特种加工小论文Word格式文档下载.docx
《特种加工小论文Word格式文档下载.docx》由会员分享,可在线阅读,更多相关《特种加工小论文Word格式文档下载.docx(20页珍藏版)》请在冰豆网上搜索。
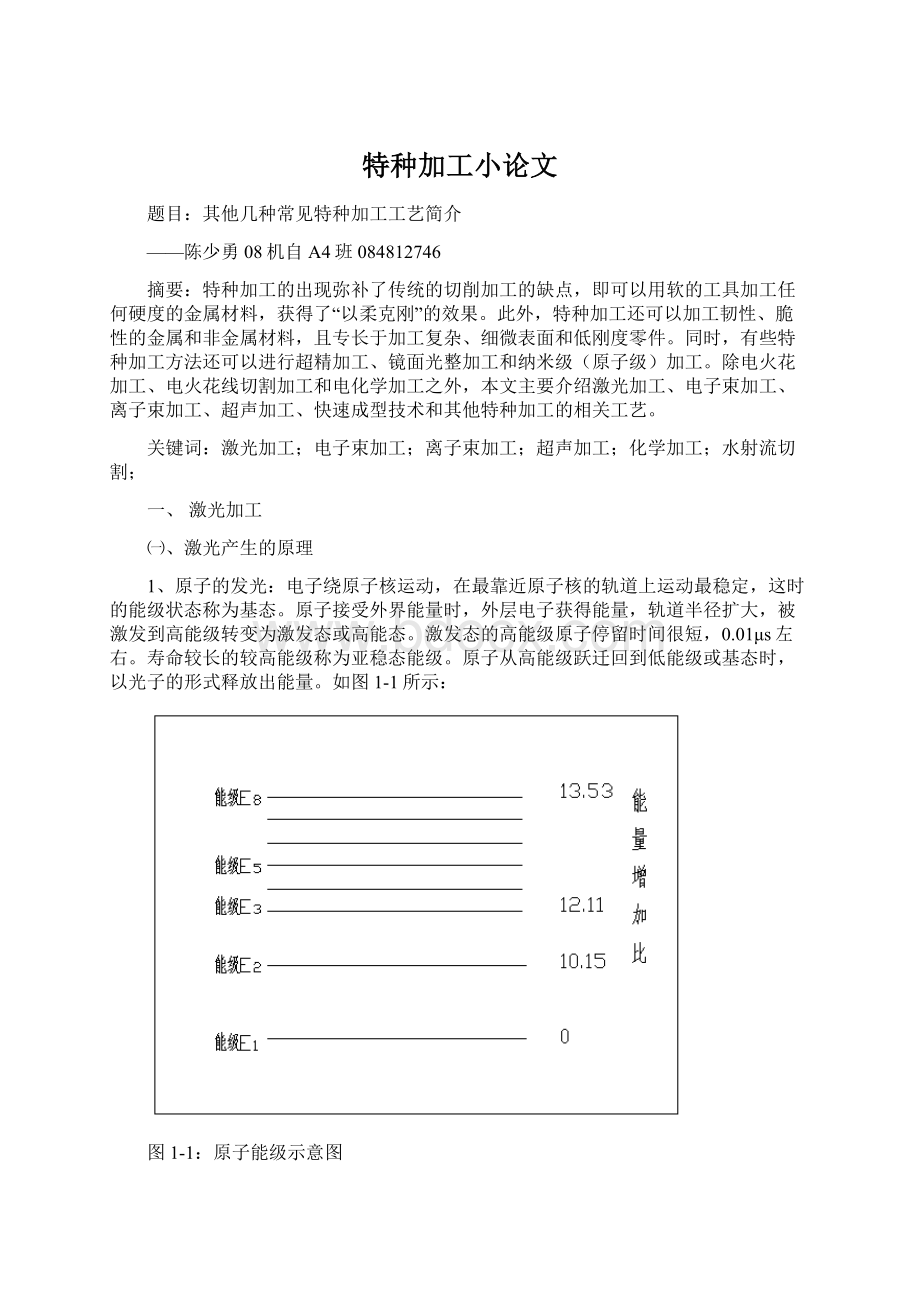
2、激光加工的原理:
激光加工是利用光的能量,经过透镜聚焦,在焦点上达到很高的能量密度,靠光热效应来加工材料的。
具体原理和特点如下:
①聚焦后,激光加工的功率密度非常高,光能转化为热能,几乎可以熔化、气化任何材料。
例如耐热合金、陶瓷、石英、金刚石等硬脆材料都能加工。
②激光光斑大小可以聚焦到微米级,输出功率可以调节,因此可以用以精密微细加工。
③加工所用工具是激光束,是非接触加工,所以没有明显的机械力,没有工具损耗问题。
加工速度快,热影响小,容易实现加工过程自动化。
还能通过透明体进行加工,如对真空管内部进行焊接加工等。
④和电子束加工等比较起来,激光加工装置比较简单,不要求复杂的抽真空装置。
⑤激光加工是一种瞬时、局部熔化、气化的热加工,影响因素很多,因此,精微加工时,精度,尤其是重复精度和表面粗糙度不易保证,必须进行反复试验,寻找合理的参数,才能达到一定的加工要求。
由于光的反射作用,对于表面光泽或透明材料的加工,必须预先进行色化或打毛处理,使更多的光能被吸收后转化为热能用于加工。
⑥加工中产生的金属气体及火星等飞溅物,要注意通风抽走,操作者应戴防护眼镜。
简而言之,激光加工的原理可以概括如下:
激光是一种亮度高、方向性好、单色性好的相干光。
由于激光发散角小和单色性好,理论上可通过一系列装置把激光聚焦成直径与光的波长相近的极小光斑,加上亮度高,其焦点处的功率密度可达107~1011w/cm2,温度高达万度左右,在此高温下,任何坚硬的或难加工的材料都将瞬时急剧熔化和气化,并产生强烈的冲击波,使熔化的物质爆炸式地喷射出去,这就是激光加工的工作原理。
㈢、激光加工的优点
根据激光的特性与其加工原理,可知激光加工有如下优点:
①激光功率密度大,加工材料范围广,激光几乎对所有的金属材料和非金属材料都可进行加工,即使熔点高、硬度大和质脆的材料(如陶瓷、金刚石等)也可用激光加工;
②激光头与工件不接触,不存在加工工具磨损问题;
③激光加工属于非接触加工,无受力变形;
受热区域小,工件热变形小,加工精度高;
