蓝牙模组在SMA中的工艺技术探讨Word文档下载推荐.docx
《蓝牙模组在SMA中的工艺技术探讨Word文档下载推荐.docx》由会员分享,可在线阅读,更多相关《蓝牙模组在SMA中的工艺技术探讨Word文档下载推荐.docx(31页珍藏版)》请在冰豆网上搜索。
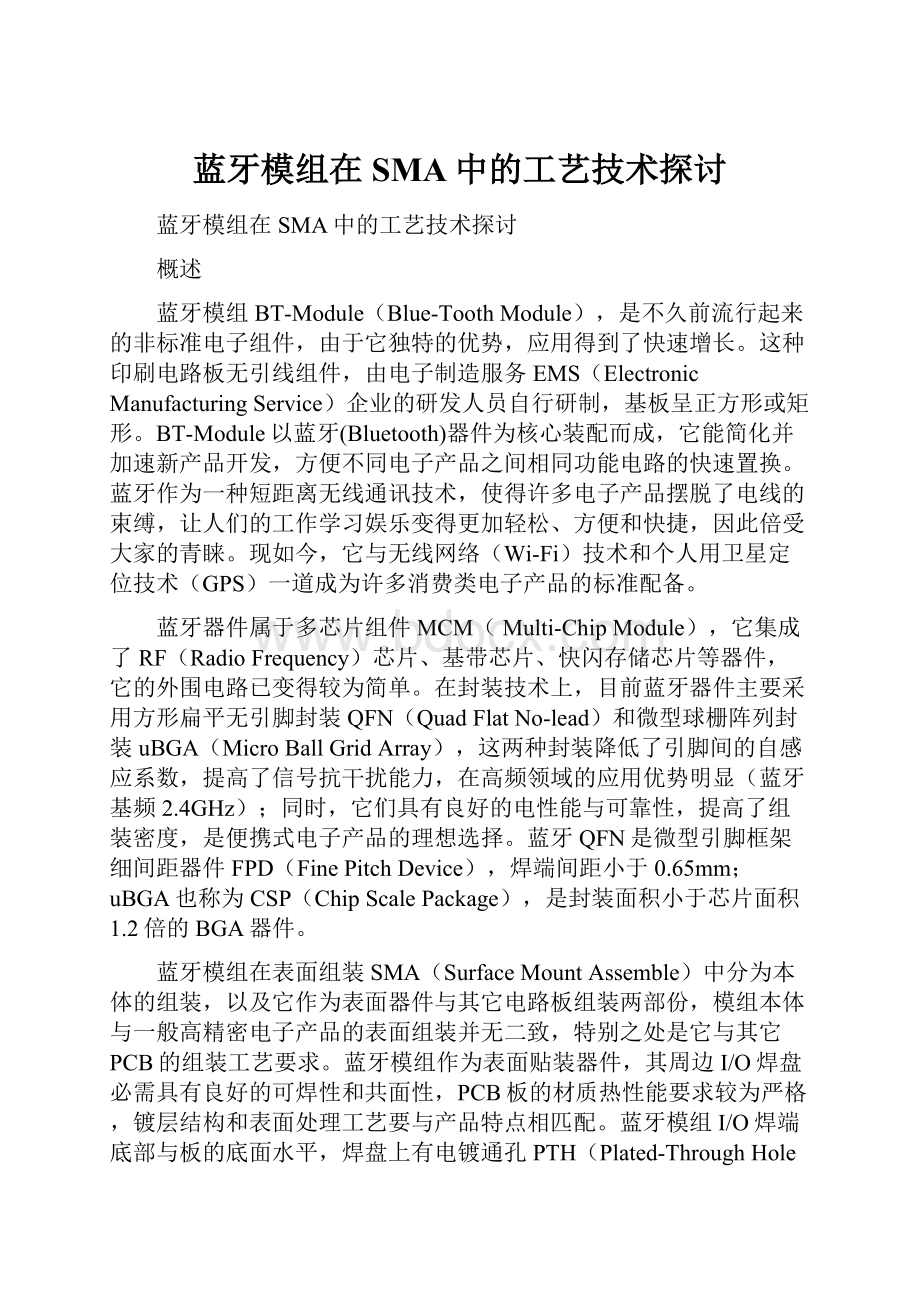
网印桥连,取料困难,贴装压力与视觉识别问题,回流焊接连锡和焊锡湿润不良等制程缺陷。
BT-Module的I/O(input/output)焊盘结构特殊,其焊点检验判定与标准零件不同;
装配一旦产生缺陷,不良检测分析困难,对其返修更是复杂,在制程工艺方面需要多层次的检测。
关键词
蓝牙模组(BTModule),电镀通孔(PTH)焊端,金属化半孔焊端,芯片底部焊端(焊球)器件,CSP,QFN,微切片(MicroCross-section);
IMC(Inter-metallicCompound)金相分析,热风枪返修台
一.蓝牙模组的结构与特性
蓝牙模组在IPC-SM-782A上未包含相关内容,没有产品手册或一般性的工业标准可供借鉴,其焊盘设计也没有固定不变的模式,I/O焊端数量与分布依据不同产器而定,焊端分布排版可以是三边、四边或不规则的形式,见图1A。
蓝牙模组是以蓝牙模块为核心器件,与傍路大功率有源或无源元器件组装而成。
核心器件QFN封装外型
图1A.BTModule常见焊端排版
大小尺寸和CSP相近,见图1B。
CSP底部I/O是焊锡球;
