冀东油田水平位移最大井完钻Word格式文档下载.docx
《冀东油田水平位移最大井完钻Word格式文档下载.docx》由会员分享,可在线阅读,更多相关《冀东油田水平位移最大井完钻Word格式文档下载.docx(5页珍藏版)》请在冰豆网上搜索。
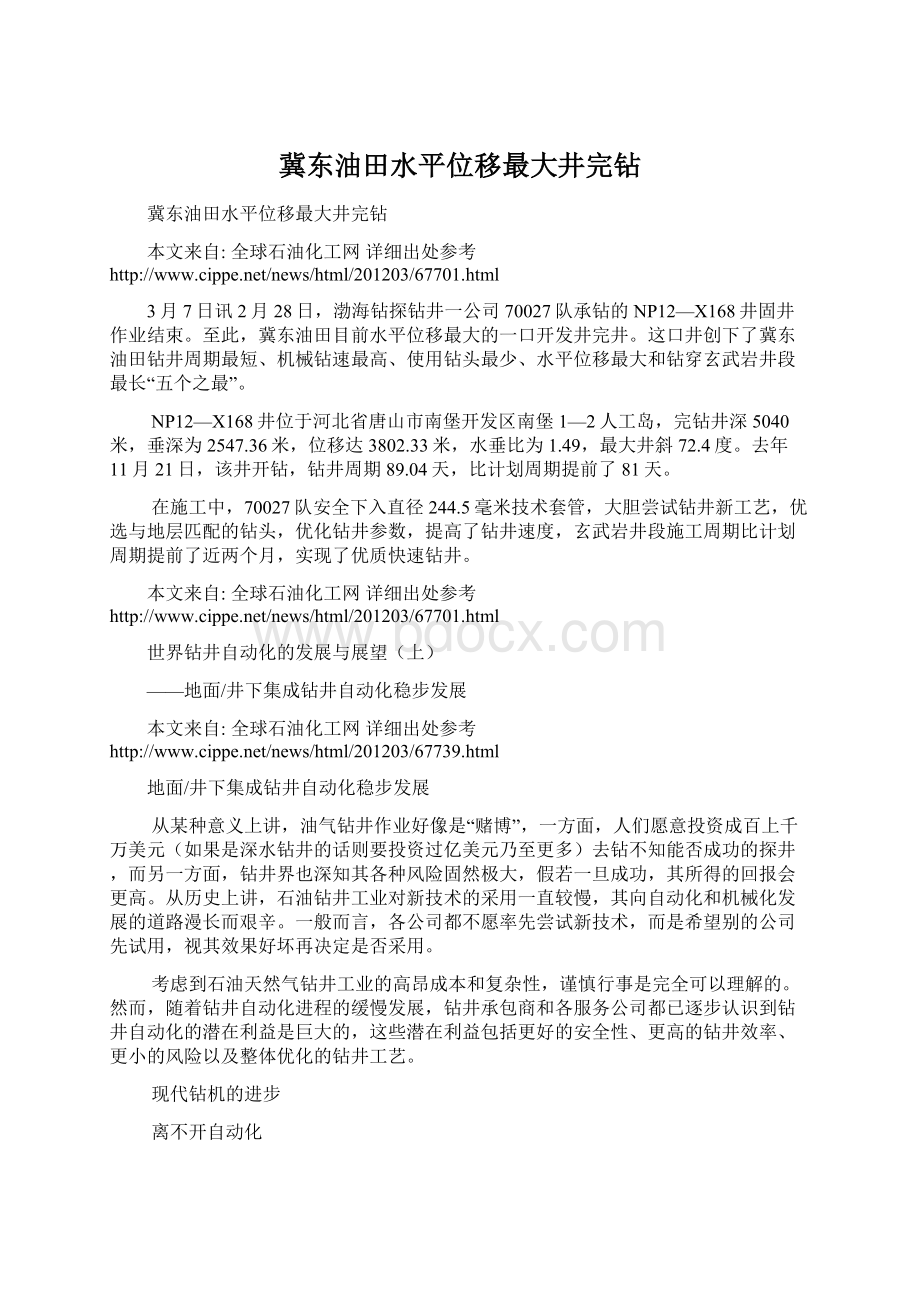
世界钻井自动化的发展与展望(上)
——地面/井下集成钻井自动化稳步发展
地面/井下集成钻井自动化稳步发展
从某种意义上讲,油气钻井作业好像是“赌博”,一方面,人们愿意投资成百上千万美元(如果是深水钻井的话则要投资过亿美元乃至更多)去钻不知能否成功的探井,而另一方面,钻井界也深知其各种风险固然极大,假若一旦成功,其所得的回报会更高。
从历史上讲,石油钻井工业对新技术的采用一直较慢,其向自动化和机械化发展的道路漫长而艰辛。
一般而言,各公司都不愿率先尝试新技术,而是希望别的公司先试用,视其效果好坏再决定是否采用。
考虑到石油天然气钻井工业的高昂成本和复杂性,谨慎行事是完全可以理解的。
然而,随着钻井自动化进程的缓慢发展,钻井承包商和各服务公司都已逐步认识到钻井自动化的潜在利益是巨大的,这些潜在利益包括更好的安全性、更高的钻井效率、更小的风险以及整体优化的钻井工艺。
现代钻机的进步
离不开自动化
整体而言,现代钻机在技术方面比以往任何时候都更为先进。
通过广泛采用交流变频电驱动钻机、电子司钻、PLC控制系统、顶驱装置、铁钻工、自动排管装置以及机械化猫道等先进设备,现代钻机不再依赖手工操作和低效率不精确的机械化系统。
先进的顶驱装置使钻机能够在起钻时进行倒划眼作业,从而更适合于钻较长的水平井段和大位移井。
PLC(可编程逻辑控制)技术也已被油田所采用,使得可以在钻台上集成多种机械装置,并使司钻能够在全天候的司钻控制室内远程协调控制各种钻井活动。
美国H&
P钻井公司在其FlexRig钻机上装配了电子司钻后,通过应用计算机、软件
和触摸屏控制装置来监控和调整多项钻井参数、优化钻井工艺并减少或消除了长期困扰钻井工业的一些常见问题,使钻井工业自动化又向前迈进了一步。
电子司钻与VFD(变频驱动)的结合应用可实现再生制动效果,取代机械制动装置,实现更精确和更稳定的控制且减轻司钻的体力负荷。
自动送钻装置也在不断发展,通过应用自动送钻装置和优化钻井工艺,在某些地区可提高钻井效率达30%。
目前通过与各种传感器、计算机和数据采集系统一起使用,先进的自动送钻装置能够连续的同时监控多项钻井参数,包括钻压、机械钻速、扭矩和压差等,根据在2009年SPE/IADE钻井大会上发表的一篇论文所披露的数据显示,与使用传统自动送钻装置钻井相比,使用先进的送钻装置钻井时机械钻速提高30%以上,而所用钻头只数则减少7%。