④可以对运动的工件或密封在玻璃壳内的材料加工;
⑤激光束的发散角可小于1毫弧,光斑直径可小到微米量级,作用时间可以短到纳秒和皮秒,同时,大功率激光器的连续输出功率又可达千瓦至十千瓦量级,因而激光既适于精密微细加工,又适于大型材料加工;
⑥激光束容易控制,易于与精密机械、精密测量技术和电子计算机相结合,实现加工的高度自动化和达到很高的加工精度;
⑦加工速度快,加工效率高。
㈣、激光加工的基本设备
⑴、固体激光器:
红宝石激光器、钕玻璃激光器、掺钕钇铝石榴石激光器等。
⑵、气体激光器:
二氧化碳激光器、氩离子激光器。
㈤常见的激光加工工艺及应用
可由激光加工方法加工的材料范围非常广,几乎所有的金属材料和非金属材料都可进行激光加工。
并且激光加工属于非接触加工,无受力变形,受热区域小,工件热变形小,因此加工精度高,可进行微细加工。
例如:
激光聚焦后可实现直径0.01mm的小孔加工和窄缝切割。
在大规模集成电路的制作中,可用激光进行切片等。
激光加工还可以进行打孔、切割、刻蚀、焊接、热处理、电子器件的微调、以及激光存储等各个领域。
现仅介绍几种常见的激光加工工艺:
1、激光打孔
利用激光几乎可以在任何材料上打微型孔,目前已应用到火箭发动机和柴油机的燃料喷嘴加工、化学纤维喷丝板打孔、钟表及仪表中的宝石轴打孔、金刚石拉丝模加工等方面。
激光打孔的成形过程是材料在激光热源照射下产生的一系列热物理现象综合的结果。
它与激光束的特性和材料的物理性质有关,分析如下:
①输出功率与照射时间:
激光的输出功率越大,照射时间越长,工件获得的能量越多。
需要注意的是,激光加工的照射时间要控制在几分之一到几毫秒之内,因为,当激光能量一定时,照射时间太长会使热量传播到非加工区,时间太短则因功率密度过高而使蚀除物以高温气体喷出,都会使激光能量的使用效率降低。
②焦距与发散角
发散角小的激光束,经短焦距的聚焦物镜以后,在焦面上可以获得更小的光斑及更高的功率密度。
激光的功率密度越大,对工件的穿透力越大。
③焦点位置
焦点位置对于孔的形状和深度都有很大的影响。
如图1-2所示:
图1-2:
焦点位置与孔的断面形状
④光斑内能量分布
激光束经聚焦后光斑内各部分的光强度是不同的。
在基模光束聚焦的情况下,焦点的中心强度是最大的,越是远离中心,光强度越小,能量是以焦点为轴心对称分布的,打出的孔自然是圆的。
