LX400立式旋压机的设计Word格式文档下载.docx
《LX400立式旋压机的设计Word格式文档下载.docx》由会员分享,可在线阅读,更多相关《LX400立式旋压机的设计Word格式文档下载.docx(53页珍藏版)》请在冰豆网上搜索。
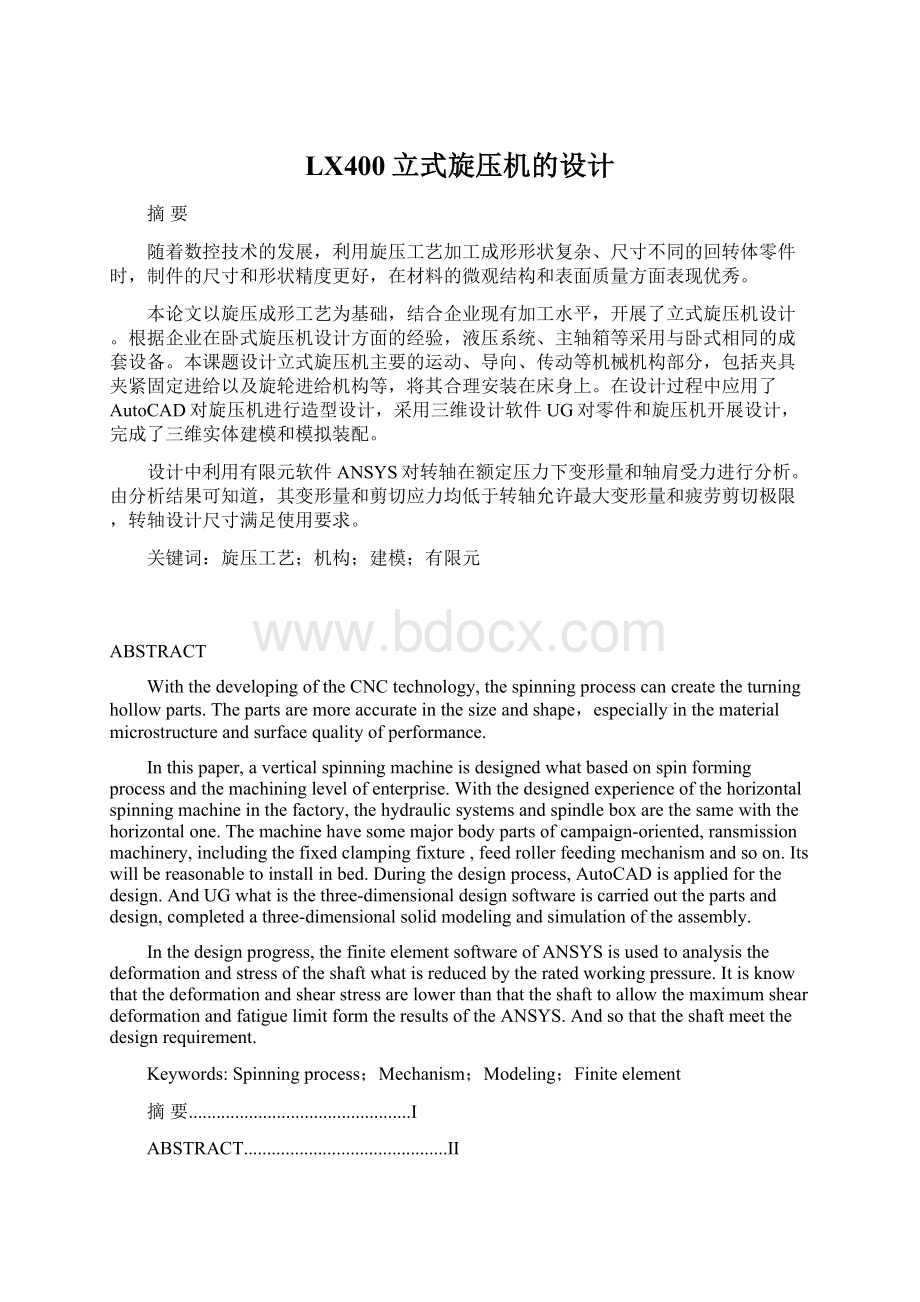
1.3研究课题目的和意义...........................7
2LXC400立式旋压机床设计..........................9
2.1理论旋压力计算...........................9
2.1.1设计实现功能.............................9
2.1.2旋压过程力计算.............................10
2.2机构设计.................................15
2.2.1工作台机构设计.............................15
2.2.2工作台纵向进给机构设计......................17
2.2.3旋轮进给机构设计...........................20
2.2.4机床机构总体设计...........................23
2.3机床零件设计.................................25
2.3.1转轴32设计................................25
2.3.2固定板31设计.............................30
2.3.3转台35设计...............................31
2.4本章小结...................................32
3主轴有限元分析..............................34
3.1有限元软件ANSYS介绍.......................34
3.2分析的材料属性..............................35
3.3ANSYS分析过程..............................36
3.4最终结果分析.................................37
3.5本章小结.....................................38
总结..............................................39
参考文献..........................................40
致谢..............................................41
附录.........................................42
1绪论
1.1旋压工艺的研究概述
金属塑性加工技术是指金属坯料在工模具的外力作用下发生塑性变形,被加工成棒材、板材、管材以及各种机械零件等技术。
随着国际市场竞争、知识经济和绿色制造的兴起,发展先进塑性加工技术己成为时代的需要。
面向21世纪,迫切需要塑性加工的零件制造向强韧化、轻型化、优质、高效、低耗、精密的方向发展。
旋压成形在加工大直径高精度薄壁筒体方面有着无可比拟的优势,在航空、航天、兵器等金属精密加工技术领域占有重要地位。
它是一种综合了锻造、挤压、拉伸、弯曲、环轧、横轧和滚压等工艺特点的少无切削加工的先进工艺,它利用旋压工具对旋转坯料施加压力,使之产生连续的局部塑性变形而成形为所需空心回转零件的塑性加工方法,是制造薄壁回转体零件常用的一种工艺方法,可以完成拉深、缩径、翻边、卷边、收口等多种不同的成形工序。
