1钻孔灌注桩试验工程总结成文Word文件下载.docx
《1钻孔灌注桩试验工程总结成文Word文件下载.docx》由会员分享,可在线阅读,更多相关《1钻孔灌注桩试验工程总结成文Word文件下载.docx(14页珍藏版)》请在冰豆网上搜索。
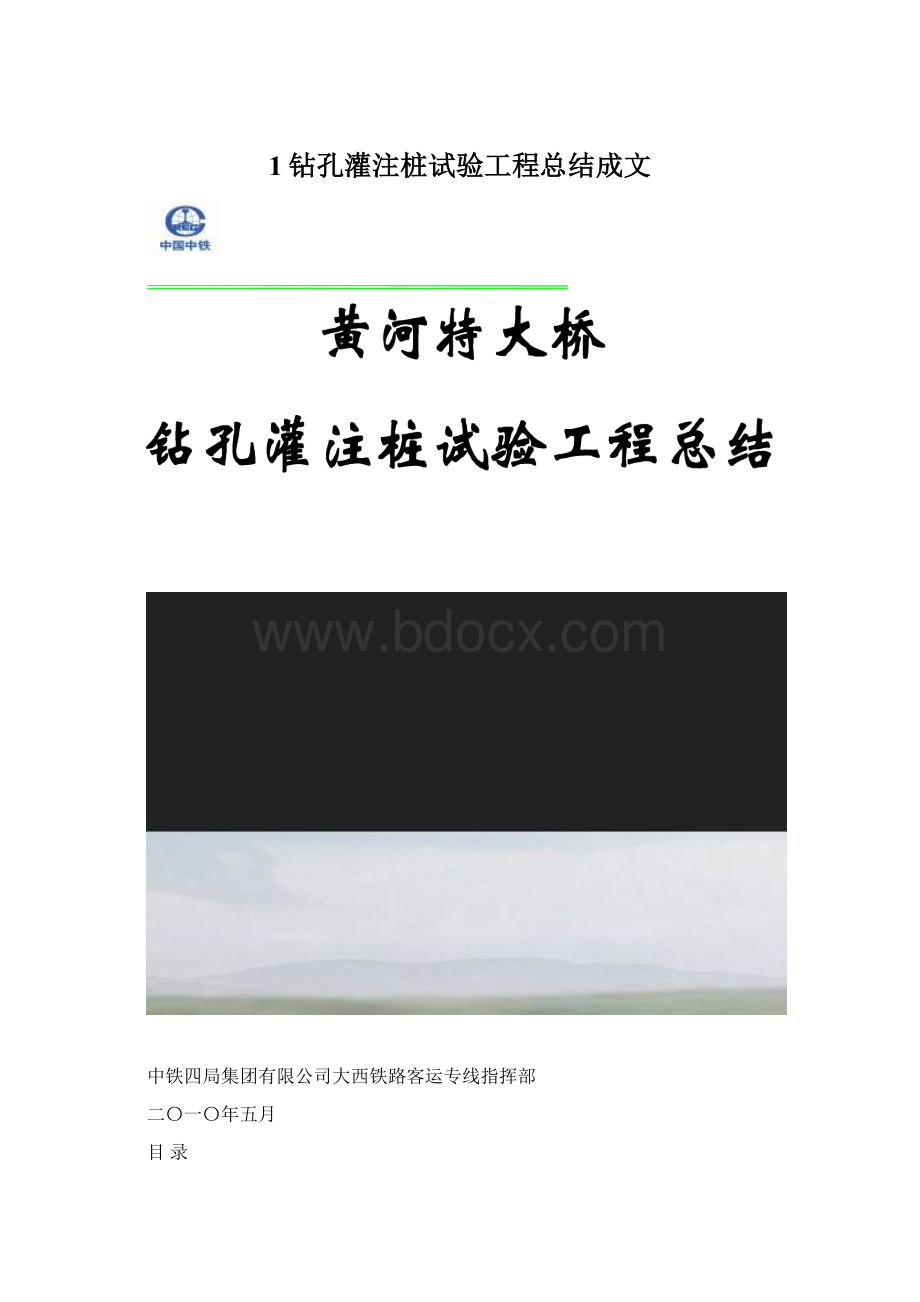
通过试验确定合理的钢筋笼分段加工长度,钢筋笼运输、安装过程中防止变形的控制措施与安装方法,垂直度控制、孔口接长的方法,声测管的安装及固定措施等。
(3)、混凝土灌注:
通过试验确定合理的首盘混凝土方量、扩孔系数、埋管深度及灌注速度。
(4)、根据试验方案的实施情况,细化工艺流程,对先前预定的质量卡控环节的适应性、可靠性及可操作性进行评估并完善。
3.试验依据
(1)、中铁第一勘察设计院集团有限公司提供图号:
大西运西施桥(特)-07《晋陕黄河特大桥32m简支梁部分(施工图)》;
(2)、《客运专线铁路桥涵工程施工技术指南(TZ213-2005)》;
(3)、《客运专线高性能混凝土暂行技术条件》;
(4)、《铁路客运专线桥涵工程质量检查与控制》;
(5)、《客运专线铁路桥涵工程施工质量验收暂行标准》。
(6)、我单位已往在砂层施工钻孔灌注桩取得施工经验。
4.地质、水文特征及设备选型
4.1.地质特征
4.1.1.地层岩性
根据大西运西施桥(特)-07《晋陕黄河特大桥32m简支梁部分(施工图)》,全桥总布置图中地层描述,28#和30#墩桩基所处地层结构为:
黏质黄土、粉(细)砂、中(粗、砾)砂、粉质粘土、粉砂、中砂和细砂。
具体地层岩性描述如下:
(1)、28#墩地层岩性自上而下描述:
黏质黄土层厚约10.7m,上部大部分呈潮湿性,下部呈饱和性;
粉(细)砂层厚约25.3m,主要呈饱和性;
粉质粘土层厚约7.2m,主要呈饱和性;
粉砂层厚约2.1m,主要呈潮湿性;
细砂层厚约17m,主要呈饱和性。
(2)、30#墩地层岩性自上而下描述:
黏质黄土层厚约13.6m,主要呈潮湿性;
粉(细)砂层厚约17.4m,主要呈饱和性;
中砂层厚约6m,主要呈饱和性;
粉质粘土层厚约7m,主要呈饱和性;
中砂层厚约9.4m,主要呈饱和性;
粉质粘土层厚约1.5m,主要呈饱和性;
中砂层厚约1.4m,主要呈饱和性;
粉质粘土层厚约4.1m,主要呈潮湿性;
中砂层厚约11.4m,主要呈饱和性。
4.1.2.特殊岩土与不良地质
(1)、湿陷性黄土
根据湿陷性黄土判定表,线路里程桩号DK702+245.00~DK703+064.00范围内,场地湿陷等级为Ⅱ级自重,湿陷土厚度为4~13m。
(2)、地震液化
本地区地震动峰值加速度0.2g,相当于地震基本烈度八度。
设计经计算分析,桥址区20m深度范围内,第四系全新统冲积饱和粉土、粉砂、细砂及中砂为可液化土层,液化土层厚13~20m。
4.2.水文特征
根据设计图纸本桥32m简支箱梁部分28#、30#墩处,地下水位埋深约在10~11m间。
4.3.钻孔设备选型
结合上述地质、水文特征描述,试验工程所选的桥墩桩基施工,属典型的陆上直埋护筒,砂层钻孔作业。
钻孔设备选择为GPS-200型正循环钻机成孔,翼锥形钻头钻进。
5.工艺实施
