毕业设计论文液位控制系统Word文档下载推荐.docx
《毕业设计论文液位控制系统Word文档下载推荐.docx》由会员分享,可在线阅读,更多相关《毕业设计论文液位控制系统Word文档下载推荐.docx(18页珍藏版)》请在冰豆网上搜索。
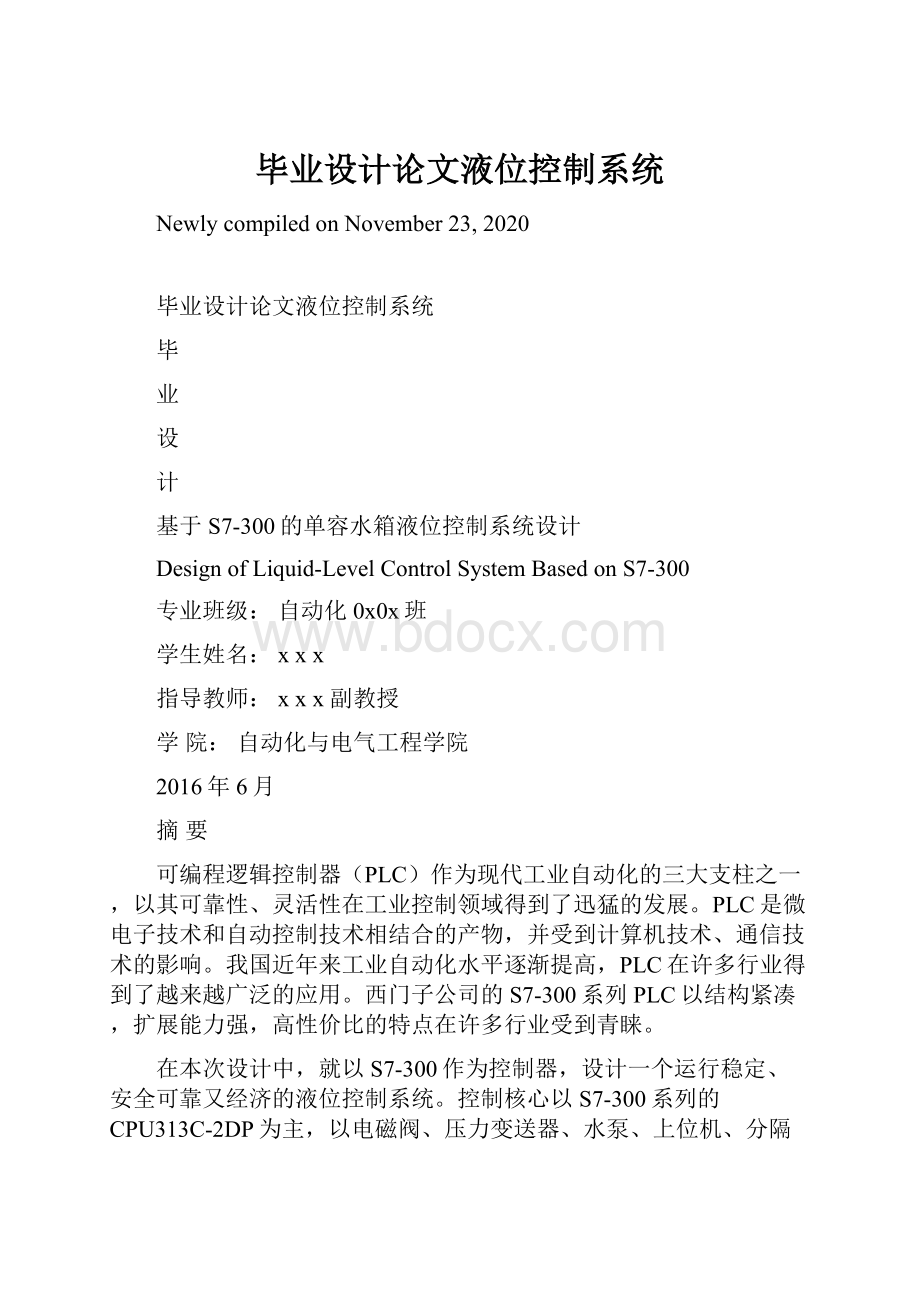
其次,针对S7-300PLC的进行模块化编程,实现数据的归一化等功能。
最后,利用组态王软件设计人机对话界面,通过上位机控制实现液位的自动控制,上下限参数的在线设置,及液位测量值的在线监控;
达到液位控制系统的技术要求。
关键词:
S7-300;
组态王;
液位控制
ABSTRACT
ProgrammableLogicController(PLC),oneofthethreepillarsofmodernindustryautomation,hasgainedrapidlydevelopmentattheindustrycontrolfieldforitshighreliabilityandflexibility.PLCistheproductofthecombinationofmicroelectronictechnologyandautomaticcontroltechnology,anditcanbeinfluencedbycomputertechnologyandcommunicationtechnology.Recentyears,astheleveloftheindustryautomationincreasedinourcountry,PLChasbeenwidelyusedinmoreandmorefields.SiemensPLCofthes7-300serieshasbeenthefavorofmanyindustries,withthecharactersofcompactedstructure,strongextensibleability,andhighfunction/priceratio.
