轧钢生产工艺流程图文档格式.docx
《轧钢生产工艺流程图文档格式.docx》由会员分享,可在线阅读,更多相关《轧钢生产工艺流程图文档格式.docx(23页珍藏版)》请在冰豆网上搜索。
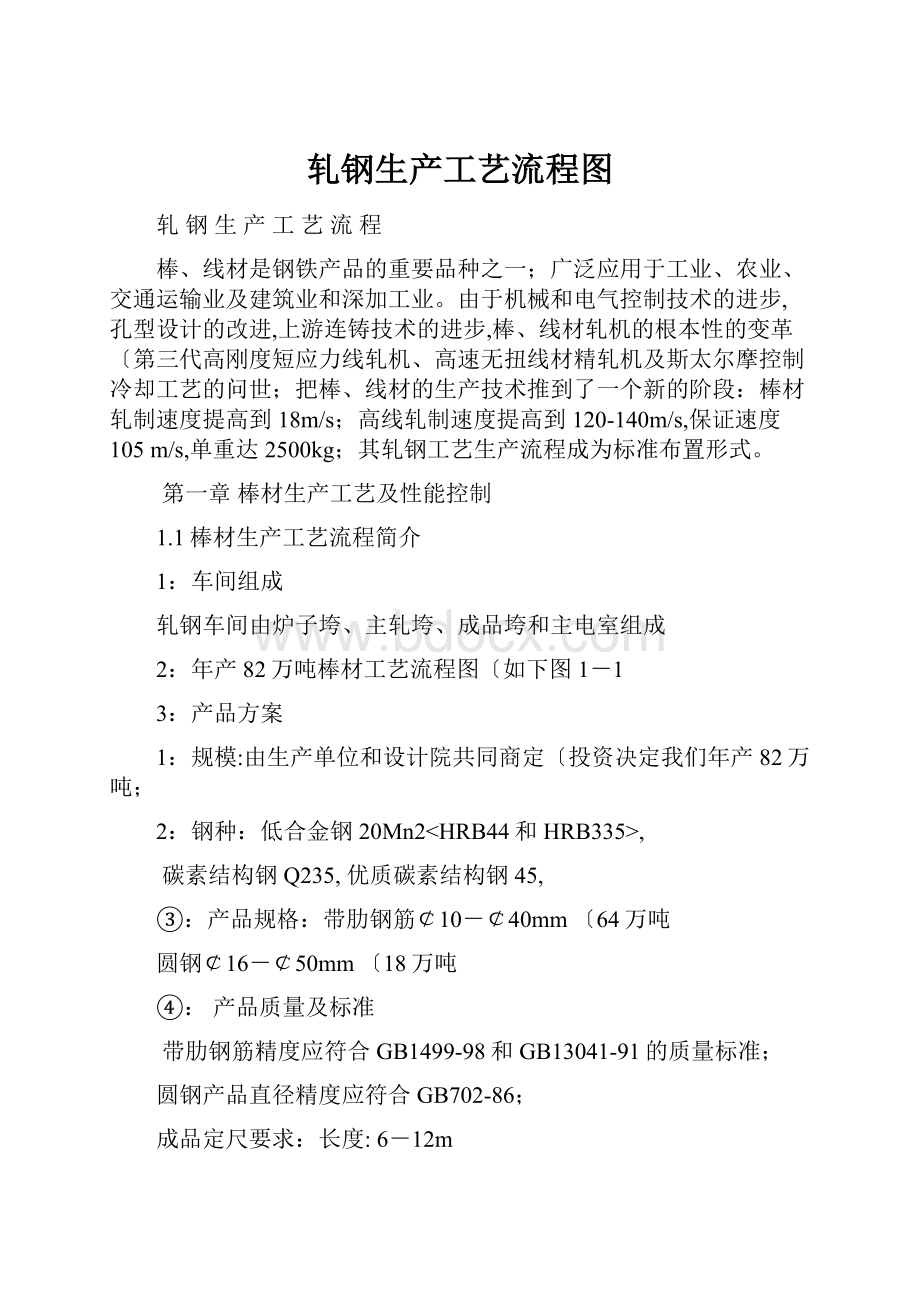
切头和轧废
原料
比例
96%
1%
3%
100%
数量
82万吨
8.542万吨
25.626万吨
85.42万吨
备注
生产熟练后,成材率可达到97%-98%
5:
坯料
120*120-150*150连铸坯,长度6-12m
连铸坯质量符合YB2011-83、YB/T154-1999、
图1-1
1.2:
车间工艺布置平面图〔见详图
1.3:
棒材工艺流程简述
轧线设备高架平台布置:
优点:
利用空间,节省投资,便于检修
设备布置在+5.0m平台上,轧线标高为+5.8m。
冷、热坯〔600℃生产时,合格的连铸坯以单根方式从连铸坯出坯台架送入热送辊道,坯料在运送过程中由自动测长装置对坯料进行测长〔使坯料进入加热炉后能准确对中,合格的单根坯料经提升装置将其提升到+5.0m平台辊道上,通过运送辊道进入入炉辊道,由推钢机推入加热炉,蓄热推钢式加热炉按不同钢种的加热制度,将坯料加热到980-1150℃,加热炉的设计能力为:
冷坯160t/h,热坯180t/h。
加热好的钢坯由出钢机推出加热炉到出炉辊道,不合格的钢坯由剔除装置剔出,合格的钢坯运送到粗轧机组第一架轧机中。
钢坯进入6架粗轧机组轧制,然后经1#飞剪切头,切尾后送入6架中轧机组轧制,粗轧和中轧为微涨力轧制,轧件从中轧机组出来,经2#飞剪切头,切尾后送入6架精轧机组轧制,精轧机组<
13#-18#轧机>
各机架之间设有活套,进行无涨力轧制,保证轧件的尺寸精度,为了Ⅲ级带肋钢筋的生产,在中轧机组后设置有预穿水冷却装置<
预留以后上>
控制轧件进入精轧机组的温度,既控制轧件的终轧温度。
全部轧机为平立交替布置,精轧机组16#、18#轧机为平、立转换轧机;
适应小规格¢10-¢18mm进行切分轧制并为以后开发产品品种奠定基础。
除切分产品外,轧件全线为无扭转轧制,不同规格的产品从其相应的机架轧出,最大轧制速度为18m/s,¢10的带肋钢筋采用四切分轧制,¢12-¢14的带肋钢筋采用三切分轧制,¢16-¢18的带肋钢筋采用二切分轧制,此时16#、18#轧机为水平轧机。
当轧线下游出现故障时,1#、2#飞剪分别对轧件进行碎断处理。
轧制成成品规格的轧件从精轧机出来后,经过水冷装置〔若不需要可空冷,在经过3#倍尺飞剪进行长度优化分段剪切。
倍尺优化分段后的轧件在冷床上进行冷却,由齐头辊道齐头。
齐头后由链式移送机构按一定数量和一定距离对其进行编组在由平移小车将轧件成组托起移到输出辊道上,由冷床输出辊道成排地运送到4#冷飞剪处切成定尺长度〔其中≥¢25规格的轧件采用孔型剪刃。
然后轧件在横移台架上进行检查、分选、计数、打捆、称重、标志、收集,最后料捆由磁盘吊车成排吊到成品库成"
十"
字形堆放。
短尺在横移台架上挑出,并送往短尺收集台架处收集。
1.4:
轧线设备组成
:
轧机组成、型式
全线轧机为全连续式棒材轧机:
共18架;