而QFN底部焊端与封装体底面水平,中央是大面积散热焊盘。
QFN与PCB的电气和机械连接是通过在PCB焊盘上印刷焊膏,经回流焊接来实现的。
QFN器件封装分为两种类型:
一种只裸露出封装底部的一面,其它部份被封装在元件内,另一种焊盘有裸露在封装侧面的部分。
BTModule焊端也有两种类型:
一种是I/O焊端上有P.T.H(PlatedThroughHole),另一种是焊端侧边有金属化半孔,见图1C&
1D。
蓝牙模组的核心器件有QFN与CSP封装两种常见类型,这两种封装的生产工艺需要在实际生产中不断积累经验,以求取得良好的焊接效果,见图1E。
图1BQFN&
CSP比照.图1C模组底部焊端.图1D电镀半孔焊端.图1E常见蓝牙模组外形轮廓
二.蓝牙模组基板与焊盘的设计
1、基材的选用
蓝牙模组基板通常采用高密度互连HDI(HighDensityInterconnection)覆銅箔層壓印制板,为确保I/O底部焊端良好的共面度,基板翘曲度需不超过0.5%。
大家知道,普通器件管脚共面度需小于0.1mm,BT-Module也当力求如此,否则底部焊端会产生空焊或外观吃锡不良。
基板材质的优劣对PCB的尺寸稳定性、抗剥离强度、以及刚性和可靠性影响很大,如果材质选择不合适,PCB可能在组装前就已经变形,这将导致精密细间距器件的印刷不良。
如果贴装及再流焊时变形,对于细间距的QFN或CSP容易产生虚焊、连锡等焊接缺陷。
那么,判定PCB基材优劣以及选用的性能指标主要有哪些呢?
