斯太尔发动机缸盖精铰阀座导杆孔机床动力装置设计Word文件下载.docx
《斯太尔发动机缸盖精铰阀座导杆孔机床动力装置设计Word文件下载.docx》由会员分享,可在线阅读,更多相关《斯太尔发动机缸盖精铰阀座导杆孔机床动力装置设计Word文件下载.docx(10页珍藏版)》请在冰豆网上搜索。
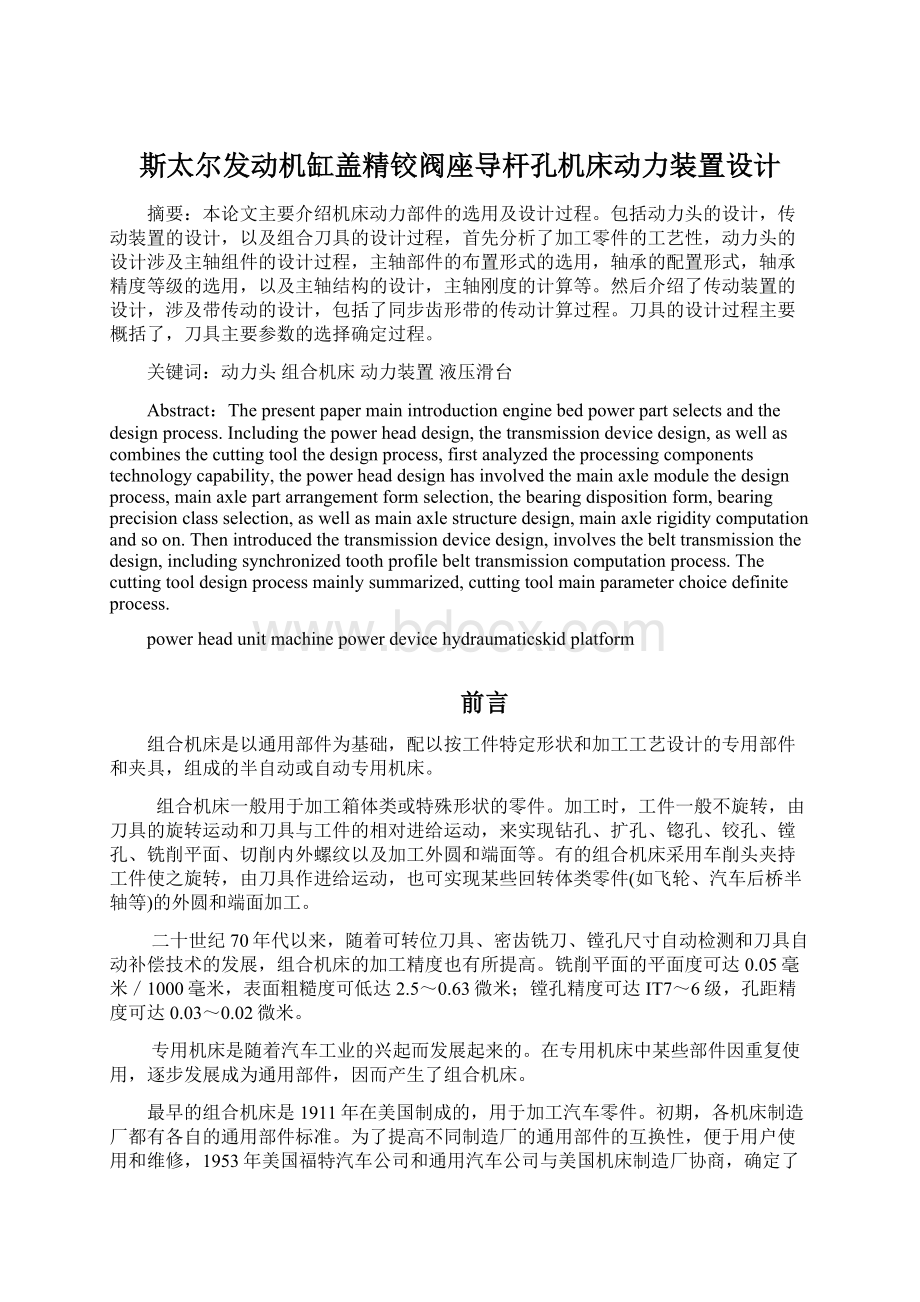
支承部件是用以安装动力滑台、带有进给机构的切削头或夹具等的部件,有侧底座、中间底座、支架、可调支架、立柱和立柱底座等。
1零件工艺分析
1.1气缸盖的作用
1.2本工序各待加工处的技术要求
加工面
尺寸及偏差
公差及精度等级
表面粗糙度
形位公差
进气孔
φ560+0.03
IT6
Ra0.8μm
◎φ0.05mmA
排气孔
φ530+0.03
◎φ0.05mmB
进气导杆孔
φ160+0.015
IT7
Ra3.2μm
⊥φ0.05mm
排气导杆孔
1.3审查气缸盖本次加工的工艺性
1.4缸盖的生产类型
N=10000台/年*m=6件/台*(1+10%)*(1+10%)=72600件/年
2组合机床动力部件选用
2.1选用通用部件的基本方法
(1)切削功率应满足加工所需的计算功率(包括切削所需功率、空转功率及传动功率)。
(2)进给部件应满足加工所需的最大计算进给力、进给速度和工作行程及工作循环的要求,同时还须考虑装刀、调刀的方便性。
2.2通用部件的选用
(1)动力部件的选用选用动力部件主要是确定动力部件的品种和规格。
根据加工工艺分析和机床总体设计选择所需的动力部件及规格如下:
表2-1
部件名称
规格
数量
铰孔铰头
DSS800-F-L
2
左液压滑台
SEHY-F630/630
1
右液压滑台
SEHY-F400/400
铰孔电机
YD132S-6/4/2-B3
切槽电机
Y100L-6B3
动力滑台主要用来实现进给运动的通用部件。
此外他还可以作为自动检验和压套等辅助工序的传动装置,以及自动线上的运输装置等用。
液压滑台主要由滑座、滑台、和液压缸三部分组成。
滑台由固定在滑座内的油缸活塞杆推动,沿滑座的导轨作直线运动,左侧滑台要承受较重的压力,故选用双矩形导轨,为提高精度,右侧选用三角形矩行组合导轨。
