普通铣床的数控化改造设计Word下载.docx
《普通铣床的数控化改造设计Word下载.docx》由会员分享,可在线阅读,更多相关《普通铣床的数控化改造设计Word下载.docx(22页珍藏版)》请在冰豆网上搜索。
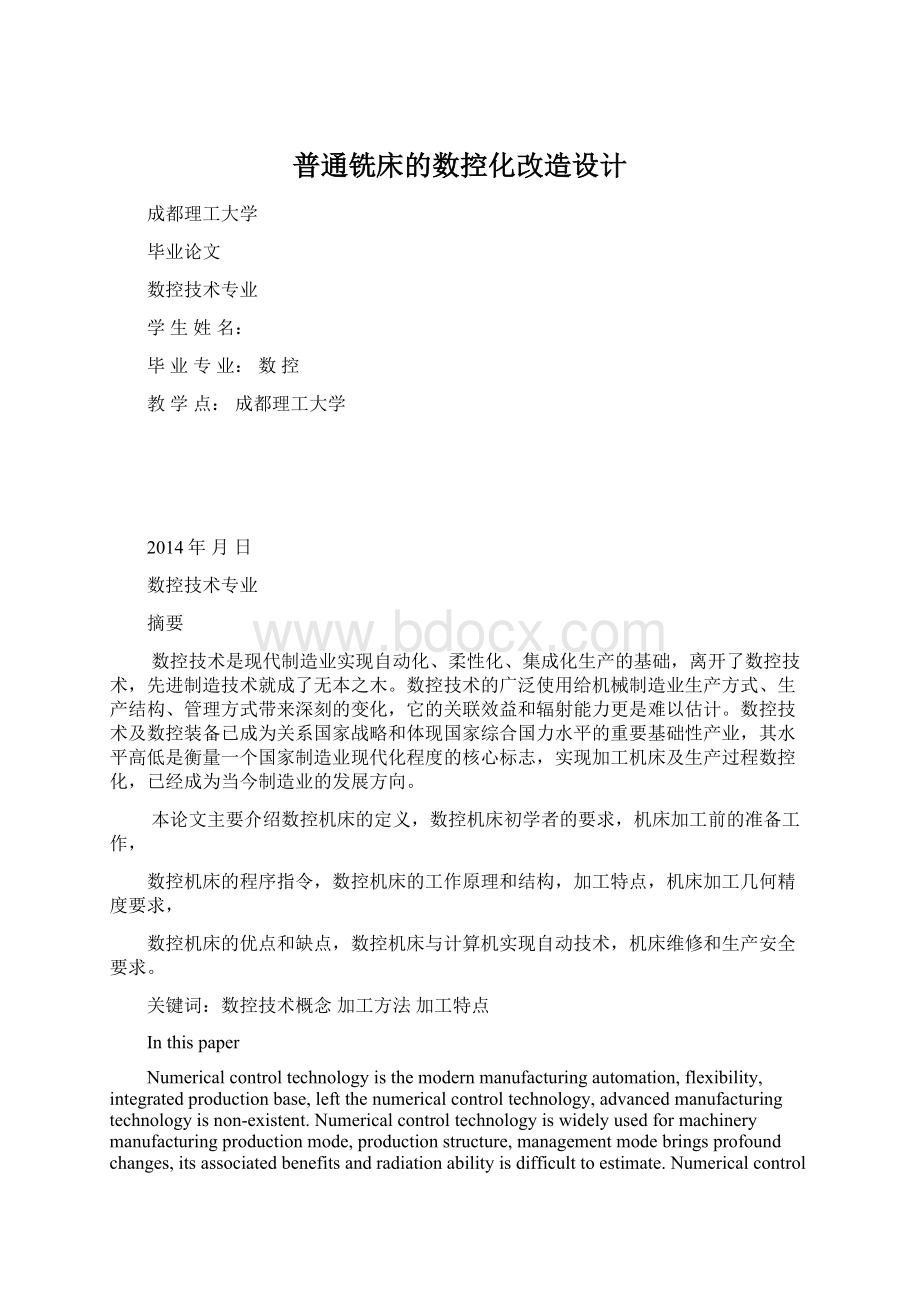
制造业是我国国民经济的支柱产业,其增加值约占我国国内生产总值的40%以上,而先进的制造技术是振兴制造业系统工程的重要组成部分。
21世纪是科学技术突飞猛进、不断取得新突破的世纪,它是数控技术全面发展的时代。
数控机床代表一个民族制造工业现代化的水平,随着现代化科学技术的迅速发展,制造技术和自动化水平的高低已成为衡量一个国家或地区经济发展水平的重要标志。
数控车床是目前使用最广泛的数控机床之一。
数控车床主要用于加工轴类、盘类等回转体零件。
通过数控加工程序的运行,可自动完成内外圆柱面、圆锥面、成形表面、螺纹和端面等工序的切削加工,并能进行车槽、钻孔、扩孔、铰孔等工作。
车削中心可在一次装夹中完成更多的加工工序,提高加工精度和生产效率,特别适合于复杂形状回转类零件的加工。
本文主要讨论的就是作为制造业的组成部分数控车床。
主要内容有关于数控车床的编程方法、编程的注意事项、加工工艺分析、刀具的选用、刀位轨迹计算。
下面就是本文的主题,关于数控车床的编程与实例。
1.1数控铣床的王要特点
(1)高柔性及工序复台化
数控铣床具有柔性(可变性)高和工序复台化的特点。
所谓“柔性”即灵活、通用
和万能性,可以适应加工不同形状工件的自动化机床。
数控铣床的发展已经模糊了粗、
精加工工序的概念,打破了传动的工序界限和分开加工的工艺规程,可最大限度地提高
设备利用率。
数控铣床般都能完成钻孔、镗孔、铰孔、铣平面、铣谢冕、铣槽、铣曲绵(凸轮)、
攻螺纹等加工。
而且,一般情况下,可以再次装夹中,完成所需的加工工序。
(2)加工精度高
目前数控装置的脉冲当量(即每发出个脉冲后精板的移动量)般为0.001m。
高精度的数控系统可达0.0001一般情况下,可以保证工件的加工精度。
另外,数控
加工可避免公认的操作误差,批加工件的尺寸同性特别好(包括工件的王要尺寸和
倒角等尺寸的同性),而且还可利用软件进行精度校正和补偿,大大提高了产品质量。
自于数控铣床的高精度和灵活性,能加工很多普通机床难以完成或根本不能加工的
复杂型面(如高精度螺旋推进器)。
因此,数控铣床首先在航空、航天工业中应用。
而加工各种复杂模具更显示优越性。
(3)生产效率高
零件加工所需要的时间包括机动实践与辅助时间两部分。
数控能自;
有效地碱少这两
部分时间。
因而加工生产率比般铣床高得多。
良好的结构性允许数控进行大切削用量的强力切削,有效地节省了机动时间。
数控铣床动部件的快速移动和定位采用了加速与碱速措施,因而选用了很高的空行程运动速度,消耗在快进、快退和定位的时间要比一
般铣床少得多。
