手机的塑料模具设计说明书高分子专业Word文档下载推荐.docx
《手机的塑料模具设计说明书高分子专业Word文档下载推荐.docx》由会员分享,可在线阅读,更多相关《手机的塑料模具设计说明书高分子专业Word文档下载推荐.docx(14页珍藏版)》请在冰豆网上搜索。
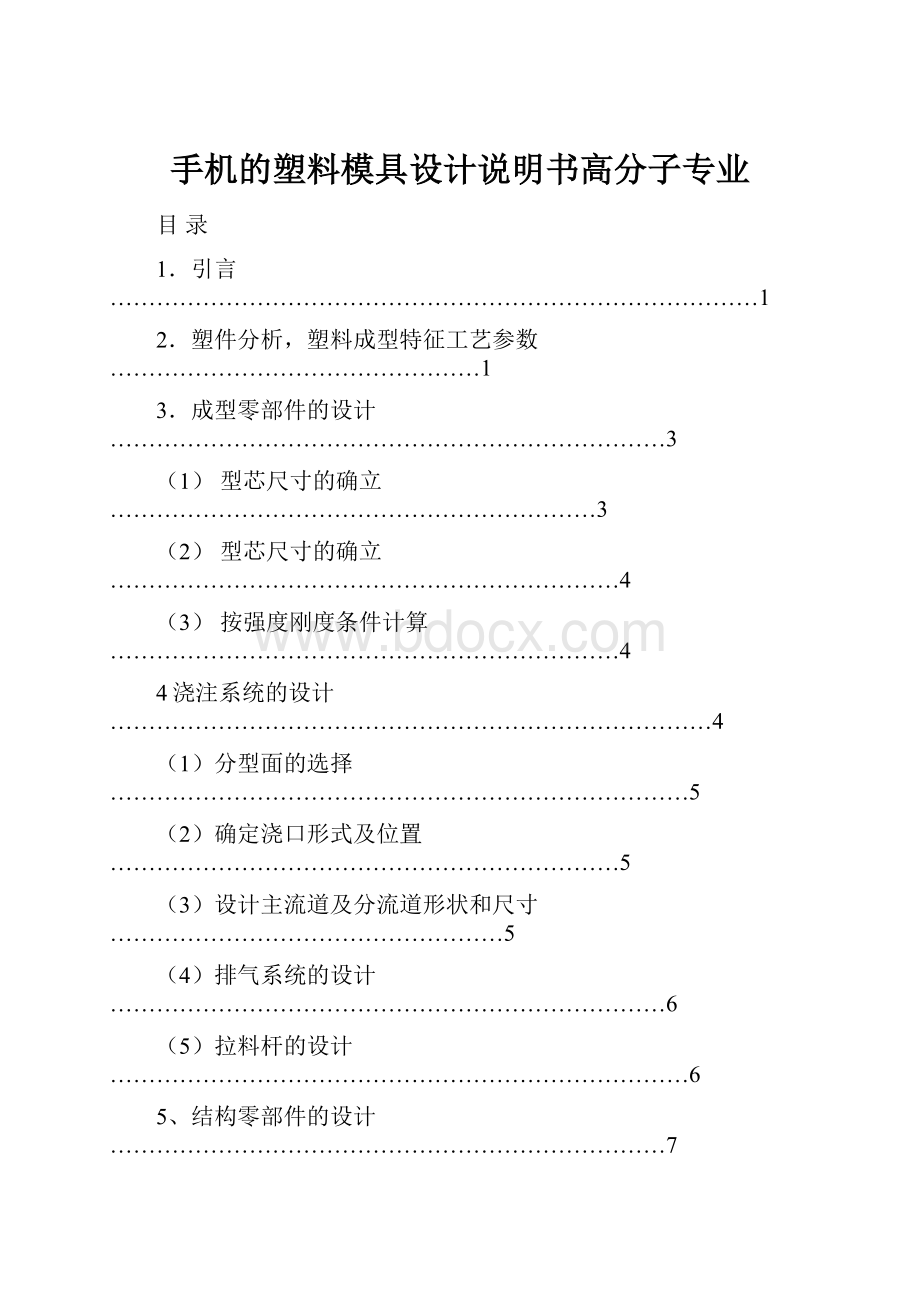
7冷却系统的设计……………………………………………………………………8
(1)冷却回路尺寸的确定及布置…………………………………………………9
8.选择注射机型号………………………………………………………………9
9结束语……………………………………………………………………………11
10参考文献…………………………………………………………………………11
笔盖的模具设计说明书
花生
化学化工学院高分子0801
摘要介绍了笔类在日常生活中的应用,重点介绍了笔盖的模具设计过程
Thesummaryintroducedpenintheapplicationinthedailylife,thepointintroducedthemoldingtoolofacoverdesignprocess
关键词日常用品模具设计实用性模具cad
1引言
日用品,有时采用精度和强度不太高的塑料传动,由于塑料具有可塑性强,密度小、比强度高、结缘性、化学稳定性高、外观多样的特点,因而受到越来越多的厂家及人民的喜爱。
塑料工业是新兴的工业,是随着石油工业的发展而应而生的,目前塑料制件几乎已经进入一切工业部门以及人民日常生活的各个领域。
随着机械工业电子工业,航空工业、仪器仪表工业和日常用品工业的发展,塑料成型制件的需求量越来越多,质量要求也越来越高,这就要求成型塑件的模具的开发,设计制造的水平也须越来越高。
本文也就对日用品中的笔盖模具设计过程进行阐述。
Dailynecessity,sometimesadoptthenotthathighplasticsofaccuracyandstrengthstospreadtomove,becausetheplasticshastheplasticitystrong,thedensityissmall,higherthanstrength,theknotgoodluck,thechemistrystabilityishigh,diversecharacteristicsofexternalappearance,asaresultbesubjectedtomoreandmorefactorieshouseandthepeople'
