酸性电镀铜基本资料Word格式文档下载.docx
《酸性电镀铜基本资料Word格式文档下载.docx》由会员分享,可在线阅读,更多相关《酸性电镀铜基本资料Word格式文档下载.docx(16页珍藏版)》请在冰豆网上搜索。
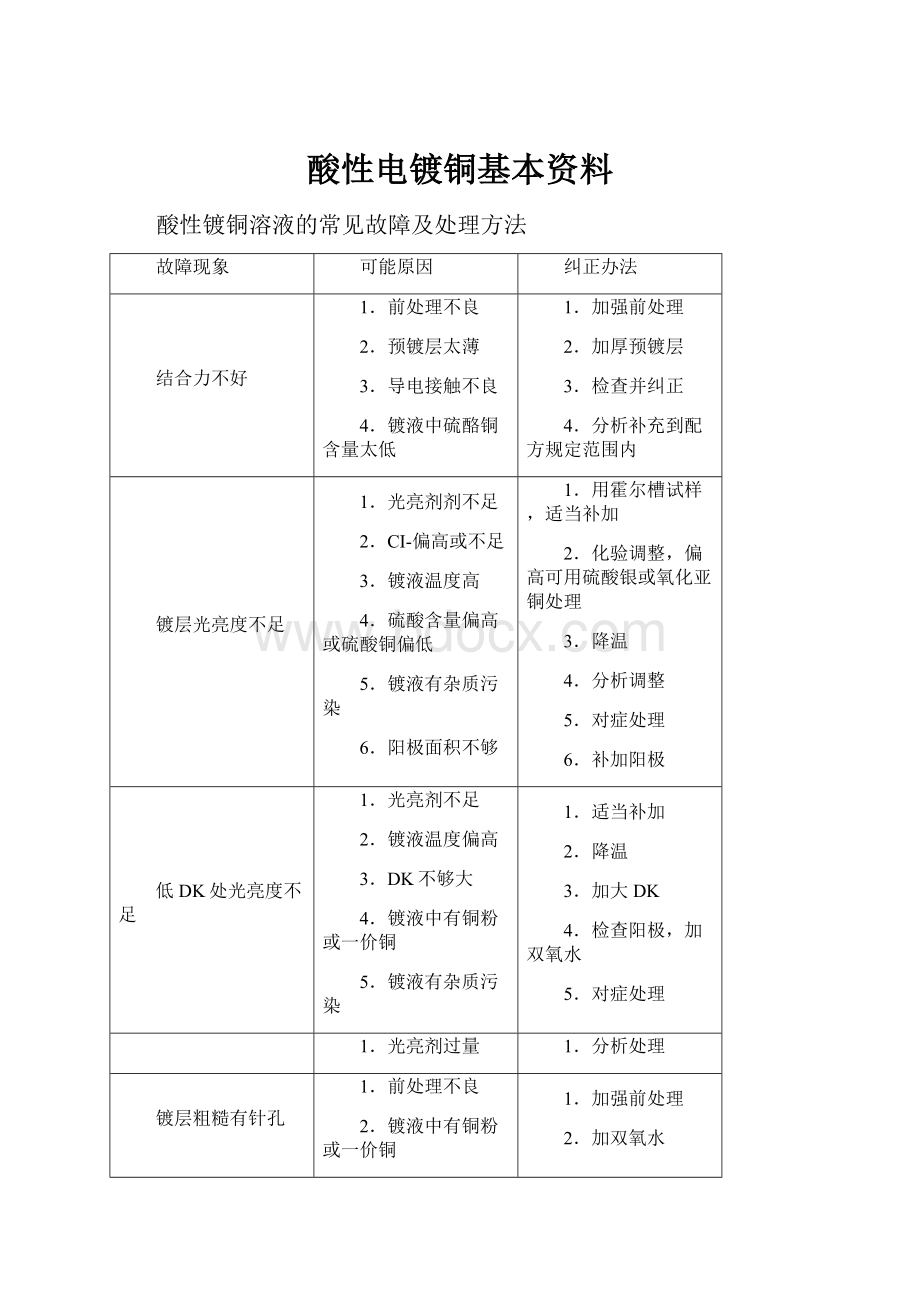
3.DK不够大
4.镀液中有铜粉或一价铜
1.适当补加
2.降温
3.加大DK
4.检查阳极,加双氧水
1.光亮剂过量
1.分析处理
镀层粗糙有针孔
2.镀液中有铜粉或一价铜
3.CI-不足
4.镕液内有杂质乐势
2.加双氧水
3.加计算量盐酸
4.对症处理
条纹镀层
1.CI-偏低
2.光亮剂过量
1.加计算量盐酸
2.调整之
镀层边缘有毛刺或烧焦
1.镀液温度偏低
2.硫酸铜浓度偏低
3.DK过大
1.适当升温
2.适量补充
3.适当降低DK
1.润湿剂过量或不足
2.310B不足
1.霍尔槽小试调整
2.补充
前处理不良
加强前处理
整平性不良
2.硫酸含量偏高
3.镀液有杂质污染
1.加入计算量盐酸
2.调整
3.对症处理
1.铁杂质过量,此时阳极上往往有蓝色结晶析出
1.更换部分或全部镀液
氯离子含量高会影响酸性亮铜层质量
酸性光亮镀铜溶液中含有适量的氯离子(30~90mg/L)能提高陵层的光亮度和平整性,还能降低镀层应力。
但不可过多,否则镀层失去光泽,光亮度下降,光亮范围狭窄,镀层还会产生树枝状的条皎,阳极发生钝化,电压明显上升,电流升不上去。
为避免过多的氯离子进入镀液,配制溶液用水必须用去离子水,瓯然配方中有少量的氯离子要求,但也无需单独加入,因为配制材料即会有少量氯离子存在,基本能满足要求。
若溶液中有过高的氯离子存在,可加入计算量的氧化亚铜予以群决。
某厂新配制的1000L酸性亮铜溶液,使用的材料除去离子水之阶,所有材料都是试剂级的,配成试镀时发现镀出样板平整性很差,也不太光亮,还见有条纹。
根据试样情况,经多方检查,无论是配制过程,还是使用材料均.无可疑之处,最后考虑到可能与氯离子含量有关。
估计氯离字含量过高的可能性不大,因为使用的材料都是试剂级的,于是吸出5L溶液,先在此小槽中镀出样板,然后加入250mg氯化钠(当时无试剂级的盐酸)约含30mg/L氯离子,然后在同样工艺条件下再镀样板,结果表面质量明显不一样。
由此可见,凡是用试剂级材料配制的光亮酸性镀铜溶液,若试镀结果质量不够理想的,有可能是氯离子浓度太低,但补充时还是先做小试为好,以免因其他原因而加入过高氯离子后引出麻烦。
用水不当引起酸性镀铜层的质量故障
由水质不符合酸性光亮镀铜工艺要求而引起镀层质量或溶液遭到污染的例子很多,在此仅举一例。
