说明书冯丹Word下载.docx
《说明书冯丹Word下载.docx》由会员分享,可在线阅读,更多相关《说明书冯丹Word下载.docx(19页珍藏版)》请在冰豆网上搜索。
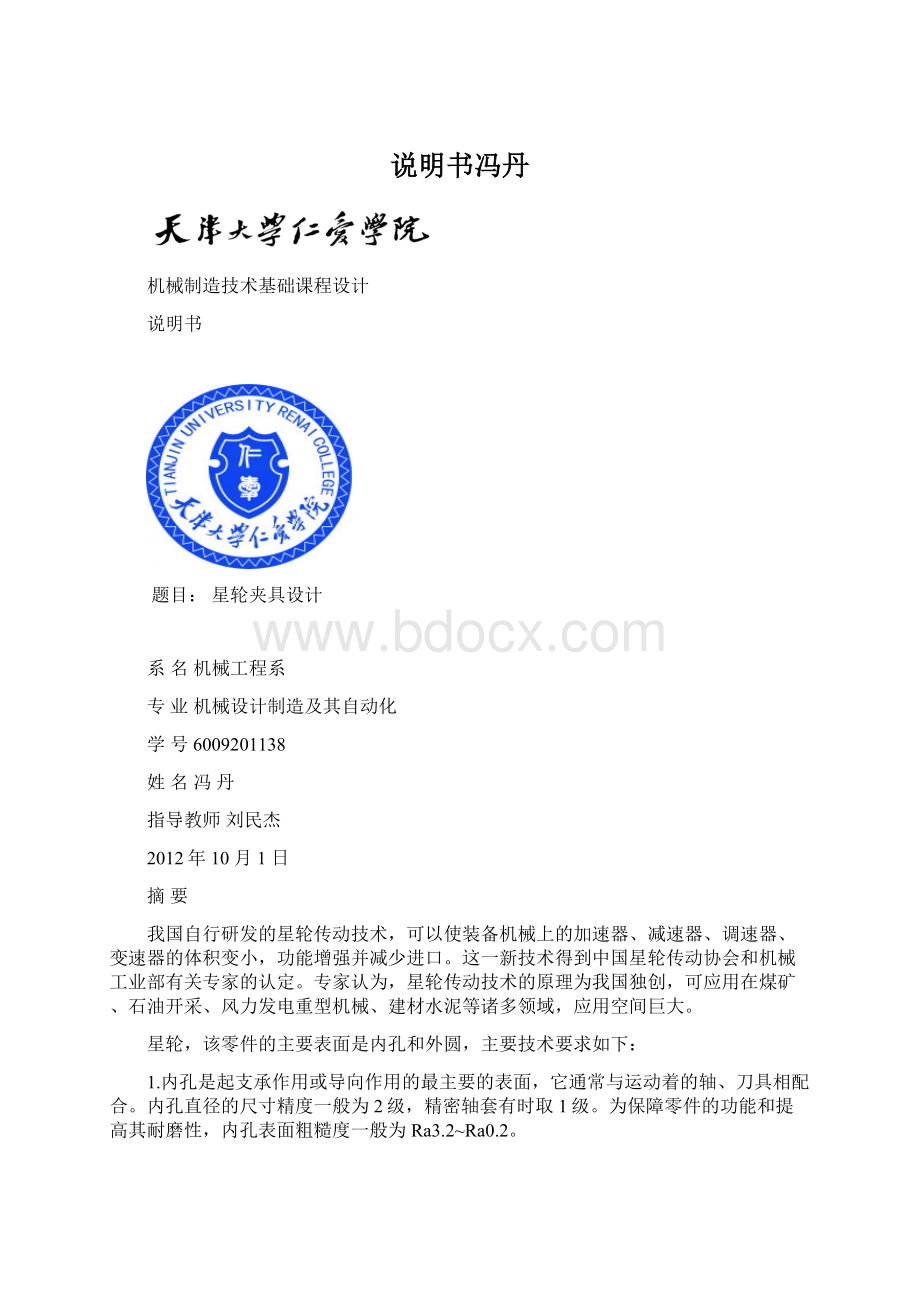
该零件的主要加工表面为孔和外圆表面。
外圆表面加工根据精度要求可选择车削和磨削。
孔加工的方法需要考虑零件的结构特点、孔径大小、长径比、精度和粗糙度要求等因素,故本次设计的星轮为保证孔的精度和表面质量,将其先后经过粗镗、半精镗、磨孔三道工序。
1.1.2保证星轮表面间位置精度的方法
由星轮零件的技术要求知,星轮零件内外表面间的同轴度以及端面与孔轴线的垂直度一般均有较高的要求,为保证这些要求,采用以下方法:
星轮主要表面加工分在几次安装中进行,先加工内孔以内孔轴线为精基准加工外圆。
这种方法制造和安装误差小,可以保证较高的位置精度。
第二章工艺规程的设计
2.1毛坯制造方法的选择
本零件选Ф68*65的冷拉棒料,材料为45钢,抗拉强度σb=600Mpa;
屈服强度为σs=355Mpa,硬度:
HBW=200,最终成品调质处理到硬度为22-27HRC。
2.2基准的选择
2.2.1粗基准的选择
对于零件而言,尽可能选择不加工表面作为粗基准,根据这个原则,本零件选取星轮外圆表面为粗基准。
2.2.2精基准的选择
精基准的选择主要应该考虑的是基准重合和基准统一的原则,选用已加工的Ф28孔中心轴线为精基准。
2.3加工方法的选择
2.4制定工艺路线
制定工艺路线的出发点应当是使零件的几何形状、尺寸精度及位置精度等技术要求能得到合理的保证,在生产纲领已确定的情况下,可以考虑采用万能机床以及专用夹具,并尽量使工序集中来提高生产率。
除此之外,还应该考虑经济效果,以便使生产成本尽量下降。
工艺路线方案
工序号
工序名称
工序内容
设备
01
打中心孔
钻、扩、镗Ф28H7孔
车床
02
车削上侧
1)粗车Ф40及Ф45端面及外围
2)半精车Ф40及Ф45端面、外圆、倒角
3)精车:
切槽
03
车削下侧
1)掉头粗车Ф45和Ф64端面及外圆面
2)半精车Ф45端面、外圆及Ф64端面、外圆、倒角
04
磨削
磨Ф28内孔
磨床
05
铣星轮缺口
铣床
06
钻孔
1)钻Ф45端面3-Ф4孔
2)钻星轮缺口3-Ф4孔
钻床
07
铣键槽
1)粗铣键槽
2)精铣键槽
08
表面处理
调质
清理
10
检验
2.5机械加工余量、工序尺寸及毛坯尺寸的确定
根据零件材料及加工工艺,分别确定各加工表面的机械加工余量、工序尺寸及毛坯尺寸。
工艺过程卡及工序图见附录。
2.5.1加工余量
2.5.1.1两外圆表面