当光束不是基模输出时,能量不对称,加工的孔也必然不是对称的。
激光在焦点附近的光强度分布与工作物质的光学均匀性及谐振腔调整精度有关。
如果对孔的圆度要求特别高,就必须使激光器只在基模振荡。
如图1-3所示:
图1-3:
激光能量分布对打孔质量的影响
⑤激光的多次照射
用激光器照射一次,加工的深度大约是孔径的五倍左右,而且锥度较大。
如果用激光多次照射,其深度可以大大增加,锥度可以减小,而孔径几乎不变,这是由于光管效应的缘故。
如图1-4所示:
图1-4:
光管效应示意图
值得注意的是,当照射20到30次后,孔的深度达到饱和,如果单位脉冲能量不变,就不能继续加深孔。
如1-5所示图:
图1-5:
照射次数与孔深关系示意图
单位脉冲能量:
1-2.0J2-1.5J3-1.0J
⑥工件材料
由于各种工件材料的吸光光谱不同,经透镜聚焦到工件上的激光能量不可能全部被吸收,生产实践中,必须根据工件材料的性能选择合理的激光器。
注意事项:
需要注意的是,激光加工的照射时间要控制在几分之一到几毫秒之内,因为当激光能量一定时,照射时间太长会使热量传播到非加工区,时间太短则因功率密度过高而使蚀除物以高温气体喷出,都会使激光能量的使用效率降低。
2、激光切割
激光可以切割各种各样的材料。
既可以切割金属,也可以切割非金属;
既可以切割无机物,也可以切割皮革之类的有机物。
由于激光对被切割材料几乎不产生机械冲击和压力,故适宜于切割玻璃、陶瓷和半导体等即硬又脆的材料。
再加上激光的斑点小、切缝窄,且便于自动控制,所以更适宜于对细小部件作各种精密切割。
切割金属材料时,采用同轴吹氧的工艺可以大大提高切割速度,而且表面粗糙度也有明显改善。
大功率二氧化碳气体激光器所输出的连续激光,可以切割钢板、钛板、石英、陶瓷以及塑料、木材、布匹、纸张等,其工艺效果都很好,如表1-1、表1-2所示:
表1-1:
二氧化碳激光器对金属材料切割的有关数据
材料
厚度/mm
切割速度m/min
激光输出/w
喷吹气体
铝
12.7
13
0.5
2.3
6000
15000
空气
碳素钢
3
6.5
0.6
250
氧气
不锈钢
2
1.3
10000
氮气
钛合金
5
3.3
850
表1-2:
二氧化碳激光器对非金属材料切割的有关数据
石英
0.43
500
陶瓷
1
4.6
0.392
0.075
有机玻璃
20
25
0.171
15
8000
混凝土
30
