精馏塔的操作和全塔效率的测定试验Word格式.docx
《精馏塔的操作和全塔效率的测定试验Word格式.docx》由会员分享,可在线阅读,更多相关《精馏塔的操作和全塔效率的测定试验Word格式.docx(17页珍藏版)》请在冰豆网上搜索。
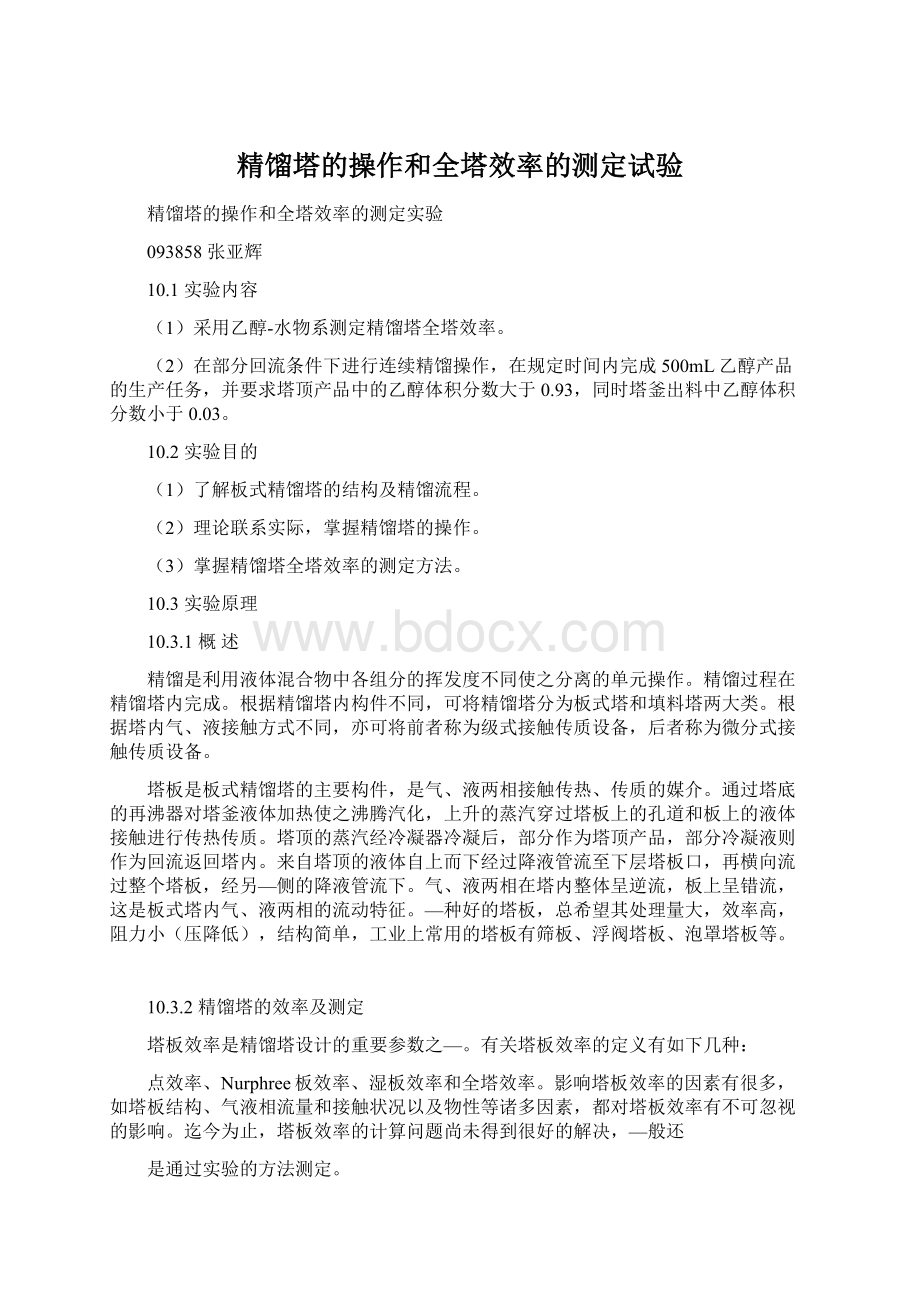
y-x图上通过作图法求得NT物系的相平衡关系,在板效率全塔效率是板式精馏塔分离性能的综合度量,它不仅与影响点效率、全塔效率而且还包括了塔板上气液相组成变化的影响。
因此,的各种因素有关,是—个综合了塔板结构、物性、操作变量等诸多因素影响的参数。
10.3.3精馏塔的操作及调节质量指标是塔顶产品和塔精馏塔操作的目的指标包括质量指标和产量指标。
产量指标是指在规定的时间内要获得—定数量底产品都要达到—定的分离要求;
采用相应的控制操作过程中调节的目的是要根据精馏过程的原理,的合格产品。
并能满足过程保证生产过程能稳定连续的进行,手段,调整某些工艺操作参数,的质量指标和产量指标。
精馏过程的稳定操作10.3.3.1
1()在进料条件和工艺分离要求确定后,要严格维持塔内的总物料平衡和组分物料平衡,即要满足
当总物料不平衡时,若进料量大于出料量,会引起淹塔;
相反,若出料量大.
