陶瓷滚压成型机总分配轴及滚压头系统设计文档格式.docx
《陶瓷滚压成型机总分配轴及滚压头系统设计文档格式.docx》由会员分享,可在线阅读,更多相关《陶瓷滚压成型机总分配轴及滚压头系统设计文档格式.docx(23页珍藏版)》请在冰豆网上搜索。
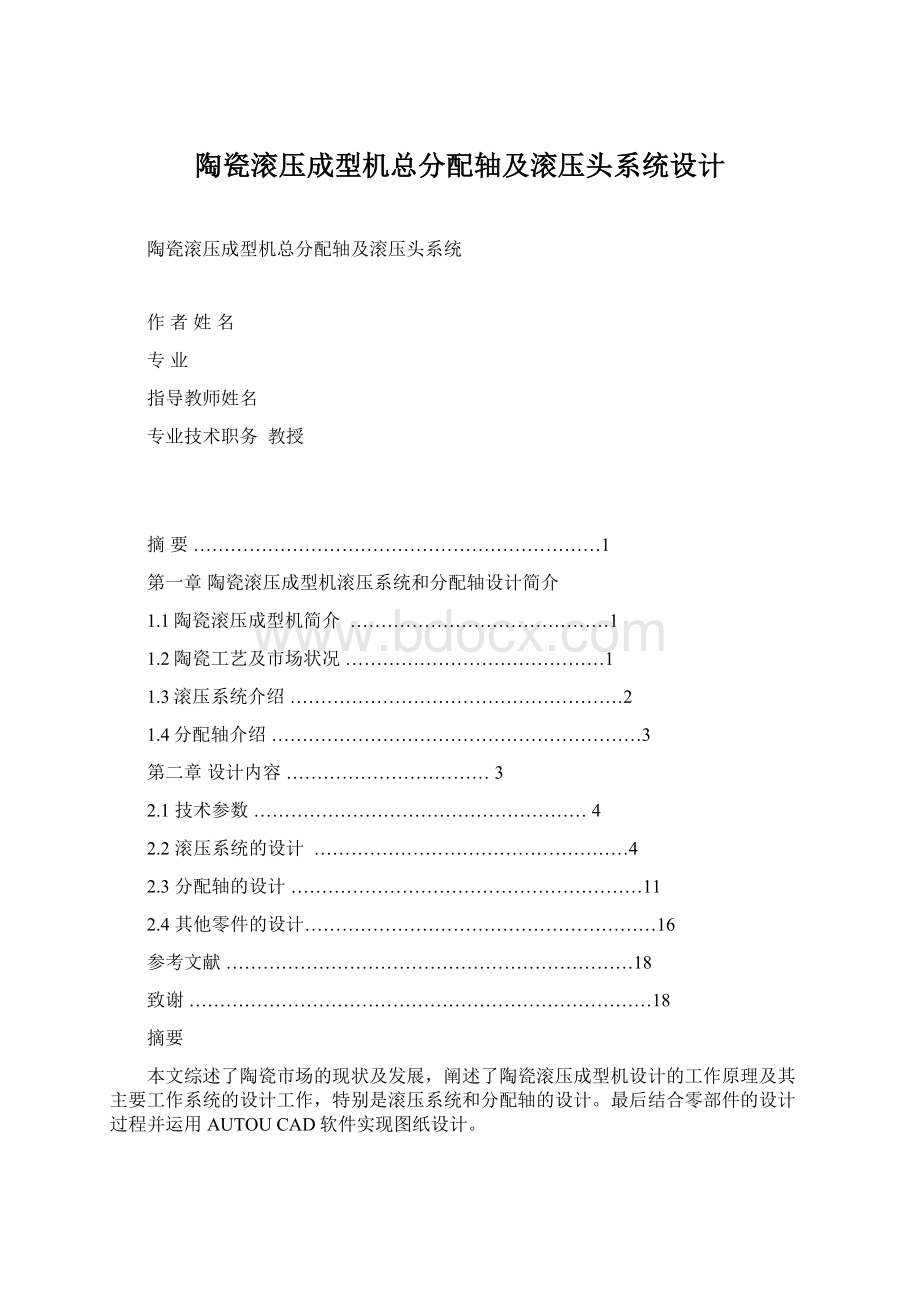
rolleraxle;
AUTOUCAD
第一章陶瓷滚压成型机滚压系统和分配轴设计简介
1.1陶瓷滚压成型机简介
滚压成型的工具是滚头,滚头是一个回转体,滚头回转体的母线与坯体成型表面的母线相同。
成型时,滚头对于泥料除有相对滑动外,主要还有相对滚动。
滚压成型由于坯体的质量好,操作简单,故得到广泛应用。
滚压成型的设备是滚压成型机,由于陶瓷产品种类繁多,形状和大小不一,因此随产品的不同,滚压成型既有不同的结构形式,以10英寸盘的单头成型机为设计对象。
1.2陶瓷工艺及市场状况
陶瓷工艺
对于制备的毛坯,通过一定的方法或手段,使坯料发生变形,制成具有一定形状的坯体,成型对坯料提出细度,含水量,可塑性,流动性等,成型性能要求,成行应满足生坯干燥强度,坯体致密度,生坯入窑含水量,器形规整度等装烧性能,成型后的坯体还是半成品,需经干燥,上釉装配,多道工序操作。
所以,足够高的生坯强度可尽可能减少生坯破坏,对于提高成型生产效益,具有重要意义。
因此,生坯应满足:
(一)成型坯满足图纸、产品样品要求的生坯形状尺寸。
(二)成型坯具有工艺要求的力学强度,以适应后续操作。
(三)坯体结构均匀,具有一定的致密度。
(四)成型适应生产组合,尽可能与前后供需联动。
市场状况
一、陶瓷产品结构的合理调整,迎合了人们的消费需求。
从生产日用陶瓷转向生产高科技陶瓷,并开始向艺术花等方面陶瓷产品总量将逐渐减少。
二、目前,日本与台湾一直是亚洲陶瓷生产技术最高,质量少,工人费用高造成利润率下降,已开始转向低产高质。
三、欧美国家陶瓷进口量猛增,其市场大有可为,近几年来,虽然英国,德国等国陶瓷进口量少,造成欧美市场的供应缺口。
但是东欧的几个主要陶瓷餐具生产国对西欧出口呈上升趋势;
成套的餐具在欧美仍有很大市场,销售约占总销量的60%。
四、陶瓷产品进口税的降低,刺激着陶瓷产品的加快进口,澳大利亚从1988年起就已经连续降低瓷器,艺术装饰陶瓷产品的进口税,从而使陶瓷进口额猛增10多倍,台湾则将瓷砖进口税从35%降至17.8%后减少至12.5%。
五、陶瓷工业在我国发展较快,销售市场逐渐转旺。
从国内市场情况看,近年形式喜人,名特优新陶瓷产品供不应求,高档陶瓷和中高档都是一样。
1.3滚压系统介绍
滚头部分
滚头是滚压系统一个重要零件,滚压头的形状、大小、及表面硬度如何直接影响制品质量的好坏。
对滚头有以下要求:
(1)能获得制品坯体所要求的形状尺寸。
(2)有利于泥料的延展和余泥的排出。
(3)寿命长,耐磨,有适当的表面硬度和光洁度。
(4)制造、维修、调整和拆卸方便。
(5)价格便宜,材料来源容易,目前常见的有钢,聚四氟乙烯。
要获得较好的制品质量,就必须设计以合理的滚头。