0.4
4000
无
皮革
3.05
225
激光加工切割布匹、纸张、木材等易燃材料时,可以采用同轴吹保护气体(二氧化碳、氮气等),以防止烧焦和缩小切缝。
3、激光刻蚀
小功率的激光束可以用于对金属或非金属表面进行刻蚀打标,加工出文字图案或工艺美术品。
激光刻蚀时,应采用小功率激光束。
二、电子束加工
㈠、电子束加工的原理
电子束加工是在真空条件下,利用聚焦后能量密度极高的电子束,以极高的速度冲击到工件表面极小面积上,在极短的时间内,其能量的大部分转变为热能,使被冲击部分的工件材料达到几千摄氏度以上的高温,从而引起材料局部熔化和气化,被真空系统抽走。
控制电子束能量密度的大小和能量注入,就可以达到不同的加工目的。
㈡、电子束加工的特点
电子束加工的特点总结如下:
⑴由于电子束能够极其微细地聚焦,甚至能聚焦到0.1μm。
所以加工面积很小,是一种精密微细的加工方法。
⑵电子束能量密度高,使照射部分的温度超过材料的融化和气化温度,去除材料主要靠瞬时蒸发,是一种非接触式加工。
工件不受机械力作用,不产生宏观应力和变形。
加工材料范围很广,对脆性、韧性、导体、非导体及半导体材料都可加工。
⑶电子束的能量密度高,因而加工生产率很高,每秒钟可以在2.5㎜厚的钢板上加工50个直径为0.4㎜的孔。
⑷可以通过磁场或电场对电子束的强度、位置、聚焦等进行直接控制,所以整个加工过程便于实现自动化。
在电子束爆光中,从加工位置找准到加工图形的扫描,都可实现自动化。
在电子束打孔和切割时,可以通过电气控制加工异形孔,实现曲面弧形切割等。
⑸电子束加工是在真空中进行,污染少,加工表面不会氧化,特别适用于加工易氧化的金属及合金材料,以及纯度要求极高的半导体材料。
⑹电子束加工需要一套专用设备和真空系统,价格较贵,生产应用有一定局限性。
㈢、电子束加工装置
电子束加工装置主要由电子枪、真空系统、控制系统和电源主成。
㈣、电子书加工的应用
电子束加工按其功率密度和能量注入时间不同,可用于打孔、切割、刻蚀、焊接、热处理和光刻加工等。
1、高速打孔
电子束打孔已经在实际生产中应用,目前最小直径可达0.003mm左右,例如:
喷气发动机套上的冷却孔,机翼的吸附屏的孔,不急内孔的密度可以连续变化,而且孔数达数百万个,有时还可以改变孔径,最宜用电子束高速打孔,打孔可以再工件运动中进行,例如在0.1mm厚度的不锈钢上加工直径为@!
$@!