某乡办电镀厂发生一起光亮酸性镀铜的槽端电压升高、电流升不上去,继续升高电压时电流虽暂时能上去,但不久又回落下来,镀层光亮区狭窄,补充光亮剂也无济于事。
阳极上还蒙有一层灰白色的膜等质量故障。
上述现象与溶液被氯离子污染引起的相似。
据查是用水不洁所故。
原来该厂地处偏僻,靠用井水,且井水由于电镀废水未能正规治理,就地排放而被污染,长期用此井水清洗工件又难免被带入镀槽,因而出现上述质量故障,由此可见电镀用水对镀层质量影响很大。
酸性亮铜上镀不上牢固镍层
有的酸性光亮镀铜溶液中含有CB型混合添加剂,有的还含有聚乙二醇,这些物质会在镀层表面形成憎水膜,憎水膜面上是难以沉上牢固镍层的。
故镀铜后尚需经过稀硫酸除膜处理,这一工序很重要,有时因被忽略而常难以获得牢固的镍层。
光亮酸性镀铜层作仿金底层的故障
仿金镀与装饰性镀铬一样,本身无光泽,靠光亮的镀层为底层来映照。
某厂仿金镀采取酸性光亮镀铜为底层,酸性光亮镀铜虽然光亮性方面能满足这方面要求,但由于仿金属厚度相当薄,而且存有孔隙,在大气中极有可能通过孔隙促使底层铜加速氧化,当底层铜开始;
氧化时,又会从仿金镀层的孔隙中泛出来,致使仿金层变色,这一故障频频出现。
了解到上述原因,并改用光亮镀镍代替酸性光亮镀铜之后,这一仿金属的变色现象再也未曾出现过。
酸性亮铜阳极材料的选择
酸性镀铜的阳极要选用由专业生产厂家供应的含磷阳极板,这是因为铜阳极在硫酸溶液中会产生铜粉,从而导致镀层产生毛刺、粗糙,由于电铸时还可能积成瘤子。
铜阳极的含磷以0.2%~0.4%为好,含磷量太低效果不好,易产生铜粉,含磷量太高时(高于l%),阳极表面会出现一层厚厚的膜层,使阳极处于钝化状态还会污染溶液。
自己铸造往往满足不了这一要求,可在电镀材料供应部门选购。
为了防止铜阳极中的不溶性杂质落入镀液内而影响铜层质量,必须用涤纶布包扎极板。
阳极电流密度太大、或阳极板含P木适当,造成阳极氧化不完全,其反应为:
Cu-e→Cu+
镀液体中二价铜离子在阴极上完全还原为:
Cu2++e→Cu+
酸性亮铜溶液被氯离子污染
某厂有一只容积为800L的酸性光亮镀铜槽。
一段时期镀出工件的光亮度越来越差,出现白雾状,低电流密度区也不亮,使用的铜阳极表面附有一层粉末状的白色产物,电压也升不上去,只得停产,厂方为此十分着急,笔者应邀参加了上述故障的讨论。
现将已查清的故障产生原因并处理结果简述如下。
该厂的酸性光亮镀铜液是请人配制的,使用还不到两个月,开始使用时效果很好,镀出铜层光亮细致,电流、电压都正常,使用不到一个月后镀层的光亮逐渐变差,最后出现上述现象,再也无法使用。