Thisdesignisgoingtofulfillaliquidlevelcontrolsystem,whichisstable,safe,andaffordable,usings7-300asthecontroller.ThecoreisCPU313C-2DPofS7-300seriesandtheauxiliarypartscontainasolenoidvalve,apressuretransmitter,amotor,PC,aseparated-typetankandsoon.Inthedesign,softwaresystemandhardwaresystemcanbedesignedcompletely.
Duringthedesigningprocess,firstofall,hardwiresarechosenanddesigned.Second,moduleprogrammingcanbedonetogetnormalizeddataandPositionControl.Third,HMIcanbefinishedusingKingsoftware,whichisusedtocontroltheliquidlevel,adjustthetopandbottomlimitationparameterson-line,monitormeasuredvalueoftheliquidlevel,andmeetthetechnicalneedsofcontrollingliquidlevel.
KeyWord:
S7-300;
Kingview;
Liquidlevel
1引言
课题的提出
过程控制通常是指连续生产过程的自动控制,是自动化技术最重要的组成部分之一。
其应用范围覆盖石油、化工、制药、生物、医疗、水利、电力、冶金、轻工、纺织、建材、核能、环境等许多领域,在国民经济中占有极其重要的地位。
近几十年来,自动控制系统已被广泛使用,在其研究与发展上也已趋于完备,而控制的概念更是应用在许多生活周围的事物。
在人们生活以及工业生产等诸多领域经常涉及到液位和流量的控制问题,液位控制系统已是一般工业界所不可缺少,例如居民生活用水的供应,饮料、食品加工,溶液过滤,化工生产等多种行业的生产加工过程,通常需要使用蓄液池,蓄液池中的液位需要维持合适的高度,既不能太满溢出造成浪费,也不能过少而无法满足需求。
假若我们能使用此系统来自动维持液位的高度,那么工作人员便可轻易的在操作室获知整个设备的储水状况,因此,液面高度是工业控制过程中一个重要的参数,特别是在动态的状态下,采用适合的方法对液位进行检测、控制,不仅能收到很好的效果,而且提升了工作效率。
随着我国科学技术和经济的不断发展,社会高度信息化,新的高科技技术不断应用到各个方面中,使得智能化已成为一种发展的必然趋势。
智能化也往往是从设备自动控制系统开始。
可编程控制器(ProgrammableLogicController,PLC)是以微处理器为基础,综合了计算机技术、自动控制技术和通信技术而发展起来的一种通用工业自动控制装置。
因此,基于PLC的液位控制系统在现代工业控制系统中具有重要的意义。
感谢您对我们的信任.已帮助1800多名毕业生完成毕业设计,顺利通过毕业.在本工作室定做,请认真阅读以下注意事项:
1.代做毕业设计/论文类型[专科/本科/工硕]PLC毕业设计,单片机毕业设计.电子|通信|电力|电气|机电|自动化类+我们将在一日之内回复你,并与你联系.
