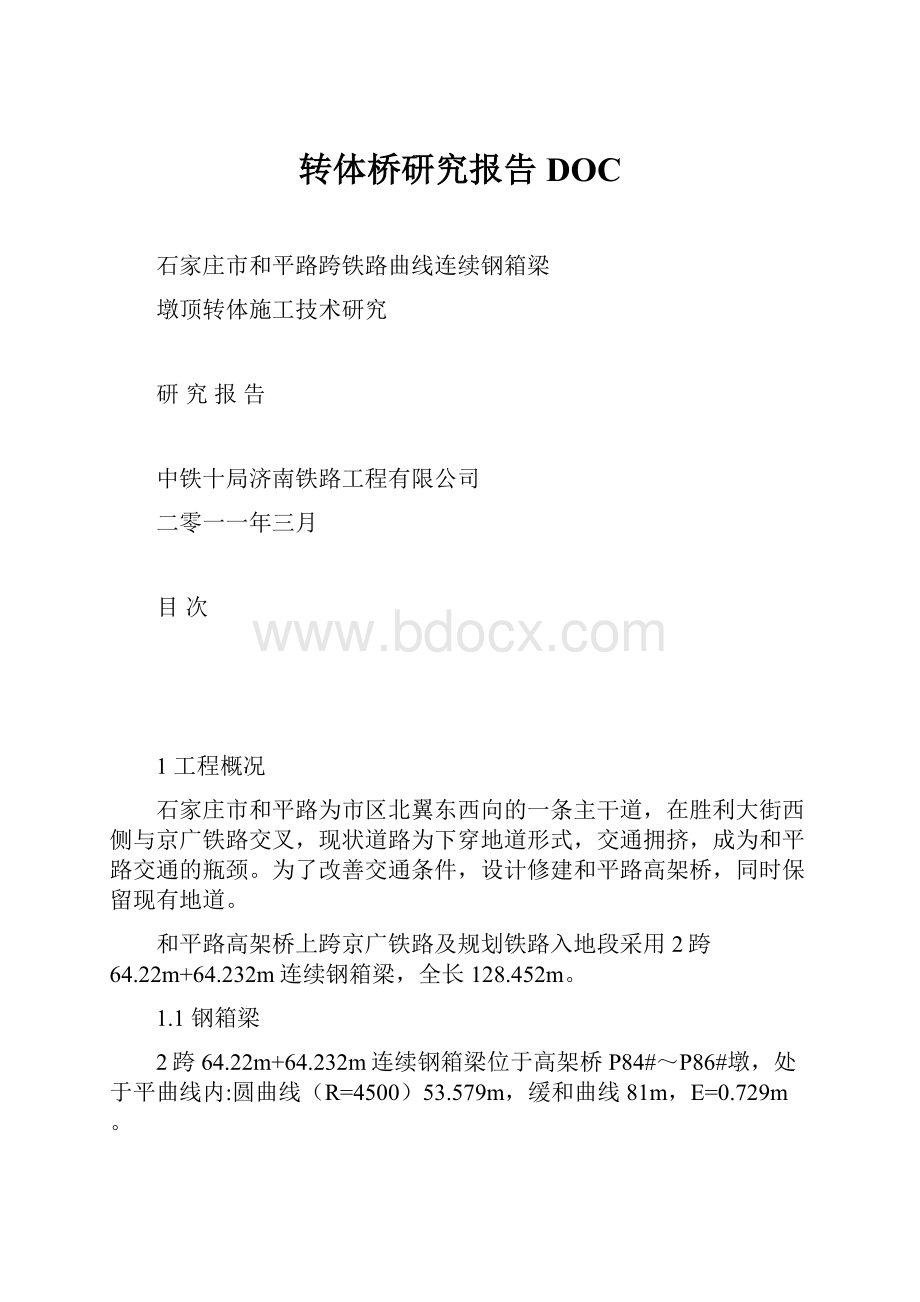
在桥梁转体施工中,为了保证梁体在转动过程中的稳定,通常将转体转心(磨盘)的位置选择在承台顶面与桥墩底之间,将墩梁临时固结后使桥墩与梁同步转体到位。
本工程中,为了适应工程建成后仍保留地面道路的通行要求,桥墩选择了双立柱加盖梁的π型结构,两立柱中心间距14m,跨度较大。
如采用传统的转体方式,转心面积及整体体积势必非常庞大,难以设置,且影响施工期间的桥下临时交通。
为此,将本桥的转体转心(转盘)位置选择在连续梁梁底与盖梁之间,即进行墩顶转体,目前这种桥梁转体方式在国内尚不多见。
2)施工工艺流程:
钢箱梁在既有铁路线东侧沿铁路线路方向进行预拼焊接,而后顺时针转体86°
就位。
具体施工工艺流程见图3
图3连续钢箱梁转体施工工艺流程图
3)转体体系设计概述
钢箱梁转体施工过程中,必须保证桥下铁路线路的安全运营,为此,铁路管理单位经论证后,对钢箱梁转体施工安全提出要求,即转体过程中必须保证结构纵向抗倾覆安全系数达到1.4以上。
而钢箱梁转体时,跨越铁路一侧的悬臂段长度为54.016m,另一侧悬臂段长度为46.959m,两侧相差7.057m,存在较大的纵向不平衡力矩,因此需要设置纵向平衡重(详见2.3节),并采取其它必要措施,在减小纵向不平衡力矩的同时,提高其纵向稳定能力,确保安全系数达到要求。
提高结构整体纵向稳定能力的方法是设置临时索塔和斜拉索对悬臂结构进行斜拉(详见2.4节),同时在短悬臂端设置稳定支腿及其支撑体系和辅助滑道系统(详见2.3节)。
由于钢箱梁在平面上处于圆曲线加缓和曲线(R=4500m,L=53.579m,L0=81m,E=0.729m)上,故整个结构存在横桥向的扭矩作用,因此需要设置横向平衡重(详见2.3节),以减小这种扭矩作用,提高转体结构的横向稳定性。
因采用墩顶转体方式,盖梁做成直径8.4m圆盘形式,故转体动力设备也考虑设置在墩顶(详见2.5节)。
钢箱梁转体结构由中心转盘、平衡重、稳定支腿和辅助滑道、临时索塔和斜拉索、转体动力设备等组成(见图4)
图4转体结构立面示意图(单位:
米)
2.2中心转盘(支座)
中心转盘(支座)采用转盘与永久支座合为一体的特殊型式。
下部为钢制球形中心支座,由下支座板、球面四氟板、球冠钢衬板、平面四氟板、不锈钢滑板和上支座板组成;
上支座板兼作转盘的底盘,上垫平面四氟板,水平转动钢板与上支座板通过中心定位钢销限位,并用螺栓与钢箱梁底部联结(图5)。
支座设计承载能力3000t。
1)钢箱梁在制造厂内加工时,安装好带套筒的支座上垫板。
2)在盖梁顶浇筑支座混凝土,并预埋好带螺栓套筒的支座下垫板,
3)下垫板与下支座板、上垫板与上支座板均采用六角头螺栓连接。
4)转体前,拆除中心转盘水平锁定装置,并拧紧竖向锁定装置。