井下自动化成果多面“开花”
除了地面设备和钻机机械化以外,另一个使钻井人员激动的领域是井下活动的自动化及其与地面设备的集成。
众多业内人士已不再仅仅局限于对井下自动化充满好奇,而是真正的想使其变为现实。
井下测量技术日益发展,使作业人员对井眼情况有了更为清晰的了解;
有线钻杆技术也有了重大突破,能够更快更大量的向地面传输数据;
而钻井专家系统的出现则使井下钻井过程与地面自动化设备间的连接有了很大的进步。
有多家公司正在开发将标准作业与控制系统相互集成的工作,比如井眼缩径检测及自动机械钻速控制等。
过去几年间,Aker公司一直与SINTEF、HPD和StatoilHydro公司共同开发一种应用井眼可视技术和钻井工艺模型来优化并控制钻井的系统,试图研制出一种自动钻井顺序装置,将井下测量数据集成到一种在线决策支持工具中去。
这种开发结果可以与一种CADS(可配置自动钻井顺序)软件工具相集成,用以控制整个的钻井顺序。
比如钻井人员只需按一个用于起钻的按钮,该控制系统便会完成起钻顺序中的每一个步骤。
而在以前,这需要操作员的许多介入才能启动和停止不同的设备。
还有一个钻井自动化项目就是Drilltronics装置的研制,参与研制者试图制造出一种钻井自动导航装置,就像是用于航空和航海界的无人导向系统,Drilltronics装置的最终目标是能够应用计算机模型来控制钻井设备,以便可以对钻井工艺过程进行分析。
StatoilHydro、BP、ENI和国民油井华高公司都是该项目的参与者。
该项目的成员们正在对钻井过程进行建模,以便能够实现自动化或是减小风险,其中的大部分工作都集中于对井下压力的研究。
例如,专家们已经建立了一种计算机模型,这种模型能够确定泥浆泵在启动时不损坏地层的最大运行速度,计算机或是通知司钻应该所处的安全“包线”范围,或是在实际上对设备进行控制,使司钻不能意外地按动按钮,无意地超过最大速度。
理想的情况是实时井下数据将用来连续校正计算机。
Drilltronics装置于2008年就已在北海水域的StatfjordC钻井平台上完成了现场试验,根据IRIS公司的报道,在对12¼
英寸和8½
英寸井段进行开窗侧钻时对起下钻控制、半自动泥浆泵启动以及自动摩擦检测等模块进行了测试,在钻入储层后对Drilltronics装置进行了试验,没有出现任何问题。
目前专家们正在对该模型进行进一步的研究,不久便会再次对其进行现场试验。
操作简化、
注重安全成为趋势
随着陆上钻井朝着更高层次自动化的发展,供货商们都在纷纷寻找如何使昂贵复杂的技术在低成本环境中工作的途径。
