210m烟囱000m以上筒壁施工方案文档格式.docx
《210m烟囱000m以上筒壁施工方案文档格式.docx》由会员分享,可在线阅读,更多相关《210m烟囱000m以上筒壁施工方案文档格式.docx(70页珍藏版)》请在冰豆网上搜索。
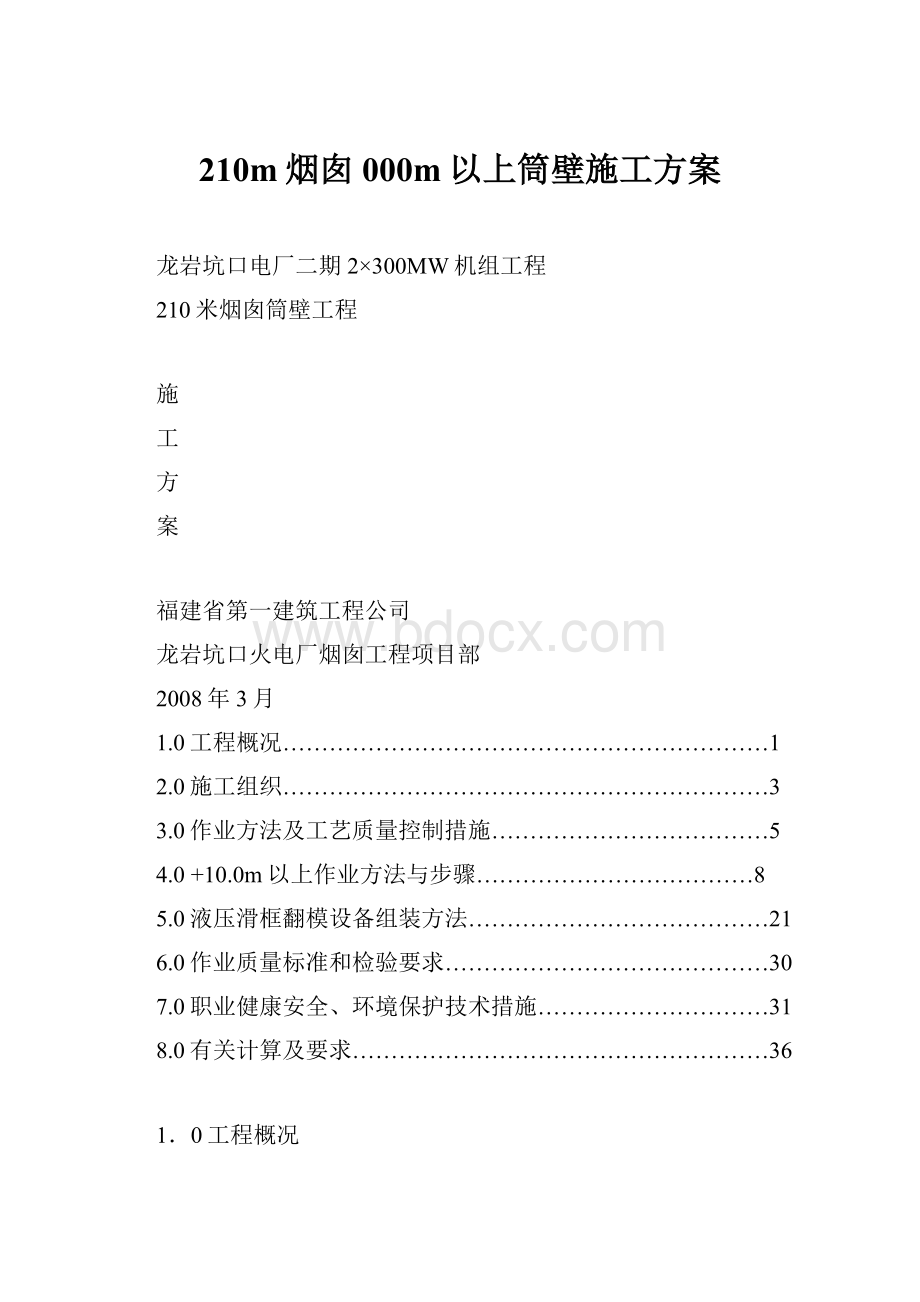
3
耐酸砖内衬
m3
967
4
内壁防腐涂料
约10000
5
保温隔热层
712
1.4工期要求
总工期235d,计划如下:
作业名称
起讫时间
总时间(d)
总计(d)
0-10m筒壁及积灰平台施工
08.3.10—08.4.19
41
235
提升设备安装
08.4.20—08.5.5
16
提升设备验收
08.5.6—08.5.7
10米至30米烟道口施工
08.5.8—08.5.26
19
30米至70米筒壁施工
08.5.27—08.6.27
32
提升设备改装
08.6.28—08.7.2
70米至150米筒壁施工
08.7.3—08.9.7
67
150米至210米筒壁施工
08.9.8—08.10.28
51
筒首施工(封顶)
08.10.29~08.10.30
2.0施工组织
2.1作业人员
人力资源配备表
负责人
1人
钢筋工
15人
生产负责
木工
16人
技术员
电工
2人
施工员
焊工
质检员
泥水工
材料员
架子工
6个
安全员
普工
10个
测量人员
75人
电工、电焊工、架子工为特殊工种,其作业人员必须经过国家规定的专业培训,持证(特殊作业人员操作证)上岗;
所有上岗人员必须经过身体检查,患有精神病、高血压、心脏病等不宜从事施工作业的人员一律不用。
单项技术员全面负责单项工程技术策划、施工质量监督及现场管理调度工作;
材料员负责施工用材料的采购、进场及检验工作。
电工负责用电设备的维护和安全防护工作;
工人要严守操作工序,把好质量关,遵守现场安全文明施工管理规定,听从指挥,服从管理。
2.2技术准备
仔细阅读图纸,进行会审。
编制施工进度计划、质量计划并进行钢筋和模板翻样,编报材料计划,制定工程数据等管理办法。
2.3材料准备
周转材料按计划单进场,对进场材料要严把质量关,不合格的材料杜绝进场。
水泥采用龙麟牌P.O.42.5级水泥。
石子选用5-30mm坚硬花岗岩破碎石子,砂子采用漳州九龙江河砂,材料经过检验合格后方可提出配合比,河砂、石子、水泥等需用的材料应提前报出用量,并储备至少一个星期的用量。
钢筋经检验合格后方可进场。
机械设备经检验、调试合格后方可使用。
2.4主要机具
机械或设备名称
型号及规格
汽车吊
50T
台
电焊机
500KVA
吊笼卷扬机
5T
氧割设备
套
导索卷扬机
3T
插入式振动棒
ZX50
摇头扒杆卷扬机
2T
高压镝灯
8
盏
调幅卷扬机
0.5T
水准仪
液压控制台
激光铅锤仪
液压千斤顶
65
只
对讲机
50千克垂球
个
高压泵
搅拌机
750
铝塑管
6分
300
米
配料斗
2.5作业条件
2.5.1现场“三通一平”已具备,施工人员已全部就位。
2.5.2施工工器具、机械准备就位,并进行运行检查,且具备正常生产能力。
2.5.3混凝土浇筑必须在钢筋和各种材料准备充分等工序自检合格报业主、监理工程师验收合格后,才进行浇筑。