分粗、中、精3组,每组6架,最高终轧速度为18m/s。
连续式棒材轧机适合坯料单一、单重大、高速度、产量高的车间。
由于棒材车间的产品基本上为普碳钢和一般优质钢平立布置的轧机可以更好地保证产品的质量,为了小规格产品的切分轧制在精轧机组布置了平、立转换轧机,全部精轧机选用无牌坊拉杠式短应力线轧机。
这种机型刚度高、产品尺寸精度高而且辊缝对称调整,轧线固定,可整机架更换,有效提高轧机的作业率。
精轧机组采用小车快速更换机架系统。
轧机性能表
机组
名称
机架号
轧机规格
机架型式
轧辊尺寸<
mm>
轧辊直径
辊身长度
最大
最小
粗
轧
机
组
1H
550H
闭口
610
520
800
2V
550V
3H
4V
5H
450H
495
420
700
6V
450V
中
7H
8V
9H
10V
11H
350H
短应力线
380
320
650
12V
350V
精
13H
14V
15H
16C
350H/V
17H
18C
其它在线设备性能表
序号
设备名称
单位
简要技术性能
1
热送辊道
2
电机4KW变频调速,速度0-1.2m/s,通常1m/s
链式提升机
台
电机30KW变频调速,速度50.7-355mm/s,
3
入炉辊道
电机4KW变频调速,速度0-1m/s,
4
推钢机
额定压力20Mpa,实际压力18.5Mpa,推力2100KN,行程1.4m速度进60mm/s,退120mm/s
5
加热炉
座
有效尺寸20986*12800mm,燃料混合煤气<
高焦转>
单耗98m3/t<
热>
130m3/t<
冷>
产量热:
180t/h,冷:
160t/h
6
出钢机
推力2000kg,行程13.2m,推速1.3m/s,退速1.5m/s,
7
出炉辊道
电机2.2KW变频调速,速度0-1m/s,
8
1#飞剪
剪切断面¢72mm,剪切速度0.7-1.66m/s,剪切精度±
20mm,剪切温度≥900℃
9
2#飞剪
剪切断面¢50mm,剪切速度3.26-9.32m/s,剪切精度±
20mm,剪切温度≥850℃
10
3#倍尺剪
剪切断面¢50mm,剪切速度3.2-18m/s,剪切精度±
5*Vmm,剪切温度≥600℃
11
4#冷飞剪
剪切断面平剪刃¢12-¢25mm,孔型剪刃¢25-¢50mm,剪切速度1-1.5m/s,剪切精度±
15mm,
12
冷床前输入辊道
套
辊道长13.695m,12个辊子,倾斜角度0°
2°
4°
6°
8°
10°
12°
单独传动,速度为2.9-24.5m/s,电机2.2KW变频调速
13
冷床输入辊道
辊道长180m,145个辊子,倾斜角度12°
单独传动,速度为2.9-24.5m/s,电机2.2KW变频调速
14
冷床
面积:
12.5x120m2,工作间隔周期6s,偏心轮偏心距55,电机75kw
15
冷床输出辊道
辊道长121.6m,76个辊子,单独传动,速度为0.71-2.83m/s,电机1.1KW变频调速
冷剪输入,输出辊道
辊道长2.502*2m,4*2个辊子,集中传动,速度为0.71-2.83m/s,
16
定尺运送辊道
辊道长13.67m,11个辊子,单独传动,速度为0.71-2.83m/s,电机1.1KW变频调速