5)待转体结束后,安装水平转动限位装置,拆除竖向锁定装置,使中心转盘变为永久性支座的正常工作状态。
图5中心转盘结构示意图
注:
1-水平转动钢板,2-上支座板,3-不锈钢滑板,4-平面四氟板
5-中心定位钢销,6-球冠钢衬板,7-球面四氟板,8-下支座板
9-地脚螺栓,10-竖向转动锁定装置,11-水平转动锁定装置
2.3纵横向平衡重
利用软件对连续钢箱梁进行实体建模,采用不同的工况进行比对分析,最终确定了合理的平衡重布置方式,计算分析过程如下:
2.3.1连续钢箱梁转体施工的有限元模型
石家庄市和平路高架桥2标84-86#墩连续钢箱梁转体施工的有限元模型采用ANSYS有限元软件建立。
其中的连续钢箱梁和转体辅助塔采用shell单元建立,连接钢箱梁与转体辅助塔的转体施工拉索采用link单元建立。
整个有限元模型共计划分单元89105个,节点78585个。
其中shell单元为89103个,link单元为2个。
相关模型图如图6、图7、图8、图9:
图6转体施工有限元模型等视图
图7转体施工有限元模型等视图局部
图8转体施工几何模型局部剖视图
图9转体施工有限元模型正视图
2.3.2第一种工况:
(简支端平衡配重为160t,转盘中心处梁顶曲线外侧横向平衡配重为73.2吨时)
表1转体施工时支座反力情况列表
简支端160吨,横向配重73吨
简支端160吨,横向配重73.2吨
主墩反力
1542.2吨
1542.4吨
简支端东支腿
26.24吨
26.43吨
简支端西支腿
26.73吨
26.53吨
合计
1595吨
1595.3吨
2.3.3第二种工况:
(简支端平衡配重为180t,转盘中心处梁顶曲线外侧横向平衡配重为73.2吨时)
表2转体施工时支座反力情况列表
简支端180吨,横向配重73.2吨
1543.7吨
35.92吨
35.69吨
1615.4吨
2.3.4第三种工况:
(简支端平衡配重为180t,重心向曲线外侧移1.8m;
转盘中心处梁顶曲线外侧横向平衡配重为28吨时)
表3转体施工时支座反力情况列表
简支端180吨,重心向曲线外侧移1.8m,横向配重28吨
1497.1吨
36.2吨
36.4吨
1570.1吨
表4连续钢箱梁转体施工时支座反力情况列表汇总
竖向反力
简支端160吨
横向73吨
横向73.2吨
简支端180吨
简支端180吨,重心东移1.8m,横向28吨
根据竖向支座反力情况可以看出,通过调整横桥向配重和前悬臂端配重的重量,使得连续钢箱梁简支端东、西两个稳定支腿处的竖向反力基本相等,反力值既能保证纵桥向的稳定性,又可以使稳定支腿和转动滑道支架满足强度和刚度要求,这种情况下进行转体施工,结构平稳、安全,对钢箱梁的转体过程和顺利就位有很大帮助。
通过上述计算和结果的对比分析,最终确定的纵、横向平衡重配置方案为:
1)纵向平衡重:
为满足纵向抗倾覆系数1.4的设计要求,根据表4计算结果,纵向平衡重取180t,以道路中心向右侧偏心1.8m布置,拉索左右两侧各设砂箱一个,每个90t(含砂箱自重)。
2)横向平衡重:
由于钢箱梁结构的平面线形为圆弧加缓和曲线(R=4500m,L=53.579m,L0=81m,E=0.729m),故整个结构存在横桥向的扭矩作用,根据表1计算结构,取横向配重28t位于85#墩箱梁顶道路中心右侧7.2m处,设砂箱1个,放置水平,底部垫H型钢找平,并限位加固。
2.4稳定支腿和辅助滑道
2.4.1结构形式
经过计算分析,纵横向配重施加后,在满足纵向抗倾覆系数1.4的情况下,转体段简支端将产生726KN的竖反力,所以在纵向配重端距中心支座半径45m处设置圆弧形辅助滑道,在对应处的箱梁梁底设置2个稳定支腿,用于支承箱梁在滑道上滑动。
辅助滑道形式为700H型钢2片焊接成箱体,箱体上铺不锈钢板,不锈钢板上涂硅脂润滑剂,以减小摩擦系数。
滑道按水平布置,支撑滑道的支架采用八三墩及扩大基础布置方式(见图10)。
稳定支腿为钢板焊接成的箱体,与钢箱梁梁底板焊接,支腿底部镶四氟板,放置在滑道顶部。
图10稳定支腿和滑道体系立面图
2.4.2设计验算
对滑道系统结构设计进行力学计算分析如下:
1、计算荷载
滑道支架上承受的荷载为移动荷载,具体如图11所示:
图11移动荷载示意图
其中,竖向力40t为支点反力,横向和侧向力均为4t,为摩擦力。
2、计算模型
根据“转体滑道设计图”,在ANSYS中建立如图12、图13所示简化计算模型,建模时军用墩柱忽略了缀板作用,截面简化为“工”字形截面,截面形状及特性如图14所示。
图12计算模型
模型中,下部支撑简化为铰支约束。
图13模型实体显示
图14军用墩柱简化截面
3、计算结果
(1)竖向约束反力
在图11所示移动荷载作用下,边支座的竖向约束反力的变化曲线如图15所示。
图15边支座竖向反力变化曲线
从图中可以看出:
当移动荷载刚作用到滑道上时,单个支座(即滑道H型钢在支架上的支点)产生最大竖向反力(0.4060E+05)N;
当移动荷载作用到距离单跨滑道端6.625m时,单个支座产生最大竖向反力2527N。
由此可知:
荷载移动过程中支座不出现上拔力,按照构造配置锚固钢筋即可。
建议各支墩下垫梁每端配置6根Φ20锚固钢筋。
(2)梁上跨中弯矩及挠度
①按图示连续梁计算
当移动荷载在滑道上移动时,跨中弯矩的变化曲线如图16所示。
当移动荷载移动到跨中时,跨中弯矩最大,最大弯矩为:
梁截面为2根H700*300*13*24,由此计算得:
由此
此时梁上挠度为:
并且满足设计跨中挠度±
2mm的要求。
图16跨中弯矩变化曲线
②按简支梁计算
轨道支架的最大净跨为5m,从偏于安全计,作为简支梁计算。
当移动荷载移动到跨中时,所产生的最大弯矩为:
由此计算得:
此时梁上最大挠度为:
满足设计满足设计跨中挠度±