在讨论会上有人提出配制溶液时十二烷基硫酸钠和光亮剂的加法不当,也有人提出配制溶液时是否忘了加氯离子,笔者认为以上分析的原因是不太可能的,若是溶液配制工艺有误,那么开始使用时问题即应暴露,而不是使用近一个月后才发生变化的,再则,目前所获镀层的症状也不像是上述原因引起的,相反却很像是溶液中氯离子含量过高所致,但氯离子从何进入槽液中呢?
笔者从光亮镀铜的生产线上进行逐道的检查,查到氰化铜后的中和槽(又称活化槽)时闻到了有刺鼻的盐酸气味,经询问确是盐酸,并发现工人操作时把工件从中和槽中取出后即在旁边的清水槽中浸一下就挂入到酸性光亮镀铜槽中去电镀。
此清水槽用pH试纸测得的pH值是4.8,可见该清水槽中氯化氢浓度是相当高的了。
从以上的所见所闻对锾铜槽中氯离子含量过高是可想而知了。
为了证实上述分析的可靠性,从光亮镀铜液中取出两烧杯溶液,将其中一只烧杯中的溶液进行除氯处理,在同样条件下两烧杯中镀出的工件进行比较,经除氯处理的一只烧杯中镀出的铜层光亮似镜,而未处理过的一只烧杯中镀出的工件表面仍有一层白雾状产物,镀层不光亮,{从以上的试验结果来看,光亮镀铜槽液被氯离子污染是无疑的了。
根据厂方要求,随后把800L的光亮镀铜溶液进行了除氯处理,恢复了正常生产,并向厂方提出了工艺上的改进措施。
亮铜溶液中氯离子用锌粉处理,步骤是:
在搅拌下加入2~3g/L锌粉,搅拌30min后再加入2~3g/L活性炭,再继续搅拌2h,静置后过滤。
处理之后需补充光亮剂。
工艺上的改进措施要求如下。
(1)中和槽(活化槽)溶液改用5%~8℅的稀硫酸代替原先用的稀盐酸。
(2)工件经中和处理后在清洗过程中要抖动和摇摆。
(3)清水槽的水要流动,每天还应更换两次,用静水是不符合要求的。
(4)镀光亮铜前增加一道蒸馏水漂洗,以提高工件表面的净洁性。
光亮镀铜溶液经处理后三个多月生产一直正常,未曾发生过质量问题。
操作说明:
(1)吸附用的活性炭要选优质的,劣质活性炭含有氯离子,会造成二次污染;
(2)治理方法效果显著,但必须认真、细致,不然有可能引起副作用。
酸性铜前的预镀
钢铁件酸性镀铜之前必须先经预镀铜或预镀镍,否则钢铁件表面印会被镀铜溶液所浸蚀,出现置换铜层,使酸性铜无法在此基材上正常沉积,不但工件因腐蚀而报废,溶液也会遭到破坏。
故预镀层不但要有一定的厚度,而且结合强度要好,并无孔隙、砂眼以及海绵状镀层等露量问题的存在。
对于形状复杂并质量上有严格要求的工件还需将预度的电镀工艺改为化学镀工艺。
以保证工件的所有表面都能沉上预镀层。
酸性亮铜层表面出现橘皮状皱纹
某电镀厂的酸性镀铜件有近20%的表面全部或局部呈橘子皮状驹皱纹。
厂方对镀铜溶液准备要大处理。
其实这一现象问题不在溶夜,因为若是如此,则不可能有的表面完好,而有的出现皱纹。