数控铣床般很少使用专用夫具和工艺装备,在更换工件时,只需调用储存于计算
机中的加工程序,装夹工件和调整刀具数据,可大大缩短生产周期。
更王要的是数控铣
床的万用性带来的高效率,如一般的数控铣床都具有铣床、镗床和钻床的功能。
使工序
高度集中,可大大提高了生产效率并碱少了工件的装夹误差。
另外,数控铣床得主轴转速和进给量都是无级变速的。
因此,有利于选择最佳切削
用量。
数控铣床都有快进、快退、快速定位功能,可大大碱少机动时间。
据统计,采用数控铣床比普通铣床可提高生产率3~5倍。
对于复杂的成型棉加工可提高十几倍,甚至几十倍。
(4)碱轻操作者的劳动强度
数控铣床对零件加工是按事先编好的程序自动完成的。
操作者障了操作键盘、装卸
工件和中间测量及观察机床运行外,不需要进行繁重的重复性操作,可大大碱轻劳动强
度。
自于数控铣床具有以上独特的优点,因此数控铣床已成为机械制造业的王要装备。
但是,数控铣床的编程操作比较复杂,对编程人员的素质要求较高。
否则,很难发
挥数控铣床的作用。
另外,数控铣床的价格昂贵,如编程操作不恒,万发生碰撞,其后果不勘设想。
为此,必须重视编程操作人员的培训。
1.2数控铣床的组成
数控铣床于般的数控机床样,是自控制介质、数控装置、伺服系统和机床本体组成。
下图实线所示为开环控制的数控铣床框图。
椭圆零件的设计宏程序编程
宏指令编程是指像高级语言一样,可以使用变竿进行箅术运算、罡辑运算和函数混合运算的程序编写形式。
在宏程序形式中一般都提供循环判断分支和子程序训用的方法,可用于编制各种复杂的零件加工程序熟鲸应用宏程序指令进行编程,可大大精简程序量,在一定意义上说还可以增强机床的加工适应能力。
2.1宏程序的分类
宏程序可分为两类.A类和B类,A类Fanuc0TD老式的数控车床窟程序需要使用“G65Hm”格式的宏指令来表达各种数学运算逻辑关系,极不直观且可读陛非常差B类FancuOi先进的数控车床宏程序具有逻辑性强、程序简单、修改方便等特点,在实际生产中也得到了广泛的应用
2.2变量
一个普通的零件加工程序指定G码并直接用数字值表示移动的距离,例:
G100X100.O。
而利用用尸宏,既可以直接使用数字值也可以使用变竿号当使用变量号时变量值既可以由程序改变也可以用MDI面板改变。
2.21变量的书写规格
当指定一个变量时,在#后指定变量号。
个人计算机允许赋名给变量,宏程序没有此功能。
例:
#1也可以用表达式指定变量号这是表达式要用方括号括起来。
#[#1+#2-12]
2.2.2忽略小数点
在程序中定义变量时,可以忽略小数点倒-当#1=123被定义时变量#1的实际值123.000。
未定义的变量:
当变量的值未定义时,这样的个变量被看作“空’变量变量#0总是“空”变量是一个只读变量。
图形一
图形二
2.3零件图样工艺分析
