货油挥发VOC回收及再利用系统技术研究Word下载.docx
《货油挥发VOC回收及再利用系统技术研究Word下载.docx》由会员分享,可在线阅读,更多相关《货油挥发VOC回收及再利用系统技术研究Word下载.docx(23页珍藏版)》请在冰豆网上搜索。
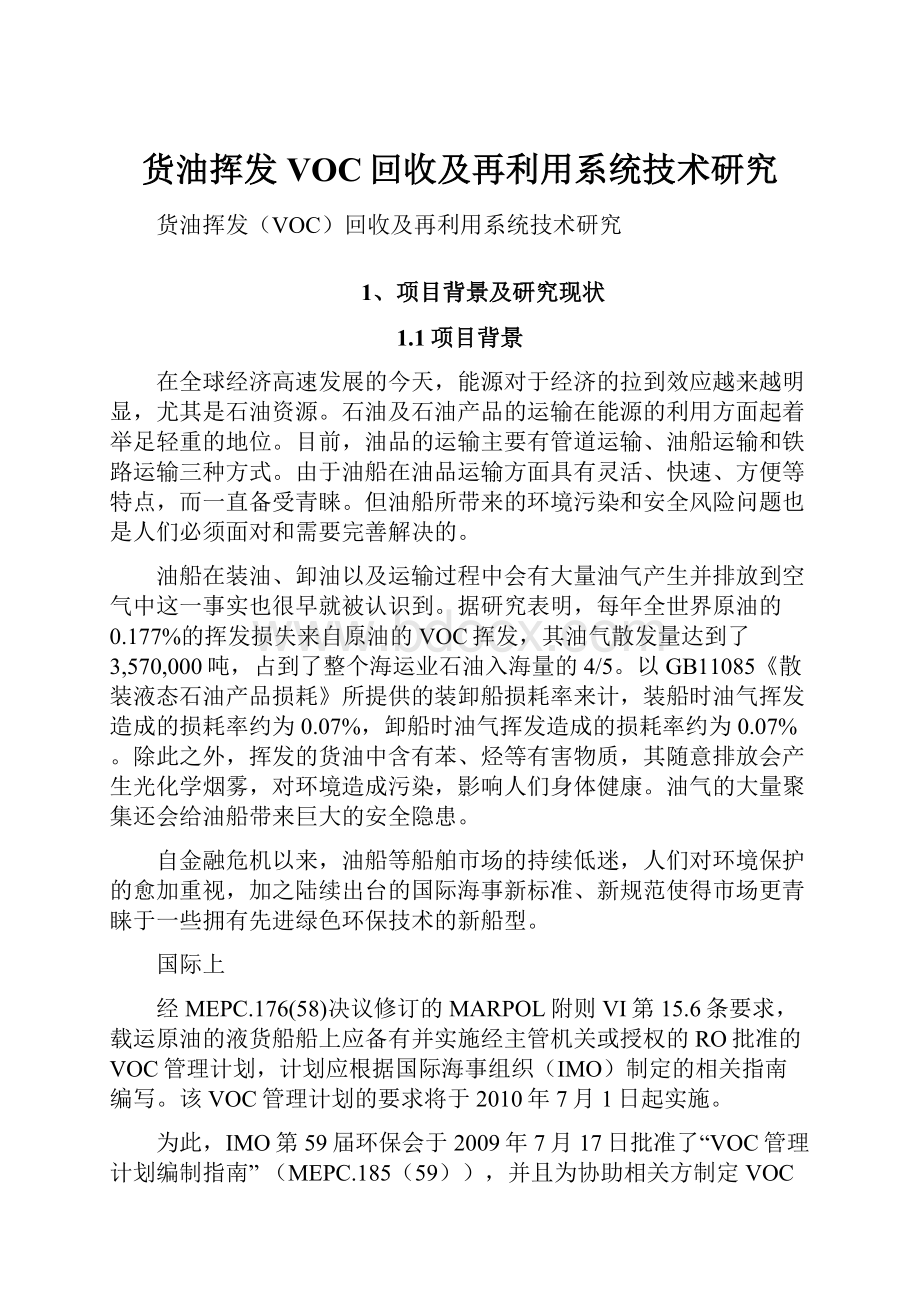
对于主管机关授权本社进行VOC管理计划审批的船舶,船公司应尽快向本社审图中心提交该计划;
对于主管机关尚未对本社执行VOC管理计划审批作出明确授权的船舶,本社将与主管机关进一步确认授权情况;
如确认由主管机关审批,将通知船公司自行联系主管机关办理审批事宜。
4、对主管机关授权本社签发IAPP证书(或符合证明)的船舶,或船东申请本社签发IAPP符合证明的船舶,验船师在2010年7月1日及以后的第一次涉及MARPOL附则VI的检验中,应核查适用船舶是否配备了经批准的VOC管理计划,以及实际操作是否满足批准的VOC管理计划的要求。
检验完成后,应换发新版的IAPP证书(或符合证明)并报告主管机关。
如果船舶在2010年7月1日及以后未能将主管机关或本社批准的VOC管理计划配备上船,将影响IAPP证书或符合证明的有效性。
1.2国内外发展现状
油船设置油气回收装置无论是从经济性,还是环保性、安全性考虑,都是必要的。
早在60年代国外就对装车、装船过程蒸发损耗油气进行回收技术的研究,70年代,世界上技术先进的国家,如美国、日本、西欧国家已广泛采用油气回收技术,解决了装车、装船过程油品损耗的问题。
在1997年9月,国际海事组织(IMO)召开缔约国大会批准“MAPOL73/78公约”附则Ⅵ——《防止船舶污染大气规则》,其中对油船挥发性有机化合物VOC(VolatileOrganicCompounds)回收处理作了规定,并于2005年5月开始生效。
在2009年第59届海事环保会上IMO通过了“VOC管理计划编制指南”,并与2010年7月1日起开始实施。
欧洲经济委员会在1999年哥德堡草案中就已经提出了VOC减排目标,凭借挪威的技术优势,尤其是在VOC回收及再利用方面的技术,欧洲走在世界的前列。
美国也是最早加入IMO《防止船舶污染大气规则》的少数几个国家之一,1998年美国沿海各州就开始要求进入其港口装货的油轮使用油气回收系统。
在国内,油气回收还是个新兴产业,实际应用不多。
根据《中国造船质量标准与钢制海船入级规范实施手册》2006版规定,对于载运闪点不超过60℃原油及石油产品的尾机型油船“船上应有在卸载后驱除货油舱油气及对所有与货油舱相邻的舱室进行驱除油气的设施,为监测可燃气体,船上应备有便携式测爆仪”。
目前国内油船通行的做法就是在装载和卸货时利用港口的油气回收设备进行油气回收,而在运输过程中产生的油气通过呼吸阀直接排放到空气中。
因此国内的油船上都没有安装VOC回收及再利用系统。