同其它加工方法相比,旋压件具有产品精度高、综合性能好、材料利用率高等优点。
1.1.1旋压工艺发展历史
旋压作为一种成形工艺方法,最早被广泛应用于陶瓷制坯作业。
经过长期的生产实践,经过一个时期的发展开始用旋压方法制作金属容器。
旋压成形技术从最初低效率的人力驱动到快速发展的电力驱动。
电力的发展与旋轮的应用使旋压的成形能力和技术水平有了很大的提高。
上个世纪中叶,旅压技术开始由普通旋压发展到强力旋压,并迅速扩大了应用范围。
强力旋压最早出现于瑞典和西德,后来被引进美国,便开始应用于航空工业。
1953年,美国制成首批专用强力旋压机,用以制造航空零件。
随后,英国、日本、前苏联等国也陆续采用了强力旋压这一新的工艺技术,使其在工业生产中的应用日益扩大。
六十年代以来,强力旋压发展非常迅速。
迄今,强力旋压已广泛应用于航空、宇航、兵器、化工、冶金、机电和民用工业,并已进入原子能工业部门。
随着旋压技术的广泛应用,旋压设备也在不断的改进和发展,旋压设备制造业日益发达。
目前德国和美国是旋压设备制造业最发达的两个国家。
德国和日本的旋压设备多为中小型,以卧式为主,系列完整,用途广泛。
美国的旋压设备,大型居多,以立式为主。
目前,国外在一般的旋压机上能旋压的制品尺寸范围为:
直径5-5000mm,壁厚0.2-150mm。
重型旋压机可旋压的最大直径达7.6m,最大长度达30m,最大重量达60吨。
虽然国内对旋压技术应用比较早,但在解放前却没有得到多大发展。
解放后,我国的一些航空工厂、电子管厂、日用品厂才开始较多地采用了手工普通旋压技术。
在六十年代初期,北京航空工艺研究所率先开始了旋压工艺研究,还与工厂合作成功地将这种技术用于航空产品的成批生产。
在六十年代有色金属研究总院也开始了立式旋压机的研制并旋制了各种铜管、铝管等急需产品。
在七十年代,旋压以其独特的优异性能被迅速应用于我国卫星、导弹、航空、舰艇、军械、原子能、冶金、通信、化工、轻工等各工业部门。
国内采用的各型旋压设备已超过百台,其中多数是我国自行研制的。
随着我国旋压技术理论研究的深入和技术积累,旋压设备得到很大发展。
许多冶金厂、研究所和重要的机械工厂发展应用旋压技术生产工艺。
重要的旋压制件包括飞机桨帽、鱼雷壳体、各种导弹封头、喷管、火箭弹壳体、炮管、潜望镜筒以及超宽板等。
旋压的材料包括钨、钼、铌、β钛合金、超高强度钢等。
经过几十年的发展,我国在旋压工艺、设备设计制造、理论研究及技术推广等方面,都取得了较大成绩,不少产品及其性能都达到了国际先进水平。
为了适应我国工业生产发展的需要,今后在研制旋压设备时应向大型化、系列化、高精度、多用途和自动化控制方向发展,提高旋压件的成形质量(尺寸精度、形状精度及性能等),并在变形机理等工艺分析方面予以充分注意和加强,以便发挥其更大的作用。
1.1.2旋压工艺的分类
旋压就其变形特点而言,可分为普通旋压和强力旋压两种。
普通旋压是指在旋压过程中,改变毛坯形状,直径增大或减小,而其厚度不变或仅有少许变化的旋压方式。
强力旋压又称变薄旋压,是指在旋压过程中,不但能改变毛坯的形状,而且还显著地改变(减薄)其壁厚的旋压方式。
强力旋压按旋轮进给方向与毛坯材料流动方向的不同,可分为正旋和反旋。
正旋时毛坯材料的流动方向与旋轮的运动方向相同;
反旋时材料的流动方向与旋轮的运动方向相反。
正旋时依靠尾顶的压力传递扭转力矩,而反旋时则依靠轴向旋压力传递扭转力矩。
工件外形不同,可分为锥形件强力旋压(包括凸、凹形曲母线回转体件)、筒形件强力旋压以及异形件强力旋压三类。
根据变形中材料流动性质的区别,称锥形件强力旋压为剪切旋压(ShearSpinning),称筒形件强力旋压为流动旋压(ExtrudeSpinning)。