该零件图由外圆柱面、槽、内外螺纹、外圆锥面、圆弧、内外椭圆等表面组成其中多个直径尺寸与轴向尺寸有较高的尺寸精度和表面粗糙度要求零件图尺寸标注完整符台数控加工尺寸标注要求:
轮廓描述清楚完整零件材料为45钢,切削性能较好无热处理和硬度要求图1毛坯为Φ45×
82、图2毛坯为Φ45x50
通过上述分析,制定工艺时采取以下几点措施:
(1)零件图上带公差的尺寸,因公差值较小故编程时不必职其平均值而取基本尺寸即可。
(2)加工图2时左右端面均为尺寸的设计基准,相应工序加工前应该先将左右端面车出来。
2.3.1装夹方案的确定
零件均为45钢,且为单件小批量,工件伸出较短所以采用三爪自定心卡盘进行装夹即可满足要求。
2.3.2加工顺序及走刀路线的确定
加工顺序的确定拄由内到外,由粗到精,有近到远的原则确定,在次装夹中尽可能加工出较多的工件表面。
结台本零件的结构特征可先加工图2左端内孔轮廓,然后调头加工内椭圆然后加工图1左端轮廓加工好以后将图2与图1螺纹配台加工图1与图2¢43外圆柱面,然后调头加工图1右端由于该零件为单件小批量生产,走刀路线设计不必考虑最短进给路线或最短空行程路线,外轮廓表而车削走月路线可沿零件轮廓顺序进行。
酒杯模型的设计与车削加工
3.1项目产品展示
3.1.2项目图纸
3.2项目教学相关知识点
序号
设计内容
方法或目的
备注
1
各工厂成立
增强学生的企业员工意识
工厂化教学
2
绘制二维图纸及实体
软件使用、CAM软件找点
CAM软件
3
设计内外轮廓的加工工艺
填写工艺卡片、刀具的选用
机械加工知识
4
编写加工程序
带凹槽的G71的使用方法
数控车编程知识
5
数控车床加工产品
机床的操作技能
数控车床的操作
6
产品成本计算
增强产品质量及成本意识
与企业接轨
7
企业机密认定
增强学生的竞争意识
职业道德
8
项目组互评及老师总评
加强团队合作意识
职业素质培养
3.21项目教案
项目
酒杯模型的加工
课型:
理论与实践
授课日期
2009年5月26日
授课时数:
6
学时
教学目标
熟练掌握复合循环G71指令的应用,掌握内轮廓加工工艺,工艺卡片的填写
教学重点
复合循环G71指令各参数含义,工艺卡片的填写方法
教学难点
指令的循环起点、终点与切削起点、终点的确定
精车轨迹的功能,程序的编制与调试、内轮廓加工中G71的使用
教学过程
教学内容
教学方法与手段
1、课堂工厂化
通过小黑板简短进行各工厂及员工描述,展示各厂风采
讨论5分钟
2、项目引入
商代酒尊(铸造)金属酒杯(数控车床加工)
讲解、演示5分钟
3、员工的任务分工
各厂小黑板写出及任务分工
讨论5分钟
4、程序编制与调试
工艺卡片的填写
G71的使用及参数含义,酒杯完整程序的编写
讨论、指导、评价
10分钟
5、项目产品加工
装工件及刀具、对刀试加工
两人合作完成30分钟
6、成本核算
及企业机密认定
产品成本、加工工艺、图纸
讨论10分钟
7、产品图纸及实体绘制
通过电脑CAM软件完成
2人合作绘制30分钟
8、反馈与评价