例如,对于许多陆上钻机而言,要求必须配备专门的软件人员就不太切合实际,所以,类似于这方面的考虑正推动着设备供应商们重新考量其产品并找出更简单的使用方法。
此类简化的一个典型实例是铁架工,也就是安装在井架上的一种排管装置,它使用一个机械臂来提升和排放钻杆和钻铤,消除了人工井架工在二层平台上工作的需要。
从过去的工业事故统计数据来看,井架工是钻机上最危险的工种,所以铁架工能给井队带来明显的安全利益。
当结合应用铁钻工、动力大钳和顶驱装置时,司钻就可以在司钻控制台处对日常的钻井作业进行控制,不需要有人待在危险的位置。
而具有机械臂的铁帮手则可以在钻杆过井架大门移向井眼中心时控制钻杆的靠近状态,有助于下套管作业的顺利进行。
另外,在过去的5年间,顶部驱动下套管装置已在钻井工业界站稳脚跟。
威德福公司的增速传动装置将多个下套管工具融为一体,包括动力大钳、吊卡充填/循环工具以及重量补偿器,这类远程控制装置能实现无人下套管作业,具有明显的安全优势,且同时还具有钻井优势,人们可以在井眼中利用套管进行循环、做起下和旋转运动,从而可以用套管对井眼中的问题井同时进行划眼和钻进。
世界钻井自动化的发展与展望(下)
知识经验的传承
限制自动化进程
在钻井作业中发挥自动化或机械化最大优势,仍有许多障碍,其中最大的障碍之一就是我们自己。
在上世纪90年代,许多第一代深水钻机建造期间,大部分厂家都对自动化设备没有经验,许多人在这方面都留下了痛苦的回忆,几乎每台钻机都是客户定制的,控制钻机所需的软件数量巨大,通常都要花两年的时间才能编制完成;
装配到钻机上的设备几乎事先都没在现场使用过,且也没有进行过全方位的实验室试验,这就导致了大量的停机时间和维护困难;
在钻机上所需要的人员不是设想的那样更少,而是需要更多且技能更好的人员参与操作;
这就导致装有自动化设备的钻机效率还没有人工操作的钻机效率高。
这类问题现在都已不存在了。
相关技术已经成熟,相关人员已学会如何维护和修理复杂的设备,且供应商投入了更多的时间和精力在运抵现场之前对其设备进行检测,诸如闭环硬件(HIL)检测等技术也已被用于用控制装置的实际硬件来对软件进行检测。
整体而言,当今的新型海洋钻机都已没有大的工作问题;
同时,针对新设备,各公司都加强了对相关人员的事先培训,且在一台钻机上所学到的知识又可以应用到另一台钻机上,从而形成良性改进循环。
现在的问题就是要稳步可靠的引入新设备,且要牢记,在首次引入新设备时总是会遇到一些相关问题。
比如,马士基钻井公司初次应用其自升式钻井平台MÆ
RSKINNOVATOR时,其操作人员就缺乏经验和能力,而当这些人员积累了一定的经验以后,设备的工作效率便大为提升。
而且,当该公司后来开始应用其姊妹钻机MÆ
RSKINSPIRER时,第一台钻机的操作经验便被传授操作人员,使他们能够应用已有的知识操作新钻机。