2.5.4气温零度以下、四十度以上不宜从事露天作业,当风力六级以上不能从事高空作业。
2.5.5每道工序开始时,需对上道工序检验合格后方可进入下一道工序施工。
2.5.6建立内部工序交接手续,做到工序之间有交代并纪录在案。
2.5.7垂直运输
井架内设2个吊笼作为施工人员上下及运输砼和内衬等材料的之用,吊笼用角钢焊成,三面围以钢板网,每次提升砼0.6m3,上人和上料吊笼宜分开且上料吊笼严禁上人。
在井架顶部设钢管悬臂桅杆,作为钢筋和其它构件的垂直运输用。
上下人及砼吊笼使用5T双滚筒卷扬机提升,拔杆用2T卷扬机提升。
2.6施工场地布置:
3.0作业方法及工艺质量控制措施
3.1烟囱施工部署
3.1.1烟囱积灰平台以下采用常规翻转模施工方法,积灰平台以上筒壁采用液压爬升翻转模施工工艺;
外爬梯和信号平台的安装与筒壁施工同步进行。
3.1.2正常施工阶段每上升一节的有效高度为1.43m,烟囱筒壁每10m高度分为7节,内外模板分别脱模,平台整体爬升。
烟囱内衬与筒壁爬模同步施工,每浇筑一节混凝土,随后砌筑一节内衬。
内衬砌筑在内吊架上进行。
3.1.3烟囱积灰平台以上筒壁爬升模板施工含扎筋、组装、浇砼、模板脱离、爬升、内衬和隔热层每天施工一节,100m以上每天施工1~2节。
3.2±
0.00m~+10.0m及积灰平台作业方法
3.2.1积灰平台施工方法
(1)整个积灰平台中间依靠4根600×
600钢筋砼柱支撑,四根主框架梁搁置在4个柱上,柱中间距为5000mm,周边直接搁置在烟囱筒壁的环形牛腿上。
因此,木模安装主要用钢管架来承受整个平台的重量,烟囱筒壁内搭设满膛钢管架支模的方法。
支模架以四条主梁为主干道,各搭设四条双排钢管架,距砼梁底70mm,在钢管架上铺设50×
100×
1500mm搁栅料,搁栅间距400mm,然后铺设梁底板(18厚九夹板)。
钢管架立杆间距为1200×
1200mm,步距为1500mm,并在对称位置设立剪刀撑4处。
其他位置可根据次梁布置再设立杆(立杆最大间距为1500mm),砼柱亦是利用主梁的双排钢管架支模。
(2)模板设计计算
(一)、模板支撑系统的设计计算
1、荷载计算
(1)模板结构自重:
0.5KN/m2。
(2)现浇砼自重:
24KN/m3。
(3)钢筋自重:
梁每m3砼1.5KN,板每m3砼1.1KN。
(4)施工人员设备自重:
取2.5KN/m2。
(5)振捣砼时产生荷载:
水平面模板为2KN/m2,对垂直面模板为4KN/m2。
(6)新浇筑砼对模板侧面的压力,最大压力用下式计算:
F=0.22γt0B1B2V1/2
(7)倾倒砼时产生的荷载:
2KN/m2。
荷载组合
荷载组合表表1
模板类别
参与组合的荷载项
计算承载能力
验算刚度
平板和薄壳的模板及支架
1、2、3、4
1、2、3
梁和拱模板的底板及支架
1、2、3、5
梁、拱柱(边长≤300mm)、墙(厚≤100mm)的侧面模板
5、6
6
大体积结构、柱(边长>300mm)
6、7
墙(厚>100mm)的侧面
q=q1+q2+q3+q5
=0.5×
1+(1.2×
0.1+0.3×
0.65×
1.2)×
24+(0.144×
1.1+0.234×
1.5)+2=0.5+8.496+0.509+2=11.51KN/m
对钢管立柱的压力=V/2=1/2×
0.6ql=0.5×
0.6×