通过该项目的实施,你还能提出哪些问题?
如何解决?
1.这些复合循环指令的精车轨迹的功能有哪些?
2.这些复合循环指令各参数的含义是什么?
3.那些图纸类型可以使用这些指令进行程序编写?
4。
零件程序及加工还有哪些地方需要改进?
数控高速车削梯形螺纹的方法
不论是在普通车床还是在数控车床上加工梯形螺纹对于中高职学生来讲总是存在较大的技术难度特别是在数控车床上高速车削梯形螺纹大部分的书籍和教材都没有做专题的介绍学生很难掌握其精细的计算和合理的加工工艺。
本文着重讲叙梯形螺纹高速车削方法。
4.1加工方法的选择
如图l所示在数控车床上加工梯形螺纹时在三爪卡盘采用一夹一项的方式为了对刀和和编制程序的方便将程序原点设置在工件右端面中心点另外还自制了对刀样板以方便粗、精车换刀时Z方向的准确性。
应该指出的是由于是高速加工梯形螺纹故选用的是硬质舍金刀具。
高速车削梯形螺纹时由于螺距过大为防止“扎刀”和“崩刃”要求在加工梯形螺纹时切削力不能太大刀具不能同时三面切削。
作者通过多年实践证明在经济型数控车床上不能用螺纹切削指令G32、G92来进行直进法或直进切槽法来加工即便近年来很多杂志上介绍的用G92结合子程序的左右摆动法来进行分层切削也不是最好的方法该方法虽然从理论上能使切削时受力小但是它忽视了我们常用的车床大多都是经济型盘控车床而经济型盘控车床控制系统为半闭环,以致左右摆动时无法使伺服系统跟上数控系统数值要求的步伐从而使加工螺距发生改变。
综合编程和加工来考虑结合实践经验我认为采用螺纹切削复合循环指令G76来加工是效果较好、安全、可靠、易行的一种方法。
4.2G76指令的相关介绍
G76指令是斜进式切削由于为单侧刃加工刀具负载较小排屑容易并且切削深度为递减式。
一般大螺距螺纹加工。
4.2.1G76指令的进刀路线和吃刀分配。
(图2)
4.3刀具几何形状的选择
根据高速车削梯形螺纹的条件首先计算出螺旋角以便正确刃磨刀具的几何角度。
螺旋角为a=[P/fd)]=arctan[5/(314×
255)1=,所以选择左侧后角6----8度右侧后角是2度是比较合适的;
为了便于排屑刀具不易损坏前角取6----8度使刀具更加锋利和有利于断屑特别指出的是我采用了粗、精车两把刀由于粗加工容易使车刀损伤和磨损故我将粗车刀刀尖角刃磨成圆弧型这样能够加强刀尖的强度即便粗加工量偏大时也有一定的保险系盘而精加工则完全按照螺纹形状刃磨。
要注意的是粗精车刀z方向对刀时零点的准确性。
粗、精车刀几何形状图如下:
4.4程序的编制
本文只讲叙梯形螺纹部分程序的编制具体如下:
%0003;
N10G90G95;
N20M3$350T0505;
N30GOX35Z.10
N40G76P020030Q20R002
G76X223Z-94P27500329F5
N50GOX120Z200,
N60M5
N70M30;
4.5影响