sfancies.Theplasticsindustryisanewlyarisenindustry,isalongwiththedevelopmentofthepetroleumindustrybutshouldbutlivingof,theplasticssystempiecealmosthavealreadyenteredeachrealmofthewholeindustrysectionsandpeople'
sdailylifescurrently.Alongwiththemachineindustryelectronicsindustry,aviationindustry,theinstrumentappearanceindustryandusuallythedevelopmentofthethingindustry,theplasticsmodelsthedemandofmakethepiecemoreandmore,thequantityrequestisalsomoreandmorehigh,thiswillbegmodelthepieceofthedevelopmentofthemoldingtool,thelevelofthedesignmanufacturingalsothebeardismoreandmorehigh.Thistextalsodesigntheprocesstocarryonelaboratetoacovermoldingtool.
2.塑件工艺分析
如图所示塑料制件材料为丙烯腈—丁二烯-----苯乙烯共聚物(ABS),查表得收缩率为:
0.3%-0.8%,取值0.4%;
大批量生产
材料分析:
ABS无毒无味,呈微黄色,成型的塑件有较好的光泽,具有良好的机械强度和一定的耐磨性,耐寒性,耐油性,耐水性,化学稳定性和电器性能,密度为1.02~1.5/cm3
ABS有一定的硬度和尺寸稳定性,易于加工,经过配色可配成任何颜色。
成型特点:
ABS在升温时粘度增高,所以成型压力较高,故塑件上的脱模斜度宜稍大,ABS易吸水,成型加压前应进行干燥处理,ABS易产节痕,模具设计时应注意尽量减少浇注系统对料流的阻力,在正常的成型条件下壁厚,熔料温度对收缩率影响极小,在要求塑件精度高时,模具温度可控制在50~60°
c,而在强调塑件光泽和耐热时,模具温度应控制在60~80°
c。
1)该塑件尺寸较小,一般精度等级4,为降低成本,采用一模多腔,并不对制品进行后加工。
2)根据塑件的生产效率及为提高成型效率采用侧浇口。
3)为了方便加工和热处理,型腔与型芯采用拼镶结构.