按旋压时加温与否可分为冷旋与热旋,通常情况下采用冷旋,即在室温下强力旋压,特殊情况下(材料冷态塑性差、设备能力不足)则采用热旋,即加温强力旋压。
按旋压工具不同可分为滚珠旋压与滚轮旋压,滚珠旋压一般限于薄壁等截面直筒,用于加工波纹管管坯及其它薄壁件。
按轮数的不同,可分为单轮和多轮(二轮、三轮等)旋。
按旋轮及芯模与毛坯的相对位置,可分为外旋和内旋。
1.2国内外旋压设备研究与发展
国内旋压技术的应用已经有50多年的历史,形成了一定的技术积累,具有了一定的科研、生产能力。
这技术的应用主要是为了满足国家国防科技的需求,国家投入科研力量、资金等,由军工科技的发展带动社会科技水平的提高。
20世纪60年代初,开始采用自制的非常简单的旋压设备来加工成形制品。
这些设备大多为机械、手动和简单液压装置。
70年代初,冶金部门为了满足国内军工、化工等部门对大型、高精度薄壁管件以及异型件(锥形件、封头、曲母形件等)的需求,开始研制大型的卧式、立式旋压机床。
这些设备绝大部分为简单的机械或液压仿形旋压机床。
由于受当时国内机械制造业水平所限,机床性能较低。
表现在:
1)可靠性差,机床故障多;
2)液压等系统的原器件(泵、阀、密封件)质量不过关,各种机床普遍存在着跑冒滴漏现象;
3)由于电子工业发展滞后,机床的操作系统落后,使旋压工艺不连贯,旋压制品质量低下;
4)加之研制机床的技术人员对工艺不熟,设计的机床有功能不完善的缺陷。
随着世界工业化进程,80年代后期至90年代末,国内各领域加强与世界技术的交流,各部门陆续引进多台进口旋压机床,大多为德国、西班牙、俄罗斯、美国等国家制造。
进口机床的优势为:
设备系列化,使用性能相对稳定可靠;
机床制造装配的专业化程度较高;
控制系统为计算机,操作方便;
液压系统稳定不漏油;
工艺成熟并能与机床设计相结合等。
在10余年中,国内几家从事旋压机床研制的企业和院所,例如北京航空航天大学现代所、航空工艺研究所、长春五五所、福州机械研究院、哈尔滨工业大学等单位先后设计制造了多台水平较高的旋压机床,不仅满足了国内的需求,还出口到南亚、东南亚和香港等国家和地区。
1.2.1旋压机分类
由于军工产品的特殊需要,国内仍然需要一批高精度数控旋压机床以满足军工产品不断增长的需求。
特别是高精度筒形件旋压机床,应该能够加工大口径、薄壁筒形件。
但是部分高端技术的引进受到国外发达国家的限制。
专用的旋压机床需求量大国内经济高速发展,各种行业的零部件加工需求非常迫切。
以汽车用旋压带轮为例,近年来每年增加设备20余台,带轮产品数百万件,仍然供不应求,也有大量国外的订单。
多功能旋压机床的应用一种由多个旋轮组成形如切削加工中心的旋压机床是目前企业所需求的。
在这台机床上可对工件进行旋薄、翻边、收口、缩颈、整形等多项成形,可以加工形状复杂、精度要求较高的零件。
其他特殊用途的旋压机
热加工用旋压机旋压设备要配备专用的加热和冷却辅助装置。
此外,还应配备加热测温,在线检测变形件温度变化以及显示屏幕等有关手段。
内旋压机床带内筋的筒形件、外表面质量要求高的异形件产品,往往采用内旋压工艺。
带张力的旋压机在旋压变形过程中,加工的管状件自由端施加一拉力。
这种拉力由计算机控制并与管材变形相匹配。
这种旋压设备加工管材时保证了管材的平直度,无需加工后校直工序,成形管材椭圆度小,还可获得较精密的壁厚公差。
1.2.2旋压机的主要功能部件、系统
1)控制系统研制的数控旋压机床大都实现了NC或CNC控制。
数控系统较为成熟的德国SIEMENS、法国NUM、日本FANUC以及国内的中国珠峰公司、北京航天机床数控系统公司、华中数控公司等研制的控制系统,可根据机床精度、驱动电机功率和用户要求进行选择。