2mm的要求
2.5临时索塔和斜拉索
由于钢箱梁跨越铁路悬臂端自由状态下悬臂根部截面负弯矩很大,且梁端挠度过大,为了保证钢箱梁在转体过程中的自身结构安全以及桥下铁路运输的安全,必须对钢箱梁进行临时斜拉。
钢箱梁两端各设1条斜拉索,上端锚固在中心索塔内,下端分别锚固在钢箱梁端部的耳板销轴上。
85#墩中心处梁顶设置临时钢箱索塔,高14.5m。
辅助塔采用钢箱结构,纵桥向4m,横桥向2m,与钢箱梁焊接。
索塔顶部箱内设张拉槽,千斤顶置于塔内,锚具置于箱梁锚垫板后方,张拉力通过耳板销轴传递至箱梁腹板。
拉索采用平行钢丝索,PES冷铸锚;
采用5000kN张拉千斤顶,千斤顶设于索塔内部,共两台,设一个共用操作台,以使张拉时,两台千斤顶联动同时张拉。
设计拉索初拉力悬臂侧为4000kN,简支侧为4050kN。
2.6转体动力设备及设施
在中心转盘移至盖梁顶部以后,转体动力设施已无法布置在地面上,由于盖梁已制作成8.4m直径的大圆盘,综合考虑后将动力设备也布置在盖梁顶上。
在85#墩盖梁顶平行对称布置2个由钢板焊接而成,并通过钢柱预埋在混凝土内的反力架,用于安放连续张拉千斤顶(图17)。
由于空间小,且转盘为钢制,无法按照传统方式预埋缠绕钢绞线用于转体张拉。
但根据钢板的可焊性,在规范允许的范围内,在距转盘中心1.75m处的钢箱梁底部焊接弧形钢板用于缠绕15-7φ15.2钢绞线,钢绞线后端采用锚具和夹片固定在箱形固定架上,固定架与钢箱梁焊接。
通过2台千斤顶张拉钢绞线,形成力矩,使钢箱梁转动。
图17盖梁顶转体动力平面布置示意图
连续张拉千斤顶为专用加工,设置位移传感器、压力传感器、锚具状态传感器,自动化控制,保证转体时2台千斤顶张拉速度、压力均保持对等和同步。
2.6.1转体千斤顶张拉力计算
1)中心磨盘是面摩擦,穿心千斤顶克服静摩擦需要的顶力:
=(2×
0.15×
1497.5×
0.75)÷
(3×
3.5)=32.09t。
式中:
T——牵引力(kN);
G——转体总重力(kN);
取值为1497.5t。
R——铰柱半径(m);
取值为0.75m。
D——牵引力偶臂(m);
取值为3.5m。
f—摩擦系数,取静摩擦系数为0.15。
2)后方支腿处承受荷载约72.6t,力臂长度为45.07m,静摩擦系数考虑为0.15,穿心千斤顶对中心的力臂为1.75m,穿心千斤顶需要的顶力:
T2=72.6*0.15*45.07/1.75*2=140.23t。
3)穿心千斤顶启动需要的顶力:
T=T1+T2=172.32t。
3)设备选择
钢箱梁转动的动力依靠两台对称布置联动的300t连续张拉千斤顶张拉钢绞线施加。
穿心千斤顶的功效按80%考虑,所以300t千斤顶能达到240t的张拉力。
连续张拉千斤顶为专用加工,设置了位移传感器、压力传感器、锚具状态传感器,自动化控制,保证转体时2台千斤顶张拉速度、压力均保持对等和同步。
