盒形件落料拉深模设计Word文件下载.docx
《盒形件落料拉深模设计Word文件下载.docx》由会员分享,可在线阅读,更多相关《盒形件落料拉深模设计Word文件下载.docx(23页珍藏版)》请在冰豆网上搜索。
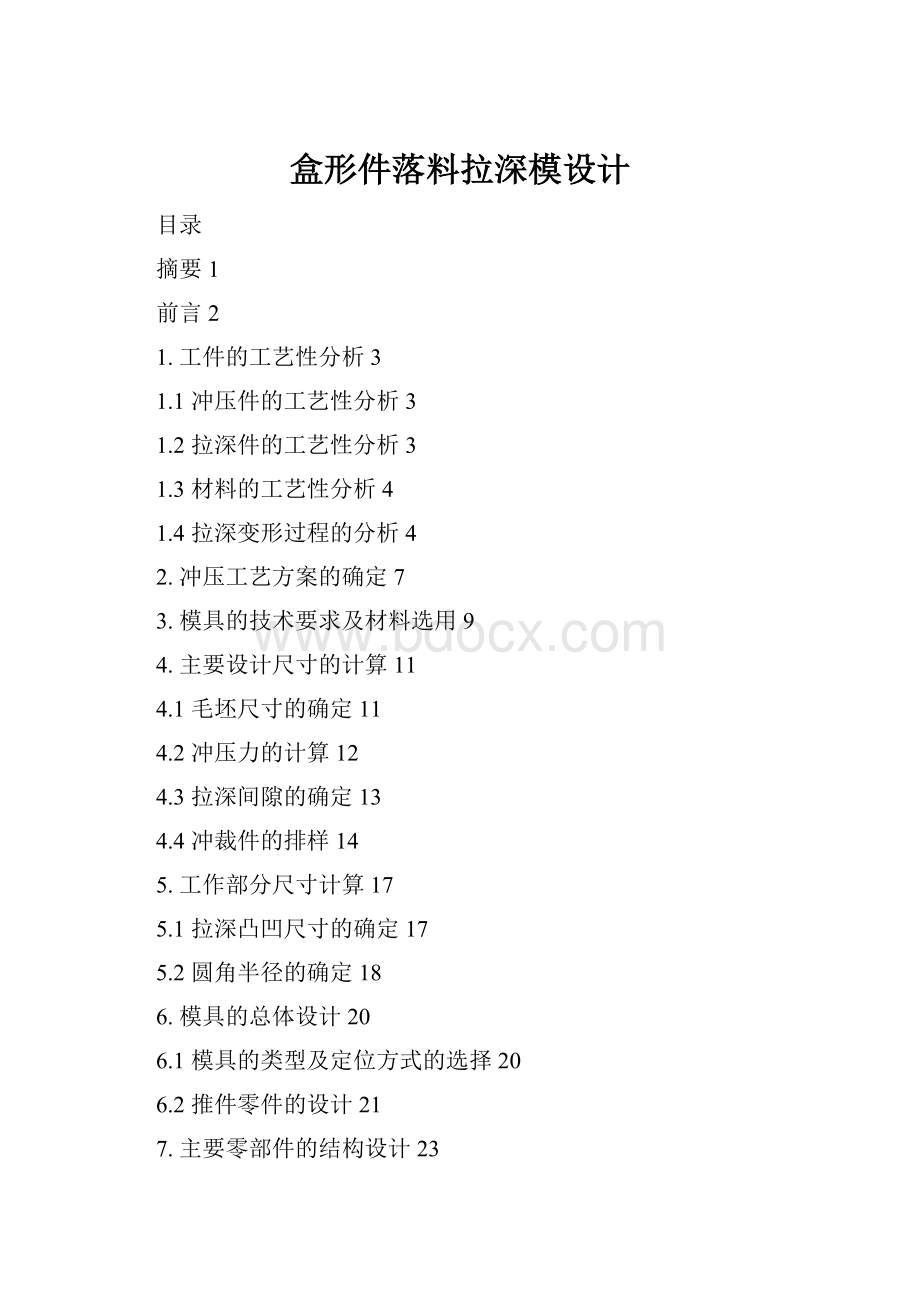
模具的总装图;
模具的装配等。
我觉得通过本次的毕业设计,达到了这样的目的:
1.综合运用本专业所学课程的理论和生产实际知识,进行一次冷冲压模具(落料拉深冲裁模)设计工作的实际训练,从而培养和提高我们独立工作的能力。
2.巩固与扩充所学有关冷冲模具设计课程的内容,掌握冷冲压模具设计的方法和步骤。
3.掌握冷冲压模具设计的基本技能,如计算、绘图、查阅设计资料和手册,熟悉标准和规范等。
关键词:
冷冲压落料拉深
前言
冲压是使板料经分离或成形而得到制件的加工方法。
冲压利用冲压模具对板料进行加工。
常温下进行的板料冲压加工称为冷冲压。
冷冲压模具在工业生产中的地位:
是大批生产同形产品的工具,同时也是工业生产的主要工艺装备。
模具工业是国民经济的基础工业。
模具可保证冲压产品的尺寸精度和质量稳定,而且在加工中不破坏产品表面。
用模具生产零件可以采用冶金厂大量生产的廉价的轧制钢板或钢带为坯料,且在生产中不需要加热,具有生产效率高、质量好、重量轻、成本低且节约能源和原材料等一系列优点,是其它加工方法所不能比拟的。
使用模具已成为当代工业生产的重要手段和工艺发展方向。
现代制造工业的发展和技术水平地提高,在很大程度上取决于模具工业的发展。
目前,工业生产中普遍采用模具成形工艺方法,以提高产品的生产效率和质量。
一般采用压力机进行零件加工,一台普通压力机每分钟可生产零件几件到几十件,而高速压力机的生产效率已达到每分钟数百件甚至上千件。
据不完全统计,飞机、汽车、拖拉机、电机、电器、仪器、仪表等产品,有60﹪左右的零件是利用模具加工出来的;
而自行车、手表、洗衣机、电冰箱及电风扇等轻工业产品,90﹪左右的零件是利用模具生产出来的;
至于日常生活所用的五金、餐具等的大批量生产基本上也是靠模具来进行生产的。
显而易见,模具作为一种专用的工艺装备,在生产中的作用和地位正日趋上升。
1.工件的工艺性分析
1.1冲压件的工艺性分析
冲压件的工艺性是指冲压件对冲压工艺的适应性。
在一般情况下,对冲压件工艺性影响最大的是它的几何形状尺寸和精度要求。
良好的冲压工艺性应能满足材料较省、工序较少、模具加工较容易、寿命较高、操作方便及产品质量稳定等要求。
1.冲裁件的形状应能符合材料合理排样,减少废料。
2.冲裁各直线或曲线的连接处,宜有适当的圆角。
3.冲裁件凸出或凹入部分宽度不宜太小,并应避免过长的悬臂与窄槽。
4.腰圆形冲裁件,如允许圆弧半径,则R应大于料宽的一半,即能采用少废料排样;
如限定圆弧半径等于工件宽度之半,就不能采用少废料排样,否则会有台肩产生。
5.冲孔时,由于受到凸模强度的限制,孔的尺寸不宜过小。