滑台的运动由液压系统控制,能实现快进-工进-停留-快退-停止。
根据所选液压滑台选用相应的组件。
以及配做相应的零件。
3主轴组件设计
主轴组件包括主轴、主轴支撑和安装在主轴上的传动件、密封件等。
因为主轴带动工件或刀具直接参加工件表面形成运动,所以它的工作性能对加工质量和生产率产生直接影响,是机床上最重要的部件之一。
3.1主轴组件的设计要求
主轴组件应达到以下几点设计基本要求:
(1)旋转精度指机床在空载低速旋转时(机动或手动),主轴前端安装工件或刀具部位的径向和轴向跳动值满足要求(其值可参见有关机床精度标准)。
目的是保证加工零件的几何精度和表面粗糙度。
(2)刚度指主轴组件在外力(例如切削力)的作用下,仍能保持一定工作精度的能力。
刚度不足时,不仅影响加工精度和表面质量,还容易引起振动。
恶化传动件和轴承的工作条件。
设计时应在其它条件允许的条件下,尽量提高刚度值。
(3)抗振性指主轴组件在切屑过程中抵抗强迫振动和自己振动保持平稳运转的能力。
抗振性直接影响加工表面质量和生产率,应尽量提高。
(4)温升和热变性温升会引起机床部件热变性,使主轴旋转中心的相对位置发生变化,影响加工精度。
并且温度过高会改变轴承等元件的间隙,破坏润滑条件,加速磨损甚至报废轴。
(5)耐磨性指长期保持其原始精度的能力。
主要影响因素有材料热处理、轴承类型和润滑方式。
同时,主轴结构要保证各零件定位可靠、工艺性好等要求。
设计时应综合考虑以上几项要求,注意吸收新技术,以获得满意的设计方案。
3.2主轴组件的设计步骤
3.3主轴组件的布局
3.3.1轴承的选取
3.3.2轴承的配置形式
3.3.3滚动轴承间隙的调整和预紧
3.3.4主轴滚动轴承的精度和配合
机床精度等级
前轴承
后轴承和推力轴承
普通精度级
D或C
E或D
精密级
C或B
C
高精度级
B
配合部位
配合
主轴轴径与轴承内圈
m5
k5
JS6
k6
座孔与轴承外圈
K6
J6或JS6
或规定一定过盈量
3.3.5主轴传动件的布置
3.3.6主轴组件布局设计
图3-1
图3-2
3.4主轴结构设计
3.4.1主轴轴径的确定
功率
2.6~3.6
3.7~5.5
5.6~7.3
7.4~11