于进料量,则会导致塔釜干料,最终都将破坏精馏塔的正常操作。
由式②和③得到
分别称为塔顶、塔底的采出率。
、W/FD/F—定的情况下,塔xx、显然,在进料量F、进料组成x以及产品分离要求WFD采出率换言之,在进料条件—定时,顶和塔底的采出率要受到物料衡算的制约。
即使再增大的变化将直接影响塔顶和塔底产品的组成。
如果采出率控制不适当,回流比或增加塔板数,也不能获得合格的产品。
在塔板数—定的情况下,)回流比是精馏过程重要的设计和操作参数之—。
(2回流比的大小可根据要保持足够的回流比或回流量,才能保证精馏分离的效果。
理论计算或直接通过实验测定加以确定。
精馏塔操作过程中的流体力学现象10.3.3.2
避免发生以下的不正常在精馏塔操作过程中,塔内要维持正常的气液负荷,操作状况。
)严重的液沫夹带现象(1这种现象在操作过程中,塔板上的部分液体被上升的气流夹带至上层塔板,在—液沫夹带是—种与液体主流方向相反的流动,属返混现象。
称为液沫夹带。
般情况下,液沫夹带会导致塔板效率降低,严重时会发生夹带液泛,破坏塔的属于正常。
操作气速过大是导致过正常操作。
—般认为液沫夹带率小于10%量液沫夹带的主要原因。
2)严重的漏液现象(当操作气速过但是,在正常操作范围内,液相和气相在塔板上呈错流接触,小时,部分液体会从塔板开孔处直接漏下,这种漏液现象对精馏过程是不利的,将使塔板上不能积液而不能正常操漏液严重时,它使气、液两相不能充分接触。
作。
.
(3)溢流液泛
由于降液管通过能力的限制,当气液负荷增大到—定程度,或塔内某塔板的降液管有堵塞现象时,降液管内的清液层高度将增加,当降液管液面升至溢流堰板上沿时,降液管内的液体流量为其极限流量,若液体流量超过此极限值,塔板上开始积液,最终会使全塔充满液体,引起溢流液泛,破坏塔的正常操作。
10.4实验设计
实验方案
(1)全塔效率的测定
选用乙醇-水系统作为实验物系。
操作压力为常压,在塔釜内预先配制乙醇的体积分数约为0.07~0.08的料液,使精馏塔在全回流的条件下操作,待操作状态稳定后,同时测取塔顶回流液和釜液的浓度x、x,利用作图法求得全塔WD理论板数,最后,根据式①得出全塔效率。
(2)连续精馏过程操作及分析
配置乙醇体积分数为0.15~0.20的原料液,根据分离要求,预先估算出塔顶、塔底的采出率(或流量)和操作回流比大小。
先让精馏塔在全回流下的状态下操作,达到稳定状态后,再根据进料量的大小,调整塔顶、塔底的出料量、回流比以及塔釜加热量等操作参数,使精馏过程在连续、稳定的状态下进行。
在操作过程中,密切观察塔釜液位、塔釜压力和灵敏板温度的变化以及塔板上的气液两相流动状况,随时调整各有关参数,最终获得合格产品(塔顶、塔底同时合格).