一些公司专门开发了电液伺服驱动的液压模块,设有多项可调参数,如PID前馈控制、死区补偿、摩擦力、非线性补偿等。
2)驱动系统旋压机床的驱动系统包括主轴驱动和进给驱动二个部分,主轴驱动可采用交流变频电机和直流变频电机驱动,进给驱动主要采用伺服电机滚珠丝杠和伺服液压缸驱动二种方式。
3)导向系统导向系统主要有滑动导轨、静压导轨和滚动导轨三种形式。
1.2.3旋压机的结构组成设计
结构设计随着对旋压变形理论研究的深入以及有限元技术的发展,设计方法和手段的不断完善,整体结构和主要承载部件均进行了有限元分析,使旋压机的布局以及结构的材料和应力分布更趋科学,既保证了结构的刚度,也考虑到结构的制造工艺性。
(1)床身床身可采用整体铸造和焊接二种结构。
导轨采用整体镶钢结构,用螺钉与床身连接,提高耐磨性,直线度达0.02mm/m-0.03mm/m。
(2)旋轮座拖板拖板结构可采用整体式和分体结构。
(3)主轴系统主轴系统主要功能是传递扭矩和实现主轴回转。
主轴系统按需要应可实现恒线速功能。
1.2.4机床精度
由于设计水平和制造水平的提高以及控制系统的不断完善,国内旋压机床的精度指标基本接近国外旋压机的水平。
横向定位精度01012-0.015mm,重复定位精度0.008-0.010mm;
纵向定位精度0.0012-0.0020mm,重复定位精度0.006-0.0012mm;
主轴径向跳动0.010-0.020mm,主轴端面跳动0.010-0.020mm。
1.2.5旋压设备的发展趋势
1)大型化、系列化国内关于大型旋压设备的研制还处于概念阶段。
欧美等国均有自主知识产权的大型旋压设备。
而国内的生产还没有形成系统、产业化,缺少行业统一的标准,不利于旋压设备整体水平的提高。
因此,大型化和系列化是旋压设备重要发展方向之一。
2)多功能、柔性化旋压不仅可以完成旋薄,而且可以完成翻边、收口、搭接、缩颈和整形等工序。
旋压机床设计应考虑其功能和柔性特点,从而提高加工效率和产品精度。
3)专业化、自动化随着国民经济的高速发展,专业化、自动化的机械可以明显提高加工的效率和加工精度。
1.3研究课题目的和意义
1.3.1本课题研究的目的
为济南重汽等汽车类企业生产汽车配件是山东小鸭模具有限公司主营业务之一。
如图
(1)所示的轮毂是汽车重要的配件之一,且市场需求量大;
图
(2)所示罩形件是日常重要配件。
这些配件虽然结构简单,但是普通的生产方式在精度、加工效率等方面有明显的不足之处,利用旋压工艺生产可以满足高效率、高精度等。
所以市场对高精度旋压设备的需求量依然在扩大,生产销售高附加值的旋压机将为企业获得更大的经济效益。
本次毕业设计的课题是LXC400立式旋压机床设计,它以加工轮毂、罩形件等零部件为主。
本次设计的重点是:
机床主要结构部分的设计、强度计算校核、工艺进给控制等。
对重要的受力零部件进行有限元强度分析,保证它们工作的安全可靠性。
图1.1轮毂
图1.2罩形件
1.3.2本课题研究的意义
旋压机作为工厂生产的重要的生产设备,其加工水平是企业生产竞争力的重要衡量标准。
作为制造业发展中国家,国内相关的旋压设备的研究水平远落后于西方发达国家,主要表现在加工精度、数控程度低,一些重要的零部件还不能满足设计要求等。
加大对高精度加工机床设备的研究,设计生产具有自主知识产权的旋压设备,不仅可以满足市场需求,对于企业和国家提高竞争力有着至关重要的作用。
本课题就是以设计立式旋压机为目的,在满足其使用功能的前提下,满足寿命和可靠性、经济性、劳动和化境保护等要求。
在设计中结合一定的应用软件对机械机构的工作强度进行可靠性分析,确保其工作中的安全性。
通过类似的工程设计,希望可以对国内旋压机的研究贡献自己的一份力量。
积极发展国内科技水平是每一个工程人员不可推卸的责任!