17
中间辊道
辊道长6.0m,10个辊子,单独传动,速度为0.71-2.83m/s,电机1.1KW变频调速
18
链式运输机
19
卸料及收集辊道
辊道长14.75m,11个辊子,单独传动,速度为0.4-1.6m/s,电机1.5KW变频调速
20
成型器打捆机
成型器液压3台/区,压力25Mpa,打捆机气动3台/区,
21
称重辊道
辊道长11.12m,12个辊子,单独传动,速度为0.38-1.5m/s,电机1.5KW变频调速
22
成品链式运输机
宽10.25m长8.845m〔升降链2.89m,运输链5.955m分二段,每段6条,每条间距分别2000、2250mm,升降链电机4kw,速度为0.152m/s;
运输链电机11kw,速度为0.152m/s
23
炉区液压站
恒压变量轴向柱塞泵额定排量117ml/r,系统额定流量519L/min,系统压力20Mpa,工作介质46#抗磨液压油
24
粗、中、精液压站
恒压变量轴向柱塞泵额定排量74ml/r,系统额定流量230L/min,系统压力18Mpa,工作介质46#抗磨液压油
25
冷床区液压站
恒压变量轴向柱塞泵额定排量131ml/r,系统额定流量518L/min,系统压力11-13Mpa,工作介质46#抗磨液压油
26
收集区液压站
恒压变量轴向柱塞泵额定排量131ml/r,系统额定流量581L/min,系统压力11-13Mpa,工作介质46#抗磨液压油
27
粗轧润滑站
螺杆泵,双筒网式过滤器精度0.08mm,管式换热器,压力0.63Mpa,流量630L/min,重负荷工业齿轮油N320,
28
中轧润滑站
29
精轧润滑站
30
吊车
加热炉垮1台、主轧垮3台、成品垮3台、轧辊车间2台
其他设备
快速换辊台车、轧机机架翻转装置、拆辊机器人等。
1.5.:
棒材轧制
棒材轧制的主要新技术、棒材轧机及其布置,
直接使用连铸坯120*120-150*150;
采用步进式加热炉、推钢式加热炉、蓄热推钢式加热炉;
连铸坯热装热送;
高压水除鳞;
低温轧制和控制轧制;
切分轧制;
棒材轧后热芯回火工艺;
在线尺寸检测;
在线多条娇直和飞剪定尺剪切;
自动堆垛机;
棒材轧机多选用闭口式、悬臂式、高刚度短应力线轧机;
其布置主轧机平、立交替布置,全线无扭转轧制,粗、中、精3组,每组6架;
各架轧机单独传动,采用微张力和无张力轧制;
1.6:
液压、润滑系统在棒材车间的作用
随着液压技术的迅速发展,液压系统在轧钢车间得到了广泛的应用,这使得设备机构得以简化,从而减轻了设备质量,同时大大提高了设备的自动化程度,如粗、中轧机的换辊装置、轧辊平衡装置等皆采用液压传动,压下机构采用液压马达代替人工手动压下,辊缝、孔型调整可实现自动操作。
润滑系统对保证工艺、生产设备的正常运转起着十分重要的作用,润滑系统能否正常工作直接影响着轧机的利用率和产量。
1.7:
轧钢生产的自动控制
自动控制能满足轧制速度的不断提高和生产过程的连续化,多品种范围的尺寸变更以及对轧件尺寸的精度要求,自动控制由计算机系统、电气驱动系统和可靠性高的检测元件组成。
1.71:
自动出钢过程控制;