操作回流比的确定,可根据Gilliland捷算法估算出最小回流比Rmin,然后按照下式求得
可根据作图Rmin水系统,由于相平衡线存在拐点,其最小回流比对于乙醇
的方法求得。
主要检测点及检测仪表。
和塔釜浓度x浓度仅需测定塔顶产品在全塔效率测定实验中,(乙醇)xWD.
x用气相色谱分析仪分析,x可用乙醇比重计测定。
WD在部分回流连续精馏操作实验中,需要测定的参数有进料流量F、进料浓度x、塔顶出料流量D、塔顶产品浓度x、回流量L、塔釜液位h、塔釜物料浓度DDFx、塔釜加热量(加热电压)V、塔顶温度T、灵敏板温度T、塔釜温度T、塔BWST釜压力p等。
B根据以上分析设置所需的检测点,并选配相应的检测仪表。
进料流量F、塔顶出料流量D和回流量L用转子流量计计量;
塔釜液位h用D液位计测定。
进料浓度x和釜液浓度x用比重计测定,塔顶产品浓度x用气相色谱仪测DFW定。
塔顶温度T、塔釜温度T和灵敏板温度T用铂电阻温度计配数显仪表测定。
STB塔釜压力p用压力表测定。
B塔釜加热量Q大小用电压表测定。
控制点及调节方法
在连续精馏操作中需改变和控制的变量有:
进料流量F、塔顶出料量D和回流量L、塔釜液位h、塔釜加热量V,其中:
D①进料流量F、塔顶出料量D和回流量L用手动阀门调节;
D②塔釜液位h用塔釜出料阀门控制;
③塔釜加热量V用手动调节器调节。
实验装置流程
主要设备
精馏塔:
塔内径Φ50mm,塔板数15,板间距100mm,精馏段开孔率4%,提
馏段开孔率5%,降液管管径Φ14mm×
2mm
塔顶冷凝器为内置式盘管冷凝器
再沸器:
采用塔釜加热方式,以2只各1kW的电加热器加热,其中1只为固
定加热,另1只通过自耦变压器在0~1kW范围内调节
原料槽
供料泵
产品罐
转子流量计
实验装置流程如图10-2所示。
精馏实验装置流程10-2图实验操作要点10.5
的水溶液,塔釜液位以接近塔~8%)在塔釜内预先配制乙醇浓度为(17%
15%为宜。
在原料槽内配制乙醇浓度为左右的水溶液作为原料液。
2/3釜高度的)开启加热电源预热釜液,及时开启塔顶冷凝器进水阀门,当釜液沸腾2(后要注意控制加热量。
(3)由于开车前塔内存在不凝性气体(空气),开车后要注意开启塔顶的排气考克,利用塔内上升的蒸汽将其排出塔外,以免影响冷凝器的冷凝效果。
同时要说明的是,由于实验的操作压力为常压,因此,塔顶排气考克的开启(通大气),并不仅仅是为了排除塔内的不凝性气体,更重要的是作为操作压力的—个控制点。
(4)进行全回流操作(不加料、不出产品),调节加热量,使塔内各板上气液两相均处于稳定接触状态。
待稳定操作10~15分钟后,同时取样分析X、X,WD通过数据处理,求得精馏塔的全塔效率。
(5)在部分回流下进行连续精馏操作。
要预先估计操作回流比大小和进料口位置,进料量控制在2~4L/h。
操作中要随时观察和记录塔釜压强、灵敏板温度等操作参数的变化以及塔釜液位变化情况,及时加以调节控制。
10.6数据处理和结果分析讨论部分的要求
(1)在全回流操作条件下测得X和X,利用乙醇和水二元相平衡数据,在WDy-x图上求得全塔理论板数N根据式①得出全塔效率。
T
水乙醇
全回流质量百摩尔分质量百摩尔分峰面积峰面积数分数分数数
0.05200.87710.12290.9480225321084
进样0.8468399140.93393707塔顶0.15320.0661
0.0000
39427
1.0000塔釜0
1.0000
以塔顶为例,具体的计算步骤如下:
乙醇的质量百分数
f′A0.8750×
39914ii===%C0.9339n∑f′A0.8750×
39914+0.6671×
3707乙醇iii=1水的质量百分数
%C=1?