6.冲裁件的孔与孔之间,孔与边缘之间的距离,受到模具强度的限制,不能太小。
7.在弯曲件或拉深件上冲孔时,其孔壁与工件之间的距离不能过小。
1.2拉深件的工艺性分析
拉深零件的结构工艺性是指拉深零件采用拉深成形工艺的难易程度。
良好的工艺性是指坯料消耗少、工序少,模具结构简单、加工容易,产品质量稳定、废料少和操作简单方便等。
在设计拉深零件时,应根据材料拉深时的变形特点和规律,提出满足工艺性的要求。
1.对拉深材料的要求
拉深件的材料应具有良好的塑性、低的屈强比、大的板厚方向性系数和小的板平面方向性。
2.对拉深零件形状和尺寸的要求
(1)拉深件的高度尽可能小,以便能通过1—2次拉深工序成形。
(2)拉深件的形状尽可能简单、对称,以保证变形均匀。
对于半敞开的非对称件,可成双拉深后再剖成两件。
(3)有凸缘的拉深件,最好满足d凸≥d+12t,而求外轮廓与直壁断面最好形状相似,否则,拉深困难,切边余量大。
(4)为了使拉深件顺利进行,凸缘圆角半径r≥2t。
当r<0.5mm时,应增加整形工序。
3.对拉深零件精度的要求。
(1)由于拉深件各个部位的料厚有较大的变化,所以对零件图上的尺寸应明确标注是外壁还是内壁。
(2)由于拉深件有回弹,所以零件横截面的尺寸公差,一般都在IT12级以下,如零件高于T12级,应增加整形工序。
(3)多次拉深的零件对外表面或凸缘的表面,允许有拉深过程中所产生的印痕和口部的回弹变形,但必须保证精度在公差允许范围之内。
1.3材料的工艺性分析
在本次设计中,选用的拉深材料为镀锌铁皮。
选择拉深材料时,首先应满足拉深件的使用要求。
由于该拉深件为另一零件的盖,不属于易损工件,对材料的耐磨度要求不高,还应满足冲压工艺对材料的要求,保证冲压过程顺利完成,即材料应具有良好的塑性和表面质量,以及板料厚度公差应符合规定,镀锌铁皮为一种优质结构钢,该结构钢已退火,而退火的目的消除钢的内应力,降低硬度提高塑性细化组织均匀化学成分,而且其抗剪和抗拉强度均不高(抗剪强度220~310MPa,抗拉强度280~390MPa)屈服强度亦不大(约为180MPa)伸长率约32%,所以综合其所有的力学性能,镀锌铁皮具有良好的拉深性能,适合拉深。
拉深是把一定形状的平板毛坯或空心件通过拉深模制成各种空心零件的工序。
在冲压生产中拉深是一种广泛使用的工序,用拉深工序可得到的制件一般可分为三类:
1.旋转体零件:
如搪瓷脸盆、铝锅等。
2.方行零件:
如饭盒、汽车油箱等。
3.复杂形状零件:
如汽车覆盖件等。
1.4拉深变形过程的分析
拉深变形过程大致是直径为D的圆形平板毛坯被凸模拉入凸凹模的间隙里,形成直径为d,高为H的空心圆柱。
在这一过程中,板料金属是如何流动的呢?
把直径为D的圆板料分成两部分:
一部分是直径为d的圆板,另一部分直径为(D—d)的圆环部分,把这块料拉深成直径为d的空心圆筒。
在这个拉深实验完成后,发现板料的第一部分变化不大,即直径为d的圆板仍然保持原形状作为空心圆筒的底,板料的圆环部分变化相当大,变成了圆柱的筒壁,这一部分的金属发生了流动。