11.51×
1.2=4.14KN<13.9KN(符合要求)
(2)底模验算
A、强度验算
M=1/8ql2
q按荷载组合表计算:
q=11.51KN/mM=1/8×
0.42=0.23KN/m。
底模18mm厚木胶合板,
0.23×
103×
103
16200
W
M
300×
182
W=bh2==16200mm3σ===14.2N/mm2<fm木胶合板的抗弯强度设计值fm=25/1.55=16.13N/mm2符合要求
B、挠度验算
5ql4
384EI
4.66×
1011
5×
11.51N/mm×
3004
44.8×
1010
384×
3.5×
1/12×
500×
203
l
ω====1.04mm
250
≤[ω]==1.6符合要求
(3)搁栅计算
A、抗弯强度验算
M=1/8qc(al-c)=1/8×
0.3×
(0.45×
1.2-0.3)
=0.10KN/m
0.10×
106
83333
1/6×
50×
1002
σ=M/W===1.2N/mm2<fm=17N/mm2
挠度验算
1200
10000×
417×
104
(8×
12003-4×
3002×
1200+3003)
qc
ω=(8l3-4c2l+c3)==2.89mm≤
=4.8mm符合要求
(4)大楞计算:
按连续梁计算,承受搁栅传来的集中荷载,简化为均布荷载计算
A、抗弯强度计算:
41.54
M=0.036ql2=0.036×
1.22=0.60KN/m
48
d14
d
π
W=(d3-)=0.098×
(483-)=0.098×
48797.31=4782.14
4.78×
0.60×
σ=M/W==125N/mm2<fm=205N/mm2
所以,大楞强度符合要求。
B、挠度验算:
64
I=(d4-d14)=0.049×
(484-41.54)=0.049×
2342270.94=114771.28
12004
100EI
ql4
206×
114771.28×
ω=0.632×
=0.632×
=1.01mm<l/250=1000/250=4mm
挠度验算符合要求。
(二)、墙模板
(1)荷载设计值
1)混凝土侧压力
①混凝土侧压力标准值
F1=0.22rctoB1B2V1/2
Vc=24KN/m3B1=1.0B2=1.0
(T+15)
200
20+15
to=T取20℃to==5.71
V浇筑速度按0.4m/n考虑
F1=0.22×
24×
5.71×
1×
0.41/2
=19.07KN/m2设计值F=F1×
1.2×
0.85=19.45KN/m2
2)倾倒混凝土时产生的水平荷载
荷载设计值=4×
1.4×
0.85=4.76CN/m2
3)进行荷载组合
F1=19.45+4.76=24.21KN/m2
(2)验算
1)胶合板验算
查表得本胶合板900×
1830×
20截面特征,I=1/12×
900×
203=6×
105mm4
W=1/6bh2=1/6×
203=6.00×
104mm3
①计算简图
q1=21.79
↓↓↓↓↓↓↓↓↓↓↓↓↓↓
500
225
化为线均布荷载:
q1=24.21×
0.9=21.79N/mm(用于计算承载力)
q2=F×
0.9=19.45×
0.9=17.51N/mm
抗弯强度验算:
M=0.1q1l2=0.1×