滚头设计除考虑上述因素外,还应跟据制品的形状、大小及工艺特点来决定,同时必须考虑泥料的性能,成型方法对制品的影响,设备条件及经济效果等因素。
滚压头做定轴运动和往复摆动,模型之作定轴转动,此种形式多见于单机。
另外也可以,滚压头作定轴运动,而模型及作定轴转动又作间歇性往复直线运动相滚压头靠拢,自动和半自动滚压机以及自动生产线中的成型机多属于此种形式。
还有一种滚压头的运动方式是直角坐标式,多用于、深杯类制品的滚压成型,胡类制品更为适用。
其滚压头处作定轴转动外,还有一个垂直向下的运动和而后的左90方向水平运动相模型周边靠拢。
滚压头作往复摆动一般都是凸轮驱动,而模型作往复直线运动的驱动方法有两种:
凸轮,液压驱动活塞。
成型方法的选择,主要针具制品的形状,大小,即工艺的特点来决定,同时还必须考虑泥料的性能,成型方法对制品的影响,设备的经济状况等因素。
滚头的平移是将滚压轴平行的向坯体中心超前移动一定距离。
滚压头坯底部分为锥体,其尖端从理论上来说是一个点。
在这点上受周围泥料的压力很小,故该店周围部分的坯体结构较疏松,而其他部位泥料压得比较比较致密。
坯体烧成后,底部中心不平。
此外,这点上的旋转线速度几乎为零。
这部位滚压头和泥料几乎没有相对运动,表面光洁度较差。
因此,为使底部中心光滑、平整,一般将滚压头锥顶适当的超过坯体中心若干毫米。
为防止底部中心不平整,除将滚压头平移外,还可将滚压头改成圆柱形状。
1.4分配轴介绍
滚压成型的工艺要求,在一个循环中,主轴和滚头的工作状态如图,滚压机的操作工过程如下:
1凸轮的转角从0-100度主轴处于静止状态,滚头在上止点位置。
在这段时间内,工人将已有的模型取出,放空模,并向空模投泥料。
2转角从100-150,主轴上的摩擦离合器结合,主轴旋转,滚头快速下降,直至滚
头于模中泥料接触为止。
3转角从150-200,主轴继续旋转,棍头慢速下降,泥料在滚头的碾压作用下逐渐在模型中成为坯体,多于的泥料从边缘排出,被同滚头一起下降的切边装置切除,直到滚头到下止点为止。
4转角从200-280,主轴继续旋转,棍头保持在下止点位置。
5转角从280-310,主轴继续旋转,主头慢速上升,离开坯体。
6转角从310-360,主轴上的摩擦离合器分离,主轴停止转动,滚头快速上升,直到滚头回到上止点为止。
第二章设计内容
2.1技术参数
该设备主要用于日用陶瓷生产。
其原理是将塑性泥料滚压成盘类、碗类产品。
本课题的主要任务是根据技术指标计算校核转轴的强度、电机功率,设计合理的传动系统。
该产品应具有简单可靠、成本低的特点。
具体技术指标为:
6~10吋盘类产品。
主要参数:
总分配轴功率N=5.0KW
总分配轴转速n=8~12rpm
滚压头转速n=260~520rpm
滚压头功率N=1.0~1.5KW
2.2滚压系统的设计
1)滚头转速的设计
滚头转速n与主轴转速n之比称为滚筒的转速比。
i=Nr/n
滚压成型时,主轴与滚头各自绕自身的轴线转动,设两周线相交于O点,在滚头与配体的接触线上去任意一点P,过P作直线OP,Op与y的方向夹角δ,与Y的正方向夹角为δ-Ф,对于坯体来说,P点的线速度
V=ωOPsin(180-δ)=OPsinФ
对于滚头来说,P点的线速度