但始终要记住一点,即使一位有经验的员工已经经过必要的培训,也一定要善于接受新知识和新技术,因为我们不可能在每个第一次都把事情做的百分之百正确。
远程作业
与无人钻机为时不远
展望未来,一些正在浮现的新技术是很重要的,比如有线钻杆和单板电脑(SBC)等,无论如何,钻井工业都已真正开始探索钻机远程操作的可能性。
如果能够从司钻控制室对钻台设备进行控制的话,那么从理论上说也应该能够从成百或上千英里以外对其进行控制。
这一理论早在2004年就已得到了证实,当时国民油井M/DTotco公司和斯伦贝谢公司通过从英国的剑桥发送指令而在美国的德克萨斯州进行钻井,在钻井过程中应用了远程联接自动控制技术(DrillLink)将远程信号传送到钻机控制系统上。
这种联接技术还被应用到墨西哥湾等地进行与地下旋转导向工具的通信以控制定向井的轨迹。
自动化和远程作业使人们对未来充满了希望,然而,如果考虑到钻井工业界在这些技术上所投入的精力与财力,我们不禁要问,我们真的需要能够自主作业的独立钻机吗?
这一点有可能实现吗?
首先,专家们都认为离实现自主钻机已经很近了,目前只是还缺少一个关键要素,即标准化。
无论是地下设备还是地面设备皆如此,都还缺少使供货商对所有操作实行标准化这一关键要素,当前也没有什么动力来推动钻井工业界对各种钻头及其它部件的不同尺寸和操作理念进行标准化,同时也没有一个“领头羊”向钻井工业推介用于钻井的“微软视窗”系统。
其次,自动化的目标真的是要在钻机上投放更少的人员(或无人)吗?
答案是否定的。
机器只适合于某些类型的工作,主要是重复性工作以及人员所不能够做到的、需要一定精度或具有一定复杂性的工作。
所以,当机器做这类工作时,并不意味着就能向钻机上派遣更少的人员,其目的是想使这些重复性工作简单化,以便使钻井人员能够集中于钻机上更为复杂的和更适合由人员来控制的一些变量。
在某种情况下,定向钻井公司需要培训其钻井人员如何安装井下工具,以便使负责定向钻井的司钻能够在远程控制中心进行工作。
类似这样的情况确实可以帮助钻井作业商,减少与人员旅行相关的费用并改善其钻井人员的安全性。
最后,自动化并不是要求“要么全有要么全无”,根据钻井环境的不同,对不同的自动化程度有着许多不同的要求。
自动化决不是最终目的,没有人仅仅是倾心于自动化,人们感兴趣的只是钻井过程的优化,而自动化只不过是工具之一。
尽管我们最终能够实现无人钻机,但这决不是目标,而是要成功地改进钻井性能。
事实上,完全自动钻机的概念——“按一下按钮,钻一口井”,对某些人来说是很有吸引力的,但对另外一些人来说则既没有吸引力又不现实。
然而,无论人们的看法如何,石油天然气钻井正向无人自动化作业稳步发展。