确定型腔;
尺寸精度等级要求一般,采用一模12腔。
按照图1塑料件图示尺寸(圆角等部位简化)近似计算:
塑件体积Vs≈1.37cm³
查表《塑料模设计手册之二》表1.4塑料ABS的密度为1.02~1.05g/cm³
单件塑件重量Ms=Vs×
ρ=0.194×
1.05≈1.78g
3.成型零部件的设计
查表《塑料模设计手册之二》表1.4塑料ABS收缩率0.3%-0.8%,取值0.4%。
3.1型腔、型芯工作尺寸计算
型腔径向尺寸Lm+0δz=[(1+S)LS-x△]+0δz
型腔深度尺寸Hm+0δz=[(1+S)Hm-x△]+0δz
型芯径向尺寸lm-0δz=[(1+S)lS-x△]-0δz
型芯高度尺寸hm-0δz=[(1+S)hS+x△]-0δz
式中LS———塑件外型径向基本尺寸的最大尺寸(mm);
lS———塑件内型径向基本尺寸的最小尺寸(mm);
HS———塑件外型高度基本尺寸的最大尺寸(mm);
hS———塑件内型深度基本尺寸的最小尺寸(mm);
CS———塑件中心距基本尺寸的平均尺寸(mm);
X———修正系数,取0.5~0.75;
△———塑件公差(mm);
δZ———模具制造公差,取(1/3~1/4)△。
3.1.1型腔尺寸计算
尺寸公差值/mm计算
140.38Lm+0δz=[(1+0.65%)X14-0.75X0.38]0+0.127=13.8060+0.127
3.50.26Lm+0δz=[(1+0.65%)X3.5-0.75X0.26]0+0.087=3.32770+0.087
510.12Hm+0δz=[(1+0.65%)X51-2/3X0.12]0+0.040=51.24150+0.040
3.1.2型芯尺寸计算
尺寸公差值/mm计算
8.50.26lm-0δz=[(1+0.65%)X8.5+0.75X0.26]0-0.087=8.750-0.087
400.16Hm-0δz=[(1+0.65%)X40+0.75X0.16]0-0.053=40.380-0.053
3.2成型零部件的强度与刚度计算
(1)刚度校核
δmax=
=
化简得出s≥1.15
式中E—型腔材料弹性模量;
J—梁的惯性矩
S—侧壁厚度
P—型腔内单位面积熔体压力
根据查表结果得出E=2.06×
10
Mpa[δ]=0.05mm P取30Mpa,代入计算得出结果19≥1.15
,成立故能满足其刚度要求。
(2)强度校核
s≥r(
式中[
—型腔材料许用拉应力为150Mpa代入计算得出19≥r(
成立故能满足其强度要求,确定最小壁厚之后,结合模具抽芯原则,初步确定选用A3型模架,模架周边尺寸为250×
160.
4.浇注系统的设计
1)分型面的选择根据分型面的设计原则,
1分型面应该选在塑件的最大轮廓处
2分型面的选择应有利于塑件的顺利脱模
3分型面的选择应保证塑件的精度要求
4分型面的选择应满足塑件的外观质量要求
5分型面的选择要便于模具的加工制造
6分型面的选择应有利于排气
综合上面几点故分型面如下图
2)
确定浇口形式及位置为了提高成型效率,采用潜伏式侧浇口。
浇口位置可以根据经验公式计算
n=0.8
W=n√A/30≈1mm
t=0.8δ=0.8×
1.3=1mm
W---侧向浇口之宽(mm)
A---型腔一侧表面积(等于v/t)(mm²
)
T和δ为塑件在浇口位置处的壁厚.
3)设计主流道及分流道形状和尺寸
主流道的设计主流道是指浇注系统中从注射机喷嘴与模具接触出开始到分流道为止的塑料体的流动通道,根据模具设定为一模8腔,可以估计一次成型所需的塑料,因此可确定型号为注射机XS-Z-30,结合厂里实际应用情况,及模架的选择及刚度与强度要求浇口套设计如下:
主流道设计成圆锥型,其锥角为2º
~6º
,内壁粗糙度Ra取1.6µ
m。
分流道截面设计成圆形截面加工容易,且热量损失与压力损失均不大,为常用形式。
圆形截面分流道的直径可根据塑件的流动性良好,所以造圆形截面。
根据经验分流道的直径d可取4~6mm。
分流道的设计在设计多型腔或者多浇口的单型腔的浇注系统时应设置分流道,考虑到U形截面加工较容易,而且热量损失与压力损失均不大,故为所选,根据经验值分流道宽度为3.2-9.5才是合理的,故分道流道宽度b=4mm,半径R=b/2=2,深度h=1.25×
2=2.5,为了能够使塑料流动平衡均匀,使排列紧凑流程尽量短,使胀模力的中心与注射机锁模力中心一致。
(4)排气系统的设计
利用配合间隙排气,这是最常见的,也是最经济的,更是具有使用性的。
利用滑块和导滑槽配合间隙便可以排气,所以这里无须开排气槽。
(5)拉料杆的设计