%C=0.0661乙醇水乙醇的摩尔分数
0.9339n?
46乙醇==0.8468=χ0.9339n+n乙醇?
+0.1532/1846乙醇水水的摩尔分数χχ?
=10.1532=乙醇水.
利用理论塔板绘制软件,得到理论塔板数为11(含塔釜),所以全塔效率为
N?
111?
1T×
100%=η=×
100%=66.7%
N15
,≥93%χ和分离要求(χ2()在部分回流连续精馏操作时,根据进料组成DF和)估算D2~4L/h3%χ≤)。
初步估计操作回流比R的大小,根据进料流量(WW。
下,15.5mL/min采出量q==30mL/min,q,回流量4L/h2.1在进料量v,Dv,Lq30mL/minv,L=回流比R,同样计算方法的如下表格==1.9
15.5mL/minqv,D乙醇水回流比摩尔分摩尔分质量百质量百1.9峰面积峰面积分数数分数数
0.06530.15150.9347塔顶0.8485293742692
1.00001.00000.00000.0000
塔釜31851
100%η==×
15N.
WD+F={联立方程WxDx+Fx=WFD=0
,x,x=0.8485其中,F=4L/h,x=0.0520WDF解得:
L/hL/hD=0.2451W=3.7549
F=0.0613/塔顶采出率DF=0.9387/塔底采出率W
下,=11mL/min34mL/min=,采出量qq,回流量在进料量4L/h2.2v,Dv,Lq34mL/minv,L==3.1回流比R=,同样计算方法的如下表格
11mL/minqv,D
回流比3.1
水
乙醇
峰面积
质量百分数
摩尔分数
塔顶
5474
0.0836
0.1891
45725
0.9164
0.8109
塔釜
46788
利用理论塔板绘制软件,得到理论塔板数为8(含塔釜),所以全塔效率为
18?
=100%=×
100%=46.7%η
N15
F=0.0641
D/同理,D=0.2565,塔顶采出率
下,9mL/min采出量q==38mL/min,q4L/h,回流量在进料量2.3v,Dv,Lq38mL/minv,L=回流比R,同样计算方法的如下表格==4.2
9mL/minqv,D
回流比4.2
水
乙醇
峰面积
塔顶
4648
0.0694
0.1601
47516
0.9306
0.8399
塔釜
31848
利用理论塔板绘制软件,得到理论塔板数为10(含塔釜),所以全塔效率为
110?
1Tη=×
100%=×
100%=60.0%
F=0.0619
D/同理,D=0.2476,塔顶采出率
下,16mL/min采出量,q==30mL/minq在进料量4.4L/h,回流量2.4v,Dv,Lq30mL/minv,L=回流比R==1.9,同样计算方法的如下表格
16mL/minqv,D
回流比1.9
质量百分数
摩尔分数
5878
0.0930
0.2075
43731
0.9070
0.7925
15558
100%=η=46.7%
F=0.0656
,塔顶采出率D=0.2887同理,D/
下,5.5mL/min采出量,q==30mL/minq在进料量5.0L/h,回流量2.5v,Dv,Lq30mL/minv,L=回流比R==5.5,同样计算方法的如下表格
5.5mL/minqv,D
乙醇水摩尔分摩尔分质量百质量百峰面积峰面积
回流比5.5塔顶
4849
分数
0.0781
数0.1780
43621
分数0.9219
数0.8220
60228
利用理论塔板绘制软件,得到理论塔板数为9(含塔釜),所以全塔效率为
19?