5.1.施工准备
(1)、人员配置
为保证试验工程顺利完成,施工过程有效控制,工艺数据采集完整。
人员配置严格按照每台钻机配机长1人,技术人员3人,兼职安全员1名,劳务工按照不大于1(正式工人):
5(劳务工)的比例。
整个试验工程配备负责人1人,技术主管3人,工程技术员12人,专职安全员1人,领工员3人。
(2)、场地平整
本试验工程钻孔桩施工位于旱地上,钻孔场地采取将桩位处杂物清理干净,地面平整压实。
施工场地大小根据钻机尺寸、施工方法、配合施工机具设施布置等因素进行确定。
(3)、桩位放样及护桩设置
施工放样依据本标段设置的独立控制网,首先,放出墩位中心线,再放出试验桩中心线,并按照十字交叉的方式引出护桩,护桩设置稳定、不易破损处。
护桩设置如图5.1.1-1所示。
图5.1.1-1护桩设置
(4)、泥浆净化系统设置
在墩旁设置泥浆池、储浆池和沉淀池,并用循环槽连接,以满足钻孔泥浆的循环和净化处理,泥浆净化采取机械净化法,即新制泥浆—泥浆池—桩孔—泥浆分离器净化—泥浆池—桩孔。
泥浆净化系统设置如图5.1.1-2所示。
图5.1.1-2泥浆净化系统
(5)、护筒埋设
护筒采用5mm厚钢板制作,内径比桩直径大0.2m,护筒长度2.5m。
护筒高出地面0.5m。
护筒埋设顶面位置偏差小于5cm,倾斜度小于1%。
(6)、钻机固定
把钻机架于平铺在护筒两侧的槽钢上,钻机的钻盘处架设一钢筋,在钢筋中心处用施工线吊放一垂球。
根据桩位中心位置用千斤顶对钻机进行调整,使桩位中心与钻盘垂下的垂线重合,用水平尺调平钻机钻盘后即可固定好钻机。
(7)、桩基施工标识牌设置
为规范桩基施工,直观、清晰的显示桩基概况、钻孔工艺流程、质量控制标准及钻孔桩施工中涉及的危险源。
在桩位处设置桩基施工标识牌,如图5.1.1-3。
图5.1.1-3桩基施工标示牌
5.2.钻孔
(1)、泥浆拌制
泥浆制备采取不分散、低固相、高粘度的聚丙烯酰胺即PHP泥浆,泥浆配合比按表5.1.2-1。
表5.1.2-1粘土造浆配合比(单位:
kg)
原料名称
淡水
粘土
CMC
纯碱
FCI
PHP
加重剂
配合比
100
8~4
0.004~0.008
0.1~0.4
0.1~0.3
0.003
试验确定
泥浆的配制严格按照泥浆的配合比进行适配,泥浆试配照片见图5.1.2-1
图5.1.2-1泥浆适配
制备的泥浆性能指标:
比重:
1.2g/cm3,粘度:
22秒,PH值:
9。
含砂率:
3.6%。
胶体率:
98%。
(2)、钻进
开始钻进时采用低档钻进,钻进速度为1.5m/h,当钻进到护筒以下1m以后,根据不同地层采用不同的钻进速度。
现场采集的数据见表5.1.2-2《28-10#桩基钻进过程各参数指标》。
表5.1.2-228-10#桩基钻进过程各参数指标
孔底标高(m)
设计地质类型
实际地质情况
理论钻进速度m/h
实际钻进速度m/h
泥浆比重g/cm3
342.3
黏质黄土
3~6
3.7
1.22
333.27
4.7
324.27
细砂
0.8~1.0
0.7
1.25
315.18
粉质黏土
3.8
1.24
306.18
3.2
291.36
1.0
289.75
