FDB机种结构设计分析实验汇总报告Word文档下载推荐.docx
《FDB机种结构设计分析实验汇总报告Word文档下载推荐.docx》由会员分享,可在线阅读,更多相关《FDB机种结构设计分析实验汇总报告Word文档下载推荐.docx(18页珍藏版)》请在冰豆网上搜索。
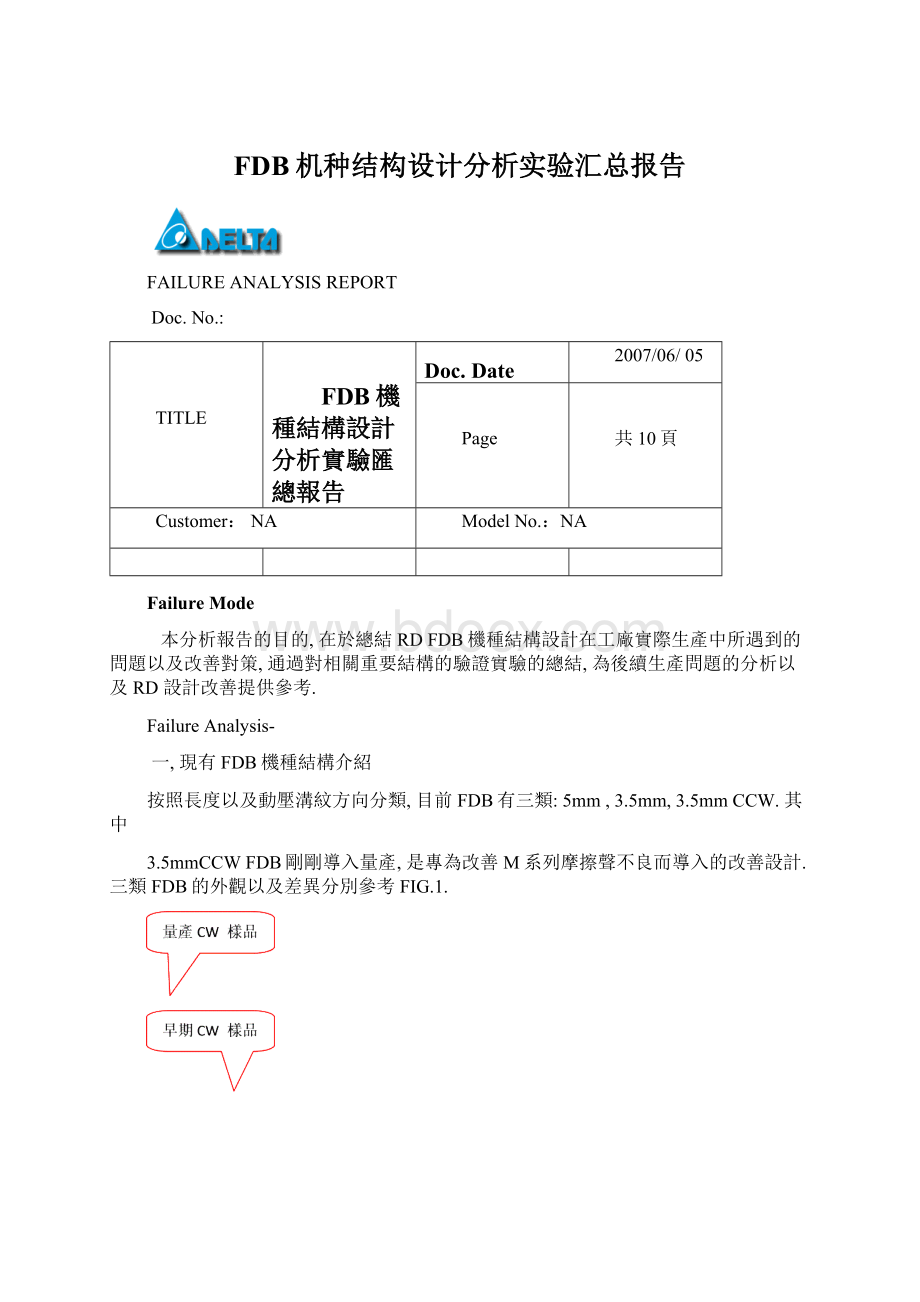
1.8*2mm
逆轉
墊片
無溝槽
3.5mm
FDB
目前為有溝槽
將設變取消溝槽
3430142400兩段
式干涉,軸向壓合
&
周向抱死(干涉量小於5mmFDB)
3430216500
1.2*2mm
無扣環/
TAB.1FDB結構/材料差異比較表
二,FDB機種在量產中所遇到的問題以及相關驗證實驗
FDB機種從導入至今,與結構有關的不良問題進行對應匯總,參考TAB.2.由量產問題統計,
與結構有關的問題可以歸結為三個,即:
1.銅套蓋脫落/高出;
2.摩擦聲不良(含3.5mmFDB縮孔);
3.因不當重工導致軸心與扣環結合力不足,在客戶端出現扇葉脫出卡死.該問題主要原因在於沒有嚴格執行正確的重工流程,破壞了相關的重要材料---扣環,造成與軸心結合強度下降,不能吸收外來的衝擊力.
