冶金 毕业论文Word格式文档下载.docx
《冶金 毕业论文Word格式文档下载.docx》由会员分享,可在线阅读,更多相关《冶金 毕业论文Word格式文档下载.docx(15页珍藏版)》请在冰豆网上搜索。
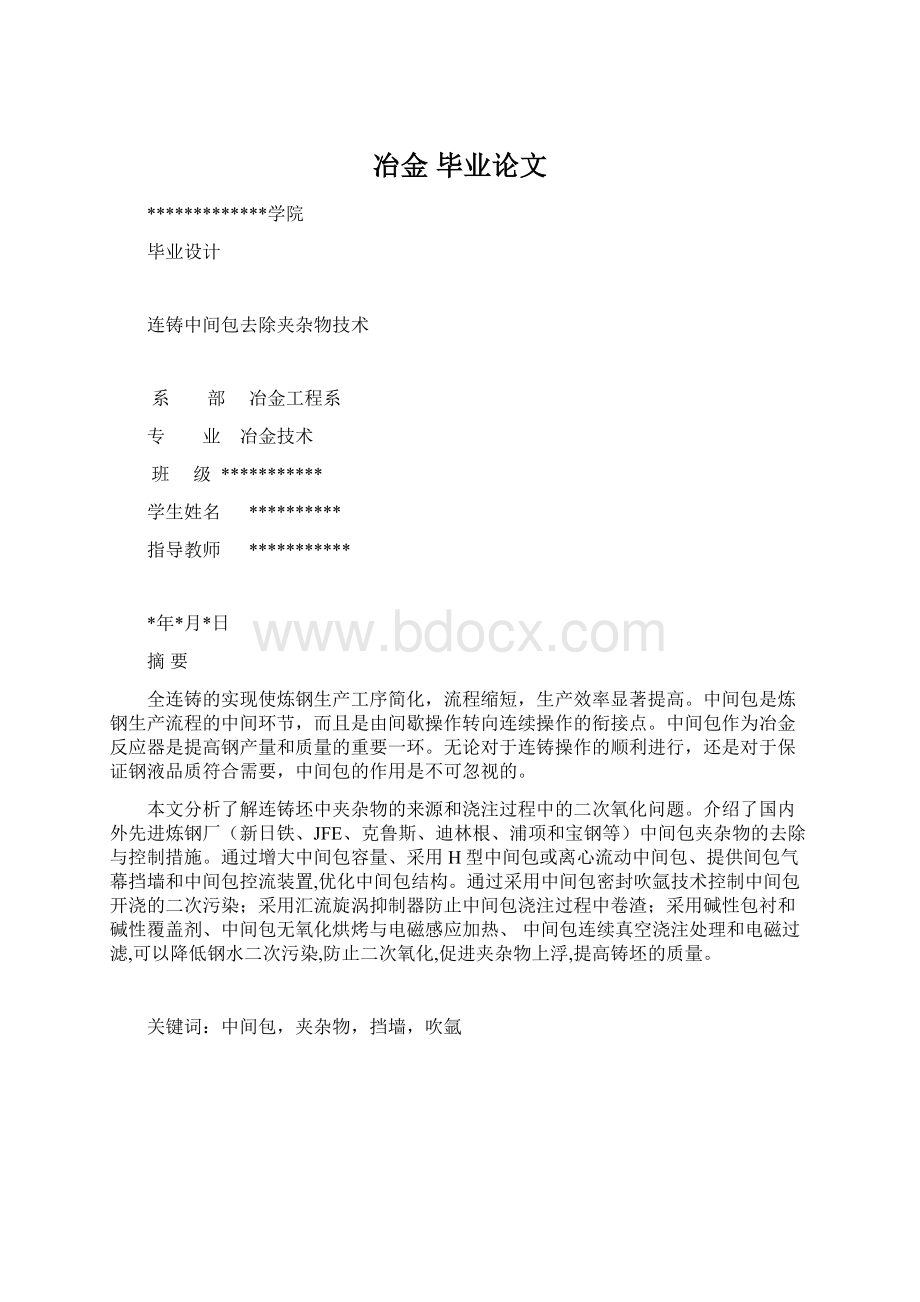
通常认为中间包起以下作用:
(1)分流作用。
对于多流连铸机,由多水口中间包对钢液进行分流。
(2)连浇作用。
在多炉连浇时,中间包存储的钢液在换盛钢桶时起到衔接的作用。
(3)减压作用。
盛钢桶内液面高度有5-6m,冲击力很大,在浇铸过程中变化幅度也很大。
中间包液面高度比盛钢桶低,变化幅度也小得多,因此可用来稳定钢液浇铸过程,减小钢流对结晶器凝固坯壳的冲刷。
(4)保护作用。
通过中间包液面的覆盖剂,长水口以及其他保护装置,减少中间包中的钢液受外界的污染。
(5)清楚杂质作用。
中间包作为钢液凝固之前所经过的最后一个耐火材料容器,对钢的质量有着重要的影响,应该尽可能使钢中非金属夹杂物的颗粒在处于液体状态时排除掉。
中间包冶金研究应该发挥的作用有:
(1)改善钢液流动条件,最大可能去除钢中非金属夹杂物;
亦即防止短路流,减少死区,改进流线方向,增加钢液的停留时间。
(2)控制好钢液温度,必要时增加加热措施,时钢液过热度保持稳定。
(3)选择合适的包衬耐火材料和熔池覆盖剂,既减轻热损失又有利于吸收分离和上浮的夹杂物。
计算流体力学对各种流场的研究是非常有效的方法。
中间包冶金的特点是在钢液流动中进行各种冶金过程,所以可以用计算流体力学方法求解中间包流场。
由于中间包结构复杂,除早期曾用二维流场计算求解外,基本上都用三维流场计算。
贺友多较早开展了三维流场计算的研究工作,并利用其计算程序计算了多种中间包内钢液流动特征及影响因素。
萧泽强等运用了他们对盛钢桶内吹氩钢液流动的长期研究的成就,也计算了多种中间包内的流场,并较早注意到非等温状态中间包流场的研究,指出了自然对流的影响不可忽视,并用水模型进行了实验验证。
计算流体力学方法现已成为中间包冶金分析的主要手段,随着计算机硬件和软件的迅速进步,计算流体力学将会在冶金科学技术中得到更广泛的应用。
1中间包概述
1.1中间包
中间包是连铸工艺流程中,位于钢包
与结晶器之间的过度容器,即钢包中的钢
水先注入中间包再通过其水口装置注入结
晶器。
中间包车是中间包的支撑、运载工
具。
(如图1.1所示)
图1.1中间包立体结构示意图
1.2中间包的作用
中间包的作用是稳定钢流,减少钢流对结晶器中初生坯壳的冲刷;
能储存钢水,并保证钢水温度均匀;
是非金属夹杂物和钢液分离、上浮;
在多流连铸机上,中间包把钢水分配给各支结晶器,起到分流的作用;
在多炉连浇过程中,中间包内储存的钢水在更换钢包时能起衔接作用,从而保证了多炉连浇的正常进行。
随着对铸坯质量要求的进一步提高,中间包也可作为一个连续的冶金反应容器。
可见中间包有减压、稳流、去渣、贮钢、分流和中间包冶金等重要作用。
1.3中间包的发展