PCB基材性能优劣首先需考察其热性能,主要参数是玻璃化转温度Tg(GlassTransitionTemperature)、热膨胀系数CTE(CoefficientofThermalExpansion)和分解温度Td(De-laminationTemperature)。
基板材质Tg是决定材料性能的临界温度,是选择基板材料的一个关键参数。
Tg过低回焊时PCB容易翘曲变形,模组底部I/O焊端产生共面性问题,产生的热应力还可能损坏焊点或元器件。
CTE反映了材料的热膨胀特性,当多层基板的层压材料、玻璃纤维与铜箔之间的CET严重不匹配,在铜铂上产生较大应力可能造成金属化孔或半孔镀层断裂失效。
蓝牙模组基板为避免回焊时热应力损伤,Td层分离裂解温度需不低于340℃。
资料显示,板材的高Td值比高Tg值更重要,例如Tg175/Td310℃比Tg140/Td350℃要好,当然Td值与Tg都能达到规格则更好。
所以,蓝牙模组应当首选耐温特性相对较高的BT/Epoxy或高TgFR-4板材,其次是FR5、CEM3。
BT/Epoxy基板主要以B(Bismaleimide)和T(Triazine)聚合而成,Tg点通常大于180℃;
高TgFR-4基材Tg范围为170℃-190℃。
这两种基材热性能较好,非常适合于蓝牙模组基板,不过日前高TgFR-4的性价比高推荐优先择之。
2、焊盘的表面镀层工艺选择
PCB的焊盘为了防止铜的氧化而造成可焊性差的问题,焊盘表面都有经过保护涂层或镀层的处理,表面涂镀工艺选择是否恰当,直接影响到产品的生产制程与组装成本。
业内人士知道,比较适合细间距精密器件焊盘的涂镀工艺主要有:
化学镀鎳浸金ENIG(ElectrolessNickelandImmersionGold)、有機防氧化保護塗層OSP(OrganicSolderabilityPreservatives)和浸银I-Ag(ImmersionSilver)三种。
ENIG、OSP和I-Ag涂镀层表面平整度和可焊性都极佳,对于蓝牙模组顶面CSP或QFN等器件焊盘都没有问题,而模组的I/O焊盘却只有ENIG符合工艺要求。
蓝牙模组本身装配完还需功能检测等工序,与其它产品回焊组装周期通常较长,它的I/O焊盘以及电镀通孔或半孔涂镀层要求苛刻,因此OSP和I-Ag涂镀层对此难以胜任。
OSP对于低热量双面板或单面板较理想,不过双面板做完一面最好在当日内完成第二面焊接,经过一次回焊高温的保护皮膜间隔时间长了将失效,于是焊盘表面颜色会变得不正常,可焊性将大打折扣,见图2。
I-Ag是在焊盘铜铂表面沉积一层薄而致密的银保护膜,但浸银层不耐脏污易氧化或硫化,与ENIG相比工艺窗口更小更受限制,所以也不建议用于模组的I/O焊盘上。
图2.OSP外观检验辨识方法图3.选化法焊盘.图4AENIG金层裂缝不良.图4BENIG镍层氧化经氯化物处理状况
ENIG相比其它两种涂镀工艺保存时间长,耐氧化,能承受多次回焊高温,金属化孔回焊后较长时期内仍有较好的可焊性。
不过它的工艺复杂成本较高,镀金层厚度(0.05-0.15um)要求严格控制,Au只是用来保护镍层防止氧化或脏污;
金层过厚使得太多的金熔解于焊点内,金含量超过3%会使焊点变脆;
金层太薄将产生镀层致密性问题,使金层产生裂隙,见图4A。
因之,镀镍焊接层失去有效保护导致其氧化或钝化,对这种有問題的ENIG銲盘进行氰化物剝金处理,不良鎳层面立即显现“黑”色本质,见图4B。