21.79×
5002=5.42×
105N.mm
5.45×
105
b×
σ=M/W==9.2N/mm2<fm=16.13
强度验算符合要求。
q2m
24EI
ω=(-l3+6m2l+3m3)
17.51×
225(-5003+6×
2252×
500+3×
2253)
6×
=
=4.77mm<[ω]
2)内钢楞验算
化为线均布荷载q1=F1×
0.5=12.01N/mm(用于计算承载力)
12.01×
0.9
φ10钢筋拉拉强度验算:
78.54
F/A==140N/mm2<fm=205N/mm2
符合要求。
3.2.2±
0.00~+10.0m筒壁采用钢模翻转模方法施工,筒内搭设满膛脚手架,筒外搭设双排架。
4.0+10.00m以上作业方法与步骤
4.1烟囱筒身采用液压滑框翻模的施工方法,工序安排:
筒身0-10m(七模)采用满樘脚手架加固普通翻模施工;
10m-210m采用液压滑框翻模施工。
混凝土采用75m3/h搅拌站搅拌,0-10m采用汽车泵浇筑。
10m以上采用物料提升机将混凝土输送到平台上进行对称浇筑。
所有筒身模板采用定型钢模,规格为:
1.43m×
0.65m、1.43m×
0.4m、1.43m×
0.2m、1.43m×
0.1m、1.43m×
0.15m,按周长分成20等分,在+0.1m处将整个圆周分成20等份,每等分安装6块1.43m×
0.65m的钢模,当收分到一定高度时用一块1.43m×
0.4m的钢模换掉一块1.43m×
0.65m的钢模,以此方法类推,这样就保证了对拉螺栓沿建筑物高度和水平方向等间距均匀排列,上下对齐。
对拉螺杆眼分布均匀规则,补螺杆洞前先把外露的穿墙管割除,所用补洞的砂浆用白水泥、普通水泥加入107胶配制,颜色要与筒壁混凝土颜色一致,不得有色差,补完洞后的表面要和筒璧混凝土表面一样光滑,若达不到即用细砂纸打磨平整,色泽达到和混凝土一致。
4.2烟囱积灰平台以上液压滑框翻模施工方法
(1)液压滑框翻模工艺的原理
液压滑框翻模工艺的原理是以烟囱筒壁为承力主体,通过附着于已具有较高强度的钢筋混凝土筒壁内的爬杆支撑操作平台,爬杆依靠提升架同操作平台连成整体,再利用液压千斤顶带动模板及整个施工装置的提升。
(2)液压滑框翻模工艺的特点
液压滑框翻模工艺是在吸取了无井架液压滑模和大模板等模板体系长处的基础上加以改进而形成的一种新型模板体系,具有质量容易保证、安全度较高、混凝土筒壁与内衬一气呵成、施工速度快等特点。
模板采用钢制模板结构,模板分块安装,模板的坡度和圆弧度易于调整和控制.可避免施工的累积误差;
在混凝土浇捣后,因混凝土与模板不作相对运行,使混凝土在爬架提升不会造成损伤,混凝土的质量可得到保证;
模板爬升就位精确,工具式支撑系统操作简单方便,劳动强度低,工效高。
内衬施工随筒壁爬模施工同步进行,筒壁防腐施工及内衬砌筑质量均可得到保证。
(3)烟囱液压滑框翻模施工装置的组成
液压滑框翻模施工装置由操作平台及垂直运输系统、模板系统、电动提升系统、电气控制系统等部分组成,详见下图。
a)操作平台及垂直运输系统
液压滑框翻模施工装置采用的操作平台及垂直运输系统与无井架液压滑模基本相似,由随升井架、平台辐射梁、鼓圈、井架支撑、拉杆等组成,平台辐射梁通过滚轮支承在内爬架上。