两外圆(Ф45mm)表面一端加工长度为61mm,与其连接的要求不高的加工外圆表面直径为Ф64mm。
Ф45外圆面表面粗糙度值为Ra1.6,要求半精车;
精车。
加工直径余量单边2mm。
2.5.1.2工件内孔加工
工件内孔加工:
钻孔:
Ф20mm
扩孔:
Ф26mm
粗镗孔:
Ф27mm
半精镗孔:
Ф27.5mm
磨孔:
Ф28mm
2.5.2确定切削用量及基本工时
2.5.2.1
工序1:
钻扩镗孔
钻孔至Ф20mm;
使用刀具:
直柄麻花钻Ф20mm。
取ap=10mm,查《机械加工工艺师手册》表3.2-10知
d0取20~25时,进给量f取0.39~0.47
f=0.4mm/r;
查《课程设计指导书及参考资料1998》表13-2,切削速度v取20m/min;
则n=
=318.2r/min
取320r/min
切削工时
粗镗孔到Ф27mm;
半精镗孔到Ф27.5mm;
1、粗镗孔到Ф24mm,单边余量Z=2.5mm,一次镗去余量,ap=2.5mm
选用机床:
T612卧式机床
进给量:
f=0.1mm/r
切削速度:
根据有关手册确定T612卧式镗床的切削速度为:
v=100m/min,
则n=
=
=359r/min
根据《工艺手册》表4.2-20知,和359r/min相近的有320r/min、414r/min,故取nw=320r/min。
切削工时:
l=66mm,l1=3mm,l23mm。
t=
=
=2.09(min)
2、半精镗孔到Ф27mm,
单边余量Z=1;
一次镗去余量:
ap=1mm;
f=0.1;
nw=320r/min,v=100m/min
t=2.3min
2.5.2.2工序2:
车削工件上侧,本工序采用计算法确定切削用量。
(1)、加工条件
工件材料为45钢
,
机床:
CA6140车床
刀具:
刀具材料为YT15,刀杆尺寸16mm*25mm,k=90°
,γ0=15°
,α0=12°
,rR=0.5mm。
(2)、计算切削用量
①、粗车外圆面由Ф49到Ф48
切削深度αp:
进给量f:
根据《切削用量简明手册》(第三版)(以下简称《切削手册》)表1.4,当刀杆尺寸为16mm*25mm,αp≤3以及工件直径为100mm时:
f=0.6~0.9。
按CA6140车床的说明书(见《切削手册》表1.30)取=0.7.
计算切削速度:
按《切削手册》表1.27,切削速度的公式为(寿命选T=60min):
(m/min)
式中,CV=242,XV=0.15,yV=0.35,m=0.2。
修正系数kV见《切削手册》表1.28,
即:
kmv=1.44,ksv=0.8,kkv=1.04,kkrv=0.81,kBv=0.97。
所以:
Vc=123.8(m/min)
确定主轴转速ns:
ns=