据笔著分析是镀前处理不彻底引起的。
为了证实这一估计的可能性,笔者取l0块5cm×
10cm的铁板,弪充分进行前处理后镀铜,镀出铜层表面完好,避免了大处理仍不能睥决的工时、材料等的浪费。
这类现象有时确实较难鉴别,如工件表面出现细麻状,待镀层稍萝时变为类似橘皮状,这种情况若遍布于整个工件表面,则极有可能黾Cu+的影响及溶液中M光亮剂不足等因素引起的,此时则需要采炙相应措施予以解决。
酸性亮铜层表面产生毛刺
铜层表面出现毛刺是一价铜干涉的结果,一价铜被水解成氧化嘲铜而产生粗糙镀层,有时产生铜粉或海绵状镀层。
镀铜层出现毛刺搠是由此而产生的。
由于一价铜析出电位比二价铜析出的电位低,于是总是优先于濯价铜的析出,从而影响二价铜有规律的电结晶过程,导致上述现象。
为排除上述因素的干涉,在溶液维护上首先要注意如下问题。
(1)质量。
使用的阳极要选用定点生产的专业厂产品淘使用中如发现无棕黑色薄膜,或局部无棕黑色薄膜则应停止使用。
前是含磷量低,后者是含磷量不均匀。
阳极要选用含磷量0.1%~0.3%铜阳极,操作时不要移动阳极,以免磷膜掉下来污染溶液。
并使工件表面产生毛刺。
要保证阳极面积与阴极面积之比不得小于l.5:
1,阳极套不萤过厚,以防堵塞(以单层涤纶布为宜)。
阳极挂钩与极杠之间接触要良好。
(2)镀件需带电人槽。
带电入槽可减轻工件浸蚀。
出槽时工件未取尽前不要关闭电源,工件与挂具非接触部位也宜经过绝缘处理
(3)保证硫酸浓度。
硫酸具有降低镀液电位、增强镀液导电雠能、防止硫酸铜水解成氧化亚铜的危害,从而减少镀液中铜粉晦作用。
(4)定期添加适量的双氧水。
添加时宜直接加入到槽底并需激烈搅拌。
添加双氧水是抑制Cu+过多积累的有效途径,当溶液中超过1.5g/L的Cu+时,镀出工件即可见有毛刺出现。
要注意的是勤加少加,以防光亮剂失效。
(5)防止产生置换铜层。
对于形状复杂件要注意预镀层的质量,防止由此而产生置换铜层。
这一方面特别要注意管状件,管状件内壁预镀铜或镍都是镀不上的。
因为工件一进入光亮酸性镀铜槽即会开始与亮铜溶液发生置换反应,结果溶液中产生大量铜粉,详见反应式:
Fe+CuS04→Cu↓+FeSO4
此外还存在着铜粉与二价铜离子的歧化反应,这时又会产生一价铜。
为解决这一问题,必须把预镀铜工序由氰化预镀铜改为化学镀铜或化学镀镍,只有这样才能保证管件内壁全部镀上预镀层,才能避免陂酸性光亮镀铜时再出现置换反应。
酸性亮铜溶液中硫酸铜结晶析出
某厂在配制酸性亮铜溶液时将57g/L硫酸误按57mL/L配制,配成后由于硫酸的加入量近多一倍,影响了硫酸铜的正常溶解,有大量的结晶析出。