粗、中轧机的微张力轧制控制;
中、精轧机的活套无张力轧制控制;
上冷床热倍尺优化剪切控制;
冷床入口的倍尺材分钢及制动控制;
倍尺材定尺剪切等。
第二章高材生产工艺及性能控制
2.1高材生产工艺流程简介
年产110万吨棒材工艺流程图〔如下图2-1
由生产单位和设计院共同商定〔投资决定我们年产110万吨;
4:
低合金钢20Mn2
碳素结构钢Q195-Q235,
优质碳素结构钢45,
产品规格:
¢5.5-¢20mm光面高速线材
盘圆外径:
¢1250mm,盘圆内径:
¢850mm,
盘圆高度:
最大-1650mm〔压紧后
交货状态:
成卷交货盘卷重量1.5-2.5t
以热轧盘卷状态交货,产品标准应符合YB/T14981-94的质量标准;
4>
110万吨
11.458万吨
34.374万吨
114.58万吨
120*120-160*160连铸坯,长度6-24m
图2-1
2.2:
2.3:
高线工艺流程简述
高线轧线由41架轧机组成,钢坯在5架水平布置的粗轧机组进行单线轧制,然后经1#飞剪切头,切尾后送入8架水平布置的中轧机组进行双线轧制,粗轧与中轧间脱头布置,由辊道相连,轧件由辊道间的分钢器分别导入中轧机组的A线〔或B线进行轧制。
粗、中轧机组内部采用微涨力轧制。
中轧机组轧出的轧件经导槽分线分别导入两条作业线中,在每条作业线中,由2#飞剪切头,切尾后经水平活套进入预精轧机组进行轧制,在预精轧机组各机架之间设有立式活套,使轧件在此区实现无扭、无涨力轧制,从而保证进入精轧机组的轧件尺寸精度,预精轧机组前设有卡断剪,若轧件在预精轧机组内发生事故,预精轧机组入口处的卡断剪立即启动将轧件切断,防止后续轧件继续进入预精轧机组。
轧件出预精轧机组经水冷冷却后在3#飞剪处切头、切尾,后经侧活套进入精轧机组轧制;
若轧件在精轧机组内发生事故,精轧机组入口处的卡断剪立即启动将轧件切断,防止后续轧件继续进入精轧机组,同时碎断剪启动将轧件碎断。
精轧机组为顶交45°
超重型无扭轧机,10架集体传动、悬臂式碳化钨辊环
轧件在精轧机组之间实现单线无扭的微涨力轧制,将轧件轧成尺寸精度高、表面质量好的线材。
根据不同的产品规格,轧制在精轧机组中轧制若干道次。
在生产¢5.5-¢7.0mm的线材时保证精轧速度90m/s。
成品由精轧机组轧出后,进入由水冷装置和风冷运输机组成控制冷却作业线,每条作业线水冷段均设有4段水冷装置,以控制线材的吐丝温度,在每段水箱之后均设有一段恢复段,使芯部和表面的温度均匀,经水冷后到达吐丝机处的温度约为800~900℃。
水冷后的线材由夹送辊送入吐丝机,高速前进的线材经吐丝机后形成直径为Ø
1050㎜的螺旋形线圈,均匀地铺放在散卷风冷运输辊道上,辊道式标准型风冷运输机设有7台大风量风机,辊道为交流变频调速传动,根据处理的钢种、规格的不同,按工艺制度可改变风机开闭的数量、风机的风量、辊道的运行速度等多种参数来调节线卷的冷却速度,使线卷在理想的冷却速度下实现金相组织的转变,从而获得具有良好的金相组织和所需要的均匀一致的机械性能的产品。
螺旋状的线材在风冷静运输辊道上按需要的冷却速度完成组织转变后,在运输机的"
尾"
部通过线圈分配器平稳地落入集卷筒,形成外径为Ø