而这种镍层被氧化的焊盘,不可能在Ni层上形成牢固的金属互化物合金,即俗称IMC(Inter-metallicCompound)的Ni3Sn4结构层,使焊接点产生严重的可靠性问题,见图4C。
由此可见,ENIG虽然是蓝牙模组I/O焊盘的首选,但对于焊盘细小的底部焊接点CSP之类器件却不是最佳选择,而OSP涂覆製程焊接点的可靠性反而更好一些。
这是因为OSP有机护膜在回焊时被祛除,焊接是直接在裸铜铂上进行,在焊接中比较容易形成强度较好的良性的IMC微型焊层结构Cu6Sn5,且又未遭其它不純金屬(如金、銀等)的熔入污染,故所表現出的強度自然最好。
OSP涂层虽然相对便宜,不过在回流焊接中必需增加氮气保护,因而增加了制程的成本。
图4C镍层氧化使焊点不良图5A良好的ENIG焊盘外观图5B不良ENIG焊盘外观
为兼取不同表层处理优长,对于类似于蓝牙模组的复杂制程产品,可考虑选择选化法混合型涂镀工艺,而且这种工艺通常也被用于手机和PDA等高精密复杂产品上。
比如蓝牙模组,对于CSP器件可以先局部OSP处理,其余器件焊盘和模组的I/O焊盘采用ENIG,这种工艺虽然复杂却很有实用价值,见图3。
但无论采用哪一种涂镀工艺,制程工艺管控都是很重要的,选择PCB供应商需要做综合考察,最好选择那些制程工艺完善、质量稳定的大厂。
焊盘涂镀层作结构性分析太过复杂,在实际生产中经验丰富的SMT品质工程师,往往通过高倍率显微镜就能发现焊盘涂镀层缺隙的端倪,见图5A&
B。
所以在拆开来料的真空包装后,需要QE或IPQC对PCB的焊盘用40倍以上的显微镜抽查检验,相关标准或具体定义应当写入作业指导书SOP(StandardOperationProcedure)当中,同时规范作业流程从而降低潜在失效的缺陷产生。
3、模组I/O焊盘的构造
电镀通孔或半孔金属化工艺简述——沉铜,对通孔作沉銅处理使孔壁沉積一層薄薄的銅;
一次镀铜,对整板電鍍处理,使孔壁和焊盘表面鍍上厚度10~15um的銅层;
二次鍍銅,使無干膜覆蓋的通孔或线路等位置銅层加厚。
最终目的,是确保电镀通孔或半孔鍍銅厚度达到30-50um,平均厚度不低于35um,比一般性的电镀通孔铜层厚度平均25um要求更高。
为了使焊点在金属化半孔形成高度合格的弯月面,焊料在电镀通孔内理想的爬升高度,孔壁镀层粗糙度需小于25um,并且孔壁上不能有明显的镀瘤、断裂、沾污和空洞不良,见图6A&
为了缩小模组的尺寸,电镀通孔或半孔应当采用微孔和小孔(孔径0.3mm以下为微孔,0.3-0.5mm为小孔),钻孔的工艺也由传统的数控机床转变为激光方式。
为了得到良好的浸镀品质,孔径和板厚的比率需控制到1:
3左右。
一般说来,蓝牙模组的I/O焊盘之电镀通孔或半孔最小孔径0.25mm,孔环直径0.35mm,焊盘间隙0.25mm,则焊盘间距最小0.6mm。
蓝牙模组I/O焊盘的PTH或半孔直径不要超过焊盘宽度,一般情况下是焊宽的80%左右,较好为焊盘宽比孔径大0.2mm。
孔径过大或过小都会降低回流焊接时毛细作用,影响到焊锡的浸润填充效果。
焊盘设计应考虑到制程能力,大小则由布线密度决定,形状通常有圆形、椭圆形、泪滴形、长方形和正方形等。
与蓝牙模组I/O焊端对应的PCBI/O焊盘,宽度保持与模组的I/O焊端一致并形成对应,而长宽应当适当地外延和内延,请参考图7A&
表7B。
正常匹配的蓝牙模组I/O焊盘与PCB的I/O焊盘推荐尺寸,请参考图8(仅作参考)。
图6A电镀通孔良品与不良品比照.图6B电镀通孔断裂不良图8I/O焊盘与模组I/O焊端匹配尺寸(仅作参考)