拉料杆的作用是注射结束模具
分型时,将主流凝料从定模浇
口套中拉出,最后推出机构开
始工作,将塑件和浇注系统冷
料一起推出模外。
该塑件表面
光滑无刮痕等缺陷,如果采用
自动脱落,塑件脱落表面相互
碰撞将造成表面刮痕等缺陷,因
此该模具采用Z字形拉料杆,
如图所示。
工作时依靠Z字形
钩将主流道凝料拉出浇口套。
5、结构零部件的设计
5.1支承板设计
支承板的作用是承受成型塑料熔体对动模型腔的作用力,以防止型腔底部产生过大的挠曲变形或防止主型芯脱出型芯固定板。
支承板需要有较高的平行度和必要的硬度和强度。
支承板的厚度计算h≥{5pbL4/32EB[δ]}1/3
式中h———支承板的厚度(mm);
p———承受的注射压力(MPa);
L———支承板跨度(mm);
b———支承板受力的宽度(mm);
E———刚的弹性模量,取2.06X105Mpa;
[δ]———允许的变形量(mm);
h≥{5X20X72X964/32X2.06X105X250X0.06}1/3mm≈18.356mm
由上面所计算的数值可知支承板厚度≥18.356mm,取20mm。
该模具支承板取160X250X20GB/T4169.8——1984
5.2垫块的设计
垫块的作用是支承动模成型部分并形成推出机构运动空间的零件。
其中相关尺寸根据模架以及推出高度而定,取250X32X50GB/T4169.6——1984。
5.3合模导向机构的设计
合模导向机构是保证动、定模和模时,正确地定位和导向的零件,承受一定的侧压力。
该模具导柱为带头导柱ф16*50*25GB/T4169.4——1984,导柱的材料为T8,淬硬到HRC50~55;
该模具导套为直导套ф16*25GB/T4169.3——1984,导套的材料为T8,淬硬到HRC50~55。
6推出机构的设计
推出机构一般由推出、复位和导向三大部件组成,推出机构按其推出动作的动力来源可分为手动推出机构、机动推出机构、和液压与气动推出机构等,按模具的结构特征可分为一次推出机构、二次推出机构、定模推出机构等等
一次推出机构又称简单推出机构,它是指开模后在动模一侧用一次推出动作完成塑件的推出。
一次推出机构,包括推杆推出机构,推管推出机构,推件板推出机构等等。
由于设置推杆的自由度较大,且截面大部分为圆形,制造维修方便、推出动作灵活可靠,推出时运动阻力小,便于跟换,结合模架的选择综合各方面因素考虑,推杆推出机构应该是首选。
(1)推杆的设计
根据推杆位置的选择要求:
推杆的位置应该选择在脱模阻力最大,当塑件各处的脱模阻力相同时需要均匀布置、推杆位置选择时应注意塑件本身的强度与刚度,推杆装入模具后,其端面应与型腔底面平齐,或高出型腔0.05-0.1mm,考虑冷料穴中有较多的塑料,根据各模板的厚度、型腔尺寸、分流道及最小壁厚考虑设计推杆如下:
(2)复位杆的设计
推出机构在注射模工作时,每开合模一次,就往复运动一次,除了推杆和复位杆与模板的活动配合以外,其余均处与浮动状态,使推出机构复位最简单最常用的方法是在推杆固定板同时安装复位杆,复位杆为圆形截面,每副模具一般设置4根根据模架的选择,复位杆设计如下:
数量为4根,中心距为146×
50mm,此外由于设置侧向抽芯的缘故,为了防止干涉需要在复位杆设置弹簧,弹簧先复位机构是利用弹簧的弹力使推出机构在合模之前进行复位的一种先复位机构,即弹簧被压缩地安装在推板固定板与动模支承板之间。
为了使复位杆能够及时复位,设计弹簧中径为14mm,截面直径为3mm。
7、冷却系统的设计
7.1冷却回路尺寸的确定及布置
由于冷却水道的位置、结构形式、孔径、表面状态、水的流速、模具材料等很多因素都会影响模具的冷却,因此用塑件的平均壁厚来确定水孔直径。
塑件平均壁厚为1.6mm,尺寸较小,确定水孔直径为8mm。
通过调节水温、水速来满足要求。
8.选择注射机型号
1)初选注射机
1注射量:
该塑料制件的单件重量
Ms≈1.78g
浇注系统重量的计算,根据浇注系统尺寸先计算浇注系统的体积Vj=20+1407.95+1030≈2527.95cm³
粗略计算浇注系统重量
Mj=Vj×
ρ≈30g
总体积V塑件=934.56+2527.95=3.3925cm³
总质量M=3.3925×
1.05≈36g
ABS的密度为1.03~1.05g/cm³
。
满足注射量:
V机≥V塑件/0.80
式中V机——额定注射(cm³
V塑件---塑件与浇注系统凝料体积和(cm³
V机=V塑件/0.8≈4.3cm³
或满足注射量M机≥M塑件/0.8
M机=
(5)吴兆祥主编.模具材料及热处理.机械工业出版社.