随着中间包冶金技术的发展与完善,中间包不仅是把钢水均匀分配给各个结晶器和实现多炉连浇的中间容器,而且承担着去除夹杂物、合金微调、控制过热等冶金功能。
中间包控流元件的设置对包内非金属夹杂物的上浮及均匀钢水温度起着至关重要的作用。
多流中间包各流出口温度及所含夹杂物的大小和数量有很大的差异,给操作和铸坯质量控制带来困难。
因此,寻找合理的中间包控流元件的设置参数,对多流连铸中间包来说具有特别重要的意义。
将原中间包结构改进为本研究的最优方案Y10,对改进前后的铸坯1流(来自l水口)和2流(来自2水口)分别取样进行总氧、显微夹杂物和大型夹杂物的检验,钢种为30CrMo,改进前后各取2炉,改进前1流和2流的总氧相差2×
106,改进后两流总氧相同,平均总氧比改进前下降了9.09%,显微夹杂物和大型夹杂物分别下降了10.75%和11.99%,且两流的差距也在减小。
说明改进后的方案更有利于钢水成分和温度的均匀,有利于提高铸坯洁净度和表面质量。
2中间包结构及功能
2.1中间包的构造
2.1.1中间包的类型
中间包的形状应具有最小的散热面积,良好的保温性能。
一般常用的类型按其断面形状可以分为圆形、椭圆形、三角形、矩形和“T”字形等(如图2.1)
图2.1中间包断面的各种形状示意图
a、e—单流;
b、f、g—双流;
c—4流;
d—6流;
h—8流
1—钢包注流位置;
2—中间包;
3—挡渣墙
中间包的形状力求简单、以便于吊装、存放、砌筑、清洁等操作。
按其水口流数可分单流、多流等,中间包的水口流数一般为1-4流。
2.1.2中间包的结构
中间包的立体结构如图所示。
它的外壳用钢板焊成,内衬砌筑有耐火材料,包的两侧有吊钩和耳轴,便于吊运;
耳轴下面还有坐垫,以稳定地坐在中间包车上(图2.2)
图2.2中间包立体结构图
中间包的结构主要由本体、包盖及水口控制机构(滑动水口机构、塞棒机构)等装置组成,如图2.3(A、B)所示。
图2.3A矩形中间包简图图2.3B三角形中间包简图
1—溢流槽;
2—吊耳;
3—中间包盖;
1—中间包盖;
2—耐火衬
4—耐火衬;
5—壳体3—壳体;
4—水口;
5—吊环
6—水口控制机构(塞棒机构)
(1)中间包本体。
中间包本体是存放钢水的容器,它主要由中间包壳体和耐火衬等零部件组成:
中间包外壳用钢板焊成的箱型结构件、中间包耐火材料由工作层、永久层和绝热层等组成。
(2)中间包盖。
中间包盖得作用是保温、防止中间包内的钢水飞溅,减少邻近设备受到罐内钢水高温辐射、烘烤的影响。
中间包盖是用钢板焊接而成,其内衬砌筑耐火材料;
或用耐热铸铁铸造而成。
在中间包盖上设置钢水注入孔、塞棒孔、中间包烘烤孔、测温孔及吊装用的吊环。
2.2中间包的功能
随着对钢的质量要求日益提高,开发了各种钢包精炼技术,其目的就是提高纯净度,把钢水净化“干净”些。
而中间包是连铸钢包与结晶器间的一个耐火材料容器。
经过炉外精炼的钢水可以说是“干净”了,但浇到中间包又可能再污染。
因此,不应把中间包看作是简单的钢水过渡容器,而应把它看成为一个连续的冶金反应器,钢包精炼中采用的措施可以移植到中间包,以进一步净化钢液。