νr=ωrOPsin(δ-Ф)
在上述两式中,ω,ωr分别为主轴和滚压头周的角速度。
滚头与坯体检完全滚动时,其相对速度为零,于是有
ν=νr
或
Nr/n=sinδ/sin(δ-Ф)
由于滚头与坯体接触线上各点大小是各不相同的,但转速比对各点来说都相同,从上式可知,无论滚轮转速是多少没滚头倾角如和选择,实际上不可能是接触线上所有点都满足上式而成为完全滚动。
也就是说,滚头与配体检处有相对滚动外,一定还有相对滑动。
W=πn/30(r-iR)
式中,W—相对滑动速度
n—主轴转速
r—坯体半径
R—滚头半径
i—滚头转速比
为了使坯体表面光滑,通常要求滚头的线速度小于坯体的线速度。
滚头速度增加,由上式知,相对速度减小,坯体表面可能不够光滑。
此外,由式知道,滚头速度增加,滚头年你的可能性也增加。
反之,滚头速度太小,相对速太大,乘兴过程接近于刀压成型,那么,通道压成型一样,在坯体内产生内压力,坯体也不致密,容易产生变形和开裂等缺陷。
滚头速度的选择,到目前为止还没有一个有理论根据的计算方法,通常是按照泥料的性质,产品的形状和大小等实际使用的数据确定。
目前工厂实际使用的是:
阳模滚压系数比i=0.6-1,阴模滚压系数比i=0.3-0.7。
由此选择电动机Y90S-4
2)生产能力和需要功率
滚压成型机尖端作硬性半自动机,其生产能力取决于完成一个工作循环所需的时间。
设t滚压机的工作循环时间,则理论生产能力
Qt=60/t
由于设备的保养、调整以及故障排除等原因,滚压及实际工作能力达不到理论值。
实际生产能力
Q=εQt
Q=60ε/t
式中Q—滚压机的生产能力,
ε—停顿系数,0.8-0.9;
t—工作循环时间。
上式用于计算单头滚压机的生产能力。
设计要求为每分钟生产10只10英寸盘,由此确定生产能力。
3)滚头特性尺寸设计
阴模滚头理论曲线的计算
由图知,
d=EC=2*BC=2*DC*cos
(1)
DC=AC-AD=D/2-AD
(2)
AD=OA*tg=h*tg(3)
由
(1)
(2)(3)式得
d=D*cos-2H*sin
式中D------坯体内口径
H------坯体内高
滚头的有效高度
由图知
h=OB=OD+DB(4)OD=OA/cos=H/cos(5)
BD=DC*sin=(AC-AD)*sin=(D/2-H*tg)*sin(6)
由(4)(5)(6)式得
h=D/2*sina+h*cosa
盘口直径D=254,H=40;
代入上式得
h=254/2+40*sin67=120mm
d=254*cos67-2*40*sin67=190mm(a取67)
4)滚头轮廓线的画法
滚头轮廓线的画法分三步进行。
第一步,计算出滚头特性尺寸(d,h,)做出理论廓线;
第二步,根据给定偏心距值的e值(经验值)做出滚头的实际轮廓线;
最后确定根部位置。
为使余泥能通畅排出,滚头根部不能不能作在坯体沿口处,要适当向上升高,升的高度h由经验值确定。
5)滚头倾角
滚头倾角直接影响到滚头中心角从而影响滚头尺寸。
=90-
=2=2(90-)=180-2
由上式可知对于一个滚头而说在成型统一制品时,若角取的值越大,则滚头中心角越小,滚头尺寸越小。