≈438(r/min)
按机床说明书取n=96r/min
所以实际切削速度v=27m/min
检验机床功率:
主切削力
按《切削手册》表1.29所示工时计算
式中:
=784N
由《切削手册》表1-30中CA6140机床说明书知,CA6140主电动机功率为7.5kw,故机床功率足够,可以正常工作。
计算切削工时:
切削工时:
l=60,l1=2,l2=0
所以t=
*2
=0.086(min)
②、半精车端面及倒角:
确定端面最大加工余量:
已知毛坯长度方向的加工余量为4mm
确定进给量f:
根据《切削手册》表1.4,当刀杆尺寸为16mm*25mm,ap≤3以及工件直径为100mm时:
按CA6140车床说明书(见《切削手册》表1.30)取f=0.7。
按《切削手册》表1.27,切削速度的公式为(寿命选T=60min):
式中,Cv=242,Xv=0.15,yv=0.35,m=0.2。
修正系数kv见《切削手册》表1.28,即:
kmv=1.44,ksv=0.8,kkv=1.04,kkrv=0.81,kBV=0.97。
所以:
=251.6(m/min)
确定主轴转速ns=
≈890(r/min)
与890r/min相近的机床转速为900r/min,现选取nw=900,所以实际切削速度v=141.3m/min。
检验机床功率:
主切削力Fc按《切削手册》表1.29所示公式计算
Fc=CFcaPxFcfyFcVcnFckFc
式中:
CFc=2795,XFc=1.0,yFc=0.75,nFc=-0.15
KMp=(
)0.75=0.86
Kkr=0.89
Fc=cFcapxFcfyFcvcnFckFc
=2795*1*0.70.75*141.3-0.15*0.86*0.89
=768N
切削时消耗功率Pc为:
Pc=
=1.81(kw)
由《切削手册》表1.30中CA6140机床说明书知,CA6140主电动机功率为7.5kw,故机床功率足够,可以正常工作。
切削工时:
l=
=15,l1=2,l2=0,
所以t=
=0.097(min)
3、精车外圆面
精车外圆,将外圆面加工到尺寸Ф45与Ф40,切R3.0槽;
车端面;
切削深度ap:
ap=
根据《切削用量简明手册》(第三版)(以下简称《切削手册》)表1.4,当刀杆尺寸为16mm*25mm,ap≤3以及工件直径为100mm时:
按CA6140车床的说明书(见《切削手册》表1.30)取f=0.7。
式中,Cv=242,xv=0.15,yv=0.35,m=0.2。
=115.8(m/min)
ns=
≈410(r/min)
与438r/min相近的机床转速为500r/min,现选取nw=438,所以实际切削速度v=123.7m/min.