为此提出了中间包冶金的概念,受到了人们的重视。
中间包冶金的功能是:
(1)净化功能。
为生产高纯净度的钢,在中间包采用挡墙加坝、吹氩、陶瓷过滤器等措施,可大幅度降低钢中非金属夹杂物含量,且在生产上已取得了明显的效果。
(2)调温功能。
为使浇注过程中中间包前、中、后期钢水温差小于5℃,接近液相线温度浇注,扩大铸坯等轴晶区,减少中心偏析,可采取向中间包加小块废钢、喷吹铁粉等措施以调节钢水温度。
(3)成分微调。
由中间包塞杆中心孔向结晶器喂入铝、钛、硼等包芯线,实现钢中微合金成分的微调,既提高了易氧化元素的收得率,又可避免水口堵塞。
(4)精炼功能。
在中间包钢水表面加入双层渣吸收钢中上浮的夹杂物,或者在中间包喂钙线改变Al2O3夹杂形态,防止水口堵塞。
(5)加热功能。
在中间包采用感应加热和等离子加热等措施,准确控制钢水浇注温度在±
3~±
5℃
3中间包去除夹杂物技术
3.1连铸坯夹杂物的来源分布
对于连铸坯夹杂物来源可分为内生的和外来的。
(1)内生夹杂物主要是脱氧元素与溶解在钢液中〔O〕的反应产物或者是钢水冷却凝固过程中的析出物。
内生夹杂一般又称显微夹杂。
它的特点是颗粒直径小(<20μm),数量多,主要是影响钢的抗疲劳性和韧性。
(2)外来夹杂物是从炼钢到浇注的全过程中,钢液与空气、耐火材料、炉渣相互作用的产物。
从广义上说,统称为二次氧化物。
钢的机械性能很大程度上取决于能产生应力集中的夹杂物和沉淀析出物的体积、尺寸、分布、化学成分以及形态。
夹杂物尺寸分布尤其重要,因为大型夹杂物对机械性能危害最大。
3.1.1外来夹杂物的形成机理
外来夹杂物主要是钢水生产过程中因外部因素产生或带入的化学和机械作用产物。
连铸坯中夹杂物的数量与钢水成分、耐火材料质量、中间包结构、钢水浇注方式、保护浇注和炉渣成分等因素有关。
外来夹杂的形成特点是:
(1)组成复杂,一般是多种氧化物组成的复合相。
(2)颗粒尺寸大,夹杂物颗粒一般大于50μm,如Al2O3簇状夹杂的当量直径达到400μm,含Ca、Al、Si、Mn的氧化物直径达200μm。
(3)形状不规则,有球形、多角形等。
(4)在钢中呈偶然性分布。
与小夹杂物均匀弥散分布不同,外来夹杂物在钢中零星分布,经常出现在表层附近。
(5)平衡氧差异,二次氧化是钢中溶解元素与空气中O2之间的平衡,空气中O2可源源不断供给钢液进行氧化反应生成二次氧化产物。
外来夹杂物总是与实际操作相关,通常可以根据它们的尺寸和化学成分判断出它们的来源,而且它们的来源主要就是二次氧化、卷渣、包衬侵蚀和化学反应。
3.2连铸中间包夹杂物控制及去除技术
3.2.1保护浇注技术
经炉外精炼的钢水可以说是很“干净”了(钢水中T[O]可达(20-30)ppm),在浇注过程中钢水与空气作用发生二次氧化,则钢水水再污染,炉外精炼的效果将前功尽弃。
试验指出,从钢水到中间包由于钢水与空气二次氧化造成[Al]损失占60%以上,是铸坯中夹杂物主要来源之一。
因此浇注过程中钢水密封是生产纯净钢的重要操作之一。
