汽车门把手模流分析分析方案.docx
《汽车门把手模流分析分析方案.docx》由会员分享,可在线阅读,更多相关《汽车门把手模流分析分析方案.docx(10页珍藏版)》请在冰豆网上搜索。
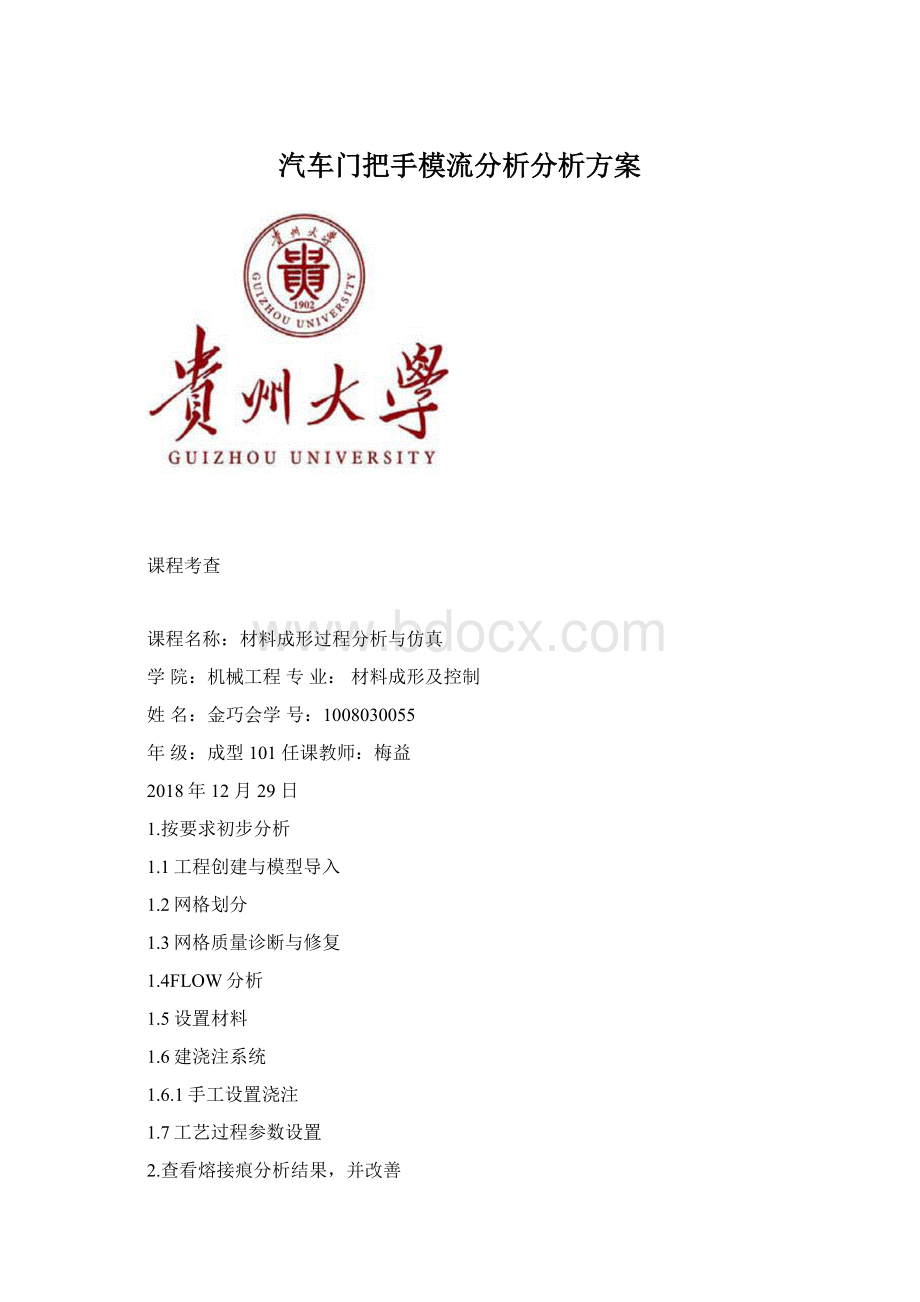
汽车门把手模流分析分析方案
课程考查
课程名称:
材料成形过程分析与仿真
学院:
机械工程专业:
材料成形及控制
姓名:
金巧会学号:
1008030055
年级:
成型101任课教师:
梅益
2018年12月29日
1.按要求初步分析
1.1工程创建与模型导入
1.2网格划分
1.3网格质量诊断与修复
1.4FLOW分析
1.5设置材料
1.6建浇注系统
1.6.1手工设置浇注
1.7工艺过程参数设置
2.查看熔接痕分析结果,并改善
2.1Flow分析结果
2.2.1原因
2.2.2减少熔接痕办法
3.针对原因对产品浇注位置进行重新设计
3.1分析最佳浇口位置
3.2浇注位置与尺寸
3.3分析结果
1.按要求初步分析
1.1工程创建与模型导入
1.2网格划分
采用默认边长设置
进行网格统计之后,发现匹配率过低,采取重新划分网格的方法,将边长修改为3,匹配率有很大的提高。
1.3网格质量诊断与修复
重新划分网格之后,进行网格统计与网格诊断,使用网格工具对其进行修改。
主要包括配向、重叠、交叉、自由边、纵横比等修复,缺陷的修复以能够顺利进行分析<即中间不自动中断分析)为准则。
修改结束之后的网格统计为
除匹配率外其他条件都已符合要求。
但花了一天时间,无论怎么修改边长,纵横比,匹配率都难以达到80%,为了继续进行分析,先暂且搁置,答辩时由梅老师来解惑。
1.4FLOW分析
分析类型设置为FLOW。
1.5设置材料
材料设置为LustranABSEliteHH1827材料。
该材料有以下特点:
良好的着色性,良好的流动性,良好的韧性,高耐热性、低光泽,用于汽车内饰件。
1.6建浇注系统
首先将门把手镜像出来。
在镜像过程中设置参考点时,默认用了<000)坐标,结果发现镜像出来的两个模型相距特别远,根本无法插入正确的浇注系统。
我曾经试图将零件模型整体移动,移回坐标原点,在经过多次尝试和思考之后,最终确定以零件上的一点为参考点,以XZ为参考平面,通过坐标与分流道的长度计算,进行了镜像复制,效果尚好。
1.6.1手工设置浇注
手工设置浇注系统如图1所示。