#%0.2MM的孔,速度为每秒3000孔。
同时,电子束打孔还能加工小深孔。
2、加工型孔及特殊表面
电子束可以用来切割各种复杂型面,切口宽度为6~3um,边缘表面粗糙度可以控制在Ra0.5左右电子束不进可以加工各种直径的型孔和型面,也可以加工弯孔和曲面。
利用电子束在磁场中偏转的原理,使电子束在工件内部偏转。
控制电子速度和磁场强度,可以控制曲率半径加工出弯曲的孔。
如果同时改变电子束和工件的相对位置,就可进行切割和开槽。
3、刻蚀
在微电子器件生产中,为了制造多层固体组建,可以利用电子束对陶瓷或者半导体材料刻出许多细微沟槽和孔来。
电子束刻蚀还可以用于制版。
4、焊接
电子束焊接是利用电子束作为热源的一种焊接工艺。
由于电子束的能量密度搞,焊接速度快,所以电子束焊接的焊缝深而窄,焊件热影响区小,变形小。
电子束焊接一半不用焊条,焊接过程在真空中进行,因此焊缝化学成分纯净,焊接接头的强度往往高于母材。
由于电子束焊接对罕见的热影响小,变形小,可以再工件精加工后进行焊接。
电子束热处理也是把电子束作为热源,但适当降低电子束的功率密度,使金属表面加热而不熔化,达到热处理的目的。
5、热处理
电子束热处理与激光热处理雷同,但电子束的电热转换效率高,可达到,而激光转换效率只有。
电子束热处理在真空中进行,可以防止材料氧化,电子束设备的功率可以做的比激光功率大,所以电子束热处理工艺很有发展前途。
㈤、注意事项
用电子束加工玻璃、陶瓷、宝石等脆生材料,由于在加工部位的附近有很大温差,容易引起变形甚至破裂,所以在加工前或者加工时,需用电阻炉或者电子束进行预热。
三、离子束加工
㈠、离子束加工的原理与物理基础
1、离子束加工的原理:
离子束加工的原理是在真空条件下,将离子源产生的离子束经过加速聚焦,使之撞击到工件表面,靠微观的机械撞击能量来加工的。
与电子束加工相比:
相同点:
①在真空条件中进行
②粒子束加工
不同点:
①带正电荷的离子。
质量比电子大数千、数万倍,如氩离子的质量是电子的7.2万倍。
②靠微观的机械撞击能量来加工的。
离子束比电子束具有更大的撞击动能。
2、离子束加工的物理基础
离子束射到材料表面时所发生的撞击效应、溅射效应、注入效应。
㈡、离子束加工的分类
离子束加工按照其所利用的物理效应和达到目的的不同,可以分为四类:
⑴离子刻蚀:
用能量为0.5-5keV的氩离子倾斜轰击工件,将工件表面的原子逐个剥离,其实质是一种原子尺度上的切削加工,所以又称离子铣削。
这就是近代发展起来的毫微米(纳米)加工工艺。
⑵离子溅射沉积:
采用能量为0.5-5keV的氩离子,倾斜轰击某种材料制成的靶,离子将靶材原子击出,垂直沉积在靶材附近的工件上,使工件表面镀上一层薄膜,溅射沉积是一种镀膜工艺。
⑶离子镀:
用0.5-5keV的氩离子,同时轰击靶材和工件表面。
轰击工件表面的目的是为了增强膜材与工件基材之间的结合力。
也可将靶材高温蒸发,同时进行离子撞击镀膜。
⑷离子注入:
采用5—500keV较高能量的离子束,直接垂直轰击被加工材料,离子就钻进被加工材料的表面层,使工件表面层含有注入离子后,就改变了化学成分,从而改变了工件表面层的机械物理和化学性能。
根据不同的目的选用不同的注入离子,如磷、硼、碳、
氮等。
㈢、离子束加工的特点
⑴离子束加工将工件表面的原子逐个剥离,其实质是一种原子尺度上的切削加工,因此,离子束加工是所有特种加工方法中最精密、最微细的加工方法,是纳米加工技术的基础。
⑵由于离子束加工是在真空中进行,所以污染少,特别适用于对易氧化的金属、合金材料和高纯度半导体材料的加工。
⑶加工应力、热变形等极小,加工质量高,适合于对各种材料和低刚度零件的加工。
⑷离子束加工设备费用贵、成本高,加工效率低,应用范围受到一定限制。
㈣、离子束加工装置
