木工部操作工艺设计流程Word格式.docx
《木工部操作工艺设计流程Word格式.docx》由会员分享,可在线阅读,更多相关《木工部操作工艺设计流程Word格式.docx(11页珍藏版)》请在冰豆网上搜索。
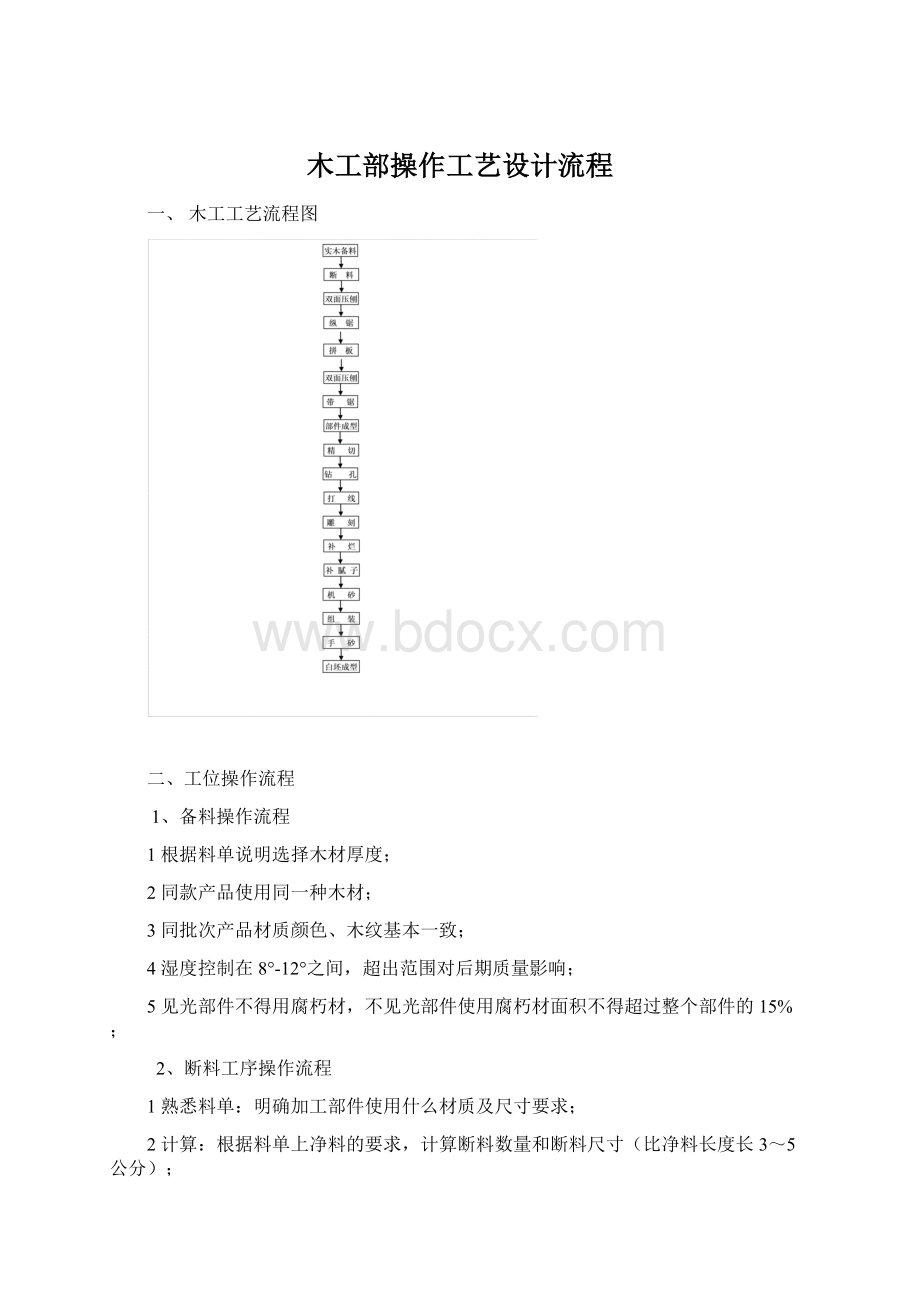
☆开料一个订单一次开完,避免生产时不能配套生产和转运时一个已经在包装有些还没有开料而影响货期;
☆断料后必须把料放到卡板上,并且排放整齐,并且木纹统一朝一个方向;
避免给后工序造成加工困扰;
3、双面压刨工序操作流程
核对纵锯后的部件尺寸是否控制在3~7MM以内;
2设备检查:
检查上下刨刀是否旋紧定位,是否锋利,是否平顺,刨刀不锋利在加工过程中部件易产生倒刺现象;
3调机:
根据部件毛料的多少,调节刨刀的深度;
4刨前检查:
a.检查每个部件是否很直,若弯曲程度超过7MM,则不要继续加工;
b.检查表面死节、腐烂、白芯等,根据部件在产品上的使用效果,确定是否使用;
c.用角尺测量两端的尺寸是否都控制在毛料范围内;
d.开机时,不能立即送料刨削,等刨刀运转平稳后方可进行加工;
5操作流程
a.刨大料时,操作员的手只能按在料上面,刨小料时,手只能按在表面两个棱角,不能小于3CM,同时禁止手在料后推动,以免伤手;
b.刨削量每次一般不得超过1cm,经过刨口时用力要轻,严禁在刨刀上方回料;
c.刨厚度小于3CM,长度小于40CM的木料,进料时不能用手推,只能用推棍;
d.遇节疤时,要减慢推动速度,禁止手按在节疤上推料;
6刨后检查:
●部件是否水平、有倒刺,棱角是否垂直;
●部件水平、棱角垂直都影响部件在产品上的工艺:
●若部件不水平将影响排孔的准确性;
又比如餐椅脚,若棱角不垂直将造成脚与侧牙或者前后牙连接不紧密的结构问题;
●倒刺现象要求:
倒刺是因刨刀不锋利或者刨刀调得太深造成的,若倒刺深度在0.5MM以内,则可通过砂光,打磨处理,若超过0.5MM,则需根据部件在产品上的位置,酌情使用。
7刨平后部件堆放整齐,贴好标识卡(订单号和订单数量、部件名称和部件数量、工位操作人);
4、纵锯工序操作流程
明确各部件的尺寸加工要求,并核对上工序加工尺寸是否符合本工序的加工范围;
操作人员需计算在卡板上每平铺一层木材能开多少部件;
3加工前检查:
检查木材有无不规则的边,比如:
带木皮的边、崩缺严重的边等,若存在,需先切除不规则边;
4加工时检查:
检查木材有无中间开裂、死节疤(主要是见光部件)、虫眼、翘曲严重的部分,若存在,需从中间切除不良部分,以便于拼料时,不会影响产品质量;
5调试机器:
根据加工要求,调试机器锯切深度和高度(加工方式:
顺首木纹方向纵切);
加工前检查:
每块部件加工前必须检查是否翘曲严重,如果弯曲度超过7MM,将影响净料尺寸,则不要加工;
边沿是否规则(不带木皮边、崩缺边、死节边),如果有不规则边,须切边后才能按要求的尺寸加工;
6首检:
加工首件后,核对料单尺寸,注意实际尺寸要比料单最终要求的尺寸大3~7MM;
7筛选:
色差太大(具体见木检实木样板),腐烂、开裂、白芯、虫眼等表面质量要筛选使用。
8点数:
清点数量,整齐堆放,做好标识(订单号和订单数量、部件名称和部件数量、工位操作人)。
●重点说明:
加工后的尺寸只是毛料尺寸,部件还需要通过平刨保证其部件垂直、水平,压刨:
去除表面,使部件变得规则、尺寸精确。
若毛料尺寸太小,可能会导致稍有弯曲的部件经过后道工序加工后,最终尺寸小于净料尺寸,若毛料尺寸太大,那么平刨的次数变多,或者二次压刨,给后道工序带来不必要的加工,因此,实际尺寸一定要控制在比净料尺寸大3~7MM;
加工后的部件,可以发现很多表面的质量问题,操作人员要结合各种部件在产品上的使用情况对无效利用的部件进行筛选,以免后面的工序无效加工。
5、拼板工序操作流程
1熟悉料单要求:
核对各部件尺寸,明确要拼什么规格的部件;
2胶水调配:
一次性不能调得太多,用不完的胶水1小时后将会硬化;
3组板:
拼接部件之间选用颜色相近的料,特别是餐椅部件,以免在同一部件上出现严重色差;
4总体宽度控制:
拼板架内空约900MM,所以组板后宽度应在内空范围内;
5材料筛选:
比如水曲柳脚,质量好的面放在表面,质量差的面拼在里面;
6涂胶:
涂胶要按照组板顺序进行,表面涂胶要均匀、全面,以免出现粘合不牢的现象(带穿孔的部件须先铣槽后拼板);
7上架:
部件上架顺序也要按照组板顺序依次进行,并平齐一端;
8压紧:
摆完后,要及时压紧,同时注意部件会不会拱起或者走位,若走位严重,要及时调整后,重新压紧;
9下架:
正常情况下,拼板后3个小时以上,胶水才能干透,若因拼板任务比较忙时,至少要等1小时才能下架,同时下架时要轻放,待放2小时以上才能弯料,以免拼接处裂开或者拼接不牢。
●胶水调配比例要求:
拼板胶与固化剂的调配比例为10:
1~10:
1.5,操作人员在调配时往往是先倒出拼板胶,再向其中适当的倒一点固化剂,没有严格按照这个比例操作,会导致拼接不牢的现象,在铣床的时,容易导致拼接板受力脱裂、飞溅,存在安全隐患。
可以制作两个符合上述比例的容器,每次可用容器来衡量调配比例;
●下架时间要求:
生产再忙,都不能违反下架时间的规定:
至少1小时以上才能下架并轻放,待放2小时以上才能弯料。
提前下架会造成拼接不牢,裂开,最终效果达不到品质要求;
●拼接板对色要求:
两块拼接板存在严重的色差问题,是达不到品质要求的;