钢水中总氧量T[O]的增加是钢水二次氧化程度的量度。
(见图3.1)
图3.1钢包内氧的变化
从钢水—中间包—结晶器钢水中[N]含量增加,也可作为钢水二次氧化的指示剂,常用的保护方法有:
(1)中间包密封:
第一炉开浇中间包内充满空气,生成大量的A10。
为此把中间包盖与本体用纤维密封,中间包内充满Ar气(02<
1%,N2<
5%)。
使钢液吸氮减少5个ppm,T[O]减少10~15ppm,[A1]s损失减少了70ppm。
(2)钢包—中间注流长水口+吹氩保护:
关键是长水口与钢包下水口接头密封,使钢水吸氮量<
1.5ppm甚至为零。
有的厂家规定钢包—中间包钢水氮增量大于10ppm,钢水达不到洁净度的要求,不能用做重要订货。
因此钢水应处于密封状态浇注。
(3)中间包—结晶器浸入式水口保护浇注,为防止注流二次氧化,在中间包到结晶器间采用浸入式水口与中间包连接处密封,采用氩密封,钢水吸氮为2.5ppm,采用悬锤式浸入式水口结缝无密封,钢水吸氮平均14.3ppm。
国内不少工厂采用这种形式,二次氧化相当严重,应加以改进。
(4)对小方坯中间包——结晶器采用氩气保护浇注,气氛中O2<
1%,对结晶器弯月面区能有效保护,夹杂明显减少。
3.2.2包渣检测、卷渣控制技术
钢包内钢液液位降低,会发生涡流,使钢液表面的渣卷入进去,造成夹杂物增加。
为了抑制钢渣卷入,通过降低钢液的流出速度来防止涡流的发生。
但是,连浇操作时,从减少中心偏析、改善表面质量等考虑,要进行恒温浇注,很难做到为防止钢渣流出而长时间降低供钢速度。
因而,以往当采用氩封法的场合,部分破开密封,人工判渣。
现在开始用于实际生产的一种方法,是利用钢渣和钢液的透磁率的不同的电磁检测法。
它与采用氩封的人工判渣相比,流渣量几乎相同。
但是,对防止空气氧化和防止大量出渣,它能起到良好的效果,采用长水口时,有报告认为与人工判渣相比能大幅度降低渣的流出量。
众所周知,前炉钢浇注结束时,流出的渣是在中间包内的钢液上部,后炉钢水浇注时与其发生搅拌,引起夹杂物的大量增加。
用耐材做成的浇铸管,管内吹氩以及利用长水口,将卷渣控制在最低限度。
但是,光这些措施是不够的,通过延长钢液在中间包内的停留时间,促使夹杂物上浮、去除也可减少这些弊病的发生。
3.2.3中间包吹氩去夹杂技术
通过吹氩来净化钢液的效果是公认的事实。
这种方法在钢包精炼中得到充分的运用。
根据相同的原理,可在连铸中间包内通过吹氩促进夹杂物的去除。
将惰性氩气体吹入中间包,使其产生小气泡幕。
气泡幕将夹杂物从钢液带到表面被表面渣吸附去除。
其机理是:
气泡与夹杂物碰撞吸附到一起,粒径增大,上浮速度增大,易于被钢液表面的渣层吸收。
由于底吹透气砖搅拌气泡合体成长引起中间包液面剧烈波动,同时使气泡吸附夹杂物的效率降低,所以已开发采用了埋入透气砖的回转喷枪,使微细气泡扩散,帮助捕捉,去除夹杂物,尤其是对50以上的夹杂物去除效果更佳,而且有效地防止AlO粘附中间包水口。