笔者用烧杯舀出半杯观察,溶液的颜色并不深,大体验证确是硫酸加过量了。
配方中若无单独标准,其计量单位应该是统一的,若有单独标的则另当别论。
这次故障采取适当稀释、使用时适当加温的方法来解决。
酸性亮铜出现光亮度不足
酸性亮铜出现光亮度不足酸性光亮镀铜出现失光,通常多由溶液中光亮剂失调引起,但并非都与此有关。
笔者曾遇到这样一起故障,有的在工件的上部,有的在工件的尾部无光泽,而有的部位仍较光亮,该厂工艺员不假思索地正在第二次补加光亮剂。
结果,原先不光亮的部位仍是暗淡无光,而原先较亮的部位显得有点发雾。
据此情况,建议检查一下阳极板,阳极布置不匀、溶断掉落、使用过久耗尽等都有可能引起工件的部分地区电流密度过小而出现上述故障。
经检查确系由此原因引起的,问题也由此而得到解决。
酸性亮铜溶液中硫酸含量渐低
酸性亮铜溶液中硫酸含量渐低某厂酸性镀铜是静镀的,施镀过程中产生的一价铜离子得不到氧化,不得不经常添加双氧水。
且溶液的分散能力低、镀层粗糙的现象总是改变不了。
实际上,用双氧水氧化一价铜的同时会消耗一定数量的硫酸:
2Cu++H2O2+2H2S04→2CuS04+2H2O+H2↑由上列反应式换算后可知,氧化lg一价铜需8.1g30%的双氧水和1.55g的硫酸。
当硫酸浓度低到一定程度时,溶液出现了与一价铜过高时的类似现象,也就是说双氧水越来越不起作用了。
要解决上述问题,必须在用双氧水氧化一价铜的同时添加其所消耗量的硫酸,不然还会引起铜盐水解沉淀、阳极钝化等不良现象出现。
酸性光亮镀铜层发雾发花的六大因素
酸性光亮镀铜层发雾发花的六大因素硫酸盐光亮镀铜液的基础成分是硫酸铜、硫酸和市上有售的光亮剂。
硫酸铜是供给镀液中的铜离子,硫酸能起到防止铜盐水解,提高镀液导电能力和阴极极化作用,光亮剂则在相应的溶液温度和电流密度的配合下能获得光亮似镜的铜层质量。
硫酸盐光亮镀铜工艺在电子工业中主要用在印制线路板和镀光亮镍之前的底层,以提高光亮镀镍层的光亮度并缩短光亮镀镍时间。
工艺技术上由于钢铁件不经预镀是不能直接镀铜的,故镀铜前、后处理工艺要掌握好。
溶液维护方法除上述基础成分之外,还要控制好十二烷基硫酸钠浓度和氯离子浓度,且阳极的合理选用,以防一价铜的形成。
酸性亮铜溶液中镀出镀件出现雾状、发花主要与以下因素有关。
(1)十二烷基硫酸钠含量过低。
这时可加入适量的十二烷基硫酸钠予以验证,如未见有所改观则可予以否定。
(2)聚二硫二丙烷硫酸钠过高。
这时可采取适当稀释溶液并补充适量其他光亮剂,若见有效即可认为是聚二硫二丙烷硫酸钠过高,可按比例予以调整,也可用双氧水来降低其含量。
(3)溶液遭到油污祷染。
可以用肉眼观察,也可用双氧水、活性!