6、二次双面刨(同一次双面刨同样操作)
7、带锯工序操作流程
明确要加工成什么部件,并核对上工序加工是否符合料单要求;
2核对模板:
将模板和大样图进行核对,检查有无变形、破损、膨胀等问题(模板尺寸是净料尺寸);
3按模画线:
根据模板在已拼好料的大板上画出部件图形,画线时需注意:
a.严格按照模板的框架画线;
b.部件图形与图形之间至少要有5MM以上便于加工的间隔;
c.若加工的是见光部件,部件图形要避开木材表面的大节疤、开裂、等现象;
d.画线时,要考虑如何最大值的利用木材,以免浪费更大。
4弯料:
弯料时,带锯沿线外锯切,送料速度不易过快,避免锯齿发热造成死机或者安全问题;
5点数:
清点部件数量,贴好标识卡(订单号和订单数量、部件名称和部件数量、工位操作人)。
6重点说明:
模板是根据大样图制作的,模板是实际加工的参照,一旦模板存在质量问题,那么加工出来的产品一定存在质量问题;
若发现模板存在问题,不要勉强使用,应及时按样图重新制作,并根据以前加工的部件进行校对,同时模板的材料要选择不易变形,发涨等受环境影响的材料;
7画线要求:
画线不会直接影响部件按模铣床,但是会影响弯料的准确性,铣床时,会根据弯料的尺寸按模铣床,一旦料弯小了,部件将不符合铣床模板的要求;
因此,必须严格按模型画线;
8弯料要求:
带锯不能弯在线内,线内是净料尺寸,一旦弯到线内,铣床铣不到,会影响产品品质。
8、部件成型工序操作流程
1(铣床)检查设备:
重点检查铣刀有无开裂、拧紧,以防人身安全问题;
2进料:
必须等机械平稳运转后,才能进料,同时部件进刀要求不同:
●双钻左铣刀是逆时针旋转,右铣刀是顺时针旋转;
●弯曲部件是从部件中间进刀,左铣刀铣左边,右铣刀铣右边,有利于去除表面的倒刺,同时也是安全操作;
●小料、直料铣斜边类,只需从一边进刀就可以;
3检查模板是否变形,走样,松动,并核对模板是否符合工艺要求;
4按模加工部件必须严格按照进料要求操作;
5加工后的实木部件需对表面质量加以筛选,同时对表面加工后的效果进行检查(比如:
有无出现没铣到位的现象),不良品不能随大货流往下道工序;
6圆形部件加工:
●根据模板,钻好定心圆孔,根据板厚确定打孔深度,同时模板不能露出板件;
●按模调试机器,首件加工后,测量直径,批量加工时,需对其进行抽检。
7打槽类部件加工:
(比如:
衣柜门板、实木脚通孔槽、穿条槽、餐椅三角木槽等)
●根据图纸要求,调试机器,安装对应的钻头;
●制作首件,按图首检槽宽、槽距、槽深,合格后,批量加工;
●若部件变形,需校正后才能加工,以免槽位不对。
8打指接部件加工:
后脚、椅脑、床头等)
●根据图纸要求和模板,调节指接深度和边距;
●相邻部件加工一套,首检组装结构是否平整,指接深度是否符合图纸要求;