其中,主流道为锥形,上下端口分别为4mm和9mm,截面为圆形,长度为60mm,分流道截面为正方形,边长为5mm,每条分流道长度为13mm,侧浇口截面为矩形,长边为5mm,短边为3mm,浇口长度为2mm
实际效果图如下
1.7工艺过程参数设置
工艺过程参数使用默认设置。
进行充填分析。
2.查看熔接痕分析结果,并改善
2.1Flow分析结果
分析结果:
1.FillTime:
充模总时间2.334s。
无欠注。
观察动画模拟结果
2.PressureatV/Pswitchover:
观察转换点压力分布图。
3.Weldline观测:
要求与Filltime图叠加观测。
由图可看出,有孔的部位和最后充填的边沿处有较多的熔接痕。
2.2分析熔接痕产生原因及消除方法
2.2.1原因
塑件熔接痕产生的主要表现是:
在塑件表面出现的一种线状痕迹,有碍塑件的外观形象,且力学性能也受到一定影响。
产生熔接痕的主要原因:
系由若干胶熔体在型腔中汇合在一起时,在其交汇处未完全熔合在一起,彼此不能熔合为一体而形成熔合印痕。
其具体分析如下。
1)浇口截面积过小,使得熔体在进入型腔后分成多股,且流速又不相同,很易产生熔接痕,对此,。
2) 浇注系统的主流道进口部位或分流道的截面积太小,导致熔体流入阻力增大,而引起熔接不良。
2.2.2减少熔接痕办法
减少熔接痕办法:
从形成熔接痕的原因而言,要减少熔接痕,就要降低注射或挤出过程中物料的“分流后汇合”现象发生的可能性。
为了减少并消除这一现象,有如下方法:
1)提高模具温度
2)调整注射速度
3)全面排气
4)保持模具表面清洁
5)调整注射压力和补塑压力
6)合理设置浇口位置
7)增大浇口截面积
8)扩大主流道及分流道截面积
3.针对原因对产品浇注位置进行重新设计
3.1分析最佳浇口位置
分析结果:
最大设计锁模力=5600.18tonne
最大设计注射压力=144.00MPa
建议的浇口位置有:
靠近节点=3891
最佳浇口位置模拟图
3.2浇注位置与尺寸
其中,主流道为锥形,上下端口分别为3mm和6mm,截面为圆形,长度为60mm,分流道截面为圆形,直径为5,每条分流道长度为15mm,弧形浇口coldgate尺寸,锥形,始端1,截面为圆形,末端3。
结构如下图所示。
3.3分析结果
1、FillTime:
记录充模总时间,是否有欠注,观察动画模拟结果。
2、PressureatV/Pswitchover:
观察转换点压力分布图。
3、Weldline观测:
要求与Filltime图叠加观测。