11~14.7
14.8~18.4
18.5~22
22~29.5
车床
70~90
70~105
95~130
110~145
140~165
150~190
220
230
升降台铣床
60~90
60~95
75~100
90~105
100~115
外圆磨床
50~60
55~70
70~80
75~90
90~100
105
3.4.2主轴前端悬伸量的选择
3.4.3主轴刚度的验算
4传动装置设计
4.1传动方案拟定
比。
4.2带传动设计
4.2.1选用的齿形带的参数一般如下:
4.2.2同步齿形带的传动计算
(1)确定计算功率)
(2)选择齿形带模
(3)确定小带轮齿数
20
(4)确定大齿轮齿数
=40
(5)确定小带轮节圆直径
(6)确定
(7)
12.18mm/s
(8)确定齿形带长度与齿数L(mm),Z
查表[1]5.2-41选区相近的带长和齿数L=1068.1Z=85
(10)核验小带轮与齿形带的啮合齿数
(11)确定1mm宽齿形带由离心力而产生的张力T(Kfg/mm)
71.2
(12)确定齿形带宽度b(mm)
取b=50mm
(13)确定齿形带传动对轴的作用力Q(kgf)
式中P——传递的圆周力
Q=1242.36kgf
5加工刀具设计
5.1本次设计中应考虑的问题及应采取的方案
5.2刀具设计
刀具是机械加工工艺中必要的工艺装备之一,而复合刀具的采用是把几道工序合并在一起,可缩短基本工作时间和辅助时间,显著提高了劳动生产率;
此外,由于工序数目的减少,导致降低工艺系统的调整误差,从而提高了零件的加工精度;
同时简化了操作过程。
用一台机床完成多台机床才能完成的加工任务,也减少了操作工人的数目。
5.2.1复合铰刀的应用
现将在气缸盖气门座孔和气门导杆孔的精加工工序中,采用一把精铰挤光复合铰刀把气门导杆孔的精铰、挤压和气门座孔的精铰加工三道工序合并一次完成介绍如下。
气门导杆孔和气门座孔图纸要求如图1所示。
气门导杆孔尺寸为
16
,圆柱度公差0.01,与底面垂直度公差为100:
0.1,表面粗糙度Ra=3.2
m.气门座孔尺寸
(
),圆柱度公差为0.015,与气门导杆孔的同轴度公差为
0.05,表面粗糙度Ra=3.2
m.