1250㎜内径为Ø
850㎜的盘卷,集卷时线材温度为350℃~600℃。
当一卷线材收集完毕后,"
快门"
托板托住"
鼻尖"
集卷装置的芯筒下降回转,将立卷翻转成卧卷状态,同时另一个芯筒<
无盘卷的芯筒>
由水平位置回转到集卷机中心的垂直位置,使集卷工作继续进行。
盘卷运输小车将套在芯筒上的松散卧卷移出,并挂到处于等待状态的悬挂式运输机<
P&
F>
的钩子上,盘卷挂好后,运卷小车返回,等待下一盘卷,载有盘卷的钩子由运输机链条带动沿轨道运行。
盘卷继续冷却,在检查站的位置由人工进行检查、取样和切头尾工作。
钩子载着盘卷继续运行到打捆站时,由自动打捆机打捆,捆好的盘卷在盘卷秤上称重、标记。
钩式运输机最后把盘卷送到卸卷站,P&
F线的空钩继续运行,返回到集卷站处循环使用。
成品库的吊车将卸卷站处的盘卷吊运至成品堆存区存储,等待发货。
2.4:
轧线设备组成
1)粗,中轧机组
选择新型的闭口式轧机,这种轧机的结构为:
<
1>
机架牌坊用厚钢板切割、焊接而成,具有结构简单、备件少、强度高、刚性好、操作维护方便;
2>
采用液压横移机架,小车换辊,定位准确,不需要更换机架,液压锁紧,操作使用方便;
3>
选用先进的弹性胶体平衡装置,代替常规的液压缸平衡或机械弹簧平衡,工作可靠又减轻了设备重量,节省能源介质,减少流体泄漏点,减轻环境污染。
此外轧辊直径和辊身长度的比例更为合理,不仅刚度高,而且提高了辊身利用率,具体技术参数见表2-3
预精轧机组
每条作业线上的预精轧机组选择4架辊环悬臂式轧机,采用平/立交替布
置,该机组的特点为:
(1)机组布置紧凑,设备结构简单,重量轻,换辊周期短,维护工作量小;
(2)立式轧机传动通过一对螺旋伞齿轮由下传动变为侧传动,水平拉出,与
水平轧机相似,这样使得基础标高距轧制线距离小,基础工作量小,安装、检修、维护方便;
〔3轧辊箱为锻造面板插入式结构,辊箱装卸方便,减轻设备重量,提高安装精度,减少面板上的配管,便于处理事故;
〔4采用新式的轧辊辊颈密封,在密封处加一偏心板,使密封圈中心始终与轧辊中心相重合,减少密封圈的磨损,延长密封圈的寿命;
〔5辊缝调整采用偏心套式调整机构,通过丝杠及螺母转动偏心套而对称地移动轧辊轴,达到调整辊缝的目的,而保持轧制中心线不变。
具体技术参数见表2-3
精轧机
精轧机组选择顶交45°
精轧机,具体技术参数详见表2-3
轧机主要技术性能
主轧机参数表见表2-3
表2-3轧机性能表
550水平
2H
4H
6H
450水平
8H
10H
12H
350水平
330
预
14H<
A>
280水平
悬臂
285
255
70
B>
15V<
280立式
95
16H<
17V<
精轧
机组
18-27<
45°
顶交精轧机
228.5/205*72*5+170.6/153*70*5
其它在线设备名称表
分钢器
预精侧活套
预精立活套
个
3#飞剪
精轧侧活套
卡断剪
预水冷
水冷装置A、B线
夹送辊A、B线
吐丝机A、B线
散卷风冷A、B线
集卷装置A、B线
运卷小车A、B线
P﹠F钩式运输机
压紧打捆机
盘卷秤
卸卷机
粗、中、轧液压站
打捆液压站
集卷液压站
31