扇形chef是从板料圆环上截取的单元,经过拉深后变成了矩形chef。
扇形单元体变形是切线方向受压缩,径向受拉深,材料向凹模口流动,多余的材料由于流动添补了双点划线部分。
设扇形面积为
,拉深后矩形面积为
,由于拉深使厚度变化很小,可认为拉深前后面积相等,即
所以,
综合起来看,平板毛坯
的环形区的金属在凸模压力的作用下,要受到拉应力和压应力的作用,径向伸长、切向缩短,依次流入凸、凹模的间隙里成为筒壁,最后使平板毛坯完全变成圆筒形工件。
拉伸时的应力状态和形变情况。
拉伸的变形区比较大,金属流动性比较大,拉深过程容易起皱、拉裂而失败。
因此,有必要分析拉深时的应力状态和变形特点,找出发生起皱、拉裂的根本原因,在制定工艺和设计模具时注意它,以提高拉深件的质量。
设在拉深件的某一时刻,分析各部分的应力状态。
1.平面凸缘部分------主变形区由于凸模向下压,迫使板料进入凹模,故在凸缘产生径向拉应力
,小单元体互相挤压产生切向压应力
,由于压边圈提供的压边力产生法向压应力
,在这3个主应力中
的绝对值比
、
绝对值小得多,凸缘上
是变化的,由凸缘外到内,
是由小变大,而
的绝对值是由大变小的,凸缘最外缘
的压应力是最大的,则材料在切向上必然是压缩变形。
如果被拉深的材料厚度较薄压边力太小,就有可能使凸缘部分的材料失稳而产生起皱现象。
2.筒壁部分------传力区该部分受到凸模传来的拉应力
和凸模阻碍材料切向自由压缩而产生的拉应力
,显然
的绝对值大,径向是拉深变形,径向的拉深是靠壁厚的变薄来实现的,故筒壁上厚下薄。
3.底部圆角部分------过渡区该部分受到径向拉应力
和切向拉应力
的作用,厚度方向上受到凸模的弯曲作用而产生压应力
。
材料变形为平面应变状态,径向拉深变形,是靠壁厚变薄来实现的,这部分材料变薄最为严重,最容易出现拉裂,此处称为危险断面。
4.圆筒的底部----不变形区这部分材料一开始就被拉入凹模中,始终保持平面状态,它受两向拉应力
和
的作用。
变形是三向的,
是拉深,
是压缩。
由于拉深变形受到凸模摩擦力的阻止,故变薄很小,可忽略不计。
拉深是材料发生塑性变形,所以必然伴随着加工硬化,如果工件需多次拉深才能成形,或工件是硬化效应强的金属,则应合理安排退火工序以恢复材料的塑性,降低其硬度和强度。
总之,了解拉深工艺的特点后,在制定工艺设计模具时,应考虑如何在保证最大变形程度下避免毛坯起皱和工件被拉裂。
2.冲压工艺方案的确定
冲压工艺方案的确定,可依据表2.1确定
表2.1冲压工艺方案
项目
单工序模
级进模
复合模
无导柱
有导柱
冲压精度
低
较低
较高,相当于IT10~IT13
高,相当于IT8~IT11
制件平整程度
不平整
一般
不平整,有时要校平
因压料较好,制件平整
制件最大尺寸和材料厚度
不受限制
300mm以下厚度达6mm
尺寸〈250mm厚度在0.1~6之间
尺寸〈300mm厚度常在0.05m~3mm
冲模制造的难度程度及价格
容易、价格低
导柱、导套的装配采用先进工艺后不难