在操作平台中心设双孔随升井架,在中心鼓圈下设砌内衬吊平台。
b)模板系统
模板采用钢结构模板,每榀内外爬架上各悬挂一块模板,两块模板之间设收分模板,模板沿径向用顶紧丝杆可将模板固定或脱开。
c)提升系统
提升系统由爬架、提升架、工具式锚固件、提升设备等部分组成。
爬架为一榀设有多层平台的立体框架,在各层平台上可进行支模、拆模、筒壁表面修饰、爬架或提升架的锚固、安装、提升及拆除等工序的操作。
提升架是设在爬架内的一个平面刚架,提升架上装有四个导轮与爬架上导轨套合,提升架在爬架内可进行一个行程的相对运动提升架上安装有电动机、摆线针轮减速器、联轴器等提升设备,通过提升传动螺杆与爬架上传力机构连接,进行提升架与爬架两者之间的相互提升。
爬架与提升架各有四个挂钩滑道,滑道内安装挂钩,挂钩挂在用穿墙螺栓固定在筒壁上的爬升靴上。
提升设备选用液压千斤顶,与提升架组合而成,经对荷载及提升阻力验算,提升能力满足施工要求。
整个提升系统由中央控制柜控制,提升系统既可同步提升,也可以单个或多组提升。
(4)烟囱液压滑框翻模施工的工艺流程
本次施工采用二套定型钢模,每一模为一流程,施工流程如下:
绑扎第一模钢筋→立第一模模板→浇筑第一模混凝土→绑扎第二模钢筋→立第二模模板→浇筑第二模混凝土→绑扎第三模钢筋→拆除第一模模板→立第三模模板→浇筑第三模混凝土
第一、二节模板混凝土浇筑完→施工平台提升一模高度→绑扎第三节模板高度的钢筋→拆第二节模板翻上去立第四节模板→浇筑第四节混凝土→再提升平台完成进入下一个循环。
(5)烟囱液压滑框翻模施工装置的制作与安装的质量要求
烟囱爬模施工装置应严格按设计要求进行加工和安装,其质量控制要求详见表1。
表1液压滑框翻模施工装置制作与安装的质量要求
项目
质量要求
制
作
爬
架
截面尺寸
±
3mm
安
装
操
平
中心位置
5mm
全高弯曲
辐射梁位置
导轨
1mm
井架垂直度
〈5mm
提升架
外形尺寸
-2mm
标高
对角线
2mm
倾斜度
电机安装孔
模
板
拼缝缝隙
〈3mm
电机中心线
拼缝平整度
〈2mm
挂钩滑道宽
圆弧度
滑道位置
(6)液压滑框翻模施工装置的安装
电动液压滑框翻模模板施工装置的安装顺序依次为:
安装爬升架—→安装提升架和爬架—→安装模板—→安装操作平台—→安装垂直运输系统。
模板组装时应随时校正烟囱的中心线,模板全部组装完毕后进行整体校正,按烟囱中心线进行逐段检查,发现半径误差超过l0mm应松紧模板丝杠进行调整并做好记录,全部调整合格后交付验收。
(7)浇筑筒壁混凝土
模板和钢筋验收后开始浇筑混凝土,混凝土必须分层均匀交圈浇灌,每一浇灌层的混凝土表面应在一个水平面上,并有顺序地浇灌。
分层浇灌的厚度为300mm,各层浇灌的间隔时间,不大于混凝土的凝结时间。
在混凝土浇捣过程中应派二名有经验的工人看模,观察模板和支撑是否走动、变形及有无漏浆现象,浇捣混凝土是否符合规定等等,如发现问题应尽早处理。
当混凝土初凝后应及时转动对拉螺丝,待混凝土终凝后就可抽去对拉螺栓。
爬升模板施工过程中全部施工荷载均支承于已具有较高强度的筒壁中的爬杆上,为了保证筒壁有足够的承压能力,混凝土要保证出模强度,根据混凝土强度控制爬升速度,如混凝土强度不能满足施工要求,应减慢升模速度或采取其它能提高混凝土早期强度的措施。