PLC及过程控制技术的概述及发展
可编程控制器是计算机家族中的一员,是在继电器控制和计算机控制的基础上开发的产品,是为工业控制应用而设计制造的以微处理器为核心,把自动化技术、计算机技术和通讯技术融为一体的新型工业自动控制装置。
早期的可编程控制器称作可编程逻辑控制器(ProgrammableLogicController),简称PLC,它主要用来代替继电器实现逻辑控制。
随着技术的发展,这种装置的功能已经大大超过了逻辑控制的范围,还可以进行算术运算和模拟量控制等,因此,美国电器制造协会(NEMA)于1980年正式将这种装置命名为可编程控制器(ProgrammableController),简称PC。
但是为了避免与个人计算机(PersonalComputer)的简称混淆,所以将可编程控制器简称PLC。
出售10元2000个财富值,足够大学4年的使用。
+威信(mk6689866)。
PLC实质是一种专门用于工业控制的计算机,所以其硬件结构基本上与微型计算机相同,主要由中央处理器(CPU)、存储器(RAM、ROM)、输入输出器件(I/O接口)、电源及编程设备几大部分组成。
PLC的硬件结构框图如图1-1所示。
图1-1PLC硬件结构框图
PLC作为一种专用于工业控制的计算机具有以下特点:
1、高可靠性
2、丰富的I/O接口模块
3、采用模块化结构
4、编程简单易学
5、安装简单,维修方便
20世纪末期,可编程控制器的发展特点是更加适应于现代工业的需要。
从控制规模上来说,这个时期发展了大型机和超小型机;
从控制能力上来说,诞生了各种各样的特殊功能单元,用于压力、温度、转速、位移等各式各样的控制场合;
从产品的配套能力来说,生产了各种人机接口单元、通信单元,使应用可编程控制器的工业控制设备配套更加容易。
目前PLC在国内外已广泛应用于钢铁、石油、化工、电力、建材、机械制造、汽车、轻纺、交通运输、环保及文化娱乐等各个行业。
而对于过程控制技术,在20世纪40年代以前,工业生产技术水平相对落后,生产过程大多处于手工操作状态,操作工通过目测判断生产过程的状态,手动调整生产过程,生产效率很低。
40年代以后,工业生产过程自动化技术发展很快,尤其是近些年来,在IT技术的带动下,过程控制技术发展十分迅猛。
过程控制装置与系统的发展大致分为以下几个阶段:
1.局部自动化阶段(20世纪50—60年代)
这个阶段的过程控制系统绝大多数是单输入-单输出系统;
被控参数主要有温度、压力、流量和物位四种参数;
控制的目的是保持这些工艺参数的稳定,确保安全生产。
生产的规模比较小,多用气动仪表进行测量与控制,采用~的气动信号作为统一标准信号,压缩空气为动力的气动仪表实现就地的简单控制。
到20世纪50年代后期至60年代,先后出现了气动和电动单元组合仪表,采用了集中监控与集中操作的控制系统,实现了工厂仪表化和局部自动化。
2.集中控制阶段(20世纪60—70年代)
在20世纪的60年代,随着工业生产规模不断扩大,生产过程越来越复杂、产品质量要求越来越高,对过程控制技术提出了新的要求,迫切需要生产过程集中控制与管理。
随着电子技术的发展,半导体产品取代了电子真空管,之后,集成电路取代了分立元件,电子仪表的可靠性大为提高,逐步替代了气动仪表。
这时的过程控制系统大量采用单元组合仪表和组装式仪表,生产过程实现了车间范围和大型系统的集中监控。
为了提高控制质量和满足特殊工艺的控制要求,开发使用了多种复杂控制系统方案,例如串级控制、前馈控制、比值控制、均匀控制等。
特别式前馈控制、选择控制的实现,使过程控制品质、安全性大为提高。
前馈控制使控制质量显着提高;
选择控制自动实现保护性自动控制,以免强制性连锁停车,改变了过去不得不切向手动或被迫连锁停车的状况,从而扩大了自动化的范围。
3.集散控制阶段(20世纪70年代中期至今)