滚头倾角的大小对成型操作和陪体质量都是有影响的。
若滚头角小,则滚头大。
泥料收押面积大,陪体结构比较致密,对减小变形有好处。
因此,滚头角的选择,应在保证派你通畅,模型强度足够,极其不发生震动的条件下,尽可能采用较小的倾角。
目前,我国各陶瓷厂采用的滚头倾角,根据制品和品种、大小及滚压方式的不同,一般都在14-25度。
6)皮带及带轮的设计
滚压头转速n=260~520rpm滚压头功率N=1.0~1.5KW
电动机型号Y90S-41.1kw1400r/min转矩2.222kg
设传动比i=2.8,工作时间〉10小时主轴直径24mm
1确定计算功率
查表知工作情况系数Ka=1Pca=Ka*P=1*3kw=1.1kw
2选取带形
确定选择B型带
确定基准轮直径d1=125mm从动轮d2=2.8*80=224mm
取d2=236
验算带的速度
v=d1n1/(60*100)=*125*1400/60/1000=9.15m/s<
35m/s
带的速度合适。
确定窄V带的基准长度和传动中心距
根据0.7(d1+d2)<
a0<
2(d1+d2),初步断定中心距a0=817mm
计算所需的基准长度L1=2a0+/2(d1+d2)+(d2-d1)^2/4a0=2236
选带的基准长度2240mm
计算实际中心距a=a0+(Ld-Ld1)/2=810mm
3验算主动轮上的包角1
1=180-(d2-d1)/a*57.5=157.68〉120主动论上的包角合适。
4计算V袋的根数
Z=Pca/[(P0+P0)KaKl]
代入数值后求得Z=1
带轮的结构设计
带轮的结构设计,主要是根据带轮的基准直径选择结构形式;
根据带轮的截型确定轮槽尺寸;
带轮的其他结构可以参照经验公式计算。
确定了带轮各部分的尺寸后,即可绘出零件图,并按工艺要求注出相应的技术要求等。
铸铁制V带轮的典型结构有以下几种形式:
实心式、腹板式、孔板式、椭圆轮辐式。
带轮的基准直径dd小于等与2.5d(d为轴的直径,单位为mm)时,可采用实心式;
当dd小于等于300mm时,采用腹板式(当D1-d1大于100mm时,可采用孔板式);
dd大于300mm时,可采用轮辐式。
综上所述,主动带轮选择实心式。
查表(GB/T11544-1997,GB/T13575.1-1992)得,B型带中的一些参数如下:
b=17,
h=11,
bd=14.0,
ha最小值为3.5,本次设计选为4,
hf最小值为14,e=19
0.4,
f的最小值为11,此处取12.5。
2.3分配轴系的设计
整个分配轴系统由分配轴,凸轮,蜗轮等零部件组成。
凸轮分别控制滚头的摇摆和主轴离合器的控制。
1)凸轮的设计
滚压成型的工艺要求,在一个循环中,主轴和滚头的工作状态如图,滚压机的操作工过程如下:
2转角从100-150,主轴上的摩擦离合器结合,主轴旋转,滚头快速下降,直至滚头于模中泥料接触为止。
如果已根据工作要求和结构条件选定了凸轮形势基本尺寸,推杆的运动规律和凸轮的转向,就可尽心凸轮轮廓线的设计。
无论采用作图法还是解析法所依据的基本原理都是反转法原理。
2)基本尺寸的确定
1凸轮机构中的作用力和凸轮机构的压力角。