当混凝土强度大于2MPa以上时,可以脱模,脱模时先松开收分模板的连接螺丝,同时松开钢丝绳上的倒链,使整圈模板仍分成16大块,转动模板丝杆即可脱开模板。
混凝土筒壁脱模后经修整即在其表面喷涂一层养生液或浇水养护。
脱模后要及时将钢板进行清理,并刷好脱模剂,然后再用。
为了加快进度,钢板应装备二套。
烟囱施工用的水泥要求使用同一厂家,同一品种的产品,以保证烟囱筒壁混凝土外观色泽一致。
(8)液压滑框翻模模板施工装置的提升
提升前应严格检查是否有障碍物影响提升。
提升架应单独提升。
每个行程高度的提升应在一个工作班内完成,提升完毕后应及时将提升架和爬架固定在混凝土筒壁爬杆上。
提升时要使模板和爬架均匀水平上升。
提升过程中,吊笼及拨杆应停止使用,吊架上不得堆放其他材料。
(10)牛腿施工
牛腿混凝土与筒壁混凝土一次浇灌完成。
利用内爬架上4根模板顶紧丝杆,将内模倾科到符合要求的位置,然后固定,绑扎牛腿钢筋及筒身的钢筋,验收合格后浇筑混凝土。
(11)烟囱中心及圆周度控制
烟囱的中心采用激光铅直仪和线锤控制,每升一模测控一次,半径用钢尺测控,并采用收分尺控制模板的坡度。
标高采用经纬仪从筒身外测控。
每次升模固定后,将烟囱地面的中心点用重锤引至上部操作平台,作为固定内外模板的中心控制和模板收分、坡度控制的基准点,同时通过校核筒壁外坡度以确保每模混凝土与下一模混凝土顺滑地连接。
4.3烟囱内衬作业方法
(1)烟囱内衬施工用的耐酸砖、耐酸胶泥等所用的原材料必须符合设计要求。
施工过程中应采取必要的防水措施。
筒壁内壁涂耐酸涂料二度,涂刷必须均匀,不得有涂料凝块,不得有漏涂和露底色现象,在牛腿位置的上、下300mm内要增涂一度。
(2)内衬砌筑工作在操作平台的内吊架上进行,每提升一次模板相应施工一模高度的内衬。
提升前要使内衬砌筑平台四周悬空,预留足够的收分量。
提升到位后,再将砌筑平台与四周筒壁撑紧,避免砌筑施工时平台过分摇晃。
(3)在砌耐酸砖内衬前,牛腿面首先要找平,以确保首皮耐酸砖砌筑平整、受力均匀,即先将牛腿上表面用水清洗干净,同时用1:
2水泥砂浆找平,其水平偏差不得超过20毫米。
砌筑时,第一皮砖要找中心线。
(4)耐火砖的砌筑采用分层轮砌法,即分层流水作业,层与层的操作面相隔1一2米,不许留直搓。
砌筑时采用挤浆法,先铺上耐火泥浆,持砖用力挤压,使水平及垂直砖缝内均挤满泥浆,再将多余的泥浆刮掉,其水平灰缝的饱满度不得低于90%。
内衬表面采用原浆沟缝,其灰缝厚度应控制在4mm左右。
内衬厚度为半砖时应用顺砖砌筑,互相交错半砖;
厚度为一砖时,用顶砖砌筑。
胶泥应及时清理,不要坠入筒壁与内衬之间的空隙内。
(5)隔热层的施工:
隔热层在砌筑耐火砖时同时填砌,上下皮、内外层垂直缝要错开,水平缝要刷胶泥。
牛腿处的滴水板要按设计要求找坡,滴水板边缘滴水线应顺直,不得有缺棱、掉角现象。
4.4定位测量
中心定位及半径控制:
在烟囱基础底板浇筑过程中,在中心点焊接一锥型钢筋,锥型钢筋中心即为烟囱的中心。
筒身施工中利用50kg线锤进行对中,每翻一板后,放下线锤以烟囱中心为中心作为模板的中心定位和筒身半径的控制,每隔10m用激光对准仪进行一次复核。
具体操作:
用钢卷尺标出该截面的外半径,以钢筋撑掌握壁厚来控制内半径,烟囱标高用卷尺沿千斤顶支撑竿进行标设。
4.5模板工程
本工程采用650mm×
1430mm(34