离子束加工装置有离子源、真空系统、控制系统和电源等部分组成,常用的离子源头有考夫曼型离子源和双等离子管型离子源等。
㈤、离子束加工的应用
1、刻蚀加工
⑴刻蚀加工的原理:
离子刻蚀是从工件上去除材料,是一个撞击溅射过程。
当离子束轰击工件,入射离子的动量传递到工件表面的原子,传递能量超过原子间的键合力时,原子就从工件表面撞击溅射出来,达到刻蚀的目的。
刻蚀加工时,对离子入射能量、束流大小、离子入射到工件上的角度工作室气压等都能分别调节控制。
根据不同加工需要选择参数,用氩离子轰击被加工表面时,其效率取决于离子能量入射角度。
离子能量从100eV增加到1000eV时,刻蚀率随能量增加而迅速增加,而后增加速率逐渐减慢。
离子刻蚀率随入射角θ增加而增加,但入射角增大会使表面有效束流减小,一般在入射角θ=40°
-60°
时刻蚀效率最高。
⑵离子束刻蚀的应用:
①离子刻蚀用于加工陀螺仪空气轴承和动压马达上的沟槽,分辨
率高,精度、重复一致性好。
②加工非球面透镜能达到其他方法不能达到的精度。
③刻蚀高精度的图形,如集成电路、声表面波器件、磁泡器件、
光电器件和光集成器件等微电子学器件亚微米图形。
④用来致薄材料,用于致薄石英晶体振荡器和压电传感器。
2、镀膜加工
离子镀膜加工有溅射沉积和离子镀两种。
离子镀时工件不仅接受靶材溅射来的原子,还同时受到离子的轰击,这使离子镀具有许多独特的优点。
3、离子注入加工
离子注入是向工件表面直接注入离子,它不受热力学限制,可以注入任何离子,且注入量可以精确控制,注入的离子是固溶在工件材料中,含量可达10%-40%,注入深度可达1um甚至更深。
㈥、经验总结
1、在高速钢刀具上用离子镀氮化钛,刀具寿命可以提高1~2倍。
2、离子注入可以提高金属材料的硬度,也可以改善金属材料的润滑性能。
四、超声加工
㈠、超声波及其特性
人耳能感受到的声波频率在16~16000Hz范围内,频率超过16000Hz超出一般人耳听觉范围,就称为超声波。
超声波可以在气、液、固体介质中纵向传播。
超声波主要具有下列特性:
⑴超声波能传递很强的能量,由于超声波频率很高,其能量密度可达100W/cm2以上。
在同一振幅时,液体、固体中的超声波强度、功率、能量密度要比空气中的声波高千万倍。
⑵当超声波经过液体介质传播时,将以极高的频率压迫液体质点振动,在液体介质中连续地形成压缩和稀疏区域,由于液体基本上不可压缩,由此产生压力正、负交变地液压冲击和空化现象。
高频振动会使液体中产生大量地小气泡,即微细间隙-空化腔。
这些小气泡会随声振动而强烈生长,最终达到更强烈的闭合,即破裂或称崩溃。
在气泡破裂瞬间,会产生极大的声冲击力作用,这种现象称为空化现象。
这一交变的脉冲压力作用在临近的零件表面上会使其破坏,引起固体物质分散、破碎等效应。
⑶超声波通过不同介质时,在界面上发生波速突变,产生波的反射和折射现象。
为改善传递条件,在连接界面加机油、凡士林等作为传递介质以消除空气及因它引起的衰减。
⑷超声波在一定条件下,会产生波的干涉和共振现象,为使弹性杆处于最大振幅共振状态,弹性杆设计成半波长的整数倍;
而固定弹性杆的支撑点,应选在振动过程中的波节(x=(2k+1)λ/4)处。
㈡、超声加工的原理
超声加工是利用工具端面作超声频振动,通过磨料悬浮液加工脆硬材料的一种成形方法。
超声加工时,在工具和工件之间加入液体(水或没有等)和磨料混合的悬浮液,并使工具以很小的力F轻轻压在工件上。
超声换能器产生16000Hz以上的超声频纵向振动,并借助于变幅杆把振幅放大到0.05~0.1mm左右,驱动工具端面作超声振动,迫使工作液中悬浮的磨粒以很大的速度和加速度不断撞击、抛磨被加工表面,把被加工表面的材料粉碎成很细的微粒,从工件上被打击下来。
同时,工作液受工具端面超声振动作用而产生的高频、交变的液压正负冲击波和“空化”作用,促使工作液钻入被加工材料的微裂缝处,加剧了机械破坏作用。