2LXC400立式旋压机床设计
2.1理论旋压力计算
2.1.1设计实现的功能
旋压成形技术是利用利用旋压工具对旋转坯料施加压力,使之产生连续的局部塑性变形而成形为所需空心回转零件的塑性加工方法。
由此可见旋压成形过程包含旋转和挤压两种性质的力。
分析图1.1和图1.2工件成形特点可知,罩形件的加工夹持固定其中心一定得区域,随转轴旋转加工;
轮毂的加工需要在工作台上安装成形模具或采用精确控制的成型加工。
旋转力可以由原动力系统带动工作台上固定的工件旋转。
根据旋压成形工件加工变形特点,由工作台带动工件转动。
工件的固定必须设计专门的夹具,与工作台配合使用夹持固定工件,同时夹具必须一定的转动机构随工作台和工件旋转。
旋压轮对工件的挤压是塑性变形的关键力,其运动过程包括横向进给和纵向进给,两个方向的力合成旋压力,对工件的加工质量起关键的因素。
为提高加工效率其横向、纵向进给速度必须合理控制,可以在空载情况下实现快进快退,工作中进给实现一定精度的微量调整。
综合上述可以知道旋压机组成机构及实现功能如图2.2所示。
图2.2旋压机组成机构及实现功能
2.1.2旋压过程受力计算
例如以如图
(1)所示的小轿车轮毂为加工工件,其材料为钢,直径最大值Dmax=400mm,最小值Dmin=240mm。
1)旋压力的计算
旋压力的计算依据三向投影接触面积,其计算因素有平均应力
,旋轮进给率
,坯料壁厚
,旋轮直径
,工作角
及系数
。
计算公式如下:
切向旋压分力:
(2.1)
径向旋压分力:
(2.2)
轴向旋压分力:
(2.3)
·
是坯料在加工前的厚度,
是加工后的厚度;
(根据加工要求取值:
t0=8mm,t=7mm)
剪切旋压变形遵循正弦规律成形,即:
tf=t0sinα(2.4)
式中 tf———工件壁厚
t0———坯料壁厚
α———工件锥角
旋轮进给率
、由工艺条件中确定;
10~1000mm/min,fmax=1000mm/min=16.7mm/s)
工作角
、旋轮直径
是由旋轮结构确定;
(
取值30°
=240mm)
平均应力
由工具书中查取。
(由文献[2]查得钢的平均值
=110MPa)
值因旋压方式而异
正旋时:
(2.5)
反旋时:
(2.6)
其中
表示摩擦状态的常数,
,式中
是取决于摩擦状态的常数,由工具书中查取,负号用于正旋,正号用于反旋。
m>
=0.1(m=0.3)
(2.7)
=1+0.3cot30+0.5×
0.3tan30
=0.39(1.60)
(2.8)
=2.44×
(1-7/8)-1.16×
0.39×
[1-7/8+(7/8)ln(7/8)]
=0.301
(2.9)
1.60×
[1-7/8+ln(7/8)]
=0.321
(2.10)
=0.301×
110×
16.7×
8
=4.4×
103N
≈4.4KN(4.7KN)
(2.11)
8(240×
cot30°
)1/2
=22×
104N
≈22KN(23.5KN)
(2.12)
8×
(240×
tan30°
=1.27×
≈12.7KN(13.5KN)
综合上述可知:
加工8mm厚度钢件,旋压过程中径向旋压力最大值为23.5KN,轴向最大