20世纪70年代,随着大规模集成电路出现及微处理器的问世,计算机的性价比和可靠性大为提高,采用了冗余技术和自诊断措施的工业计算机完全满足工业控制对可靠性的要求,为新的过程控制仪表、装置与系统的设计开发提供了强有力的支持。
此时的大型生产过程一般都是分散系统,这样可以使生产过程控制分散进行,将发生故障和危险的风险分散。
基于“集中管理,分散控制”理念,在数字仪表和计算机与网络技术基础上开发的集散型控制系统(DCS,DistributedControlSystem)在大型生产过程控制中得到广泛应用。
过程控制系统的结构也由单变量控制系统发展到多变量系统,由生产过程的定值控制发展到最优控制、自适应控制等。
到20世纪90年代以后,随着测量仪表数字化、通信系统网络化和集散型控制技术日益成熟、现场总线技术以及基于现场总线技术的网络化分布式控制系统逐步推广、使用,使过程控制系统的开放性、兼容性和现场仪表与装置的智能化水平发生了质的飞跃。
工厂自动化(FA)、计算机集成过程控制(CIPS)、计算机集成制造系统(CIMS)和企业资源综合规划(ERP)等方案的规划和实施,正在成为提高工业生产过程经济效益的关键手段。
本课题研究的内容与目的
液位自动控制系统中,主要是针对单容水箱液位控制系统的设计过程,涉及到液位的动态控制、控制系统的总体设计、PLC控制、位式控制算法、压力变送器和电磁阀等一系列的知识。
设计单容液位控制系统中,控制方式采用了位式控制算法,控制核心为S7-300系列的CPU313C-2DP以及PLC内部A/D、D/A转换模块,检测元件为压力传感器,执行器为电动调节阀。
通过以上的器件设备、位式控制算法和上位机的组态等,实现液位自动控制系统的设计。
本课题研究内容:
(1)控制器的算法
(2)通过PLC实现液位自动控制
(3)对输入变量的转换与归一化
(4)组态软件的使用
(5)实现上位机对液位的实时监控
2液位控制系统硬件设计
液位控制系统的系统设计
硬件设计是在对课题进行深入分析,对相关信息进行调查之后所进行的基础性工作,是软件设计实现的前提。
硬件的合理选用,对于整个课题的设计至关重要,既要合理、适合,也要经济适用。
本设计要实现用S7-300PLC作为控制器,通过变频器控制电机速度,同时由变送器和四个液位检测开关收集液位信号反馈给PLC来进行进一步控制,从而实现使液位保持在设定值附近的自动控制系统。
单容水箱的液位控制系统如下图2-1所示。
图2-1液位控制系统
PLC的选型
S7-300是模块化的通用型PLC,适用于中等性能的控制要求。
SIMATICS7-300编程序控制器是模块化结构设计。
各种单独的模块之间可进行广泛组合以用于扩展。
其CPU集成了过程控制功能,用于执行用户程序。
不需附加任何硬件、软件、编程,就可建立一个MPI网络。
若有PROFIBUS-DP接口,就可建立一个DP网络。
S7-300可大范围扩展各种功能模块,很好的满足自动控制任务。
简单实用的分散式结构和多界面网络能力,使其应用十分灵活。
且指令集成功能强大,可用于复杂控制。
其功能较S7-200要强大很多。
而且,就其价格而言,又较S7-400要经济得多。
所以,S7-300是本次设计中控制器的首选。
CPU型号的选择
S7-300有20种不同等级的CPU,分别使用于不同等级的控制要求。
CPU313C-2DP带集成数字量输入/输出和PROFIBUSDP主站/从站接口的紧凑型CPU,带有与过程相关的功能,可以完成具有特殊功能的任务,可以连接单独的I/O设备。
该控制器配置为:
16DI/16DO
DC24V、FlashEPROM微存储器卡(MMC)、一个MPI接口和一个DP总线接口。
相比之下,CPU312C适用于对处理能力有较高要求的小型应用;
CPU313C满足对处理能力和响应时间要求较高的场合,但不带主站/从站接口;
CPU312适用于全集成自动化的基本型CPU及中等处理速度的小规模应用;
CPU314适用于中等处理量的应用;