2.6.2千斤顶反力架局部加劲验算
1)模型
参照反力架局部加劲图纸,反力架加劲计算模型如下:
图18千斤顶反力架局部加劲计算模型
2)边界条件与荷载
底边与底板焊接,故底边限制三个方向自由度;
荷载按照300t最不利荷载情况考虑,采用均布荷载作用于锚头处。
3)计算结果
a、变形:
最大位移为0.572mm,满足结构变形条件要求。
b、应力:
锚头最大局部应力221Mpa;
锚头加劲中间两个竖向加劲最大局部应力274Mpa;
锚头后侧加劲最大应力107Mpa。
考虑局部应力条件下,锚头加劲中间两个竖向加劲受力最大,采用较厚钢板,钢材选用16Mn钢,其他钢材选用A3钢,满足规范要求。
2.6.3钢绞线缠绕弧形加劲板验算
1)计算模型
图19弧形板局部加劲计算模型
底边与箱梁底板焊接,故底边限制三个方向自由度;
荷载按照300t最不利荷载情况考虑,采用均布荷载作用于高度295mm处。
最大位移为0.91mm,满足结构变形条件要求。
弧形板最大应力203Mpa;
加劲除局部应力点超过205Mpa外,大部分区域应力小于205Mpa,满足应力要求。
3转体施工工艺
3.1转体施工工艺流程
图20箱梁转体施工工艺流程图
3.2转体操作要点
3.2.1箱梁工厂制作
钢箱梁分段、分片在厂内加工,运至现场进行纵横向拼装焊接,钢梁分段、分片位置应避开应力高峰区。
1)钢箱梁纵向共分为13段,其中转体部分为6段(图21)。
2)5个较长段横向分为6片(图22)。
3)中心支座段横向分3片。
4)箱梁工厂制作时,同时焊接安装好带套筒的支座上垫板、弧形围板、后方支腿及连接斜拉索的耳板。
5)最大吊重(中心支座段中片)74t,高20m。
图21钢梁纵向分段示意图
图22钢梁横向分片示意图
3.2.2箱梁拼焊支架搭设
1)箱梁现场拼装焊接支架。
根据钢箱梁转体部分工厂制作分6片、6段的情况,搭设7排拼焊支架。
7#支架利用辅助滑道,需再搭设6排支架。
2)1#~6#支架采用八三式军用钢支墩,顶部铺设六四式军用梁,军用梁顶部采用钢枕分配梁作焊接平台。
支墩下设C20混凝土基础。
3)支架应进行各种工况情况下的强度、刚度、稳定性检算。
4)在六四梁顶部继续搭设钢结构拼焊胎架,胎架顶部通过砂箱来调整钢箱梁的标高及预拱度。
见图23。
图23箱梁焊接拼装支架示意图
3.2.3中心支座(转盘)安装
1)安装前,先在盖梁顶浇筑支座混凝土,并预埋好带螺栓套筒的下垫板。
位置必须准确,安装水平。
2)在钢箱梁拼焊前,安装中心支座。
中心支座下垫板与下支座板采用六角头螺栓连接。
3)拆除水平转动锁定装置,并拧紧竖向锁定装置。
将转动钢板旋动86°
,使其与钢箱梁预拼方向一致。
4)吊装中心支座梁片,精确对位,支座上垫板与转动钢板用螺栓连接。
5)安装水平转动锁定装置。