图7A&
蓝牙模组I/O焊端草图
4、阻焊膜的设计
焊盘设计有SMD(SolderMaskDefined)和NSMD(Non-SolderMaskDefined)两种,即阻焊膜限定和非阻焊膜限定,由于在铜腐蚀工艺中NSMD更易控制,蓝牙模组的表面器件与I/O焊盘NSMD更优选。
相同间距的焊盘,NSMD焊盘比SMD要设计得稍小一些,这就增大了焊盘与过孔或走线之间的安全间隙,有利于提高组装密度和器件安全特性。
SMD焊盘由阻焊膜开口直接决定焊盘形状与大小,相同器件焊盘的对称性与一致性佳,例如CSP焊盘大小相同,有利于确保焊球形状高度统一,可以防止焊球高度不一致的虚焊或空焊。
然而,阻焊膜覆盖于焊盘上,使得焊盘阻焊层与焊盘金属重叠区域压力集中,阻焊膜陷入焊点的尖端处往往成了焊点的“软肋”,焊点失效多半缘起于此,尤其以球形焊点为甚。
NSMD阻焊膜开孔略大于焊盘,使得焊盘侧沿以及表层走线露铜部份与焊点熔为一体,从而焊点可靠性在结构上明显优于SMD的焊盘,见图9。
虽然NSMD焊盘比SMD焊盘对于蓝牙模组更能“趋利避害”,但设计者要注意汲取SMD焊盘的优点,在细节方面更需审慎。
CSP器件无论采用SMD或NSMD焊盘,在组装测试合格后,建议都应当以环氧树脂(Epoxy)对其做底部填充(Underfill)处理,以此补强焊点增加可靠性。
NSMD焊盘设计,需要注意两点:
㈠、为减少阻焊膜开口比焊盘大而产生的问题,焊盘的表层露铜导线宽应缩减为焊盘的1/2-2/3,成瓶颈形状,减少焊盘“尾巴”部份吸收过多的焊料,导致空焊或少锡等缺陷。
㈡、阻焊膜的开口相比焊盘只需大4-6mil,阻焊膜开口相对焊盘位置偏差需少于4mil,阻焊膜不能覆盖于焊盘上,这是NSMD焊盘管控重点之一,见图10。
另外,在大面积的铜铂上制作焊盘,不能简单地通过阻焊膜隔开,而是应该将铜铂挖开成网格形设计,见图11。
采用网格形设计有助于焊盘与接地层铜铂热隔离,而热隔离连线长度至少1mm。
于是NSMD焊盘工艺得以扬长避短,元件焊盘得以与SMD焊盘一样匀称一致,可使焊接应力和受热平衡,有效减少了制程缺陷。
QFN阻焊层设计,引脚间距小于0.5mm时,焊盘之间的阻焊膜可以省略,应当采取开孔块(openblock)方法,即NSMD将焊盘整体“开天窗”,盖在一排水平或垂直的焊盘上;
当间距大于0.5mm,焊盘之间要求用阻焊层隔开,见图12。
另外,焊端裸露封装侧面的QFN,焊盘应当适当外延,便于改善外侧焊点目视检验。
CSP的焊盘设计注意避免:
焊盘尺寸不规范,不一致过大或过小;
焊盘通孔埋孔处理不良产生肓孔;
焊盘大小与间距不匹配,形状比例失调;
没有设计阻焊或阻焊不规范等等,见图13。
QFN和CSP器件焊接连锡、虚焊、空洞、自对中不良,焊点不饱满以及焊点高度不均等缺陷,焊盘制作不够精细往往是其根源。
图9NSMD焊盘焊点结构与SMD对比图10阻焊膜与焊盘形状关系图11大焊盘上制作焊盘正确方法
图12QFN焊盘阻焊膜两种方式对照图13BGA不良焊盘对应的不良焊点X-Ray照片图14正确的模组拼板底面局部照片
5、模组板的拼板方法
PCB的拼板设计,是NPI(新产品导入)工程师做DFM(可制造性设计)评审的重要内容之一,合理的拼板对于充分利用基材、提高贴装效率和产品质量举足轻重。
拼板设计时首先要考虑到工厂设备和制程能力,以及产品外形或特性要求,应以制造、装配和测试过程中便于加工、不产生较大变形为宜。