4.5.1螺纹加工程序段中指令的螺距/导程值,相当于以每转进给量表示的进给速度如果将机床的主轴转速选择过高则其换算后的进给速度必定大大超过机床参数所允许的最大进给量此时会发生机床按照“极限螺距”(极限螺距=最大进给量/转速1进行加工的现象。
4.5.2刀具在其位移的始终都将受到伺服驱动系统升,降频率和数控装置插补运算速度的约束。
由于升/降频率特性满足不了加工需要等原因则可能因主进给运动产生的“超前”和“滞后”而导致部分螺牙的螺距不符合要求;
车削螺纹必须通过主轴的同步运行功能实现即车削螺纹需要有主轴脉冲发生器编码器。
当其主轴转速选择过高时,通过编码器发出的定位脉冲(即主轴每转一周时所发出的一个基准脉冲信号)将可能发生“过冲“特别是当编码器的质量不稳定时将导致工件螺纹产生乱扣。
4.6因此车梯形螺纹时主轴转速选择遵循以下几个原则:
4.6.1在保证生产效率和正常切削的情况下,要根据“极限螺
距”计算公式求得加工最高转速宜选择较低的主轴转速;
4.6.2当螺纹加工程序段中的导入长度和切除长度较小时,选用相对较低的主轴转速;
4.6.3最大转速时可尽量选择高一些的主轴转速:
4.6.4通常隋况下车螺纹时的主轴转速应按其机床或数控系统说明书中规定的计算公式确定。
4.7另外还应注意:
4.7.1由于主轴速度发生变化有可能切不出正确的螺距、因此在螺纹切削期间不要使用叵表面切削速度控制指令G96。
4.7.2在螺纹切削期间进给速度倍率无效涸定在100蛳速度固定在100%。
4.7.3在螺纹切削程序段的前一程序段中不能指定倒角或倒圆。
4.7.4通常由于伺服系统滞后等原因会在螺纹切削的起点和终点产生不正确的导程因此螺纹的起点和终点位置应当比指定的螺纹长度要长。
减速器传动装置的设计
5.1设计说明及数据计算
箱体是减速器的重要组成部件。
它是传动零件的基座,应具有足够的强度和刚度。
本箱体采用灰铸铁制造。
灰铸铁具有很好的铸造性能和减振性能。
为了便于轴系部件的安装和拆卸,箱体制成沿轴心线水平剖分式。
上箱盖和下箱体用螺栓联接成一体。
轴承座的联接螺栓靠近轴承座孔。
为保证箱体具有足够的刚度,在轴承孔附近加支撑肋。
为保证减速器安置在基础上的稳定性并尽可能减少箱体底座平面的机械加工面积,箱体底座采用两纵向长条形加工基面。
根据所设计齿轮及轴的尺寸,初步确定减速箱的箱体尺寸为:
长×
宽×
高=540mm×
300mm×
440mm,其余各尺寸如下表:
5.1减速器机体结构尺寸
名称
符号
减速器形式及尺寸mm
机座壁厚
δ
0.025a+1取9
机盖壁厚
δ1
0.02a+1,因其小于8,故取其为8
机座凸缘厚度
b
1.5δ=13.5取其为14
机盖凸缘厚度
b1
1.5δ1=12
机座底凸缘厚度
b2
2.5δ=22.5
地脚螺钉直径
df
0.036a+12=24
地脚螺钉数目
n
因a<
250,故取n=4
轴承旁联接螺栓直径
d1
0.75df=15,因螺栓为标准件,故取其直径d1=18