但吹气量不宜过大,否则会导致结瘤.使钢水搅动加剧,从而使夹杂物上浮到表面后,由于惯性力作用,使之难以在钢液上停留而返回到钢水内,对去除夹杂物不利,甚至出现相反效果。
中岛等人所做的吹氩搅拌法,该方法的特征是砖中埋设200m的细管,吹入最佳氩量,促进夹杂物的上浮。
若吹氩量过大,会使钢液流动过快,反过来会使已经浮上来的夹杂物又卷入钢中,造成钢液的恶化。
也有通过旋转水口生成微细气泡,除去夹杂物的方法。
它特别对去除小于50m的夹杂物效果显著。
有报道说,这样做可使这类夹杂物的缺陷发生量减少一半。
已证明该法用于实践时,将有效地减少浸入式水口内粘附的A1203量。
中间包吹入惰性气体不是为了增强搅拌,而是用惰性的气泡清洗钢液。
最初在中间包吹惰性气体着眼于脱氢。
试验证明吹入惰性气体(标态)50~80L/min可清除开浇阶段的增氢现象。
但是中间包吹惰性气体最明显的效果是去除夹杂物。
中间包吹入惰性气体的方式主要是在中间包底部某个部位通过多孔砖或多孔气管吹入微小气泡。
在中间包底部吹其有如下三个作用:
(1)排列成列的吹气孔口垂直于沿包底流动的液流布置,类似于在包底设置了坝,促使钢液转向上方流动,其作用比坝还强烈;
(2)气泡的浮力产生气泡泵现象,促使该局部的湍流动能耗散率显著增大,有利于夹杂物颗粒的碰撞长大去除;
(3)上浮的气泡可以捕获夹杂物颗粒,并携带它一起上浮,这样就使微细的夹杂物颗粒上浮速度增大到气泡上浮速度。
法国研制了一套包底吹惰性气体生产纯净钢的工艺。
吹气装置埋在加入合成纤堆的耐火材料浇包和整体包衬内,吹气管组成网络,管上有2mm的小孔.吹气时从孔隙均匀吹出细小气泡.在中间包中形成一堵“墙”。
加强了钢液向液面的循环运动和夹杂物的垂直运动。
形成气泡与夹杂物碰撞并吸收夹杂物。
促进夹杂物的上浮排除此工艺去除夹杂物净化钢液效果明显。
对大于200m的大型夹杂去除效率为98%,对100-200的中型夹杂去除效率为93%,对小于l00的夹杂物去除效率为47%。
3.2.4间包容量大型化
中间包容量大型化一方面有利于高速连铸;
另一方面能保证钢液在中间包内停留更长时间,以利夹杂充分上浮、净化钢质、避免中间包渣卷入结晶器。
中间包大型化后,钢坯表面无缺陷率由57%增至92%。
采用大容量中间包是为了提高连浇时钢的清洁度,使换包时保持稳定状态,不卷渣又不必降低拉速,这在生产表面质量和内部质量要求高的产品如深冲产品和汽车板时尤为重要。
为了不使钢包涡流卷渣发生,保证中间包操作最小深度是必要的。
研究认为,板坯连铸中间包的最小深度是16~20英寸(406~508mm),即容量大约为20t才行。
若95%的换包时间在5min以下,当注速为5t/min时,则有25t钢水贮留以满足中间包钢液最小深度的要求。
Saeki等人的研究指出,当中间包容量从40t增大到65t,则换钢包期间无缺陷的铸坯比例可从75%提高到92%。
S.Hintikka等人用数学模型计算了中间包容量对钢中夹杂物去除的影响。
增大中间包容量使钢液在中间包内有较长的停留时间,从而有利于夹杂物的充分上浮。