炭联合处理,处理后加足光亮剂、添加剂后试镀,确认有效后可按此{法进行处理,此法也适用除去溶液中的有机杂质。
(4)氰化镀铜前或后工件表面未经清洗干净,有油污或有镀液。
(5)配送的电流密度过小。
这时可提高电流密度做验证试验。
(6)溶液中有铁杂质的存在。
酸性镀铜溶液中存在少量铁离子对镀铜层质量无明显影响,这是因为铜的电位较正之故,但当铁的含量过高时也会出现镀层发花,确定原因可通过化验证实。
用硫化钠处理氰化镀液中重金属杂质
用硫化钠处理氰化镀液中重金属杂质氰化镀铜溶液中加入硫化钠后,溶液中的铅、镉等有害杂质即能沉淀后除去,铜离子本身因为有游离氰化钠的存在,不会因此而遭到破坏,但当游离氰化物不足时,溶液中的铜离子也同样会被沉淀。
为避免这类现象的发生,在沉淀氰化物镀铜溶液中的金属杂质时首先要补足游氰化物含量。
氰化镀锌溶液中加入硫化钠能获得与加入氰化镀铜溶液中同样的效果,但仍不能除去铜。
氰化镀银溶液中若混入金属杂质,则不可用硫化钠来处理,否则溶液将会遭到破坏。
在利用硫化钠来除去某些氰化镀液中的金属杂质时,溶液浓度宜适当稀释,添加速度要慢,且需剧烈搅拌。
氰化镀铜工艺中六点注意事项
氰化镀铜工艺中六点注意事项
(1)不宜采用高电流密度,这是因为阴极极化作用是随着电流密度的升高而增高,从而降低了电流效率;
(2)镀液不宜剧烈搅拌,否则溶液中的氰化物易遭到破坏;
(3)镀液不宜加温过高,否则溶液中的氰化物会随着温度的升高而加速分解;
(4)镀液遭到有机质污染后不可用双氧水处理,以免镀液中氰化物遭到破坏;
(5)工件入槽时必须充分清洗,以免酸性物质进入镀槽与氰化镀液相遇时产生极毒的氢化氰气体而引起中毒事故;
(6)溶液毒性大,工作时有极毒气体逸出,要在有排风的条件下方可操作。
氰化镀铜溶液中碳酸钠过快积累
氰化镀铜溶液中碳酸钠过快积累某厂氰化镀铜出现小泡、脱皮、呈不均匀的褐色宜十分粗糙,甚至出现可擦去的粉末状铜层。
镀液也因此而出现混浊,沉积速度减缓,阳极表面有致密并较厚的灰色膜层。
笔者应邀参与讨论。
笔者分析,有可能溶液中积累过多碳酸钠,遂取了一小瓶溶液放在冰块中冷冻试验(该厂有现成的用来冷却铝阳极氧化溶液的天然冰块),不多时只是瓶内全是白色晶体,犹如一瓶冰醋酸,看来这一故障由溶液中碳酸钠积累过多引起是无疑的。
于是利用现有的天然冰块,采取冷冻方法进行结晶沉淀处理之后,上述质量问题立即得到解决。
氰化镀铜溶液中碳酸钠的允许量为80~1009/L。
其来源主要是由氰化钠分解形成的,当溶液中的氰化钠遇到空气中的二氧化碳时即起下列反应:
2NaCN+H2O+C02→Na2C03+2HCN当阳极钝化时还有下列反应发生:
2NaCN+2H20+2NaOH+0→2Na2C03+2NH3↑故要控制碳酸钠过快积累,除要避免溶液与空气过多接触之外,还要防止阳极钝化,而防止阳极钝化除需保证足够阳极面积之外,还要保证溶液中足够的游离氰化钠含量。
为缓解上述现象的形成,笔者还建议该厂在原碱式碳酸铜、氰化钠和碳酸钠组成配方的基础上添加40g/L的酒石酸钾钠。
酒石酸钾i钠在氰化镀铜溶液中不仅是一种较强的络合剂,还能活化阳极,促使;