(空化作用会引起极强的液压冲击波)
空化作用可强化加工过程,液压冲击也是悬浮工作液强迫循环,使变钝的磨粒得到更新。
由此可见,超声加工是磨粒在超声振动作用下的机械撞击以及超声空化作用的综合结果,其中磨粒的撞击作用是主要的。
㈢、超声加工的特点
⑴适合于加工各种硬脆材料,特别是不导电的非金属材料,例如玻璃、陶瓷、石英、锗、硅、宝石、金刚石等。
⑵由于工具可用较软材料,做成复杂形状,故不需工具与工件做比较复杂的相对运动,因此超声加工机床的结构比较简单,只需一个方向的进给,操作维修方便。
⑶去除材料靠磨料瞬时局部的撞击作用,宏观切削力很小,切削应力、切削热很小,不会引起变形和烧伤,表面粗糙度也较好,而且可加工薄壁、窄缝、低刚度零件。
㈣、超声加工设备及其组成部分
超声加工设备包括超声发生器、超生振动系统、机床本体和磨料工作液循环系统。
㈤、超声加工速度、精度、表面质量及其影响因素
⑴加工速度及其影响因素
定义:
加工速度是指单位时间内去除材料的多少,单位以g/min或mm3/min,玻璃的最大加工速度可达2000~4000mm3/min。
影响因素:
工具振动频率、振幅、工具和工件间的静压力、磨料的种类和粒度、磨料悬浮液的浓度、供给及循环方式、工具与工件材料、加工面积、加工深度等。
1工具的振幅和频率的影响
过大的振幅和过高的频率会使工具和变速杆承受很大的内应力,可能超过它的疲劳强度而降低使用寿命,而且联接处损耗加大。
因此一般取振幅在0.01~0.1mm,频率在16000~25000Hz。
实际加工时调至共振频率,以获得最大的振幅。
②进给压力的影响
加工时工具对工件应有一个合适的进给压力。
压力过小,工具末端与工件加工表面间的间隙增大,从而减弱了磨料对工件的撞击力和打击深度;
压力过大,会使工具与工件间隙减小,磨料与工作液不能顺利循环更新,都将降低生产率。
一般而言,加工面积较小时,单位面积最小静压力较大。
加工面积5~13mm2时,最佳静压力约400kPa,加工面积20mm2以上时,最佳静压力约在200~300Kpa。
③磨料种类和粒度的影响
硬度高,加工速度快,但要考虑价格成本。
另外,磨料粒度越粗,加工速度越快,但精度和表面粗糙度则会变差。
④磨料悬浮液浓度的影响
浓度低,加工速度大大下降,浓度增加加工速度增加,但不宜太高。
通常采用的浓度为磨料对水的质量比为0.5~1左右。
⑤被加工材料的影响
脆性材料,易于加工;
韧性材料,不易加工。
⑵超声加工的加工精度及其影响因素
超声加工的精度,除受机床、夹具精度影响之外,主要与磨料粒度、工具精度及其磨损情况、工具横向振动大小、加工深度、被加工材料性质等有关。
一般加工孔的尺寸精度可达±
0.02~0.05mm。
①孔加工范围:
一般超声加工的孔径范围为0.1~90mm,深度可达直径10~20倍以上,如下1-3表所示:
表1-3:
超声加工功率与最大孔径的关系
超声加工输出功率/w
50~100
200~300
500~700
1000~1500
2000~2500
最大加工不通孔直径/mm
5~10
15~20
25~30
30~40
40~50
>
60
用中空工具加工最大通孔直径/mm
20~30
60~80
80~90
90
②孔的尺寸精度
超声加工孔的精度,在采用240#~280#磨粒,一般可达±
0.05mm;
采用W28~W7磨粒,可达±
0.02mm或更高。
如表1-4所示:
表1-4:
磨料粒度及其基本磨粒尺寸范围
磨粒粒度
120#
180#
240#
W40
W20
W7
磨粒尺寸范围/um
125~100
80~63
63~50
40~28
20~14
7~5
⑶表面质量及其影响因素
①表面质量较好,不会产生表面烧伤和表面变质层。
②