軸心結構
量產問題
1.銅套蓋脫落/高出;
2.不當重工導致軸心與扣環結合力不足,扇葉脫出;
3.摩擦聲
1.銅套蓋脫落/高出
2.摩擦聲(含縮孔)
TAB.2FDB機種結構與量產問題點對應表
1.對銅套蓋脫落/高出的驗證實驗與分析
幾乎所有FDB機種都曾經發生過這種不良,其中尤以5mmFDB機種AT系列為甚.
異常現象:
流線至異音站發現有摩擦聲,拆開後發現是銅套蓋高出或者脫落(銅套蓋與銅套側壁規格高度0.08mm)全檢中也發現有銅套蓋高出或脫落.
原因分析:
序號
相關材料尺寸
重要配合尺寸(UNIT:
mm)
銅套蓋(UNIT:
銅套(UNIT:
1
上端外徑
4.04+/-0.01
上端孔徑
4.01+0.01/-0.00
過盈量
0.01~0.04
2
下端外徑
3.98+/-0.01
下段孔徑
3.96+0/-0.01
3
上段長度
0.34+/-0.02
端口C角
C0.05
實際配合
長度
0.19~0.23
4
頂部至
台階高
1.28~1.32
底部台階
到頂部
6.45~6.53
FDB與銅套軸
向幹涉實際長度
0.06
銅套蓋與銅套之間為緊配方式結合,銅套蓋高出/脫落主要與軸向以及徑向干涉量以及受力狀況有關,銅套蓋高出/脫落的直接原因是銅套蓋軸向受力,附圖FIG.4是該機種的設計LAYOUT,可能產生軸向力的位置有三處:
銅套蓋與銅套上段干涉位置--該位置的軸向力產生主要與壓合過程中銅套與銅套蓋結合面處材料流動有關;
銅套蓋與銅套下段干涉處--該處因為圓角,以及壓合中首先產生軸向翻翹變形有關;
銅套蓋與FDB軸向干涉位置—軸向干涉,直接產生軸向推出力.
FIG.4AT8銅套蓋受力圖TAB.3AT8重要配合尺寸
依據已有實驗結果,可知導致銅套蓋高出/脫落的主要原因有三個:
銅套蓋與銅套軸向干涉量不足&
軸向受力&
壓合銅套蓋製程不良.為增加銅套蓋與銅套軸向干涉量,設變改善銅套蓋,將銅套蓋上段與銅套軸向干涉長度增加到0.65mm,新舊銅套蓋結合力對比實驗數據參考TAB.4.
新銅套蓋結合力(kg)
舊銅套蓋結合力(kg)
16.5
10
4.3
15.3
11
3.1
15.4
12
4.8
16.3
13
4.4
5
15.7
14
2.8
6
13.2
15
5.4
7
16
8
14.8
17
4.5
9
14.5
18
2.7
AVG.