简单形状制件的级进模比复合模具制造难度低,价格亦较低
形状复杂的制件用复合模比级进模制造难度低,相对价格低
生产率
可用自动送料出料装置,效率较高
工序组合后效率高
使用高速冲床的可能性
只能单冲不能连冲
有自动送料装置可以连冲,但速度不能太高
使用于高速冲床高达400次/分以上
由于有弹性缓冲器,不宜用高速,不宜连冲
材料要求
可用边角料
条料要求不严格
条料或卷料要求严格
除用条料外,小件可用边角料,但生产率低
生产安全性
不安全
手在冲模过程区不安全
比较安全
手在冲模工作区不安全,要有安全装置
冲模安装调整与操作
调整麻烦操作不便
安装、调整较容易、操作方便
安装、调整较容易,操作简单
安装、调整比级进模更容易,操作简单
分析表2.1,采用:
单工序模具结构简单,但需要两道工序两副模具才能完成,且生产效率低难以满足该工件大量生产的要求。
复合模需一副模具,生产率较高,尽管模具结构较单工序模复杂,但由于零件的几何零件形状简单对称,模具制造并不困难。
虽然级进模也需一副模具,且生产率较高,但模具结构复杂,送进料不方便,加之工件尺寸偏大。
通过分析对上述三种模具的比较,该件若能一次成形,则采用复合模最佳。
3.模具的技术要求及材料选用
利用模具生产制品零件,其模具质量的好坏,寿命的长短,直接关系到产品制造精度、性能和成本,是提高劳动生产率、降低消耗、创造效益,尽快使产品占领市场的重要性条件。
而模具的质量、使用寿命、制造精度及合格率很大程度上取决于设计时对模具材料的选用、热处理工艺要求、模具零件配合精度及公差等级的选择和表面质量要求。
一、冷冲模材料的性能
冷冲模包括冲裁模、弯曲模、拉深模、成形模和冷挤压模等。
冷冲模在工作中承受冲击、拉深、压缩弯曲、疲劳磨擦等机械的作用。
模具常常发生脆断、堆塌、磨损、啃伤和软化等形成的失效。
因此,作为冷冲模主要材料的钢材,应具有以下几个方面的性能:
1.应具有较高的变形抗力:
主要抗力指标包括淬火、回火抗压强度、抗弯强度等。
其中硬度是模具重要的抗力指标,高的硬度是保持模具耐磨性的必要条件。
工作零件热处理后的硬度在60HRC,强度和抗弯强度才能保证,模具才会具有较高的变形能力。
2.应具有较高的断裂抗力:
主要抗力指标有材料的抗冲击性能、抗压强度、抗弯强度、断裂抗力等。
冲击载荷下抵抗模具产生裂纹的性质也是作为防止断裂的一个重要依据,模具材料基体中碳含量越高,冲击韧性越高。
故载荷较大的冷冲镦及剪切模易受偏心弯曲载荷的细长凸模或有应力集中的模具,都需要有较高的韧性。
3.应具有较高的耐磨性和抗疲劳性能:
对于在一定条件下工作的模具钢,为了提高耐磨性,可在硬度高的材料表面上均匀涂抹大量细小硬的碳化物。
在相同硬度下提高钢的耐磨性可减小模具在交变应力条件下产生的疲劳破坏,如模具长期使用刮痕凹槽等。
4.应具有较好的冷、热加工工艺性:
钢材的加工工艺性能包括可锻性、可加工性、淬透性、淬硬性较小的脱碳敏感性和较小变形倾向等,以方便模具的加工,易于成形及防止热处理后变形等。