阳极正常溶解,有利镀层获得细致光亮和稳定氰化钠过快分解,缓解碳酸钠过快积累。
氰化镀铜溶液中铜离子下降
在通常情况下,氰化镀铜溶液中铜离子浓度有上升趋势,这是因静铜阳极有化学溶解倾向,阴极电流效率又较低。
但一次故障是铜离子浓度下降。
铜离子的下降与阳极钝化有关,阳极钝化通常是阳极面积过小或溶液中游离氰化物浓度过低引起的。
经检查铜阳极确实覆有灰白色膜。
在进一步检查中发现,用帆布做的布袋已结成不透水的破壳,这显然会影响离子的正常扩散,从而造成布袋内外浓差极化增大,阳极溶解下来的铜离子无法通过已结成硬壳的布袋与氰化钠形成铜的络合物。
这完全与使用过厚的帆布阳极套有关。
笔者根据这一现象更换成一层丙纶布袋,经一年多来的多次化验分析,不但未曾发现铜离子浓度有降低趋势,相反有所提高,阳极溶解也很正常。
为维护溶液正常运行,每隔一定时间取出阳极,洗刷阳极板和布袋的工作是很有必要的。
游离氰化钠浓度过低引起镀层掉皮
当溶液中游离氰化钠含量不足时会产生微量的二价铜离子,此时钢铁工件入槽后在接通电源之前即会在其表面上还原析出。
此置换铜层只是疏松地吸附在其表面,在此置换铜层上加厚镀层极易从基体上剿下来,与基体分离。
由此可见氰化镀铜溶液中维持足够浓度游离氰化钠是何等重要。
要解决这一故障,只要向溶液中添加适量的氰化钠即可使二价铜离子重新与氰化钠络合。
氰化镀铜后再酸性镀铜引起镀层掉皮
某厂由于氰化预镀铜溶液中氰化钠含量不足,阳极面积过小,按正常的工艺条件难以沉上铜,最后电流密度调至近lOA/dm2,在此条件下镀上铜后再转镀酸性亮铜,结果镀上的酸性亮铜层与氰化预镀铜层之间结合不好,严重掉皮。
经分析,原因可能是此氰化预镀铜层表面附有有机膜层,为证实这一分析的真实性,做了以下试验。
将镀过氰化铜的工件再经洗刷,然后再镀酸性亮铜,此时掉皮现象消失,由此可见采用l0A/dm2的大电流镀上的铜层表面确有有机膜存在。
溶液的处理方法:
添加l0g/L氰化钠,增加阳极面积,当时库里无现成铜板而用铁板代替(用铁板代替是可以的,这样做还能调整溶液中铜的成分)。
经调整后按正常的工艺条件即能镀上铜层,且再镀酸性亮铜时也未见有起泡现象发生。
氰化镀铜溶液治理不当而影响生产进度
某电镀厂有一只500L中型专供锌铝合金预镀铜的氰化镀铜槽。
镀出铜层逐渐出现粗糙、色暗、深镀能力差等故障现象。
厂方给笔裹来电话,当时在电话中告之:
这一现象很有可能是镀铜溶液遭到了镯离子的污染所致,要他们用硫化钠处理一下,但没有交待详细的处璃方法。
结果未能达到处理目的,来电话要亲自去一次。
在该厂见到治理过的溶液呈青灰色,这是溶液中氰化钠浓度过低、有二价铜离子析出所致;
滤出的污泥呈黑色,这表明还握有硫化铜沉淀,镀层粗糙、色暗、深镀能力差等问题仍未得蓼解决。
见到上述现象,并经了解,原来该厂用硫化钠处理锌的方法过简单,溶液也未经化验(倘若镀铜溶液中游离氰化钠不足,加入的翻化钠会与铜离子起作用,生成硫化铜沉淀),据介绍处理的速度也鞠快,溶液的搅拌要求也不够。
针对这一情况,对这槽镀铜溶液作了蔫下补充处理。