拼板互连方式通常有断签式、双面对刻V形槽和邮票孔互连,适合蓝牙模组拼板的方式是前两者,邮票孔拼板方式分板后板边难免不平整或残余边屑,所以较少采用。
不过,断签式互连方式需要自动Route机分板,较多用于异型板边和复杂产品;
V形直线槽连板采用剪切或滚刀机分板,因作业简单方便而应用广泛,分板后需要使用细砂纸祛除板边毛屑。
蓝牙模组的每个单板,连接边应当尽量避开它的I/O焊端,为确保I/O焊盘板边的整洁,见图14。
PCB连板外形尺寸大小要求与板厚相匹配,较薄的PCB板面不能过大,也不宜太小,1mm厚度的PCB拼板尺寸推荐(150*100~200*150mm)。
板面较大厚度在1mm左右的拼板,生产过程中应当采用载具(一般由工程塑料或铝合金材料制作),便于校正PCB板的翘曲变形。
三、模板设计与网印要点
模板的制作工艺和开孔设计方案,直接决定着模板的制作品质,它是保证获得最佳网印效果的要素之一。
当然,对于以精密器件为主的蓝牙模组,良好的网板设计并不等于就有完美的印刷效果,印刷的工艺过程控制同样不可等闲视之。
为获得良好的印刷和焊接效果,形成可靠性的焊点,选用优质的焊锡膏也同等重要。
为兼顾考虑到回流后的效果,模板设计需考虑以下关键因素。
精密器件模板漏孔很小,焊膏填充和脱模能力较差,对模板开口孔壁光滑度和宽厚比/面积比要求更高,漏孔尺寸首先需符合以下比例:
面积比>
0.71,宽厚比>
1.6。
在当前制作的模板中,最具性价比的是激光加电抛光工艺制造的模板,品质最好却价格不菲的是电铸型模板,它们都能满足蓝牙模组的网印要求。
其实,采用激光切割的模板漏孔形状颇为理想,孔壁呈梯形上小下大;
电解抛光让孔壁更光滑,有利于减少磨擦。
采用激光加电抛光工艺制作的模板,只要漏孔设计正确工艺控制恰当,对于0.4mm间距的QFN和CSP精密器件,以及0201或01005等细小元件,都能获得良好的下锡效果和印刷稳定性。
资料显示,方形边长27mm以上的大型BGA,由于元件与基材之间热膨胀系数的差异,在回流焊接过程中可能会发生BGA四边向上翘曲的问题,使得BGA边沿的焊球更多地产生空焊。
为此,涂覆的焊膏量必须相应调整,模板的漏孔尺寸应当由外向内分层次渐趋缩减,见图15。
采用这种开孔方案,可以降低由于基板翘曲变形可能产生的空焊、短路和锡裂等潜在不良风险。
不过,CSP外形尺寸较小受热膨胀影响不明显,可以不计入考虑,焊盘与漏孔比可以1:
1.1;
采用方形开孔并适当放大,可保证更多下锡量并避免短路不良发生,见图16。
QFN器件模板设计分为中间散热焊盘和四周I/O焊端两部份,针对焊端锡膏量需求不同,网板厚度需依据焊端间距的大小选择。
中间大焊盘的开孔一般采用网状隔成田字或圆形矩阵,开孔的总面积为PCB焊盘的40-60%。
管脚间距0.5mm以下时,网板厚度不要超过0.12mm,并缩小网板开孔宽度为对应I/O焊盘的90-95%;
否则锡量偏多容易发生桥连现象。
对于“底部即焊端”的QFN周边管脚焊盘,模板的开口长度与焊盘相同即可;
如果焊端有裸露在封装侧面,则模板开口需向外延到PCB阻焊层上4mil-8mil,以便目视检验和增加焊点可靠性。
可是也有人认为,PCB焊盘两端表层走线铜铂难免导致焊锡少量流失,为保证底部焊点焊锡达到大约50-75um的高度,无论何种类型QFN,模板与之对应的开孔最少两端应外延2-6mil,不过内延时需注意与中央焊盘不低于0.25mm安全距离。
图15大面积BGA模板漏孔设计图16方形漏孔与圆形漏孔网印比照图17模组的模板局部加厚.