6)预吊装两个边支座到位,以减少以后吊装的难度。
3.2.4箱梁现场拼装焊接
厂内分段、分片焊接好的箱梁采用大件运输车运至施工现场,利用500t吊车吊至拼装支架上拼装、焊接。
1)在中心支座安装合格,并将转动钢板逆时针方向旋转86°
后,吊装中心支座梁片,精确对位,使其与转动座板对中,将钢箱梁下落,中心支座受力,检查合格后,用螺栓与转动钢板连接,再将转动钢板与上座板临时锁定。
然后,向两侧逐片拼焊,完成中间节段。
2)依次吊装中心支座段各梁片,调整合格后焊接。
3)由支座向两侧、由里向外逐步展开,依次吊装其他各段梁片,调整合格后焊接。
4)全部梁段拼装焊接后,调整预拱度合格,焊接各梁段成整体,全面检查合格。
5)全部焊缝必须100%探伤,合格率必须达到100%。
3.2.5稳定支腿和滑道安装
1)稳定支腿为钢板焊接成的箱体,间距14.4m,距转盘中心径向距离45m,在箱梁工厂制作时,与钢箱梁焊接,支腿底部镶四氟板。
2)下滑道形式为2片700H型钢焊接成的箱体,上铺不锈钢板。
滑道按水平布置,支架采用八三墩及扩大基础布置方式。
滑道在箱梁拼装前完成支承箱梁部分,其余部分在落架前施工完毕。
3.2.6平衡重施加
1)纵向平衡重。
为满足纵向抗倾覆系数1.4的设计要求,经计算,纵向平衡重为180t,以道路中心向右侧偏心1.8m布置,拉索左右两侧各设砂箱一个,每个90t(含砂箱自重)。
2)横向平衡重。
由于钢箱梁结构的平面线形为圆弧加缓和曲线(R=4500m,L=53.579m,L0=81m,E=0.729m),故整个结构存在横桥向的扭矩作用,经计算,需横向配重30t,位于85#墩箱梁顶道路中心右侧7.2m处,设砂箱1个,放置水平,底部垫H型钢找平,并限位加固。
3)纵、横向平衡重在箱梁斜拉前施加,位置、重量一定要准确。
且平衡重砂箱底部要采用纵横H型钢抄垫水平,并与钢箱梁顶焊接加固。
3.2.7钢箱梁斜拉
1)安装索塔。
在85#墩中心处梁顶设置临时钢箱索塔,高14.5m。
索塔采用钢箱结构,纵桥向4m,横桥向2m,与钢箱梁焊接。
2)安装斜拉索。
采用平行钢丝索,PES冷铸锚;
上端锚固在中心索塔内,下端分别锚固在钢箱梁端部的耳板销轴上。
3)安装千斤顶。
采用500t张拉千斤顶,千斤顶设于索塔内部,共两台,设一个共用操作台,以使张拉时,两台千斤顶联动同时张拉。
4)斜拉索张拉。
两侧对称、同步张拉,终拉达到设计要求。
3.2.8转体动力设施安装
1)安装反力架。
在85#盖梁施工时,按设计施工预埋件,安装钢制反力架。
且反力架必须平行、对称,标高一致。
2)安装张拉设备。
在箱梁落架前,连续张拉千斤顶安装在反力架上;
安装位移传感器、压力传感器、锚具状态传感器;
安装自动控制柜。
保证转体时两台千斤顶张拉速度、压力均同步进行。
3)安装张拉钢绞线。