方案一
气门导杆孔和气门座孔加工工艺过程是在二孔半精镗后,再用专用铰刀精铰孔至
15.79
再在40吨油压机上用推挤刀挤压孔为
。
方案二采用精铰挤光复合铰刀合并工序
精铰刀部分是六齿铰刀.具体结构如图总体分五部分,前导部分精铰刀部分,挤光部分(无刃铰刀),铰座孔部分和刀柄部分.采用精铰挤光复合铰刀,可以使气门导杆孔的精铰和挤光两道工序连续进行,而且在挤光气门导杆孔的同时又能铰削气门座孔。
使三道工序合并。
5.2.2采用精铰挤光复合铰刀的作用
(1)无刃铰刀的过度刃和每一个刀的前后角几何形状都制成圆滑过渡面,并且和精铰刀尺寸公差一样,无刃铰刀外圆及过渡面的粗糙度与精铰刀的外圆表面粗糙度一致。
这样,刀具在导杆中平滑挤压通过时,挤去精铰后孔的收缩量及中心歪斜引起的附加量,使孔表面呈现黑色,且发亮,粗糙度可达Ra=0.8
m,尺寸精度可达H7,且孔径尺寸稳定。
(3)由于挤光段无刃铰刀和导杆孔的精铰刀具有相同的尺寸公差,当无刃铰刀全长进入导杆孔后,无刃铰刀的中心线就代表了导杆孔的中心线,在精铰座圈孔时,无刃铰刀起定心作用,而且提高了座圈孔中心线与导杆孔中心线的同轴度。
减少了工件在原工序时的装夹次数,避免了多次装夹带来的安装误差。
(4)采用精铰挤光复合铰刀,使挤压导杆孔和精铰阀座孔的机动时间重合。
这样使机加工时缩短,而且由于工序合并减少了多次装卸的辅助时间,由原精加工工时29分钟缩减为12分钟,提高工效近1.5倍。
(5)精铰挤光复合铰刀代替了原3个工序所用的刀具,使刀具成本降低了50%.
(6)精铰挤光复合铰刀做到了工序集中,这样,减少了机床和生产工人的数量,减少了车间面积和运输工作量,同时也简化了生产计划和组织工作。
采用精铰挤光复合铰刀加工气门导杆孔和气门座孔,既可以保证零件加工质量,提高加工精度,又提高了劳动生产率,降低了成本,具有明显的技术经济效益。
5.2.3铰刀刀片材料选择
所加工缸盖倒杆孔材料为合金铸铁,硬度为HB200-230,铸件。
导杆孔要求低的表面粗糙度和高的加工精度。
5.2.4精铰刀直径和公差确定
铰刀的直径与公差直接影响到被加工孔的尺寸精度、铰刀的制造成本与使用寿命。
铰刀在加工合金铸铁件时,由于刀齿的径向跳动、工作与刀具的安装偏差、积屑瘤的作用,铰出的孔要比校准部分的实际直径大,即产生所谓的“扩张”现象。
因此确定枪铰刀公差上、下极限值的规则[2]为:
⑴铰刀直径的上限尺寸等于孔的最大直径减0.1IT,0.1IT的值应圆整到0.001mm整数倍。
⑵铰刀直径的下限尺寸等于孔的最大直径减0.35IT,0.35IT的值应圆整到0.001mm整数倍。
因加工孔的公差为φ16H7
mm,所以铰刀公差为:
上限尺寸=16.015-0.1×
0.015=16.013mm
下限尺寸=16.013-0.35×
0.015=16.008mm
所以铰刀直径公差为φ16
mm
5.2.5铰刀齿数Z选择
如铰刀齿数过少,加工出的孔精度和表面粗糙度达不到要求,齿数过多,容屑槽尺寸小,刀齿强度削弱。
加工韧性材料取小值,脆性材料取大值。
为了便于测量,齿数取偶数。
根据铰刀直径确定齿数,d=(16~32)之间的且孔精度较高,Z=6比较合适。
5.2.6铰刀齿槽形状确定
选择导杆孔铰刀齿槽为直槽。
5.2.7铰刀几何参数确定
⑴主偏角Kr
切削厚度a
=
sinKr,轴向力Fx=F
sinKr。
由此可见,Kr愈小,轴向力Fx和切削厚度a
也愈小,铰削时,铰刀的导向性好,已加工表面粗糙度较小,加工精度高。
但Kr过小时,铰削时,挤压摩擦较大,铰刀耐用度低,切入和切出时间长。
铰加工铸铁时Kr取值3°
~5°
,取Kr=5°
为了减小表面粗糙度,在切削刃和校准部分之间磨出长度为1~2mm的过渡刃,其偏角Kr=1°
~2°
⑵前角γp
铰削余量一般很小,切屑很薄,切屑与前刀面接触长度很短,前角作用不大。
一般为γ
=0
但在加工韧性材料时,为了减小切屑变形及抑制积屑瘤产生,可取
γ
=5°
~10°
取γ
=5°