蓝牙模组I/O焊端对应PCB焊盘的开口设计,首先需要考量焊盘形状和间距,并通过计算模组焊端金属化孔或半孔生成理想焊点所需要的锡膏量,决定模板的厚度与漏孔大小。
理想焊点固态焊料体积=(焊端底部焊锡体积+电镀通孔的体积)*2,由于印刷用焊锡膏金属含量的体积只占焊料的约50%。
理想焊点是PTH回流焊后完全填充或半孔侧边全部浸润的弯月面焊点,可接受外观为焊锡对通孔或半孔全面润湿。
为了得到额定锡量,模板的厚度与开口面积之间需要有合理化分配。
开口大过焊盘太多,焊锡涂覆于阻焊层会导致焊点周围助焊物残留和锡珠问题;
所以,增多焊锡量依靠扩大开口是有限的,主要方法还是得增加模板厚度,为了不影响其它零件锡量,需要针对模组I/O对应焊盘采用局部加厚(Stepupstencil)方式,局部厚度可达到0.15~0.35mm。
蓝牙模组的I/O焊端对应焊盘和局部加厚模板,局部加厚既可以是模板的顶面也可以位于模板的底部,图17是顶面局部加厚模板。
有条件的话,可以考虑采用双模板印刷工艺,细小元件用薄模板先印刷锡膏,而厚模板在薄模板印刷了焊锡的位置被蚀空,在厚模板印刷时不能碰触到薄模板印刷的锡膏,这方式能满足宽范围印刷工艺的要求。
当焊膏填充通孔和细间距精密器件近距离混装,不同元件对焊锡量需求悬殊时,传统模板印刷方式不能很好的解决这个问题,则不防尝试采用新型机器点锡膏的方式。
有了制作精良的模板,只是获得良好印刷效果的第一步,印刷工艺的控制也至关重要:
锡膏的合理选择和使用、印刷参数的正确设置、模板的管理与有效清洁、印刷工作环境的温湿度控制等等。
对于核心器件较多地采用间距0.4mm的QFN或CSP蓝牙模组,锡膏优选Type4(锡粉颗粒分布20-38um)型号,要求润湿能力强、重复印刷性和抗塌陷效果好。
印刷参数设置要求充分地考虑到精密器件特性,印刷压力以刚好刮干净模板为好,印刷速度(20~30mm/sec).、脱模速度应选用慢速模式,模板清洁选用湿擦干擦真空模式,同时PCB板面与模板底部紧贴。
模板每使用8-12小时后,应当从网印机上卸下来作彻底得的清洁,由作业员手工清洗或通过自动模板清洗机清洗,然后烘干再使用。
印刷环境应当控制在25+/-2°
C温度,50+/-10%相对湿度。
另外,与蓝牙模组进行组装的PCB,模板通常采用的是局部加厚阶梯钢网,生产过程中印刷速度在不降低生产效率的情况下应当力求慢速,压力要适中;
刮刀的角度通常45~60度,如果有精细间距零件靠近模组I/O焊脚,刮刀的角度应当设定为60度,避免加厚钢网部份影响就近零件的焊锡量。
通过良好的制程控制,锡膏印刷避免了坍塌连锡、拉尖少锡等缺陷,从而得到令人满意的网印效果,见图18和图19。
图18CSP和QFN良好的网印效果.图19蓝牙模组良好的网图.图20厚薄规模组变形量检测
四、贴装工艺过程
1、贴装前确认
非气密性的湿度敏感性器件MSD(MoistureSensitiveDevices),上线生产前需要检查其包装情况,确认其没有受潮才可以进行贴装。
如果来料是真空包装,比如QFN或CSP器件拆封后首先务必检验湿度指示卡,确认正常则可以当即进行组装,反之则必需烘干后再使用;
如果器件散装并常期暴露在潮湿环境中,最好先进行低温除湿(置于湿度小于5%干燥柜中192小时)然后高温烘干处理(120摄氏度6-8小时)。
蓝牙模组需要经过检测及多道工序才能进行组装,因为长时间暴露空气中必然吸湿受潮,所以组装前务必除湿烘烤处理。
而ESD敏感性器件作业过程中还需要做好静电防护处理,贴片料盘或其它辅材等都必需是防静电的。
另外,蓝牙模组如果明显有翘曲变形,则需要用厚薄规对其I/O焊端变形量检测,确保其共面度符合规格要求,见图20。
2、贴装的管控
通常CSP和QFN的来料都是真空包装,多半采用真空料盘和塑料编带方式