RAHerad等人对水平连铸机上的大容量中间包内的钢液流动形态进行了模拟,并得出了最佳控流装置。
Mazumdar等人研究表明,增加中间包深度,降低了旋涡的产生,改善了铸坯超声波探伤缺陷。
SHiraki等人研究认为:
采用大容量中间包提高了高速连铸薄板坯(厚为90~100mm)的纯净度,同时进行低液位操作促进了夹杂物的上浮.英国钢铁公司Ravenscraig厂的中间包由25t扩大到45t后,氧化铝夹杂不仅数量减少,而且在铸坯内弧侧聚集的现象明显改善。
张立峰等人研究指出,在控流装置相同的条件下,60t的中间包比10t的中间包T[O]多去除42.4%,大颗粒夹杂物多去除25.9%,微观夹杂物多去除11.8%。
吴永生等人对扩容中间包的冶金效果进行了研究,得到如下结论。
在相同的挡墙条件下,中间包加高能延长钢液停留时间约30%,有利于钢中夹杂物的上浮分离。
3.2.5挡墙、和坝、过滤器(多孔挡板)
70年代开始出现了中间包安装挡墙和坝的方法,80年代又出现了安装过滤器的方法。
目的是控制中间包中流场形态,使流动合理,液面保持平稳,尽量减轻湍流的干扰,减少死区,增大钢水平均停留时间,有利于夹杂物去除,提高钢水清洁度。
(见图3.2a、b)
图3.2(a)中间包内钢液无控制流动示意图
图3.2(b)中间包砌有挡墙后钢液的流动
中间包内加设挡墙、坝装置,进一步延长了钢水到达水口时间,可有效地促进夹杂物上浮分离以及均匀成分和温度。
合理的墙、坝组合以及二挡墙/双坝组合可促进钢水流载的最佳化,使活塞流(层状流)区扩大,混合流区减小。
死区大幅减小,为稳定连铸获得优质的纯净钢创造了条件。
中间包内设置挡墙、坝、堰是中间包冶金发展成熟,应用最普遍的技术措施。
通过在中间包内设置挡墙,坝等,总趋势是可以增加钢液在中间包的平均停留时间,促进夹杂上浮,导致合理的温度场分布。
关于中间包的水模、数模研究主要内容是主要挡墙、坝的研究。
包燕平认为在中间包设置挡墙等,能显著改善夹杂物上浮条件,而挡墙的位置、大小和数量对结果影响很大。
对于双挡墙结构,其去除夹杂物的能力基本上随挡墙数量的增加而增加,而所选择的坝-墙-坎效果最佳。
上下堰的组合可以使平均停留时间最长。
但中间包容量相对浇铸速度足够大时,包内无任何物理流动控制元件,其平均停留时间也并不十分短。
数学模拟结果表明:
浇铸速度大于2.5t/min时,大于150m的夹杂对所有包内结构,都能完全上浮。
而中间包内采用上下堰对直径50~100m的夹杂上浮最有利。
矩型包内上下堰组合仅是个别因素和选择的配合,Q.L.He重点强调了入口注流条件的重要性,即注流保护,钢包到中间包高度及滑板的使用。
李润生提出在下挡墙上游增加上挡墙,可以使钢液返到表面,结果减轻渣子的卷入,延长平均停留时间。
挡墙和吹气结果使包内液体接近均匀混合状态,消除了旁路击穿流,使包中有效容积增大、停留时间增加、夹杂物上浮率增加。
Sarbjit.singh认为坝+堰可以增加平均停留时间,相对死区减少。
中间包内设置墙、坝、堰的系统研究基本反映了墙坝的优点。