15.2
4.0
SIGMA
1.0
0.9
TAB.4AT8新舊銅套蓋結合力對比實驗數據
銅套蓋軸向受力主要來源于底部墊片,並與軸向干涉量直接相關.表現于墊片壓縮反彈而產生彈力.墊片的彈性係數對該力大小有著決定影響,墊片原來材質為MYLAR,變更後為NYLON66,兩種墊片彈性實驗數據參考TAB.5.
MYLAR
NO.
實驗
項目
數據
第一次
壓力(kgf)
第二次
墊片壓縮後
厚度(mm)
395
0.25
402
401
0.24
399
411
410
0.23
412
409
422
421
0.22
423
420
433
434
0.21
431
430
429
444
443
0.2
441
439
440
456
455
0.19
446
445
465
0.18
453
452
474
473
0.17
464
454
480
0.16
475
476
467
489
487
0.15
497
495
0.14
493
491
485
486
差值
102
94
0.11
98
92
90
85
K
(kgf/mm)
890.91
863.64
795.45
NYLON
382
384
385
387
383
389
388
391
386
396
390
394
398
397
392
403
405
406
404
407
408
413
28
27
0.09
31
29
305.56
333.33
300.00
TAB.5兩種材質墊片彈性係數測試數據
由數據可以看出,NYLON66墊片彈性係數約為MYLAR墊片的1/3,同時考慮到過軟墊片會影響FDB排氣性,也不宜選擇過軟材質,在經過耐NS3油&
信賴性測試評估後,對墊片材質進行了設變.
影響銅套蓋與銅套結合力的製程因素,主要有:
1)壓合銅套蓋速度2)壓頭是否為彈性壓頭3)銅套蓋管控高度
為實現對製程參數的精準控制,可以通過使用電子壓床壓合銅套蓋來輕鬆做到.使用電子壓床與普通氣壓床生產的比對結果參考TAB.6.
機種
時間
線別
製程條件
銅套蓋高出/脫落不良狀況統計
KDB05205HC
-6B24
9/159:
00-11:
40
F10
電子壓床+剛性壓頭+定行程模式;
接近速度166mm/S,壓合速度0.5mm/S暫停時間0.2S,調機銅套蓋高度0.06,0.07,中間抽測0.06,0.06;
扭力180.180.400(有異常,推測CAP沾膠)
在流線中有少量舊銅套PILLOW混入(<
30PCS),有產線舊的不良品重新流線(<
10PCS);
摩擦聲5PCS,其中1PCS銅套蓋高出(舊銅套高出0.33MM);
其餘不良為抖動,卡PILLOW;
下午1:
40確認,摩擦聲不良7pcs(含上午不良品)銅套蓋高出2pcs(含上午不良品),全部為舊銅套;
約2:
00開始同時使用氣壓床,未繼續統計.
-6B26
40-11:
F12
氣壓床+剛性壓頭
9:
40-10:
20,異音室27PCS銅套蓋高出全部為舊銅套;
10:
20-11:
40共有銅套蓋高出/脫落不良品48PCS,6PCS脫落(2PCS舊銅套,4PCS新銅套);
50以後使用新銅套PILLOW
TAB.6使用電子壓床與普通壓床生產對比
從使用電子壓床壓合銅套蓋與氣壓床壓合銅套蓋的效果比較可以看出,壓合速度,壓合瞬間有無緩衝,對銅套蓋壓合品質有較大影響,對目前產線製程條件進行匯總比較,其優缺點以及推薦產線使用的製程條件,參考TAB.7
製程類別
治工具搭配
設定條件
優點
缺點
產線製程
氣壓床+
剛性壓頭+
定心底座
壓床壓力5-6kgf/cm^2,速度不定
換線容易
衝擊速度快,速度無法定量管控調整銅套蓋定高度時,調機困難
彈性壓頭+
壓床壓力5-6kgf/cm^3,速度不定;
壓頭預壓力
與剛性壓頭相比衝擊減小,但要實現銅套蓋的定高度控制時,調機困難
要實現銅套蓋的定高度控制時,調機困難
電子壓床+
壓合速度,
高度設定
壓合速度兩段式,高度可以設定,壓合高度一致性好
離線作業,取放不便,產能有限,兩台電子壓床才能供一條線
建議做法
定心限高底座
壓床壓力5-6kgf/cm^3,速度稍慢合適,建議100MM/S以內,具體還需驗證
能保證定高度壓合,衝擊較小,壓合力可以較大從而保證壓合到位,且換線調機迅速
不能夠控制壓合速度,定位精度因磨損存在需定時抽檢
TAB.7目前產線製程以及建議做法
導致銅套蓋高出/脫落並在產線發生過異常的其他因素:
1>
彈性壓頭彈簧斷裂;
2>
多裝一個墊片;
3>
銅套上端孔未倒C角;
4>
銅套與銅套蓋干涉位置壁厚.