随着逐鹿国际海工船舶市场份额不断扩大,国内环境问题的日益重视,对穿梭油轮、LNG船、采油平台等VOC回收及再利用系统研究将具有重要意义。
我国在2003年才开始自主研发油气回收系统。
2006年2月,位于“中国光谷”武汉东湖新技术开发区的湖北楚冠实业股份有限公司经过多年的研究,成功开发出我国陆上第一套具有自主知识产权的吸附法油气回收装置。
经过中石化环保专家现场严格的测试,其油气回收率大于99%,排放的尾气中非甲烷总烃浓度低于3g/m3,性能水平能满足国外严格的排放标准要求,填补了国内空白。
该吸附法油气回收装置已经形成多种规格的系列化产品,并制定出了严格的企业标准,确保了装置在设计、制造、安装等方面的质量,适宜于炼油厂、油库、加油站等易燃易爆危险性场所使用。
即便VOC回收及再利用系统在国外很早就有应用,但基本形式都是采用吸收法、吸附法、冷凝法、膜分离法等几种方法。
膜分离法由于目前技术难度大,成本高,采用的比较少,油船VOC回收更多地采用前三种方法。
Ø
吸收法
图1.1吸收法油气回收装置
吸收法吸收法去油气是利用原油中所含的吸油剂对油气进行喷淋,使油气与吸油剂液体相结合并被吸收。
基本技术为,在货油主管路引出一支管,将部分原油泵入吸收罐内,同时VOC从吸收罐底部注入,逆向流动原油作为吸附介质。
包含VOC的原油会重新流入到原油主管中。
油泵和压缩机将被被使用用来压缩原油和油气。
不能吸附的气体直接经过惰气排放柱排放。
吸收法的优点是结构简单,其缺点在于回收率相对低一些,约为80%。
吸附法
吸附法的基本原理是利用吸附剂的吸附性对油气进行吸附回收。
VOC将会通过吸附器过滤,吸收碳氢。
然后吸附器再生用于下一个循环。
通过真空泵可以降低压力直致碳氢从吸附器中抽出,抽出高浓度的油气经过分离罐,通过原油吸附并返回到货油舱。
图1.2吸附法油气回收装置
吸附法的优点在于回收率很高,通常在90%以上,最高甚至可以达到99%,缺点在于吸附剂在吸附过程中会放热,使分离罐中温度升高,具有一定危险性,同时吸附剂随着温度升高吸附能力会降低,目前通常采用的吸附剂为活性炭,活性炭吸附器寿命通常比较短。
冷凝法
冷凝法是利用制冷剂通过热交换器对油气进行冷凝。
首先油气经过预冷器,温度降低到4℃,油气中的大部分水汽凝结成水排出,油气进入一级冷却器冷却到-40℃,再经过二级冷却器冷却到-80℃。
图1.3冷凝法油气回收装置
冷凝法回收率根据冷却技术不同而不同,二级冷却通常可以达到95%的回收率。
冷凝法由于需要多级冷却,因此能耗比较大。
由于国家环保法规不健全,船舶设备技术滞后,使得我国油船基本都没有采用VOC回收及再利用系统,更多地是依靠港口码头等陆上VOC回收及再利用系统。
与陆上的VOC回收及再利用系统相比,油船所采用的VOC回收及再利用系统具有以下几个差异:
一,系统中设备布置需要更紧凑。
陆上不受空间限制,可以采用很多种VOC回收方法并用,以及浮顶的形式。
二,船舶上应尽量采用低能耗的VOC回收型式。