F=G/[cos(+ψ1)-(1+2b/l)sin(+ψ1)tanψ2]
在凸轮机构中,压力角是影响机构受力情况的一个重要参数,在其他情况相同的条件下,压力角越大,凸轮机构中作用力将越大,若压力角大到使分母为零,则作用力F将增至无穷大,此时机构发生自锁,此时的压力角称为临界压力角。
在实际生产中,为提高机构的效率,改善其受力情况,通常规定凸轮机构的最大压力角应小于某亦须应压力角。
根据实际经验,在推程时许用压力角得知一般为:
对制动推杆取30度。
在回程中,对于力封闭的凸轮机构,由于这时是推杆运动的不是凸轮对推杆的作用力,而是推杆所受的封闭力,其不存在自锁现象,故允许较大的压力角。
2凸轮半径的选择
对一定是的凸轮机构,在推杆的运动规律选定后,该凸轮的压力角与凸轮圆基圆半径的大小直接相关。
在图所示的凸轮机构中,又瞬心知识可知,P点推杆与凸轮的相对速度瞬心。
故Vp=v=ds/dδ
又有图中ΔBCP可得
Tana=(OP-e)/(s0+s)=[(ds/dδ0-e)/[(r0^2-e^2)^1/2+s]
由此可知,在偏距一定,推杆运动规律已知的情况下,加大基圆半径,可见减小压力a从而改善机构的传力特性。
但此时机构的尺寸将增大。
顾在满足,amax<
[a],的条件下,合理的确定凸轮的基圆半径,十几轮的结构尺寸不至于过大。
对于制动推杆盘凸轮机构,如果限定推程压力角a<
=[a],可导出基圆半径的计算公式
R0>
={(ds/dδ0-e)/tan[a]-s]^2+e^2}^1/2
用上式算得的基圆半径随凸轮轮廓线的点ds/dδ,s值得不同而不同。
故须确定基圆半径的极值,给应用打来不便。
在实际工作中,土伦的基圆半径r0的确定,不仅要受到Amax<
=[a]限制,还要考虑到凸轮的结构及强度要求。
因为根据此时得出结论普遍偏小,所以,实际设计工作中,凸轮结构根据具体结构条件来选择,必要时校核根据此式。
3棍子推杆半径的选择和平底推杆平底尺寸的确定
采用滚子推杆时,滚子半径的选择,要考虑滚子的结构,强度及凸轮轮廓线的形状等多方面的因素。
凸轮在尖点处处很容易磨损,但当凸轮半径很小时,工作轮廓线发生交叉,使推杆没有达到预期的运动规律,称之为失真现象。
根据以上的讨论,在进行凸轮廓线设计之前,需先进选定凸轮的基圆半径,而凸轮基圆半径的选择,需考虑到实际的机构条件,压力角,以及凸轮工作廓线是否会出现变尖和失真等因素.除此之外,当为之动推杆时,应在结构许可的条件下,尽可能取较大的导轨长度和较小的悬臂尺寸;
当为滚子推杆时,应恰当地选取滚子半径;
当为平底推杆时,应正确地确定底尺寸等等。
然,上述这些尺寸的确定,还必须考虑到强度和工艺等方面的要求。
理选择这些尺寸是保证凸轮机构具有良好的工作性能的重要因素。
二、蜗杆-蜗轮的设计
选定蜗杆的功率为4KW,转速n1=600r/mm,传动比i=60,小批量生产,传动不反向,工作载荷较稳定,但有不大的冲击,要求寿命Lh=12000h。
1.选用蜗杆传动的类型
根据GB/T10085-1998的推荐使用渐开线蜗杆(ZI)。
2.选择材料
根据库存材料的情况,并考虑到蜗杆传动传递的功率不大,速度只是中等,故蜗杆采用45钢;