主切削力Fc按《切削手册》表1.29所示公式计算
Fc=cFcaPxFcfyFcvcnFckFc
式中:
CFc=2795,xFc=1.0,yFc=0.75,nFc=-0.15
Fc=cFcapxFcfyFcVcnFckFc
=2795*31*0.70.75*141.3-0.15*0.86*0.89
=765N
切削时消耗功率PC为:
≈1.57(kw)
2.5.2.3工序3:
车削工件下侧。
与工序二的车削过程相同。
第三章夹具设计
3.1工件的加工工艺分析
采用立式铣床,选取Ф45K6端面为定位基准面。
以基准面和Ф28孔中心轴线定位,夹紧件由工件顶面向定位基准面夹紧,采用螺旋夹紧机构。
该工件加工所需限制的自由度为六个。
下图为工序简图:
3.2夹具结构方案
采用螺旋夹紧机构,以阶梯心轴和顶尖定位,用带肩六角螺母拧紧,由于要在星轮上铣缺口,角度为120°
,均匀地分布在星轮上,故应用到分度装置,将阶梯心轴的阶梯面打三个孔(角度为120°
)来充当分度装置。
夹具结构简图:
1、阶梯心轴:
2、对刀块
3.3定位误差的计算结果
3.3.1定位误差的分析
夹具的作用首先是要保证工序加工精度,在夹具选择和确定工件的定位方案时,根据工件定位原理选用相应的定位元件外,还必须对选定的工件定位方案能否满足工序加工精度要求作出判断,为此,就需对可能产生的定位误差进行分析和计算。
定位误差是指由于定位不准造成某一工序在工序尺寸(通常指加工表面对工序基准的距离尺寸)或位置要求方面的加工误差,对某一定位方案,经分析计算其可能产生的定位误差,只要小于工件有关尺寸或位置公差的1/3~1/5,一般即认为此定位方案能满足该工序的加工精度要求
3.3.2定位误差的计算
在本次设计中采用一面两孔组合定位。
采用几何方法计算定位误差通常要画出定位简图,并在途中画出工件变动的极限,然后运用几何知识,求出工序基准在工序尺寸方向上的最大变动量,即为所求定位误差。
本次设计的工件孔Ф28H7为定位基准,并且孔与心轴采用H7/g6配合,孔的尺寸为Ф28H7,轴的尺寸为Ф28g6
孔:
∵IT7=+0.021mm轴IT6=0.013mm
EI=0es=-0.007mm
ES=0+0.021=+0.021mmei=-0.007-0.013=-0.02mm
∴Ф280+0.021
采用固定单边接触——设计基准与定位基准重合,定位误差为
ΔDw=
=0.0205mm
这时计算出来的定位误差小于保证工序尺寸公差的1/3-1/5,所以该定位合理。
3.4铣削力的计算
铣星轮缺口采用的是d16mm的高速钢立铣刀,粗车时选齿数为3,半精车时齿数为4。
经分析,粗车的铣削力远大于精车,故仅计算粗车即可。
根据高速钢立铣刀圆周切向力公式:
Fc=CfKfae0.86af0.72d0-0.86Zap
Cf——切削系数,取669;
Kf——修正系数,取0,85
ae——垂直于铣刀轴线方向的切削层尺寸,ae=14mm
ap——平行于铣刀轴线方向的切削层尺寸,ap=3mm
af——每齿进给量,af=0.05~0.08,取af=0.06,根据公式af=f/Z,Z=3得f=0.18.