例如降温加压等方法可能会造成船舶较大的燃料消耗,陆上可以采用电力等方式实现降温加压,成本会更低。
三,VOC处理方式的差异。
陆上回收的VOC直接可以储存。
油船上回收的VOC为考虑其经济性,最好的方法是直接用来作为主机、锅炉的燃料,目前VOC作为辅机燃料还不够成熟。
随着国民经济的发展,环保意识的增强、节能减排和可持续发展的要求,国家对油气的排放已经开始有序管理,油气回收工作将会受到越来越多的重视。
但油船货油挥发(VOC)回收及再利用技术在国内尚属新型技术,存在诸多问题,需要在技术、经济、管理等方面进行深入研究。
2、研究目标
依据国家工信部组织的高技术船舶科研专项要求,以满足绿色环保新型油船配套的VOC回收及再利用系统为目标,通过产、学、研、用联合,开展油船VOC回收及再利用系统集成设计技术、节能减排技术、典型样机设计制造及试验验证技术的研究。
在此基础上,以国际同类产品的技术水平为目标,完成一型为VLCC配套的VOC回收及再利用系统的自主研发和样机研制,并完成实船配套,为填补国内空白,建成具有国际竞争力的VOC回收及再利用系统奠定基础。
3、研究内容
根据《货油挥发(VOC)回收及再利用系统技术研究》项目指南的研究目标,具体的研究内容初步分为下列四项专题:
子专题一:
VOC回收及再利用共性技术研究
子专题二:
VLCC船型VOC回收及再利用系统设计技术研究
子专题三:
VLCC配套VOC回收及再利用系统样机研制及试验验证
子专题四:
VOC回收及再利用系统标准规范研究
⏹子专题一:
以MAPOL73/78公约”附则Ⅵ——《防止船舶污染大气规则》,IMOMSC/Circular.585中的油气回收(VECS)手册,IMOMEPC.185(59)通过的“VOC管理计划编制指南”以及DNV等船级社规范标准为切入点,在对规范和标准研究透彻的基础上,深入研究VOC回收及再利用的共性技术。
主要研究内容如下:
1)减少和控制VOC排放技术研究
原油油船VOC释放发生在3个不连续的情况下,分别是:
装载中,装载航行至卸载港以及液货舱在卸载港压载。
根据3种情况的不同特点,研究适用于各种工况的VOC排放控制、回收及再利用技术,控制VOC的排放将减轻VOC回收装置的压力(功耗、体积等),减少VOC生成量及控制合理惰气量与VOC回收利用相结合才能最大限度减少货物装载、海上航行及在卸载港压载时的VOC排放,同时对VOC释放进行监测和控制。
2)回收VOC燃料应用设计技术研究
回收的VOC液态可燃气进行回收利用,可以直接作为双燃料锅炉和辅助发电机的燃料,需要对相关装置及系统布置设计进行技术研究。
研发出自持式VOC回收装置,所谓自持式就是靠部分VOC来推动燃气透平或让部分VOC在锅炉中燃烧产生蒸汽带动蒸汽透平以满足再液化装置所需要的动力,同时让其对剩余的VOC再液化。
这样就不需船舶发电机组提供动力。
采用此种方法就不需要消耗额外的能量。
实现了VOC再液化的“自给自足”。
研究表明:
大约消耗1/3左右的VOC可以使得2/3左右的VOC得到回收,因此有很高的经济价值。
自持式再液化装置流程图(日本实船实例)制冷剂为氮气:
3)VOC回收及再利用系统与船舶适配性研究;
4)VOC回收及再利用系统总体集成设计技术研究
⏹子专题二:
VLCC船型VOC回收及再利用设计技术研究
目前通行的VOC回收方式有:
冷凝法、吸收法、吸附法、膜分离法。
1)VOC回收装置-低温冷凝系统设计技术研究
VOC通过两级压缩和液化,分离的液化气可以低压下储存,或者直接用于锅炉和主机的燃料(含甲烷和乙炔)。
具体处理过程如下图示意:
低温冷凝VOC回收装置的主要设备为压缩机、冷凝器、储藏罐。
其关键技术在于实现-40℃~-80℃的冷凝环境,以及低温液化气的储罐设计。
设计要求二级吸收率达到95%。
2)VOC回收装置-原油吸收系统设计技术研究
吸收法的主要设备有小型货油泵、压缩机、吸收罐,另外还需要惰气系统参与,其关键点在于VOC恒压力控制,以及惰气系统的自动调节控制。
设计要求吸收率达到80%。
目前,挪威研发的吸收法VOC回收装置,据该公司发布的信息,其吸收率已达到100%。
3)VOC回收装置-活性碳再生及吸附回收系统设计技术研究
具体处理过程如下图示意:
吸附法的主要设备有碳化滤器,真空泵、吸收器、多台小型货油泵。
吸附回收装置的关键点在于吸附剂、吸附设备的开发,吸附剂性能的好坏影响其使用寿命以及吸附性。
设计
要求VOC回收率可以达到99%。
目前,吸附法在实船已有应用,吸附剂再生技术也较成熟,但是,LPG船产生的VOC成分较复杂,在产生VOC最多的装货过程中,PM2.5以上颗粒较多,将严重影响活性炭吸附效果,且管理工作量较大,更换吸附剂成本较高。
建议:
研发以吸收法为主,冷凝法为辅的综合系统,研发以吸收法为主,吸附法为辅的综合系统,以便应对于不同工况。
吸收法主要用于油舱液位较高工况,如航行工况及装载工况;
而冷凝或吸附法用于卸货港压载工况和其他油舱液位较低工况。
⏹子专题三:
VLCC船型VOC回收及再利用系统样机研制及试验验证
结合关键技术研究和设计开发的成果,针对示范船要求,完成一套VLCC船型VOC回收及再利用系统(包括回收及再利用装置及VOC恒压控制检测系统)样机研制。
并完成试验研制和船级社检验,实现船舶配套使用。
研究主要内容有:
1)一套VOC回收及再利用装置的样机研制(包含确定VOC再液化后的成分及物理和化学性能,然后确定存储和管理标准;
确定再利用方式等技术。
2)一套VOC恒压控制监测系统的样机研制;
研究确定油舱压力的成分;
各分压力比例;
压力与装载速度的关系;
恒压力的实现。
3)VOC回收及再利用系统的样机厂内试验验证
4)VOC回收及再利用系统航海试验验证
⏹子专题四:
根据示范工程要求,在完成样机研制,部件及系统厂内联调试验,实船安装调试的基础上,形成设计、制造、试验及安装维护的标准规范。