在钻进过程中每增加一次钻杆对泥浆进行检测,并取钻渣来判断地质情况。
通过地质情况及时调整泥浆指标和钻进速度,保证钻机高效运行及桩基护壁的良好。
钻孔到设计深度后,进行孔径、孔深、倾斜度检测。
孔深检查:
检查钻孔记录,并用测绳量测孔深与钻杆总长进行对比,确定孔深是否达到设计孔深。
孔径、倾斜度检查:
采取长度6m,直径等桩径的自制探孔器全孔深检查,判定孔径是否存在缩孔现象。
并且,通过护桩引十字线,量测钢丝绳偏位,测绳量测高度,计算出孔径倾斜度。
经对试验工程3根桩基终孔后,通过上述方法检测后,其检测数据统计见表5.1.2-3:
表5.1.2-3试验工程终孔数据统计表
桩基编号
28-10#
30-1#
30-12#
检测方法
孔位中心(mm)
30
35
33
尺量
孔深(mm)
+50
+41
+38
测绳
孔径(mm)
+12
+11
+13
探孔器
倾斜度(%)
0.6
0.75
注:
表中“+”号表示大于设计值
(3)、一清
钻进进尺达到设计标高,经复核无误后,立即进行第一次清孔,清孔采用换浆法。
清孔时钻头略微提起15cm,转速由高变低进行空转,将孔内泥浆换出。
因砂层地质较厚,一清泥浆比重控制在1.25g/cm3,粘度19s,沉淀厚度12cm后,进行钢筋笼安装作业。
5.3.钢筋笼制作、运输(吊装)和安装
(1)、钢筋笼制作
钢筋接长:
主筋接长采用电弧搭接焊,通过计算主筋搭接处设置4度角,焊接后两根钢筋中心处于同一轴线;
“同一截面”钢筋接头数量按照不超过主筋总数50%控制,两个接头距离小于主筋直径35d范围且小于500mm;
焊接质量控制为:
焊接长度,双面焊大于5d(d主筋直径),单面焊大于10d;
焊接宽度大于0.7d,且大于8mm;
焊缝深度大于0.3d,且大于4mm。
焊缝饱满、无夹碴和气泡现象。
搭接焊接头按照200个接头的频次进行取样,取样数量为一组(50cm长,3个搭接焊接头),做拉伸试验,试验结果满足规范要求。
钢筋笼制作:
钢筋笼按照主筋间距制作加工胎具,以保证主筋间距满足规范要求。
钢筋分段为减少孔口接长时间,根据设计图纸,该试验工程桩基钢筋笼为40m长,将单桩钢筋笼长度按照每节20m制作。
制作完毕后,在其两端搭接缝中心处作出垂直于钢筋笼轴线的截面,并在钢筋上作出明显标记,使两节钢筋笼孔口接长时,上下标记互相重合,来保证钢筋笼垂直度。
并且,为防止钢筋笼在运输、吊装过程中变形,在钢筋笼每道加强箍筋处设置“十字撑”。
保护层厚度控制(钢筋笼顶底外)方式为:
钢筋笼加强箍筋四周设“耳朵”形定位筋。
孔口钢筋笼保护层采取在垂直轴线方向设置定位筋,固定于钢护筒上。
声测管安装:
根据设计图纸要求,在素砼中声测管固定,采取φ8钢筋按照2m间距制作成箍筋的形式绑扎固定声测管。
经试验工程首根桩验证,该方式固定声测管效果不佳,声测管摆动较大。
通过实践将声测管固定方式变更为采用φ20钢筋作加强箍筋,并且将箍筋三等份处的主筋延伸与声测管同长的方式来固定,效果更佳。
(2)、钢筋笼运输、吊装
钢筋笼运输采用自制的平板车,通过施工便道进行运输。
运输过程中为防止钢筋笼倾倒产生变形,在平板车上安装简易挡架,挡架按照单侧4m间距设置。
(3)、钢筋笼安装