而CPU315-2DP、CPU315-2PN/DP、CPU317-2DP、CPU317-2PN/DP及CPU319-3PN/DP,固然有较高的性能,可用于要求较高的应用,但对于本设计来说是不经济的,也是不必要的。
CPU313C-2DP实物如图2-2所示。
图2-2CPU313C-2DP图2-3SM334模拟量输入/输出模块
模拟量模块(SM)的确定
S7-300的模拟量I/O模块包括模拟量输入模块SM331、模拟量输出模块SM332和模拟量输入输出模块SM334和SM335,通常选用SM334系列的模块。
它既有模拟量输入通道,又有模拟量输出通道,用于连接模拟量传感器和执行器。
这种模块目前有SM334AI4/AO2
8/8位和SM334A4/AO2
12位两个型号。
这里选用的是SM334AI4/AO2
8/8位的模块,它具有4个输入、2个输出,精度是8位。
它是不可编程的,通过硬件连线来定义测量和输出类型。
实物如图2-3所示。
模拟量输入模块用于将模拟信号转换为CPU内部处理用的数字信号,其主要部分是A/D转换器。
模拟量输入模块的输入信号一般是模拟量变送器输出的标准直流电压、电流信号。
各模拟量通道转换是顺序执行的,每个模拟量通道的输入信号是被依次轮流转换的。
由图2-4知,模拟量输入模块由多路开关、A/D转换器、光隔离元件、内部电源和逻辑电路组成。
图2-4SM334模拟量输入模块原理图
SM334模拟量输入模块的接线如图2-5所示。
图2-5SM334模拟量输入端子接线图
模拟量输出模块用于将CPU送给它的数字信号转换为成比例的电流信号或电压信号,对执行机构进行调节或控制,其主要转换部分是D/A转换器。
如图2-6所示。
图2-6SM334模拟量输出模块原理图
电源模块的选用
电源模块选用的是PS3072A,电源效率是83%。
模块输入电压为单相交流120/230V,50/60Hz;
输出电压为DC24V,具有短路和断路保护。
正常状态时,绿色LED亮;
当输出电路过载时,LED指示灯会闪烁;
如果输出端断路,则输出电压为0,此时LED变暗。
输入电压过高,可能损坏模块;
输入欠压,模块关闭,停止工作。
如图2-7所示。
图2-7电源模块
变频器的选型
变频器选用的是MICROMASTER420系列,MM420是用于控制三相交流电机速度的变频器系列。
本变频器由微处理器控制,并采用绝缘栅双极型晶体管作为功率输出器件,具有很高的运行可靠性和功能多样性。
具有易于安装、调试,快速相应,正常状态下无跳闸运行,更好的动态特性,过/欠电压保护,短路保护等优点。
本变频器必须可靠接地,断开电源后可进行电源及电机端子的接线,接线方法如图2-8所示。
图2-8电动机和电源接线方法
变送器的确定
可采用扩散硅液位变送器,用于收集液位信号,产生4~20mA模拟信号,作为模拟量输入信号传递给PLC,进行进一步控制。
液位变送器包括一个表头,两边都有盖子,打开盖子,一边的表内部可以调节零点或满量程,另一边内部用于接线。
如图2-9所示。
图2-9变送器接线和调节图
水位检测开关的选定
水位开关分为:
电容式水位开关、电子式水位开关、电极式水位开关、光电式水位开关、音叉式水位开关、浮球式水位开关等。
这里选用的是电子式水位开关BZ2401,检测方式为有水时闭合。
它可以直接与PLC搭配工作,判断有水时输出24V,无水时0V,电流容量2A。
高低电平的信号可通过PLC来读取,并驱动水泵等用电器工作。
可以任意方向安装,当横向安装时,水位到达蓝线就动作,且精度较高。
产品竖向安装时,水位到达红线就动作,有一定的防波浪功能。
而且具有耐污、耐颠簸、抗摔性强、耐酸碱,不怕磁场影响、不怕金属体影响、不怕水压变化影响、不怕光线影响,没有盲区,不怕固体漂浮物的影响的优点。
下图2-10为BZ2401普通型电子式水位开关竖向安装时的工作情况,适用常温水体环境。
图2-10电子式水位开关BZ2401
3液位控制系统的软件设计
液位控制系统结构设计
单容水箱液位控制系统控制框图如下图3-1所示。