1)VOC回收及再利用系统设计、制造、试验标准规范研究;
2)VOC回收及再利用系统安装、调试、维护规范研究;
3)VOC回收及再利用系统航海试验标准规范研究
4、成果形式
●形成VOC回收及再利用系统技术研究报告4份;
●完成VLCC配套的低温冷凝VOC回收装置、VOC循环吸收装置、VOC活性炭再生及吸附回收装置设计开发图纸各一套,并取得船级社审查;
●完成一套VOC回收及再利用系统样机研制,完成其相关试验验证及工艺指导,实现船舶配套;
●形成VOC回收及再利用设计、制造、工厂试验及航海试验标准及规范;
●形成发明或实用新型专利2~3项,论文1~2篇。
5、技术基础
武汉船用机械有限责任公司自上世纪50年代以来,一直致力于船舶各类设备的配套。
自2008年开始进行油船装卸系统的开发设计和制造,2010年完成国内首台3000m3/h货油泵的研制,2011年完成国内首套76000DWT油船货油与压载综合系统研制并通过CCS审查,该年还同时完成首台货油泵实船配套,性能达到国际先进水平。
目前,武汉船用机械有限责任公司还同时进行油船、FPSO的深井泵系统、外输系统、泵舱泵系统、机舱泵系统、透平驱动系统的设计开发工作。
通过这么多年对液货装卸系统的设计和研究,武汉船用机械有限责任公司在国内本领域一枝独秀,各项研究成果均是在填补国内空白,部分设备的设计水平已达到国际先进行列。
VOC回收及再利用系统与液货装卸系统紧密相连,液货装卸系统集成化设计,隔舱传动,密封及防爆设计的经验均可作为借鉴。
武汉船用机械有限责任公司具有压力容器、低温液化气储罐的生产能力和资质,可以为VOC回收装置中的VOC储藏罐实现配套。
长期起来,公司认真贯彻国家科技战略发展规划纲要,坚持把科技进步作为推动企业持续发展的战略基点,大力实施科技兴企战略,逐步构建起以企业为主体,市场为导向,项目为载体,产学研相结合、资源共享,人才共建的技术创新体系。
2007年,公司获得国家级企业技术中心认定,并顺利通过2009年和2011年复评,排名120位,在全国729家国家技术中心中处于上等水平。
近年来,公司承担了国家高技术船舶科研专项、863计划、国家科技重大专项、国家重点新产品计划、国家高技术产业发展项目计划等一大批国家科研项目,获得了60多项省部级成果奖和180余项国家专利,承担一批行业、国家和国际标准的编制,装备技术研发水平始终保持与国际先进技术发展同步。
大连海事大学
以下为LNG及LPG船再液化系统设计方案及实例,供参考
复叠式循环再液化装置实质上与单级压缩直接循环再液化装置相同,不同的是冷凝器中的冷却介质是R22、R404A、R134a或丙烷之类的制冷剂而不是海水。
为此,除了液化气再液化循环外,还需配置一个制冷剂循环,两者通过一个冷凝/蒸发器(即在液化气再液化循环中用作冷凝器而在制冷剂循环中又用作蒸发器)复叠起来。
复叠式再液化循环压—焓图