为保证钢筋笼在起吊时不发生变形,采取钢筋笼顶端第二道加强箍筋沿直径方向设置双吊点,并在钢筋笼尾端设置辅助吊点。
通过顶部吊点起吊钢筋笼,底部吊点约束摆动的方式,缓缓起吊钢筋笼,待整节钢筋笼脱离平板车后,逐渐解除底部约束吊点,使钢筋笼处于自然铅锤状态,移动钢筋笼至孔位,对准后缓慢下放,下放过程中拆除钢筋笼加强箍筋部位的“十字撑”,直至便于钢筋笼接长停止,采用临时设施固定钢筋笼于孔口,再重复上述作业,吊装下节钢筋,待两节钢筋笼标识主筋对位后,采用搭接焊的方式将两节钢筋笼接长,焊接质量按照主筋接长搭接焊要求进行控制。
5.4.导管安装
根据孔深及导管底部高于孔底40cm导管顶部高出孔顶50cm的要求计算导管总长。
导管中间段采取标准节3m,底节采取4m一节,顶部根据需要配置合适的短节导管。
在安放导管前先对导管进行试拼,保证其顺直,并逐一编号标识,然后,进行导管水密性试验。
经试验:
导管内水压力按照0.6mpa稳压30min后观测导管未出现漏水现象,以及现场导管拆除比较顺利,未出现卡管、滑丝现象。
5.5.二次清孔
导管安装完后,将泥浆管与导管连接,采用换浆法进行清孔。
清孔泥浆指标选择为:
比重1.05g/cm3,黏度18s,含砂率1.7%,胶体率98%的泥浆通过导管注入孔内置换含渣的泥浆。
当从孔内取出的泥浆手摸无2~3mm颗粒,测得泥浆比重1.07,含沙率小于1.8%,黏度18s;
孔底沉渣厚度8cm时,停止清孔进行水下混凝土灌注。
5.6.水下混凝土灌注
根据首盘混凝土灌注后导管埋深≥1m的要求,采用2.0m3的灌注料斗和8m3的混凝土罐车来保证混凝土的供应量。
混凝土灌注在素混凝土段时,按照常规方法进行,并且,结合混凝土运输车方量,加强量测混凝土浇筑高度,计算导管埋入深度,基本控制埋入深度在3m左右,当混凝土面接近钢筋笼底时,以防止钢筋笼上浮,采取放慢混凝土灌注速度和一次性灌注混凝土高度满足拔管时导管底距笼底2m的方式,恢复正常灌注速度和埋管深度,直至混凝土灌至大于设计桩顶标高1m左右,完成整桩混凝土灌注。
具体现场灌注情况参见表5.1.6-1《28-10#水下混凝土灌注过程中砼面与导管埋设关系表》。
表5.1.6-128-10#水下混凝土灌注过程中砼面与导管埋设关系表
导管拔管次数
混凝土塌落度(cm)
混凝土面高程(m)
导管埋深(m)
备注
1
20.0
301.75
3.5
2
20.5
307.75
控制灌注速度,防止钢筋笼上浮
3
21.0
314.75
2.9
4
326.75
2.1
5
19.5
339.75
2.0
6
345.25
7
348.78
根据对试验工程三根桩灌注方量统计,并与设计方量进行比较,钻孔扩孔系数如表5.1.5-2所示。
表5.1.2-2试验工程桩基扩孔系数统计表
桩基号
桩长(m)
桩径(m)
高出设计桩顶(m)
混凝土设计方量(m3)
混凝土实际方量(m3)
扩孔系数
58
1.2
71.1
74.6
1.028
1.5
75.2
1.032
74.8
1.035
6.施工工艺总结
(1)、根据现场施工情况与钻进情况,以上人员及机械配备能满足现场施工的要求,可保证各工序间衔接要求。