Fc=CfKfae0.86af0.72d0-0.86Zap
=669*0.85*140.860.060.7216-0.86*3*3
=601.84N
总铣削力公式:
F=√Ff2+FfN2+Fe2
查表可知:
立铣时:
Ff/Fc——(0.8,0.9)取0,85
FfN/Fc——(0.75,0.8)取0.8
Fe/Fc——(0.35,0.4)取0.35
得Ff=510.85N
FfN=480.8N
Fe=210.35N
F=√Ff2+FfN2+Fe2
=√510.852+480.82+210.352
=731N
故总铣削力为731N。
3.5夹紧力的计算
Fj—沿螺旋轴向作用的夹紧力
Fx—作用在扳手上的力Fx取100N
L—作用力的力臂L=100mm
d0—螺纹中径查表知M16*1.5螺纹d0=15.026
α—螺纹升角
α=arctan(np/πd0)
单线螺纹n=1d0=15.026p=1.5
得α=1.82°
φ1’—螺纹副的当量摩擦角
φ1’=arctan(1.15f1)
查相关手册得tanφ1=f1=tanφ2=0.15
得φ1’=arctan(1.15f1)=9.79°
φ2—螺杆(螺母)端部与工件之间的当量摩擦角
tanφ2=f1=0.15
r’—螺母端部与工件之间的当量摩擦半径
r’=(D3-d3)/3(D2-d2)
D—垫片直径D=40mm
d=16mm
得r’=29.71
故
=1657N>731N
经分析,夹紧力大于铣削力,故此夹紧装置满足条件。
设计体会
课程设计是大学理论基础知识和专业基础知识学习过程中最后阶段采用的一种总结性的实践教育环节,是对专业基础知识的一次综合运用的考验。
通过课程设计能使学生综合运用大学几年来所学的理论和专业知识,以全面、系统地培养学生独立思考能力、创新能力、解决实际问题等能力。
课程设计这一个多月以来,在每一个环节我都严格要求自己,一个学习机械专业的人员,既要熟悉设计,更要熟悉工艺和控制。
在这个过程中,不但培养了我独立思考,分析问题的能力也培养了我的创新能力,解决实际问题的能力以及理论与实践相结合的能力。
在这短短的一个多月里,我也深感自己还存在许多不足,如理论知识不扎实,实践经验欠缺。
我将在以后的学习和工作中继续对专业理论知识深入学习和对实践经验认真总结,做到理论与实践有机结合。
参考文献
[1]杨叔子等,《机床夹具设计手册》第二版,上海科学技术出版社
[2]吴国梁等,《铣工实用技术手册》
[3]杨叔子等,《机械加工工艺手册》
[4]曹岩,姚敏茹等,《机床夹具手册与三维图库》
[5]张世昌等,《课程设计指导书及参考资料》,天津大学1998
[6]刘朝儒等,《机械制图》(第四版)
附表1
零件各加工表面及技术要求(查公差与配合表)
序号
加工表面
基本尺寸(mm)
公差等级(mm)
尺寸公差(mm)
位置公差(mm)
Ra(µ
m)
1.
Ф28内孔
Ф28
IT7
+0.021
O
0.8
2.
Ф45外圆表面
Ф45
IT6
+0.018
+0.002
未标注
1.6
3.
3x0.5
未注公差
—
6.3
4.
Ф64外圆面
Ф64
5.
Ф45外圆面
-0.025
-0.05
6.
Ф40外圆面
Ф40
-0.014
7.
Ф40端面
0.02
8.
45端面
45
9.
键槽
40.5
IT11
-0.16
10.
3-Ф4孔
Ф4
11.
12.
星轮缺口