因为希望效率较高些,耐磨性好些,蜗杆采用螺旋面表面淬火,硬度为45-55HRC。
蜗轮采用铸锡磷青铜ZCuSn10P1,金属模铸造。
为了更好的节约贵重的有色金属,仅齿圈用青铜铸造,而轮芯用灰铸铁HT100制造。
3.按齿面接触疲劳强度进行设计
根据闭式蜗杆传动的设计准则,先按齿面接触疲劳强度进行设计,再校核齿根弯曲疲劳强度.有式知传动中心距a=
1)确定作用在蜗轮上的转矩T2
按Z1=1,估取效率=0.8,则
T2=9.55*10*p/(n1/i12)=9.55*10*4*0.8/(600/60)=3056000mm.
2)确定载荷系数K
因为工作载荷较稳定,故载荷不均匀系数K=1;
由表11-5选取使用系数KA=1.15;
由于转速不高,冲击不大,可取动载荷系数KV=1.05;
则
K=1.15*1*1.05=1.21.
3)确定弹性影响系数ZE
因选用的是铸锡磷青铜ZCuSn10P1蜗轮和钢蜗杆相配,故ZE=160MPa
4)先假设蜗杆分度圆直径d1和传动中心距a的比值d1/a=0.35,从图11-18中可查得Z=2.9.
5)确定许用应力H
根据蜗轮材料为铸锡磷青铜ZCuSn10P1,金属模制造,蜗杆螺旋齿面硬度.>
45HRC,可以从表11-7中查得蜗轮的基本许用应力为H’=268MPa。
.
应力循环次数N=60jn2lh=60*1810*12000=720000;
寿命系数 KNH=0.8134
6)计算中心距
取中心矩a=160mm,因i=60,从表11-2中查得m=4mm;
蜗杆分度圆直径d1=71mm.这时d1/a=71/160=0.44375,从图11-18中可查得接触系数Z‘=2.74,因为Z‘〈Z,因此以上结果可以用。
4.蜗杆与蜗轮的主要参数与几何尺寸
1)轴向齿距Pa=25.133mm;
直径系数q=17.75;
齿顶圆直径dd1=d1+2*ham=71+2*1*4=79mm;
df=55mm;
分度圆导程角=313‘28“;
蜗杆轴向齿厚sa=1/2**4=6.28mm.
2)蜗轮
蜗轮齿数Z=60;
验算齿轮传动比i=Z2/Z1=60,传动比符合要求;
蜗轮分度圆直径d2=m*Z2=4*60=240;
蜗轮喉圆直径da2=d2+2ha=248;
蜗轮齿根圆直径df2=d2-2hf2=238.2;
蜗轮咽喉母圆半径rg2=a-1/2d2=36;
2.3轴的设计
1.轴设计的主要内容
轴的设计跟其他零件的实际相似,包括结构设计和工作能力计算两个方面的内容。
轴的结构设计是根据轴上零件的安装、定位以及轴的制造工艺等方面的要求,合理的确定轴的结构和尺寸。
轴的结构设计不合理,会影响轴的工作的可靠性,还会增加轴的制造成本和轴上零件装配的困难等。
因此,轴的结构设计是轴设计中的重要内容。
轴的工作能力计算指的是轴的强度、刚度和振动稳定性等方面的计算。
多数情况下,轴的工作能力主要取决于轴的强度。
这时只需对轴进行强度计算,以防止断裂或塑性变形。
而对刚度要求高的轴(如车床主轴)和受力大的细长轴,还应进行强度计算,以防止工作时产生过大的弹性变形。
对高速运转的轴,还应进行振动稳定计算,以防止发生共振