图3-1液位控制系统框图
其中A/D转换、PLC调节、D/A转换等运算都是在PLC内部执行,同时为上位机提供可用的数据,用以显示。
上位机也可对相应的地址进行赋值,来设定相关参数。
如图3-2所示,以S7-300作为控制器,西门子公司的变频器MM420作为执行器,并利用它的顺序控制功能,输出7个可设定的固定频率来控制电机的转速,从而控制进水流量达到控制水位的目的。
其中,液位信号由液位变送器LT和水位检测开关传送给PLC,作为控制依据,并由PLC向变频器输出3个开关量信号。
图3-2水位控制系统
PLC程序设计
固定频率的设定
PLC输出的3个开关量地址为、、,它们与变频器输出频率之间的关系如表3-1所示。
表3-1变频器输出频率与PLC输出的关系
速度
1
0Hz
10Hz
15Hz
20Hz
30Hz
40Hz
50Hz
不用
PLC控制要求和策略
水位检测信号的安置如图3-3所示,一共设置4个水位检测开关,检测方式为有水时闭合。
除了上、下限位之外,开关1、2的作用是将水位划分为3个状态,状态Ⅰ为水位偏高,Ⅱ为适中,Ⅲ为偏低。
控制要求和策略:
1)上限位:
点亮上限位报警指示灯,开关输出组合为001(0Hz)。
2)下限位:
点亮下限位报警指示灯,开关输出组合为111(50Hz)。
3)状态Ⅰ:
延时若干时间后若依然为状态Ⅰ,则开关输出组合减1,使MM420的输出频率下调一个级别,直至水位进入状态Ⅱ,或者开关输出组合为001(0Hz)。
4)状态Ⅱ:
输出不变。
5)状态Ⅲ:
延时若干时间后若依然为状态Ⅲ,则开关输出组合加1,使MM420的输出频率上调一个级别,直至水位进入状态Ⅱ,或者开关输出组合为111(50Hz)。
最终目的是使得水位稳定在状态Ⅱ。
PLC程序控制流程
PLC程序控制流程图如图3-4所示。
图3-3水位检测示意图图3-4控制流程图
STEP7编程过程
1.创建项目和硬件组态
激活SIMATIC管理器(SIMATICManager),在新建项目窗口输入“液位控制”,建立新项目。
单击SIMANTIC300Station和Hardware图标,在HWConfig窗口中进行硬件组态设置。
如图3-5所示。
图3-5STEP7硬件组态
2.符号编辑
单击Symbols图标,进入符号编辑器,对全局变量命名,这样可以增加程序的可读性,而且有利于程序的输入及变量的变更。
如图3-6所示,对各个开关、水位状态、报警指示灯等等都进行了变量命名。
3.编辑用户程序
1)主程序OB1的编程
单击Blocks图标,再单击OB1进入对用户主程序的编程。
在OB1中首相对上、下限位的状态进行处理,然后通过对水位状态1、3的判断结果,调用相应的减速、升速功能F1、F2。
OB1的程序片段如图3-7所示。
图3-6编辑符号表
图3-7OB1中主程序片段
2)编制功能FC
在SIMATIC管理器中用Inset下拉菜单生成功能FC1和FC2.
当水位为状态1时,FC1用于向下调节变频器的输出频率;
而FC2用于当水位为状态3时的频率上调。
单击FC1和FC2的图标,可分别对它们进行编程,图3-8是功能FC1的部分程序。
图3-8FC1程序片段
4.程序下载与调试
OB1、FC1、FC2编制完成后,通过硬件接口将计算机和PLC连接起来,就可以将程序下载给CPU进行在线调试。
下载之前应将CPU存储器复位,将其切换到STOP模式,下载完成后在切换到运行模式运行用户程序。
为了便于调试可以建立变量表,用于显示各个变量的实时状态。
OB1、FC1、FC2的完整程序见附录。
上位机组态软件设计
组态王(KINGVIEW)软件是国内第一家较有影响的组态软件开发公司产品。
组态王软件提供了资源管理器式的操作界面,并且提供了以汉字作为关键字的脚本语言支持,也提供了多种硬件驱动程序。
它是一种通用的工业监控软件,它融过程控制设计、现场操作以及工厂资源管理于一体,将一个企业内部的各种生产系统和应用以及信息交流汇集在一起,