●加工时,部件指接不能打斜了,以免安装不密缝
9打线部件加工:
●操作前务必确保已靠紧模板,调紧了工具架。
●有模加工部件,首先检查模板的牢固性。
无模加工部件,首先按图纸要求制作首件;
●首件加工后,按图对斜边工艺进行首检,合格后,方能批量生产;
10打孔工序操作流程
●熟悉流程卡或料单:
明确要加工的部件,并核对模板是否符合流程卡要求;
●按模画线:
根据模板大样图尺寸要求,在首件在画好加工尺寸;
●调试机器:
安装钻头,根据样图要求调节加工深度;
●首件制作:
根据画线制作首件,并首检孔位长、宽、深度,孔边距,可拿合格的相邻出榫部件连接测试;
●.制模定位:
根据合格的首件部件,在台面上固定加工位置;
●再次检查:
定位后,加工的第一件,需再次核对孔位要求;
●配套:
分左右的部件需先分好后,再打孔;
●抽检:
加工过程中,需对部件孔位进行抽检,以免出现因定位模松动造成加工不良的现象;
●打孔时,必须保证每一次都要压到底,不能深浅不一;
●打孔前,要对表面存在质量问题的部件进行筛选;
11砂带工序操作流程:
●熟悉料单要求:
明确待砂部件的总体尺寸要求;
●检查设备:
重点检查砂带接口有无裂痕,砂带是否装紧;
●床头部件:
为了侧面砂平,部件砂出后,必须对每块测量部件尺寸和相邻角垂直,保证部件上下长度、左右宽度尺寸符合要求;
●注意砂磨铣床后留下的倒刺或其它表面不平滑的问题;
●补灰部件:
部件必须表面平整;
●倒角:
主要是餐台或者茶几脚底部倒角,倒角效果要均匀;
12砂带后检查:
每次砂带后,检验表面处理是否平整或者平滑;
☆以上工序完成后必须自检,并且有规律的放在卡板上,并且清楚(订单号和订单数量、部件名称和部件数量、工位操作人);
☆以上工序完成后需要雕刻的部件转入雕花部门,雕刻完成后完成以下工序
9、补烂工序操作流程
1根据部件材质选择胶水种类和调配比例;
调胶时必须调匀,湿度合适;
2检查部件是否符合工艺要求,如有崩缺、虫眼、雕刻部对称等问题,应补平和对称;
3在补的过程中,不宜补过多胶和原子灰,不免给后工序增加无效工作;
10、组装工序操作流程
1部件核对:
根据料单和样板、图片逐一核对,核对待加工部件材质、数量是否正确和符合要求;
核对订单数量和部件数量是否完全一致,否则会影响生产周期;
2组装:
整装产品,先试装一件,确认外观尺寸、结构功能、表面质量是否符合工艺要求;
3筛选:
批量组装前,需对每一个部件针对表面问题(如:
节疤、开裂、白芯、虫眼、崩缺等)加以筛选;
颜色相近且符合实木颜色样板的才能组装在一起,存在以上表面问题的部件,只能放在不见光部位;
4涂胶:
打胶必须均匀到位,不宜太厚;
5结构控制:
组装时,要做到指接密缝、斜口拼接成90度、椅类着地水平、床类或镜框类内空对角线相等,上下长度,左右宽度相等;
6胶水处理:
松夹后,需将表面的胶水处理干净;
7手砂:
待结构稳固后(放置3小时以上),用手砂机进行修理,便于最终成形;
8打气磨:
能看得见的部位都需处理平滑、圆滑,特别是要清除手砂印;
9开工艺线:
工艺线要求V形1.5*1.5MM,线条笔直、流畅;
10组装时内角必须加三角木打胶之后用枪钉死,避免开裂;
11组装时
12最后检验:
对结构的连接牢固性、表面质量、工艺线有无漏加工进行再次检验。
13配套:
板件分左右(比如:
带路轨的外侧板),对纹对号(比如:
斗面、门板);
14点数:
需转运到下工序再加工需清点各部件数量,按照下大上小、下长上短的原则合理摆放,贴好标识卡(注明订单号码、数量、部件数量、操作人)。
15重点说明:
操作人员在发现质量问题时,首先要具备基本的品质意识,想法有依据的,可自行判断,决定结果,若对发现的品质问题判断失误,只需在以后遇到类似问题时纠正即可,若想法不确定的情况下,要反馈给上师,协同处理。
16操作人员不应该受生产进度或者个人利益的影响,对发现的质量问题随意处理。
这样会造成因问题处理不彻底导致的返工现象。
木工部自检验标准
检验类型
检验项目
检验方式
检验方法
要求值
试装结构检验
用材
抽检
订单、图纸
符合订单及图纸要求
外观尺寸
卷尺
±
5MM以内
结构
测试
平整,稳固
功能
符合开发功能
实木干湿度
湿度仪
8~12度
试装效果检验
抽面/柜门对号对纹
目视
全部对纹对号
抽面/柜门缝隙
放平后测试
均匀,2~3MM之间,白/黑漆3~4MM之间
路轨/门铰灵活性
开合测试
开合顺畅,无杂音
部件连接
测量
被盖面不能突出盖面,被盖面嵌入2MM以内
脚架效果
正视五金不露出部件,安装良好
拉手效果
安装
不滑丝,安装良好
部件检验
与图纸相符
尺寸
孔位
配套
点数
全部左右配对、对纹对号
外观检验
三胺板脱纸
不允许
三胺板杂质
允许整装产品不见光部位
三胺板爆边
允许整装产品不见光部位,5*2MM以内
三胺板刮花
允许整装产品不见光部位,30*1MM以内
三胺板边露白
实木开裂
全检
实木节疤
允许见光部位三处不集中5MM以内未修补的节疤,椅脑见光部位不能有节疤(哑白色除外)
实木白芯
不允许见光部位(哑白色除外)
实木/中纤收缩
木皮起泡
脱胶
木皮纹理
纹理符合部件等级要求,方向符合开发或订单要求
掉皮
只允许整装不见光部位,10*2MM以内
明显刮花
只允许整装不见光部位,30*1MM以内
木皮发霉
只允许整装不见光部位,50*50MM以内
胶水印
只允许整装不见光部位,30*2MM以内