二、冷冲模材料的选择原则
1.要选择满足模具零件工作要求的最佳综合性能的材料。
2.要针对模具失效形式选用钢材:
钢材的失效是影响模具寿命的主要因素,包括:
(1)为防模具开裂,要选用韧性好的材料
(2)为防磨损,应选用合金元素高的材料
(3)对于大型冲模应选用淬透性好的材料
(4)为保持钢材硬度性能,要选用耐回火性高的含铬、钼合金钢
(5)为防热处理变形,对于形杂的零件应选用含碳量高、淬透性好的高合金材料
3.要根据制品批量大小,以最低成本的选材原则选用:
对于需冲压数量较多模具,一般采用优质合金钢,而数量少的则采用碳素钢,以降低成本。
4.要根据冲模零件的作用选择:
凸、凹模模具应选用优质的钢材制作,对于数量不多或厚度不大的可采用有色金属或黑色金属。
而对于支撑板、卸料零件、导向件应选用一般钢材。
5.要根据冲模精密程度选用:
在制造小型精密模具而又复杂时,可选用优质合金钢制作,而对于比较简单,形状、精度要求不高的模具应选用比较便宜的碳钢或低合金钢。
4.主要设计尺寸的计算
4.1毛坯尺寸的确定
根据毛坯尺寸的确定原则可知有两种方法来计算毛坯的计算原则:
1.面积相等原则:
由于拉深前和拉深后材料的体积不变,对于不变薄拉深,假设材料厚度拉深前后不变,拉深毛坯的尺寸按“拉深前后的表面积相等”来确定。
2.形状相似原则:
拉深毛坯的形状一般与拉深件横截面的形状相似,即当零件的形此处删减NNNNNNNNNNNNNNNN字
需要整套设计请联系q:
99872184。
6.1模具的类型及定位方式的选择
6.1.1模具类型的选择
由冲压工艺分析可知,采用复合冲压,所以模具类型为落料——拉深复合模。
6.1.2定位方式的选择
为保证条料的正确送进和毛坯在模具中的正确位置,冲裁出外形完整的合格零件,模具设计时必须考虑条料或毛坯的定位。
正确位置是依靠定位零件来保证的。
由于毛坯形式和模具结构不同,所以定位零件的种类很多。
设计时应根据毛坯形式、模具结构、零件公差大小、生产效率等进行选择。
定位包含控制送料步距的挡料和垂直方向的导料等。
1.挡料销
挡料销的作用是挡住条料搭边或冲压轮廓以限制条料的送进距离。
国家标准中常见的挡料销有三种形式:
固定挡料销、活动挡料销和始用挡料销。
固定挡料销安装在凹模上,用来控制条料的进距,特点是结构简单,制造方便。
由于安装在凹模上,安装孔可能会造成凹模强度的削弱,常用的结构有圆形和钩形挡料销。
活动挡料销常有于倒装复合模中。
始用挡料销用于级进模中开始定位。
2.导正销
在级进模中导正销通常与挡料销配合使用,以减少定位误差,保证孔与外形的相对位置尺寸精度要求。
当零件上没有适宜于导正销导正用的孔时,对于工步数较多、零件精度要求较高的级进模,应在条料两侧的空位处设置工艺孔,以供导正销导正条料使用。
此时,导正销固定在凸模固定板或弹压卸料板上。
3.侧刃
在级进模中,常采用侧刃控制条料步距,从而达到准确定位的目的。
侧刃实质上是裁切边料凸模,通过侧刃的两侧刃口,切除条料两侧边缘部分材料,形成一台阶。