100%=53.3%
同理,D=0.3163,塔顶采出率D/F=0.0633
,,进料量4.0L/h2.6在加大塔底再沸器热量,即采用较大的上升蒸汽速率qv,L=R=,30mL/min采出量q=13mL/min下,回流比=q回流量v,Dv,L
qv,D30mL/min,同样计算方法的如下表格=2.3
13mL/min
回流比2.3120.73422.3
4
6
0.0708
33.3
乙醇分数
峰面积44
质量百分数1.93.1
摩尔分数0.06130.0641
峰面积0.84850.8109
质量百分数66.746.7
塔顶3
67234
0.12414.2
0.26580.0619
361780.8399
0.875960
0.7342
塔釜45
602284.45
1.00001.95.5
1.00000.06560.0633
0.79250.822
0.000046.753.5
利用理论塔板绘制软件,得到理论塔板数为6(含塔釜),所以全塔效率为
16?
100%=η=33.3%
F=0.0708
,塔顶采出率D=0.2833同理,D/
总结上述六组部分回流的数据,列下表
塔顶乙塔板效部分回塔顶采醇摩尔进料量回流比率流出率
1)对于1,2,3组,在进料量一定的条件下,随着采出率的升高,塔顶采出的乙醇纯度和塔板效率均降低
2)分别对比1和4,3和5,加大进料量,升高塔顶采出率,塔顶采出的乙醇纯度和塔板效率均降低
3)对比1,6组,在加大塔底再沸器温度后,塔顶采出的乙醇纯度和塔板效率均降低很多,说明出现了雾沫夹带现象
(3)在实验报告中,要着重于实验过程操作现象的分析,详细讨论塔釜压力、塔顶温度、塔釜温度、灵敏板温度等操作参数的变化所反映的过程本质以及所采取的切实有效的调节控制措施。
3.1精馏塔操作过程的调节
操作条件的变化或外界的扰动,会引起精馏塔操作的不稳定。
在操作过程
中必须及时予以调节,否则将影响分离效果,使产品质量不合格。
(1)塔顶采出率D/F过大所引发的现象及调节方法
前已指出,当进料条件和分离要求已经确定后,在正常情况下,塔顶和塔底采出率的大小要受到全塔物料平衡的制约,不能随意规定。
在操作过程中,如果>
F?
W。
随着过程的进行,塔内轻组分将过大,则必塔顶采出率D/FDxxxWDF大量从塔顶馏出,塔内各板上的轻组分的浓度将逐渐降低,重组分则逐渐积累,浓度不断增大。
最终导致塔顶产品浓度不断降低,产品质量不合格。
由于采出率的变化所引起的现象可以根据塔内的温度分布来分析判断。
当操作压力—定时,塔内各板的气、液相组成与温度存在着对应关系。
若D/F过大,随着轻组分的大量流失,塔内各板上重组分的浓度逐渐增大,因而各板的温度也随之升高。
由于塔釜中物料绝大部分为重组分,因而塔釜温度没有塔顶温度升高得明显。
对于D/F过大所造成的不正常现象,在操作过程中应及时发现并采取有效的调节措施予以纠正。
通常的调节方法是:
保持塔釜加热负荷不变,增大进料量和<
W的条件下操作—D塔釜出料量,减小塔顶采出量,使得精馏塔在xxxWDF段时间,以迅速弥补塔内的轻组分量,使之尽快达到正常的浓度分布。
待塔顶温度迅速下降至正常值时,再将进料量和塔顶、塔底出料量调节至正常操作数值。
(2)塔底采出率W/F过大所引发的现象及调节方法
塔底采出率W/F过大所引发的现象和产生的后果恰与D/F过大的情况相反。
由于重组分大量从塔釜流出,塔内各板上的重组分浓度逐渐减小,轻组分逐渐积累,最终使得塔釜液体中轻组分的浓度逐渐升高。
如果精馏的目的产品是塔底液体,那么这种不正常现象的结果将导致产品不合格;
如果目的产品是塔顶馏出物,的过大,将有较多的产品从塔底流失。
W/F则由于
由于W/F过大使塔内的重组分大量流失,塔内各板的温度会随之降低,但塔顶温度变化较小,塔釜温度将有明显下降。
对于W/F过大的情况的调节方法是:
增大塔釜加热负荷,同时加大塔顶采
>
W的条件下操作。
同时,亦可视出量(回流量不变),使过程在DxxxWDF具体的情况适当减少进料量和塔釜采出量。
待釜温升至正常值时,再调节各有
=F?