复叠式循环再液化装置适用于全冷式液化气船,其主要优点是装置的再液化能力不像其他类型的再液化装置受海水温度的影响很大,运行工况稳定。
而且,由于货物冷凝器中的冷却介质R22的温度可低于0℃,因此再液化效率较高。
某船单级压缩直接循环再液化装置的布置
LPG船上的再液化装置
海水冷却式货物冷凝器
海水冷却式货物冷凝器是一个圆柱形的耐压筒体,内部排列许多细的镀铸钢管(或铜管)。
筒体两端的盖极与简体外壳用螺栓连接,盖板内有隔板。
海水在冷凝器内的管子里流动,由于受盖板和隔板的作用,海水流过管子呈“S”形路径,来自压缩机的高温高压货物蒸气在冷凝器内的管子外部空间穿过冷凝器,并与海水进行热交换。
货物蒸气被海水冷却,冷凝成液货;
海水则将货物蒸气的潜热和凝结热带走并排至舷外。
双级压缩机直接循环再液化装置的布置
氟利昂冷却式货物冷凝器
氟利昂冷却式货物冷凝器在复叠式和间接式再液化装置中使用。
它是一水平的圆筒形钢质压力容器,里面排列有许多钢管或铜管。
液体氟利昂冷却剂在冷凝器里的管子内汽化蒸发吸热,端板处有隔板,正在蒸发的氟利昂冷却剂沿“S”形路径流过冷凝器。
来自于压缩机的高温高压货物蒸气在冷凝器内的管子外被冷却至过饱和状态而液化。
不可冷凝气体分离器
在货物冷凝器顶部装有一只不可冷凝气体分离器。
将无法冷凝的气体如空气、氮气、甲烷等气体分离后,达到一定压力时,通过透气梳从高空排入大气中。
同时将少量冷凝液体货物通到分离器内的盘管蒸发,使气体分离器内的气体急剧降温。
由于气体分离器内的温度要远低于主货物冷凝器内的温度,所以部分在主货物冷凝器内无法液化的货物蒸气在气体分离器内被冷却液化而被回收。
液化后的货物以及在分离器蒸发盘管内蒸发的货物蒸气一起被送回液货舱。
热交换器
热交换器的主要作用:
(1)将来自液货舱的冷的货物蒸气和来自冷凝器的热的货物冷凝液进行热交换,使热的冷凝液进一步冷却降温,而进入压缩机前的冷的货物蒸气得到加热升温,提高了系统的效率。
(2)系统内有热交换器后,可以不再设液气分离器。
除非液体数量过多,否则随货物蒸气夹带来的液滴会被加热汽化掉。
从冷凝器来的货物冷凝液通过换热器里面的管子内部,而从液货舱来的货物蒸气在换热器里的管子外流过换热器,然后才进入压缩机。
热交换器位于冷凝器的下方。
热交换器的封头处应设有示液镜,以监测热交换器内的液位。
有些系统,装有浮子控制的压缩机切断开关,当加热器内液位太高时,为防止压缩机吸入液体而中断压缩机运行。
中间冷却器
中间冷却器设于两级压缩再液化装置中,在两级压缩中,第一级(低压级)压缩机排出的货物蒸气温度很高,如直接供给第三级(高压级)压缩机吸入,那么第二级压缩机的排出温度会过高,导致压缩机因高温而中断运行。
因此,从第一级压缩机来的货物蒸气通入中间冷却器,用少量来自冷凝器内的液货冷凝液喷淋这部分液体,这部分液体遇热急剧汽化,吸收货物蒸气的汽化潜热,这样进入第二级的压缩机前货物蒸气已冷却降温。