机盖与机座联接螺栓直径
d2
(0.5~0.6)df=12
联接螺栓d2的间距
l
150~200,取其值为150
轴承端盖螺钉直径
d3
(0.4~0.5)df=8
窥视孔盖螺钉直径
d4
(0.3~0.4)df=10
定位销直径
d
(0.7~0.8)d2=8
df,d1,d2至外机壁距离
C1
34,24,18
df,d2至凸缘边缘距离
C2
28,16
轴承旁凸台半径
R1
20
凸台高度
h
外机壁至轴承座端面距离
l1
C1+C2+(8~12)=50
齿轮端面与内机壁距离
Δ2
>
δ=8大齿轮取12,小齿轮取9.5
机盖,机座肋厚
m1,m
m1≈0.85δ1=7,m≈0.85δ=8
轴承盖外径
D1,D2
D1=120,D2=150。
D1,D2分别为轴承6208,6211外圈外径。
轴承端盖凸缘厚度
t
(1~1.2)d3=10
轴承旁联接螺栓距离
s
160
5.2画得草图及附属零件的名称和作用如下
5.2.1箱座:
用于安装传动零件及其它附属零件
5.2.2箱盖:
5.2.3上、下箱联接螺栓:
将上、下箱联结成一个整体
5.2.4通气孔:
使箱体内热涨气体自由逸出,达到箱体内外气压相等,提高箱体有缝隙处的密封性能。
5.2.5窥视孔盖板:
检查孔用于检查齿面接触斑点和齿侧间隙,了解啮合情况以及注入润滑油。
检查孔盖板用于防止污物进入箱体内和润滑油飞溅出来。
5.2.6吊耳:
用于搬运及拆卸机盖。
5.2.7定位销:
保证轴承座孔的安装精度。
5.2.8油标尺:
用来检查油面高度,以保证有正常油量。
5.2.9放油螺栓:
用于排出污油,注油前用螺塞堵住。
5.2.10平键:
用于联接其它传动机构,如带轮,联轴器。
5.2.11油封:
防止润滑油飞溅出来。
5.2.12齿轮轴:
用于安装传动齿轮。
5.2.13挡油环:
防止箱体内润滑油进入轴承。
5.2.14轴承:
用于支撑齿轮轴。
5.2.15轴承端盖:
防止轴承润滑脂泄漏及污物进入轴承。
5.2.16齿轮:
用于传递运动和动力。
5.2.17轴套:
用于定位轴承。
在普通车床上设计自动钻孔装置
6.1流程
上PIN→钻孔→检查
6.2上PIN作业
钻孔作业时除了钻盲孔,或者非常高层次板孔位精准度要求很严,用单片钻之外,通常都以多片钻,意即每个stack两片或以上.至于几片一钻则视1.板子要求精度2.最小孔径3.总厚度4.总铜层数.来加以考虑.因为多片一钻,所以钻之前先以pin将每片板子固定住,此动作由上pin机(pinningmaching)执行之.双面板很简单,大半用靠边方式,打孔上pin连续动作一次完成.多层板比较复杂,另须多层板专用上PIN机作业.
6.3钻孔
6.4.钻孔机
钻孔机的型式及配备功能种类非常多,以下List评估重点
A.轴数:
和产量有直接关系
B.有效钻板尺寸
C.钻孔机台面:
选择振动小,强度平整好的材质。
D.轴承(