但是在中间包内部结构对平均停留时间以及非正常工作液位下的平均停留时间研究中,得到了一些相触、甚至相反的结论。
陈惠青认为在非正常工作液位下中间包内设置坝、堰等甚至增加了活塞流,降低了全混流。
S.D.Melville设置下研究得出:
坝、堰、墙的设置不可能明显提高平均停留时间,虽然两坝、两墙的设置有一定改进。
P.rasmussen针对某一中间包得出,使用无流动控制装置与使用挡墙和坝相比,钢中T[O]减少了25%,使用过滤器后钢中T[O]减少了33%-58%。
S.chakraborty等人研究了挡墙和坝及过滤器对去除钢中AlO能力的影响。
中间包使用挡墙和坝、过滤器之后,击穿流减少,钢水向上流动趋势增强,钢水在中间包中的平均停留时间延长。
E.S.Maria等人针对某一中间包研究表明,无流动控制措施时,中间包内死区占18%,使用坝是14%,使用挡墙和坝时为12%。
浦项使用中间包挡墙和坝,并将坝改为高铝质多孔过滤器,使钢中大颗粒夹杂减少了50%以上。
M.Byrne等人详细研究了60t中间包挡墙和坝结构,发现入水口到出水口使用一套挡墙和坝时,活塞流体积为10%,全混流体积为82%,死区为8%;
使用两套挡墙和坝时,活塞流体积为20%~28%,全混流体积为66%~77%,死区为3%~6%。
总之,有关中间包内设置附件的研究结果普遍认为坝、墙、堰的组合可以提高平均停留时间、促进夹杂上浮。
3.2.6中间包湍流控制技术
对中间包中钢液流场分析可知,盛钢桶注流对中间包内钢液有强烈的冲击作用,形成注流冲击区,在该区域由于注流的冲击,导致了部分中间包覆盖剂被卷入钢液中而形成夹杂。
同时,容易卷入空气发生二次氧化,冲击包底造成包底该处耐火材料过分侵蚀,再有,对中间包出口处形成汇流漩涡也有影响。
因此,有必要研究消除其涡流的措施。
在盛钢桶注流冲击点放置湍流抑制器,可缓解注流的冲击。
缓冲区结构简单,安装方便,容易在中间包上应用。
应用缓冲器可以改善中间包钢液的流动,起到以下作用:
(1)减弱盛钢桶钢流的冲击作用,减少卷渣、卷入气体;
(2)增大滞止时间,减少中间包死区比例;
(3)减少注流对中间包耐火材料的冲刷、侵蚀;
(4)减缓汇流漩涡的生成,取得控制钢液流动的效果。
3.2.7中间包覆盖剂去夹杂技术
中间包是去除钢水夹杂物的理想场所。
钢水面上的覆盖剂能有效地吸收上浮
夹杂物。
常用覆盖剂有:
(1)碳化稻壳:
绝热性能好,但钢、渣界面不能形成液渣层。
(2)中性渣:
一般Ca0/Si02=0.9~1.0,钢水面上形成液态渣,有强的吸收A12O3能力,但渣子不保温。
(3)碱性渣:
(CaO十MgO)/SiO23,渣子吸收A12O3能力强,但碱度太高,渣子易结壳。
(4)双层渣:
钢水面上形成液渣吸收夹杂物,再加碳化稻壳保温。
随着覆盖渣中SiO2含量的增加,钢水中T[O]是增加的。
生产洁净钢,中间包应用碱性覆盖剂为宜。
3.2.8碱性包衬去夹杂技术
要转移钢水中夹杂物,钢水与环境(包衬)的热力学性质必须是稳定的,这是生产纯净钢的一个重要条件。
为此生产纯净钢要选用碱性包衬。
中间