結論:
銅套蓋高出/脫落為涉及產品信賴性的重大品質問題,通過設計改善&
製程管控的方式可以使該問題得以解決;
同時值得慶幸是客戶端並沒有發生與之相關的客訴反饋,這應當歸功於我們堅持異常解決以前全檢出貨,確保出貨品質的臨時對策.
2.摩擦聲不良的驗證實驗與分析
摩擦聲不良在5mmFDB扣環機種以及3.5mmFDB機種中曾經發生過嚴重不良,代表性的機種有AKITA(KDB0505HB-5K86,5mmFDB扣環)M系列(3.5mmFDB),兩個機種摩擦不良發生的具體原因分析如下:
2.1AKITA(KDB0505HB-5K86)摩擦聲分析
該機種早期設計為扣環結構,量產初期不良現象為動聽摩擦聲與靜聽摩擦聲,不良率約15~20%.不良品有扇葉浮起現象,為明顯的磁偏不足,摩擦聲部分來源于軸心運轉中與扣環摩擦,改善對策是修模扇葉拉高軸心,加大磁偏,修模改善後產線仍存在5~10%的不良.在觀察不良品軸心過程中發現軸心得兩處溝槽有嚴重的毛刺,而且規格要求的R0.05角位置,實物卻為利邊,這樣就導致毛刺&
利邊刮傷FDB,並與FDB內壁摩擦導致不良.不良軸心參考FIG.5.
FIG.5AKITA不良軸心照片
將此不良反映給軸心廠商(東莞金益成),回覆通過增加噴砂製程來去除毛刺,但對於R0.05卻無法做到,而且從後來提供的樣品確認,利邊確無改善.取消扣環的設計變更也給摩擦聲改善帶來契機,產線試投500PCS取消溝槽的軸心與當天有溝槽軸心良率統計狀況參考TAB.8
類別
投入總數
(PCS)
轉動卡住声
靜聽卡住声
不良數量
不良率
4090
310
7.58%
0.20%
TAB.8有無溝槽軸心摩擦聲不良率比對數據
小量試效果確認后,RD設變,將軸心變更為無溝槽軸心,設變完成後,該機種摩擦聲不良率維持在2%以內,生產順利,未發生過類似異常.
2.2M系列(3.5mmFDB)摩擦聲不良(含縮孔不良)分析
M系列為最早使用3.5mmFDB的量產機種,量產後摩擦聲不良就一直存在,從已知的分析結果看,其影響因素有三方面:
原材料,結構設計,製程條件.原材料方面,主要是通過比較3.5mmFDB早期工程模具品與量產模具品的動壓溝差異發現,前者動壓溝品質較好,溝紋清晰,深度明顯深於後者,內孔表面光潔度較好;
而量產品動壓溝則模糊,較淺,內孔表面較為粗糙.結構設計方面,該系列機種為無扣環,無墊片且使用有溝槽軸心機種,組裝扇葉以及FDB在被銅套蓋壓合的過程中少了緩衝保護,就易發生FDB縮孔和動壓溝破壞,從而產生摩擦聲.製程條件,主要指壓合銅套蓋的速度,壓頭是否為彈性壓頭,以及銅套蓋壓合的高度,三者不當時即會導致FDB的縮孔和動壓溝紋的破壞,產生摩擦聲不良.