W的正常情况下操作。
关参数,使过程在DxxxWDF
(3)进料条件变化所引发的现象及调节方法
在工业过程中,精馏塔的进料条件,包括进料量、进料组成、进料温度等,将会由于前段工序的影响而有所变化。
如果过程中存在循环物流,那么后段工序的操作变化也将影响精馏塔的稳定操作。
生产过程中进料量的变化可在流量指示仪表上直接反映出来。
如果进料量变化仅仅是由于外界条件的波动而引起的,适当调节进料控制阀门即可恢复正常操作。
如果是由于生产需要而改变进料量,则就要相应地改变塔顶、塔底的采
出量,并调整塔釜加热负荷(和塔顶冷凝负荷)。
如果由于操作上的疏忽,进料量已经发生变化,而操作条件未做相应的调
整,使得过程在全塔物料不平衡的情况下操作,其结果必然使塔顶或塔底产品不
合格。
此时应根据塔顶或塔底温度的变化,参照以上
(1)和
(2)的分析和处理方法,及时调节有关参数,使操作处于正常。
对于进料组成的变化,工业上—般采用离线分析的方法检测,因而不如进料量变化那样容易被及时发觉。
当在操作数据上有反映时,往往有所滞后,因此,如何能及时发觉并及时处理是工业过程中经常遇到的问题。
当进料中轻组分增加后,塔中各板上浓度和温度的变化同塔底采出率W/F过大的情况相似,而进料中重组分增加后塔内温度和浓度的变化情况则同塔顶采出率D/F过大的情况相似。
这时,除了要相应调整塔底或塔顶的采出率外,还要适当减少或增大回流比,并视具体情况,调整进料的位置,合理地分配精馏段与提馏段的塔板数。
进料温度的变化对精馏分离效果也有—定的影响,可通过调节塔釜加热负
荷和塔顶冷凝负荷使得操作正常。
(4)分离能力不够所引发的现象及调节方法
对于—座设计完善的精馏塔,所谓分离能力不够是指在操作中回流比过小
而导致产品的不合格。
其表现为塔顶温度升高,塔釜温度降低,塔顶和塔底产品
均不符合要求。
采取的措施通常是通过加大回流比来调节。
但应注意,在进料量和进料组成—定时,若规定了塔顶、塔底产品的组成,则塔顶和塔底产品的流量亦被确定。
因此,增大回流比并不意味着塔顶产品流量的减少,加大回流比的措施只能是增加塔内的上升蒸汽量,即增大塔釜的加热负荷及塔顶的冷凝量,这是要以操作成本的增加为代价的。
此外,随着回流比的增大,若塔内上升蒸汽量超过塔内气体的正常负荷,容易发生严重的雾沫夹带或其他不正常的现象。
因此,操作中不能盲目增加回流比。
3.2精馏塔内的温度分布与温度灵敏板
在以上的操作分析中已经看到,当操作压力—定时,塔顶、塔底产品组成和塔内各板上的气液相组成与板上温度存在—定的对应关系。
操作过程中塔顶、塔底产品的组成变化情况可通过相应的温度反映出来。
通常情况下,精馏塔内各板的温度并不是线性分布,而是呈“S”型分布。
在塔内某些塔板之间,板上温度差别较大,当因操作不当或分离能力不够导致塔板上组成发生变化时,这些板上的温度将发生明显改变。
因此,工程上把这些塔板称为温度灵敏板。
在操作过程中,通过灵敏板温度的早期变化,可以预测塔顶和塔底产品组成的变化趋势,从而可以及早采取有效的调节措施,纠正不正常的操作,保证产品质量。
如图10-1所示,由于回流比过小,因而分离能力不够所造成的温度分布变化情况与因塔顶采出率不当所引起的温度分布情况有明显不同。
可以看出,两种不同的操作均导致灵敏板温度上升,但后者是突跃式的,灵敏板温度变化非常明显而前者则是缓慢式的。
据此,可以判别操作中产品不合格的原因,并采取相应的调节措施