在未能及时化验的条件下,根据镀铜溶液所显示颜色和阳极期状态分析,溶液中游离氰化钠的含量太少,因而添加了l5g/L氰铂钠,以保证溶液中的铜离子充分络合(添加氰化钠之后溶液显得曼清,溶液颜色也当即由青灰色变成微黄色),在不断搅拌下加入2g/l已稀释成l0%浓度的硫化钠,净置后用过滤机过滤,滤出沉淀物呈白色(略有点灰),这就说明滤出的主要是硫化锌。
从而镀铜层的质量问题彻底得到解决。
对不符合防渗碳铜工艺的纠正
某厂接受一批防渗碳镀铜的加工任务,由于未能按防渗碳镀铜工,艺加工而造成质量问题,全部返修,造成了一定的经济损失。
原来该厂对此工艺的技术要求不甚熟悉,只认为厂里有镀铜槽隧预镀铜槽,任务就接了下来,结果全部都漏渗碳,出现了本例开头龌到的质量故障。
防渗碳镀铜工艺要求甚严。
首先镀层要求精密的工艺配方;
滕次是镀层的孔隙要低(低孔隙率可以阻挡漏渗碳),分散能力鼙深镀能力要好(能满足渗碳层深度要求的镀层厚度通常不低于酗30~50um)。
该厂利用预镀铜工艺设备镀铜显然是不妥当的,无论在孔隙率还眨层厚度方面都是难以满腰求的镀成后螂返修也是意料之中。
笔者根据厂方要求推荐了下列工艺配方:
氰化亚铜30~50g/L氢氧化钠10~20g/L
氰化钠40~60g/L温度50~60℃
酒石酸钾钠30~60g/L阴阳电流密度1~3A/dm2
氰化镀铜溶液中氰化钠含量过高
氰化钠含量过高时为什么会无铜的沉积,而只冒气泡呢?
这是因为此时铜的析出电位较负,而氢离子相对地更易于放电所致,从而降低了阴极电流效率。
某厂电镀车间的氰化镀铜溶液由外厂协作化验,化验结果游离氰化钠含量略低于配方范围,本无多大关系,而新上任的加料员却不懂报告单上所指“游离”二字的含义,直接按配方中氰化钠的总含量相比,加入所比之差,整整多加了26g/L,结果镀铜时阴极上只冒泡,未见有铜的沉积,这时加料者惊慌失措,不知如何是好,邀笔者去帮助解决。
显然,这是溶液中氰化钠过剩所致,后经了解氰化钠的加入量并:
查阅分析报告数据,计算出氰化钠过剩量,并采取稀释溶液、补充碱式碳酸铜的方法予以调整,经过调整当即恢复正常。
氰化镀铜溶液被铅离子污染
某厂氰化镀铜溶液的阳极发生严重钝化,表面呈褐色,镀出工件表面有黑色斑点,经讨论认为是由铅离子污染引起的。
为验证,进行了如下试验:
(1)取氰化镀铜溶液lOOmL,加热至60℃;
(2)往溶液中加入0.02~0.04g硫化钠。
添加并晃动后立即见溶液中有黑色沉淀物出现,由此可见确系被铅离子所污染。
然后确定如下治理方案:
(1)分析溶液中游离氰化钠含量,并补充至工艺配方上限(以防止加入硫化钠处理时形成硫化铜沉淀);
(2)加入0.2~0.4g/L硫化钠(添加前先用少量水溶化并在不断搅拌下加入);
(3)加入0.2~0.4g/L活性炭;
(4)搅拌2h后过滤。
经过滤后镀层出现黑色斑点问题得到了彻底解决。
经进一步的了解,原是作为光亮剂的添加时,铅盐过量加入逐渐积累以致污染。
氰化镀铜溶液被铬雾污染
某厂氰化镀溶液一时期来镀出铜层色泽灰暗,沉积速度缓慢,起泡现象严重,无法正常生产。
厂方很着急,笔者应邀到现场了解情况。
实际情况是:
铜、镍、铬三个镀种都挤在一个不足50m2