条料切去部分边料后,宽度才能够继续送入到凹模,送进的距离为切去的长度。
当材料送到切料后形成的台阶时,侧刃挡块阻止了材料继续送进,只有通过模具下一次地工作,新的送料步长才能形成。
4.定位板和定位钉
定位板和定位钉是为单个毛坯定位用的元件,以保证前后工序相对位置精度或工件的内孔与外轮廓的位置精度要求。
5.送料方向的控制
条料的送料方向是条料靠着一侧导料板,沿着设计的送料方向导向送料,为使条料靠紧一侧的导料板,保证送料的精度,可采用侧压装置。
因为该模具使用的是条料,所以导料采用导料板(本副模具中固定卸料板与导料板为一体),采用挡料销控制送进距。
6.2推件零件的设计
6.2.1卸料零件的设计
设计卸料零件的目的,是将冲裁后卡在凸模上或凸凹模上,或凸模上的制件或废料卸掉,保证下次冲压时能正常进行,常用的卸料方式有以下几种:
(1)刚性卸料
刚性卸料是采用固定卸料板卸料,常用于较硬、较厚且精度要求不高的工件冲裁后卸料。
当卸料板只起卸料作用时,与凸模的间隙随着材料厚度的增加而增大,单面间隙取
;
当固定卸料板还要起到对凸模的导向作用时,卸料板与凸模的配合间隙应小于冲裁间隙。
此时要求卸料后凸模不能完全脱离卸料板,保证凸模与卸料板配合大于
常用的固定卸料板有几种:
卸料与导料为一体的整体式卸料板;
卸料板与导料板分开的组合式卸料板(在冲裁中应用最广泛);
用于窄长零件的冲孔或切口卸件的悬臂式卸料板;
在冲孔底部用来卸空心件或弯曲的拱形卸料板。
(2)弹性卸料板
弹性卸料板具有卸料和压料的双重作用,主要用于冲裁料厚在
以下的板料。
由于有压料作用,冲裁比较平整。
弹压卸料与弹性元件、卸料螺钉组成弹性卸料装置,卸料板与凸模配合的单边间隙选择
,若弹压卸料板还要起到对凸模的导向作用,二者的配合应小于冲裁间隙。
弹性元件的选择应满足卸料力和冲模结构要求。
6.2.2顶件装置的确定
推件和顶件的作用是将制件从凹模中推出来(凹模在上模)或顶出(凹模在写模)。
推件力是通过压力机的横梁作用在一些传力元件上,使推件力传递到推件板上将制品(或废料)推出凹模。
推板的形状和推杆的位置应根据被推材料的尺寸和形状来确定。
设计在下模的弹性顶件装置,通过凸模下压使弹性元件在冲压时储存能量,模具回程时顶件器的弹性元件释放能量,顶件块将废料从凹模中顶出。
模具采用固定卸料,刚性打件,并利用装在压力机工作台下的标准缓冲器提供压边力。
6.2.3导向方式的选择
常用的模架有:
滑动式导柱导套模架、滚动式导柱导套模架。
模架有上、下模座和导向零件组成,是整副模具的骨架,模具的全部零件都固定在它的上面,并承受冲压全过程的全部载荷。
模具上模座和下模座分别与冲压设备的滑块和工作台固定。
上、下模间的精度由导柱、导套的导向来实现。
主要模架形式有:
对角模架:
由于导柱安装在模具的中心对称的对角线上,所以上模座在导柱上滑动平稳,常用于横向送料级进模或纵向送料的落料模、复合模。
后侧导柱模架:
由于前面和左右不受限制,送料和操作比较方便,因导柱安装在后侧,工作时偏心距会造成导柱导套单边磨损,并且不能用浮动模柄结构。
中间导柱模架:
导柱安装在模具的对称线上,导向平稳,准确,但只能在一个方向送料。
四导柱模架:
具有平稳、导向准确可靠、刚性好等优点,常用于冲压尺寸较大或精度较高的冲压件。
滚动式导柱导套模架的导向精度高,使用寿命长。
主要用于高精度、高寿命的精密模具及薄材料的冲裁模具。
根据标准模架的选择,为了提高模具寿命和工件质量,方便安装调整,该复合模采用中间导柱的导向方式。
7.主要零部件的结构设计
7.1工作零件的结构设计
由于工件形状简单对称,所以模具的工作零件均采用整体结构,拉深凸
模、落料凹模的结构如下图:
图7.1为拉深凸模,图7.2为落料凹模。
图7.1拉深凸模
图7.2落料凹模
为了实现先落料后拉深,模具装配后,应使拉深凸模的端面比落料凹模端面低。
所以图7.1所示拉深凸模,其长度L可按下式计算:
式中
凸模固定板的厚度,
凹模的厚度,
装配后,拉深凸模的端面低于落料凹模端面的高度,根据板厚大小,决定
7.2其他零部件的设计与选用
7.2.1弹性元件的选用
该模具中的弹性元件主要采用弹簧,顶件块在成形过程中一方面起压边力作用,另一方面还可将成形后包在拉深凸模上的工件卸下。
其压边力由标准缓冲器提供。
7.2.2模架的选用
模具选用中间导柱标准模架,可承受较大的冲压力。
为防止装模时,上无转
装配,将模架中两对导柱与导套制作成粗细不等:
导柱
分别为
导套
上模座厚度取
,即
上模垫板厚度取
固定卸料板厚度
下固定板厚度取
下模垫板厚度取
下模座厚度取
模具闭合高度
式中
凸、凹模的高度,
凸、凹模进入落料凹模的深度
可见该模具闭合高度小于所选压力机J23-25的最大装模高度(220mm),可以使用。
7.2.3模具辅助零件的材料选用及热处理
模具辅助零件的材料选用及热处理,见表7.1。
表7.1模具辅助零件的材料选用及热处理
零件名称
选用材料
热处理
硬度HRC
上模座、下模座
HT20~40HT25~47、ZG25、ZG35A3、A5
模柄
A3、A5
凸模固定板、凸凹模固定板
侧面导板
45
淬火
43~48
20
渗碳0.8~1
58~62
58~60
导正销、定位销
T7、T8
52~56
挡料销、挡料板
45~48
垫板、定位板
45、T7A
螺母、垫圈
A3
固定螺栓、螺钉
A3、45
销钉
顶杆、推杆
8.模具的总装图
由以上设计可得如图8.1所示的模具总装图。
为了实现先落料,后拉深,应保证模具装配后,拉深凸模的端面比落料凹模端面低
图8.1模具的总装图
模具工作过程:
将条料送入刚性卸料板下长条形槽中,平放在凹模面上,并靠槽的一侧,压力机滑块带着上模下行,凸凹模下表面首先接触条料,并与顶件块一起压住条料,先落料后拉深;
当拉深结束后,上模回程,落料后的条料由刚性卸料板从凸凹模上卸下,拉深成形的工件由压力机上活动横梁通过推件块从凸凹模中刚性打下,手工将工件取走后,将条料往前送进一个步距,进行下一个工件生产。