(2)、正循环钻孔时,泥浆性能指标、钻进速度,按照开始钻进时,钻孔速度为1.5m/h;
护筒底以下1m后,在黏性黄土和粉质粘土钻进速度控制在3~6m/h,砂层中控制在0.8~1.0m/h;
泥浆指标为相对密度1.1~1.3、黏度16~22s、含砂率≤4%,胶体率≥95%,砂层时取值偏大值,可控制在该种地层中出现塌孔和缩孔等事故出现,钻孔质量满足验标要求。
(3)、根据图纸显示钢筋笼为外箍筋形式加工,在制作时主筋间距控制难度大,制作时间较长,建议是否可变更为内箍筋形式。
并且,本试验工程钢筋笼制作在临时钢筋加工厂内制作,由于受空间影响,钢筋笼按照分段单独制作,孔口接长时需确定的上下节钢筋笼对接断面,不易确定。
在大面积桩基施工时,钢筋笼加工采取长线法制作,即按照桩基钢筋笼总长度,在一个完整的胎具上制作,实现钢筋笼接长时的空间转移,以保证钢筋笼孔口接长质量。
(4)、结合高性能混凝土特性,具有较高的耐久性特点及本桥址钻孔桩所处T1、H1、L1环境等级限制,为保证桩基使用寿命满足设计要求的100年。
保护层厚度保证方式建议将原设计采用“耳筋”变更为与桩基混凝土同等级的高性混凝土垫块,布置数量不变。
(5)、声测管定位,建议采取试验工程中将固定箍筋直径由Ф8变更为Ф20,箍筋等份处的三根主筋延长与声测管通长的方式。
(6)、在清孔过程当中,清孔泥浆采用相对密度1.05~1.1g/cm3,粘度18~20s,含砂率小于2%,胶体率大于95%的性能指标进行清孔,在2~3个小时可完成清孔,清孔后的泥浆比重≤1.1g/cm3,,粘度≤20s,含砂率≤2%。
清孔后的泥浆指标能满足规范要求。
成渣厚度在10cm之内,能满足设计要求。
(7)、混凝土灌注时,经对坍落度不定时的检测总结,在上述情孔后的泥浆性能下,坍落度控制180~220mm,灌注过程顺利。
(8)、通过混凝土灌注结束,实际混凝土用量情况看,按照上述钻孔、清孔、钢筋和导管安装总用时,桩基扩孔系数为1.03,效果较好。
7.施工管理总结
(1)、制定施工管理体系,明确分工责任,做到专人、专长、专项管理。
即工序有专人负责,负责人员有专业特长,管理内容有专门分工。
保证现场操作的任何工序有人监控,有人解决。
(2)、工序衔接要合理,合理调整钻孔及清孔时间,根据不同地层情况及钻孔遇到的情况,综合分析成孔,泥浆比重调整及混凝土灌注的时机,合理调配机械、材料、人员等资源。
(3)、建立质量保证体系,确定参与人员的质量控制的义务和职责,牢固建立质量控制目标意识。
(4)、加强桩基钢筋笼吊装、水下混凝土灌注关键工序现场管理工作。
钢筋笼起吊、安装时,设专职司索指挥,专职安全员负责督促起吊工检测吊机工作性能,专检吊机停放处地质情况、支撑稳定性和钢筋笼起吊点布置位置、牢固性等项目,满足要求后,方可进行起吊作业;
水下混凝土灌注时,在前后盘分别设置专职联络员,保证混凝土供应及时。
领工员主要负责便道畅通、指挥车辆就位和设备摆放等;
现场旁站技术人员主要负责水下混凝土灌注质量,确保导管埋设满足规范要求,钢筋笼稳定,无上浮现象及混凝土灌注标高控制。
(5)、建立安全、环保、文明施工管理制度,切实做好现场安全教育、安全防护,环境保护及文明施工的宣传和落实,满足标准化工地的建设要求。