为了保证中间冷却器的正常工作,液体喷射是通过一个控制器操纵阀门,使中间冷却器只维持一个低液位,如因故障使液位上升,则有一浮子开关停止压缩机运转,防止液体进入压缩机内。
液滴分离器设在中间冷却器及第二级压缩机吸口之间,以去除所有带入的液滴。
如压缩机停机,压缩机润滑油的压力下降,会操纵一个控制器,使它停止输入中间冷却器的液体,避免液体货物充满中间冷却器。
耗电量
但在液化BOG的过程中需要消耗的大量的电能,再液化装置由发电机组提供动力,对于一艘125O00m3的LPG船来说,若每天的蒸发率为0.15%,则所需的电力约为3600KW,这样要求电网的负荷较大,需要对船舶电站重新进行改造和设计,这就对船舶电站提出了更高的要求。
自持式再液化装置(回收利用)
此流程包括两个循环:
(1)制冷剂循环:
从冷箱出来的氮气经过第一级压缩机压缩后海水冷却,再进入第二级氮气压缩机压缩,再用海水冷却,最后经膨胀机驱动的第三级压缩机压缩后由海水冷却,进入冷箱预冷,再经过膨胀机膨胀,变成低温的氮气(约-160℃),与用压缩后的BOG进行热交换,之后进入另两个换热器对BOG和膨胀机前的冷剂预冷,最后进入第一级氮气压缩机,完成一个循环。
(2)液化循环:
从液货舱出来的BOG首先经过两级货物压缩机压缩后,进入到冷为第二个换热器进行热交换,之后进入液气分离器,液态的天然气进入最低温的换热器再次冷却后进入液货舱,而从分离器出来的气态天然气进入锅炉燃烧产生的蒸汽已满足蒸汽透平。
与此同时,还有部分没有进入到两级压缩的BOG直接经过向锅炉供气的压缩机后进入锅炉燃烧。
某LNG船设计的部分再液化装置图
这对那些BOR(Boi1offRate)高而主机用不完这些BOG的LNG船有用,而对于那些BOR较低的LPG船意义不大。
目前,大部分的LNG船仍然还是用蒸汽轮机推进的。
现有LNG船航行时把BOG(BoilOffGas)引入锅炉与重油一起混烧,所产生的蒸汽用来驱动蒸汽轮机,但在机动航行或停泊时,全部或部分BOG只好浪费掉,这种方法成本大,在建造和运行期间又需要特殊的技术。
然而,最近,由于燃油价格的变化和有蒸汽轮机推进经验的船员的短缺,传统的蒸汽轮机的推进系统受到极大的挑战,为此,人们开始对LNG船上装备再液化装置的可行性进行研究。
MossRSLNG再液化系统流程图
第三代MossRSLNG再液化系统流程图
LNG船安装位置(参考)
法国EcoRel再液化系统流程图
目前法国CRYOSTAR公司有14套EcoRelReliquefactionUnits订单安装在265000m3的Q-maxLNG船上。
再液化循环的选择原则
用于LPG船的再液化装置必须有一定的原则要求:
1.运行安全可靠。
2.耗功低,结构紧凑。
3.操作方便。
4.经济性要好,无二次污染。
5.整套再液化装置要尽可能模块化制造,整体装船。
6.充分计算对船舶电站的影响。
7.设计好液化石油气再利用整体方案,在船舶设计时统一布局。
附大庆炼油厂油气回收装置系统图
(不适用于船舶,可供参考)