在距转盘中心1.75m处的钢箱梁底部焊接的弧形钢板用于缠绕15-7φ15.2钢绞线,钢绞线后端采用锚具和夹片固定在箱形固定架上,固定架与钢箱梁焊接。
4)试运行。
经全面检查合格,空载试运行,再检查确认正常。
3.2.9顶升支架施工
经计算,转体时,箱梁悬臂端下挠34cm,所以转体到位后,需要对悬臂端进行顶升。
经计算顶升力约需3000kN,采用2台2000kN千斤顶顶升。
顶升支架与后拼段支架共用,采用八三式钢墩,布置于84#墩东侧地道桥桥面上,支架顶面距设计梁底标高预留70cm,在箱梁落架前完成。
3.2.10钢箱梁落架
1)落架前,在85#盖梁顶钢箱梁横向用2台300t千斤顶临时顶紧,此时千斤顶内缸必须伸出一定的行程。
并搭设保护垫木,以增加落架过程中钢箱梁的稳定性,记下此时内缸伸出的长度,并作为横向调平衡的检验标志。
2)先落悬臂端支架。
2#、3#、4#排架依次落架,最后1#落架,使悬臂端悬空发生受力变形。
减少另一端支架的压力,便于落架。
3)再落另一端支架。
先撤出7#排架(滑道支架)的多余支承,使2个后方支腿承受压力,再6#、5#依次落架,此时,钢箱梁中心由转盘(中心支座)和2台千斤顶、后方2个支腿支承。
4)落架后,由于悬臂端悬空,为防止在外力作用下发生颤振,需对悬臂端加保护支点,因钢结构在白天阳光照射下,悬臂端挠度变化较大,保护支点应采用千斤顶,当白天温度发生变化时,利用千斤顶适当调节高度,消除挠度变化。
3.2.11钢箱梁调平衡
1)后方支腿反力称重。
在施工支架完全拆除后及在转体过程中,转动体的自平衡或配重平衡又对施工过程的安全性起着至关重要的作用。
为了保证桥梁转动体形成整体后拆架过程中的安全和转体过程的顺利进行,及时为大桥转体阶段的指挥和决策提供依据,有必要在转体前进行转动体平衡重称重试验,及时提供落架后最终产生的后端支反力。
在后方支腿处各方1台千斤顶,每台千斤顶上设置荷重传感器,测试试验过程中临时支点的支反力值。
将钢箱梁顶起,使支腿脱空,根据称重系统显示的反力大小与计算值相比较,差值应在允许范围内;
若超出,则调整压重。
见图24。
千斤顶及压力传感器测点
图24千斤顶、压力传感器测点布置图(单位:
mm)
于4月13日6:
06测试(已全部落架),西支点支反力:
44t,东支点支反力:
30t
2)调整横向平衡。
转盘中心处横向2台千斤顶同步、缓慢下落,若同时脱空,表明已经平衡;
若有1台先脱空,则需增减横向平衡重,使其达到平衡。
此时,整个力系转换完成,转体结构由后方支腿和中心转盘(中心支座)支承。
3.2.12试转体
1)建立转体组织、指挥机构。
操作、观测、检查人员定岗到位,明确职责,指挥、应答、报告语言要及时、清楚、准确、简练,令行禁止。
2)试转体前,应全面检查转体设施、设备情况,确认符合转体要求。
清理撤出箱梁上的所有物件。
3)转体前,中心转盘