量產中發現,該系列中順時針(CW)運轉的機種摩擦聲不良率,以及發生縮孔不良的狀況明顯少于逆時針(CCW)運轉的機種,而兩者的差異僅有FDB放置的方向不同,順時針運轉機種環形逃氣槽在上,與銅套蓋接觸面積較小因而可以吸收外來壓力產生較大變形量;
而逆時針運轉機種環形淘氣槽在下,上端與銅套蓋接觸面積較大,下端逃氣槽與銅套底部接觸面積也較大,導致受外力作用時易產生縮孔與動壓溝破壞.對該系列機種的改善,主要針對增加墊片以及CW,CCW風扇FDB放置的變形改善來進行.
2.2.1墊片對FDB機種摩擦聲的影響
由於M系列機種增加墊片的相關資料疏於整理導致資料丟失,同時實驗結論與AKITA機種墊片實驗一致,故可以借監AKITA有無墊片對摩擦聲影響的相關結果.
從打樣30PCS無墊片銅套驗證結果看,無墊片的不良率為3.3%(1/30),不良品靜聽即有摩擦聲,且另有7PCS有輕度尾音(尚屬允收);
但是有墊片(量產正常結構)摩擦聲不良在2%以內(無尾音不良發生),在無異常狀況時,該機種總不良甚至可以做到1%以內.量測FDB內孔真圓度,有無墊片的圖片參考FIG.6,FIG.7
FIG.5AKITA有墊片FDB真圓度(產線製程品,CAP高0.02MM)
FIG.5AKITA無墊片FDB真圓度(CAP高0.04MM)
由真圓度量測可以看出:
有墊片FDB動壓溝紋完整,表面光潔;
2>
無墊片FDB在壓合中受到破壞,動壓溝紋雖然完整,但已經出現崩裂,而且是動壓溝的上下兩段都被破壞;
有墊片結構下,可以降低FDBD對銅套蓋壓合高度的敏感度.
2.2.2FDB原材料對CCW機種摩擦聲與縮孔的影響
CCW機種因為FDB放置方向不同而造成較高的摩擦聲與縮孔的不良率,改善的方法是導入CCW機種專用FDB,即CCWFDB,兩端逃氣槽形狀參考FIG.1,目前CCWFDB已經導入量產,未發現縮孔不良,摩擦聲不良率也有較好改善,不良率在3%左右.
結論:
FDB機種摩擦聲改善,主要是通過設計變更實現.通過該問題的分析與解決,使我們對FDB的使用以及5mm/3.5mmFDB結構的優缺點有了更為深入的認識:
底部墊片對於FDB受壓具有一定保護作用;
軸心溝槽因為加工工藝的限制導致R0.05無法加工,進而引發組裝后的摩擦干涉;
3.5mmFDB強度不及5mmFDB,結構上沒有墊片緩衝,同時還存在原材料的其它不良,是導致M系列量產不順利的主要原因.
導致摩擦聲不良的其它原因:
點油量不足,導致油膜無法形成;
FDB方向放置錯誤,造成油膜無法形成,軸心與FDB摩擦,且迅速惡化失效;
異物顆粒侵入.
CONCLUSION
FDB機種量產後,以其獨特的優勢解決了NBFAN異音問題,使得異音不良率為0成為可能,但同時由於FDB使用與固定方式存在較高的要求,所以也給RD的結構設計帶來考驗.我司設計
採用較為簡單易行的方式實現了FDB的定位,大大降低了製程的難度,作業效率較高,但FDB與銅套蓋的剛性接觸以及外力衝擊下的快速壓合,也給產品品質帶來隱患.
儘管在FDB機種量產中遇到了諸多困難,但RD直接與間接的參與,以及RD與工廠端的良好互動,為生產異常的快速改善提供了源源動力!
Reportedby:
李鴻波
Checkedby:
Approvedby: